Реферат за темою випускної роботи
Реферат носить попередній характер, оскільки час його складання - березень-квітень 2013р., тоді як захист магістерської дисертації запланований на січень 2014р.
Зміст
- Актуальність заявленої теми
- 1. Мета, методи та завдання дослідження
- 2. Аналіз сучасного стану питань дослідження
- 2.1 Аналіз технологічності виробів для автоматизації складальних процесів вузлів пневмо-і гідроапаратури
- 2.2 Аналіз існуючих методів автоматичного складання циліндричних виробів з зазором
- 2.3 Аналіз існуючих методик проектування технологічних процесів автоматичного складання
- 3. Практичне значення
- 4. Наукова новизна одержаних результатів
- Висновки
- Список джерел
- 2.2 Аналіз існуючих методів автоматичного складання циліндричних виробів з зазором
Актуальність заявленої теми
Частка складальних робіт у загальному обсязі машинобудівного виробництва знаходиться в межах від 25 до 40%, а в галузі приладобудування досягає 70%. У дослідному виробництві ці показники зростають удвічі.
Але навіть при настільки високих значеннях трудомісткості питома вага загальних капіталовкладень в складальне виробництво складає всього 5..10% від загальної маси. Унаслідок такої стратегії автоматизація складальних операцій все ще недостатньо поширена: на сьогоднішній день в машинобудуванні механізовано 25..30% складальних робіт, а автоматизовано - близько 5%.
Перешкодами на шляху автоматизації складальних робіт можуть стати:
- технологічна неотработанность конструкції;
- недостатній рівень уніфікації складальних одиниць;
- невисока якість деталей;
- потреба в спецоснащення;
- недоліки складального обладнання;
- загальна дорожнеча проекту.
Цілий ряд перерахованих вище проблем автоматично вирішується при розгляді питання автоматизації збирання пневмо-і гідроапаратури. Вузли подібного плану мають ряд особливостей:
- загальні стандарти конструкцій випускається номенклатури;
- досить міцні і жорсткі деталі;
- переважна більшість з'єднань - циліндричні з'єднання з зазором;
- уніфікація розмірів посадкових поверхонь;
- малі габаритні розміри окремих деталей, вузлів і виробів в цілому;
- послідовна збірка із зручними базовими поверхнями.
Окремим, важливим достоїнством вузлів пневмо-і гідроапаратури слід назвати досить малий обсяг зібраних деталей.
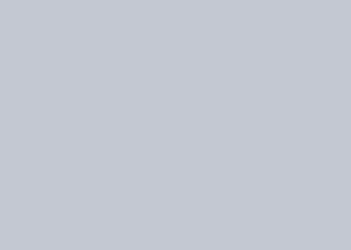
Малюнок 1 - Візуалізація послідовного процесу складання найпростішого гідровузла (клапан кульковий).
Зображення збірки виконано в програмному середовищі 3D-моделювання SolidWorks.
Анімація складається з 27 кадрів із затримкою в 0,5 с на ключових кадрах зображення вузла і без задежки - між усіма іншими кадрами.
Кількість відтворень необмежена.
На підставі вищевикладеного можна робити попередні висновки про актуальності розвитку питання часткової або навіть комплексної автоматизації складання вузлів пневмо-і гідроапаратури . Це дозволить значною мірою знизити загальну трудомісткість виготовлення подібної продукції, забезпечити стабільний випуск і підвищити загальний рівень технічної підготовки виробництва.
1. Мета, методи та завдання дослідження
Мета магістерської роботи - підвищення продуктивності складання вузлів пневмо-і гідроапаратури за рахунок автоматизації складальних процесів.
Для реалізації поставленої мети потрібно вирішити такі завдання :
- Виконати аналіз сучасного стану питання автоматизації складальних процесів вузлів пневмо-і гідроапаратури.
- Провести синтез існуючих складальних технологічних процесів для умов автоматизації.
- Розробити математичну модель складальних процесів вузлів пневмо-і гідроапаратури для подальшої оптимізації технологічних процесів складання за різними критеріями.
- Провести експериментальні дослідження складання гладких циліндричних з'єднань з гарантованим зазором під впливом коливань, переданих базової деталі уздовж осі збірки.
- Отримати еперіко-статистичну залежність впливу розглянутих факторів (частота вібрації, форма заходная частини зібраних виробів, кут відносного нахилу один до одного) на час складання.
- Розробити рекомендації щодо підвищення рівня автоматизації складальних процесів вузлів пневмо-і гідроапаратури
Об'єкт дослідження - циліндричні з'єднання з зазором, використовувані у вузлах пневмо-і гідроапаратури.
Предмет дослідження - технологічний процес складання виробів, а також характерні особливості здійснення процесів складання з'єднань і вузлів пневмо-і гідроапаратури в умовах сучасних машинобудівних виробництв.
В якості методів дослідження були вибрані і задіяні: теорія графів, алгебра множин, алгебра логіки, методи статистичної обробки експериментальних даних і теорія планування експерименту.
2. Аналіз сучасного стану питань дослідження
Загальний спектр питань, присвячених автоматизації складальних процесів у машинобудуванні, можна умовно розділити на декілька категорій:
- Теоретичні основи автоматизації збірки;
- Оцінка точності і надійності автоматизованої збірки, включаючи комплексний показник якості;
- Розгляд механіки, динаміки та інших характеристик процесу автоматизованої і автоматичної збірки;
- Конструювання, адаптація та експлуатація автоматичного складального обладнання (окремі складальні автомати, гнучкі автоматизовані лінії складання, автоматичні лінії складання, автоматичні складальні системи);
- Моделювання складальних процесів і автоматизація їх проектування.
Відповідно подібної класифікації можна більш детально та систематично розглянути сучасний стан питання підвищення рівня автоматизації складання вузлів пневмо-і гідроустаткування.
Серед основних теоретичних питань, уражених при вирішенні питання автоматизації складальних процесів, необхідно назвати:
- вибір методу досягнення точності останнього у ланки та рішення розмірних ланцюгів при складанні;
- оцінка технологічності конструкції виробу на всіх рівнях збірки - технологічність кінцевого продукту, складальних вузлів, деталей, комплектуючих і т.д.;
- визначення та аналіз просторових взаємозв'язків елементів складальної одиниці;
- визначення умов збирання з'єднань;
- розробка раціональних технологічних процесів складання;
- пошук та оцінка варіантів послідовності здійснення кожного етапу технологічного процесу складання;
Під методом складання виробу мають на увазі сукупність правил досягнення заданої точності останнього у ланки розмірної ланцюга. Точність, яка досягається в процесі складання, повинна забезпечувати відповідність значень параметрів виробу заданим в конструкторської документації. Забезпечення заданої точності складання шляхом використання найбільш економічних методів складання досягається на основі розрахунку і аналізу складальних розмірних ланцюгів, за допомогою яких визначається точність відносного розташування поверхонь або осей деталей, що входять до складу складальної одиниці [1].
Для досягнення заданої точності останньої ланки розмірного ланцюга використовується п'ять різних методів: метод повної взаємозамінності, метод неповної взаємозамінності, метод групової взаємозамінності (селективна збірка), метод регулювання та метод пригону. Для цілей складального виробництва з високим ступенем автоматизації найбільш підходять перші два методи. Зрозуміло, комплексної або часткової автоматизації можуть підлягати технологічні процеси складання за будь-яким з перерахованих вище методів, але максимальну простоту організації і зручність контролю за системою технологічного складального обладнання дають тільки методи повної та неповної взаємозамінності.
Лебедовський М.С. у своїх наукових працях вимагав дотримання основоположного, з його точки зору, принципу підвищення рівня автоматизації складальних процесів: аналіз і синтез технологічної системи автоматичного складання повинен виконуватися як для єдиної та нерозривної ланки комплекту «виріб - технологія - машина» [2]. Такий підхід можна розцінювати як основу для можливості переоцінки проектування технологічних процесів складання з точки зору функціонально-орієнтованого виробництва - методики нового покоління в машинобудуванні.
Балакшиним Б.С. неодноразово піднімалося питання впливу виникаючих пружних деформацій на протікання технологічного процесу і кінцеву якість зібраного вузла. Подібний фактор може бути одним з найбільш значущих при виникненні геометричних похибок збірки, які, у свою чергу, можуть згодом призвести до виникнення надлишкових деформацій вигину, крутіння та інших, значно знижують загальні показники якості складального вузла і працездатність виробу в цілому. Загроза виникнення пружних деформацій деталей може бути великомасштабною проблемою якості збірки в тому випадку, якщо окремі деталі і вузли відрізняються низькою жорсткістю і незручністю базування, що не дозволяє в необхідній мірі надійно провести їх відносне орієнтування і з'єднання [3].
Косилов В.В. у сфері теоретичного обгрунтування можливості та актуальності автоматизації складальних процесів у машинобудуванні спирався на вимоги до високої технологічності виробів, що збираються, - на рівнях збірки і вузлів, і кінцевого виробу. Зручність орієнтування та базування деталей в процесі складання, вважав він, є чи не основним чинником серед критеріїв автоматизації. Другим найбільш значимим фактором, логічно залежним і від технологічності складальних одиниць і від їх базування в процесі складання, Косилов В.В. називав дотримання умов збирання, визначених геометричними і силовими характеристиками сполук [4].
Реалізація процесів автоматизації складання з точки зору кінематики повинна бути максимально простою, забезпечувати мінімальну кількість рухів для досягнення необхідних точності і надійності заданих з'єднань. У питаннях автоматизації складальних процесів слід робити переоцінку застарілих класичних методів реалізації різного роду з'єднань і шукати нові, більш економічні і продуктивні рішення. Це вимагає нестандартного підходу до вирішення завдань кінематики процесу і планового відходу від звичних механізмів складання виробів в машинобудуванні.
Питаннями пошуку нових, прогресивних рішень в області автоматизації складальних процесів різного типу та складності, займалися такі автори, як А.А. Гусєв, М.Г. Кристаль, З.С. Корсаков, М. Н. Бабушкін, В.М. Жоміру, В.М. Бедрин і А.В. Бедрина, Д.М. Левчук, О.В. Воронін, К.Н. Муценек, В.О. Яхимович та інші. Серед розглянутих напрямків особливий інтерес в машинобудуванні мала тема застосування допоміжних вібрацій при маніпулюванні компонентами складання, складання в обертовому потоці газів, складання з нестандартними траєкторіями переміщення деталей, складання із застосуванням дії магнітних потоків та інші.
Питанням моделювання складальних процесів з метою спрощення пошуку оптимальних рішень протікання та організації технології для безпосередньої автоматизації збирання присвячені праці таких авторів, як Вавілов О.О., Кузьмін В.В., Павлов П.Г., Схиртладзе О.Г. , Тимченко О.О. та інших. У їхніх роботах основна увага приділялася розробці методик формалізації опису технологічних процесів складання, структурного аналізу і синтезу їх моделей, вирішенню питань автоматизації складальних операцій.
Неодноразово загострював увагу на пропозиції використовувати метод моделювання процесів складання на основі теорії графів Лебедовський М.С. Особливо актуальним, вважав він, цей метод може стати для проектування алгоритмів роботи автоматичного складального обладнання. Такі автори, як Достанко О.П., Стариков В.Ш., Попов О.П. та Ципкіна Я.З. працювали над темою дослідження складальних систем різного роду з дискретним керуванням і формалізацією структур. Окремі наукові роботи були присвячені темі математичних моделей складальних процесів з використанням методів розпізнавання образів (Чімітов П.Є.) та застосування логіко-динамічних графів для структурування та аналізу технологічних маршрутів збірки (Жигалов М.М.).
Істотний внесок у розвиток питання автоматизації складальних процесів внесли наукові колективи таких організацій, як: Московський авіаційний інститут (МАІ), Московський державний технічний університет імені Н.Е. Баумана, Московський державний технологічний університет «Станкін», Московський державний технічний університет "МАМІ", науково-дослідний інститут технології автомобільної промисловості, науково-дослідний інститут технології тракторного і сільськогосподарського машинобудування та інші.
2.1 Аналіз технологічності виробів для автоматизації складальних процесів вузлів пневмо-і гідроапаратури
Технологічна раціональність конструкції виробу (ТРКВ) визначається сукупністю властивостей виробу, які виражають його технологічність з точки зору відповідності прийнятих конструктивних рішень умовам виробництва, експлуатації та ремонту. ТРКВ забезпечується за рахунок застосування методів:
- блочно-модульної побудови систем і пристроїв;
- агрегатування складових частин;
- оптимізації вибору і призначення конструктивних елементів деталей і матеріалів, розмірного аналізу конструктивних виконань деталей і складальних одиниць;
- функціонально-вартісного аналізу виробу і його складових частин;
- економіко-математичного моделювання взаємозв'язків основних функціональних і конструктивно-технологічних характеристик виробу [1].
Стратегія виробництва в плані підвищення серійності випуску виробів і комплексної або часткової автоматизації складальних процесів тягне за собою зростання і посилення вимог до технологічності конструкції виробу.
Підвищення рівня технологічності конструкції виробу досягається на основі проведення технологічного аналізу та відпрацювання конструкції виробу на технологічність. Технологічний аналіз конструкції виробу в збірці - аналіз конструкції виробу з метою застосування технологічного процесу складання, що забезпечує виконання програми випуску виробів заданої якості у встановлених умовах виробництва. Відпрацювання конструкції виробу на технологічність - комплекс заходів, що проводяться на всіх етапах розробки виробу, з метою досягнення оптимального заданого рівня технологічності. Відпрацювання конструкції виробу на технологічність повинна проводитися на всіх стадіях розробки конструкторської документації [1].
При автоматизації складальних процесів технологічність конструкції виробу і його складових частин повинна відповідати особливостям виконання автоматичного складання із застосуванням найбільш простих й ефективних засобів автоматизації, тобто вимоги до технологічності повинні розроблятися з урахуванням максимального спрощення збірки і безперешкодної реалізації всіх складових етапів і елементів процесу автоматичного складання [5].
Основні вимоги до технологічності конструкції виробу і його компонентів для умови автоматизованої і автоматичної збірки можна сформулювати в переліку рекомендацій:
- Конструкція виробів, структура яких включає в себе велику кількість компонентів, повинна будуватися за модульним принципом. Це передбачає навмисне розчленовування вироби на раціональне число самостійних вузлів з метою забезпечення можливості їх паралельної збірки, випробувань, балансування, контролю і т.д.
- Конструкція виробу повинна виключати необхідність проміжних розбирання і повторного складання на певних стадіях технологічного процесу. Виконання складальних робіт повинно складатися з ряду послідовних закінчених етапів, за результатами яких отримують готовий вузол, який переміщують на наступний етап.
- Виріб повинен складатися з мінімальної кількості деталей, при цьому - перевага повинна віддаватися деталям простих форм.
- Виріб повинен складатися з максимально можливого числа стандартних і уніфікованих компонентів.
- Конструкція виробу повинна передбачати зручні та надійні технологічні бази, використання яких дозволить максимально спростити механіку маніпулювання на складальній позиції і дасть можливість досягти необхідних показників точності складання.
- У конструкції виробу повинна бути передбачена базова складова частина, роль якої буде співзвучна ролі основи для установки інших компонентів. У процесі складання переміщення і зміна положення базової деталі повинні бути зведені до мінімуму і в ідеалі - виключені зовсім.
- Кожен складовий елемент збірки повинен мати мінімальну кількість поверхонь і точок сполучення з іншими частинами виробу.
- При розробці конструкції виробу і плануванні розмірних ланцюгів, що визначають відносне положення і зв'язку компонентів в готовому виробі, слід дотримуватися найбільш точних методів досягнення точності останнього у ланки - методу повної та неповної взаємозамінності.
- Слід уникати багатоланкових розмірних ланцюгів в конструкції виробу, що збирається і його вузлів, що може значно ускладнити процес досягнення необхідної точності складання, а також ускладнює саму механіку збірки складальної одиниці.
- При розробці конструкції виробу слід мінімізувати варіацію типів сполучення поверхонь і з'єднань деталей, віддаючи перевагу тим типам, механіка виконання яких найбільш проста при здійсненні в автоматичному циклі.
- Конструкція виробу і його компонентів повинна забезпечувати вільний доступ робочих органів складального обладнання, інструментів і засобів контролю.
- Вироб та його компоненти повинні мати зручні поверхні для можливості захвату та маніпулювання в автоматичному режимі.
- Конструкція виробу повинна забезпечувати зборку при мінімальному числі напрямків збірки. Найбільш переважним повинен бути варіант одного напрямку збірки, що в максимальній мірі спрощує організацію складального процесу і конструкцію устаткування.
- Закономірним розвитком попередньої рекомендації буде адаптація конструкції виробу для складання в автоматичному циклі з тим розрахунком, що всі сполучення і з'єднання деталей виконуються застосуванням найпростішої кінематики рухів.
- Виріб і його складові елементи повинні маим необхідну стійкість та здатність до зберігання й переміщення.
- Складальні одиниці повинні бути кінематично замкнутими, тобто забезпечувати орієнтування, переміщення і маніпулювання без можливості розчленування на складові елементи.
На сьогоднішній момент високе значення приділяється як потребі проведення ретельної оцінки виробу на технологічність конструкції та адаптації до умов автоматичного складання, так і методиками цієї оцінки.
Існуючі методи визначення технологічності конструкції виробу з точки зору можливої ??автоматизації складальних процесів базуються на суб'єктивній оцінці. На сьогоднішній момент розробляються методики автоматизованої оцінки технологічності, що грунтуються на принципах абстрагування, диференціювання, зіставлення розглянутих об'єктів із аналогами з баз даних, а також математичній обробці результатів. Оцінка виробу на технологічність конструкції та адаптованість до умов автоматичного складання при своїй високій трудомісткості також вимагає відповідальності й компетентності експертних осіб. Як показує практика, саме на стадії розробки попереднього проекту та оцінки його перспектив допускається найбільша кількість помилок, і саме на початковому етапі роботи можна звести до мінімуму можливості виникнення проблем при реалізації проекту. Автоматизація оцінки технологічної підготовленості виробу до умов автоматичного складання дозволяє виключити суб'єктивний людський фактор і максимально точно оцінити максимально можливий і економічно обгрунтований необхідний рівень автоматизації виробничих процесів.
З відомих в даний час методів оцінки виробу на технологічність конструкції слід згадати методику А.Г. Холодкової (Московський державний відкритий університет) і повністю автоматизований проект програмного забезпечення B. Reifur (Вроцлавський технічний університет).
2.2 Аналіз існуючих методів автоматичного складання циліндричних виробів з зазором
Збірка гладких циліндричних з'єднань з гарантованим зазором в більшості випадків легко піддається автоматизації. Такі з'єднання можна збирати під дією сили тяжіння присоединяемой деталі і примусовим (силовим) методом. з>
Збірка під дією сили тяжіння можливо при вертикальному розташуванні осей сполучених деталей або положенні, близькому до вертикального (відхилення від вертикалі не більше 10 .. 15 про ), а також при значних зазорах в з'єднанні (у десятих частках міліметра), масі та розмірах деталей (не менше 0,05 кг і діаметром не менше 10 мм). Однак з'єднання деталей під дією гравітаційних сил може не забезпечувати високій надійності процесу, особливо при складанні відносно легких деталей і значному сумарному зміщенні осей відносно один одного [5].
При автоматичному складанні циліндричних деталей найчастіше використовується схема, в якій орієнтація деталей, що збираються на складальній позиції здійснюється за їх зовнішніх поверхнях в призмах. На початку циклу автоматичного складання вісь присоединяемой деталі може займати різні положення по відношенню до осі базової, при цьому осі деталей можуть перебувати в одній або різних площинах. До найбільш простим для реалізації схемами складання відносяться такі, в яких відсутні рухи, необхідні для поєднання осей деталей, що збираються [1].
Для автоматичного сполучення циліндричних деталей найчастіше використовують пристрої, які повідомляють однією з деталей, що сполучаються відносне обертання руху. Обертовий уловлювачі передає рух присоединяемой деталі таким чином, що вона в певний момент часу займає відносно базової таке положення, при якому подальший процес складання гарантується. По своїй фізичній сутності параметри, що визначають безвідмовність складального процесу, можна віднести до наступних груп.
- Конструктивні параметри (зазор в з'єднанні, номінальний діаметр з'єднання, сумарний розмір радіальних катетів фасок на сполучених поверхнях, довжина з'єднання).
- Параметри виконавчого механізму (зазор між уловлювачем і присоединяемой деталлю, відстань між торцями уловлювачів, жорсткість уловлювачі).
- Режими складального процесу (величини зусилля збірки, швидкість складального руху, кутова швидкість уловлювачі) [7].
Ефективна високопродуктивна автоматична збірка можлива лише при значній безвідмовності пристроїв автоматизації. Найбільша частка відмов автоматичного складання циліндричних з'єднань відбувається при проходженні сполучаються поверхнями зони фасок або крайок через те, що похибка взаємного орієнтування цих поверхонь більше допустимої для застосовуваного типу складального пристрою.
У способі автоматичного складання, запропонованому фахівцями Київського політехнічного університету, самоорієнтація сполучених циліндричних поверхонь відбувається під дією сили, точка прикладання якої переміщується по концентричному колу на торці присоединяемой втулки, встановленої в податливій пристосуванні, при контакті з нерухомо встановленим валом. Якщо втулка і вал стикаються торцями при деякому зсуві осей сполучених поверхонь, то сила, прикладена в певній зоні на зовнішньому торці втулки, викликає її поворот навколо осі, що проходить через дві точки контакту крайок сполучених поверхонь, і переміщення контактує з валом торця у бік зменшення ексцентриситету до торкання кромки втулки і утворює валу в третій точці. Можливий захоплення крайок, що перешкоджає поверненню втулки в початкове положення і обумовлює другий етап самооріентаціі, що полягає в тому, що точки дотику крайок сполучених поверхонь зближуються, поки не зіллються в одну точку. При цьому поступово зменшується перекіс осі втулки і до кінця другого етапу її вісь поєднується з віссю валу. Переміщення самооріентаціі сполучених поверхонь закінчуються, й відбувається складання [8].
На сьогоднішній день розроблено методика високопродуктивної збірки циліндричних з'єднань з гарантованим зазором для умов безперервного автоматичного циклу технологічного процесу. Суть методу полягає в тому, що в зоні збірки розташовують плоскі базуючі елементи, які вчиняють у площині, перпендикулярній напряму транспортування валика і втулки, зворотно-поступальний рух по заданому закону. Рух кожного елемента зрушено щодо попереднього на деякий фазовий кут таким чином, що в конкретний момент часу у частини базових елементів швидкість більше нуля, менше нуля або дорівнює нулю. Площина, дотична до базують поверхонь елементів, швидкості яких позитивні, утворює з площиною, дотичною до зв'язаних з розглянутими елементам, кінематичну призму, що забезпечує аерірованіе і транспортування деталей. Ступінчастий профіль базують елементів дозволяє співісний базувати сполучаються деталі з різними діаметрами базових поверхонь. Багаторазове повторення циклу зворотно-поступального руху через заданий період часу призводить до формування у зоні збірки ряду кінематичних призм, віддалених один від одного на постійний крок. Сталість кроку між складальними комплектами наближає потоки деталей до регулярних.
Внаслідок дії сил тертя між базовими поверхнями складального комплекту спостерігається їх обертальний рух. Так як діаметри базових поверхонь різні, то різниця кутових швидкостей валика і втулки обумовлює відносне обертання сполучених поверхонь. Наявність ексцентриситету між сопрягаемой і базовою поверхнею втулки призводить до відносного скануванню осей деталей в результаті спільного обертально-вібраційного впливу. При контакті торців сполучених поверхонь їх відносне переміщення за рахунок вібрації і обертання призводить до зниження сил тертя в напрямку дії зусилля збірки. Отже, поліпшуються умови самооріентірованія деталей [9].
Розглядом питань, пов'язаних з автоматизацією процесів складання рухливих циліндричних з'єднань, в різний час займалися такі автори, як О.В. Воронін, М.М. Стржемечний, Є.В. Писарєв, А.Г. Холодкова, Є.І. Кольчугін, В.М. Похмільних, Т.Ю. Родівіліна та інші.
2.3 Аналіз існуючих методик проектування технологічних процесів автоматичного складання
Технологічний процес складання включає в себе перелік необхідних дій по встановленню та структурованому утворенню з'єднаннь із складових компонентів виробу в заданій послідовності. Технологічний процес складання може складатися з однієї (одноопераційних) або пов'язаної безлічі (багатоопераційний) операцій збірки.
Класична послідовність проектування технологічного процесу складання включає в себе ряд етапів:
- Аналіз вхідних даних.
- Завдання граничних умов.
- Вибір організаційної форми складання.
- Оцінка технологічності конструкції виробу.
- Проведення розмірного аналізу конструкції виробу.
- Вибір технологічних баз і схем базування.
- Пошук раціональних методів складання з'єднань.
- Оцінка технологічних можливостей цеху та підбір обладнання і оснащення.
- Складання маршрутного технологічного процесу складання.
- Уточнення технологічних операцій складання.
- Нормування.
- Розрахунок економічної ефективності розглянутих варіантів технологічного процесу складання, вибір найбільш пріоритетним.
- Оформлення супровідної документації.
Проектування технологічного процесу складання має завершитися переліком задокументованих результатів. Як то:
- технологічна схема складання;
- пакет технологічних карт складання;
- пакет технологічних карт контролю;
- пакет технологічних інструкцій.
Схема збірки являє собою графічний документ послідовності складання оригінальних, нормальних, покупних деталей у вузлах і послідовність складання комплектів і вузлів. Такі схеми дозволяють прискорити освоєння збірки і комплектування її деталями, комплектами та вузлами [12].
Кожен складовий елемент виробу зображується на схемі у вигляді прямокутника, розділеного на три частини: у верхній частині дано найменування елемента; в лівій нижній - числовий індекс елемента за специфікацією; в правій нижній - число елементів, що входять в дане з'єднання. Технологічні схеми складання постачають написами-виносками, пояснюючими характер складальних робіт, коли вони неясні зі схеми [13].
В основу розробки технологічних процесів автоматичного складання покладено два принципи: технічний і економічний. Відповідно до технічного принципа спроектований технологічний процес автоматичного складання повинен повністю забезпечувати виконання всіх вимог робочого креслення та ТВ приймання виробу. У відповідність економічному принципу збірку виробу потрібно вести з мінімальними витратами уречевленої і живої праці і з мінімальними витратами виробництва [15].
Важливою умовою розробки раціонального технологічного процесу автоматизованого складання є уніфікація і нормалізація з'єднань, тобто приведення їх до певної номенклатурі видів і точностей. На основі уніфікації і нормалізації з'єднань у складальних одиницях і виробах розробляють типові складальні процеси, операції і переходи, що виконуються на типовому складальному обладнанні з використанням типових інструментів і пристосувань [14].
Процес проектування технологічних процесів автоматичного складання складається з комплексу взаємопов'язаних етапів, що виконуються в певній послідовності:
- Збір та аналіз вихідних даних.
- Відпрацювання виробу на технологічність під умови автоматичного складання, внесення в конструкцію виробу корективів.
- Проведення розмірного аналізу.
- Встановлення та затвердження методів здійснення з'єднань.
- Складання технологічних схем загальної та вузлової зборки.
- Складання маршруту збірки.
- Уточнення змісту операцій складання, коригування на основі оптимальних умов виконання з'єднань.
- Вибір типу автоматичного складального обладнання.
- Розробка і конструювання спеціального обладнання.
- Розрахунок економічних показників ефективності автоматизації.
Складання виробів варіативне. Методом математичного моделювання та перебору варіантів можна визначити оптимальну послідовність набору операцій і переходів для отримання заданої якості результату складання виробу.
В якості критеріїв досконалості (оптимальності) процесу складання приймають найменшу складність автоматизації збирання, найменшу вартість продукції при заданому її якості, тобто визначають такий варіант, який має мінімальний «потенціал» моделі. Для вирішення такого завдання розробляють топологічну модель, яка формалірованно описує всі можливі варіанти технологічного процесу, приводячи їх до мережевої моделі [2]. Мережеву модель складального процесу отримують математичним об'єднанням вихідних характеризуючих моделей першого типу [11] . На всіх етапах розробки і синтезу моделей використовується теорія логіко-динамічних графів.
Скорочення часу на операції та суміщення переходів можна досягти застосуванням відповідних схем побудови складальних операцій. До таких схем відносяться: одно-і багатомісні схеми, залежно від числа встановлюваних виробів на позицію збірки; одно-і багатоінструментальні схеми, залежно від числа одночасно застосовуваних при збірці інструментів. За послідовностю технологічних переходів операції можуть бути послідовними, паралельними і змішаного типу. При різному поєднанні зазначених схем утворюється комплекс схем побудови операцій, які відрізняються в значній мірі один від одного часом виконання операцій і собівартістю складання [4].
При побудові операцій складання слід враховувати те, що на їх проектування не повинні впливати особливості ручної збірки. Деякі прийоми, насилу здійснювані вручну, часто легко виконуються механізмами, і навпаки - окремі прийоми, легко здійснювані складальником, виконуються механізмами набагато складніше. Тому спроби копіювати ручну збірку зазвичай не дають добрих результатів [15]. При проектуванні методів виконання з'єднань на позиціях автоматичного складання слід приділяти увагу як класичними схемами складання, так і пошуку нестандартних рішень, орієнтованих на складання конкретного з'єднання.
При розробці технологічних операцій автоматичного складання визначають оптимальні режими збірки і знаходять настроювальні розміри для налагодження обладнання. Після прийняття схем побудови складальних операцій і виконання розрахунку режимів визначають вимоги, пропоновані до базуючих пристроїв, пристроїв відносної орієнтації, складальних голівок та іншим функціональним елементам складального обладнання, а також до обладнання в цілому. При проектуванні складних технологічних операцій, виконуваних на багатопозиційному складальному обладнанні, визначається завантаження обладнання по окремих позиціях і будуються циклограми його роботи [1].
Необхідним етапом проектування технологічного процесу автоматичного складання є розробка циклограми - допоміжного графічного документа, що відображає часові взаємозв'язки здійснення переліку операцій і переходів технологічного процесу.
Циклограма збірки виконує наступні задачі:
- Візуальне подання тимчасових взаємозв'язків між елементами технологічного процесу різного рівня (операції, переходи і т.д.).
- Візуальне подання витрат часу на здійснення всіх елементів технологічного процесу.
- Відкриття можливостей для точної синхронізації часу виконання заданих елементарних процесів усередині технологічного процесу складання.
- Відкриття широких можливостей для докладного аналізу технологічного процесу складання і можливості своєчасного внесення корективів на стадії технічного планування.
Створення технології автоматичного складання тісно пов'язане з глибоким вивченням сутності складальних процесів для виявлення закономірності їх перебігу та ефективного управління ними. На базі наукових і методичних основ автоматизації складання розробляються технологічні основи проектування складального автоматичного обладнання і створюються типові виконавчі пристрої, з яких за принципом агрегатування можна швидко компонувати автоматичне складальне обладнання різного цільового призначення. В основі цієї роботи повинна лежати типізація технологічних процесів складання [6].
3. Практичне значення
У роботі детально розглянуті всі аспекти і можливості автоматизації складальних процесів для умов випуску пневмо-і гідроапаратури, з метою розробки комплексу рекомендацій щодо підвищення рівня автоматизації складальних робіт з точки зору оптимізації за різного роду критеріями (продуктивність, економічний ефект, поліпшення умов праці та ін.)
4. Наукова новизна одержаних результатів
На даному етапі науково-дослідної діяльності питання про актуальність автоматизації збирання для умов виробництва конкретного типу продукції піднімається рідко, частіше акцент ведеться на оцінку річних обсягів випуску. У даній роботі розглянута актуальність підвищення рівня автоматизації складальних процесів вузлів пневмо-і гідроапаратури, підібрані і науково обгрунтовані методи та засоби підвищення рівня автоматизації, розроблено комплекс рекомендацій, спроектовано автоматичне складальне обладнання. Для оцінки та синтезу виробничо-технологічних процесів з метою їх реорганізації та оптимізації використовуються математико-статистичні методи вирішення завдань, теорія графів, алгебра логіки і алгебра множин.
Висновки
Відповідно до класичного підходу до вирішення проблеми автоматизації процесів складання, передумовами до її здійснення є стабільність і масовість випуску. Рішення про необхідність автоматизації на 90% залежить від обсягів випуску продукції і частки трудомісткості збірки в сукупному виробничому процесі. Також не останню роль в прийнятті рішення про автоматизацію складальних процесів грає метод досягнення точності остаточної ланки, який використовується на підприємстві та побічно і прямо впливає на організацію всього виробничого процесу.
Мабуть, основним стопором, який у корені перешкоджає всім спробам автоматизувати складальне виробництво, є складність і дорожнеча виготовлення машин-автоматів для майбутньої складальної лінії. Конструкція кожної машини повинна відповідати складанню конкретного з'єднання, а система автоматів в кінцевому підсумку - послідовно проводити повноцінне скадання виробу. Велика номенклатура виробів практично зводить нанівець сам принцип подібної організації - витрати на регулярну переналагодження і часті зміни конструкції автоматичної лінії здатні розорити будь-яке підприємство.
Основним економічним недоліком автоматизованих систем зборки слід назвати довгий термін окупності. В умовах досить нестабільної ринкової ситуації дозволити собі таку довгострокову стратегію можуть лише підприємства, твердо впевнені у своїй конкурентоспроможності в очах споживача.
Список джерел
- Замятін В.К. Технологія та оснащення складального виробництва: Довідник. - М.: Машинобудування, 1995. - 608 с.
- Лебедовсmкий М.С., Вейц В.Л., Федотов О.І. Наукові основи автоматичного складання. - Л.: Машинобудування, 1985. - 316 с.
- Балакшин Б.С. Основи технології машинобудування. - М.: Машинобудування, 1969. - 358 с.
- Косилов В.В. Технологічні основи проектування автоматичного складального обладнання. - М.: Машинобудування, 1976 - 382 с.
- Замятін В.К. Технологія та автоматизація збірки. - М.: Машинобудування, 1993. - 464 с.
- Новіков М.П. Основи технології складання машин і механізмів. - М.: Машинобудування, 1969. - 632 с.
- Інформаційний портал «Інновації бізнесу». Найменування проекту: Установка для автоматичного з'єднання циліндричних деталей з використанням обертового двигуна. Режим доступу: http://www.ideasandmoney.ru/Ntrr/Details/124950
- Хлебцевіч В.Д., Задерей О.М., Лапковський С.В. Підвищення ефективності автоматичного складання нестаціонарним додатком зусилля. Режим доступу: http://www.rusnauka.com/PRNIT_2006/Tecnic/15945.doc. htm
- Інформаційний портал «Інновації бізнесу». Найменування проекту: Пристрій для автоматичного складання деталей в кінематичних призмах. Режим доступу: http://www.ideasandmoney.ru/Ntrr/Details/125008
- Солодов М.Д., Золотаревський Ю.М. Методика розрахунку ймовірності безвідмовного виконання циліндричних з'єднань при автоматичному складанні. - Л.: Вісник машинобудування, 1976. - З 61-64.
- Лебедовский М.С. Автоматизація процесів у машинобудуванні. Ч-1. - Л.: СЗПІ, 1977. - 81 с.
- Картавов С.О. Технологія машинобудування (спеціальна частина). Вид. 2-е, перераб. і доп. - Київ.: Вища школа, 1974. - 272 с.
- Михайлов А.В., Расторгуєв Д.А., Схіртладзе О.Г. Основи проектування технологічних процесів машинобудівних виробництв: навчальний посібник. - Старий Оскол: ТНТ, 2010. - 336 с.
- Автоматизація виробничих процесів у машинобудуванні: Підручник для втузів / Н.М. Капустін, П.М. Кузнєцов, О.Г. Схиртладзе та ін Под ред. Н.М. Капустіна. - М.: Вища школа, 2004. - 415 с.
- Корсаков В.С. Автоматизація виробничих процесів. Підручник для вузів. - М.: Вища школа, 1978. - 295 с.