Реферат по теме выпускной работы
Содержание
- Введение и актуальность темы
- 1. Анализ кислородно-конвертерного производства на зарубежных и отечественных предприятиях
- 2. Современная проблема кислородно-конвертерного производства стали
- 2.1 Дефицит металлолома
- 3. Отходы конвертерного производства
- 3.1. Конвертерные газы
- 3.1.1. Способы и схемы охлаждения газов
- 3.2. Очистка конвертерных газов
- 3.3. Использование конвертерных газов
- 4. Шлаки конвертерного процесса
- 5. Пыли и шламы конвертерного производства
- 5.1. Способы утилизации конвертерной пыли и шламов
- Выводы
- Перечень ссылок
Введение и актуальность темы
Актуальность темы
Современный кислородно–конвертерный процесс, получивший широкое распространение в мире благодаря технологическим возможностям, является в настоящее время ведущим сталеплавильным процессом. Причем в последние годы по многочисленным сведениям, несмотря на кризисные явления в мировой металлургии, доля конвертерной стали стабилизировалась и сохраняется на уровне 70-75 % общего объема выплавляемого металла.
В Украине доля производства конвертерной стали постоянно увеличивается и в 2010 году составила 52% от общей выплавки стали.
Современный уровень развития кислородно–конвертерного способа производства стали, подтверждает его преимущества: высокую производительность, низкие удельные капитальные вложения и расходы по переделу, многовариантность технологии и сырьевой базы, возможность производства высококачественной стали широкого сортамента из чугуна различного химического состава. Вместе с тем для достижения повышения экологической безопасности данного производства стали, необходима оптимизация кислородно–конвертерного процесса, путем разработки рациональных мероприятий по ее повышению [1]. Такая оптимизация должна благотворно повлиять на состояние окружающей природной среды.
Наличие запасов руды и кокса, широкое развитие доменного производства подтверждает, что конвертерный передел в Украине имеет хорошие перспективы для развития.
Но, несмотря на наличие предпосылок для развития данного сталеплавильного процесса, практика сегодняшнего дня показывает, что лом, который используется в конвертерной плавке в качестве охладителя, поставляемый на металлургические предприятия, не соответствует предъявляемым к нему требованиям по содержанию таких элементов как Cr, Cu и т.п., а также физическим свойствам [3]. Наблюдается резкое сокращение доли оборотного лома, в котором вследствие многократного переплава и новых методов обработки металла повышается содержание различных примесей, способствующих снижению эксплуатационных свойств стали. Их удаление при выплавке и дальнейшей обработке чрезвычайно затруднено или практически невозможно. Неудовлетворительные показатели по физическим свойствам связаны с организацией сбора и качества подготовки металлолома в целом. Одним из факторов влияющим на снижение доли качественного оборотного лома является возрастание доли непрерывной разливки стали на металлургических предприятиях.
Таким образом, способы повышения экологической безопасности конвертерного производства и проблема дефицита стального лома на сегодняшний день являются актуальными.
Цель и задачи
Целью работы является разработка мероприятий и повышение уровня экологической безопасности кислородно-конвертерного производства стали, а так же решение проблемы дефицита металлургического лома.
Для достижения указанной цели необходимо решить такие задачи [6]:
- проанализировать технологию и материальный баланс конвертерной плавки;
- рассчитать тепловой баланс плавки, определить влияние физических и химических показателей шихтовых материалов на показатели процесса;
- определить альтернативные варианты замены металлургического лома и выбрать рациональные охладител конвертерной плавки;
- проанализировать влияние массы используемой добавки по ходу продувки и додувок на выход жидкой стали и образование выбросов;
- проанализировать эффективность отвода, очистки конвертерного газа и использавания пылей , шламов и шлаков;
- произвести эколого–экономическую оценку разработанных мероприятий.
Объект исследования — технология производства стали в кислородных конвертерах.
Предмет исследования — шихтовый и теловой режимы конвертерной плавки, определение и выбор рациональной охлаждающей добавки для процесса, способы очистки технологического газа, методы использования отходов производства.
Методы исследования — аналитический анализ литературных источников по проблеме воздействия на окружающую среду кислородно конвертерных процессов производства стали.
Научная новизна — выбор альтернативных металлолому охладителей конвертерной плавки, обоснование сухого способа очистки конвертерного газа и выбор наиболее рационального способа утилизации отходов.
1. Анализ кислородно-конвертерного производства на зарубежных и отечественных предприятиях
Совершенствование технологии конвертерного процесса является наиболее актуальной задачей современной чёрной металлургии. В силу того, что 70% стали в мире производится данным способом, существует острая потребность оптимизации затрат для него. Для отечественных предприятий это особенно важно, потому как они находятся на стадии реформирования и реорганизации своих технологий.
В настоящее время в Украине шесть конвертерных цехов (металлургические комбинаты «Арселор Миттал Кривой Рог», Мариупольские «Азовсталь» и им. Ильича, Днепровский им. Дзержинского, а также Днепропетровский и Енакиевский металлургические заводы), имеющих в своем составе 16 кислородных конвертеров и один конвертер для газокислородного рафинирования стали (завод «Днепроспецсталь»). Примечательно то, что в большинстве из них разливка стали осуществляется на МНЛЗ (исключение — «Арселор Миттал Кривой Рог» и Днепропетровский металлургический завод) [7].
В последнее десятилетие за рубежом и в Украине для развития конвертерных процессов ведутся работы по таким направлениям [10]:
- усовершенствование конструкции агрегатов и технологических вариантов продувки;
- разработка технологии производства сталей с минимальным содержанием вредных и балластовых примесей, «чистых» и «особенно чистых» сталей;
- увеличение продуктивности конвертеров при одновременном решении экологических задач;
- совершенствование гаоочистки и пути использования конвертерного газа;
- повышение стойкости огнеупорной футеровки;
- уменьшение образования и утилизация отходов производства.
Серьёзных успехов за последнее десятилетие в мире и в Украине добились в повышении стойкости футеровки конвертеров, главным образом, благодаря использованию периклазо-углеродных огнеупоров, разбрызгиванию конечного шлака по футеровке и разным видам торкертования. Достигнуты рекордные показатели – 17 тыс. плавок -(США), 12 тыс.- (КНР), 5 тыс.- (Россия), 2,5 тыс.- (Украина).
К положительным чертам развития сталеплавильного производства Украины также следует отнести последовательное завоевание на мировых рынках стали значительной ниши украинскими производителями – 8,9 % от общего объёма мировой торговли металлопродукцией, что обеспечило значительный (~40 %) взнос металлургии в валютное пополнение бюджета страны [8].
В общем плане модернизация конвертерного производства обеспечивает достижение традиционных целей: повышение качества продукции, снижение расходов производства, увеличение продуктивности, улучшение охраны окружающей среды. Неотъемлемыми составными элементами современной технологии являются:
- соединение верхней кислородной продувки с донной продувкой инертными газами (~80 % из 660 конвертеров мира) с целью улучшения хода и результатов продувки, обработки плавки перед выпуском;
- отсечение шлака, чаще всего – газодинамическое для уменьшения попадания шлака из конвертера в ковш во время выпуска;
- автоматизация процесса с использованием вспомогательной фурмы-зонда, а также анализа отходящих газов для точного определения момента повалки конвертера и выпуска плавки без додувки и, в ряде случаев, без ожидания анализа (“прямой выпуск”);
- система предотвращения выбросов для увеличения выхода годного, усовершенствование управления технологическими процессами и обеспечения безопасности персонала.
2. Современная проблема кислородно-конвертерного производства стали
2.1. Дефицит металлолома
Проблема дефицита стального лома на сегодняшний день является актуальной. В сложившихся условиях ее решение возможно при совершенствовании традиционного состава и технологического режима формирования металлошихты - этапов предопределяющих ход и результаты конвертерного процесса. Поиск альтернативных материалов на основе первородного сырья с высокими физическими характеристиками взамен металлического лома является актуальным. К классу этих материалов для оптимизации теплового баланса плавки относятся такие охладители как: твердый чугун, железная руда, железорудные металлизованные окатыши и железо прямого восстановления, горячебрикетированное железо и др.
Железная руда, как охладитель, применяется сравнительно редко. При использовании руды избыточное тепло расходуется на ее нагрев и восстановление железа из оксидов. Восстановленное железо несколько повышает выход годной стали. Охлаждающее действие руды в 3,0-3,8 раза выше охлаждающего действия равного количества лома; расход руды доходит до 8 %.
По сравнению с ломом руда, как охладитель, имеет несколько преимуществ [5]:
- она обеспечивает охлаждение высокотемпературной подфурменной зоны;
- для загрузки руды не требуется останавливать продувку;
- содержащиеся в руде оксиды железа ускоряют растворение в шлаке извести, и тем самым, ускоряют шлакообразование;
- наличие кислорода в руде снижает (на 10-15 %) расход газообразного кислорода.
Но, наряду с преимуществами, имеется ряд недостатков применеия руды. Она вносит в шлак много SiO2, в связи с чем возрастает расход извести и количество шлака, что обычно вызывает уменьшение выхода годного. Кроме того, при большом расходе руды на плавку (> 5-6 %) и ее введении одной порцией возрастает количество выбросов и снижается выход годного металла.
Применение в качестве охладителей агломерата и окатышей оказывает такое же охлаждающее действие, как и железная руда.
При использовании в качестве охладителей известняка и доломита тепло расходуется на разложение содержащихся в них CaCO3 и MgCO3. Охлаждающая способность доломита и известняка близки к охлаждающей способности руды. Редкое использование этих охладителей связано с тем, что они не увеличивают выход годного металла.
В соответствии с тем, что все выше перечисленные альтернативные варианты охладителей имеют ряд недостатков, возник интерес к металлизованному сырью как возможному охладителю в кислородно-конвертерном процессе [4].
Что касается мировой практики, то исследования по изучению особенностей и эффективности применения металлизованного сырья в кислородно-конверторном производстве были проведены, в основном, в Германии и Англии. Наиболее полные и всесторонние исследования были проведены фирмой «Август Тиссен» с использованием в качестве охладителя 70 тыс. т металлизованного сырья, полученного на установке Пурофер в Оберхаузене из окатышей и кусковой руды с последующим брикетированием и без него.
В Украине тоже существует практика применения металлизированного сырья [1]. На ОАО «Алчевский металлургический комбинат»(АМК) опробована замена стального скрапа горячебрикетированным железом (ГБЖ), произведенным на Лебединском ГОКе. Исходным сырьем для получения ГБЖ являются офлюсованные окатыши с массовой долей железа более 66,5 %, получаемые из железорудного концентрата. В основе производства металлизованных брикетов лежат процессы прямого восстановления железа по технологиям MIDREX и HYL-III в шахтных восстановительных печах ОАО «Лебединский ГОК» мощностью 2,4 млн. т брикетов в год.
Опытные плавки с заменой стального скрапа на ГБЖ проведены в кислородно-конвертерном цехе ОАО «АМК», который имеет в своем составе 2 конвертера комбинированного дутья садкой 300 т каждый, двухпозиционную установку «ковш-печь» и две слябовые двухручьевые машины непрерывного литья заготовок.
Технология производства стали в современных конвертерных цехах требует минимального содержания цветных металлов в металлургическом ломе. Использование ГБЖ, как заменителя металлолома позволяет соответствовать данному требованию, так как ГБЖ производится из первородной шихты - железорудного концентрата. При работе с горячебрикетированным железом снижается окисленность конечного шлака, что способствует снижению степени дефосфорации металла. Например, при производстве стали в конвертерах комбинированного дутья, одним из критериев оценки технологий является степень удаления фосфора. Таким образом, горячебрикетированное железо может быть использовано в конвертерном производстве, как для замены металлолома, так и по ходу продувки в качестве охладителя.
Полная замена лома на ГБЖ позволит:
- улучшить прогнозируемость хода конвертерной плавки и химического состава получаемого продукта, в связи со стабильным химическим составом ГБЖ;
- повысить выход жидкой стали;
- снизить окисленность металла и шлака на выпуске из конвертера;
- снизить содержание в стали цветных металлов.
3. Отходы конвертерного производства
3.1. Конвертерные газы
В ходе конвертерной плавки образуется конвертерный газ. Выход и состав газа зависят от свойств шихты, режима и интенсивности продувки, конструкции фурмы, типа процесса и других факторов. Отходящий из конвертера газ, в основном, состоит из СО и содержит значительное количество пили. Выход и состав его в течение плавки значительно изменяется.
В практике конвертерного производства используется газоочистка с дожиганием и без дожигания СО. В качестве топливных вторичных энергетических ресурсов конвертерный газ используют при отводе газа без дожигания. В этом случае он представляет собой весьма ценное технологическое и энергетическое топливо. . В большинстве случаев оказывается целесообразным использовать не только физическое тепло отходящего газа, но и утилизировать его как химическое сырье или топливо. Чтобы утилизировать конвертерный газ, как технологический, его отводят, охладают и очищают, в основном, в электрофильтрах.
3.1.1. Способы и схемы охлаждения газов
Температура газов перед газоочисткой не должна превышать 200–300°С. Поскольку температура газов на выходе из конвертера в среднем составляет 1600°С, перед газоочисткой их следует охлаждать. Схема компоновки конвертера с основным оборудованием охладителей и газоочистки представлена на рисунке 1.
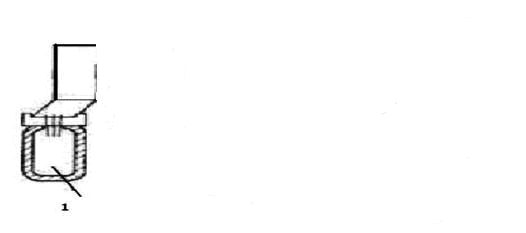
1 - конвертер; 2 - охладитель газов; 3 - газоочистка; 4 – газгольдер
(анимация: 5 кадров, 5 циклов повторения, 140 килобайт)
Рисунок 1 – Схема газового тракта за конвертером
Для охлаждения конвертерных газов используют разнообразные по конструкции и принципу действия котлы-утилизаторы, получившие название охладителей конвертерных газов (ОКГ).
Учитывая, что конвертерные газы содержат высокие концентрации оксида углерода, применяемые охладители и вся система отвода дыма по газовому тракту должны быть взрывобезопасными. Для обеспечения взрывобезопасности в основе систем отвода конвертерных газов могут быть положены два принципа:
1) снижение концентрации оксида углерода за счет многократного его разбавления;
2) отвод газов с высокой концентрацией оксида углерода (≥ 74,5 %).
Это достигается различными способами, которые отличаются, в основном, коэффициентом избытка воздуха на выходе из охладителя.
При любом способе отвода и охлаждения газов газоочистка должна обеспечить очистку настолько, чтобы при выбросе газов в атмосферу в приземном слое концентрация пыли не должна превышать санитарные нормы (ПДК).
При охлаждении конвертерного газа имеется возможность насыщения газа водяными парами, что нежелательно с точки зрения использования этого газа, как технологического.
3.2. Очистка конвертерных газов
Система газоочистки должна обеспечить снижение содержания пыли независимо от способа отвода и охлаждения конвертерных газов, выбрасываемых в атмосферу [9]. В настоящее время в мировой практике существует большое разнообразие систем и конструкций газоочистных аппаратов. Все их можно объединить в три большие группы по способам очистки: сухую, мокрую и электроочистку.
В некоторых кислородно-конвертерных цехах очистку газов по-прежнему ведут в системах мокрого пылеулавливания. Сначала из потока газа удаляется крупная пыль в охладителях с орошением водой. На втором этапе очистки удаляется мелкая пыль в коническом скруббере с кольцевым зазором. Такие скрубберы отличаются простотой конструкции, эффективность очистки – 30 мг/м3, малым энергопотреблением и низкими капитальными затратами. При необходимости применяют также скрубберы Вентури с прямоугольной горловиной.
Сравнивая мокрую и сухую очистку газов, необходимо отметить, что капитальные затраты на мокрую очистку составляют лишь около 70% от капитальных затрат на сухую очистку[7]. Однако в системе мокрой очистки для достижения высокой эффективности пылеулавливания необходимо поддерживать высокий перепад давления, что обуславливает применение более мощных дымососов и более высокий расход электроэнергии. Кроме того, в системах мокрой очистки образуется шлам, требующий обезвоживания, сушки или захоронения. Сухие системы позволяют обойтись без установки по обезвоживания шлама и очистки воды. Пыль из систем сухого типа можно брикетировать и использовать в сталеплавильном процессе. Эти особенности, характерные для сухих систем очистки, значительно снижают эксплуатационные затраты. Кроме того, более высокая эффективность очистки позволяет полностью удовлетворить требования международного законодательства, относящиеся к загрязняющим выбросам конвертеров, в том числе более строгие требования, которые можно ожидать в будущем. Поэтому системы сухой очистки с утилизацией газа обычно оказываются более экономичными по сравнению с системами мокрой очистки.
Для сухой очистки газов устанавливают преимущественно электрофильтры, в частности, сухие пластинчатые [3]. Сравнительно крупная пыль позволяет эксплуатировать электрофильтры при высоких скоростях газового потока. Удельное электрическое сопротивление исключает образование обратной короны. На осадительных электродах образуется рыхлый, легко стряхиваемый слой пыли. Cхема пластинчатого электрофильтра типа ДГПН представлена на рисунке 2.
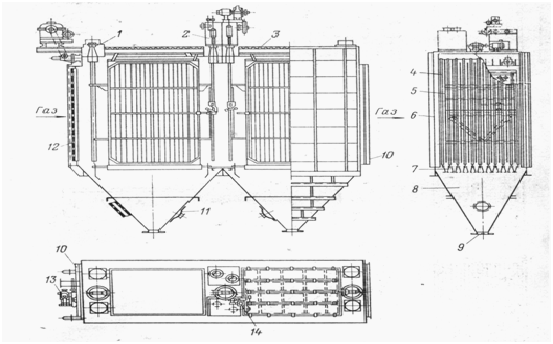
1 - крайняя изоляторная коробка; 2 - средняя изоляторная коробка;3 - монтажный люк; 4 - осадительные электроды; 5 коронирующие электроды; 6 - корпус электрофильтра; 7 - газоотражатели; 8 - бункер; 9 - фланец отверстия выпуска пыли; 10 - фланец входа (выхода) газа; 11 - люк; 12 -газораспределительная решетка; 13 - привод встряхивания осадительных электродов; 14 - привод встряхивания коронирующих электродов.
Рисунок 2 – Cхема пластинчатого электрофильтра типа ДГПН
Метод очистки газа в электрофильтрах от взвешенных в нем частиц пыли и жидкости, основан на использовании явления ионизации газовых молекул в электрическом поле высокого напряжения. Эти частицы получают заряд от ионов газа и осаждаются на электродах электрофильтра, а очищенный газ выводят из аппарата.
3.3. Использование конвертерных газов
При отводе конвертерного газа без дожигания после охлаждения и очистки его можно использовать для следующих целей: в качестве топлива, химического сырья, для подогрева шихтовых материалов конвертерной плавки, а также как восстановитель железорудного сырья.
Применение конвертерного газа в качестве топлива является одним из резервов экономии топливно-энергетических ресурсов. Однако, применение его затруднено, в связи по следующим причинам: непостоянством выхода конвертерного газа как по времени, так и по количеству; резкими колебаниями состава газа в разные периоды плавки; возможностью подсоса в газоотводящий тракт воздуха, что может привести к образованию газокислородной смеси и взрыву у потребляющих агрегатов. Для компенсации неравномерного выхода и усреднения состава газа применяют газгольдеры.
Возможность применения конвертерного газа для восстановления железорудного сырья обусловлена его высоким восстановительным потенциалом [2]. Это создает предпосылки к разработке эффективной схемы использования газа, включающей получение металлизованного продукта и последующее применение его в конвертерной плавке.
На рисунке 3 представлена принципиальная схема использования конвертерного газа в качестве восстановителя. За счет создаваемого нагнетателем разрежения конвертерный газ отбирается из газохода ОКГ при температуре 950-1050?С и через обводной газоход направляется в восстановительный аппарат. Затем он проходит через слой железорудных окатышей, нагревает их до 750-850?С и восстанавливает до степени металлизации 95%. Отработанный газ с температурой 550-650?С и содержанием СО около 35% поступает в газоочистку, размещенную в обводном газоходе за восстановительным аппаратом, в каплеотделитель, а затем нагнетателем подается на свечу. Оставшийся после восстановления оксидов железа СО, дожигается на свече.
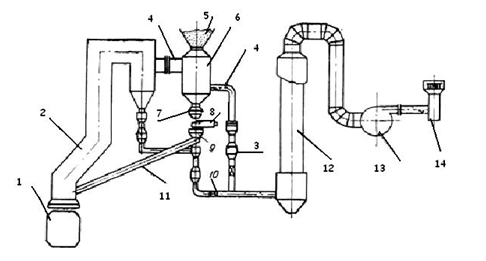
1 - конвертер; 2 - ОКГ; 3 - газоочистка; 4 - обводной газоход; 5 - бункер; 6 - восстановительный аппарат; 7 - бункер-накопитель; 8 - питатель; 9 - дозатор; 10 - шибер; 11 - течка; 12 - каплеотделитель;13 - нагнетатель; 14 - свеча.
Рисунок 3 – Принципиальная схема использования конвертерного газа в качестве восстановителя
Использование конвертерного газа для восстановления железа из железорудных окатышей, минуя доменный процесс, дает экономию дефицитных и дорогостоящих восстановителей. По сравнению с использованием лома применение металлизованных окатышей упрощает транспортировку и загрузку материалов в конвертер, обеспечивает более чистую сталь. Однако для этого необходимы дополнительные капитальные и эксплуатационные затраты в цехе, объем которых определяет уровень экономической эффективности системы.
4. Шлаки конвертерного процесса
Шлакообразование – один из наиболее важных физико-химических процессов в конверторном переделе, так как обеспечивает качество готовой стали. В основном он определяет дефосфорацию, десульфурацию и другие реакции. В зависимости от хода шлакообразования и его результатов изменяется степень усвоения флюсов и износа футеровки, потери металла с выносами и выбросами. Главными источниками шлака в конвертерах являются: продукты окисления элементов, содержащихся в металле (железа, кремния, марганца, фосфора, хрома, ванадия и др.); окислы и соли, входящие в состав добавок, вводимых в конвертер (в основных процессах, главным образом - извести, железной руды, плавикового шпата и др,). Остальные окислы попадают в конвертер с доменным (миксерным) шлаком и разрушают футеровку (стены и днище). . В основных конвертерных процессах для получения активного основного шлака в конвертер в период продувки подают известь, плавиковый шпат. При этом продувка расплава прекращается.
Переработка шлака происходит в два этапа [6]:
1) Первичная переработка
Шлаки поступают на переработку в жидком виде в ковшах, или в виде смеси твердых и жидких шлаков. Жидкий шлак сливается в траншею бескранового типа, где охлаждается водой. Интенсивное охлаждение водой приводит к нарастанию напряжений, образованию микротрещин и термическому разрушению шлакового монолита. Скорость охлаждения шлака при термодроблении возрастает в 30-60 раз, выход мелких фракций увеличивается в 2-3 раза, а извлечение металла из шлака – в 1,5 раза. Оставшуюся часть шлака разрабатывают экскаватором. Застывшие ковшовые остатки в этом случае выгружают в отдельную траншею, оборудованную магнитно-грейферным краном. При переработке смесей жидких и твердых шлаков, они выгружаются в отдельную траншею (аналогичную), охлаждаются водой, дробятся падающим грузом и из них извлекается магнитной шайбой металл. При такой технологии процесс термодроблени происходит слабее и в шлаке увеличивается содержание крупных кусков.
2) Вторичная переработка
Полученный в траншеях первичной переработки шлак доставляют на вторичную переработку в дробильно-сортировочное отделение (ДСО). На рисунке 4 представлена технологическая схема дробильно-сортировочной установки отвальных шлаков. Дробление шлака осуществляется на щековых, иногда молотковых дробилках. Рассев – на грохотах. Транспортировка – ленточными конвейерами. Перед и после каждой стадии дробления производится отбор металла подвесными магнитными сепараторами или электромагнитными шкивами. ДСО может быть открытого и закрытого типа.
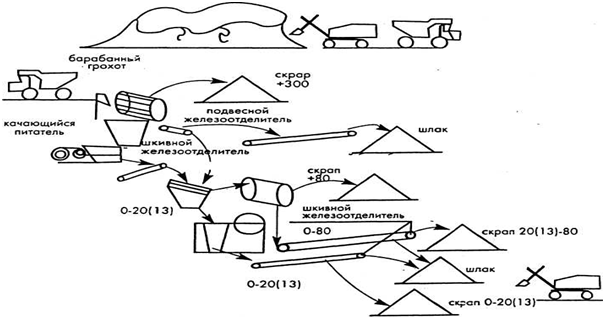
Рисунок 4 – Технологическая схема переработки отвальных шлаков
5. Пыли и шламы конвертерного производства
Отходящие конвертерные газы выносят много пыли. Вместе с оксидом углерода из конвертера увлекается значительное количество паров металла и капелек, выбрасываемых из ванны в процессе обезуглероживания. Пары частиц в основном состоят из FeO, Fe2С, FeСO3. В зависимости от состава сырья, конструкции печей и условий плавки на тонну стали образуется 12–25 кг. тонкодисперсной пыли при «сухом» и шлама при «мокром» способе улавливания с размером частиц от 0,1 до 10 мкм.
5.1. Способы утилизации конвертерной пыли и шламов
Пыль и шламы конвертерного производства после предварительной подготовки используют в качестве добавки в агломерационную шихту. Конвертерный шлам является интенсификатором аглопроцесса, оказывает положительное влияние не только на процесс окомкования вследствие своей дисперсности, но и на динамику плавления шихты при спекании. Это объясняется присутствием в шламе большого количества СаО, МgO и MnO.
Возможно использование конвертерных шламов в смеси с доменными шламами в качестве добавки в аглошихту. Использование смеси шламов в количестве до 6% значительно увеличивает производительность агломашин и дает больший эффект, чем добавка одного доменного шлама и меньший эффект при использовании конвертерного шлама. Использование такой смеси незначительно снижает производительность, но улучшает показатель спекания аглошихты [9]. Это объясняется увеличением скорости фильтрации воздуха и ростом скорости спекания. Качество агломерата, его механическая прочность после барабана также зависят от расхода углерода, а при добавлении шлама практически не изменяется. Некоторое ухудшение механической прочности агломерата при 5,2% шлама в шихте объясняется избытком тепла в процессе спекания. Увеличение производительности происходит как за счет увеличения выхода агломерата, так из-за увеличения скорости спекания. Качественные характеристики агломерата по прочности также заметно улучшаются.
Наиболее распространенные за рубежом схемы обезвоживания предусматривают сгущение шламовой пульпы в радиальных сгустителях, фильтрование на вакуум-фильтрах и сушку в сушильных барабанах. Однако эти схемы отличаются повышенными затратами при сушке шламов в капитало-энергоемких сушильных барабанах. Кроме того, шламы после сушки теряют свои гидрофильные свойства, особо ценные при окусковании.
На Днепровском металлургическом комбинате им. Дзержинского одновременно с пуском кислородно-конвертерного цеха была введена в эксплуатацию первая очередь комплекса подготовки пылей и шламов этого производства по технологии, разработанной ДонНТУ. Одной из основных задач комплекса была рациональная подготовка к утилизации в аглопроизводстве всех железосодержащих отходов кислородно-конвертерного цеха: шламов, известковой пыли, пылей аспирационных систем, отсевов извести и известняка, а также гранулированного конвертерного шлака. Впервые в отечественной практике на комплексе подготовки отходов была внедрена новая технология совместной подготовки сухой известковой пыли известково-обжигового участка и влажного конвертерного шлама.
Шламоизвестковая смесь является интенсификатором агломерационного процесса [4]. При оптимальной их подготовке и введении в состав железорудной части агломерационной шихты улучшаются практически все показатели аглопроцесса. Существенно возрастает производительность (до 10% при расходе смеси 10-30 кг/т агломерата), повышается выход годного в среднем на 2% на каждые 10 кг смеси. Также повышается качество агломерата после испытаний в стандартном барабане.
Выводы
Роль металлического лома как основного материала-охладителя предопределена не только его технологическими характеристиками как шихтового материала, но и тем, что лом представляет собой отходы. Лом образуется на предприятиях и в организациях всех отраслей промышленности в процессе производства и обработки металла, а также вследствие замены оборудования по мере морального и физического износа. На сегодняшний день вопросы обеспечения потребностей сталеплавильного производства металлошихтой имеют особое значение и волнуют не только украинских, российских, но и металлургов промышленно развитых стран (США, Германия, Япония и др.). Прежде всего, они связаны с сокращением доли «чистого» стального лома, его количественным дефицитом и прогрессирующим ухудшением качественных характеристик.
Поэтому исследования по замене металлолома другими охладителями плавки являются актуальными. Например, применение горячебрикетированного железа, является одним из решений проблемы дефицита металлургического лома.
Таким образом, внедрение предлагаемых мероприятий позволит повысить экологическую безопасность конверторного производства, а также при рациональном использовании вторичных материальных ресурсов возможно получить определенный экономический эффект.
Так интерес вызывают конвертерные шлаки, которые занимают огромные площади земли, если их не перерабатывать. Основные направления использования сталеплавильных шлаков - дорожное строительство, наполнители асфальтобетона и бетона, в сельском хозяйстве для раскисления почв, а также в качестве железосодержащего материала для вторичной переплавки в доменных печах. Эффект при введении в доменную шихту конверторного шлака текущего производства в количестве 50 кг/т достигается за счет замены сырого известняка на СаО шлака, что снижает расход кокса на 3,2 кг/т и увеличивает производительность доменніх печей на 0,55%. То же происходит и при введении шлака в аглошихту с повышением основности агломерата.
Не остаются без внимания железосодержащие пыль и шламы газоочисток, которые в основном, используются в качестве сырья для дальнейшей переработки в металлургических агрегатах в виде сгущенного, обезвоженного и высушенного полупродукта в шихте аглофабрик.
Использование конверторного газа после охлаждения и очистки в качестве топлива, для подогрева шихтовых материалов конверторного производства, в качестве восстановителя железорудного сырья для доменных печей, для выработки электроэнергии и пара позволит экономить топливно-энергетические ресурсы и первичные природные ресурсы.
Перечень ссылок
- Близнюков, А. С. Инновационные решения в области очистки и утилизации отходящих газов в сталеплавильном производстве // Новости черной металлургии за рубежом.- 2010 - №5. – с. 77-80.
- Розенгарт, Ю.И., Якобсон Б.И., Мурадова З.А. Вторичные энергетические ресурсы черной металлургии и их использование.-К.: Выща школа, 1988.
- Панфилов, М. И., Школьник Я. Ш. и др. Переработка шлаков и безотходная технология в металлургии. - М.: Металлургия, 1987. – 238с.
- Бачинин, А. А., Мищенко И. М., Ткалич К. Н., Гелюх Л. Л. Эффективность использования конверторного шлака в аглодоменном производстве // Сталь. – 2004 - №2. – С. 7-10.
- Бережинский А.И., Циммерман А.Ф. Охлаждение и очистка газов кислородных конвертеров. - М.: Металлургия, 1975.
- В.Г. Воскобойников, В.А. Кудрин, А.М. Якушев и др. Общая металлургия: Учебник для вузов. - М.: Металлургия, 2005. – 765с.
- Старк С.Б. Газоочистные аппараты и установки в металлургическом производстве. – М.: Металлургия, 1990. – 400 с.
- Юдашкин М.Я. Пылеулавливание и очистка газов в черной металлургии. – М.: Металлургия, 1984. – 320 с.
- Толочко А.И., Филлипов В.И., Филипьев О.В. Очистка технологических газов в черной металлургии. – М.: Металлургия, 1982. – 277с.
- Казюта В. И., Казюта М. В., Сосонкин А. С. Технология комплексной переработки металлургических шламов и пыли газоочистки // Сталь. – 2010.- №2.- с. 85-87.