Contents
Introduction
1. Overview and analysis the current approach to automating the process of descaling
1.1 General information about the process of descaling
1.2 Investigation of the device and the functioning of the system descaling
1.2.1 Characteristics of the process of removing scale
1.2.2 Characteristics and design of the descaling device
1.3 Characteristics of ways to remove scale
1.4 Statement of the Problem
Conclusion
Literature
INTRODUCTION
In the current economic climate of increased competition in the market of metal deciding factor is the quality of products. One of the ways, ensuring production of quality rolled products, is the effective removal of dross from the surface of billets and finished steel during rolling.
Descaling after heat treatment and other types of heat from the surface were carried out mechanically or by etching. The most common scale is removed by etching in a mixture of acids or alkalis.
An alternative to etching are the mechanical methods of removing scale. One is the removal of scale jet of water under pressure – descaling water.
At the moment, descaling water is actively used at the enterprises of ferrous and nonferrous metallurgy. As demonstrated by long – term operation of these systems, they do not provide the necessary creation of dynamic pressure jets of water that can effectively clean sheets on the scale.
So far there is a need to develop a descaling system with customizable, automatic regulation and control as a separate water jet parameters and their relation to empirical data, the surface quality of rolled products at the outlet of the mill.
1 OVERVIEW AND ANALYSIS THE CURRENT APPROACH TO AUTOMATING THE PROCESS OF DESCALING
1.1 General information about the process of descaling
In the general case, the oxidation of the steel understand the interaction of gases (air, combustion products or controlled atmosphere) with iron, accompanied by the formation of oxide layer (scale) on the metal surface. With respect to heat of steel in the fiery furnace before treating pressure main oxidizing gases are: carbon dioxide (CO2), oxygen (O2), water vapor (H2O), sulfur dioxide (SO2). The oxidation of iron - exothermic and occur as follows:
Fe + 0,5 O2 = FeO,
3FeO + 0,5 O2 = Fe304,
2Fe304 + 0,5 O2 = 3Fe203,
Fe + C02 = FeO + CO,
Fe + H20 = FeO + H2,
3FeO + C02 = Fe304 + CO,
3FeO + H20 = Fe304 + H2.
In the process of oxidation of the iron layer thickness of 1 mm thick layer of scale formed up to 2.8 mm.
Oxidation (scale) has a negative impact not only on the quality of metal, but also on the work of heating furnaces and rolling equipment.
Subject to a rational technology of heating furnace slag from the metal surface is almost completely removed when transporting continuously cast billets from the furnace to the rolling mill, deformation and manipulation at the first peal passages in the roughing stand rolls. A radical way to remove scale from metal surfaces is the use descaling systems. Using descaling, water is supplied to the surface of the steel through special nozzles at pressures up to 80 – 140 atmospheres. Following the issuance of the heating furnace of the metal coated slag, an abrupt cooling of the surface, resulting in a layer of scale is covered with a grid of cracks. The impact of a jet of water supplied under high pressure leads to a cinder block anchors and their detachment from the metal surface. At the same time, descaling water contributes to a more intensive cooling of the metal during rolling, its use is not recommended in cases of low plasticity of the steel [1].
1.2 Investigation of the device and the functioning of the system descaling
1.2.1 Characteristics of the process of removing scale
For descaling the surface of the rolled metal is subjected to shock against powerful jets of water directed to it accordingly. Figure 1.1 shows the mechanisms of cracking the layer of scale under the influence of the kinetic energy of water jets.
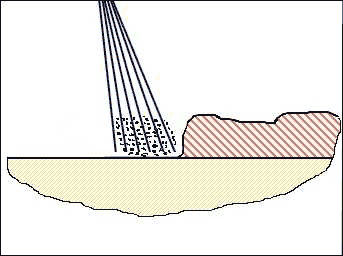
Figure 1.1 – Hydromechanical descaling
(Animation; frames – 4, the delay between shots – 0.5 seconds, the number of cycles of repetition – 6, the volume – 36,6 kb)
Water cooling is uneven shrinkage of the steel and oxides. As seen in Figure 1.1, the contact pressure of the jet is cracking of the layer of scale. The splitting is due to the scale of the explosive expansion of the water droplets that travel under her coat.
Separated slag is removed from the surface of the water jets are directed at an angle through the nozzle.
The main parameter characterizing the unit for removal of scale is created by shock (measured in N/mm2), which is defined as the force developed by a jet of water to the area to which it applies. Shock depends on the following parameters:
1) The type of spray nozzles;
2) The angle of the jets of water supply;
3) The flow of water;
4) The pressure at which water is pumped to the surface of steel;
5) The height of splash.
Pressure spray nozzle size, angle of incidence of the jets and the water flow is linear with a shock load, height spray is a parameter related to the shock load of the exponential dependence.
If you change the height of spray (regardless of the angle of the jets) change just two geometric parameters of the process descaling – the width and depth of exposure to water. Therefore, the height of the spray is the most effective parameter adjustment. By reducing the distance between the nozzle and the surface of the metal in half, you can increase the impact load is about four times.
This means that in terms of saving the distance between the nozzle and the metal should be minimal, although in practical use should take into account such factors as heat loss, speed metal, and variations of its shape and size (footprint) [2] .
The initial data for the design of hydraulic descaling devices are: the fluid pressure p, velocity of the rental v; width of the surface treated steel B $, type of nozzles used for nozzle flow and characterized by the disclosure of Vc and angles α, β; the average specific energy e with descaling surface of the steel subjected to treatment. In the design of hydraulic descaling devices primarily determined by the following parameters: the number n and the step of installing A nozzles, nozzle installation height H above the surface of the processed products. The energy of jets per unit of treated surface, e, is determined by the expression:
e = F * V / (B2 * T * v * cosθ). (1)
where F – force produced by a jet of fluid on the treated surface;
V – volumetric flow rate;
B – width of the contact area of the jet on the workpiece;
T – the depth of the contact area of the jet on the workpiece;
v – velocity of the rental;
θ – angle of rotation of the nozzle injector relative to the longitudinal axis of the section.
As shown in [7], the most rational approach for determining the basic parameters of the reservoir for the hydraulic removal of scale is an approach based on providing the necessary energy of the jets of fluid for removing scale, which is specific for each grade of steel [7]. So for the specific energy of carbon steel removal of scale is 17 kJ/m2 for alloyed steel – 42 kJ/m2. The authors of [7] proved that there is no need to expend more energy is produced by jets of fluid than is required for a particular grade of steel and the type of scale.
The specific energy is inversely proportional to the distance. Then, when permanently installed reservoir required an increase in energy can compensate for the higher pressure. Another is that the required amount of energy can be achieved by changing the distance. It is necessary to change the nozzle setting step and the collector. When assigning step installation nozzles should provide overlapping plumes jets of water to prevent rolling on the treated surface bands with unremoved dross [8].
e = F * V * cos3γ / (8 * H3 * v * tg (α / 2) * tg (β / 2) * cosθ). (2)
It should be noted that the force produced by a jet of fluid on the treated surface depends on the pressure and volumetric flow rate, nozzle height setting, the geometric parameters of the nozzle, ie, F = f (p, V, H, α, β). Then, as seen from (2), the specific energy descaling produced by a jet of fluid is determined by the pressure and volumetric flow rate of fluid speed steel, installation height and angle of nozzles on the surface of the steel, as well as opening angle of the jet fluid.
Upon cooling, the resulting scale in her state of stress grinds scale and flow coolant washes away from the surface of a sliding tackle. The state of stress depends on the velocity scale of the process of cooling and heat transfer coefficient. A higher value of the coefficient of heat transfer between the dross contributes to the creation and the base metal of high stress, which favorably affects the process of cleaning the metal on the scale [5,6].
1.2.2 Characteristics and design of the descaling device
Department of MOZCHM Donetsk National Technical University developed the device for descaling jet of fluid pressure.
This device comprises a body placed in it with the holder of a nozzle, hoist and turn the nozzles, the invention further comprises a linear motion mechanism nozzles made in the form of the drive shaft of a sectional, with at least five sections, fixed in the housing so that its longitudinal axis located in the same plane with the longitudinal axis of the holder [9].
1.3 Characteristics of ways to remove scale
Department of MOZCHM Donetsk National Technical University have developed a method for removing scale rolling mill sheets.
Since the form, structure and location of the scale formed on the heterogeneous surface of workpiece, the configuration parameters of the liquid jet on the statistical average values of the characteristics of scale leads to the appearance on the surface of the product areas of unremoved scale and purified from the dross, but the supercooled regions. The presence of sites with unremoved slag due to the fact that to remove more durable scale requires removal of the specific energy, whose value is greater than the average, and the presence of supercooled regions due to the fact that the removal of less resistant scale requires removal of the specific energy, whose value is less than the average.
Figure 1.2 shows a diagram of a system that implements the method of removing scale from the leaf surface.
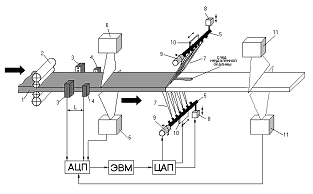
Figure 1.2 – Structure of descaling
As can be seen from Figure 1.2, the system control parameters of the jet, depending on the input data. Sheet (1) when leaving the finishing stand (2) fixed sensors (3,4). Based on data from the scanner (6) establishes the specific energy descaling produced by jets of liquid (7). Also based on data from the scanner is installed height of the jet, due to mechanisms (8) reciprocating vertical collectors, the angle of attack, due to mechanisms (9) the slope of the nozzles, and the position of the nozzles (5), by mechanisms (10) back -and-forth movement of the nozzles horizontally. With the help of the scanner (11) is monitoring the quality of clean sheets on the scale.
This method has impressive advantages in comparison with analogues. First of all, the presence of the scanner allows you to adjust the parameters of the jet in real time. This innovation reduces the operator to monitor the process, eliminating the need to manually configure knocking. However, this method does not consider the analysis of input data and their interpretation of the ADC, so there is a need for refinement of the system.
From the foregoing it can be concluded that this method does not allow for complete removal of scale from the leaf surface, so currently it is advisable to create a descaling system with adjustable pressure nozzle to improve the quality of products.
1.4 Statement of the Problem
Analysis of existing methods and systems for descaling showed that these systems do not provide adequate removal of scale. It is therefore advisable to conduct further research in this area.
The purpose of this system is to reduce production costs by minimizing the consumption of water and electricity, competitiveness and grade rolling by addressing the problem of automating the descaling process, in particular regulation of pressure on the nozzles.
The goal is achieved the following tasks:
a) Development of models and algorithms for automated hydraulic removal of scale;
b) Development of the structure of the system;
c) Selection of software and technical support;
d) Software development.
CONCLUSION
In the production of sheets of carbon, low alloyed and alloyed steel, rolling mills, slab formed on the surfaces of scale, which is the reason for the decline of product quality and reduce the resistance of the working rolls. Poorly cleaned furnace and mill scale, rolled into the thickness of the metal definitely become a cause of marriage and the criticism for steel plant, and vice versa, high-quality refined metal surface is the basis for high-quality product.
In this connection it is becoming urgent task of cleaning the surface of the rental scale.
Currently, there are many ways to remove scale from steel surfaces, but the most common, environmentally friendly and cost – effective scale removal is a stream of water under pressure – descaling water. To date, there is no method of descaling parameters calculating allowing him to choose the optimal uniquely hydromechanical parameters.
Analysis of existing methods and systems for descaling showed that these systems do not provide adequate removal of scale. Therefore, at present it is advisable to create a descaling system with the ability to configuration management and automated control of a single water jet parameters and their relation.
The result of analysis of existing systems of hydrodynamic descaling is the problem and formulation of the goal of creating an automated descaling system.
LITERATURE
1. Павлов В.В. Дефекты и качество
рельсовой стали: Справ. изд./ Павлов В.В., Темлянцев М.В., Корнева Л.В.
– М.: Теплотехник, 2006 – 218 с.
2. Современные способы удаления окалины // Металлургическое производство и технология №1 – М, 2008 – С 42-55 (Доступ к публикации: http://www.schaefer-urbach.de/downloads/pdf/08-09-28-MPT_Russland_SU_Entzunderung.pdf)
3. Михеев В.А. Гидросбив окалины в прокатных
цехах. / Михеев В.А., Павлов А.М. – М.: Металлургия, 1964. – 107 с.
4. Беккер Э.Г. Оптимизация сопел для гидросбива окалины на
широкополосном стане горячей прокатки / Беккер Э.Г., Биркемайер Г.,
Бюхеле В. И. // Металлургический завод и технология, 2000. –
С.74 –78.
5. Патент РФ № 2247616. Способ удаления окалины с поверхности
изделия. В 21 В 45/08 / Руденко Р.В., Руденко В.И., Ошовская Е.В.,
Суков Г.С., Черносвитов А.В. Опубл. 10.03.2005 Бюл. №7.
6. Руденко В.И., Определение основных параметров устройств для
гидравлического удаления окалины/ Руденко В.И., Суков Г.С., Руденко
Р.В., Ошовская Е.В., Антыкуз О.В. // Металлургическая и горнорудная
промышлен–ность. – 2004. – №4. – С. 28 – 30.
7. N.J. Silk. The impact energy primary descaling / N.J. Silk.
// Steel Times. – 1999. – №5. – P.184 – 185.
8. Суков Г.C. Теоретические основы проектирования устройств
для гидравлического удаления окалины/ Суков Г.C., Руденко В.И.,
Ошовская Е.В., Антыкуз О.В, Руденко Р.В. // Металлургические процессы и
оборудование. – 2005. – №1. – С. 35 – 39.
9. Патент РФ № 2247617. Устройство для подачи жидкости на
поверхность проката. В 21 В 45/08 / Руденко Р.В., Руденко В.И.,
Ошовская Е.В., Суков Г.С., Черносвитов А.В., Антыкуз О.В. Опубл.
10.03.2005 Бюл. №7.
10. Чекулаев Е.Ф. Промышленные исследования энергетических
параметров низконапорной машины гидросбива вторичной окалины. /
Чекулаев Е.Ф. Денщик Р.В. // Восточно-Европейский журнал передовых
технологий 2/2(14) – Харьков, 2005 |