Abstract
Content
- Introduction
- 1. Relevance of the topic
- 2. The purpose and objectives of the research, the expected results
- 3. Determining the degree of influence of the imbalance in the range of power characteristics of the grinding process
- Findings
- List of sources
Introduction
Scientific and technological progress and the associated increase in demand for high-tech engineering products - are forcing manufacturers to look for new materials with higher figures for resistance to chemicals, heat resistance, wear resistance, corrosion resistance and other properties of the material, depending on the application product to be made [1].
As these new materials are increasingly used, and non-metallic composite materials, in particular, various kinds of engineering ceramics.
Ceramic materials favorably from metal and polymer by the following properties: versatility, availability of raw materials, production of low energy, high corrosion resistance and resistance to radiation damage, biocompatibility, low density.
These are promising materials for the manufacture of tool parts of internal combustion engines, filters, membranes with different bandwidth, abrasion-resistant coatings, the heating elements. Products made of technical ceramics used in instrument, nuclear energy, aircraft, space technology and in general engineering.
In engineering, the interest in ceramics based on its high-temperature strength and creep resistance. Ceramics based on silicon nitride, silicon carbide and zirconium dioxide used in diesel and gas turbine engines. Fully ceramic engine running at very high temperatures successfully tested in vitro [2].
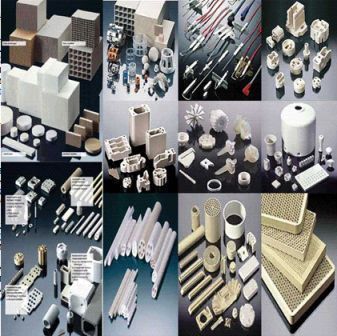
Figure 1 – Articles of technical ceramics
Industrial ceramics widely used at normal temperatures in circumstances requiring the material hardness, resistance to abrasion and strength. Of silicon carbide and alumina ceramic seals are manufactured pumps and valve components that are subject to abrasive action of suspensions and liquids. Tool with a cutting edge of alumina ceramics in many areas of metalworking tool change based on tungsten carbide. Solid, durable ceramic silicon nitrite sialonovoy group was developed for specialized applications such as high-speed machining cutting nickel alloys and cast iron pipe rolling and cutting carbon. There is a widespread demand for ceramic materials for the guide of good mechanical characteristics.
However, ceramics and several inherent disadvantages, including sensitivity to thermal shocks (especially hypothermia), fragility, low tensile strength and complexity of the machining is due to the hardness and brittleness of ceramics and leads to defects in the surface layer in the form of chips and microcracks.
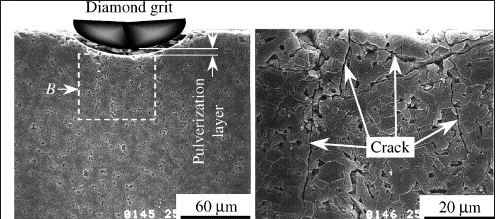
Figure 2 – Education chips and cracks in the surface layer of technical ceramic products for grinding.
There are a large number of high-precision processing techniques of ceramic materials, such as ultrasound, laser, physical-chemical and other processing methods.
The most commonly used method for processing of ceramic products is the diamond grinding, which is associated with the need to remove large allowances received because of imperfect technology blanks. Therefore, the input parameters of the grinding process to a large extent on the quality of the resulting surface and the depth of the defect layer. Therefore, improving the processing methods of ceramics associated with the study of complex multi-factor of the grinding process and its impact on the performance of the products [3].
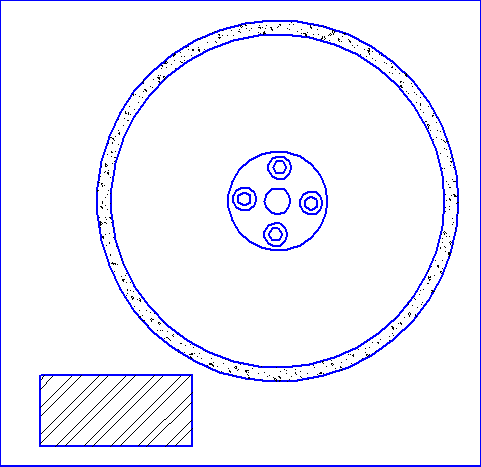
Figure 3 – An animated example of the process of surface grinding of ceramics (8 images, 6 shots, 51 kb)
1.Relevance of the topic
The theme of master's work is: "The influence of vibration on the formation of a defect layer in surface grinding of ceramics using a test bench based on the 3672 machine for the measurement of vibration parameters." The presence of the defective or cracked layer is characteristic of all kinds of abrasive machining brittle materials (loose abrasive grinding, abrasive and diamond wheels, mechanical polishing).
The depth of the defect layer is dependent on the intensity of the processes of dispersion, decreasing from rough to finish machining operations. In this defective layer formed radically affect the performance properties of the products from brittle materials, primarily for strength.
Imperfections technological processes, accompanied by the appearance of vibrations in the cutting, in conjunction with increased dynamic impact force onto the surface (especially on rough grinding operations) give rise to a defect of the surface of the developed layer. Its depth of penetration can reach more than 300 m, which adversely affects the complexity of the subsequent finishing operations, and in the case of incomplete removal of defects may be associated with the destruction of products exploitation.
The relevance of the subject is stated that to ensure the performance characteristics of products need to be clear about the impact of the input parameters of the process, as well as the phenomena that occur in the processing of products (eg vibration) on the performance of defects, especially the structure and depth of impaired treating layer
2. The purpose and objectives of the research, the expected results
The purpose of the master's work is to identify the effect of vibrations that occur in the machine-tool-tool for grinding brittle nonmetallic materials on cutting forces and surface quality (its defectiveness).
The main objectives of the study:
- Based on the analysis of the technological system grinding to establish the cause of vibration grinding brittle non-metallic materials;
- To carry out pilot studies and to determine the effect of imbalance on the circle cutting forces in the glass-ceramic processing scheme ostrozatochennym flat plunge grinding wheel.
The result of the master's work should be recommendations on the number of rational cutting grinding brittle non-metallic materials.
3. Determining the degree of influence of the imbalance in the range of power characteristics of the grinding process
In the course of the master's works have been carried out experimental studies related to the determination of the cutting forces when grinding samples of composite glass-ceramic-defective AS-418, first of all, the normal component of the cutting force, which measures the intensity of the defect layer and depends on the parameters of the mode of grinding in a different the degree of imbalance of the grinding wheel.
Grinding was carried out by varying the parameters of the cutting conditions: speed range Vk = (34, 23.7) m / s velocity of the sample Vd = (1,1; 6,0) m / min cutting depth t = (0,1; 0.4) mm in the implementation of the scheme of flat plunge grinding on the stand, mounted on the base of the machine model 3672. The samples were treated in a different level of dynamic disturbances on the system of cuts. The machine is equipped with a system for measuring and detecting components of the grinding force. A complete measuring system consists of: a table torque, low-frequency amplifier model 8UN4, recorder H33S-4. As a cutting tool used in diamond circles IAI 250x76x20x3 AS6 315/250 - 4 - M2-01. To maintain the cutting ability of the instrument during the experiment was carried out at the same level of his dressing loose abrasive.
The phenomenon of imbalance range ensured by using the normalized load weight mounted on the end surface of the grinding wheel, and an offset relative to the axis of the latter. The presence of imbalance is accompanied by centrifugal force Rd, the value of which was adjusted by changing the weight of the cargo. During the experiment, the value of Pд chose to be, respectively, 10, 25 and 50 Н.
Studies have shown that by increasing the centrifugal force (of unbalance of the circle) changes the values of the normal component of the cutting force (Figure 4). The average value of the normal component of the cutting force can both increase with increasing imbalance or fall. Moreover, this phenomenon is more clearly seen in the intensive treatment regimens (high velocities detail and depth of cut) - curves 1 and 2
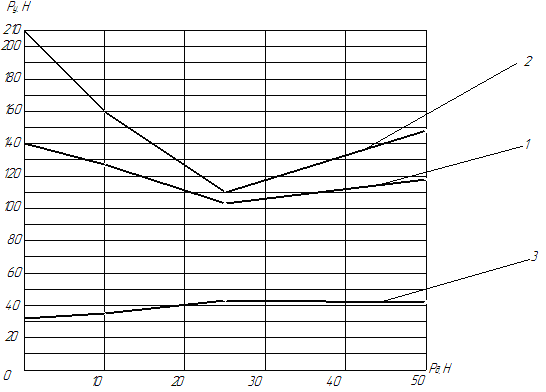
Figure 4 – Еffect of the centrifugal force to change Pд normal component force Py in the cutting plane with a plunge grinding mode 1 - Vk = 34 m / c, Vд = 6 m / min, t = 0,4 mm 2 - Vk = 23.7 m / c, Vd = 6 m / min, t = 0,4 mm, 3 - Vk = 34 m / c, Vd = 1,1 m / min, t = 0,1 mm
The intensification of the cutting results in an increase of energy coming into the contact zone of the circle and the sample, resulting in a change of the conditions of the defect layer in the glass-ceramics, which will affect the quality of the forming surface.
Findings
In the course of the master's work, carried out experimental research, which resulted in the acquired and analyzed force characteristics of the glass-ceramic grinding process with varying degrees of imbalance of diamond tools. It was found that the intensity of the vibrations caused by the unbalance circle has an effect on the level of the cutting forces and, as a consequence, cause changes in the structure and the depth of the defect, treatment of impaired product layer. The obtained data allow us to establish the most favorable combination of parameters of the treatment regime and the state of the grinding tool on the basis of ensuring the required quality of the machined surface.
In writing this essay master's work is not yet complete. Final completion: December 2013. Full text of the work and materials on the topic can be obtained from the author or his manager after that date.
List of references
1. Гусев В.В. Обеспечение эксплуатационных характеристик изделий из конструкционной керамики на стадии их производства / В.В Гусев, Л.П. Калафатова // Сучасні технології у машинобудуванні: Зб. наук. статей/ За заг. ред. А.І. Грабченка. – Том 2. – Харків: НТУ «ХПІ», 2006. – С. 334-346.
2. Гусев В.В. Влияние виброустойчивости системы шлифования на структуру дефектного слоя ситал лов / В.В. Гусев, Л.П. Калафатова, Д.В. Поколенко // Резание и инструмент в технологических системах. - 2006. - Вып. 70.– С. 154-161.
3.Гусев В.В. Обеспечение эксплуатационных характеристик изделий из технической керамики : монография / В.В Гусев, Л.П. Калафатова - Донецк ГВУЗ "ДонНТУ", 2012. - 250 с.
4.Капанец Э.Ф. Точность обработки при шлифовании / Э.Ф Капанец, К.К. Кузьмич, В.И. Прибыльскийи др.; под ред. П.И. Ящерицына. – Мн.: Наука и техника, 1987. – 152 с.
5.Гусев В.В. Исследование динамических характеристик элементов системы СПИД при шлифовании деталей сложной пространственной формы из ситаллов / В.В. Гусев, Л.П. Калафатова, И.С. Каракуц // Надійність інструменту та оптимізація технологічних систем. Збірник наукових праць. – Краматорск, 2007. – Вип. №21. – С. 148 – 155.
6. Якушев Н.З. Коническая оболочка под действием подвижных нагрузок / Якушев Н. З., Якушев Р. С. // Исследования по теории пластин и оболочек. - Казань: Изд-во Казанского ун-та, 1975. - С. 303 - 316.
7. Гусев В.В. Обоснование расчетной схемы для исследования динамического состояния технологической системы алмазно-абразивной обработки тонкостенных оболочек из ситалла / Гусев В.В., Калафатова Л.П., Олейник С.Ю. // Сучасні технології в машинобудуванні. - Харьков: Изд-во НТУ "ХПИ", 2011. - С. 14-23.