Реферат за темою випускної роботи
Зміст
- Вступ
- 1. Аналіз киснево-конвертерного виробництва на зарубіжних і вітчизняних підприємствах
- 2. Сучасна проблема киснево-конвертерного виробництва сталі
- 2.1 Дефіцит металобрухту
- 3. Відходи конвертерного виробництва
- 3.1 Конвертерні гази
- 3.1.1 Способи та схеми охолодження газів
- 3.2 Очищення конвертерних газів
- 3.3 Використання конвертерних газів
- 4. Шлаки конвертерного процесу
- 5. Пил і шлами конвертерного виробництва
- 5.1. Способи утилізації конвертерного пилу і шламів
- Висновки
- Перелік посилань
Вступ
Актуальність теми
Сучасний киснево-конвертерний процес, що отримав широке поширення у світі завдяки технологічним можливостям, є нині провідним сталеплавильним процесом. Причому останніми роками за численними відомостями, незважаючи на кризові явища у світовій металургії, доля конвертерної сталі стабілізувалася і зберігається на рівні 70-75 % загального об'єму металу, що виплавляється.
В Україні доля виробництва конвертерної сталі постійно збільшується і в 2010 році склала 52 % загальної виплавки сталі.
Сучасний рівень розвитку киснево-конвертерного способу виробництва сталі, підтверджує його переваги: високу продуктивність, низькі питомі капітальні вкладення і витрати по переділу, багатоваріантність технології і сировинної бази, можливість виробництва високоякісної сталі широкого сортаменту з чавуну різного хімічного складу. В той же час для досягнення підвищення екологічної безпеки цього виробництва сталі, потрібна оптимізація киснево-конвертерного процесу, шляхом розробки раціональних заходів по її підвищенню [1]. Така оптимізація повинна благотворно вплинути на стан навколишнього природного середовища.
Наявність запасів руди і коксу, широкий розвиток доменного виробництва підтверджує, що конвертерний переділ в Україні має хороші перспективи для розвитку.
Але, незважаючи на наявність передумов для розвитку цього сталеплавильного процесу, практика сьогоднішнього дня показує, що брухт, який використовується в конвертерній плавці в якості охолоджувача, поставляється на металургійні підприємства, не відповідає вимогам, що пред'являються до нього, за змістом таких елементів як Сr, Сu, і тому подібне, а також фізичним властивостям [3]. Спостерігається різке скорочення долі оборотного брухту, в якому внаслідок багатократної переплавки і нових методів обробки металу підвищується зміст різних домішок, сприяючих зниженню експлуатаційних властивостей сталі. Їх видалення при виплавці і подальшій обробці надзвичайно ускладнене або практично неможливе. Незадовільні показники за фізичними властивостями пов'язані з організацією збору і якості підготовки металобрухту в цібрухту. Одним із чинників,який впливає на зниження долі якісного оборотного брухту є зростання долі безперервного розливання сталі на металургійних підприємствах.
Таким чином, способи підвищення екологічної безпеки конвертерного виробництва і проблема дефіциту сталевого брухту на сьогодні є актуальними.
Мета і завдання
Метою роботи є розробка заходів і підвищення рівня екологічної безпеки киснево-конвертерного виробництва сталі, а так само вирішення проблеми дефіциту металургійного брухту.
Для досягнення вказаної мети необхідно вирішити такі завдання [6]:
- проаналізувати технологію і матеріальний баланс конвертерної плавки;
- розрахувати тепловий баланс плавки, визначити вплив фізичних і хімічних показників шихтових матеріалів на показники процесу;
- визначити альтернативні варіанти заміни металургійного брухту і вибрати раціональні види охолоджувачів конвертерної плавки;
- проаналізувати вплив маси використовуваної домішки по ходу продування і додувок на вихід рідкої сталі і утворення викидів;
- проаналізувати ефективність відведення, очищення конвертерного газу і використування пилу, шламів і шлаків;
- зробити еколого-економічну оцінку розроблених заходів.
Об'єкт дослідження — технологія виробництва сталі в кисневих конвертерах.
Предмет дослідження — шихтовий і теловий режими конвертерної плавки, визначення і вибір раціональної охолоджувальної домішки для процесу, способи очищення технологічного газу, методи використання відходів виробництва.
Методи дослідження — аналітичний аналіз літературних джерел з проблеми дії на довкілля кисневих конвертерних процесів виробництва сталі.
Наукова новизна — вибір альтернативних охолоджувачів металобрухту конвертерної плавки, обгрунтування сухого способу очищення конвертерного газу і вибір найбільш раціонального способу утилізації відходів.
1. Аналіз киснево-конвертерного виробництва на зарубіжних і вітчизняних підприємствах
Вдосконалення технології конвертерного процесу є найбільш актуальним завданням сучасної чорної металургії. Внаслідок того, що 70% сталі у світі виробляється цим способом, існує гостра потреба оптимізації витрат для нього. Для вітчизняних підприємств це особливо важливо, тому як вони знаходяться на стадії реформування і реорганізації своїх технологій.
Нині в Україні шість конвертерних цехів(металургійні комбінати «Арселор Мітал Кривий Ріг», Маріупольські «Азовсталь» і ім. Ілліча, Дніпровський ім. Дзержинського, а також Дніпропетровський і Єнакіївський металургійні заводи), що мають у своєму складі 16 кисневих конвертерів і один конвертер для газокисневого рафінування сталі(завод «Дніпроспецсталь»). Примітне те, що у більшості з них розливання сталі здійснюється на МНЛЗ(виключення – «Арселор Мітал Кривий Ріг» і Дніпропетровський металургійний завод).
У світі експлуатується близько 280 киснево-конвертерних цехів, що мають у своєму складі до 700 конвертерів, 65,5т сумарного світового об'єму металу(811 млн. т в 2006 році), що виробляють. При цьому, тільки 18 цехів у світі мають у своєму складі надвеликі конвертери місткістю 290 - 300 т і більше. Чотири з них знаходяться в Росії(Череповецький, Магнітогорський, Новолипецький і Західносибірський меткомбінати), чотири - в Японії(JFE Steel, заводи Mizushima і Keihin; Nippon Steel, заводи Yawata і Kimitsu), два - в Німеччині(TKS Thyssen Krupp Stahl і Arcelor Mittal, завод Stahlwerke Bremen), по одному - в Україні(«Азовсталь» і Алчевский меткомбінат), США(Weirton Steel), Південній Кореї(Posco), Польщі(Arcelor Mittal, завод Huta Katowice), Великобританії(Corus/Tata Steel, завод Scunthorpe), Франції(Arcelor, Fos sur Mer), Індії(компанія SAIL, завод Bokaro) і Нідерландах(Corus/Tata Steel, завод Hoogovens Ijmuiden BV). При цьому, як показує практика, конвертерний цех у складі трьох 400 тонних конвертерів може забезпечити річний обсяг виробництва на рівні 10 млн. т [7].
У останнє десятиліття за кордоном і в Україні для розвитку конвертерних процесів ведуться роботи за такими напрямами [10]:
- удосконалення конструкції агрегатів і технологічних варіантів продування;
- розробка технології виробництва сталей з мінімальним змістом шкідливих і баластних домішок, «чистих» і «особливо чистих» сталей;
- збільшення продуктивності конвертерів при одночасному рішенні екологічних завдань;
- вдосконалення газоочищення і шляхи використання конвертерного газу;
- підвищення стійкості вогнетривкого футерування;
- зменшення утворення і утилізація відходів виробництва.
Серйозних успіхів за останнє десятиліття у світі і в Україні добилися в підвищенні стійкості футерування конвертерів, головним чином, завдяки використання периклазо-вуглецевих вогнетривів, розбризкуванню кінцевого шлаку по футеруванню і різним видам торкертованія. Досягнуті рекордні показники - 17 тис. плавок - (США), 12 тис.- (КНР), 5 тис.- (Росія), 2,5 тис. - (Україна).
До позитивних рис розвитку сталеплавильного виробництва України також слід віднести послідовне завоювання на світових ринках сталі значної ніші українськими виробниками - 8,9 т загального об'єму світової торгівлі металопродукцією, що забезпечило значний (~40) внесок металургії у валютне поповнення бюджету країни [8].
У загальному плані модернізація конвертерного виробництва забезпечує досягнення традиційних цілей : підвищення якості продукції, зниження витрат виробництва, збільшення продуктивності, поліпшення охорони довкілля. Невід'ємними складовими елементами сучасної технології є:
- з'єднання верхнього кисневого продування з донним продуванням інертними газами(~80 з 660 конвертерів світу) з метою поліпшення ходу і результатів продування, обробки плавки перед випуском;
- відсікання шлаку, найчастіше - газодинамічне для зменшення попадання шлаку з конвертера в ковш під час випуску;
- автоматизація процесу з використанням допоміжної фурми-зонду, а також аналізу газів, що відходять, для точного визначення моменту повалки конвертера і випуску плавки без додувки і, у ряді випадків, без очікування аналізу(«прямий випуск»);
- система відвертання викидів для збільшення виходу придатного, удосконалення управління технологічними процесами і забезпечення безпеки персоналу.
2. Сучасна проблема киснево-конвертерного виробництва сталі
2.1 Дефіцит металобрухту
Проблема дефіциту сталевого брухту на сьогодні є актуальною. У умовах, що склалися, її рішення можливе при вдосконаленні традиційного складу і технологічного режиму формування металошихти – тих етапів, що зумовлюють хід і результати конвертерного процесу. Пошук альтернативних матеріалів на основі первородної сировини з високими фізичними характеристиками замість металевого брухту є актуальним. До класу цих матеріалів для оптимізації теплового балансу плавки відносяться такі охолоджувачі як: твердий чавун, залізна руда, залізорудні металлізованні окатиші і залізо прямого відновлення, горячебрікетированне залізо та ін.
Залізна руда, як охолоджувач, застосовується порівняно рідко. При використанні руди надмірне тепло витрачається на її нагрів і відновлення заліза з оксидів. Відновлене залізо дещо підвищує вихід придатної сталі. Охолоджувальна дія руди в 3,0-3,8 разу вище охолоджувальної дії рівної кількості брухту; витрата руди доходить до 8 %.
В порівнянні з брухтом руда, як охолоджувач, має декілька переваг [5]:
- вона забезпечує охолодження високотемпературної підфурменої зони;
- для завантаження руди не вимагається зупиняти продування;
- оксиди заліза, що містяться в руді, прискорюють розчинення в шлаку вапна, і тим самим, прискорюють шлакоутворення;
- наявність кисню в руді знижує (на 10-15 %) витрату газоподібного кисню.
Але, разом з перевагами, є ряд недоліків застосування руди. Вона вносить в шлак багато SiO2, у зв'язку з чим зростає витрата вапна і кількість шлаку, що зазвичай викликає зменшення виходу придатного. Крім того, при великій витраті руди на плавку (> 5-6 %) і її введенні однією порцією зростає кількість викидів і знижується вихід придатного металу.
Застосування в якості охолоджувачів агломерату і окатишів чинить таку ж охолоджувальну дію, як і залізна руда.
При використанні таких охолоджувачів, як вапняк і доломіт - тепло витрачається на розкладання тих, що містяться в них CaCO3 і MgCO3. Охолоджувальна здатність доломіту і вапняку близькі до охолоджувальної здатності руди. Рідкісне використання цих охолоджувачів пов'язане з тим, що вони не збільшують вихід придатного металу.
Відповідно до того, що всі перелічені вище альтернативні варіанти охолоджувачів мають ряд недоліків, виникла зацікавленість до металізованої сировини, як можливого охолоджувача в киснево-конвертерному процесі [4].
Що стосується світової практики, то дослідження по вивченню особливостей і ефективності застосування металізованої сировини в киснево-конверторному виробництві були проведені, в основному, в Німеччині і Англії. Найбільш повні і всебічні дослідження були проведені фірмою «Август Тіссен» з використанням у якості охолоджувача 70 тис. т металізованної сировини, отриманої на установці Пурофер в Оберхаузені з окатишів і кускової руди з подальшим брикетуванням і без нього.
У Україні теж існує практика застосування металізованої сировини [1]. На ВАТ «Алчевський металургійний комбінат»(АМК) випробувана заміна сталевого брухту горячебрікетированним залізом (ГБЗ), зробленим на Лебединському ГЗК. Початковою сировиною для отримання ГБЗ є офлюсовані окатиші з масовою часткою заліза більше 66,5%, одержувані з залізорудного концентрату. В основі виробництва металізованих брикетів лежать процеси прямого відновлення заліза по технологіях MIDREX і HYL - III у шахтних відновних печах ВАТ «Лебединський ГЗК» потужністю 2,4 млн. т брикетів в рік.
Досвідчені плавки із заміною сталевого брухту на ГБЗ проведені в киснево-конвертерному цеху ВАТ «АМК», який має у своєму складі 2 конвертери комбінованого дуття садкою 300 т кожен, двопозиційну установку «ковш-піч» і дві слябові двухручьові машини безперервного лиття заготівель.
Технологія виробництва сталі в сучасних конвертерних цехах вимагає мінімального вмісту кольорових металів в металургійному брухті. Використання ГБЗ, як замінника металобрухту дозволяє відповідати цій вимозі, оскільки ГБЗ робиться з первородної шихти - залізорудного концентрату. При роботі з горячебрікетированним залізом знижується окисленність кінцевого шлаку, що сприяє зниженню міри дефосфорації металу. Наприклад, при виробництві сталі в конвертерах комбінованого дуття, одним з критеріїв оцінки технологій є міра видалення фосфору. Таким чином, горячебрікетированне залізо може бути використане в конвертерному виробництві, як для заміни металобрухту, так і по ходу продування в якості охолоджувача.
Повна заміна брухту на ГБЖ дозволить:
- поліпшити прогнозованість ходу конвертерної плавки і хімічного складу одержуваного продукту, у зв'язку із стабільним хімічним складом ГБЗ;
- підвищити вихід рідкої сталі;
- понизити окисленність металу і шлаку на випуску з конвертеру;
- понизити зміст в сталі кольорових металів.
3. Відходи конвертерного виробництва
3.1. Конвертерні гази
В ході конвертерної плавки утворюється конвертерний газ. Вихід і склад газу залежать від властивостей шихти, режиму і інтенсивності продування, конструкції фурми, типу процесу і інших чинників. Газ, що відходить з конвертера, в основному, складається із CO і містить значну кількість пилу. Вихід і склад його впродовж плавки значно змінюється.
У практиці конвертерного виробництва використовується газоочищення з допалюванням і без допалювання СО. В якості паливних вторинних енергетичних ресурсів конвертерний газ використовують при відведенні газу без допалювання. В цьому випадку він є дуже цінним технологічним і енергетичним паливом. У більшості випадків виявляється доцільним використати не лише фізичне тепло газу, що відходить, але і утилізувати його як хімічну сировину або паливо. Щоб утилізувати конвертерний газ, як технологічний, його відводять, охолоджують і очищують, в основному, в електрофільтрах.
3.1.1. Способи і схеми охолодження газів
Температура газів перед газоочищенням не повинна перевищувати 200-300°С. Оскільки, температура газів на виході з конвертеру в середньому складає 1600°С, перед газоочищенням їх слід охолоджувати. Схема компанування конвертеру з основним устаткуванням охолоджувачів і газоочищення представлена на рисунку 1.
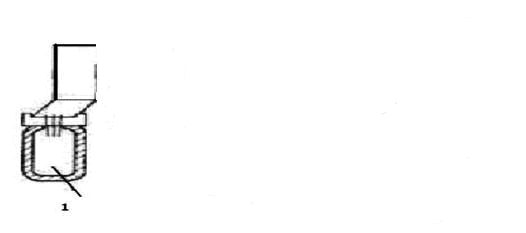
1 - конвертер; 2 - охолоджувач газів; 3 - газоочищення; 4 – газгольдер
(анімація: 5 кадрів, 5 циклів повторення, 140 кілобайт)
Рисунок 1 – Схема газового тракту за конвертером
Для охолодження конвертерних газів використовують різноманітні по конструкції і принципу дії котли-утилізатори, що дісталі назву охолоджувачів конвертерних газів (ОКГ).
Враховуючи, що конвертерні гази містять високі концентрації оксиду вуглецю, застосовувані охолоджувачі і уся система відведення диму по газовому тракту мають бути вибухобезпечними. Для забезпечення вибухобезпечності в основі систем відведення конвертерних газів можуть бути покладені два принципи:
1) зниження концентрації оксиду вуглецю за рахунок багатократного його розбавлення;
2) відведення газів з високою концентрацією оксиду вуглецю (≥ 74,5 %).
Це досягається різними способами, які відрізняються, в основному, коефіцієнтом надлишку повітря на виході з охолоджувача.
При будь-якому способі відведення і охолодження газів, газоочищення повинне забезпечити очищення настільки, щоб при викиді газів в атмосферу в приземному шарі концентрація пилу не перевиувала санітарні норми (ГДК).
При охолодженні конвертерного газу є можливість насичення газу водяними парами, що небажано з точки зору використання цього газу, як технологічного.
3.2. Очищення конвертерних газів
Система газоочищення повинна забезпечити зниження змісту пилу незалежно від способу відведення і охолодження конвертерних газів, що викидаються в атмосферу [9]. Нині у світовій практиці існує велика різноманітність систем і конструкцій газоочисних апаратів. Всі їх можна об'єднати в три великі групи по способу очищення : сухе, мокре і електроочищення.
У деяких киснево-конвертерних цехах очищення газів як і раніше ведуть в системах мокрого пиловловлення. Спочатку з потоку газу видаляється великі частинки пилу в охолоджувачах з зрошенням водою. На другому етапі очищення видаляється дрібні частинки пилу в конічному скрубері з кільцевим зазором. Такі скрубери відрізняються простотою конструкції, ефективність очищення - 30 мг/м3, малим енергоспоживанням і низькими капітальними витратами. При необхідності застосовують також скрубери Вентурі з прямокутною горловиною.
Порівнюючи мокре і сухе очищення газів, необхідно відмітити, що капітальні витрати на мокре очищення складають лише близько 70% капітальних витрат на сухе очищення [7]. Проте в системі мокрого очищення для досягнення високої ефективності пиловловлювання необхідно підтримувати високий перепад тиску, що обумовлює застосування потужніших дымососів і більш високу витрату електроенергії. Крім того, в системах мокрого очищення утворюється шлам, що вимагає обезводнення, сушки або утилізації. Сухі системи дозволяють обійтися без установки по обезводненню шламу і очищенню води. Пил з систем сухого типу можна брикетувати і використати в сталеплавильному процесі. Ці особливості, характерні для сухих систем очищення і значно знижують експлуатаційні витрати. Крім того, більш висока ефективність очищення дозволяє повністю задовольнити вимоги міжнародного законодавства, що відносяться до забруднюючих викидів конвертерів, у тому числі суворіші вимоги, які можна чекати в майбутньому. Тому системи сухого очищення з утилізацією газу зазвичай виявляються економічнішими в порівнянні з системами мокрої очистки
Для сухого очищення газів встановлюють переважно електрофільтри, зокрема, сухі пластинчаті [3]. Порівняно великі частинки пилу дозволяють експлуатувати електрофільтри при високих швидкостях газового потоку. Питомий електричний опір виключає утворення зворотної корони. На осаджувальних електродах утворюється рихлий, легко струшуваний шар пилу. Cхема пластинчатого електрофільтру типу ДГПН представлена на рисунку 2.
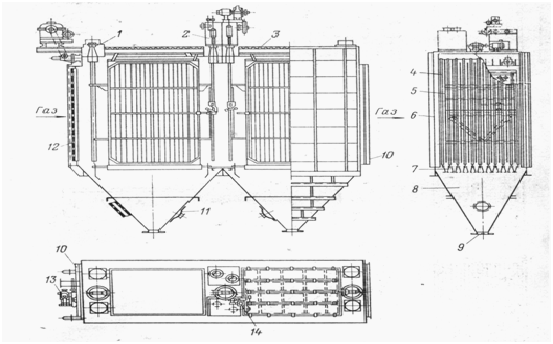
1 - крайня ізоляторна коробка; 2 - середня ізоляторна коробка;3 - монтажний люк; 4 – осаджувальні електроди; 5 коронируючі електроди; 6 - корпус електрофільтру; 7 - газовідбивачі; 8 - бункер; 9 - фланець отвору випуску пилу; 10 - фланець входу(виходу) газу; 11 - люк; 12 - газорозподільна решітка; 13 - привід струшування осаджувальних електродів; 14 - привід струшування коронируючих електродів.
Рисунок 2 – пластинчатого електрофільтру типу ДГПН
Метод очищення газу в електрофільтрах від зважених у ньому часток пилу і рідини, заснований на використанні явища іонізації газових молекул в електричному полі високої напруги. Ці частки отримують заряд від іонів газу і осідають на електродах електрофільтру, а очищений газ виводять з апарата.
3.3. Використання конвертерних газів
При відведенні конвертерного газу без допалювання після охолодження і очищення його можна використати для наступних цілей: в якості палива, хімічної сировини, для підігрівання шихтових матеріалів конвертерної плавки, а також як відновник залізорудної сировини. Застосування конвертерного газу в якості палива є одним з резервів економії паливно-енергетичних ресурсів. Проте, застосування його ускладнене, у зв'язку з наступних причин: непостійністю виходу конвертерного газу як за часом, так і по кількості; різкими коливаннями складу газу в різні періоди плавки; можливістю підсосу в газовідвідний тракт повітря, що може привести до утворення газокисневої суміші і вибуху у споживаючих агрегатах. Для компенсації нерівномірного виходу і усереднювання складу газу застосовують газгольдери.
Можливість застосування конвертерного газу для відновлення залізорудної сировини обумовлена його високим відновним потенціалом [2]. Це створює передумови до розробки ефективної схеми використання газу, що включає отримання металізованого продукту і подальше застосування його в конвертерній плавці.
На рисунку 3 представлена принципова схема використання конвертерного газу в якості відновника. За рахунок створюваного нагнітачем розрідження конвертерний газ відбирається з газоходу ОКГ при температурі 950-1050 °С і через обвідний газохід спрямовується у відновний апарат. Потім він проходить через шар залізорудних окатишів, нагріває їх до 750-850 °С і відновлює до міри металізації 95 %.
Відпрацьований газ з температурою 550-650°С і змістом CO близько 35 % поступає в газоочищення, розміщену в обвідному газоході за відновним апаратом, в каплевідділювач, а потім нагнітачем подається на свіч. Залишившийся після відновлення оксидів заліза, CO допалюється на свічі.
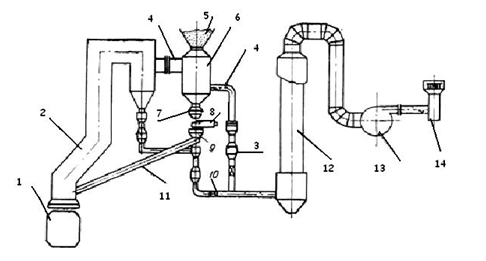
1 - конвертер; 2 - ОКГ; 3 - газоочищення; 4 - обвідний газохід; 5 - бункер; 6 - відновний апарат; 7 - бункер-накопичувач; 8 - живильник; 9 - дозатор; 10 - шибер; 11 - тічка; 12 - каплевідділювач;13 - нагнітач; 14 - свіч.
Рисунок 3 – Принципова схема використання конвертерного газу в якості відновника
Використання конвертерного газу для відновлення заліза із залізорудних окатишів, минувши доменний процес, дає економію дефіцитних і дорогих відновників. В порівнянні з використанням брухту застосування металізованих окатишів спрощує транспортування і завантаження матеріалів в конвертер, забезпечує чистішу сталь. Проте для цього потрібні додаткові капітальні і експлуатаційні витрати в цеху, об'єм яких визначає рівень економічної ефективності системи.
4. Шлаки технологічного процесу
Шлакоутворення - один з найбільш важливих фізико-хімічних процесів в конверторному переділі, оскільки забезпечує якість готової сталі. В основному він визначає дефосфорацію, десульфурацію і інші реакції. Залежно від ходу шлакоутворення і його результатів змінюється міра засвоєння флюсів і зносу футерування, втрати металу з виносами і викидами. Головними джерелами шлаку в конвертерах є: продукти окислення елементів, що містяться в металі (заліза, кремнію, марганцю, фосфору, хрому, ванадію та ін.); оксиди і солі, що входять до складу домішок, що вводяться в конвертер (в основних процесах, головним чином - вапна, залізної руди, плавикового шпату та ін.). Інші оксиди потрапляють в конвертер з доменним (міксерним) шлаком і руйнують футерування (стіни і днище). У основних конвертерних процесах для отримання активного основного шлаку в конвертер в період продування подають вапно, плавиковий шпат. При цьому продування розплаву припиняється.
Переробка шлаку відбувається в два етапи [6]:
1) Первинна переробка
Шлаки поступають на переробку в рідкому вигляді в ковшах, або у вигляді суміші твердих і рідких шлаків. Рідкий шлак зливається в траншею бескранового типу, де охолоджується водою. Інтенсивне охолодження водою призводить до наростання напруги, утворення мікротріщин і термічного руйнування шлакового моноліту. Швидкість охолодження шлаку при термодробленні зростає в 30-60 разів, вихід дрібних фракцій збільшується в 2-3 рази, а вилучення металу з шлаку - в 1,5 разу. Частину шлаку, що залишилася, розробляють екскаватором. Застиглі ковшові залишки в цьому випадку вивантажують в окрему траншею, обладнану магнітно-грейферним краном. При переробці сумішей рідких і твердих шлаків, вони вивантажуються в окрему траншею (аналогічну), охолоджуються водою, дробляться вантажем, що падає, і з них вилучається магнітною шайбою метал. При такій технології процес термодроблення відбувається слабкіше і в шлаку збільшується зміст великих шматків.
2) Вторинна переробка
Отриманий в траншеях первинної переробки шлак доставляють на вторинну переробку в подрібнювально-сортувальне відділення (ДСВ). На рисунку 4 представлена технологічна схема подрібнювально-сортувальної установки відвальних шлаків. Дроблення шлаку здійснюється на щокових, іноді молоткових дробарках. Розсів - на грохотах. Транспортування - стрічковими конвеєрами. Перед і після кожної стадії дроблення робиться відбір металу підвісними магнітними сепараторами або електромагнітними шківами. ДСВ може бути відкритого і закритого типу.
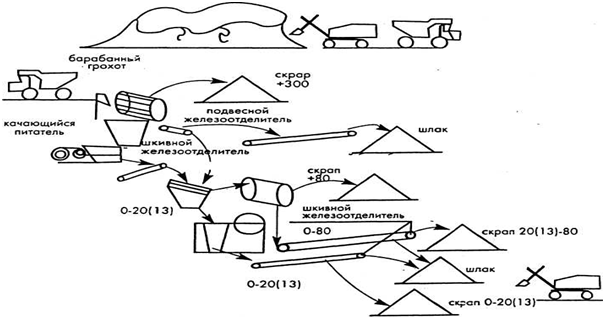
Рисунок 4 – Технологічна схема переробки відвальних шлаків
5. Пил і шлами конвертерного виробництва
Конвертерні гази, що відходять, виносять багато пилу. Разом з оксидом вуглецю з конвертеру захоплюється значна кількість пари металу і крапельок, що викидаються з ванни в процесі зневуглецювання. Пари часток в основному складаються з FeO, Fe2С, FeСO3. Залежно від складу сировини, конструкції печей і умов плавки на тонну сталі утворюється 12-25 кг тонкодисперсного пилу при «сухому» і шламу при «мокрому» способі уловлювання з розміром часток від 0,1 до 10 мкм.
5.1. Способи утилізації конвертерного пилу і шламів
Пил і шлами конвертерного виробництва після попередньої підготовки використовують як добавку в агломераційну шихту. Конвертерний шлам є інтенсифікатором аглопроцесу, надає позитивний вплив не лише на процес грудкування внаслідок своєї дисперсності, але і на динаміку плавлення шихти при спіканні. Це пояснюється присутністю в шламі великої кількості Сао, МgO і MnO.
Можливе використання конвертерних шламів в суміші з доменними шламами в якості добавки в аглошихту. Використання суміші шламів в кількості до 6 % значно збільшує продуктивність агломашин і дає більший ефект, ніж добавка одного доменного шламу і менший ефект при використанні конвертерного шламу. Використання такої суміші трохи знижує продуктивність, але покращує показник спікання аглошихти [9]. Це пояснюється збільшенням швидкості фільтрації повітря і зростанням швидкості спікання. Якість агломерату, його механічна міцність після барабана також залежать від витрати вуглецю, а при додаванні шламу практично не змінюється. Деяке погіршення механічної міцності агломерату при 5,2 % шламу в шихті пояснюється надлишком тепла в процесі спікання. Збільшення продуктивності відбувається як за рахунок збільшення виходу агломерату, так і із-за збільшення швидкості спікання. Якісні характеристики агломерату по міцності також помітно покращуються.
Найбільш поширені за кордоном схеми обезводнення передбачають згущування шламової пульпи в радіальних згущувачах, фільтрування на вакуум-фільтрах і сушку в сушильних барабанах. Проте ці схеми відрізняються підвищеними витратами при сушці шламів в капітало-енергоємних сушильних барабанах. Крім того, шлами після сушки втрачають свої гідрофільні властивості, особливо цінні при кускуванні.
На Дніпровському металургійному комбінаті ім. Дзержинського одночасно з пуском киснево-конвертерного цеху була введена в експлуатацію перша черга комплексу підготовки пилу і шламів цього виробництва за технологією, розробленою ДонНТУ. Одним з основних завдань комплексу була раціональна підготовка до утилізації в агловиробництві всіх залізовмісних відходів киснево-конвертерного цеху : шламів, вапняного пилу, пилу аспіраційних систем, відсівів вапна і вапняку, а також гранульованого конвертерного шлаку. Вперше у вітчизняній практиці на комплексі підготовки відходів була впроваджена нова технологія спільної підготовки сухого вапняного пилу вапняно-обпалювальної ділянки і вологого конвертерного шламу.
Шламоізвесткова суміш є інтенсифікатором агломераційного процесу [4]. При оптимальній її підготовці і введенні до складу залізорудної частини агломераційної шихти покращуються практично всі показники аглопроцесу. Істотно зростає продуктивність(до 10% при витраті суміші 10-30 кг/т агломерату), підвищується вихід придатного в середньому на 2% на кожні 10 кг суміші. Також підвищується якість агломерату після випробувань в стандартному барабані.
Висновки
Роль металевого брухту як основного матеріалу-охолоджувача зумовлена не лише його технологічними характеристиками як шихтового матеріалу, але і тим, що брухт є відходами. Брухт утворюється на підприємствах і в організаціях усіх галузей промисловості в процесі виробництва і обробки металу, а також внаслідок заміни устаткування у міру морального і фізичного зносу. На сьогодні питання забезпечення потреб сталеплавильного виробництва металошихтой мають особливе значення і хвилюють не лише українських, російських, але і металургів промислово розвинених країн(США, Німеччина, Японія та ін.). Передусім, вони пов'язані із скороченням долі «чистого» сталевого брухту, його кількісним дефіцитом і прогресуючим погіршенням якісних характеристик.
Тому дослідження по заміні металобрухту другими охолоджувачами плавки є актуальними. Наприклад, застосування горячебрікетированого заліза, є одним з вирішень проблеми дефіциту металургійного брухту.
Таким чином, впровадження пропонованих заходів дозволить підвищити екологічну безпеку конверторного виробництва, а також при раціональному використанні вторинних матеріальних ресурсів можливо отримати певний економічний ефект.
Викликають інтерес конвертерні шлаки, які займають величезні площі землі, якщо їх не переробляти. Основні напрями використання сталеплавильних шлаків - дорожнє будівництво, наповнювачі асфальтобетону і бетону, в сільському господарстві для розкислювання грунтів, а також в якості залізовмісного матеріалу для вторинної переплавки в доменних печах. Ефект при введенні в доменну шихту конверторного шлаку поточного виробництва у кількості 50 кг/т досягається за рахунок заміни сирого вапняку на СаО шлаку, що знижує витрату коксу на 3,2 кг/т і збільшує продуктивність доменних печей на 0,55 %. Те ж саме відбувається і при введенні шлаку в аглошихту з підвищенням основності агломерату.
Не залишаються без уваги залізовмісні пил і шлами газоочищень, які в основному, використовуються як сировина для подальшої переробки в металургійних агрегатах у вигляді згущеного, зневодненого і висушеного напівпродукту в шихті аглофабрик.
Використання конверторного газу після охолодження і очищення в якості палива, для підігрівання шихтових матеріалів конверторного виробництва, в якості відновника залізорудної сировини для доменних печей, для виробництва електроенергії і пари дозволить економити паливно-енергетичні ресурси і первинні природні ресурси.
Перелік посилань
- Близнюков, А. С. Инновационные решения в области очистки и утилизации отходящих газов в сталеплавильном производстве // Новости черной металлургии за рубежом.- 2010 - №5. – с. 77-80.
- Розенгарт, Ю.И., Якобсон Б.И., Мурадова З.А. Вторичные энергетические ресурсы черной металлургии и их использование.-К.: Выща школа, 1988.
- Панфилов, М. И., Школьник Я. Ш. и др. Переработка шлаков и безотходная технология в металлургии. - М.: Металлургия, 1987. – 238с.
- Бачинин, А. А., Мищенко И. М., Ткалич К. Н., Гелюх Л. Л. Эффективность использования конверторного шлака в аглодоменном производстве // Сталь. – 2004 - №2. – С. 7-10.
- Бережинский А.И., Циммерман А.Ф. Охлаждение и очистка газов кислородных конвертеров. - М.: Металлургия, 1975.
- В.Г. Воскобойников, В.А. Кудрин, А.М. Якушев и др. Общая металлургия: Учебник для вузов. - М.: Металлургия, 2005. – 765с.
- Старк С.Б. Газоочистные аппараты и установки в металлургическом производстве. – М.: Металлургия, 1990. – 400 с.
- Юдашкин М.Я. Пылеулавливание и очистка газов в черной металлургии. – М.: Металлургия, 1984. – 320 с.
- Толочко А.И., Филлипов В.И., Филипьев О.В. Очистка технологических газов в черной металлургии. – М.: Металлургия, 1982. – 277с.
- Казюта В. И., Казюта М. В., Сосонкин А. С. Технология комплексной переработки металлургических шламов и пыли газоочистки // Сталь. – 2010.- №2.- с. 85-87.