Abstract
CONTENT
- Introduction
- 1 Coal tar pitch: composition and properties
- 1.1 Composition and properties of coal tar pitch
- 1.2 Thermochemical conversion of pitch
- 2 Phisical and chemical basis of stabilizers action
- 2.1 The mechanism Irganox action
- 2.2 Methods for assessing the stabilizer effectiveness
- 3 Investigation of stabilize influense on the pitch thermal destruction and it is composites
- Conclusion
- List of references
Introduction
Creating a polymeric compositional materials (PCM) is currently regarded as the main reserve of new materials with improved properties.
The main advantage of polymer compositional materials is a unique combination of properties and the ability to manage them in the right direction by changing the composition and conditions of preparation [1].
Modification of coal tar pitch active by additives affects on the structure and properties that can be used as a modification of these polymer matrix in pitch composite.
The new composite materials a major component in pitch composites is coal tar pitch. Coal tar pitch has polymer properties that allows it to form and be part of them.
Processing of composites based on coal tar pitch is different when heated by mechanical means, so you need to study the effect of temperature on thermo-chemical transformations that occur in coal tar pitch. Considering influence of stabilizers on the thermal properties of has led to detection of a research and stabilizers pitch composite for further work were selected [2].
1 Coal tar pitch: composition and properties
1.1 Composition and properties of coal tar pitch
Coal tar pitch is a base for compositional materials, therefore for its further use for these purposes, it is necessary to explore its complex composition and different properties, as well as their changes by various factors.
The most important for technological purposes properties are pitch density, viscosity, surface tension, wettability, thermal stability, sintering and the ability to give a carbon residue. These properties of pitches with different softening temperature (from 60 to 300 °C) are not the same and are dependent on the quality of raw materials and the conditions for pitch obtaining [3].
Density of coal tar pitch obtained under analogous conditions varies with temperature softening linearly. The viscosity of the coal tar pitch, regardless of the temperature determined by the softening temperature of heating and the properties of the pitch. Pitches do not have strictly defined melting point, it replaces the softening temperature range, ie, the transition from solid to liquid.
Coal tar pitch is slightly elastic, and as the temperature of softening increases it is elasticity decreases. Regardless of the softening temperature coal tar pitch is characterized by a combination of fragility in the rapidly emerging efforts and stability in their slow action and low resistance to bending forces [4].
Pitch refers to a poor heat conductors, heat ability is also small, the pitch of the other properties that are of practical significance can be a flash point which increases with increasing softening point temperature. For medium pitches, it is 200–250 °C, and for high pitches is 360–400 °C.
Due to the complexity of chemical composition of coal tar pitch it is characterized by group composition, to study the pitch is divided into fractions. The element composition of pitch and its fractions is characterized by high carbon content and a low hydrogen content. With softening temperature increasing the carbon content of the coal tar pitch and its fractions increases markedly.
It is believed that part of pitch is a large number of structures for literature, more than 180, according to others, of the order of 5000. Identified compounds are not more than 500.
The chemical composition of the coal tar pitch by chromatography indicates a high content of polycyclic compounds that have more than four rings [5]. The chromatogram (Figure 1.1) shows the number of components in the low molecular weight of the pitch. These include quad-hydrocarbon fluoranthene, pyrene, chrysene, pyatiyadernye - benzofluoranten, perylene, Picenum; semiyaderny — a crown and a series of eight-type benzokoronena.
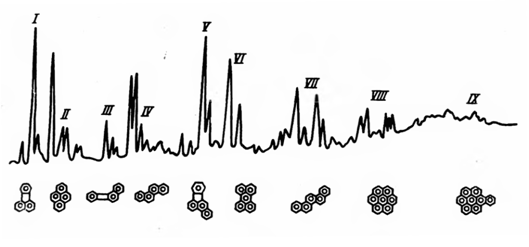
Figure 1.1 — The chromatogram of coal tar pitch: I–fluoranthene; II–pyrene; III–benzodifenilensulphid; IV–chrysene; V–benzofluorantan; VI–perylene; VII–Picenum; VIII–coronene; IX–benzokoronen
As it can be seen from the data presented the coal tar is a complex heterogeneous system of were also examined carbo-and heterocyclic compounds, various properties of coal tar pitch, and their dependence on various factors [6].
1.2 Thermochemical conversion of pitch
Composites processing based on coal tar is carried out at high temperatures, various mechanical means, so it is necessary to examine the influence of temperature and air oxidation on coal tar pitch.
Coal tar pitch is a reactive material. Under the action of temperature in the presence of oxygen flow different chemical processes, in coal tar pitch take place which lead to a change in its properties. Common to most of the work is split by thermochemical transformations process on stages: the first stage (200–400 °C), evaporation of light components, the second step (400–480 °C) associated with intensive destruction of bond at great speed, and the third step (450–550 °C) covers a polycondensation of solid and liquid products, the fourth stage corresponds to a set of processes and dehydrogenation and demethylation char above 550 °C [7].
Analysis of the literature showed that under the action of high temperature coal tar pitch, its composition and properties change and it must be considered in the processing of compositional materials based on it.
2 Phisical and chemical basis of stabilizers action
2.1 The mechanism Irganox action
As the ageing of many polymers proceeds mainly through the mechanism of radical chain reactions, when to protect them from ageing it is necessary to suppress these reactions.
To brake thermal–oxidative ageing of the polymers, antioxidants, heat stabilizers are added. The effectiveness of a heat stabilizer, the higher the less active in the development of chain reactions and more stable over time his radical is. As the heat stabilizer the Irganox-1010, which belongs to the first type of antioxidants will be used.
Irganox–1010 — an effective stabilizer of wide range of polymeric materials, various kinds of rubbers. Externally Irganox–1010 is a white or off-white crystalline powder. Non-toxic , it is allowed for use in articles that contact food, and biological organisms. Not soluble in water. Soluble in oils, toluene, acetone, ethanol partially, chlorinated solvents [8].
Compared with other antioxidants in the production Irganox–1010 has a number of advantages, such as colourless, a high oxidation efficiency, thereby reducing its massive particle in the target material, the duration of action and good compatibility with other additives.
Inhibiting oxidation process is in separately polymeric radical hydrogen atom from an antioxidant molecule AN:
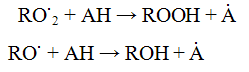
Active radicals A must be lower than the activity of the radical polymer RO, with which it interacts. However, we can not assume that the separation of hydrogen from a molecule of antioxidant — is the main mechanism of inhibition. Antioxidants may interact with other radical reactions [9].
Effect of stabilizers are well studied in relation to the polymers presented in this section. However, there is no mention in the literature data concerning effects of stabilizers on the coal tar pitch or resin compound with pitch. The aim of this work is to study the effect of polymer stabilizers on pitch composites.
2.2 Methods for assessing the stabilizer effectiveness
The stabilizers effectiveness is estimated depending on what properties of the polymers vary. The basic properties of polymers: thermal, mechanical, rheological, chemical, physical, and others.
For this work the most attention should be paid to thermal and physical properties and the method of evaluation. The main problem of many compositional materials is a change in their primary properties under the influence of temperature. Therefore, the compositional material is introduced with stabilizers that increase their ability to withstand on higher temperatures than primary without changing its structure and properties.
Methods for assessing the effects of stabilizers and many in this course project conducted research on one of them. This method is to evaluate the effect of stabilizers on the weight change of the sample during its thermal ageing at T=150 °C for different times (one, and five hours).
The change in mass is due to decomposition of components in the mixture as a consequence of thermal-oxidative processes. The lower the weight loss, the more efficient is the stabilizing effect in the antioxidant [10].
Each method shows the effect of the stabilizer on some of its properties (thermal, mechanical, rheological), due to the experimenter gets some data, fron analyzing it can be concluded if the stabilizer suitable or not and what needs to change it.
3 Investigation of stabilize influense on the pitch thermal destruction and it is composites
To study the effect of stabilizer on the thermochemical conversion of coal tar pitch components and it is composites, a series of experiments was conducted. First of all the effect of thermal ageing (at T=150 °C for 5 hours) of coal tar pitch and pitch composite with stabilizer or without it was considered. Figure 3.1 shows the data obtained.
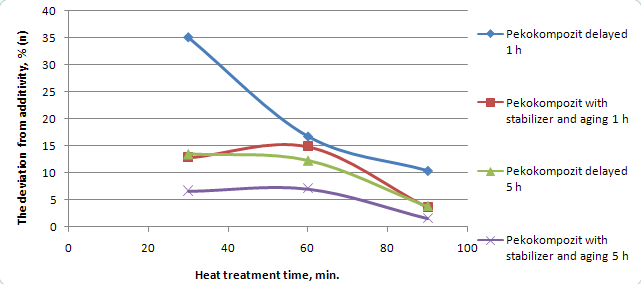
Figure 3.1 — Dependence of coal tar pitch weight loss and it is compounds from different time of heat treatment
From the obtained experimental data it is seen that the weight loss in the presence of Irganox pitch is smaller than without it. These results suggest that Irganox reacts with coal tar pitch by preventing its degradation to low molecular weight substances. However, a weight loss of pitch composite with Irganox is higher than without it, and at 90 minute thermal pretreatment is almost equal. This demonstrates the complex of physical and chemical transformations that occur in pitch composite and Irganox.
Giver pitch composite comprises PVC therefore the degree of deviation from additivity of pitch composite with stabilizer and without it, while thermal exposure times for 1 and 5 hours at T=150 °C was examined, the data calculated by the formula and are shown in Figure 3.2.
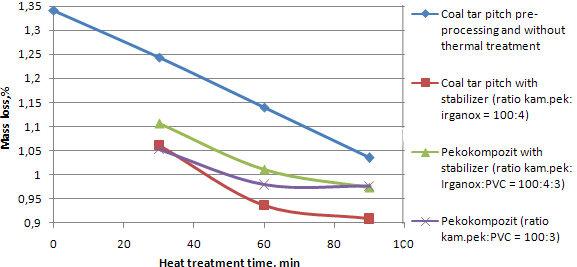
Figure 3.2 — Dependence of deviation degree additivity by in pitch composite with stabilizer and without it from heat treatment time
Analysis of the data showed that the actual weight loss in all cases is less than the losses calculated by the additivity. This indicates that the thermal treatment of pitch and pitch composites with thermochemical conversion of Irganox occur, resulting in low molecular weight substances which are distinguished. Thus, the experimental studies performed have shown that the use of only Irganox does not provide stability of the composition and properties of the pitch to the thermal influence on it, so to stabilize the complex stabilizer should be used.
Conclusion
Analysis of the data showed that the actual weight loss in all cases less than the losses calculated by the additivity. This indicates that the thermal treatment of pitch and pitch composites with thermochemical conversion of Irganox occur, resulting in low molecular weight substances which are distinguished.
To stabilize the coal tar pitch and pitch composite Irganox was used. From the obtained experimental data it is seen that the pitch weight loss in the presence of Irganox is smaller than without it.
However, a weight loss of pitch composite with Irganox is higher than of pure pitch composite. It follows that the use of only Irganox das not provide stability of composition and properties of pitch to the thermal action on it, so to stabilize the complex stabilizer should be used.
This master's work is not completed yet. Final completion: December 2013. The full text of the work and materials on the topic can be obtained from the author or his head after this date.
List of references
- Полимерные композиционные материалы (полимерные композиты, ПКМ) [Электронный ресурс]. — Режим доступа: http://p-km.ru/
- Композиты с полимерной матрицей [Электронный ресурс]. — Режим доступа: http://thesaurus.rusnano.com/...
- Основы коксования пека [Электронный ресурс]. — Режим доступа: http://bibliofond.ru/...
- Привалов В. Е. Каменноугольный пек. / В. Е. Привалов, М. А. Степаненко. — М.: «Металлургия», 1981. — 208 с.
- Лейбович Р. Е. Технология коксохимического производства : учебник [для техникумов] / Р. Е. Лейбович, Е. И. Яковлева, А. Б. Филатов. Изд. 3–е., доп. и перераб. — М.: «Металлургия», 1982. — 360 с.
- Власов С. В. Основытехнологиипереработкипластмасс: учебник [для вузов]/ С.В. Власов, Л.Б.Кандырин, В.Н. Кулезнев. — М.: Химия, 2004. — 600 с. : ил.
- Барамбойм Н.К. Физика и химия полимерных материалов обувного производства: учебник [для вузов] / Н. К. Барамбойм, В. В. Анохин. — К.: 1961. — 250 с.
- Irganox 1010 [Электронный ресурс]. — Режим доступа: http://www.telko.com/...
- Николаев А.Ф . Технология полимерных материалов. — К.: 2008. — 300 с.
- Метод определения температуры размягчения термопластов по Вика. ГОСТ 15088–83 [Электронный ресурс]. – Режим доступа: http://vsegost.com/...
- Композиты с полимерной матрицей [Электронный ресурс]. — Режим доступа: http://thesaurus.rusnano.com/...