Скрипник Роман Сергійович
Фізико-металлургійний факультет
Кафедра Обробки металу тиском
Спеціальність Обробки металу тиском
Организація виробництва холоднокатаного листа
Науковий керівник: д.т.н., проф. Конновалов Юрій В'ячеславович
Реферат за темою випускної роботи
Зміст
- Вступ
- 1. Сучасне становище в Україні з холоднокатаних листів і актуальність теми
- 2. Мета і завданняб що вирішуються в наданій роботі
- 3. Вибір типу стана
- 3.1 Аналіз існуючих станів і вибір табору
- 3.2 Вибір параметрів для даного типу стана
- 4. Вибір методики для розрахунку сили прокатки
- 5. Розрахунок режимів і сили прокатки на даному типі стану
- 6. Рекомендаціі з установки систем автоматики на стані
- Перелік посилань
Вступ
Високоякісний холоднокатаний лист є основою машинобудівної галузі, тому даний вид продукції має широкий попит як на внутрішньому так і на світовому ринку. При нанесенні захисних покриттів на холоднокатану смугу або лист їхня вартість значно зростає.
У 2010 р. в Україну почали роботу два нових заводи з виробництва оцинкованого і пофарбованого плоского прокату - «Юність» (Кривий Ріг) та «Метали і полімери» (Алчевськ). Найближчим часом, обидва підприємства планують суттєво збільшити обсяги виробництва. Ще один діючий завод «Модуль» спеціалізується на оцинкування холоднокатаного листа знаходиться в Кам'янець-Подільському. Загальна потреба трьох даних заводів в х / к прокаті складає приблизно 1 млн. тонн на рік.
1. Сучасне становище в Україні з холоднокатаних листів і актуальність тем
Виробники прокату з покриттями в основному використовують імпортний х / к прокат, пояснюючи це рішення тим, що рулони виробництва ВАТ «ЗМК« Запоріжсталь »і ВАТ ММК ім. Ілліча не відповідають сучасним вимогам: у них занадто високі допуски по товщині прокату та інші вади, які пояснюються застарілим обладнанням прокатних цехів меткомбінатів. Стан 1700 ПАТ ММК ім. Ілліча холодної прокатки відноситься до другого покоління безперервних станів, реконструкція основного обладнання проходила в 70-х роках і на даний момент сильно застаріло, всі системи автоматики на стані так само не відповідають сучасним світовим стандартам. Безперервний стан холодної прокатки 1700 ВАТ «ЗМК« Запоріжсталь »відноситься до станам першого покоління і його модернізація практично неможлива.
Ситуація, що склалася робить наш ринок залежним від імпорту холоднокатаного листа.
2. Мета і задачі дослідження та заплановані результати
Метою цієї роботи, є розробка пропозицій з організації виробництва холоднокатаного листа обсягом до 1 млн. тонн / рік в умовах економічної ситуації, що склалася в Україні. Вибір типу табору, встановлення оптимальних режимів обтиснення, і рекомендацій щодо застосування систем автоматики на таборі.
3. Вибор типу стана
3.1 Аналіз існуючих станів і вибір стана
В даний час на великих металургійних комбінатах холоднокатаний лист виробляють безперервним способом на безперервних станах і станах нескінченної прокатки. При невеликих обсягах використовують реверсивну прокатку на одноклетьових і, тільки в самий останній час, на двоклетьових станах реверсивної прокатки [1-3].
В умови відсутності сучасних станів холодної прокатки на території Україні доцільно будівництво нового стану холодної прокатки. Загальна потреба внутрішнього ринку в холоднокатаного листа складає близько 3 млн. тонн на рік. Будівництво стана нескінченної прокатки продуктивністю близько 2,5 млн. тонн на рік дозволило б практично повністю покрити потреби внутрішнього ринку Україні в даному виді продукції. Однак вартість одного тільки стана без допоміжного устаткування становить понад 500 млн. доларів. Для сучасної економіки Україні ця сума поки нереальна. Тому на першому етапі вирішення проблеми з холоднокатаних листів в Україну і відмовою від імпорту, пропонується будівництво двоклітьового реверсивного стану, для того, щоб в найкоротші терміни покрити першорядну потреба в прокаті трьох цехів з нанесення захисних покриттів. Продуктивність такого стану становить 800-1000 тис. тонн на рік, а його вартість більш ніж в 2 рази нижче ніж 5-и клітьового безперервного стану.
3.2 Вибір параметрів для даного типу стана
Довжину бочки клітей цього стану доцільно мати 1700 мм або 1680 мм, що дозволить використовувати підкат зі стану гарячої прокатки 1700. Обов'язкова умова - встановлення на цьому таборі однакових моталок з обох сторін табору. Це дозволить здійснювати будь-яке число проходів і при необхідності проводить проміжний відпал.
Все це дозволить використовувати гарячекатаний підкат у великому діапазоні товщини: від 2 до 6 мм. Це дозволить застосовувати підкат як з діючих в Україну ШСГП, так імпортний підкат (який значно дешевше холоднокатаного листа).
Широкі можливості по вибору товщини підкату з одного боку дозволяє вибрати варіант, який переслідує мету мінімальних витрат на нього, а з іншого можливість вибору товщини підкату з існуючих в Україну ШСГП.
Сам процес прокатки на двоклітьовому реверсивному стані здійснюється наступним чином. Рулон після травлення розміщують на оправці, передній кінець задають в правлячу - тягне пристрій і далі він надходить в першу і другу кліті. Виходить з кліті передній кінець смуги захоплюється моталки, після намотування 2-3 витків встановлюється необхідний натяг і стан прискорюється до заданої швидкості прокатки. Перед закінченням прокатки смуг стан автоматично сповільнюється, реверсують і процес повторюється.
Оскільки стан і з передньою і з заднього боку обладнаний пристроями знімання рулонів з моталок і транспортерами рулонів, то на стані можна робити будь-яке число проходів.
При визначенні відносних обжатий, а, отже, і силових параметрів прокатки слід враховувати те, що безпосередньо при холодній прокатці після обтиснення смуги рекристалізації її структури не відбувається. Тобто, кожне наступне обтиснення смуги буде відбуватися при наявності збільшується наклепа металу. Саме через наклепу число обжатий на безперервних станах обмежена, воно не повинно перевищувати число клітей.
Тому дуже важливо те, що при прокатці на реверсивному стані можливо проведення проміжного відпалу, що дає можливість отримувати смугу із заданими пластичними властивостями для подальшого проходу. Тобто існує можливість зняти рулон після накопичення критичного наклепу, провести отжиг і продовжити прокатку.
Прокатка на двухклетьевим реверсивно стані, як і на будь-якому стані холодної прокатки, ведеться тільки з мастилом через наявність великих сил тертя виникають при холодній прокатці [4-9].
4. Вибір методики для розрахунку сили прокатки
Для вибору оптимальних умов по принципам техніко - економічних і якісних показників необхідно дослідження різних варіантів товщини підкату і режимів прокатки, а для цих цілей необхідно вибрати варіанти розрахунку енергосилових параметрів на ньому. Всі існуючі методики для розрахунку сили холодної прокатки базуються на рівнянні Т.Кармана.
P = pcp·b·lд,
де
Р - сила холодної прокатки;
рcp - середнє контактна нормальне напруження;
b - ширина смуги;
lд - довжина дуги захоплення;
Інженерні аналітичні (теоретичні) та емпіричні моделі середніх тисків при прокатці - ключовий інструмент як для проведення попередніх технологічних розрахунків і оптимізації процесів прокатки, так і для систем автоматичного управління процесом прокатки. В їх відносній простоті полягає вигідну відміну від складних чисельних моделей, призначених для детальних досліджень процесу, не обмежених тимчасовими рамками і можливостями ЕОМ.
Більшість вітчизняних методик по знаходженню середнього контактного тиску грунтуються на методиці А. І. Целікова. В роботі [3] був проведений порівняльний аналіз даної методики і емпіричної моделі В. М. Луговського в зв'язку з більш широким діапазоном працездатності. Порівняльний аналіз інженерних моделей середніх контактних тисків А. І. Целікова і В. М.Луговського показав перевагу використання теоретичної моделі А. І. Целікова у випадках, коли необхідно зробити вибір оптимального режиму прокатки тонких смуг з високими обтиску і низьким коефіцієнтом тертя. Показано, що в цих умовах модель ОД А. І. Целікова дозволяє врахувати істотно зростаючий вплив розтягуючих напружень у вогнищі деформації, що не враховує модель В. М. Луговського, розрахунок за якою призводить до завищених результатів.
Тому при виборі методики для визначення середніх контактних напружень була обрана методика А.В.Третьякова - Б.Є.Локшина, в основу якої покладена методика А. І. Целікова.Методиці А.В.Третьякова - Б.Є. Локшина має ряд переваг, основними з яких є визначення сили та роботи прокатки в процесі єдиного енергосилового процесу, що дозволяє точніше визначати силу прокатки, момент прокатки і ступінь наклепу металу по ходу прокатки.
Незважаючи на те, що методика А.В.Третьякова - Б.Е.Локшіна зазвичай застосовують для розрахунку сили прокатки на станах безперервної прокатки, наявність двох послідовно розташованих клітей на двоклітьовому стані робить можливим застосування методики А.В.Третьякова для даного розрахунку.
Нами вона прийнята і для реверсивного двоклітьового стану.
Наявність реверсу враховується також при розрахунку режимів прокатки на одноклітьовим реверсивному стані. Тому можна сказати, що розрахунок режиму прокатки для двоклітьового стану має спільні риси з розрахунком режимів, як на одноклітьовому стані, так і на стані безперервної прокатки [10,11]. Нижче наведено алгоритм розрахунку відповідно до методики А.В.Третьякова - Б.Е.Локшіна.
Рисунок 1. Алгоритм розрахунку сили холодної прокатки за методикою А.В.Третьякова - Б.Е.Локшіна [11].
На рис. 1 прийняті наступні позначення:
hп - товщина підкату, мм;
hK - товщин готової смуги;
b0 - ширина смуги до прокатки;
Vв - окружна швидкість валків;
σ 0 і σ1 -заднє і переднє натяг смуги;
R - радіус робочих валків;
μ - коефіцієнт тертя;
σ0,2 - межа текучості до і після деформації;
σд - середнє опір металу пластичної деформації;
ам - енергетичний еквівалент опору металу деформації за даний прохід в даній кліті;
z0, z1, q0, q1 - коефіцієнти визначаються за відповідними формулами;
єΣ0, єΣ1 - сумарні відносні обтиску до і після проходу.
5. Розрахунок режимів і сили прокатки на даному типі стану
Таблиця 1. Вихідні дані для розрахунку (Сталь 08 пс, використовувана мастило -. Емульсія)
hп,мм | hk,мм | b0,мм | Vв,м/c | σ0 МПа | σ0,2 исх.,MПа | R,мм | a1 | n1 | μ | σ1,МПа |
2,0 | 0,35 | 1250 | 4,36 | 40 | 200 | 250 | 3,46 | 0,60 | 0,13 | 60 |
Один з основних принципів вибору числа проходів на стані є принцип рівномірності завантаження клітей по проходах. Оскільки стан двоклітьовий, то можливе число проходів може бути тільки парним. Для прокатки смуги товщиною 0,35 мм з підкату 2 мм, приймаємо 6 проходів. Розрахунок сили прокатки був проведений в програмі Microsoft Excel, для кожного з проходів і відповідних їм обжатий.
Схема вікна наведена на рис 2.
Прийняте число проходів дозволить отримає смугу заданої товщини при найбільш рівномірної завантаженості клітей, що видно з розрахунків, результати яких наведені в таблиці 2.
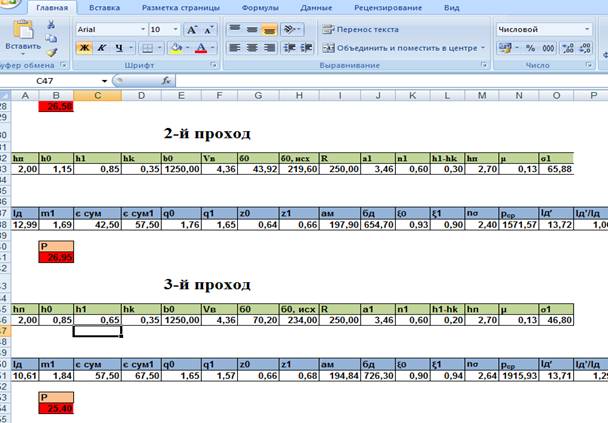
Рисунок 2. Вікно програми Microsoft Excel. Розрахунок сили прокатки в кожному з проходів.
Таблиця 2. Режим обжатий і сила прокатки на двоклітьовому стані холодної прокатки
Проход |
Товщина, мм |
Відносне обтиснення, % | Сила прокатки, МН | |
На входе | На виході | |||
1 |
2 |
1,15 |
42,5 |
26,58 |
2 |
1,15 |
0,85 |
26,1 |
26,95 |
3 |
0,85 |
0,65 |
23,5 |
25,4 |
4 |
0,65 |
0,5 |
23 |
27,71 |
5 |
0,5 |
0,4 |
20 |
25,11 |
6 |
0,4 |
0,35 |
14,2 |
14,84 |
З отриманих результатів видно, що максимальне відносне обтиснення припадає на перший прохід і становить 42,5%, сила прокатки при цьому становить 26,58 МН. Надалі відносні обтиснення зменшуються, але при цьому відбувається підвищення сили прокатки аж до 27,7 МН при обтисненні 23% у четвертій кліті. Це пов'язано із зростанням наклепу в металі і його зміцненням, що веде до збільшення сили прокатки навіть при менших обтиснення. Не дивлячись на це, найменша сила прокатки (14,8 МН) в останній кліті, так як відносне обтиснення в ній становить всього 14,2%.
6. Рекомендаціі з установки систем автоматики на стані
Установка сучасних систем автоматики на стані зможе забезпечити необхідні вимоги до аркуша, які пред'являють на світовому ринку металопрокату, підвищити вихід придатного і загальну продуктивність стану.
На двухклетьевим стані холодної прокатки можна робити дрібні партії прокату і легко змінювати сортамент і товщину металу в залежності від вимог замовника. Для виконання цих завдань стан повинен швидко переналагоджувати, інакше втрати металу через відхилення від допусків зменшать його продуктивність. У зв'язку з цим настройка стану виконується математичними моделями технологічного процесу, що встановлюють обтиснення смуги і установка заданих параметрів (положення гідронажімних пристроїв, зусилля прокатки, позиція при зміні валків, протівоізгіб робочих валків та ін) Для відповідних виконавчих механізмів [12]
Перелік посилань
- Гарбер Э.А.Производство проката. Том 1. Книга 1. Производство холоднокатаных полос и листов. - //: Теплотехник, 2007.368с
- Современный цех холодной прокатки углеродистых сталей / И.В. Франценюк, Ю.Д. Железнов, Л.А. Кузнецов, В.Г. Камышев.-М.: Металлургия, 1984.-154с.
- Особенности современного оборудования и технологии бесконечной холодной прокатки / Г. Финштерманн, Н. Моньер, С. Наппез, Г. Прадайрол // Сталь.-2004.-№1.-С.43-46.
- Ангербауэр А., Джумлия Г., Кенигсхофер М. Новое оборудование для холодной прокатки стали // Сталь.-1999.-№12.-С.48-53.
- Хекуэт Р. Новый двухклетевой реверсивный стан холодной прокатки на металлургическом заводе фирмы «Heartland Steel» // Черные металлы.-2000.-Сентябрь.-С.84-87.
- Создание и освоение двухклетевого реверсивного стана холодной прокатки / В.Ф. Рашников, Р.С. Тахаутдинов, А.И. Антипенко и др. // Сталь.-2003.-№7.-С.41-45.
- Современные концепции управления двухклетевыми реверсивными станами холодной прокатки / И.И. Бондяев, А. Дюммлер, Р. Польтер, Э. Вильке // Сталь.-2004.-№5.-С.70-72.
- Беняковский М.А., Мазур В.Л., Мелешко В.И. Производство автомобильного листа.-М.: Металлургия,1979.-256с.
- . Гусева С.С., Гуренко В.Д., Зварковский Ю.Д. Непрерывная термическая обработка автолистовой стали.-М.: Металлургия, 1979.-224с.
- Третьяков А.В., Зюзин В.И.Механические свойства металлов и сплавов при их обработке давлением, Металлургия 1973.-224с
- Теория прокатки. Справочник/ А. И. Целиков, А.Д. Томленов, В.И. Зюзин Металлургия 1952.-335с
- Бондяев И.И. Современные концепции управления ддвухклетевым реверсивным станом холодной прокатки / И.И Бондяев // «Сталь» Украины. - 204. - №5. - С. 70-71.