Osovska Anastasiia
Faculty of ecology and chemical technology
Department of applied ecology and environmental protection
Speciality Chemical technology of refractory nonmetallic and silicate materials
The mechanism of allocation of aluminium hydroxide from solutions of sodium aluminate
Scientific adviser: Dr. of Chem., Prof. Valery Shapovalov
Abstract
Content
Introduction1. Relevance of the topic
2. The goals and objectives of the study
3. Mechanism for the allocation of aluminum hydroxide from sodium aluminate
Conclusion
References
Introduction
Alumina is the main raw material for the production of primary aluminum, the rest — the production of sintered and fused alumina ceramics, refractories, high alumina cement, etc. Each area of application of alumina needs to perform certain technical conditions as set out in DSTU or GOST [1].
Aluminum — metal of strategic importance, which combines a number of physical and chemical properties, which are supported by a wide range of application areas, from consumer goods to the aircraft. Amphoteric properties of aluminum significantly extend the capabilities of the production of alumina from ores of different composition. The aluminum content by weight in the earth's crust — 8.13% — the third after oxygen and silicon. However, for the aluminum oxide — a necessary precursor to the technology of aluminum — used by a limited number of minerals and ores.
One of the main methods for the production of alumina is the carbonation. Carbonation is necessary for the decomposition of aluminate solutions in order to separate aluminum hydroxide [2].
It consists of treating the aluminate solution with gases containing carbon dioxide.
The complexity of this process is that the carbonation of aluminate solution, i.e. on during the process and on the quality of the aluminum hydroxide, are strongly influenced by the following factors:
- temperature conditions;
- stirring;
- the duration (rate of carbonation);
- the degree (depth) of the decomposition solution.
1. Relevance of the topic
The paper considers new scheme carbonization process aluminate solution comprising the formation as the primary product alyumokarbonata solution and its subsequent conversion to aluminum hydroxide in the reaction with sodium aluminate.
2. The goals and objectives of the study
The main purpose is to investigate and confirm the new scheme of the carbonization process aluminate solutions and an explanation of the reasons for pollution aluminum hydroxide, sodium compounds.
The objective is to obtain experimental data that confirm the new scheme of the carbonization process aluminate solutions.
3 Mechanism for the allocation of aluminum hydroxide from sodium aluminate
Carbonation — one of the methods used in the practice of alumina production for the decomposition of aluminate solutions in order to isolate the crystalline aluminum hydroxide [3].
To isolate the Al(OH) 3 are appropriate carbonization, since along with the aluminum hydroxide, sodium carbonate solution is obtained, which is used as a working solution. From a chemical standpoint carbonization process takes place in several stages [4]. The carbon dioxide is consumed in overcoming the first buffer tank and the subsequent formation of amorphous phase, which dissolves in excess caustic:
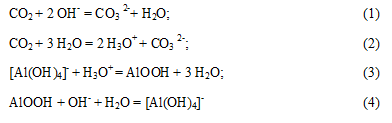
In comparable conditions, the rates of formation of new particles in the solid phase crystallization allocated aluminum trihydroxide:

In further carbonization carbon dioxide is spent on education in a solution of bicarbonate ions:

At pH values below the liquid phase 10. and increasing its content of HCO3-ions are formed alyumokarbonatov alkali metals:

On carbonation of aluminate solution, i.e. on during the process, and mainly - on the quality of the aluminum hydroxide, are strongly influenced by the following factors: 1) temperature condition, 2) mixing 3) Duration (carbonization speed) 4) degree (depth) of the decomposition solution. In industrial applications, these factors must be combined so that the resulting aluminum hydroxide may contain less impurities silica and alkali and size of its crystal was such that the hydrate pulp is well filtered [5]. If contamination of aluminum hydroxide silica most significantly affected purity of the starting aluminate solution, the alkali hydrate pollution affects the sum of many factors, so nature (origin) of alkali in the aluminum hydroxide is not so simple. The admixture of alkali hydroxide contained in the aluminum, first, a so-called alkali laundered which may be completely removed from the boiling water hydrate and represents an alkali hydroxide adsorbed from the mother liquor and, secondly, connected in the form of alkali (sodium hydroaluminosilicates ) and thirdly, in the form of so-called alkali mezhkristalnoy which is enclosed between the edges of individual crystals in the aggregates hydroxide. Lye between crystals can only be removed by heating aluminum hydroxide at high temperature. The admixture of alkali hydroxide of aluminum, in addition to deterioration resulting Аl2О3, increases the deadweight loss [6].
The basis of the published schemes carbonization process (similar to the scheme 1-7) put the fact that alyumokarbonaty alkali metals are obtained at the end of the carbonization process and are considered as impurity products [7].
However, the most complete and systematic study of the influence of various factors on the process of carbonization of aluminate solutions shows that a greater or lesser extent, the resulting aluminum hydroxide gidroalyumokarbonat always contains sodium.
Based on the concepts of coordination chemistry, given that sodium aluminate is the coordination compound can propose an alternative scheme emanating from the carbonisation of the product that the primary carbonization is gidroalyumokarbonat sodium, which further reacted with the alkali aluminate and sodium hydroxide to form alumina. The process of carbonization of the above positions can be represented by the following formula:
Of sodium aluminate solution:

The initial period of carbonization (induction period), the no-observed precipitation giroksida aluminum and sodium gidroalyumokarbonata:

or total:

In solution the equilibrium of reaction (8), the binding of NaOH, is shifted toward the formation of Na[Al(OH)4] and begins to form its carbonation gidroalyumokarbonata sodium:

Precipitate Na[Al(OH)2СО3] (т) is reacted with sodium aluminate solution to form an aluminum hydroxide:

The proposed scheme is confirmed by the following experimental data:
1. Carbonation aluminate solution has an induction time during which a solution of sodium carbonate concentration increases, but there is no selection of solution phase solid aluminum hydroxide and hydrogen - the reaction proceed in a solution (8 - 10).
2. Sodium bicarbonate can be reacted with sodium aluminate according to reaction (12) to form Al(OH)3, which is confirmed by the change of IR spectra of products containing GAKN. After exposure to the aluminate solution IR spectrum was identical to that of Al(OH)3 (Fig. 1). Since the reaction (12) is heterogeneous (solid - solution), then its speed is relatively low
3. Samples of sediment after the induction period gidroalyumokarbonat contain sodium. It depends on the conditions of carbonization (Tables 1-3) and Fig. 2. This is due to reaction (11). The rate of the latter will increase with the concentration of СО2, speed of feed (Table 3) and with increasing temperature (Fig. 2).
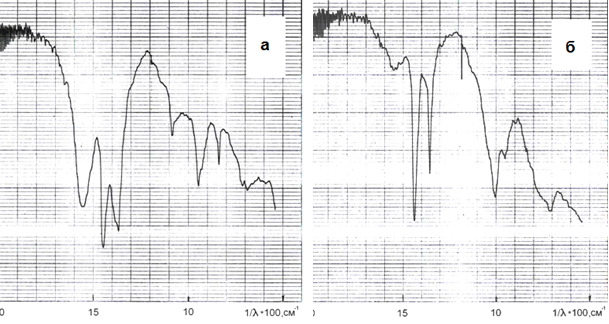
Figure 1. IR spectra carbonization aluminate solution (a) and the product of its interaction with the aluminate solution (b).
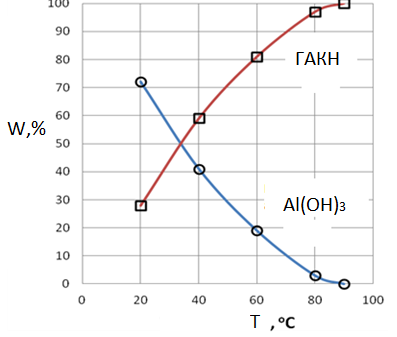
Figure 2. The effect of temperature on the formation of aluminum hydroxide and sodium gidroalyumokarbonata.
Scheme (9-12) corresponds to the following system of differential equations:
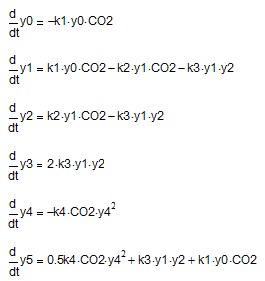
where y0, y1, y2, y3, y4, y5 — current concentration Na3[Al(OH)6], Na[Al(OH)4], Na3[Al(OH)2CO3], Al(OH)3, NaOН та Na2CO3 respectively; СО2 – conditional concentration СО2.
The kinetic parameters (ki) heterogeneous reactions (9 - 12) represent some complex values, including direct chemical interaction hydrodynamic and thermal conditions, the particle size of the solid phase, the stirring rate of the solution, etc. For this reason, they can be relatively certain only at fixed conditions of the process of carbonization of aluminate solutions. For this reason, making the task of analyzing this system of equations is not to obtain specific numerical results, and the possibility in principle to confirm the correct response of the proposed scheme of reactions to changes in the conditions of carbonation.
The calculation results in the form of formal kinetic curves are shown in Fig. 3 и 4.
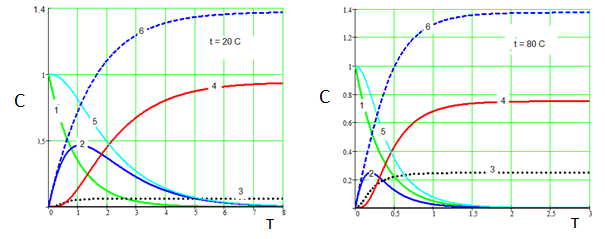
Figure.3. Temperature effect on carbonation of aluminate solution. 1 – Na3[Al(OH)6], 2 - Na[Al(OH)4], 3 - Na3[Al(OH)2CO3], 4 - Al(OH)3, 5 – суммарная концентрация Al3+ в растворе, 6 – Na2CO3. СО2 = 0.5. (k01=1∙103 , E1 =15000; k02 =2∙106, E2=36000; k03=2∙103, E2=14000; k4=4)
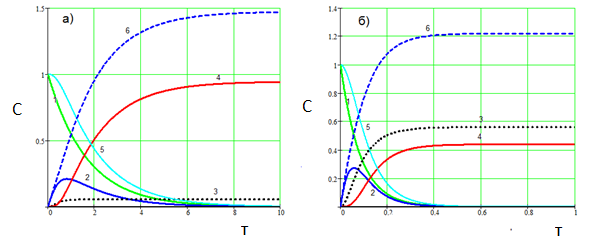
Figure.4. Effect of the CO2 carbonation aluminate solution. а) СО2 = 0.1 б) СО2 = 2.0. Температура 80 °С. 1 – Na3[Al(OH)6], 2 – Na[Al(OH)4], 3 - Na3[Al(OH)2CO3], 4 - Al(OH)3, 5 – the total concentration of Al3+ in solution, 6 – Na2CO3. (k01=1∙103, E1=15000; k02=2∙106, E2=36000; k03=2∙103, E2=14000; k4=4))
As seen from Fig 3, the carbonization temperature significantly affects the ratio (aluminum hydroxide) (alyumokarbonat sodium). With increasing temperature, the proportion of alyumokarbonata sodium increases substantially. With increasing speed of the transmission СО2 quantity obtained Na3[Al(OH)2CO3] may exceed the number of Al(OH)3 (Fig. 4, b). At the same time, (Fig.4), decrease in the rate of СО2 supply can be isolated from the aluminate solution mainly aluminum hydroxide even at high temperatures (Fig.4, а).
The theoretical curves of the effect of temperature on the formation of aluminum hydroxide and sodium gidroalyumokarbonata (Fig.5) identical curves constructed on the basis of experimental data and presented at the Fig. 2.
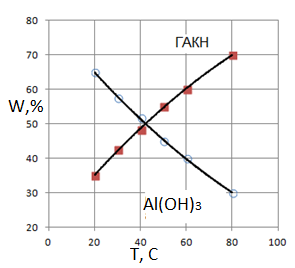
Figure.5. The theoretical curves of the effect of temperature on the formation of aluminum hydroxide and sodium gidroalyumokarbonata. СО2=1.5. (k01=1∙103, E1=15000; k02=2∙106, E2=36000; k03=2∙103, E2=14000; k4=4)
Conclusion
Thus the proposed scheme of chemical reactions can fundamentally change the organization of the process of carbonization of aluminate solutions. Instead, difficult to control a step of carbonizing the aluminate solution coming from leaching separation, obtaining an aluminum hydroxide can be made in two well-controlled stage. To this solution after leaching of alumina should be divided into two parts. The first part of the solution until the char to release alumina as a precipitate gidroalyumokarbonata solution. After separation of the precipitate is mixed with a second part of the aluminate solution, and the reaction (12) is converted to aluminum hydroxide. The resulting sodium carbonate solution enters the leaching of caking.
References
1. Лайнер, А. И. Производство глинозема / А. И. Лайнер, Н. И. Еремин, Ю. А. Лайнер. М.: Металлургия, 1978. 420 с.
2. Мазель, В. А. Производство глинозема / В.А. Мазель. - М.: Металлургиздат, 1955. - 430 с.
3. Клименко А.А. О возможности получения глинозема из отходов угле- и горнодобывающей промышленности методом спекания бесщелочного сырья с известняком / В.Н. Вечерко, Л.И. Кукоба, В.В. Шаповалов, В.И. Ванин // Наукові праці ДонНТУ. Серія: Хімія і хімічна технологія. 2012. Вип. 19(199). С. 151-157.
4. Патент 2197429 (РФ) C01F7/38, C01F7/14 Способ переработки алюминийсодержащего сырья / Липин В.А., Шмаргуненко А.Н., Беликов Е.А., Кузнецов А.А., Лазарев В.Г., Макаров С.Н 14.11.2000 (43). Дата публикации заявки: 27.09.2002 (45). Опубликовано: 27.01.2003.
5. Ханамирова, А. А. Глинозем и пути уменьшения содержания в нем примесей / А. А. Ханамирова / Отв. ред. И.З. Певзнер. Ереван: Изд-во АН АрмССР, 1983. 243 с
6. Томилов Н.П. Об условиях образования гидроалюмокарбонатов при взаимодействии алюминия с растворами карбонатов щелочных металлов / Н.П. Томилов, А.С. Бергер, А.И. Бойкова // Ж. нерган. химии. 1969. Т. 14, № 3. С. 674-680.
7. Абрамов, В. Я. Физико-химические основы комплексной переработки алюминиевого сырья / В.Я. Абрамов, И.В. Николаев, Г.Д. Стельмакова. - М.: Металлургия, 1985. - 288 с.