Summary on the theme of master's work
Summary of a preliminary nature, since the time of its preparation - March-April 2013. While defense of master's thesis is planned for January 2014.
Content
- The relevance of the topic
- 1. Purpose, methods and objectives of the study
- 2. An analysis of the current state of research questions
- 2.1 Analysis of the technological products to automate the assembly process nodes pneumatic and hydraulic equipment
- 2.2 Analysis of existing methods for automatic assembly of cylindrical products with a clearance
- 3. The practical significance
- 4. The scientific novelty of the results
- Findings
- List of sources
- 2.2 Analysis of existing methods for automatic assembly of cylindrical products with a clearance
The relevance of the topic
Ratio assembly works in total production engineering ranges from 25 to 40%, and in the field instrument reaches 70%. In the pilot plant, these figures increase by half.
But even with such high values of the labor share of total investment in the assembly plant is only 5 .. 10% of the total weight. Because of such a strategy, automation of assembly operations are still not rare: to date in mechanical engineering mechanized 25 .. 30% of assembly work, and automated - about 5%.
The obstacles in the way of automation of assembly work could be:
- Technological neotrabotannosti design;
- Lack of harmonization of assembly units;
- Poor quality parts;- The need for special equipment;
- Disadvantages of assembly equipment;
- The general high cost of the project.
A number of these problems are automatically solved when considering the build automation pneumatic and hydraulic equipment. The nodes of such a plan has several features:
- General standards of construction output range;
- Sufficiently strong and rigid parts;
- The vast majority of connections - cylindrical joints with clearance;
- Unification of sizes seating surfaces;
- Small size of individual parts and products in general;
- Sequential assembly with convenient reference surfaces.
Separately, the important advantage of nodes pneumatic and hydraulic equipment should be called fairly small amount of collected items.
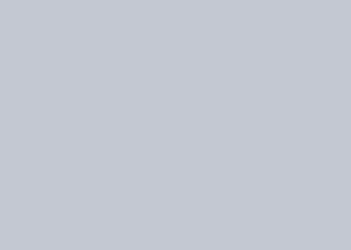
Figure 1 - Visualization sequential assembly process simple hydro (ball valve).
Image of assembly done in the software environment of 3D-modeling SolidWorks.
Animation consists of 27 frames with a delay of 0.5 s at keyframes image node without zadezhki - among all the other frames.
unlimited number of plays.
Based on the foregoing, we can make preliminary conclusions about the relevance of the issue of partial or even complex automation assembly of units pneumatic and hydraulic equipment. This will significantly reduce the overall complexity of manufacturing of such products, to ensure stable production and to increase the overall level of technical preparation of production.
1. Purpose, methods and objectives of the study
The purpose of the master's work - increasing productivity assembly of units pneumatic and hydraulic equipment by automating the assembly process.
To achieve this goal requires the following tasks:
- Perform analysis of the current status of the problem of automation of assembly processes nodes pneumatic and hydraulic equipment.
- To synthesize existing assembly processes for the conditions of automation.
- Develop a mathematical model assembly process nodes pneumatic and hydraulic equipment for further process optimization assembly according to various criteria.
- Carry out pilot studies assembly of smooth cylindrical joints with clearance under the influence of vibrations transmitted by the base member along the axis of the assembly.
- Get emperiko-statistical correlation effects considered factors (frequency of vibration, the shape of the lead-in assembled products, the angle of inclination relative to each other) at the time of assembly.
- Develop recommendations to improve the level of automation of assembly processes nodes pneumatic and hydraulic equipment.
The object of study - cylindrical joints with clearance used in the nodes of pneumatic and hydraulic equipment.
The subject of the study - product assembly process, as well as the characteristics of the processes of assembly joints and connections pneumatic and hydraulic equipment in the conditions of modern engineering industries.
The methods of the study were selected and involved: graph theory, algebra of sets, algebra, logic, methods of statistical processing of the experimental data and the theory of experimental design.
2. An analysis of the current state of research questions
The scope of issues dealing with the automation of assembly processes in the engineering industry can be divided into several categories:
- Theoretical basis of build automation;
- Assessment of the accuracy and reliability of the automated assembly, including a comprehensive indicator of quality;
- Consideration of mechanics, dynamics, and other characteristics of process automation and automated assembly;
- Design, adaptation and operation of automatic assembly equipment (some assembly machines, flexible automated assembly line, automatic assembly lines, automated assembly systems);
- Simulation of assembly processes and automation of their design.
Accordingly, such a classification, detail and systematically review the current status of the problem increasing the automation of assembly units pneumatic and hydraulic equipment.
Among the major theoretical issues raised when considering automation of assembly processes must include:
- choice of method of achieving the closing level of accuracy and resolution of the size of chains in the assembly;
- assessment of the technological design products at all levels of the assembly - manufacturability of the final product, sub-assemblies, parts, components, etc.;
- Identify and analyze the spatial relationships of elements assembly unit;
- determine the conditions collection of compounds;
- development of efficient assembly process;
- search and assessment of sequence variants of each process step assembly.
Under the method of assembly of a product implies a set of rules to achieve a given level of dimensional accuracy of the closing circuit. The achievable accuracy in the assembly process should ensure that the values ??of the parameters of the product specified in the design documentation. Ensuring the accuracy of the assembly specified by using the most efficient methods of assembly is achieved on the basis of the calculation and analysis of the assembly dimensional chains, which is determined by the accuracy of the relative position of surfaces or axes of parts that make up the assembly unit [1].
To achieve the specified accuracy of the closing level of dimensional chain using five different methods: the complete interchangeability, the method of partial interchangeability interchangeability group method (selective assembly), control method and the method of fit. For the purpose of assembling a high degree of automation of the first two methods are suitable. Of course, a comprehensive or partial automation can be subjected to technological processes of assembly of any one of the above methods, but the maximum simplicity and convenience of the organization control system of technological equipment assembly methods provide only full and part interchangeability.
Lebedovsky M.S. In their scientific works demanded a fundamental aging, from his point of view, the principle of increasing the automation of assembly processes: analysis and synthesis of the automatic assembly process must be carried out for both single and indissoluble link kit "product - technology - machine" [2]. This approach can be considered as the basis for the possibility of re-evaluation of design processes from the point of view of the assembly of functionally-oriented production - a new generation of techniques in engineering.
Balakshin B.S. repeatedly raised the question of the influence of the elastic deformations on the course of the process and the final quality of the assembled unit. Such a factor may be one of the most important geometrical errors occur when the assembly which, in turn, may subsequently lead to excessive bending deformation, twisting and other parameters significantly reduce the overall quality and efficiency of the assembly as a whole product. The threat of the elastic deformation of parts may be a large-scale problem of the quality of the assembly, if the individual parts and components have low stiffness and inconvenience based, that does not allow to the extent necessary to produce them reliably and relative orientation of the connection [3].
Kosilov V.V. in the field of theoretical justification and relevance of the possibility of automation of assembly processes in the engineering industry was based on the requirements of high technology products collected - at the levels of the assembly and components, and the final product. Ease of deployment and orientation of parts in the assembly process, he believed, is perhaps the main factor among the criteria of automation. The second most important factor, logically dependent on the manufacturability and assembly units, and from their bases in the assembly process, Kosilov V.V. called compliance collection defined geometric and strength characteristics of the compounds [4].
Implementation of automated assembly processes from the point of view of kinematics should be as simple as providing the minimum number of moves needed to achieve the accuracy and reliability of the specified compounds. In the automation of assembly processes should re-evaluate the established classical methods of the various compounds and the search for new, more fuel-efficient and productive solutions. This requires a non-standard approach to solving the kinematics of the process and the planned departure from the usual mechanisms for assembly of products in mechanical engineering.
Questions to find new, innovative solutions in the field of automation of assembly processes of different types and complexities involved authors such as A.A. Gusev, M.G. Cristal, Z.S. Korsakov, M.N. Grandmother, V.N. Zhomiru, V.M. Bedrin and A.V. Bedrina, D.M. Liauchuk, A.V. Voronin, K.N. Mutsenek, V.A. Yahimovich and others. Among the considered areas of particular interest in engineering had a theme using assisted vibrations when handling assembly components, assembly of the rotating gas stream, the assembly with non-standard paths of moving parts, assembly using the action of magnetic flux, and others.
The issue of modeling the assembly process in order to simplify the search for optimal solutions flow and the organization of technology for direct automated assembly devoted to the works of authors such as Vavilov A.A, Kuzmin V.V. Pavlov P.G., Skhirtladze A.G., Timchenko A.A. and others. Their work focused on the development of methods of formalizing the description of the assembly process, structural analysis and synthesis of models addressing the automation of assembly operations.
ÍHas repeatedly drawn attention to the proposal to use the method of modeling based assembly graph theory Lebedovsky M.S. Particularly relevant, he believed, this method may be for the design of algorithms for the automatic assembly equipment. Authors such as Dostanko A.P., Starikov V.S., Popov E.P. and Tsypkina Y.Z., working on a research topic assembly systems with different kinds of discrete control and formalization of structures. Some research work has been devoted to the topic of mathematical models of assembly processes using pattern recognition methods (Chimitov P.E.) and the use of logic-dynamic graphs for the structuring and analysis of process flows assembly (Zhigalev N.N.).
Significant contribution to the development of the problem of automation of assembly processes have research teams of organizations such as the Moscow Aviation Institute (MAI), Moscow State Technical University named after NE Bauman Moscow State Technological University "STANKIN", Moscow State Technical University "MAMI", a research institute of technology the automotive industry, a research institute of technology tractor and agricultural machinery, and others.
2.1 Analysis of the technological products to automate the assembly process nodes pneumatic and hydraulic equipment.
Technological rationality product design (TORFL) is defined by a set of properties of the product, which express its adaptability in terms of the conformity of construction solutions conditions of production, operation, and maintenance. TORFL achieved through the use of methods:
- modular building systems and devices;
- building-block components;
- optimize the selection and appointment of the structural elements of parts and materials, dimensional analysis of designs of parts and assembly units;
- functional-cost analysis product and its components;
- economic and mathematical modeling of the relationship of the main functional and structural and technological characteristics of the product [1].
Production strategy in terms of increasing production and serial production of complex or partial automation of assembly process inevitably entails an increase and stricter requirements for the technological design of the product.
Increasing adaptability of product design is achieved on the basis of technological analysis and testing of product design for manufacturability. Technological analysis of product design in the assembly - the analysis of product design in order to build the application process, ensure the implementation of the program given the quality of the product was installed in a production environment. Testing of product design for manufacturability - a set of activities carried out at all stages of product development, in order to achieve an optimal set level of adaptability. Testing of product design for manufacturability should be carried out at all stages of the design documentation [1].
When automating assembly processes of product design and manufacturability of its component parts shall conform to the peculiarities of the automatic assembly using the most simple and effective means of automation, ie requirements for manufacturability must be designed to account for easier assembly and smooth implementation of all components of the stages and elements of the automated build process [5].
The main requirements for the technological design product and its components for the condition of automated and automatic assembly can be stated in the list of recommendations:
- The product design, the structure of which includes a large number of components must be built according to the modular principle. This implies a deliberate dismemberment products on a rational number of independent nodes in order to enable their side assembly, testing, balancing, control, etc.
- Product design should eliminate the need for intermediate disassembly and reassembly at certain stages of the process. Execution of assembly work should consist of a series of successive stages completed, the results of which are ready to receive the node moves to the next stage.
- The product shall consist of a minimum number of parts, with preference to be given to the details of simple shapes.
- The product shall consist of a maximum possible number of standard and standardized components.
- Product design should provide convenient and reliable technological base, the use of which will simplify the mechanics of manipulating the assembly position and will give the opportunity to achieve the required performance precision assembly.
- The design of the product should be provided the basic component, the role of which will be in harmony with the role of the basis for the installation of other components. During assembly, movement and change of positions of the base items should be kept to a minimum and ideally - be excluded altogether.
- Each component assembly has to have a minimum number of points and surfaces interfacing with other parts of the product.
- When developing a product design and layout of the size of chains, determining the relative position and connection of components in the final product, should follow the most accurate methods of achieving the closing level of accuracy - the method of full and part interchangeability.
- Avoid multi-tier dimensional chains in the construction of the collected product and its components, which can complicate the process of achieving the necessary precision assembly, and also makes the mechanics of assembly assembly unit.
- In the design of the product should be minimized variation in types of surfaces and interface connections for parts, giving preference to those types that mechanics who perform the most simple in the implementation of the automatic cycle.
- The design of the product and its components must ensure free access of workers assembling equipment, instruments and controls.
- Products and components must have suitable surface to enable capture and handling in automatic mode.
- Product design should provide for a minimum number of assembly lines assembly. The most preferred embodiment should be in one direction assembly, to the maximum extent simplifies the organization of the assembly process and equipment design.
- The logical evolution of the previous recommendations will be to adapt product design for assembly into an automatic cycle with the expectation that all pairing and connection details are carried out using a simple kinematic motions.
- The product and its components must have the necessary stability and the ability to share to the storage and movement.
- Assembly units must be kinematically closed, ie provide orientation, movement and manipulation without the possibility of separation into constituent parts.
To date, the highest value is given as the need for careful evaluation of the product design for manufacturability, and adaptation to the automatic assembly and methods of assessment.
Existing methods for determining the assessment of the technological design products from the point of view of possible automation of assembly processes are based on a subjective evaluation. To date, the techniques developed an automated manufacturability evaluation, based on the principles of abstraction, differentiation, comparison of the objects with analogues of existing databases, as well as the mathematical treatment of the results.Evaluation on product design and manufacturability of adaptation to the conditions of automatic assembly at their high complexity also requires responsibility and competence of expert individuals. As practice shows, the development stage of the project and preliminary assessment of its prospects may be the most bugs and that at the initial stage of the work can minimize the possibility of problems in the implementation of the project. Automation of technological readiness assessment product to the conditions of automatic assembly eliminates the subjective human factor and as accurately estimate the maximum possible and economically feasible the necessary level of automation of production processes.
Of the currently known methods for assessing product design for manufacturability should be mentioned methodology A.G. Kholodkova (Moscow State Open University) and fully automated software project B. Reifur (Wroclaw Technical University).
2.2 Analysis of existing methods for automatic assembly of cylindrical products with a clearance
The assembly of smooth cylindrical joints with clearance in most cases is susceptible to automation. Such compounds may be collected under the action of gravity and forced the connecting parts (power) method.
Assembly under the influence of gravity is possible with a vertical axis arrangement of mating parts or a position close to the vertical (the deviation from the vertical is not more than 10 .. 15o), and also with significant gaps in the compound (in tenths of a millimeter), weight and size of parts (not at least 0.05 kg and a diameter of not less than 10 mm). However, the connection parts under the influence of gravitational forces can not provide high reliability of the process, especially when relatively light assembly parts and significant total misalignment relative to each other [5].
In automatic assembly of cylindrical components most commonly used scheme in which the orientation of parts assembled on the assembly position is blocked by the outer surfaces in the prisms. Early automatic cycle axle assembly attachable part can occupy different positions relative to the axis of the base, the axes of parts may be in the same or different planes. The most simple implementation of such schemes include the assembly in which no movement required to align the axes of the assembled parts. [1]
For automatic coupling of cylindrical parts often use devices that tell a mating parts relative rotation movement. The rotating movement of the connecting passes catcher details so that it at some point of time is relative to the base is a position at which the further process of assembly is guaranteed. By its physical nature of the parameters that determine the reliability of the assembly process can be attributed to the following groups:
- The design parameters (joint gap, the nominal diameter of the connection, the total size of the radial legs of the bevels on the mating surfaces, the length of the connection).
- The parameters of the actuator (the gap between the catcher and the connecting piece, the distance between the ends of catchers, stiffness catcher).
- Modes of the assembly process (the amount of force the assembly, the speed of movement of assembly, the angular velocity of the catcher) [7].
Efficient high-performance automatic assembly is only possible with considerable reliability of automation devices. The largest share of failures automatic assembly of cylindrical joints occurs during the passage of the mating surfaces of the zone or chamfering the edges because the error relative orientation of these surfaces is more acceptable for the applicable type of assembly unit.
In automatic assembling method proposed by specialists Kiev Polytechnic University, self-aligning cylindrical mating surfaces occurs due to the force application point which moves along the concentric circle on the end of the connecting sleeve fixed in the compliant device, in contact with the shaft is fixedly mounted. If the sleeve and the shaft ends in contact with an offset axis of mating surfaces, the force applied in a specific area on the outer end of the sleeve causes it to rotate about an axis passing through the two points of contact edges of the mating surfaces in contact and moving with the shaft end in the direction of eccentricity reduction Touch-edge and forming a sleeve bore at a third point. Possible to capture the edges, which prevents the return of the sleeve to the starting position and the second phase of self-orientation conditioning, which consists in the fact that the point of contact surfaces of mating edges closer, until it merged into a single point. This gradually decreases, and skewing the axis of the sleeve to the end of the second stage with its axis aligned with the axis of the shaft. Self-orientation movement of the mating surfaces to an end, and the build [8].
To date, the technique of high-performance assembly of cylindrical joints with clearance conditions for continuous automatic cycle of the process. The essence of the method consists in the fact that in the area of ??assembling a flat basing elements of committing a plane perpendicular to the direction of transport rollers and bushings, reciprocated by a given law. The movement of each element is shifted from the previous by a certain phase angle, so that at any given time at the speed of the basic elements is greater than zero, equals zero or is less than zero. The plane tangent to the surface of the element is based, the speed of which are positive, makes with the plane tangent to the conjugate with the considered elements, kinematic prism providing aeration and transport details. The stepped profile basing elements allows coaxial base mating parts with different diameters of base surfaces. Repeated cycles of reciprocating motion of a predetermined period of time leads to the formation of a number of kinematic assembly zone prisms spaced at constant pitch. Persistence of steps between assembly kits closer to the regular flow of parts.
As a result of the forces of friction between the surfaces of the base assembly kit seen their rotational motion. Since the surface of various base diameters, the difference between the angular velocities of roller and the relative rotation of the sleeve causes the mating surfaces. Presence of eccentricity between the base and the mating surface of the sleeve causes a relative scanning axes joint parts due to the rotation-vibration effect. When the mating contact surfaces of the ends of the relative movement due to vibration and reduces the rotational friction force in the direction of assembly. Therefore, improving the conditions samoorientirovaniya details [9].
Consideration of issues related to the automation of assembly processes movable cylindrical assemblies at different times engaged writers such as A.V. Voronin, M.M. Strzhemechny, E.V. Pisarev, A.G. Kholodkova, E.I. Kolchugin, V.M. Pohmelnyh, T.Y. Rodivilina and other.
2.3 Analysis of the existing design methodologies automated assembly processes
The technological process of the assembly includes a list of necessary steps for the installation and structured formation of compounds of the constituent components of the product in the specified sequence. The technological process of the assembly can consist of one (single-purpose) or a related set (multioperational) assembly operations.
The classic design of the sequence assembly process involves a number of stages:
- Analysis of the initial data.
- Setting the boundary conditions.
- Choice of organizational form assembly.
- Evaluation of the technological design of the product.
- Carrying dimensional analysis of product design.
- Choice of technological bases and basing schemes.
- The search for rational methods of assembly joints.
- Evaluation of technological capabilities and selection of plant equipment and tooling.
- Drawing up of the shuttle assembly process.Clarifying process of assembly.
- Rationing.Cost-effectiveness of the options under consideration build process, the choice of preference.
- Registration of accompanying documentation.
Assembly diagram is a graphic document assembly sequence of the original, normal, purchased parts at the nodes and the sequence of assembly kits and assemblies. Such schemes can speed up the development of the assembly and its acquisition of parts, components and assemblies [12].
Each constituent element of the product depicted in the diagram as a rectangle divided into three parts: the top part is given the name element, in the left lower - numeric index element specification, the lower right - the number of elements included in the compound. Flow charts assembly is provided with inscriptions, footnotes explaining the nature of the assembly work when they are not clear from the scheme ofû [13].
The basis of the development of an automated build process is based on two principles: technical and economic. In accordance with the principle of technological process designed automated assembly must fully implement all the demands of the working drawings and specifications of acceptance of the product. In line with the economic principle of assembly products should be conducted with minimal materialized and living labor and with minimal production costs [15].
An important condition for the development of efficient automated build process is to standardize and normalize compounds, ie bringing them to a particular nomenclature of species and accuracies. On the basis of unification and normalization of compounds in terms of assembly and product develop model assembly processes, operations and conversions performed on a standard assembly equipment using standard tools and accessories [14].
The process of designing an automated build process consists of a set of interconnected and operated in a sequence of stages:
- Collection and analysis of baseline data.
- Testing of products for manufacturability under the terms of an automated build, making adjustments to the product.
- Carrying dimensional analysis.
- Establishment and validation of methods of connectivity.
- Drawing up the general process flow diagrams and component assembly.
- Route planning assembly.
- Clarifying the content of assembly, adjustment is based on the optimal conditions to make the connections.
- Select the type of automatic assembly equipment.
- Design and construction of special equipment.
- The calculation of economic performance automation.
Assembling the product is a variable one. By mathematical modeling and sorting options can be set to determine the optimal sequence of operations and transitions for a given quality of the assembly.
The criteria of excellence (optimality) of the assembly process has the smallest complexity of assembly automation, the lowest cost of production for a given quality and quantity, ie determine the option that has the minimum "potential" model. To solve this problem develop a topological model formalirovanno describing all the possible options of the process, leading them to the network model [2]. Network model of the assembly process is obtained by combining mathematical models of the original characteristic of the first type [11] . At all stages of the design and synthesis of models uses the theory of logic-dynamic graphs.
Reduction of time for the operation and alignment transitions can be achieved by applying the relevant schemes of building assembly operations. These circuits include single and multi-circuits, depending on the number of products on the mounted assembly position, one and mnogoinstrumentalnye circuits, depending on the number of simultaneously used during assembly tools. From the sequence of technological transitions operations can be sequential, parallel and mixed type. When various combinations of these schemes complexed operations of schemes which differ greatly from each other in the run-time operation and assembly cost [4].
In the construction of an assembly process should take into account the fact that their design should not be affected especially manual assembly. Some techniques, hardly implemented manually, often easily performed mechanisms and vice versa - some tricks easily handled by the garbage, made ??more complicated mechanisms. Therefore, attempts to copy the manual assembly usually do not give good results [15] . In the design of methods to make the connections on the positions of the automatic assembly should be given equal attention as a classic circuit assembly, and seeking unconventional solutions, focused on the assembly of a particular compound.
In the development of an automated build process operations determine optimal modes of assembly and tuning dimensions are for setting up the equipment. After the adoption of schemes of assembly operations and performance of the operating conditions determine the assembly requirements are based devices, the relative orientation assembly heads and other functional elements of the assembly equipment, as well as to the equipment as a whole. In the design of complex manufacturing operations performed on the multi-position assembly equipment, loading equipment is determined by the individual items and sequence diagrams are constructed his work [1].
A necessary step in the design process is the development of automated assembly sequence diagrams - auxiliary graphic document that shows the temporal relationship of the list of transactions and transition process.
Sequence diagram assembly performs the following tasks:
- A visual representation of the time relationships between the elements of the process at various levels (steps, transitions, etc.).
- visual representation of the time required to implement all elements of the process.
- opening opportunities for precise time synchronization of the set of elementary processes in the assembly process.
- opening opportunities for a detailed analysis of the process of assembly and the timely adjustments to the stage of technical planning.
Development of technology for automatic assembly is closely connected with a deep study of the essence of the assembly process to identify the patterns of their occurrence and effective management of them. Based on scientific and methodological foundations of automatic assembly technology developed principles of design and assembly automation equipment are standard actuators, of which the principle of aggregation can quickly assemble automatic assembly equipment for various purposes. At the core of this work should be based typing process assembly [6].
3. The practical significance
In detail all aspects of automation and assembly processes for the conditions of manufacture pneumatic and hydraulic equipment, to develop a set of recommendations to improve the level of automation of assembly work from the point of view of optimization on various criteria (productivity, economic benefits, working conditions, etc. ).
4. The scientific novelty of the results
At this stage of the research activities of the relevance of the automated build environment for the production of a particular type of production rises rare, often the focus is on the estimation of the annual production volumes. In this paper we consider the relevance of increasing the automation of assembly processes nodes pneumatic and hydraulic equipment, selected and scientifically sound methods and means to improve the level of automation, developed a set of recommendations designed auto assembler. For the evaluation and synthesis of production and technological processes for restructuring and optimizing the use of mathematical and statistical methods for solving problems, graph theory, algebra, logic, and the algebra of sets.
Findings
According to the classical approach to the problem of automated assembly processes, preconditions for its implementation are stable and mass manufactured products. The decision to automate up to 90% depending on the volume of output and the share of labor in total assembly manufacturing process. Also a role in the decision to automate assembly processes used at the plant has a method of achieving the closing level of accuracy of the final product assembly, indirectly and directly affects the organization of the production process.
Perhaps the main stopper, nipped in the bud all attempts to automate the assembly line is the complexity and high cost of manufacture of automatic machines for the future assembly line. The design of each machine must comply with the assembly of the particular compound, and the system eventually machines - consistently produce a full assembly of the product. Large product range almost negates the very principle of such an organization - the cost of a regular and frequent changeovers redesign automatic line can ruin any business.
The main economic disadvantage of automated assembly systems should be called a long payback period. In a fairly volatile market conditions afford the long-term strategy can only companies who are convinced their competitiveness in the eyes of the consumer.
List of sources
- Zamyatin V.K. Technology and equipment assembly plant: A Handbook. - M.: Mechanical Engineering, 1995. - 608 p.
- Lebedovsky M.S., Weitz V.L., Fedotov A.I. Scientific basis of automatic assembly. - L.: Mechanical Engineering, 1985. - 316 p.
- Balakshin B.S. Fundamentals of Mechanical Engineering. - M.: Mechanical Engineering, 1969. - 358 p.
- Kosilov V.V. Technological bases of designing automated assembly equipment. - M.: Mechanical Engineering, 1976 - 382 p.
- Zamyatin V.K. Technology and automation of the assembly. - M.: Mechanical Engineering, 1993. - 464 p.
- Novikov M.P. The basic technology of the assembly machinery. - M.: Mechanical Engineering, 1969. - 632 p.
- Information portal "Innovations business." Name of the project: Installation of automatic coupling of cylindrical parts with a rotating motor. Access: http://www.ideasandmoney.ru/Ntrr/Details/124950
- Khlebtsevich V.D., Zaderei A.M., Lapkovsky S.V. Improving the efficiency of automatic assembly unsteady efforts. Access: http://www.rusnauka.com/PRNIT_2006/Tecnic/15945.doc.htm
- Information portal "Innovations business." Project title: Device for automatic assembly of parts in the kinematic prisms. Access: http://www.ideasandmoney.ru/Ntrr/Details/125008
- Malts M.D., Zolotarevskiy YM Method of calculating the probability of failure of the cylindrical assemblies for automatic assembly. - L: Journal of Mechanical Engineering, 1976. - From 61-64 p.
- Lebedovsky M.S. Automation of processes in mechanical engineering. W-1. - L.: SZPI, 1977. - 81 p.
- Lisping S.A. Engineering Technology (special section). Ed. 2nd, revised. and add. - Kiev. Vishcha School, 1974. - 272 p.
- Mikhailov A.V., Rastorgouev D.A., Shirtladze A.G. Fundamentals of the design process engineering industries: a training manual. - Stary Oskol: TNT, 2010. - 336 p.
- Automation of production processes in engineering: A Textbook for technical colleges / NM Kapustin, PM Kuznetsov, AG Skhirtladze and others, ed. NM Kapustin. - M.??: Higher School, 2004. - 415 p.
- Korsakov V.S. Automation of production processes. Textbook for high schools. - M.??: Higher School, 1978. - 295 p.