Abstract
Сontent
- Introduction
- 1. Analysis of the BOF production on foreign and domestic enterprises
- 2. Modern problem of BOF steel production
- 2.1. Deficiency scrap
- 3. Waste converter production
- 3.1 BOF gas
- 3.1.1. The methods and schemes of gas cooling
- 3.2. Cleaning of converter gas
- 3.3. Use of converter gas
- 4. BOF slag process
- 5. Dust and slimes of converter production
- 5.1. Disposal of converter dust and sludge
- Conclusions
- References
Introduction
Relevance of the topic
Modern oxygen-converter process, widely spread in the world due to technological capabilities, is now the leading steel-making process. And in recent years, numerous reports, despite the crisis in the global steel industry, the share of converter steel stabilized and maintained at 70-75% of the total volume of melted metal.
In Ukraine, the share of converter steel production has grown steadily and in 2010 accounted for 52% of total steel production.
The present level of development of the BOF steelmaking process, confirms its advantages: high performance, low specific capital investments and the costs of redistribution, multi-variant technology and raw materials, the ability to produce high quality steel of a wide assortment of cast iron with different chemical composition. However, to achieve the improvement of environmental safety of the production of steel, should be optimized BOF process by developing a rational measures for its improvement. This optimization should positively affect the state of the environment.
The presence of coke and ore reserves, extensive development of blast furnace production confirms that the converter redistribution in Ukraine has good prospects for development.
But despite the presence of the prerequisites for the development of the steel-making process, the practice of the present day shows that the scrap, which is used in the smelting of converter as the coolant supplied to steel plants, does not meet its requirements on the content of elements such as Cr, Cu, etc., as well as physical properties. There is a sharp decline in the share of scrap recycling, which as a result of repeated melting and new methods of metal increases the content of various impurities that reduce the operational properties of the steel. Their removal by melting and further processing extremely difficult or almost impossible. Poor performance on the physical properties associated with the organization of the collection and the quality of scrap metal in general. One of the factors influencing the decline in the share of working-quality scrap is the increase in the share of continuous casting of steel on steel mills.
Thus, methods to improve the environmental safety of converter production and the problem of shortage of steel scrap to date are relevant.
Purpose and Objectives
The objective is to develop activities and to increase the environmental safety of BOF steel production, as well as addressing the shortage of steel scrap.
To achieve this goal it is necessary to solve the following problems:
- To analyze the technology and material balance converter smelting;
- Calculate the heat balance of the melting, to determine the influence of physical and chemical parameters of the charge materials on the performance of the process;
- Identify alternative options for replacing the steel scrap and choose rational cooler converter smelting;
- Analyze the impact of the mass of the additive used during purging and doduvok output of liquid steel and the formation of emissions;
- To analyze the efficiency of removal, cleaning and converter gas from reliance dusts, sludges and wastes;
- To make ecological and economic assessment designed activities.
Research object — the technology of production of steel in oxygen converters.
Research subject — Raw material and Telov mode converter smelting, identification and selection of a rational cooling additive for the process, the process gas cleaning methods, methods of waste production.
Methods of research — analytical analysis of the literature on the issue of environmental impact oxygen converter steelmaking process.
Scientific innovation — choice of alternative refrigerants converter melting scrap, justification dry-cleaning of converter gas and selection of the most rational way of disposing of waste.
1. Analysis of oxygen and converter production at the foreign and domestic enterprises
Improving technology converter process is the most urgent task of the modern steel industry. Due to the fact that 70% of world steel produced by this method, there is an urgent need for cost optimization for it. For domestic enterprises is particularly important, because they are in the process of reforming and restructuring of its technology.
In the last decade, both abroad and in Ukraine for the development of the converter process underway in the following areas:
- The improvement of the design of units and technological options purge;
- Production engineering steels with low content of impurities and ballast, "clean" and "especially pure" steel;
- Increasing the productivity of converters while addressing environmental challenges;
- Improving gaoochistki and ways to use converter gas;
- Increase in the durability refractory lining;
- Reduction education and waste production.
In general, the modernization of converter production achieves the traditional objectives: improving product quality, reducing production costs, increasing productivity, improving the environment. Its integral elements of modern technology are:
- Connect the top oxygen blowing with bottom blowing inert gases (~ 80% of the world's 660 converters) to improve the process and results of the purge process before the release of fusion;
- Cutting off the slag, most of all - to reduce the gas-dynamic falling slag from the converter to the ladle during tapping;
- Automation of the process using the auxiliary sublance and off-gas analysis to determine the exact moment Povalko converter and tapping without final blow and, in some cases, without waiting Analysis ("direct release");
- The system of preventing emissions to increase the yield of usable, improved process control and personnel safety.
2. Modern problem of oxygen and converter production of steel
2.1 Deficiency of scrap metal
The problem of shortage of scrap steel is by far the actual. Under these circumstances, it can be solved if the improvement of the traditional and the technological mode of formation of metal stock - stages predetermine the course and the results of the converter process. The search for alternative materials based on original material with high physical characteristics instead of scrap is important. The class of these materials to optimize heat balance melting coolers are such as: solid cast iron, iron ore, iron ore pellets and metalized DRI, HBI, etc.Iron ore is cooler, is relatively rare. When using ore waste heat consumed for its heating and reduction of iron oxide. Reduced iron somewhat increases the yield of steel. The cooling effect of ore in the 3.0-3.8 times higher than the cooling effect of an equal number of scrap and flow of the ore reaches 8%.
Compared with crowbar ore as cooler has several advantages:- It provides a high podfurmennoy cooling zone;- To load the ore does not need to stop the purge;- Contained in the ore accelerate the dissolution of iron oxides in the slag lime, and thereby accelerate the slag;- The presence of oxygen reduces the ore (10-15%) the rate of oxygen gas.
However, along with the benefits, there are several disadvantages primeneiya ore. It brings a lot of slag SiO2, and therefore increased consumption of lime and amount of slag which usually causes a reduction in weight yield. Furthermore, when a large flow ore smelting (> 5-6%) and its introduction in one portion increases the amount of emissions and reduces the yield of the metal.
Use as sinter and pellets cooler has the same cooling effect as iron ore.
When used as a cooling heat limestone and dolomite consumed by decomposition contained therein, CaCO3 and MgCO3. The cooling capacity of dolomite and limestone are close to the cooling capacity of the ore. Rare use of the cooler is connected with the fact that they do not increase the yield of the metal.
In accordance with the fact that all of the above alternative refrigerants have several disadvantages, an interest in the sintered raw material in the cooler as possible BOF process.
3. Waste of converter production
3.1. Converter gases
During the converter smelting converter gas is formed. Yield and composition of the gas depends on the properties of the charge, and intensity of flushing mode, lance design, process type and other factors. The exhaust gas from the converter is mainly composed of CO and contains significant amounts drink. Yield and composition throughout its melting varies considerably. In practice, the converter is used in production and post-combustion gas cleaning with no post-combustion CO. As a secondary fuel energy converter gas is used in the disqualification of the gas without burning. In this case, it is a very valuable fuel and energy technology. . In most cases it is advisable to use not only the sensible heat exhaust gas, but also to utilize it as a chemical feedstock or fuel. To dispose converter gas as process, it is withdrawn, purified and ohladayut mainly in electrostatic precipitators.
3.1.1. The methods and schemes of gas cooling
The gas temperature before gas treatment should not exceed 200-300 °C. Since the gas temperature at the outlet of the converter to average 1600 °C before gas treatment should be cooled. Layout drawing of the converter with basic equipment coolers and gas purification is shown in Figure 1.
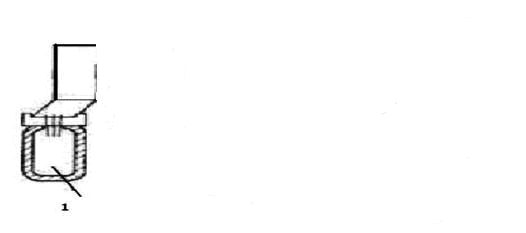
1 - converter; 2 - cooler of gases; 3 - gas purification; 4 – gas-holder
(Animation: 5 shots, 5 cycles of repetition, 140 KB)
Figure 1 – The scheme of a gas path behind the converter
3.2. Cleaning of converter gas
Gas cleaning system to ensure the reduction of dust, regardless of how removal and cooling of converter gases emitted into the atmosphere. Currently, in the world there is a great variety of systems and designs of gas cleaning devices. All of them can be grouped into three broad groups of methods for cleaning: dry, wet and electrocleaning.In some BOF shops oxygen gas cleaning are still wet dedusting systems. First, from the gas stream is removed in the rough dust with irrigation water coolers. The second cleaning step removes fine dust scrubber conical annular gap. These scrubbers are easy to design, cleaning efficiency - 30 mg/m3, low power consumption and low capital costs. If necessary, also used with venturi scrubbers rectangular orifice.
Comparing wet and dry scrubbing, it should be noted that the investment costs on the wet cleaning is only about 70% of the capital cost of the dry cleaning. However, in the wet scrubbing system to achieve a high dust removal efficiency must maintain a high pressure drop, which leads to more robust exhausters and higher power consumption. Furthermore, in systems scrubbing slurry is formed, which requires dehydration, drying, or disposal. Dry systems can do without the installation dewatering sludge and purification. Dust dry type of systems can briquetting and use in the steelmaking process. These characteristics are typical for dry cleaning systems significantly reduce operational costs. In addition, higher cleaning efficiency can fully meet the requirements of international law relating to polluting emissions converters, including more stringent requirements, which can be expected in the future. Therefore, the dry cleaning system with waste gas are usually more cost effective than scrubbing systems.
3.3. Use of converter gases
At removal of converter gas without reburning after cooling and cleaning it can be used for the following purposes: as fuel, chemical raw materials, for heating of shikhtovy materials of converter melting, and also as a reducer of iron ore raw materials.
Application of converter gas as fuel is one of reserves of economy of fuel and energy resources. However, its application is complicated, in communication for the following reasons: inconstancy of an exit of converter gas both on time, and by quantity; sharp fluctuations of composition of gas during the different periods of melting; possibility of a suction to the gas outlet highway of air that can lead to formation of a gas-oxygen mix and explosion at consuming units. To compensation of an uneven exit and averaging of composition of gas apply gas-holders.
The possibility of application of converter gas recovery of iron ore due to its high reduction potential. This is a prerequisite to the development of an effective scheme of gas use, including receipt of metallized product and then apply it to the converter process.Figure 2 is a schematic diagram Frequency converter gas as a reductant. Due to the negative pressure created by the supercharger converter gas is taken from the flue gas lasers at 950-1050 °C and is directed through the bypass duct in the recovery unit. Then it passes through the bed of iron ore pellets heats them up to 750-850 °C and recovers to a degree of metallization of 95%. The exhaust gas at 550-650 °C and containing about 35% CO enters the gas purification disposed in the bypass duct for reducing apparatus in droplet separator and then supplied to the supercharged spark. Remaining after the reduction of iron oxides CO, afterburned on the candle.
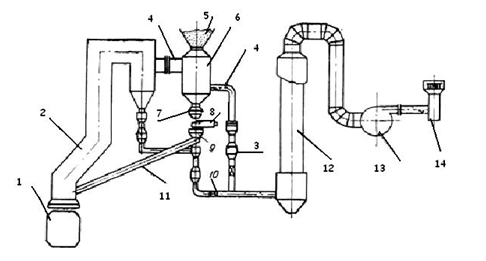
1 - Converter 2 - lasers, 3 - gas cleaning, 4 - bypass duct 5 - bunker, 6 - recovery unit, 7 - storage bin, 8 - Feeder, 9 - dispenser, 10 - gate 11 - estrus, 12 - demister, 13 - blower, 14 - candle.
Figure 2 – Schematic diagram Frequency converter gas as reducing
4. Slags of technological process
Slag - one of the most important physical and chemical processes in the converter redistribution, as it provides a quality finished steel. Basically it identifies dephosphorization, desulfurization and other reactions. Depending on the progress of slag formation and the results vary the degree of assimilation fluxes and liner wear, metal loss and emissions offsets. The main sources of slag converters are products of oxidation of the elements contained in the metal (iron, silicon, manganese, phosphorus, chromium, vanadium, etc.), oxides and salts are included in the additives introduced into the converter (basic processes, mainly - lime, iron ore, fluorite, etc,). The other oxides fall into the domain converter (mixing) slag and destroy the lining (walls and bottom). In the basic converter process for active primary converter slag during purging serves lime, fluorspar. When this melt blowing is stopped.
1) Primary processing
Slag coming recycled in liquid form in the ladle or in a mixture of solid and liquid wastes. Molten slag is drained into the trench Ros type where it is cooled with water. Intensive cooling water leads to an increase in stress, micro-cracking and thermal destruction of the slag monolith. The rate of cooling of the slag at termodroblenii increases of 30-60, the yield of fines increased by 2-3 times, and the extraction of metal from slag - 1.5 times. The rest of the slag develop excavator. Frozen bucket residues discharged in this case a separate trench, equipped with magnetic bucket crane. During the processing of mixtures of liquid and solid wastes, they are unloaded in a separate trench (similar), water-cooled, crushed drop weight and have extracted a magnetic metal plate. With this technology, process termodrobleni is weaker and increases the content of the slag lumps.
2) Recycling
Resulting in the trenches of primary processing of slag delivered for recycling in the waste Sorting Office (DSO). Crushing of the slag is carried out on the jaw, sometimes hammer mills. Sieving - on screens. Transportation - a conveyor belt. Before and after each crushing stage selection is made of metal suspended magnetic separators and electromagnetic pulleys. DSO can be open or closed.
5. Dust and slimes of converter production
BOF off-gas endure a lot of dust. Together with carbon monoxide converter is interested in a large amount of metal vapor and droplets emitted from the bath during decarburization. A pair of particles consist mainly of FeO, Fe2C, FeSO3. Depending on the composition of raw materials, the design of furnaces and smelting conditions per tonne of steel produced 12-25 kg. fine dust "dry" and sludge in "wet" method of trapping a particle size from 0.1 to 10 microns.
5.1. Disposal of converter dust and sludge
BOF dust and sludge production after preconditioning is used as an additive in the sinter mix. BOF sludge is an intensifier agloprotsessa has a positive impact not only on the pelletizing process, because of their dispersion, but also the dynamics of the melting of the charge during sintering. This is due to the presence of sludge in a large amount of CaO, MgO and MnO.
Function BOF sludge in admixture with domain slurry as an additive in agloshihtu. Use of a mixture slurry in an amount up to 6% significantly increases the sintering machine, and a greater effect than the additive slurry and one domain less effect using BOF sludge. Using such a mixture slightly reduces performance but improves the sintering agloshihty. This is explained by the increase in the rate of air filtration and increased shrinkage rate. Quality agglomerate its mechanical strength after the drum is also dependent on the flow rate of carbon slurry while adding virtually no change. Some deterioration of mechanical strength of the agglomerate slurry at 5.2% in the mixture due to excess heat during sintering. Performance is enhanced both by increasing the output of sinter, so because of the increase in the rate of sintering. The qualitative characteristics of the agglomerate strength is also markedly improved.
The most common overseas scheme of dehydration include thickening of the pulp slurry in the radial thickeners, filtration in vacuum filters and tumble drying. However, these schemes differ in increased costs for drying sludge in the capital-energy-intensive drying drums. Furthermore, sludge after drying losing its hydrophilic property particularly valuable in agglomeration.
On the Dnieper Metallurgical Plant them. Dzerzhinsky simultaneously with the launch of the oxygen-converter plant was put into operation the first phase of the complex preparation of dusts and sludges of production technology developed Donetsk National Technical University. One of the main tasks of the complex was a rational preparation for the disposal of waste iron agloproizvodstve all the oxygen-converter shop: sludge, lime dust, dust aspiration systems, screenings of lime and limestone, as well as granulated BOF slag. The nation's first on the complex preparation of the waste was a new technology joint preparation of dry lime dust lime-kiln area and wet BOF sludge.
Shlamoizvestkovaya mixture is an intensifier of the sintering process. At the optimum of their training and the introduction of the iron ore sinter mix of improved almost all the indicators agloprotsessa. Significantly higher productivity (up to 10% at a flow rate of 10-30 kg of mixture / t sinter) the yield increases in an average of 2% for each 10 kg of the mixture. Also improves the quality of sinter after the tests in a standard drum.
Conclusions
The role of scrap metal as the main material of the cooling predetermined not only its technological characteristics as feed material, but also the fact that scrap is a waste. Scrap generated in businesses and organizations of all industries in the production and processing of metals, and also due to the replacement of equipment as the moral and physical deterioration. To date, the issues of the needs of steelmaking metal stock are of particular importance and concern not only Ukrainian, Russian, but metallurgists industrialized countries (USA, Germany, Japan, etc.). First of all, they are associated with the share of "clean" scrap steel, its quantitative deficiency and progressive deterioration of the quality characteristics.
Therefore, studies on the replacement of metal smelting other coolers are relevant. For example, the use of HBI, is one of the solutions to the shortage of steel scrap.
Thus, the introduction of the proposed measures will improve the environmental safety of the converter output, as well as the rational use of secondary material resources may gain some economic benefit.
Since interest is the BOF slag, which occupy vast areas of land if they do not recycle. The main uses of steel slag - road construction, asphalt and concrete fillers, in agriculture for soil deoxidation, and as a ferrous material for secondary smelting in blast furnaces. The effect of introducing the blast furnace charge current converter slag production of 50 kg / m is achieved by replacing the raw limestone CaO slag that reduces coke consumption of 3.2 kg / t and increases productivity furnaces domennіh 0.55%. The same happens with the introduction of slag agloshihtu with increasing basicity of sinter.
Do not go unheeded iron dust and sludge from gas cleaning systems, which are mainly used as raw material for further processing into metallurgical aggregates in the form of condensed, dehydrated and dried in a semi batch sintering.
Using the converter gas after cooling and cleaning as fuel for heating the charge materials converter production, as a reducing agent of iron ore for blast furnaces to generate electricity and steam will save fuel and energy resources and primary natural resources.
References
- Близнюков, А. С. Инновационные решения в области очистки и утилизации отходящих газов в сталеплавильном производстве // Новости черной металлургии за рубежом.- 2010 - №5. – с. 77-80.
- Розенгарт, Ю.И., Якобсон Б.И., Мурадова З.А. Вторичные энергетические ресурсы черной металлургии и их использование.-К.: Выща школа, 1988.
- Панфилов, М. И., Школьник Я. Ш. и др. Переработка шлаков и безотходная технология в металлургии. - М.: Металлургия, 1987. – 238с.
- Бачинин, А. А., Мищенко И. М., Ткалич К. Н., Гелюх Л. Л. Эффективность использования конверторного шлака в аглодоменном производстве // Сталь. – 2004 - №2. – С. 7-10.
- Бережинский А.И., Циммерман А.Ф. Охлаждение и очистка газов кислородных конвертеров. - М.: Металлургия, 1975.
- В.Г. Воскобойников, В.А. Кудрин, А.М. Якушев и др. Общая металлургия: Учебник для вузов. - М.: Металлургия, 2005. – 765с.
- Старк С.Б. Газоочистные аппараты и установки в металлургическом производстве. – М.: Металлургия, 1990. – 400 с.
- Юдашкин М.Я. Пылеулавливание и очистка газов в черной металлургии. – М.: Металлургия, 1984. – 320 с.
- Толочко А.И., Филлипов В.И., Филипьев О.В. Очистка технологических газов в черной металлургии. – М.: Металлургия, 1982. – 277с.
- Казюта В. И., Казюта М. В., Сосонкин А. С. Технология комплексной переработки металлургических шламов и пыли газоочистки // Сталь. – 2010.- №2.- с. 85-87.