Реферат по теме выпускной работы
Реферат носит предварительный характер, поскольку время его составления – март-апрель 2013г., тогда как защита магистерской диссертации запланирована на январь 2014г.
Содержание
- Актуальность заявленной темы
- 1. Цель, методы и задачи исследования
- 2. Анализ современного состояния вопросов исследования
- 2.1 Анализ технологичности изделий для автоматизации сборочных процессов узлов пневмо- и гидроаппаратуры.
- 2.2 Анализ существующих методов автоматической сборки цилиндрических изделий с зазором
- 2.3 Анализ существующих методик проектирования технологических процессов автоматической сборки
- 3. Практическое значение
- 4. Научная новизна полученных результатов
- Выводы
- Список источников
- 2.2 Анализ существующих методов автоматической сборки цилиндрических изделий с зазором
Актуальность заявленной темы.
Доля сборочных работ в общем объеме машиностроительного производства колеблется в пределах от 25 до 40%, а в отрасли приборостроения достигает 70%. В опытном производстве эти показатели возрастают вдвое.
Но даже при столь высоких значениях трудоемкости удельный вес общих капиталовложений в сборочное производство составляет всего 5..10% от общей массы. По причине такой стратегии автоматизация сборочных операций всё еще недостаточно распространена: на сегодняшний день в машиностроении механизировано 25..30% сборочных работ, а автоматизировано – около 5%.
Препятствиями на пути автоматизации сборочных работ могут стать:
- технологическая неотработанность конструкции;
- недостаточный уровень унификации сборочных единиц;
- невысокое качество деталей;
- потребность в спецоснастке;
- недостатки сборочного оборудования;
- общая дороговизна проекта.
Целый ряд вышеперечисленных проблем автоматически решается при рассмотрении вопроса автоматизации сборки пневмо- и гидроаппаратуры. Узлы подобного плана имеют ряд особенностей:
- общие стандарты конструкций выпускаемой номенклатуры;
- достаточно прочные и жесткие детали;
- подавляющее большинство соединений – цилиндрические соединения с зазором;
- унификация размеров посадочных поверхностей;
- малые габаритные размеры отдельных деталей, узлов и изделий в целом;
- последовательная сборка с удобными базовыми поверхностями.
Отдельным, немаловажным достоинством узлов пневмо- и гидроаппаратуры следует назвать достаточно малый объем собираемых деталей.
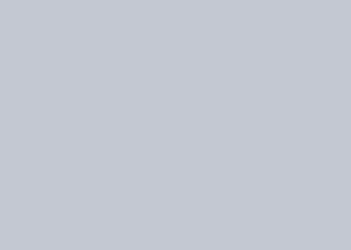
Рисунок 1 - Визуализация последовательного процесса сборки простейшего гидроузла (клапан шариковый).
Изображение сборки выполнено в программной среде 3D-моделирования SolidWorks.
Анимация состоит из 27 кадров с задержкой в 0,5 с на ключевых кадрах изображения узла и без задежки - между всеми остальными кадрами.
Количество воспроизведений неограничено.
На основании вышеизложенного можно делать предварительные выводы об актуальности развития вопроса частичной или даже комплексной автоматизации сборки узлов пневмо- и гидроаппаратуры. Это позволит в значительной мере снизить общую трудоемкость изготовления подобной продукции, обеспечить стабильный выпуск и повысить общий уровень технической подготовки производства.
1. Цель, методы и задачи исследования.
Цель магистерской работы - повышение производительности сборки узлов пневмо- и гидроаппаратуры за счет автоматизации сборочных процессов.
Для реализации поставленной цели требуется решить следующие задачи:
- Выполнить анализ современного состояния вопроса автоматизации сборочных процессов узлов пневмо- и гидроаппаратуры.
- Провести синтез существующих сборочных технологических процессов для условий автоматизации.
- Разработать математическую модель сборочных процессов узлов пневмо- и гидроаппаратуры для последующей оптимизации технологических процессов сборки по различным критериям.
- Провести экспериментальные исследования сборки гладких цилиндрических соединений с гарантированным зазором под воздействием колебаний, передаваемых базовой детали вдоль оси сборки.
- Получить эмперико-статистическую зависимость влияния рассматриваемых факторов (частота вибрации, форма заходной части собираемых изделий, угол относительного наклона друг к другу) на время сборки.
- Разработать рекомендации по повышению уровня автоматизации сборочных процессов узлов пневмо- и гидроаппаратуры
Объект исследования – цилиндрические соединения с зазором, используемые в узлах пневмо- и гидроаппаратуры.
Предмет исследования - технологический процесс сборки изделий, а также характерные особенности осуществления процессов сборки соединений и узлов пневмо- и гидроаппаратуры в условиях современных машиностроительных производств.
В качестве методов исследования были выбраны и задействованы: теория графов, алгебра множеств, алгебра логики, методы статистической обработки экспериментальных данных и теория планирования эксперимента.
2. Анализ современного состояния вопросов исследования
Общий спектр вопросов, посвященных автоматизации сборочных процессов в машиностроении, можно условно разделить на несколько категорий:
- Теоретические основы автоматизации сборки;
- Оценка точности и надежности автоматизированной сборки, включая комплексный показатель качества;
- Рассмотрение механики, динамики и прочих характеристик процесса автоматизированной и автоматической сборки;
- Конструирование, адаптация и эксплуатация автоматического сборочного оборудования (отдельные сборочные автоматы, гибкие автоматизированные линии сборки, автоматические линии сборки, автоматические сборочные системы);
- Моделирование сборочных процессов и автоматизация их проектирования.
Соответственно подобной классификации можно более подробно и систематично рассмотреть современное состояние вопроса повышения уровня автоматизации сборки узлов пневмо- и гидрооборудования.
Среди основных теоретических вопросов, затрагиваемых при решении вопроса автоматизации сборочных процессов, необходимо назвать:
- выбор метода достижения точности замыкающего звена и разрешение размерных цепей при сборке;
- оценка технологичности конструкции изделия на всех уровнях сборки – технологичность конечного продукта, сборочных узлов, деталей, комплектующих и т.д.;
- определение и анализ пространственных взаимосвязей элементов сборочной единицы;
- определение условий собираемости соединений;
- разработка рациональных технологических процессов сборки;
- поиск и оценка вариантов последовательности осуществления каждого этапа технологического процесса сборки;
Под методом сборки изделия подразумевают совокупность правил достижения заданной точности замыкающего звена размерной цепи. Достигаемая в процессе сборки точность должна обеспечивать соответствие значений параметров изделия заданным в конструкторской документации. Обеспечение заданной точности сборки путем использования наиболее экономичных методов сборки достигается на основе расчета и анализа сборочных размерных цепей, с помощью которых определяется точность относительного расположения поверхностей или осей деталей, входящих в состав сборочной единицы [1].
Для достижения заданной точности замыкающего звена размерной цепи используется пять различных методов: метод полной взаимозаменяемости, метод неполной взаимозаменяемости, метод групповой взаимозаменяемости (селективная сборка), метод регулирования и метод пригонки. Для целей сборочного производства с высокой степенью автоматизации наиболее подходят первые два метода. Разумеется, комплексной или частичной автоматизации могут быть подвергнуты технологические процессы сборки по любому из вышеперечисленных методов, но максимальную простоту организации и удобство контроля за системой технологического сборочного оборудования дают только методы полной и неполной взаимозаменяемости.
Лебедовский М.С. в своих научных трудах требовал выдерживания основополагающего, с его точки зрения, принципа повышения уровня автоматизации сборочных процессов: анализ и синтез технологической системы автоматической сборки должен выполняться как для единого и неразрывного звена комплекта «изделие – технология – машина» [2]. Подобный подход можно расценивать как основу для возможности переоценки проектирования технологических процессов сборки с точки зрения функционально-ориентированного производства – методики нового поколения в машиностроении.
Балакшиным Б.С. неоднократно поднимался вопрос влияния возникающих упругих деформаций на протекание технологического процесса и конечное качество собранного узла. Подобный фактор может быть одним из наиболее значимых при возникновении геометрических погрешностей сборки, которые, в свою очередь, могут впоследствии привести к возникновению избыточных деформаций изгиба, кручения и других, значительно снижающих общие показатели качества сборочного узла и работоспособность изделия в целом. Угроза возникновения упругих деформаций деталей может быть крупномасштабной проблемой качества сборки в том случае, если отдельные детали и узлы отличаются низкой жесткостью и неудобством базирования, что не позволяет в необходимой мере надежно произвести их относительное ориентирование и соединение [3].
Косилов В.В. в сфере теоретического обоснования возможности и актуальности автоматизации сборочных процессов в машиностроении опирался на требования к высокой технологичности собираемых изделий – на уровнях сборки и узлов, и конечного изделия. Удобство ориентирования и базирования деталей в процессе сборки, считал он, является едва ли не основным фактором среди критериев автоматизации. Вторым наиболее значимым фактором, логично зависимым и от технологичности сборочных единиц, и от их базирования в процессе сборки, Косилов В.В. называл соблюдения условий собираемости, определяемых геометрическими и силовыми характеристиками соединений [4].
Реализация процессов автоматизации сборки с точки зрения кинематики должна быть максимально простой, обеспечивающей минимальное количество движений для достижения необходимых точности и надежности заданных соединений. В вопросах автоматизации сборочных процессов следует производить переоценку устоявшихся классических методов реализации различного рода соединений и искать новые, более экономичные и производительные решения. Это требует нестандартного подхода к решению задач кинематики процесса и планового ухода от привычных механизмов сборки изделий в машиностроении.
Вопросами поиска новых, прогрессивных решений в области автоматизации сборочных процессов различного типа и сложности, занимались такие авторы, как А.А. Гусев, М.Г. Кристаль, З.С. Корсаков, М.Н. Бабушкин, В.Н. Жомиру, В.М. Бедрин и А.В. Бедрина, Д.М. Левчук, А.В. Воронин, К.Н. Муценек, В.А. Яхимович и другие. Среди рассматриваемых направлений особенный интерес в машиностроении имела тема применения вспомогательных вибраций при манипулировании компонентами сборки, сборка во вращающемся потоке газов, сборка с нестандартными траекториями перемещения деталей, сборка с применением действия магнитных потоков и другие.
Вопросом моделирования сборочных процессов с целью упрощения поиска оптимальных решений протекания и организации технологии для непосредственной автоматизации сборки посвящены труды таких авторов, как Вавилов А.А., Кузьмин В.В., Павлов П.Г., Схиртладзе А.Г., Тимченко А.А. и других. В их работах основное внимание уделялось разработке методик формализации описания технологических процессов сборки, структурного анализа и синтеза их моделей, решению вопросов автоматизации сборочных операций.
Неоднократно заострял внимание на предложении использовать метод моделирования процессов сборки на основе теории графов Лебедовский М.С. Особенно актуальным, считал он, этот метод может стать для проектирования алгоритмов работы автоматического сборочного оборудования. Такие авторы, как Достанко А.П., Стариков В.Ш., Попов Е.П. и Цыпкина Я.З., работали над темой исследования сборочных систем различного рода с дискретным управлением и формализацией структур. Отдельные научные работы были посвящены теме математических моделей сборочных процессов с использованием методов распознавания образов (Чимитов П.Е.) и применения логико-динамических графов для структурирования и анализа технологических маршрутов сборки (Жигалев Н.Н.).
Существенный вклад в развитие вопроса автоматизации сборочных процессов внесли научные коллективы таких организаций, как: Московский авиационный институт (МАИ), Московский государственный технический университет имени Н.Э. Баумана, Московский государственный технологический университет «Станкин», Московский государственный технический университет «МАМИ», научно-исследовательский институт технологии автомобильной промышленности, научно-исследовательский институт технологии тракторного и сельскохозяйственного машиностроения и другие.
2.1 Анализ технологичности изделий для автоматизации сборочных процессов узлов пневмо- и гидроаппаратуры.
Технологическая рациональность конструкции изделия (ТРКИ) определяется совокупностью свойств изделия, которые выражают его технологичность с точки зрения соответствия принятых конструктивных решений условиям производства, эксплуатации и ремонта. ТРКИ обеспечивается за счет применения методов:
- блочно-модульного построения систем и устройств;
- агрегатирования составных частей;
- оптимизации выбора и назначения конструктивных элементов деталей и материалов, размерного анализа конструктивных исполнений деталей и сборочных единиц;
- функционально-стоимостного анализа изделия и его составных частей;
- экономико-математического моделирования взаимосвязей основных функциональных и конструктивно-технологических характеристик изделия [1].
Стратегия производства в плане повышения серийности выпуска изделий и комплексной или частичной автоматизации сборочных процессов неумолимо влечет за собой возрастание и ужесточение требований к технологичности конструкции изделия.
Повышение уровня технологичности конструкции изделия достигается на основе проведения технологического анализа и отработки конструкции изделия на технологичность. Технологический анализ конструкции изделия в сборке – анализ конструкции изделия с целью применения технологического процесса сборки, обеспечивающего выполнение программы выпуска изделий заданного качества в установленных условиях производства. Отработка конструкции изделия на технологичность – комплекс мероприятий, проводимых на всех этапах разработки изделия, с целью достижения оптимального заданного уровня технологичности. Отработка конструкции изделия на технологичность должна проводиться на всех стадиях разработки конструкторской документации [1].
При автоматизации сборочных процессов технологичность конструкции изделия и его составных частей должна соответствовать особенностям выполнения автоматической сборки с применением наиболее простых и эффективных средств автоматизации, т.е. требования к технологичности должны разрабатываться с учетом максимального упрощения сборки и беспрепятственной реализации всех составляющих этапов и элементов процесса автоматической сборки [5].
Основные требования к технологичности конструкции изделия и его компонентов для условия автоматизированной и автоматической сборки можно сформулировать в перечне рекомендаций:
- Конструкция изделий, структура которых включает в себя большое количество компонентов, должна строиться согласно модульному принципу. Это подразумевает преднамеренное расчленение изделия на рациональное число самостоятельных узлов с целью обеспечения возможности их параллельной сборки, испытаний, балансировки, контроля и т.д.
- Конструкция изделия должна исключать необходимость промежуточных разборки и повторной сборки на определенных стадиях технологического процесса. Выполнение сборочных работ должно состоять из ряда последовательных законченных этапов, по результатам которых получают готовый узел, перемещаемый на следующий этап.
- Изделие должно состоять из минимального числа деталей, при этом предпочтение должно отдаваться деталям простых форм.
- Изделие должно состоять из максимально возможного числа стандартных и унифицированных компонентов.
- Конструкция изделия должна предусматривать удобные и надежные технологические базы, использование которых позволит максимально упростить механику манипулирования на сборочной позиции и даст возможность достигнуть необходимых показателей точности сборки.
- В конструкции изделия должна быть предусмотрена базовая составная часть, роль которой будет созвучна роли основы для установки остальных компонентов. В процессе сборки перемещение и смена положения базовой детали должны быть сведены к минимуму и в идеале – исключены вовсе.
- Каждый составной элемент сборки должен иметь минимальное число поверхностей и точек сопряжения с другими частями изделия.
- При разработке конструкции изделия и планировке размерных цепей, определяющих относительное положение и связи компонентов в готовом изделии, следует придерживаться наиболее точных методов достижения точности замыкающего звена – метода полной и неполной взаимозаменяемости.
- Следует избегать многозвенных размерных цепей в конструкции собираемого изделия и его узлов, что может значительно усложнить процесс достижения необходимой точности сборки, а также затрудняет саму механику сборки сборочной единицы.
- При разработке конструкции изделия следует минимизировать вариацию типов сопряжения поверхностей и соединений деталей, отдавая предпочтение тем типам, что механика выполнения которых наиболее проста при осуществлении в автоматическом цикле.
- Конструкция изделия и его компонентов должна обеспечивать свободный доступ рабочих органов сборочного оборудования, инструментов и средств контроля.
- Изделия и его компоненты должны иметь удобные поверхности для возможности захвата и манипулирования в автоматическом режиме.
- Конструкция изделия должна обеспечивать сборку при минимальном числе направлений сборки. Наиболее предпочтительным должен быть вариант одного направления сборки, что в максимальной мере упрощает организацию сборочного процесса и конструкцию оборудования.
- Закономерным развитием предыдущей рекомендации будет адаптация конструкции изделия для сборки в автоматическом цикле с тем расчетом, что все сопряжения и соединения деталей выполняются применением простейшей кинематики движений.
- Изделие и его составные элементы должны обладать необходимой долей устойчивости и способностью к складированию и перемещению.
- Сборочные единицы должны быть кинематически замкнутыми, т.е. обеспечивать ориентирование, перемещение и манипулирование без возможности расчленения на составные элементы.
На сегодняшний момент высокое значение уделяется как необходимости проведения тщательной оценки изделия на технологичность конструкции и адаптацию к условиям автоматической сборки, так и методикам этой оценки.
Существующие методы определения оценки технологичности конструкции изделия с точки зрения возможной автоматизации сборочных процессов базируются на субъективной оценке. На сегодняшний момент разрабатываются методики автоматизированной оценки технологичности, основывающиеся на принципах абстрагирования, дифференцирования, сопоставления рассматриваемых объектов с аналогами из имеющихся баз данных, а также математической обработке результатов. Оценка изделия на технологичность конструкции и адаптированность к условиям автоматической сборки при своей высокой трудоемкости также требует ответственности и компетентности экспертных лиц. Как показывает практика, именно на стадии разработки предварительного проекта и оценки его перспектив допускается наибольшее количество ошибок и именно на начальном этапе работы можно свести к минимуму возможности возникновения проблем при реализации проекта. Автоматизация оценки технологической подготовленности изделия к условиям автоматической сборки позволяет исключить субъективный человеческий фактор и максимально точно оценить максимально возможный и экономически обоснованный необходимый уровень автоматизации производственных процессов.
Из известных в настоящее время методов оценки изделия на технологичность конструкции следует упомянуть методику А.Г. Холодковой (Московский государственный открытый университет) и полностью автоматизированный проект программного обеспечения B. Reifur (Вроцлавский технический университет).
2.2 Анализ существующих методов автоматической сборки цилиндрических изделий с зазором
Сборка гладких цилиндрических соединений с гарантированным зазором в большинстве случаев легко подвергается автоматизации. Такие соединения можно собирать под действием силы тяжести присоединяемой детали и принудительным (силовым) методом.
Сборка под действием силы тяжести возможно при вертикальном расположении осей сопрягаемых деталей или положении, близком к вертикальному (отклонение от вертикали не более 10..15о), а также при значительных зазорах в соединении (в десятых долях миллиметра), массе и размерах деталей (не менее 0,05 кг и диаметром не менее 10 мм). Однако соединение деталей под действием гравитационных сил может не обеспечивать высокой надежности процесса, особенно при сборке относительно легких деталей и значительном суммарном смещении осей относительно друг друга [5].
При автоматической сборке цилиндрических деталей чаще всего используется схема, в которой ориентация собираемых деталей на сборочной позиции осуществляется по их наружным поверхностям в призмах. В начале цикла автоматической сборки ось присоединяемой детали может занимать различные положения по отношению к оси базовой, при этом оси деталей могут находиться в одной или разных плоскостях. К наиболее простым для реализации схемам сборки относятся такие, в которых отсутствуют движения, необходимые для совмещения осей собираемых деталей [1].
Для автоматического сопряжения цилиндрических деталей зачастую используют устройства, которые сообщают одной из сопрягаемых деталей относительное вращение движения. Вращающийся ловитель передает движение присоединяемой детали таким образом, что она в определенный момент времени занимает относительно базовой такое положение, при котором дальнейший процесс сборки гарантируется. По своей физической сущности параметры, определяющие безотказность сборочного процесса, можно отнести к следующим группам.
Конструктивные параметры (зазор в соединении, номинальный диаметр соединения, суммарный размер радиальных катетов фасок на сопрягаемых поверхностях, длина соединения). Параметры исполнительного механизма (зазор между ловителем и присоединяемой деталью, расстояние между торцами ловителей, жесткость ловителя). Режимы сборочного процесса (величины усилия сборки, скорость сборочного движения, угловая скорость ловителя) [7].
Эффективная высокопроизводительная автоматическая сборка возможна только при значительной безотказности устройств автоматизации. Наибольшая доля отказов автоматической сборки цилиндрических соединений происходит при прохождении сопрягаемыми поверхностями зоны фасок или кромок из-за того, что погрешность взаимного ориентирования этих поверхностей больше допустимой для применяемого типа сборочного устройства.
В способе автоматической сборки, предложенном специалистами Киевского политехнического университета, самоориентация сопрягаемых цилиндрических поверхностей происходит под действием силы, точка приложения которой перемещается по концентрической окружности на торце присоединяемой втулки, установленной в податливом приспособлении, при контакте с неподвижно установленным валом. Если втулка и вал соприкасаются торцами при некотором смещении осей сопрягаемых поверхностей, то сила, приложенная в определенной зоне на внешнем торце втулки, вызывает ее поворот вокруг оси, проходящей через две точки контакта кромок сопрягаемых поверхностей, и перемещение контактирующего с валом торца в сторону уменьшения эксцентриситета до касания кромки втулки и образующей вала в третьей точке. Возможен захват кромок, препятствующий возврату втулки в исходное положение и обусловливающий второй этап самоориентации, заключающийся в том, что точки касания кромок сопрягаемых поверхностей сближаются, пока не сольются в одну точку. При этом постепенно уменьшается перекос оси втулки и к концу второго этапа ее ось совмещается с осью вала. Перемещения самоориентации сопрягаемых поверхностей заканчиваются, и происходит сборка [8].
На сегодняшний день разработана методика высокопроизводительной сборки цилиндрических соединений с гарантированным зазором для условий непрерывного автоматического цикла технологического процесса. Сущность метода заключается в том, что в зоне сборки располагают плоские базирующие элементы, совершающие в плоскости, перпендикулярной направлению транспортирования валика и втулки, возвратно-поступательное движение по заданному закону. Движение каждого элемента сдвинуто относительно предыдущего на некоторый фазовый угол таким образом, что в конкретный момент времени у части базовых элементов скорость больше нуля, меньше нуля или равна нулю. Плоскость, касательная к базирующим поверхностям элементов, скорости которых положительны, образует с плоскостью, касательной к сопряженным с рассмотренными элементам, кинематическую призму, обеспечивающую аэрирование и транспортирование деталей. Ступенчатый профиль базирующих элементов позволяет соосно базировать сопрягаемые детали с разными диаметрами базовых поверхностей. Многократное повторение цикла возвратно-поступательного движения через заданный период времени приводит к формированию в зоне сборки ряда кинематических призм, отстоящих друг от друга на постоянный шаг. Постоянство шага между сборочными комплектами приближает потоки деталей к регулярным. Вследствие действия сил трения между базовыми поверхностями сборочного комплекта наблюдается их вращательное движение. Так как диаметры базовых поверхностей различны, то разность угловых скоростей валика и втулки обуславливает относительное вращение сопрягаемых поверхностей. Наличие эксцентриситета между сопрягаемой и базовой поверхностью втулки приводит к относительному сканированию осей деталей в результате совместного вращательно-вибрационного воздействия. При контакте торцов сопрягаемых поверхностей их относительное перемещение за счет вибрации и вращения приводит к снижению сил трения в направлении действия усилия сборки. Следовательно, улучшаются условия самоориентирования деталей [9].
Рассмотрением вопросов, связанных с автоматизацией процессов сборки подвижных цилиндрических соединений, в разное время занимались такие авторы, как А.В. Воронин, М.М. Стржемечный, Е.В. Писарев, А.Г. Холодкова, Е.И. Кольчугин, В.М. Похмельных, Т.Ю. Родивилина и другие.
2.3 Анализ существующих методик проектирования технологических процессов автоматической сборки
Технологический процесс сборки включает в себя перечень необходимых действий по установке и структурированному образованию соединений из составных компонентов изделия в заданной последовательности. Технологический процесс сборки может состоять из одной (однооперационный) или связанного множества (многооперационный) операций сборки.
Классическая последовательность проектирования технологического процесса сборки включает в себя ряд этапов:
- Анализ исходных данных.
- Задание граничных условий.
- Выбор организационной формы сборки.
- Оценка технологичности конструкции изделия.
- Проведение размерного анализа конструкции изделия.
- Выбор технологических баз и схем базирования.
- Поиск рациональных методов сборки соединений.
- Оценка технологических возможностей цеха и подбор оборудования и оснастки.
- Составление маршрутного технологического процесса сборки.
- Уточнение технологических операций сборки.
- Нормирование.
- Расчет экономической эффективности рассматриваемых вариантов технологического процесса сборки, выбор наиболее предпочтительного.
- Оформление сопроводительной документации.
Проектирование технологического процесса сборки должно завершиться перечнем задокументированных результатов. Как то:
- технологическая схема сборки;
- пакет технологических карт сборки;
- пакет технологических карт контроля;
- пакет технологических инструкций.
Схема сборки представляет собой графический документ последовательности сборки оригинальных, нормальных, покупных деталей в узлах и последовательность сборки комплектов и узлов. Такие схемы позволяют ускорить освоение сборки и комплектование ее деталями, комплектами и узлами [12].
Каждый составной элемент изделия изображается на схеме в виде прямоугольника, разделенного на три части: в верхней части дано наименование элемента; в левой нижний – числовой индекс элемента по спецификации; в правой нижней – число элементов, входящих в данное соединение. Технологические схемы сборки снабжают надписями-сносками, поясняющими характер сборочных работ, когда они неясны из схемы [13].
В основу разработки технологических процессов автоматической сборки положены два принципы: технический и экономический. В соответствии с техническим принципом спроектированный технологический процесс автоматической сборки должен полностью обеспечивать выполнение всех требований рабочего чертежа и ТУ приемки изделия. В соответствие с экономическим принципом сборку изделия нужно вести с минимальными затратами овеществленного и живого труда и с минимальными издержками производства [15].
Важным условием разработки рационального технологического процесса автоматизированной сборки является унификация и нормализация соединений, т.е. приведение их к определенной номенклатуре видов и точностей. На основе унификации и нормализации соединений в сборочных единицах и изделиях разрабатывают типовые сборочные процессы, операции и переходы, выполняемые на типовом сборочном оборудовании с использованием типовых инструментов и приспособлений [14].
Процесс проектирования технологических процессов автоматической сборки состоит из комплекса взаимосвязанных и выполняемых в определенной последовательности этапов:
- Сбор и анализ исходных данных.
- Отработка изделия на технологичность под условия автоматической сборки, внесение в конструкцию изделия коррективов.
- Проведение размерного анализа.
- Установление и утверждение методов осуществления соединений.
- Составление технологических схем общей и узловой сборки.
- Составление маршрута сборки.
- Уточнение содержания операций сборки, корректировка на основе оптимальных условий выполнения соединений.
- Выбор типа автоматического сборочного оборудования.
- Разработка и конструирование специального оборудования.
- Расчет экономических показателей эффективности автоматизации.
Сборка изделий вариативна. Методом математического моделирования и перебора вариантов можно определить оптимальную последовательность набора операций и переходов для получения заданного качества результата сборки изделия.
В качестве критериев совершенства (оптимальности) процесса сборки принимают наименьшую сложность автоматизации сборки, наименьшую стоимость продукции при заданном ее качестве, т.е. определяют такой вариант, который имеет минимальный «потенциал» модели. Для решения такой задачи разрабатывают топологическую модель, формалированно описывающую все возможные варианты технологического процесса, приводя их к сетевой модели [2]. Сетевую модель сборочного процесса получают математическим объединением исходных характеристических моделей первого типа [11]. На всех этапах разработки и синтеза моделей используется теория логико-динамических графов.
Сокращения времени на операции и совмещения переходов можно достичь применением соответствующих схем построения сборочных операций. К таким схемам относятся: одно- и многоместные схемы, в зависимости от числа устанавливаемых изделий на позицию сборки; одно- и многоинструментальные схемы, в зависимости от числа одновременно применяемых при сборке инструментов. По последовательности технологических переходов операции могут быть последовательными, параллельными и смешанного типа. При различном сочетании указанных схем образуется комплекс схем построения операций, отличающихся в значительной степени друг от друга по времени выполнения операций и себестоимости сборки. [4]
При построении операций сборки следует учитывать то, что на их проектирование не должны оказывать влияние особенности ручной сборки. Некоторые приемы, с трудом осуществляемые вручную, зачастую легко выполняются механизмами и наоборот – отдельные приемы, легко осуществляемые сборщиком, выполняются механизмами гораздо сложнее. Поэтому попытки копировать ручную сборку обычно не дают хороших результатов [15]. При проектировании методов выполнения соединений на позициях автоматической сборки следует уделять равно пристальное внимание, как классическим схемам сборки, так и поиску нестандартных решений, ориентированных на сборку конкретного соединения.
При разработке технологических операций автоматической сборки определяют оптимальные режимы сборки и находят настроечные размеры для наладки оборудования. После принятия схем построения сборочных операций и выполнения расчета режимов сборки определяют требования, предъявляемые к базирующим устройствам, устройствам относительной ориентации, сборочным головкам и другим функциональным элементам сборочного оборудования, а также к оборудованию в целом. При проектировании сложных технологических операций, выполняемых на многопозиционном сборочном оборудовании, определяется загрузка оборудования по отдельным позициям и строятся циклограммы его работы [1].
Необходимым этапом проектирования технологического процесса автоматической сборки является разработка циклограммы – вспомогательного графического документа, отображающего временные взаимосвязи осуществления перечня операций и переходов технологического процесса.
Циклограмма сборки выполняет следующие задачи:
- Визуальное представление временных взаимосвязей между элементами технологического процесса различного уровня (операции, переходы и т.д.).
- Визуальное представление затрат времени на осуществление всех элементов технологического процесса.
- Открытие возможностей для точной синхронизации времени выполнения заданных элементарных процессов внутри технологического процесса сборки.
- Открытие широких возможностей для подробного анализа технологического процесса сборки и возможности своевременного внесения коррективов на стадии технического планирования.
Создание технологии автоматической сборки тесно связано с глубоким изучением сущности сборочных процессов для выявления закономерности их протекания и эффективного управления ними. На базе научных и методических основ автоматизации сборки разрабатываются технологические основы проектирования сборочного автоматического оборудования и создаются типовые исполнительные устройства, из которых по принципу агрегатирования можно быстро компоновать автоматическое сборочное оборудование различного целевого назначения. В основе этой работы должна лежать типизация технологических процессов сборки [6].
3. Практическое значение
В работе подробно рассмотрены все аспекты и возможности автоматизации сборочных процессов для условий выпуска пневмо- и гидроаппаратуры, с целью разработки комплекса рекомендацией по повышению уровня автоматизации сборочных работ с точки зрения оптимизации по различного рода критериям (производительность, экономический эффект, улучшение условий труда и др.).
4. Научная новизна полученных результатов
На данном этапе научно-исследовательской деятельности вопрос об актуальности автоматизации сборки для условий производства конкретного типа продукции поднимается редко, чаще акцент ведется на оценку годовых объемов выпуска. В данной работе рассмотрена актуальность повышения уровня автоматизации сборочных процессов узлов пневмо- и гидроаппаратуры, подобраны и научно обоснованы методы и средства повышения уровня автоматизации, разработан комплекс рекомендаций, спроектировано автоматическое сборочное устройство. Для оценки и синтеза производственно-технологических процессов с целью их реорганизации и оптимизации используются математико-статистические методы решения задач, теория графов, алгебра логики и алгебра множеств.
Выводы
Согласно классическому подходу к решению проблемы автоматизации процессов сборки, предпосылками к ее осуществлению являются стабильность и массовость выпускаемой продукции. Решение о необходимости автоматизации на 90% зависит от объемов выпуска продукции и доли трудоемкости сборки в совокупном производственном процессе. Также не последнюю роль на принятие решения об автоматизации сборочных процессов оказывает используемый на предприятии метод достижения точности замыкающего звена сборки конечного изделия, косвенно и прямо влияющий на организацию всего производственного процесса.
Пожалуй, основным стопором, пресекающим в корне все попытки автоматизировать сборочное производство, является сложность и дороговизна изготовления машин-автоматов для будущей сборочной линии. Конструкция каждой машины должна соответствовать сборке конкретного соединения, а система автоматов в конечном итоге – последовательно производить полноценную сборку изделия. Большая номенклатура изделий практически сводит на нет сам принцип подобной организации – затраты на регулярную переналадку и частые изменения конструкции автоматической линии способны разорить любое предприятие.
Основным экономическим недостатком автоматизированных систем сборки следует назвать долгий срок окупаемости. В условиях достаточно нестабильной рыночной ситуации позволить себе такую долгосрочную стратегию могут лишь предприятия, твердо уверенные в своей конкурентоспособности в глазах потребителя.
Список источников
- Замятин В.К. Технология и оснащение сборочного производства: Справочник. - М.: Машиностроение, 1995. - 608 с.
- Лебедовский М.С., Вейц В.Л., Федотов А.И. Научные основы автоматической сборки. - Л.:Машиностроение, 1985. - 316 с.
- Балакшин Б.С. Основы технологии машиностроения. - М.: Машиностроение, 1969. - 358 с.
- Косилов В.В. Технологические основы проектирования автоматического сборочного оборудования. — М.: Машиностроение, 1976 – 382 с.
- Замятин В.К. Технология и автоматизация сборки. - М.: Машиностроение, 1993. - 464 с.
- Новиков М.П. Основы технологии сборки машин и механизмов. – М.: Машиностроение, 1969. – 632 с.
- Информационный портал «Инновации бизнесу». Наименование проекта: Установка для автоматического сопряжения цилиндрических деталей с использованием вращающегося двигателя. Режим доступа: http://www.ideasandmoney.ru/Ntrr/Details/124950
- Хлебцевич В.Д., Задерей А.М., Лапковский С.В. Повышение эффективности автоматической сборки нестационарным приложением усилия. Режим доступа: http://www.rusnauka.com/PRNIT_2006/Tecnic/15945.doc.htm
- Информационный портал «Инновации бизнесу». Наименование проекта: Устройство для автоматической сборки деталей в кинематических призмах. Режим доступа: http://www.ideasandmoney.ru/Ntrr/Details/125008
- Солодов М.Д., Золотаревский Ю.М. Методика расчета вероятности безотказного выполнения цилиндрических соединений при автоматической сборке. – Л.: Вестник машиностроения, 1976. – с 61-64.
- Лебедовский М.С. Автоматизация процессов в машиностроении. Ч-1. – Л.: СЗПИ, 1977. – 81 с.
- Картавов С.А. Технология машиностроения (специальная часть). Изд. 2-е, перераб. и доп. – Киев.: Вища школа, 1974. – 272 с.
- Михайлов А.В., Расторгуев Д.А., Схиртладзе А.Г. Основы проектирования технологических процессов машиностроительных производств: учебное пособие. – Старый Оскол: ТНТ, 2010. – 336 с.
- Автоматизация производственных процессов в машиностроении: Учебник для втузов / Н.М. Капустин, П.М. Кузнецов, А.Г. Схиртладзе и др. Под ред. Н.М. Капустина. – М.: Высшая школа, 2004. – 415 с.
- Корсаков В.С. Автоматизация производственных процессов. Учебник для вузов. – М.: Высшая школа, 1978. – 295 с.