Реферат за темою випускної роботи
Зміст
- Вступ
- 1. Актуальність теми магістерської роботи
- 2. Мета і задачі дослідження
- 3. Основні напрямки вдосконалення технології безперервного розливання сталі і устаткування для її реалізації
- 4. Доцільність вдосконалення розливних систем проміжних ковшів МБЛЗ і необхідність розробки методики їх розрахунку
- 5. Дослідження і розробка вдосконаленої комплексної системи швидкої заміни занурювальних стаканів при серійному розливанні сталі на слябових МБЛЗ
- 5.1 Вдосконалення конструкції комплексної розливної системи проміжного ковша
- 5.2 Отримання теоретичних залежностей для розрахунку кінематичних і енергосилових параметрів маніпулятора механізованої заміни занурювального стакана
- 6. Фізичний аналог системи швидкої зміни занурювальних стаканів і його технічна характеристика
- Висновки
- Перелік використаної літератури
Вступ
Ідея заміни технології розливання металів у виливниці на безперервну відома досить давно – ще з середини XIX століття, але технологія безперервного розливання почала остаточно формуватися на рубежі 1950-60-х років, коли і отримала інтенсивне розповсюдження і широке впровадження у вигляді машин безперервного лиття заготовок (МБЛЗ) в країнах Західної Європи, СРСР, Японії, США. Нині безперервне розливання сталі освоєне більш ніж в 90 країнах світу. Успішно діє приблизно 1750 МБЛЗ, що дозволяє відливати на них більше 85% усієї сталі, яка виплавляється [1]. Приблизно 2/3 усього об’єму виплавляємої у світі сталі розливається на слябових МБЛЗ. При цьому у світі налічується більше 650 слябових МБЛЗ із загальним числом струменів понад 900 штук [2].
Безперервне розливання сталі істотно впливає на техніко-економічні показники сталеплавильного виробництва, тому що є його заключним етапом. Головними критеріями оцінки ефективності функціонування МБЛЗ являються її продуктивність і якість отримуваної заготовки. У зв’язку з цим значна частина науково-дослідних і конструкторських робіт, які виконані за останні роки в країні і за кордоном, були спрямовані на підвищення вказаних показників.
Продуктивність МБЛЗ залежить, як відомо, від швидкості витягування заготовки, яка у свою чергу регламентована інтенсивністю і рівномірністю відведення тепла від безперервнолитого злитка, що кристалізується. Для поліпшення умов формування кірочки злитка і підвищення кількості тепла, що відводиться в одиницю часу від його поверхні, провідні зарубіжні фірми запропонували ряд розробок, які пов’язані з вдосконаленням конструктивних елементів кристалізатора МБЛЗ, що дозволили підвищити швидкість розливання. Проте при цьому помітно стали проявлятися побічні ефекти, які пов’язані з турбулентним режимом руху потоків металу в об’ємі, обмеженому кірочкою безперервнолитого злитка, що утворюється. Для зниження міри їх негативного впливу на оптимальні умови формування кірочки злитка і глибини проникнення небажаних домішок в метал, що кристалізується, нині прибігають до використання дуже дорогих систем електромагнітного гальмування металевих потоків, що погіршує підсумкові економічні показники виробництва безперервнолитої заготовки. Тому в якості альтернативної міри, спрямованої на підвищення продуктивності сучасних МБЛЗ, слід визнати підвищення серійності розливання сталі, завдяки чому росте вихід придатного і зменшуються простої устаткування, пов’язані з технічними паузами, обумовленими зупинкою машини після завершення розливання декількох плавок і підготовкою її до чергового запуску [3-5].
1. Актуальність теми магістерської роботи
В умовах експлуатації слябових МБЛЗ реалізація розливання ізольованим від атмосфери струменем обумовлена відомими труднощами, які пов’язані з передчасним виходом з ладу занурювальних стаканів внаслідок ерозії їх поверхонь, що контактують з розплавом, або появи значного шару відкладень, які змінюють форму і розміри каналу і негативно впливають на умови організації потоків рідкої сталі в порожнині кристалізатора. Під час заміни занурювального стакана, що вийшов з ладу, навіть при короткочасному припиненні подачі рідкої сталі в кристалізатор на поверхні отримуваної заготовки утворюється так званий перетиск
, в зоні розташування якого метал вважається некондиційним, через що має бути вирізаний і відправлений в якості шихти на повторну переплавку.
Число плавок, що розливаються в серії, залежить від терміну служби вогнетривкої футерівки проміжного ковша і експлуатаційного ресурсу його систем, які забезпечують переливання сталі в кристалізатори МБЛЗ. Так, наприклад, кварцевий занурювальний стакан витримує розливання 1-3 плавок. Найбільш високу експлуатаційну стійкість забезпечують корундографітові занурювальні стакани, посилені спеціальним цирконовим поясом в зоні контакту з шлакоутворювальною сумішшю, що при певних технологічних заходах може збільшити тривалість їх роботи, дорівнювану терміну експлуатації футерівки промковша і стопора-моноблока (8-10 плавок) [1]. Проте, як показали промислові експерименти, технологічна стійкість занурювального стакана в цьому випадку лімітується швидкістю заростання його внутрішньої порожнини оксидами алюмінію, кремнію і ін. При цьому стакан може вийти з ладу вже після розливання 2,5-3 плавок, тобто значно менше терміну служби робочого шару футерівки промковша. Тому переваги безперервного розливання якісної сталі на слябову заготовку довгими і наддовгими серіями повною мірою проявляються у тому випадку, коли проміжний ківш МБЛЗ обладнаний системою швидкої зміни занурювальних стаканів, які захищають рідкий метал від вторинного окислення, що є одним із заходів по захисту струменя металу від кисню навколишньої атмосфери на ділянках проміжний ківш – кристалізатор і забезпечує досягнення необхідного рівня якості безперервнолитої заготовки.
У системах, які пропонуються потенційному споживачеві зарубіжними фірмами (Interstop Corp. (Швейцарія), Vesuvius Group (Бельгія) і Danieli & С. Officine Meccaniche S.p.A. (Італія)), заміна занурювального стакана супроводжується операціями, що виконуються вручну або із застосуванням спеціальних маніпуляторів з ручним приводом, що викликає певні незручності через відсутність вільного місця на робочій площадці біля промковша.
Вказані обставини послужили спонукальними мотивами до створення вдосконаленої системи швидкої заміни занурювальних стаканів, яка дозволяла б вирішити зазначені проблеми.
2. Мета і завдання дослідження
Метою цього дослідження є розробка і обґрунтування конструктивних і енергосилових параметрів системи швидкої заміни занурювальних стаканів, при функціонуванні якої виключалася б важка фізична праця обслуговуючого персоналу МБЛЗ, скорочувався час технологічної операції, мінімізувалися енергетичні витрати на її проведення і раціонально використовувалося вільне місце на робочій площадці.
Для досягнення поставленої мети необхідно вирішити наступні завдання:
- На основі порівняльного аналізу існуючих технічних рішень розробити вдосконалену комплексну систему швидкої заміни занурювальних вогнетривких стаканів.
- Розробити методику розрахунку кінематичних і енергосилових параметрів запропонованої системи.
- Провести перевірку правильності прийнятих технічних рішень і отриманих розрахункових залежностей на фізичному аналогу запропонованої системи.
- Видати рекомендації для промислового використання запропонованої розробки.
- Виконати оцінку техніко-економічної ефективності розроблених технічних рішень.
3. Основні напрямки вдосконалення технології безперервного розливання сталі і устаткування для її реалізації
Раціональна технологія безперервного розливання сталі є дуже важливим складовим елементом сталеплавильного виробництва, що визначає техніко-економічні показники роботи цеху і собівартість металопродукції. Нині головними умовами поліпшення показників техніко-економічної ефективності виробництва якісної заготовки на слябових МБЛЗ є підвищення її продуктивності шляхом збільшення серійності безперервного розливання і поліпшення якості заготовки за рахунок організації захисту сталі від вторинного окислення на ділянках сталерозливний ківш – проміжний ківш – кристалізатор.
Важливим етапом в отриманні конкурентоспроможних на ринку безперервнолитих заготовок є процес виробництва якісної сталі, який вимагає дотримання цілого ряду операцій по всьому технологічному ланцюгу, спрямованих на усунення або послаблення дії багатьох чинників, які негативно впливають на механічні характеристики і службові властивості металопродукції. Однією з таких операцій є захист сталі від вторинного окислення під час безперервного розливання. Ця операція вимагає екранування поверхні перетікаючого струменя металу на відкритих його ділянках. В ході багаторічних досліджень було встановлено, що найбільш ефективними засобами захисту безперервнорозливаємої якісної сталі є вогнетривкі труби і занурювальні стакани на ділянках сталерозливний ківш – промковш і промковш – кристалізатор відповідно. Але практика експлуатації слябових МБЛЗ свідчить, що реалізація розливання ізольованим від атмосфери струменем рідкої сталі, супроводжується труднощами, пов’язаними з передчасним виходом з ладу занурювальних вогнетривких стаканів. Кожна заміна занурювального стакана в ході розливання обумовлена його руйнуванням або заростанням внутрішньої порожнини і потребує зупинки на деякий час відповідного струменя МБЛЗ, що згодом вимагає видалення із заготовки тієї частини, яка знаходилася у процесі заміни безпосередньо в кристалізаторі. Тому часта заміна занурювавальних стаканів не просто порушує технологічний ритм розливання, але також підвищує відходи металу і знижує вихід придатного на 1…2 % [1].
Головною причиною виходу занурювальних стаканів з експлуатації є ерозійний знос в зоні шлакового пояса, заростання внутрішньої порожнини в зоні вихідного отвору і розтріскування верхньої частини виробу, пов’язане з підсосом повітря у стик між стаканом-дозатором і занурювальним стаканом, а також з утворенням подовжніх наскрізних тріщин при термоудару (недостатньому підігріванні стакана перед розливанням; наприклад, корундографітові занурювальні стакани перед початком розливання нагріваються до температури 1000-1100 °С).
Динаміка руху струменя сталі з промковша в кристалізатор представляється дуже важливою з точки зору експлуатації занурювального стакана [5]. Тому слід вважати перспективними розробки, які спрямовані на створення систем швидкої заміни занурювальних стаканів, використання яких дозволить виключити проблеми, що викликані перериванням струменя металу, що витікає з проміжного ковша в кристалізатор МБЛЗ.
4. Доцільність вдосконалення розливних систем проміжних ковшів МБЛЗ і необхідність розробки методики їх розрахунку
У процесі тривалого розливання форма і розміри каналів дозуючих і захисних стаканів, як відмічено раніш, можуть істотно змінюватися, що призводить до погіршення умов формування струменя і порушення швидкісних режимів витікання сталі. У зв’язку з цим проміжні ковші сучасних слябових МБЛЗ укомплектовані системами швидкої заміни занурювальних стаканів, розроблених відомими фірмами [6-8].
У системах, що пропонуються потенційному споживачеві зарубіжними фірмами (Interstop Corp.і Vesuvius Group) заміна занурювального стакана здійснюється у два етапи. Спочатку заздалегідь розігрітий резервний стакан вручну або за допомогою спеціального маніпулятора (рис. 4.1) встановлюють на приймальні напрямні розливного пристрою за відпрацьованим вогнетривом по ходу його можливого переміщення. Після відведення захватного пристрою маніпулятора убік в замковій частині розливної системи фіксують силовий гідроциліндр, центруючи його шток відносно подовжньої осі змінного вогнетривкого стакана. У необхідний момент, подавши з гідроакумулятора в порожнину гідроциліндра під надмірним тиском робочу рідину, впродовж доль секунди здійснюють одночасне переміщення обох занурювальних стаканів на задану відстань, внаслідок чого резервний вогнетривкий елемент практично без переривання струменя займає робочу позицію і виштовхує зношений, який потім видаляють з-під ковша (рис. 4.2). Після завершення операції зміни занурювального стакана силовий гідроциліндр від’єднують від замкового вузла розливного пристрою. При такій конструктивній схемі процес заміни занурювального стакана не може бути здійснений відразу ж після розміщення резервного вогнетривкого елементу на вихідній позиції із-за необхідності попереднього виконання декількох додаткових операцій по встановленню силового гідроциліндра, що вимагають певних витрат робочого часу. На деяких зарубіжних МБЛЗ для полегшення подачі гідроциліндра до розливного пристрою і подальшого відведення від нього передбачено застосування додаткового маніпулятора з ручним приводом, що викликає певні незручності через відсутність вільного місця на робочій площадці біля проміжного ковша [9].
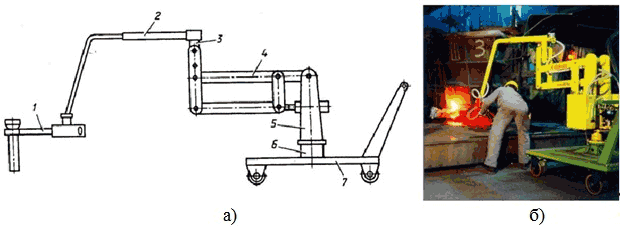
Рисунок 4.1 – Конструкція (а) і загальний вигляд маніпулятора (б) для швидкої зміни занурювальних стаканів фірми Interstop Corp. (Швейцарія):
1 – спеціальні кліщі; 2 – Г-подібна консоль; 3 – підйомний гідроциліндр; 4 – паралелограмний механізм; 5 – вертикальна стійка;
6 – поворотна опора; 7 – візок
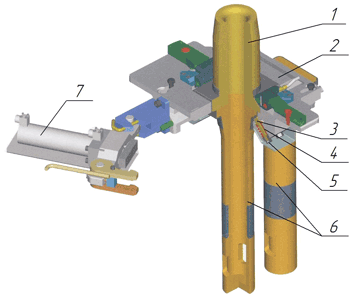
Рисунок 4.2 – Загальний вигляд пристрою фірми Vesuvius Group (Бельгія) для швидкої заміни занурювальних стаканів:
1 – розливний стакан; 2 – базова плита; 3 – штифт; 4 – вита пружина; 5 – різьбова пробка; 6 – змінний комплект занурювальних стаканів;7 – силовий гідроциліндр
У вказаних системах найважливішою конструктивною частиною є вузол притиснення змінного стакана до базового вогнетривкого блоку. Цей вузол в розливних пристроях зарубіжних фірм (рис. 4.3) включає дві групи коромисел, встановлених на осях симетрично по обидві сторони вогнетривкого стакана уздовж напряму його можливого переміщення. При цьому кожне коромисло одним кінцем давить на тильну частину сталевого кожуха стакана за рахунок сили стискування витої або тарілчастої пружини, що впливає на протилежний кінець коромисла.
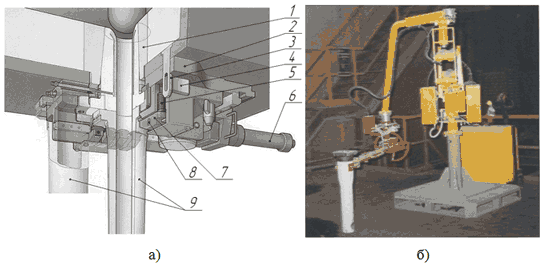
Рисунок 4.3 – Конструкція розливного пристрою (а) і маніпулятора (б) фірми Interstop Corp. (Швейцарія) для швидкої заміни занурювальних стаканів:
1 – розливний стакан; 2 – базова плита; 3 – штир; 4 – клин; 5 – блок пружин; 6 – силовий гідроциліндр;7 – важіль; 8 – вісь; 9 – змінний комплект занурювальних стаканів
Важливо зазначити, що із-за значної маси занурювальних стаканів при їх установці вручну на приймальні напрямні розливного пристрою обслуговуючий персонал переносить великі фізичні навантаженням, а обмежені умови вимагають забезпечення складної траєкторії руху резервного занурювального стакана в робочій порожнині кристалізатора. У зв’язку з цим актуальним завданням є механізація вказаних технологічних операцій за рахунок застосування спеціальних маніпуляторів, які б функціонували в комплексі з пристроями швидкої заміни занурювальних стаканів.
Вищезгадані обставини були враховані у ряді вітчизняних розробок систем швидкої заміни занурювальних стаканів. Наприклад, на кафедрі Механічне обладнання заводів чорної металургії
(МОЗЧМ) Донецького національного технічного університету за останні роки запатентовані і спроектовані декілька типів систем, що дозволяють практично без переривання розливання здійснювати заміну занурювальних стаканів, що екранують струмінь сталі на ділянці проміжний ківш – кристалізатор на слябовій МБЛЗ [10-13].
Комплекс, розроблений співробітниками кафедри МОЗЧМ ДонНТУ, включає розливну і маніпуляційну системи. Механічна частина запропонованої розливної системи відрізняється від зарубіжних аналогів тим, що силовий гідроциліндр безпосередньо з нею не пов’язаний, а розміщений стаціонарно на маніпуляторі. Крім того, були внесені зміни в конструкцію вузла притиснення занурювального стакана до базової вогнетривкої плити. Стакан своєю металевою обоймою спирається на кульки, що підтискаються пружинами, розміщеними в похилих каналах, в які зовні угвинчені різьбові пробки. Застосування тіл кочення в опорному вузлі дозволило зменшити силу опору переміщенню занурювального стакана і понизити інтенсивність зносу контактних поверхонь взаємодіючих елементів розливного пристрою. Маніпуляційна система зображена на рис. 4.4.
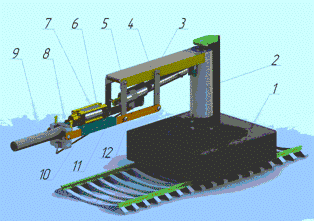
Рисунок 4.4 – Маніпуляційна система для швидкої заміни занурювальних стаканів конструкції кафедри МОЗЧМ ДонНТУ:
1 – візок; 2 – поворотна колона; 3 – горизонтальна консоль; 4, 5 – планки; 6 – важіль; 7 – силовий циліндр; 8 – скоба; 9 – резервний занурювальний стакан; 10 – тяга; 11 – палець; 12 – корпус циліндра
Розроблена конструктивна схема пристрою дозволяє реалізувати необхідний закон руху резервного занурювального стакана в обмеженому просторі за допомогою лише одного силового циліндра, що вигідно відрізняє її від зарубіжних аналогів. Проте, маніпулятор, що входить до складу вказаної системи, розташовується на робочій площадці зі сторони торцевої частини проміжного ковша. Така схема відносного розміщення маніпулятора повною мірою відповідає умовам розливання сталі на однострумових МБЛЗ, проміжні ковші яких переводяться в робочу позицію за допомогою підйомно-поворотних столів. На машинах з більшим числом струменів заміну проміжного ковша здійснюють, як відомо, з використанням самохідного візка, що рухається у напрямі його подовжньої осі. В цьому випадку маніпулятор є перешкодою візку, який переміщується, що ускладняє його експлуатацію.
Результати виконаного аналізу свідчать про те, що подальше підвищення продуктивності слябових МБЛЗ стримується відсутністю конструктивно простих і надійних в експлуатації пристроїв швидкої заміни занурювальних вогнетривких стаканів. Тому роботи, пов’язані з розробкою нових, більш досконаліших розливних систем, і методів розрахунку їх конструктивних і енергосилових параметрів необхідно вважати важливим науково-практичним завданням.
Результати літературного і патентного пошуку, виконаного за проблемою, який вивчається, свідчать, що останніми роками практично відсутні роботи з викладеними в доступній формі методологій розрахунку конструктивних і енергосилових параметрів зразків устаткування, введених в експлуатацію за розглянутий п’ятнадцятирічний період. Це обумовлено прагненням зарубіжних розробників захистити свої технічні секрети від можливих конкурентів, тому вони, як правило, обмежуються наданням інформації, що носить рекламний характер. Відсутність результатів теоретичних і практичних досліджень нового металургійного устаткування вносить значні ускладнення в подальший розвиток і вдосконалення функціональних систем МБЛЗ.
5. Дослідження і розробка вдосконаленої комплексної системи швидкої заміни занурювальних стаканів при серійному розливанні сталі на слябових МБЛЗ
В умовах безперервного розливання сталі довгими серіями із застосуванням захисних занурювальних стаканів стабілізація швидкісних режимів витікання металу з проміжного ковша в кристалізатор МБЛЗ є важливим технологічним завданням, рішення якого вимагає створення спеціальних пристроїв, що дозволяють при необхідності здійснювати швидку заміну вогнетривкого елементу, який екранує струмінь розплаву від навколишньої атмосфери [3, 4, 14].
Практика експлуатації подібних пристроїв на ряду зарубіжних і вітчизняних металургійних підприємств показала, що ефективність їх застосування значно підвищується якщо вони працюють в комплексі з маніпуляторами, які забезпечують механізовану подачу на приймальні напрямні розливного пристрою проміжного ковша заздалегідь розігрітого до необхідної температури резервного вогнетривкого виробу, який повинен за долі секунди під дією силового циліндра змінити стакан, що вийшов з ладу.
Різноманіття схем відносного розташування устаткування сучасних МБЛЗ і особливості його функціонування є головними передумовами для розробки систем швидкої заміни занурювальних стаканів, які в найбільшій мірі відповідають умовам безперервного розливання металу конкретного сталеплавильного цеху.
5.1 Вдосконалення конструкції комплексної розливної системи проміжного ковша
Враховуючи переваги і недоліки, виявлені при експлуатації зарубіжних зразків устаткування, призначеного для виконання механізованої заміни занурювальних стаканів в умовах серійного розливання сталі на слябових МБЛЗ, пропонується нова конструктивна схема системи швидкої заміни захисних вогнетривких елементів, що включає стаціонарно розміщеного на робочій площадці маніпулятор і закріплений на зовнішній поверхні днища проміжного ковша розливний пристрій, забезпечений занурювальним вогнетривким стаканом. Маніпулятор (рис. 5.1) дозволяє в заданій послідовності без застосування дорогих засобів автоматики забезпечити подачу змінного занурювального стакана по розрахунковій траєкторії на приймальні напрямні розливного пристрою проміжного ковша і силового гідроциліндра, що здійснює по команді переміщення стакана з вихідної позиції в робочу.
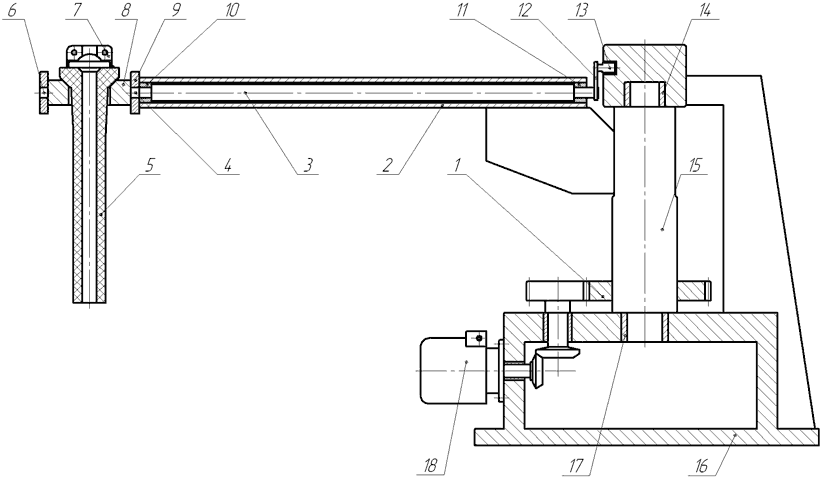
Рисунок 5.1 – Схема розробленої системи швидкої зміни занурювального стакана:
1 – зубчастий вінець; 2 – порожниста консоль; 3 – трансмісійний вал; 4,6 – цапфи; 5 – змінний занурювальний стакан; 7 – силовий гідроциліндр; 8 – скоба; 9 – платформа; 10,11 – підшипникові опори; 12 – важіль; 13 – ролик; 14,17 – верхня і нижня підшипникові опори; 15 – поворотна колона; 16 – основа; 18 – електромеханічний привід
Принцип роботи пропонованої системи швидкої заміни занурювальних стаканів пояснює рисунок 5.2. Під час серійного розливання сталі маніпулятор розташований у вихідній позиції на робочій площадці 19 перед проміжним ковшем 20, обладнаним розливним пристроєм 21, забезпеченим захисним стаканом 22, нижня частина якого занурена в розплав, що знаходиться в кристалізаторі 23. У цій позиції поворотна колона 15, консоль 2 і несуча скоба 8 з встановленим у ній змінним занурювальним стаканом 5 займають відносне положення, показане на рисунку 5.2, а. При цьому розігрітий до потрібної температури змінний стакан 5 розташований горизонтально і утримується затискачами несучої скоби, яка розвернута у вирізі платформи 9. Фіксація скоби зі стаканом щодо платформи забезпечена трансмісійним валом, важіль 12 якого своїм роликом 13, що знаходиться в профільованому спрямовуючому пазу, утримує вказані елементи механізму в заданому положенні.
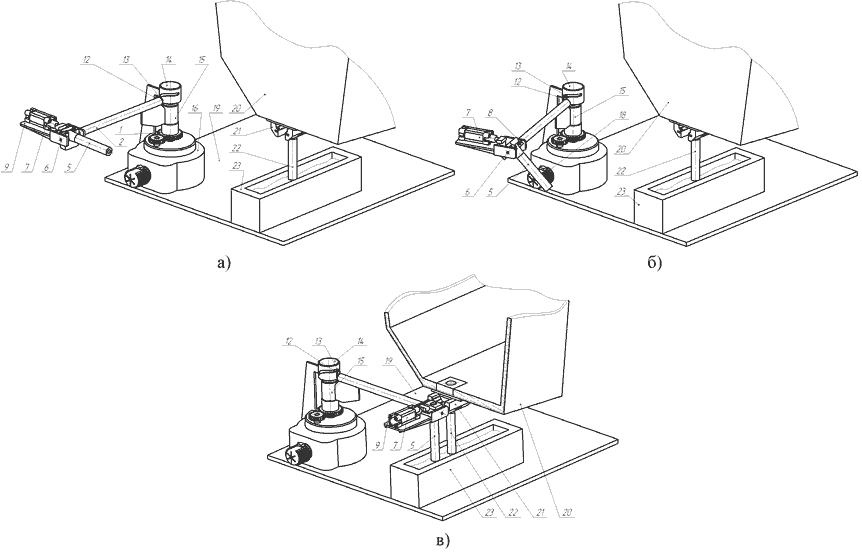
Рисунок 5.2 – Послідовність виконання операції швидкої заміни занурювальних стаканів
Для заміни занурювального стакана необхідно включити привід 18, який через зубчасті передачі і вінець 1 здійснює поворот колони 15 в нижній і верхній 14 нерухомих підшипникових опорах. Разом з колоною обертається пустотіла консоль 2 і встановлений усередині неї в підшипникових опорах 10 і 11 трансмісійний вал 3 (рис. 5.1) з прикріпленим важелем 12. Ролик 13, перекочуючись по горизонтальній ділянці профільованого направляючого паза, який виконаний на зовнішній циліндричній поверхні верхньої нерухомої опори 14, буде забезпечувати незмінність положення важеля 12, трансмісійного вала 3 і пов’язаної з ним цапфою 4 несучої скоби 8, яка утримує паралельно робочій площадці змінний занурювальний стакан 5. У момент переходу криволінійної ділянки направляючого паза ролик 13, що впливає на кінець важеля 12, змушує повертатися трансмісійний вал в опорах 10 і 11 (рис. 5.1) щодо горизонтальної консолі 2. Обертання валу 3 через цапфу 4 (рис. 5.1) і передається скобі 8, яка здійснює поворот відносно платформи 9 змінного занурювального стакана 5 (рис. 5.2, б) до повного його переведення у вертикальне положення. Це переведення завершиться при підводі стакана до торця розливного пристрою 21 і розташуванні його співвісно з напрямними. Після цього силовим гідроциліндром 7, що розташований на платформі 9, змінний стакан 5 переміщається по напрямних розливного пристрою 21 до тих пір, поки він не займе місце занурювального стакана, що вийшов з ладу, 22, який екранує струмінь сталі, що витікає з проміжного ковша 20 в кристалізатор 23 (рис. 5.2, в). Швидкість переміщення стаканів така, що процес їх заміни триває 0,2...0,3 с, тобто практично без переривання струменя рідкої сталі. Замінений занурювальний стакан видаляють з напрямних пазів розливного пристрою за допомогою спеціального пристосування, а консоль маніпулятора повертається у вихідну позицію при повороті колони у зворотному напрямі. У вихідній позиції елементи конструкції маніпулятора не перешкоджають переміщенню візка з проміжним ковшем при аварійному з’їзді або в разі передачі ковша на ремонтну площадку для заміни його футерівки [15].
З метою оптимізації енергосилових параметрів процесу заміни вогнетривких елементів і зниження сили тертя між контактними поверхнями металевої обойми занурювального стакана і опорної частини розливного пристрою промковша МБЛЗ, що викликає інтенсивний знос контактної поверхні притискних елементів та вимагає їх частої заміни, при розробці вдосконаленої конструкції розливного пристрою вирішувалося завдання зі зниженню сил тертя між контактними поверхнями його рухливо сполучених елементів шляхом зміни в розливному пристрої конструктивного виконання вузла притиснення занурювального стакана.
Для вирішення поставленого завдання модернізований розливний пристрій (рис. 5.3), включає металевий корпус 1, забезпечений засобами кріплення у вигляді штирів 2 з отворами під клини 3 до зовнішньої поверхні днища проміжного ковша 4. Корпус 1 має центральний вертикальний отвір, в якому розміщена нижня частина сталевипускного стакана 5, закріпленого в гніздовому блоку 6. У тілі корпусу 1 виконаний подовжній направляючий паз для розміщення робочого 7 і резервного 8 вогнетривких занурювальних стаканів, верхні частини яких поміщені в металеві обойми.
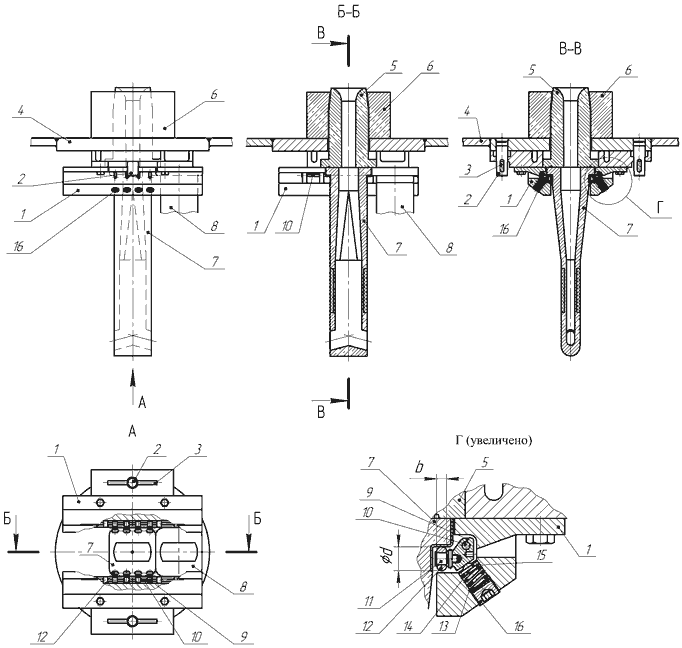
Рисунок 5.3 – Конструкція вдосконаленого розливного пристрою
Занурювальний стакан 7 примикає знизу до сталевипускному стакана 5 і встановлений з можливістю переміщення уздовж подовжнього паза силовим гідроциліндром, змонтованим на платформі маніпулятора. Притискання занурювального стакана до нижньої частини сталевипускного стакана здійснюється механізмом, який включає поворотні елементи 9 з отворами, симетрично встановлені на осях 10 по обидві сторони занурювального стакана 7 уздовж осі його переміщення в направляючому пазу металевого корпусу 1. Причому кожен поворотний елемент 9 забезпечений консольно закріпленим пальцем 11, що несе ролик12, який вільно обертається. Тіло ролика має форму поверхні обертання з твірною у вигляді дуги радіусом 0,5b…0,5d, де b і d – відповідно товщина в поперечному перерізі симетрії ролика і його зовнішній діаметр, пов’язані співвідношенням d/b=2…2,5. Завдяки вказаним значенням геометричних параметрів ролика забезпечується його постійний контакт з опорною поверхнею металевої обойми вогнетривкого стакана незалежно від кута повороту елементу, який несе сам ролик.
Передача зусилля притиснення занурювальному стакану здійснюється завдяки кінематичному зв’язку поворотних елементів із заздалегідь стиснутими пружинами 13, які встановлені у виконаних в корпусі 1 похилих циліндричних каналах на направляючих стрижнях 14 із притисненням до їх підпірних буртиків 15 за допомогою угвинчених в циліндричні канали пробок 16. Кожна з пробок своєю торцевою частиною виходить назовні металевого корпусу 1. Для обертання пробок на їх вихідних торцевих частинах передбачені шліци під викрутку або голівки під ключ [16].
Розроблена вдосконалена система швидкої заміни занурювальних стаканів при серійному розливанні сталі на слябових МБЛЗ вигідно відрізняється від відомих зарубіжних аналогів тим, що при її використанні забезпечується механізоване виконання усіх операцій, пов’язаних з подачею і установкою змінного вогнетривкого елементу на розливний пристрій, кріпленням до нього силового гідроциліндра і подальшим виведенням його із зони інтенсивної теплової дії, викликаної випромінюванням рідкої сталі, яка знаходиться в кристалізаторі. Завдяки застосуванню в опорному вузлі розливного пристрою притискних елементів, забезпечених роликами, істотно знижується навантаження на гідропривід за рахунок зменшення сили тертя між рухливими контактними поверхнями, усувається їх інтенсивний знос, у зв’язку з чим скорочуються експлуатаційні витрати, пов’язані з необхідною витратою зношуваних деталей і проведенням ремонтних робіт по їх періодичній заміні.
5.2 Отримання теоретичних залежностей для розрахунку кінематичних і енергосилових параметрів маніпулятора механізованої заміни занурювального стакана
До складу запропонованої системи швидкої заміни занурювальних стаканів входять комбінований електромеханічний привід, що забезпечує одночасний поворот колони з консоллю в горизонтальній і змінного стакана у вертикальній площинах, і гідравлічний, здійснюючий прискорене переміщення замінюваного і нового стаканів по напрямним розливного пристрою. При цьому розрахунок енергосилових параметрів гідравлічного приводу необхідно розглядати стосовно конкретної конструктивної схеми вузла притиснення вогнетривкого стакана. Розглянемо кінематичні і енергосилові параметри електромеханічного приводу.
Для виконання силового розрахунку важільного механізму використаний принцип Д’Аламбера, згідно з яким рухлива система тіл знаходиться в кожен момент часу в рівновазі під дією зовнішніх сил, включаючи і сили інерції. При цьому розділимо механізм на дві структурні групи (рис. 5.4) і розрахунок розпочнемо з останньої з них [17]. До її складу (рис. 5.4, а) входять встановлена на цапфах в підшипникових опорах D і Е скоба, що несе змінний занурювальний стакан.
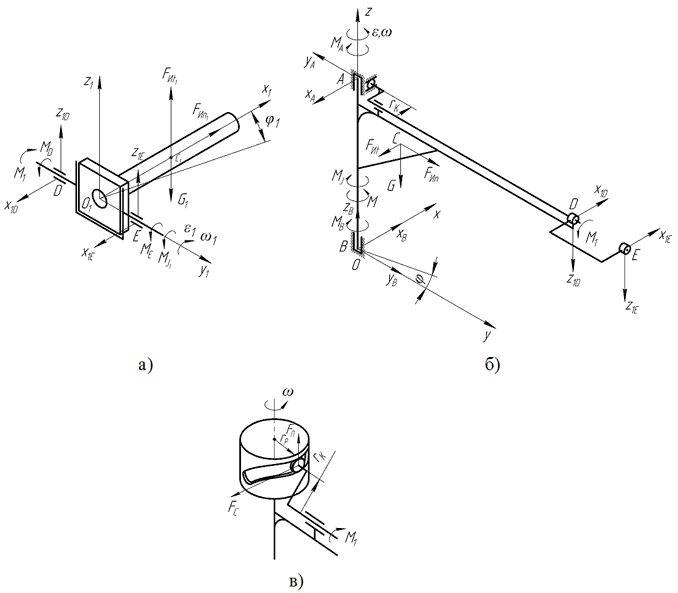
Рисунок 5.4 – Розрахункова схема механічного приводу системи швидкої заміни занурювальних стаканів
В період пуску приводу маніпулятора на ланки даної структурної групи діють сили тяжіння стакана Gст і скоби Gск; опір тертя в підшипникових опорах D і E, викликаний силами реакцій; сили інерції; момент, прикладений до цапфи скоби і необхідний для подолання вказаних сил.
Вибираємо систему координат, орієнтуючи напрям осі Y1 перпендикулярно подовжній осі симетрії консолі. Від осі Х1 вестимемо відлік кута повороту змінного стакана φ1.
Заздалегідь знаходимо координати центру тяжіння системи С1 (хС1, yC1, zC1), в якому прикладені сумарна сила тяжіння G1 = Gст + Gск.
Визначаємо сили інерції, що виникають при повороті скоби зі стаканом навколо осі Y1 з кутовим прискоренням ε1 і кутовою швидкістю ω1.
При обертальному русі дотична FИt1 і нормальна FИn1 сили інерції рівні:
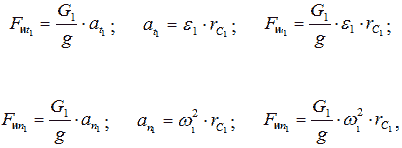
где rC1 – відстань від осі обертання до центру тяжіння системи С1:
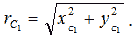
Положення центру тяжіння С1 в площині O1Х1Z1 виразимо через кут φ1:

Сили інерції FИt1 і FИn1 прикладені в точці К1, положення якої визначається по формулі:
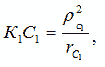
де ρc1 – радіус інерції системи відносно осі, що проходить через центр тяжіння С1 паралельно осі обертання.
Переносимо сили FИt1 і FИn1 в точку С1. Силу FИn1 переносимо по лінії дії. Силу FИt1 переносимо паралельно в точку С1 з додаванням пари, момент якої рівний:
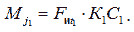
Підставивши в цей вираз значення FИt1 і К1С1 , отримаємо:
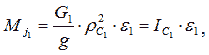
де IC1 – момент інерції поворотної системи відносно горизонтальній осі, що проходить через центр тяжіння С1:
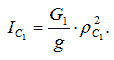
Момент Мj1 спрямований убік, протилежний до напряму обертання елементів системи. Усі сили інерції, що діють на поворотну систему, розташовані в одній площині, перпендикулярній осі обертання скоби зі стаканом Y1. Прикладені до системи сили і моменти: M1 – момент, що діє на цапфу скоби; МЕ і МD – моменти від сили тертя в опорах E і D; X1D, X1E, Z1D, Z1E складові реакцій в цих опорах.
Складемо рівняння рівноваги за законами статики:
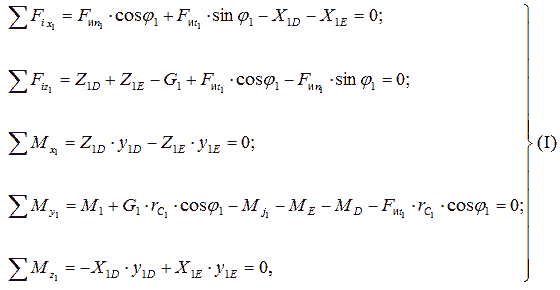
де y1D, y1E – плечі сил;
МD, ME – моменти тертя в опорах поворотної скоби:
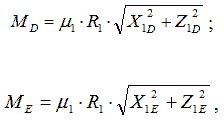
де R1 – радіус опор E і D;
μ1 – коефіцієнт тертя в опорах Е і D.
Вирішуємо систему рівнянь (I) і знаходимо реакції опор E, D і момент М1, прикладений до цапфи скоби для подолання статичних і динамічних навантажень при її повороті разом зі змінним стаканом:
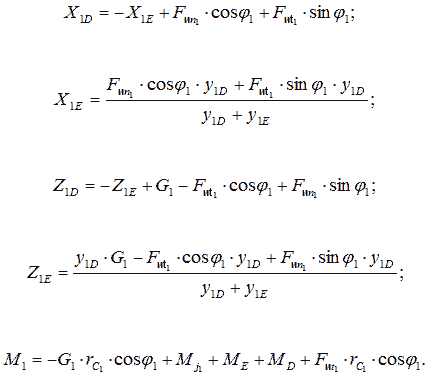
Отримані значення М1 і реакцій опор використовуємо при силовому розрахунку першої групи, що включає поворотну колону і консоль. Момент М1 прикладемо до трансмісійного валу зі зміненим напрямом на протилежний, а реакції опор E і D – до платформи консолі, змінивши їх напрям (рис. 5.4, б). Разом з цим на елементи системи діють сили тяжіння колони Gкол і консолі Gкон; моменти МА і МВ від сил тертя в підшипникових опорах А і В поворотної колони, викликані силами реакцій XА, YА, XВ, YВ в цих опорах; сили інерції; момент М на зубчастому колесі колони, необхідний для подолання вказаних сил.
Вибираємо систему координат і знаходимо координати центру її тяжіння С (xC, yC, zC), в якому прикладена сумарна сила G = Gкол + Gкон. Розраховуємо сили інерції, що виникають при повороті колони з консоллю навколо осі Z з кутовим прискоренням ε і кутовою швидкістю ω.
При обертальному русі дотична FИt і нормальна FИn сили інерції рівні:
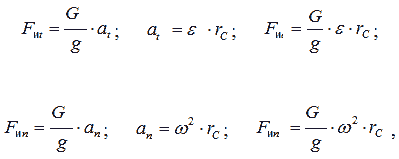
де rC – відстань від осі обертання до центру тяжіння системи С:
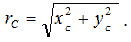
Положення центру тяжіння С виражаємо через кут φ:

Момент пари сил, що додається, при перенесенні сили інерції FИt в точку С рівний:

де IC – момент інерції поворотної системи відносно вертикальної осі, що проходить через центр тяжіння С:
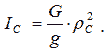
Момент Mj спрямований у бік, протилежний до напряму обертання елементів виділеної системи. Усі сили інерції, що діють на поворотну систему, розташовані в одній площині, перпендикулярній осі обертання колони Z. Крім того, до системи прикладені: М – момент на зубчастому колесі колони; МА, МВ – моменти від сил тертя в опорах А і В; складові реакцій в цих опорах XА, YА, XВ, YВ, ZВ; складові реакцій в опорах D, E і момент М1, що діють з боку елементів першої структурної групи.
Заздалегідь приведемо до осі поворотної колони момент М1, прикладений до трансмісійного валу. Відповідно до схеми вантаження ролика (рис. 5.4, в) на нього діє сила Fп, що притискає його до направляючої поверхні паза, і сила опору його переміщенню Fс.
Сила притиснення ролика:

де rк – довжина важеля, який несе ролик.
Сила опору, що діє на ролик при його переміщенні в спрямовуючому пазу:
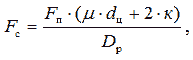
де μ – коефіцієнт тертя ковзання в опорі ролика;
dц – діаметр цапфи ролика;
к – коефіцієнт тертя кочення;
Dр – діаметр ролика.
Момент опору повороту колони, викликаний дією сили Fс:
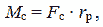
де rр – відстань від осі поворотної колони до направляючої поверхні паза, по якій перекочується ролик.
Складемо рівняння рівноваги за законами статики:
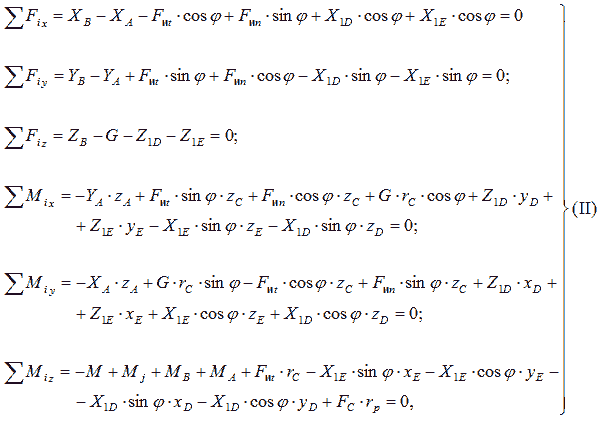
де xC, xE, xD, yC, yE, yD, zA, zC, zD, zE – плечі сил;
МА, МВ – моменти тертя в опорах вертикального валу:

де R – радіус опор A и B;
μ1 – коефіцієнт тертя в опорах A і B;
dц – діаметр підп’ятника в опорі В;
μ2 – коефіцієнт тертя в підп’ятнику опори В.
Вирішуємо систему рівнянь(II) і знаходимо реакції опор А і В, а також момент М, прикладений до приводного колеса для подолання статичних і динамічних навантажень при повороті колони з консоллю і одночасному відносному розвороті скоби зі стаканом:
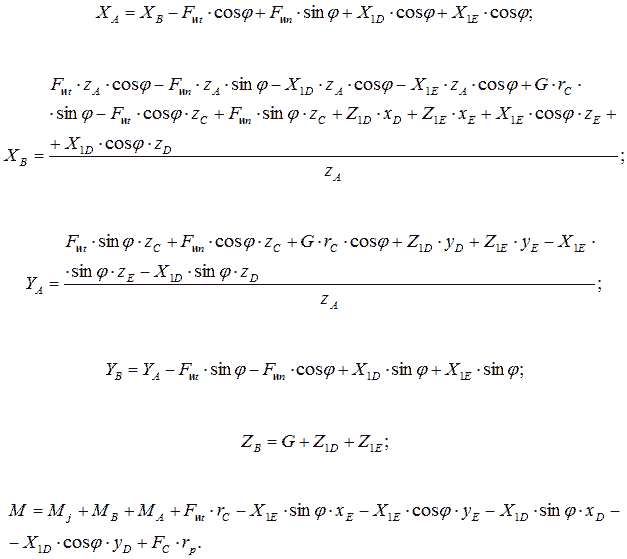
Потужність електродвигуна, що використовується в приводі маніпулятора, визначається з виразу:
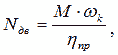
де ωк – необхідна кутова швидкість повороту колони;
ηпр – к.к.д. приводу маніпулятора.
Сумарне передатне число понижувальних передач приводу маніпуляційної системи:

де ωдв – кутова швидкість вибраного по каталогу електродвигуна;
ωк – необхідна кутова швидкість повороту колони.
6. Фізичний аналог системи швидкої зміни занурювальних стаканів і його технічна характеристика
Для перевірки правильності прийнятих технічних рішень і коректності отриманих розрахункових залежностей, а також з метою внесення відповідних коригувань в технічну документацію на стадії проектування промислового зразка системи швидкої заміни занурювальних стаканів для серійного розливання сталі був розроблений, спроектований і виготовлений фізичний аналог досліджуваної механічної системи.
Фізичний аналог маніпулятора (рис. 6.1) був виготовлений для лабораторних умов на базі наявної моделі проміжного ковша і кристалізатора. При проектуванні фізичного аналога маніпулятора використовувалася методика розрахунку енергосилових і конструктивних параметрів системи швидкої заміни занурювальних стаканів при безперервному розливанні сталі [17] з урахуванням габаритів лабораторної моделі проміжного ковша, виготовленого з органічного скла з розмірами 2000×500×600 мм. Масштаб фізичної моделі конструкції маніпулятора дорівнює 1 : 2,5. Технічна характеристика фізичного аналога системи швидкої заміни занурювальних стаканів приведена в таблиці 6.1.
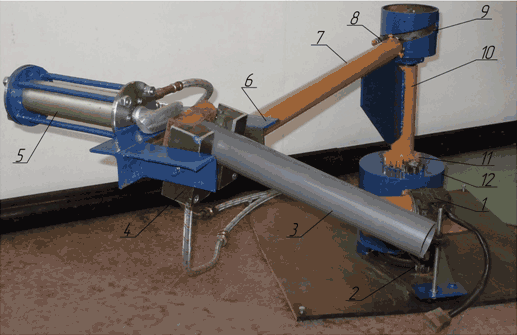
Рисунок 6.1 – Фізична модель пропонованої конструкції маніпулятора:
1 – електромеханічний привід; 2 – швидкохідна циліндрична зубчаста передача; 3 – модель занурювального стакана; 4 – скоба;
5 – силовий гідроциліндр; 6 – платформа; 7 – консоль; 8 – ролик; 9 – профільований направляючий паз на зовнішній циліндричній поверхні корпусу верхньої нерухомої підшипникової опори; 10 – поворотна колона; 11 – тихохідна циліндрична зубчаста передача; 12 – основа маніпулятора
Для приведення маніпулятора в роботу використовується мотор-редуктор постійного струму МЭ14А, який працює від джерела живлення 12 В. З метою забезпечення необхідного передатного числа були спроектовані і виготовлені швидкохідна 2 і тихохідна 11 відкриті циліндричні зубчасті передачі.
Параметр | Значення |
Маніпулятор: | |
– потужність електродвигуна, кВт | 0,03 |
– частота обертання електродвигуна, об/хв | 1500 |
– передатне число мотор-редуктора | 120 |
– передатне число швидкохідної зубчастої передачі | 6 |
– передатне число тихохідної зубчастої передачі | 2 |
– маса, кг | 36 |
Розливний пристрій: | |
– маса занурювального стакана, кг | 6 |
– тривалість заміни стакана, с | 0,3…0,5 |
– діаметр ролика притискного елементу, мм | 20 |
– число притискних елементів | 8 |
– маса пристрою, кг | 20,8 |
Силовий гідроциліндр: | |
– діаметр поршня, мм | 32 |
– діаметр штока, мм | 20 |
– хід штока, мм | 160 |
– швидкість переміщення штока, м/с | 0,5 |
– робочий тиск, МПа | 1,25 |
– маса, кг | 4,8 |
Після зборки моделі аналога маніпулятора і розміщення його біля об’ємної моделі проміжного ковша здійснили тестування функціонування механізмів при імітації швидкої заміни занурювального стакана, що вийшов з ладу. Аналогічні випробування були проведені і на 3D моделі запропонованої системи, яка заздалегідь була побудована за допомогою систем автоматичного проектування (САПР) КОМПАС- 3D і SolidWorks. Послідовність виконуваних операцій показана на рисунку 6.2.
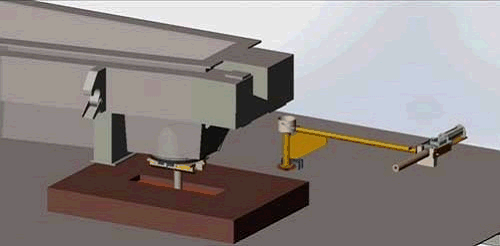
Рисунок 6.2 – Принцип роботи системи швидкої заміни занурювальних стаканів
(анімація: 5 кадрів, 5 циклів повторення, 160 кілобайт)
Тестування фізичного аналога і 3D моделі системи швидкої заміни занурювальних стаканів для серійного розливання сталі на слябових МБЛЗ підтвердило працездатність усіх її структурних елементів; маніпулятор дозволяє реалізувати задану траєкторію руху в просторі змінного вогнетривкого стакана з вихідної позиції в робочу і здійснити механізовану операцію по його швидкій заміні.
Висновки
Таким чином, розробки, що спрямовані на створення систем швидкої заміни занурювальних стаканів, використання яких дозволить виключити проблеми, викликані перериванням струменя металу, що витікає з проміжного ковша в кристалізатор МБЛЗ під час розливання, є найбільш перспективними.
Запропонована комплексна система є більше універсальною порівняно з відомими вітчизняними і зарубіжними аналогами, оскільки дозволяє здійснювати швидку заміну занурювальних стаканів на слябовій МБЛЗ при будь-якому числі струменів і різному типі пристроїв, що здійснюють транспортування проміжного ковша з робочої позиції в резервну.
Розроблена методика розрахунку дозволяє обґрунтувати і раціоналізувати конструктивні і енергосилові параметри комплексної системи швидкої заміни занурювальних стаканів, зокрема скоротити загальний час проведення технологічної операції, мінімізувати енергетичні витрати на її виконання, і раціонально використати вільне місце на робочій площадці.
З впровадженням системи швидкої зміни занурювальних стаканів скорочується тривалість технологічної операції зі зміні занурювального стакана скорочується на 42% з 1,2 хв до 0,7 хв, при цьому заміну здійснює один оператор (замість 2-3 чоловік), фізична праця якого у важких умовах зведена до мінімуму.
При написанні даного реферату магістерська робота ще не завершена. Остаточне завершення: січень 2014 року. Повний текст роботи та матеріали по темі можуть бути отримані у автора або його керівника після вказаної дати.
Перелік використаної літератури
- Процессы непрерывной разливки / А.Н. Смирнов, В.Л. Пилюшенко, А.А. Минаев и др. – Донецк: ДонНТУ, 2002. – 536 с.
- Смирнов А.Н., Куберский С.В., Штепан Е.В. Непрерывная разливка стали. – Донецк: ДонНТУ, 2011. – 482 с.
- Jungreithmeier A., Pessenberger E., Burgstaller K/ Production of UL CIF Steel Gradies at Voest-Alpine Stahl GmbH // Iron and Steel Technology. – 2004. – Vol. 1. №4. – P. 41-48.
- Еронько С.П., Быковских С.В. Разливка стали: Оборудование. Технология. – К.: Техніка, 2003. – 216 с.
- Металлургические мини-заводы / А.Н. Смирнов, В.М. Сафонов, Л.В. Дорохова и др. – Донецк: НОРД-ПРЕСС, 2005. – 469 с.
- New generation ladle slide gate system for performance improvement / J. Chaudhuri, G. Choudhury, S. Kumar, V. Rajgopalan // MPT International. – 2007. – Vol.30, №6. – pp. 38- 42.
- Mutsaarts P. Submerged entry nozzle exchange system for tundishes / Millennium Steel. – 2006. –pp. 143-146.
- Achieving higher perfomance & longer service life of Slide Plate / J. Chaudhuri, G. Choudhury, S. Kumar et. al. // Iron & Steel Review. – 2007. – June. – pp. 86-91.
- Еронько С.П., Сотников А.Л., Ткачев М.Ю. Совершенствование системы быстрой смены погружных стаканов для серийной разливки стали на слябовых МНЛЗ // Металлургические процессы и оборудование. – 2012. – №3. – С. 26-38.
- Разработка эффективных разливочных систем промежуточных ковшей МНЛЗ / С.П. Еронько, Д.А. Яковлев, И.А. Орлов и др. // Металлургические процессы и оборудование. – 2009. – №2. – С. 39-48.
- Исследование и разработка системы быстрой замены погружных стаканов при непрерывной разливке стали / С.П. Еронько, Е.В. Ошовская, Д.А. Яковлев и др. // Металлургическая и горнорудная промышленность. – 2009. – №4. – С. 105-108.
- Совершенствование разливочных систем промежуточных ковшей МНЛЗ / С.П. Еронько, А.Ю. Цупрун, К.В. Дубойский и др. // Электрометаллургия. – 2009. – №7. – С. 37-43.
- Еронько С.П. Разработка отечественного конкурентоспособного оборудования для дозированного перелива стали // Металлургическая и горнорудная промышленность. – 2010. – №2. – С. 180-185.
- Аксельрод Л.М., Паршин В.М., Мазурок Е.Ф. Механизм зарастания погружных стаканов при непрерывной разливке стали // Сталь. – 2007. – №4. – С.30-33.
- Патент 96891 Україна, В22D41/56, В22D11/106. Маніпулятор для заміни занурювального стакана на слябовій машині безперервного лиття заготовок / С.П. Єронько, М.Ю. Ткачов, К.В. Дубойський; Донец. нац. техн. ун-т. №2010155511; заявлено 23.12.2010; опубл. 12.12.2011. Бюл. №23. – 5 с.
- Заявка на винахід а 2012 08740, Україна, В22D41/56 (2006.01). Пристрій для заміни занурювального стакана проміжного ковша машини безперервного лиття заготовок / С.П. Єронько, М.Ю. Ткачов; Донец. нац. техн. ун-т; заявлено 16.07.2012.
- Расчет и конструирование системы быстрой замены погружных стаканов при непрерывной разливки стали / С.П. Еронько, А.Л. Сотников, М.Ю. Ткачев и др. // Металл и литье Украины. – 2011. - №12. С. 36-44.