Реферат по теме выпускной работы
Содержание
- Введение
- 1. Актуальность темы магистерской работы
- 2. Цель и задачи исследования
- 3. Основные направления совершенствования технологии непрерывной разливки стали и оборудование для ее реализации
- 4. Целесообразность совершенствования разливочных систем промежуточных ковшей МНЛЗ и необходимость разработки методики их расчета
- 5. Исследование и разработка усовершенствованной комплексной системы быстрой смены погружных стаканов при серийной разливке стали на слябовых МНЛЗ
- 5.1 Совершенствование конструкции комплексной разливочной системы промежуточного ковша
- 5.2 Получение теоретических зависимостей для расчета кинематических и энергосиловых параметров манипулятора механизированной замены
- 6. Физический аналог системы быстрой смены погружных стаканов и его техническая характеристика
- Выводы
- Перечень использованной литературы
Введение
Идея замены технологии разливки металлов в изложницы на непрерывную известно достаточно давно – еще с середины XIX века, но технология непрерывной разливки начала окончательно формироваться на рубеже 1950-60-х годов, когда и получила бурное распространение и широкое внедрение в виде машин непрерывного литья заготовок (МНЛЗ) в странах Западной Европы, СССР, Японии, США. В настоящее время непрерывная разливка стали освоена более чем в 90 странах мира. Успешно действует примерно 1750 МНЛЗ, что позволяет отливать на них более 85% всей производимой стали [1]. Примерно 2/3 всего объема производимой в мире стали разливается на слябовых МНЛЗ. При этом в мире насчитывается более 650 слябовых МНЛЗ с общим числом ручьев свыше 900 штук [2].
Непрерывная разливка стали оказывает существенное влияние на технико-экономические показатели сталеплавильного производства, потому что является его завершающим этапом. Главными критериями оценки эффективности функционирования МНЛЗ являются ее производительность и качество получаемой заготовки. В связи с этим значительная часть научно-исследовательских и конструкторских работ, выполненных за последние годы в стране и за рубежом, были направлены на повышение указанных показателей.
Производительность МНЛЗ зависит, как известно, от скорости вытягивания заготовки, которая в свою очередь регламентирована интенсивностью и равномерностью отвода тепла от кристаллизующегося непрерывнолитого слитка. Для улучшения условий формирования корочки слитка и повышения количества тепла, отводимого в единицу времени от его поверхности, ведущие зарубежные фирмы предложили ряд разработок, связанных с совершенствованием конструктивных элементов кристаллизатора МНЛЗ, позволивших повысить скорость разливки. Однако при этом заметно стали проявляться побочные эффекты, связанные с турбулентным режимом движения потоков металла в объеме, ограниченном образующейся корочкой непрерывнолитого слитка. Для снижения степени их негативного влияния на оптимальные условия формирования корочки слитка и глубины проникновения нежелательных примесей в кристаллизующийся металл в настоящее время прибегают к использованию весьма дорогостоящих систем электромагнитного торможения металлических потоков, что ухудшает итоговые экономические показатели производства непрерывнолитой заготовки. Поэтому в качестве альтернативной меры, направленной на повышение производительности современных МНЛЗ, следует признать увеличение серийности разливки стали, благодаря чему растет выход годного и уменьшаются простои оборудования, связанные с техническими паузами, обусловленными остановкой машины после завершения разливки нескольких плавок и подготовкой ее к очередному запуску [3-5].
1. Актуальность темы магистерской работы
В условиях эксплуатации слябовых МНЛЗ реализация разливки изолированной от атмосферы струей связана с известными трудностями, связанными с преждевременным выходом из строя погружных стаканов вследствие эрозии их поверхностей, контактирующих с расплавом, или появления значительного слоя отложений, которые изменяют форму и размеры канала и негативно влияют на условия организации потоков жидкой стали в полости кристаллизатора. Во время замены вышедшего из строя погружного стакана, даже при кратковременном прекращении поступления жидкой стали в кристаллизатор, на поверхности получаемой заготовки образуется так называемый «пережим», в зоне расположения которого металл считается некондиционным, из-за чего должен быть вырезан и отправлен в качестве шихты на повторную переплавку.
Число плавок, разливаемых в серии, зависит от срока службы огнеупорной футеровки промежуточного ковша и эксплуатационного ресурса его систем, которые обеспечивают перелив стали в кристаллизаторы МНЛЗ. Так, например, кварцевый погружной стакан выдерживает разливку 1-3 плавок. Наиболее высокую эксплуатационную стойкость обеспечивают корундографитовые погружные стаканы, усиленные специальным цирконовым поясом в зоне контакта со шлакообразующей смесью, что при определенных технологических мероприятиях может увеличить длительность их работы, равную сроку эксплуатации футеровки промковша и стопора-моноблока (8-10 плавок) [1]. Однако, как показали промышленные эксперименты, технологическая стойкость погружного стакана в этом случае лимитируется скоростью зарастания его внутренней полости оксидами алюминия, кремния и пр. При этом стакан может выйти из строя уже через 2,5-3 плавки, т.е. значительно меньше срока службы рабочего слоя футеровки промковша. Поэтому преимущества непрерывной разливки качественной стали на слябовую заготовку длинными и сверхдлинными сериями в полной мере проявляются в том случае, когда промежуточный ковш МНЛЗ оборудован системой быстрой смены погружных стаканов, защищающих разливаемый металл от вторичного окисления, что является одним из мер по защите струи металла от кислорода окружающей атмосферы на участках промежуточный ковш – кристаллизатор и обеспечивает достижение требуемого уровня качества отливаемой заготовки.
В системах, предлагаемых потенциальному потребителю зарубежными фирмами (Interstop Corp. (Швейцария), Vesuvius Group (Бельгия) и Danieli & С. Officine Meccaniche S.p.A. (Италия)), замена погружного стакана сопровождается операциями, выполняемыми вручную или с применением специальных манипуляторов с ручным приводом, что вызывает определенные неудобства из-за отсутствия свободного места на рабочей площадке у промковша.
Указанные обстоятельства послужили побудительными мотивами к созданию усовершенствованной системы быстрой смены погружных стаканов, которая позволяла бы решить отмеченные проблемы.
2. Цель и задачи исследования
Целью настоящего исследования является разработка и обоснование конструктивных и энергосиловых параметров системы быстрой смены погружных стаканов, при функционировании которой исключался бы тяжелый физический труд обслуживающего персонала МНЛЗ, сокращалось время проводимой технологической операции, минимизировались энергетические затраты на ее выполнение и рационально использовалось свободное место на рабочей площадке.
Для достижения поставленной цели необходимо решить следующие задачи:
- На основе сопоставительного анализа существующих технических решений разработать усовершенствованную комплексную систему быстрой смены погружных огнеупорных стаканов.
- Разработать методику расчета кинематических и энергосиловых параметров предложенной системы.
- Провести проверку правильности принятых технических решений и полученных расчетных зависимостей на физическом аналоге предложенной системы.
- Выдать рекомендации для промышленного использования предложенной разработки.
- Выполнить оценку технико-экономической эффективности разработанных технических решений.
3. Основные направления совершенствования технологии непрерывной разливки стали и оборудование для ее реализации
Рациональная технология непрерывной разливки стали является весьма важным составляющим элементом сталеплавильного производства, определяющим технико-экономические показатели работы цеха и себестоимость металлопродукции. В настоящее время главными условиями улучшения показателей технико-экономической эффективности производства качественной заготовки на слябовых МНЛЗ являются повышение её производительности путем увеличения серийности непрерывной разливки и улучшения качества отливаемой заготовки за счет организации защиты стали от вторичного окисления на участках сталеразливочный ковш – промежуточный ковш – кристаллизатор.
Важным этапом в получении качественных непрерывнолитых заготовок является процесс производства качественной стали, который требует соблюдения целого ряда операций по всей технологической цепи, направленных на устранение или ослабление воздействия многих факторов, которые отрицательно влияют на механические характеристики и служебные свойства металлопродукции. Одной из таких операций является защита стали от вторичного окисления во время непрерывной разливки. Эта операция предполагает экранирование поверхности истекающей струи металла на открытых ее участках. В ходе многолетних исследований было установлено, что наиболее эффективными средствами защиты непрерывно разливаемой качественной стали являются огнеупорные трубы и погружные стаканы на участках сталеразливочный ковш – промковш и промковш – кристаллизатор соответственно. Но практика эксплуатации слябовых МНЛЗ показывает, что реализация разливки изолированной от атмосферы струей жидкой стали сопровождается трудностями, связанными с преждевременным выходом из строя погружных огнеупорных стаканов. Каждая замена погружного стакана в ходе разливки, вызванная его разрушением или зарастанием внутренней полости, предполагает остановку на некоторое время соответствующего ручья МНЛЗ, что впоследствии требует вырезания из заготовки той части, которая находилась в процессе замены непосредственно в кристаллизаторе. Поэтому частая замена погружных стаканов не просто нарушает технологический ритм разливки, но также повышает отходы металла и снижает выход годного на 1…2 % [1].
Основной причиной выхода погружных стаканов из эксплуатации является эрозионный износ в зоне шлакового пояса, зарастание внутренней полости в зоне выходного отверстия и растрескивание верхней части изделия, связанное с подсосом воздуха в стык между стаканом – дозатором и погружным стаканом, и образование продольных сквозных трещин при термоударе (недостаточном подогреве стакана перед разливкой; например, корундографитовые погружные стаканы перед началом разливки нагреваются до температуры 1000-1100 °С).
Динамика движения струи стали из промковша в кристаллизатор представляется весьма важной с точки зрения эксплуатации погружного стакана [5]. Поэтому следует считать перспективными разработки, направленные на создание систем быстрой смены погружных стаканов, использование которых позволит исключить проблемы, вызванные прерыванием струи металла, истекающей из промежуточного ковша в кристаллизатор МНЛЗ.
4. Целесообразность совершенствования разливочных систем промежуточных ковшей МНЛЗ и необходимость разработки методики их расчета
В процессе длительной разливки форма и размеры каналов дозирующих и защитных стаканов по ряду причин могут существенно изменяться, что приводит к ухудшению условий формирования струи и нарушению скоростные режимов истечения стали. В связи с этим промежуточные ковши современных слябовых МНЛЗ укомплектованы системами быстрой замены погружных стаканов, разработанных известными фирмами [6-8].
В системах, предлагаемых потенциальному потребителю зарубежными фирмами (Interstop Corp.и Vesuvius Group) замена погружного стакана осуществляется в два этапа. Вначале предварительно разогретый резервный стакан вручную или с помощью специального манипулятора (рис. 4.1) устанавливают на приемные салазки разливочного устройства за отработанным огнеупором по ходу его возможного перемещения. После отвода захватного устройства манипулятора в сторону в замковой части разливочной системы фиксируют силовой гидроцилиндр, центрируя его шток относительно продольной оси сменного огнеупора. В нужный момент, подав из гидроаккумулятора в полость гидроцилиндра под избыточным давлением рабочую жидкость, в течение долей секунды осуществляют одновременное перемещение обоих погружных стаканов на заданное расстояние, в результате чего резервный огнеупорный элемент практически без прерывания струи занимает рабочую позицию и выталкивает изношенный, который затем удаляют из-под ковша (рис. 4.2). После завершения операции смены погружного стакана силовой гидроцилиндр отсоединяют от замкового узла разливочного устройства. При такой конструктивной схеме процесс замены погружного стакана не может быть осуществлен сразу же после размещения резервного огнеупорного элемента на исходной позиции из-за необходимости предварительного выполнения нескольких дополнительных операций по установке силового гидроцилиндра, требующих определенных затрат рабочего времени. На некоторых зарубежных МНЛЗ для облегчения подачи гидроцилиндра к разливочному устройству и последующего отвода от него предусмотрено применение дополнительного манипулятора с ручным приводом, что вызывает определенные неудобства из-за отсутствия свободного места на рабочей площадке у промежуточного ковша [9].
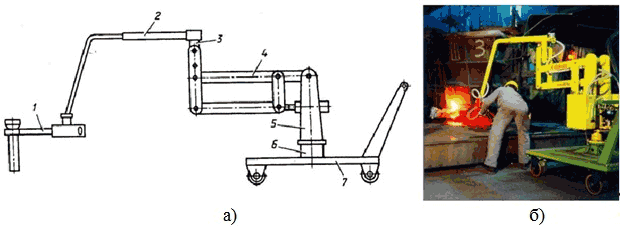
Рисунок 4.1 – Конструкция (а) и общий вид манипулятора (б) для быстрой смены погружных стаканов фирмы Interstop Corp. (Швейцария):
1 – специальные клещи; 2 – Г-образная консоль; 3 – подъемный гидроцилиндр; 4 – параллелограммный механизм; 5 – вертикальная стойка; 6 – поворотная опора; 7 – тележка
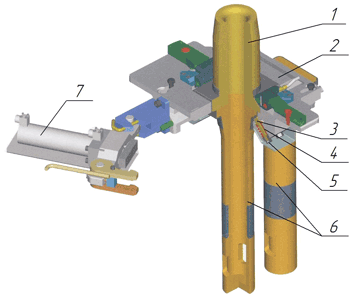
Рисунок 4.2 – Общий вид устройства фирмы Vesuvius Group (Бельгия) для быстрой замены погружных стаканов:
1 – разливочный стакан; 2 – базовая плита; 3 – штифт; 4 – витая пружина; 5 – резьбовая пробка; 6 – сменный комплект погружных стаканов; 7 – силовой гидроцилиндр
В указанных системах важнейшей конструктивной частью является узел прижатия сменного стакана к базовому огнеупорному блоку. Данный узел в разливочных устройствах зарубежных фирм (рис. 4.3) включает две группы коромысел, установленных на осях симметрично по обе стороны огнеупорного стакана вдоль направления его возможного перемещения. При этом каждое коромысло одним концом давит на тыльную часть стального кожуха стакана за счет силы сжатия витой или тарельчатой пружины, воздействующей на противоположный конец коромысла.
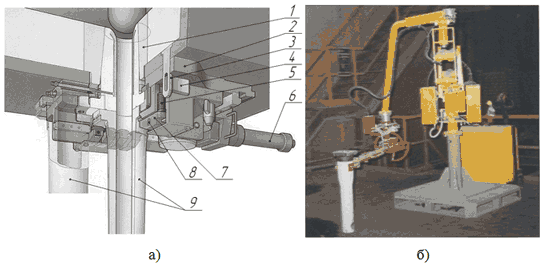
Рисунок 4.3 – Конструктивное исполнение устройства (а) и манипулятора (б) фирмы Interstop Corp. (Швейцария) для быстрой замены погружных стаканов:
1 – разливочный стакан; 2 – базовая плита; 3 – штырь; 4 – клин; 5 – блок пружин; 6 – силовой гидроцилиндр; 7 – рычаг; 8 – ось;
9 – сменный комплект погружных стаканов
Важно отметить, что из-за значительной массы погружных стаканов при их установке вручную на приемные направляющие разливочного устройства обслуживающий персонал подвергается большим физическим нагрузкам, а стесненные условия требуют обеспечения сложной траектории движения резервного погружного стакана в рабочей полости кристаллизатора. В связи с этим актуальной задачей является механизация указанных технологических операций за счет применения специальных манипуляторов, которые бы функционировали в комплексе с устройствами быстрой замены погружных стаканов.
Вышеуказанные обстоятельства были учтены в ряде отечественных разработок систем быстрой смены погружных стаканов. Например, на кафедре «Механическое оборудование заводов черной металлургии» (МОЗЧМ) Донецкого национального технического университета за последние годы запатентованы и спроектированы несколько типов систем, позволяющих практически без прерывания разливки осуществлять замену погружных стаканов, экранирующих струю стали на участке промежуточный ковш – кристаллизатор слябовой МНЛЗ [10-13].
Комплекс, разработанный сотрудниками кафедры МОЗЧМ ДонНТУ, включает разливочную и манипуляционную системы. Механическая часть предложенной разливочной системы отличается от зарубежных аналогов тем, что силовой гидроцилиндр непосредственно с нею не связан, а размещен стационарно на манипуляторе. Кроме того, были внесены изменения в конструкцию узла прижатия погружного стакана к базовой огнеупорной плите. Стакан своей металлической обоймой опирается на ролики, поджимаемые пружинами, размещенными в наклонных каналах, в которые снаружи ввинчены резьбовые пробки. Применение тел качения в опорном узле позволило уменьшить силу сопротивления перемещению погружного стакана и снизить интенсивность износа контактных поверхностей взаимодействующих элементов разливочного устройства. Манипуляционная система изображена на рис. 4.4.
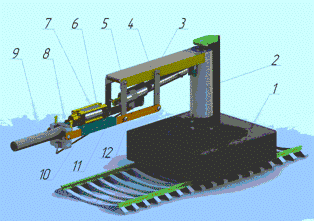
Рисунок 4.4 – Манипуляционная система для быстрой смены погружных стаканов конструкции кафедры МОЗЧМ ДонНТУ:
1 – тележка; 2 – поворотная колонна; 3 – горизонтальная консоль; 4, 5 – планки; 6 – рычаг; 7 – силовой цилиндр; 8 – скоба;
9 – резервный погружной стакан; 10 – тяга; 11 – палец; 12 – корпус цилиндра
Разработанная конструктивная схема устройства позволяет реализовать требуемый закон движения резервного погружного стакана в ограниченном пространстве с помощью лишь одного силового цилиндра, что выгодно отличает её от зарубежных аналогов. Однако, манипулятор, входящий в состав указанной системы, располагается на рабочей площадке со стороны торцевой части промежуточного ковша. Такая схема относительного размещения манипулятора в полной мере отвечает условиям разливки стали на одноручьевых МНЛЗ, промежуточные ковши которых переводятся в рабочую позицию с помощью подъемно-поворотных столов. На машинах с большим числом ручьев замену промежуточного ковша осуществляют, как известно, с использованием самоходной тележки, движущейся в направлении его продольной оси. В этом случае манипулятор является помехой перемещающейся тележке, что затрудняет его эксплуатацию.
Результаты выполненного анализа свидетельствуют о том, что дальнейшее повышение производительности слябовой МНЛЗ сдерживается отсутствием конструктивно простых и надежных в эксплуатации устройств быстрой смены погружных огнеупорных стаканов. Поэтому работы, связанные с разработкой новых, более совершенных разливочных систем, и методов расчета их конструктивных и энергосиловых параметров необходимо считать важной научно-практической задачей.
Результаты литературного и патентного поиска, выполненного по изучаемой проблеме, показали, что в последние годы практически отсутствуют работы, в которых изложены в доступной форме методология расчета конструктивных и энергосиловых параметров образцов оборудования, введенных в эксплуатацию за рассмотренный пятнадцатилетний период. Это обусловлено стремлением зарубежных разработчиков защитить свои технические секреты от возможных конкурентов, поэтому они, как правило, ограничиваются предоставлением информации, носящей рекламный характер. Отсутствие результатов теоретических и практических исследований нового металлургического оборудования вносит значительные осложнения в дальнейшее развитие и совершенствование функциональных систем МНЛЗ.
5. Исследование и разработка усовершенствованной комплексной системы быстрой смены погружных стаканов при серийной разливке стали на слябовых МНЛЗ
В условиях непрерывной разливки стали длинными сериями с применением защитных погружных стаканов стабилизация скоростных режимов истечения металла из промежуточного ковша в кристаллизатор МНЛЗ является важной технологической задачей, решение которой требует создания специальных устройств, позволяющих при необходимости осуществлять быструю замену огнеупорного элемента, экранирующего струю расплава от окружающей атмосферы [3, 4, 14].
Практика эксплуатации подобных устройств на ряде зарубежных и отечественных металлургических предприятий показала, что эффективность их применения значительно повышается если они работают в комплексе с манипуляторами, обеспечивающими механизированную подачу на приемные направляющие разливочного устройства промежуточного ковша предварительно разогретого до требуемой температуры резервного огнеупорного изделия, которое должно за доли секунды под действием силового цилиндра сменить вышедший из строя стакан.
Многообразие схем относительного расположения оборудования современных МНЛЗ и особенности его функционирования являются главными предпосылками для разработки систем быстрой замены погружных стаканов, которые в наибольшей мере соответствуют условиям непрерывной разливки металла конкретного сталеплавильного цеха.
5.1 Совершенствование конструкции комплексной разливочной системы промежуточного ковша
Учитывая достоинства и недостатки, выявленные при эксплуатации зарубежных образцов оборудования, предназначенного для выполнения механизированной замены погружных стаканов в условиях серийной разливки стали на слябовых МНЛЗ, предлагается новая конструктивная схема системы быстрой смены защитных огнеупорных элементов, включающая стационарно размещенный на рабочей площадке манипулятор и закрепленное на наружной поверхности днища промежуточного ковша разливочное устройство, снабженное погружным огнеупорным стаканом. Манипулятор (рис. 5.1) позволяет в заданной последовательности без применения дорогостоящих средств автоматики обеспечить подачу сменного погружного стакана по расчетной траектории на приемные салазки разливочного устройства промежуточного ковша и силового гидроцилиндра, осуществляющего по команде перемещение стакана из исходной позиции в рабочую.
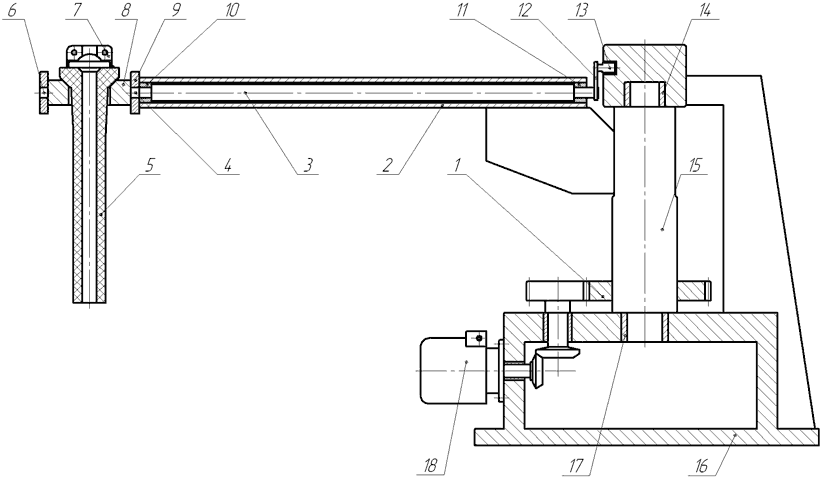
Рисунок 5.1 – Схема разработанной системы быстрой смены погружного стакана:
1 – зубчатый венец; 2 – пустотелая консоль;3 – трансмиссионный вал; 4, 6 – цапфы; 5 – сменный погружной стакан; 7 – силовой гидроцилиндр; 8 – скоба; 9 – платформа;10, 11 – подшипниковые опоры; 12 – рычаг; 13 – ролик; 14, 17 – верхняя и нижняя неподвижные подшипниковые опоры; 15 – поворотная колонна; 16 – основание; 18 – электромеханический привод
Принцип работы предлагаемой системы быстрой замены погружных стаканов поясняет рисунок 5.2. Во время серийной разливки стали манипулятор расположен в исходной позиции на рабочей площадке 19 перед промежуточным ковшом 20, оборудованным разливочным устройством 21, снабженным защитным стаканом 22, нижняя часть которого погружена в расплав, находящийся в кристаллизаторе 23. В этой позиции поворотная колонна 15, консоль 2 и несущая скоба 8 с установленным в ней сменным погружным стаканом 5 занимают относительное положение, показанное на рисунке 5.2, а. При этом разогретый до нужной температуры сменный стакан 5 расположен горизонтально и удерживается зажимами несущей скобы 8, развернутой в вырезе платформы 9. Фиксация скобы со стаканом относительно платформы обеспечена трансмиссионным валом, рычаг 12 которого своим роликом 13, находящимся в профилированном направляющем пазу, удерживает указанные элементы механизма в заданном положении.
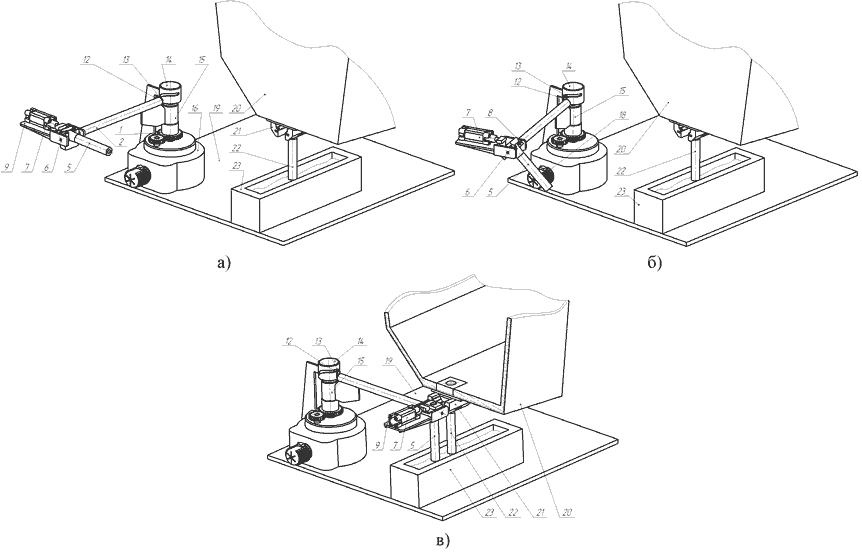
Рисунок 5.2 – Последовательность выполнения операции быстрой смены погружных стаканов
Для замены погружного стакана запускают привод 18, который через зубчатые передачи и венец 1 осуществляет поворот колонны 15 в нижней и верхней 14 неподвижных подшипниковых опорах. Вместе с колонной поворачивается пустотелая консоль. 2 и установленный внутри нее в подшипниковых опорах 10 и 11 трансмиссионный вал 3 (рис. 5.1) с прикрепленным рычагом 12. Ролик 13, перекатываясь в направляющем пазу, выполненном на наружной цилиндрической поверхности верхней неподвижной опоры 14, воздействует на конец рычага 12, поворачивающего трансмиссионный вал в опорах 10 и 11 (рис. 5.1) относительно консоли 2. Вращение вала 3 через цапфу 4 (рис. 5.1) и передается скобе 8, которая осуществляет поворот относительно платформы 9 сменного погружного стакана 5 (рис. 5.2, б) до полного его перевода в вертикальное положение. Этот перевод завершится при подходе стакана к торцу разливочного устройства 21 и расположении его соосно с направляющими. После этого силовым гидроцилиндром 7, расположенным на платформе 9, сменный стакан 5 перемещается по направляющим разливочного устройства 21 до тех пор, пока он не займет место вышедшего из строя погружного стакана 22, экранирующего струю стали, истекающей из промежуточного ковша 20 в кристаллизатор 23 (рис. 5.2, в). Скорость перемещения стаканов такова, что процесс их замены длится 0,2...0,3 с, т.е. практически без прерывания струи жидкой стали. Замененный погружной стакан удаляют из направляющих пазов разливочного устройства с помощью специального приспособления, а консоль манипулятора возвращается в исходную позицию при повороте колонны в обратном направлении. В исходной позиции элементы конструкции манипулятора не препятствуют перемещению тележки с промежуточным ковшом при аварийном съезде или в случае передачи ковша на ремонтную площадку для замены его футеровки [15].
С целью оптимизации энергосиловых параметров процесса смены огнеупорных элементов и снижения силы трения между контактными поверхностями металлической обоймы погружного стакана и опорной части разливочного устройства промковша МНЛЗ, вызывающей интенсивный износ контактной поверхности прижимных элементов, что требует их частой замены, при разработке усовершенствованной конструкции разливочного устройства решалась задача по снижению сил трения между контактными поверхностями его подвижно сопряженных элементов путем изменения в разливочном устройстве конструктивного исполнения узла прижатия погружного стакана.
Для решения поставленной задачи модернизированное разливочное устройство (рис. 5.3), включает металлический корпус 1, снабженный средствами крепления в виде штырей 2 с отверстиями под клинья 3 к наружной поверхности днища промежуточного ковша 4. Корпус 1 имеет центральное вертикальное отверстие, в котором размещена нижняя часть сталевыпускного стакана 5, закрепленного в гнездовом блоке 6. В теле корпуса 1 выполнен продольный направляющий паз для размещения рабочего 7 и резервного 8 огнеупорных погружных стаканов, верхние части которых помещены в металлические обечайки.
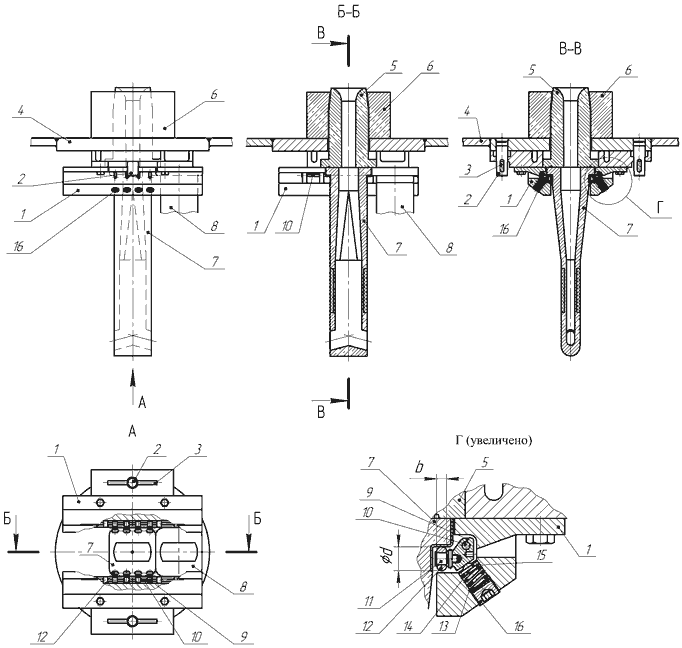
Рисунок 5.3 – Конструктивное исполнение усовершенствованного разливочного устройства
Погружной стакан 7 примыкает снизу к сталевыпускному стакану 5 и установлен с возможностью перемещения вдоль продольного паза силовым гидроцилиндром, смонтированным на платформе манипулятора. Прижатие погружного стакана к нижней части сталевыпускного стакана осуществляется механизмом, который включает поворотные элементы 9 с отверстиями, симметрично установленные на осях 10 по обе стороны погружного стакана 7 вдоль оси его перемещения в направляющем пазу металлического корпуса 1. Причем каждый поворотный элемент 9 снабжен консольно закрепленным пальцем 11, несущим свободно вращающийся ролик 12. Тело ролика имеет форму поверхности вращения с образующей в виде дуги с радиусом 0,5b...0,5d, где b и d – соответственно внешний диаметр ролика и его толщина в поперечном сечении симметрии, находящиеся между собой в соотношении d/b=2...2,5. Благодаря указанным значениям геометрических параметров ролика обеспечивается его постоянный контакт с опорной поверхностью металлической обечайки огнеупорного стакана независимо от угла поворота элемента, несущего сам ролик.
Передача усилия прижатия погружному стакану осуществляется благодаря кинематической связи поворотных элементов с предварительно сжатыми пружинами 13, которые установлены в выполненных в корпусе 1 наклонных цилиндрических каналах на направляющих стержнях 14 с поджатием к их подпорным буртикам 15 с помощью ввинченных в цилиндрические каналы пробок 16. Каждая из пробок своей торцевой частью выходит наружу металлического корпуса 1. Для поворота пробок на их выходящих торцевых частях предусмотрены шлицы под отвертку или головки под ключ [16].
Разработанная усовершенствованная система быстрой смены погружных стаканов при серийной разливке стали на слябовых МНЛЗ выгодно отличающаяся от известных зарубежных аналогов тем, что при ее использовании обеспечивается механизированное выполнение всех операций, связанных с подачей и установкой сменного огнеупорного элемента на разливочное устройство, креплением к нему силового гидроцилиндра и последующим выводом его из зоны интенсивного теплового воздействия, вызванного излучением жидкой стали, находящейся в кристаллизаторе. Благодаря применению в опорном узле разливочного устройства прижимных элементов, снабженных роликами, существенно снижается нагрузка на гидропривод за счет уменьшения силы трения между подвижными контактными поверхностями, устраняется их интенсивный износ, в связи с чем сокращаются эксплуатационные затраты, обусловленные потребным расходом изнашиваемых деталей и проведением ремонтных работ по их периодической замене.
5.2 Получение теоретических зависимостей для расчета кинематических и энергосиловых параметров манипулятора механизированной замены
В состав предложенной системы быстрой замены погружных стаканов входят комбинированный электромеханический привод, обеспечивающий одновременный поворот колонны с консолью в горизонтальной и сменного стакана в вертикальной плоскостях, и гидравлический, осуществляющий ускоренное перемещение заменяемого и нового стаканов по опорным направляющим разливочного устройства. При этом расчет энергосиловых параметров гидравлического привода необходимо рассматривать применительно к конкретной конструктивной схеме узла прижатия огнеупорного стакана. Рассмотрим кинематические и энергосиловые параметры электромеханического привода.
Для выполнения силового расчета рычажного механизма использован принцип Даламбера, согласно с которым подвижная система тел находится в каждый момент времени в равновесии под действием внешних сил, включая и силы инерции. При этом разделим механизм на две структурные группы (рис. 5.4) и расчет начнем с последней из них [17]. В ее состав (рис. 5.4, а) входят установленная на цапфах в подшипниковых опорах D и Е скоба, несущая сменный погружной стакан.
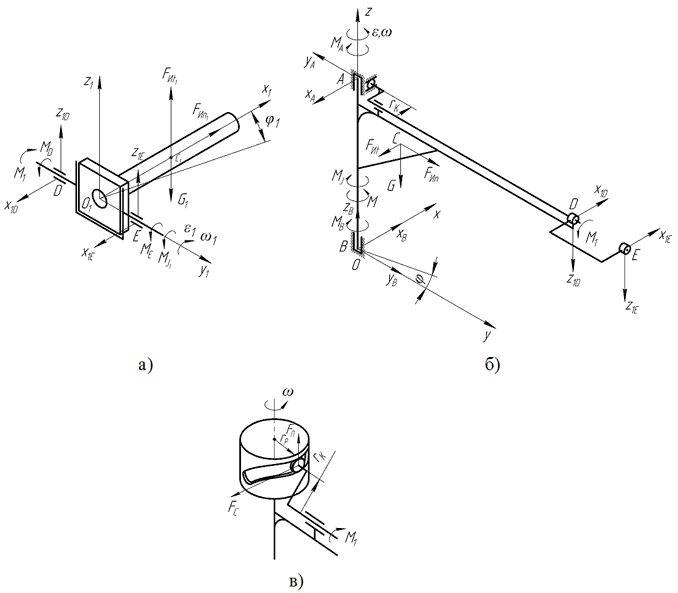
Рисунок 5.4 – Расчетная схема механического привода системы быстрой смены погружных стаканов
В период пуска привода манипулятора на звенья рассматриваемой структурной группы действуют силы тяжести стакана Gст и скобы Gск; сопротивление трения в подшипниковых опорах D и E, вызванное силами реакций; силы инерции; момент, приложенный к цапфе скобы и необходимый для преодоления указанных сил.
Выбираем систему координат, ориентируя направление оси Y1 перпендикулярно продольной оси симметрии консоли. От оси Х1 будем вести отсчет угла поворота сменного стакана φ1.
Предварительно находим координаты центра тяжести системы С1 (хС1, yC1, zC1), в котором приложены суммарная сила тяжести G1 = Gст + Gск.
Определяем силы инерции, возникающие при повороте скобы со стаканом вокруг оси Y1 с угловым ускорением ε1 и угловой скоростью ω1.
При вращательном движении касательная FИt1 и нормальная FИn1 силы инерции равны:
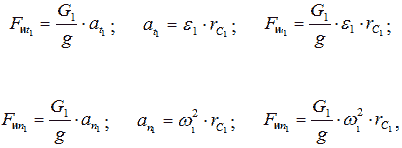
где rC1 – расстояние от оси вращения до центра тяжести системы С1:
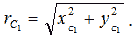
Положение центра тяжести С1 в плоскости O1Х1Z1 выразим через угол φ1:

Силы инерции FИt1 и FИn1 приложены в точке К1, положение которой определяется по формуле:
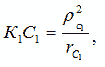
где ρc1 – радиус инерции системы относительно оси, проходящей через центр тяжести С1 параллельно оси вращения.
Переносим силы FИt1 и FИn1 в точку С1. Силу FИn1 переносим по линии действия. Силу FИt1 переносим параллельно в точку С1 с добавлением пары, момент которой равен:
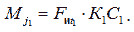
Подставив в это выражение значения FИt1 и К1С1, получим:
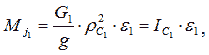
где IC1 – момент инерции поворотной системы относительно горизонтальной оси, проходящей через центр тяжести С1:
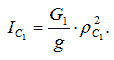
Момент Мj1 направлен в сторону, противоположную направлению вращения элементов системы. Все силы инерции, действующие на поворотную систему, расположены в одной плоскости, перпендикулярной оси вращения скобы со стаканом Y1. Приложенные к системе силы и моменты: M1 – момент, действующий на цапфу скобы; МЕ и МD – моменты от силы трения в опорах E и D; X1D, X1E, Z1D, Z1E составляющие реакций в этих опорах.
Составим уравнения равновесия по законам статики:
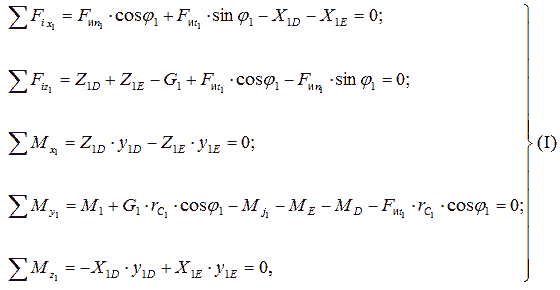
где y1D, y1E – плечи сил;
МD, ME – моменты трения в опорах поворотной скобы:
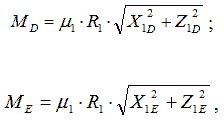
где R1 – радиус опор E и D;
μ1 – коэффициент трения в опорах Е и D.
Решаем систему уравнений (I) и находим реакции опор E, D и момент М1, приложенный к цапфе скобы для преодоления статических и динамических нагрузок при ее повороте вместе со сменным стаканом:
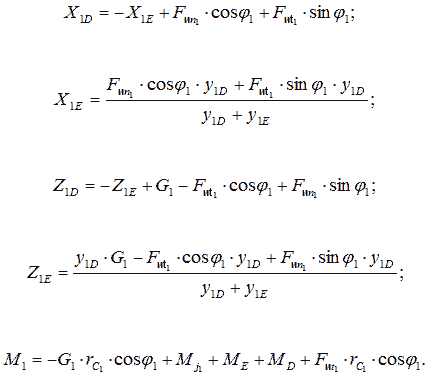
Полученные значения М1 и реакций опор используем при силовом расчете первой группы, включающей поворотную колонну и консоль. Момент М1 приложим к трансмиссионному валу с измененным направлением на противоположное, а реакции опор E и D – к платформе консоли, изменив их направление (рис. 5.4, б). Наряду с этим на элементы системы действуют силы тяжести колонны Gкол и консоли Gкон; моменты МА и МВ от сил трения в подшипниковых опорах А и В поворотной колонны, вызванные силами реакций XА, YА, XВ, YВ в этих опорах; силы инерции; момент М на зубчатом колесе колонны, необходимый для преодоления указанных сил.
Выбираем систему координат и находим координаты центра ее тяжести С (xC, yC, zC), в котором приложена суммарная сила G = Gкол + Gкон. Рассчитываем силы инерции, возникающие при повороте колонны с консолью вокруг оси Z с угловым ускорением ε и угловой скоростью ω.
При вращательном движении касательная FИt и нормальная FИn силы инерции равны:
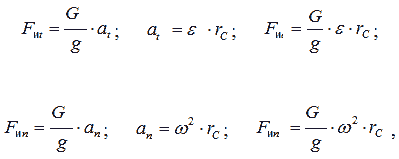
где rC – расстояние от оси вращения до центра тяжести системы С:
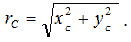
Положение центра тяжести С выражаем через угол φ:

Момент добавляемой пары сил при переносе силы инерции FИt в точку С равен:

где IC – момент инерции поворотной системы относительно вертикальной оси, проходящей через центр тяжести С:
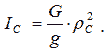
Момент Mj направлен в сторону, противоположную направлению вращения элементов выделенной системы. Все силы инерции, действующие на поворотную систему, расположены в одной плоскости, перпендикулярной оси вращения колонны Z. Кроме того, к системе приложены: М – момент на зубчатом колесе колонны; МА, МВ – моменты от сил трения в опорах А и В; составляющие реакций в этих опорах XА, YА, XВ, YВ, ZВ; составляющие реакций в опорах D, E и момент М1, действующие со стороны элементов первой структурной группы.
Предварительно приведем к оси поворотной колонны момент М1, приложенный к трансмиссионному валу. В соответствии со схемой нагружения ролика (рис. 5.4, в) на него действует сила Fп, прижимающая его к направляющей поверхности паза, и сила сопротивления его перемещению Fс.
Сила прижатия ролика:

где rк – длина рычага, несущего ролик.
Сила сопротивления, действующая на ролик при его перемещении в направляющем пазу:
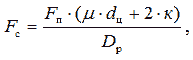
где μ – коэффициент трения скольжения в опоре ролика;
dц – диаметр цапфы ролика;
к – коэффициент трения качения;
Dр – диаметр ролика.
Момент сопротивления повороту колонны, вызванный действием силы Fс:
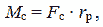
где rр – расстояние от оси поворотной колонны до направляющей поверхности паза, по которой перекатывается ролик.
Составим уравнения равновесия по законам статики:
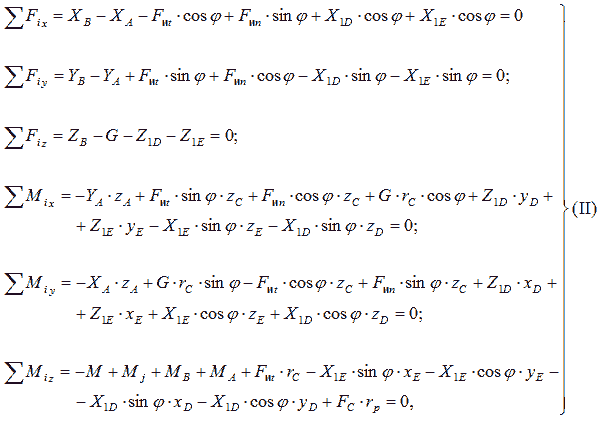
где xC, xE, xD, yC, yE, yD, zA, zC, zD, zE – плечи сил;
МА, МВ – моменты трения в опорах вертикального вала:

где R – радиус опор A и B;
μ1 – коэффициент трения в опорах A и B;
dц – диаметр подпятника в опоре В;
μ2 – коэффициент трения в подпятнике опоры В.
Решаем систему уравнений (II) и находим реакции опор А и В, а также момент М, приложенный к приводному колесу для преодоления статических и динамических нагрузок при повороте колонны с консолью и одновременном относительном развороте скобы со стаканом:
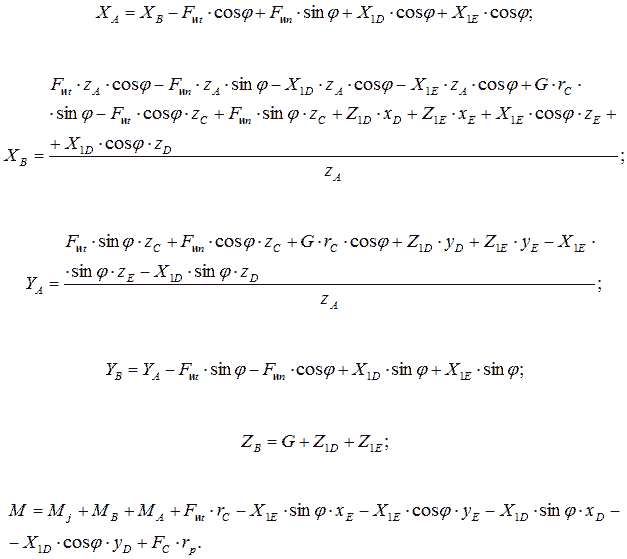
Мощность электродвигателя, используемого в приводе манипулятора, определяется из выражения:
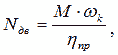
где ωк – требуемая угловая скорость поворота колонны;
ηпр – к.п.д. привода манипулятора.
Суммарное передаточное число понижающих передач привода манипуляционной системы:

где ωдв – угловая скорость выбранного по каталогу электродвигателя;
ωк – требуемая угловая скорость поворота колонны.
6. Физический аналог системы быстрой смены погружных стаканов и его техническая характеристика
Для проверки правильности принятых технических решений и корректности полученных расчетных зависимостей, а также с целью внесения соответствующих корректировок в техническую документацию на стадии проектирования промышленного образца системы быстрой смены погружных стаканов для серийной разливки стали был разработан, спроектирован и изготовлен физический аналог исследуемой механической системы.
Физический аналог манипулятора (рис. 6.1) был изготовлен для лабораторных условий на базе имеющейся модели промежуточного ковша и кристаллизатора. При проектировании физического аналога манипулятора использовалась методика расчета энергосиловых и конструктивных параметров системы быстрой замены погружных стаканов при непрерывной разливке стали [17] с учетом габаритов лабораторной модели промежуточного ковша, изготовленного из органического стекла с размерами 2000×500×600 мм. Масштаб физической модели конструкции манипулятора составил 1:2,5. Техническая характеристика физического аналога системы быстрой смены погружных стаканов приведена в таблице 6.1.
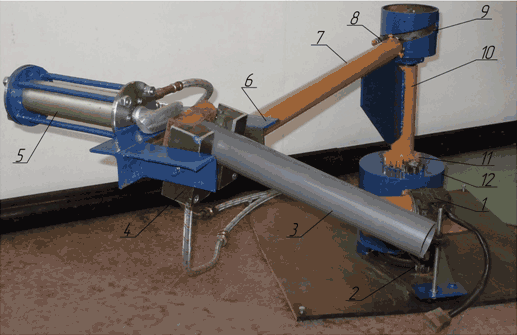
Рисунок 6.1 – Физическая модель предлагаемой конструкции манипулятора:
1 – электромеханический привод; 2 – быстроходная цилиндрическая зубчатая передача; 3 – модель погружного стакана; 4 – скоба;
5 – силовой гидроцилиндр; 6 – платформа; 7 – консоль; 8 – ролик; 9 – профилированный направляющий паз на наружной цилиндрической поверхности корпуса верхней неподвижной подшипниковой опоры; 10 – поворотная колонна; 11 – тихоходная цилиндрическая зубчатая передача; 12 – основание манипулятора
Для осуществления приведения манипулятора в движение используется мотор-редуктор постоянного тока МЭ14А работающий от источника питания 12 В. С целью обеспечения необходимого передаточного числа были спроектирована и изготовлены быстроходная 2 и тихоходная 11 открытые цилиндрические зубчатые передачи.
Параметр | Значение |
Манипулятор: | |
– мощность электродвигателя, кВт | 0,03 |
– частота вращения электродвигателя, об/мин | 1500 |
– передаточное число мотор-редуктора | 120 |
– передаточное число быстроходной зубчатой передачи | 6 |
– передаточное число тихоходной зубчатой передачи | 2 |
– масса, кг | 36 |
Разливочное устройство: | |
– масса погружного стакана, кг | 6 |
– длительность замены стакана, с | 0,3…0,5 |
– диаметр ролика прижимного элемента, мм | 20 |
– число прижимных элементов | 8 |
– масса устройства, кг | 20,8 |
Силовой гидроцилиндр: | |
– диаметр поршня, мм | 32 |
– диаметр штока, мм | 20 |
– ход штока, мм | 160 |
– скорость перемещения штока, м/с | 0,5 |
– рабочее давление, МПа | 1,25 |
– масса, кг | 4,8 |
После сборки модели аналога манипулятора и размещения его возле объемной модели промежуточного ковша осуществили тестирование функционирования механизмов при имитации быстрой замены вышедшего из строя погружного стакана. Аналогичные испытания были проведены и на 3D модели предлагаемой системы, которая предварительно была построена с помощью систем автоматического проектирования (САПР) КОМПАС-3D и SolidWorks. Последовательность выполняемых операций показана на рисунке 6.2.
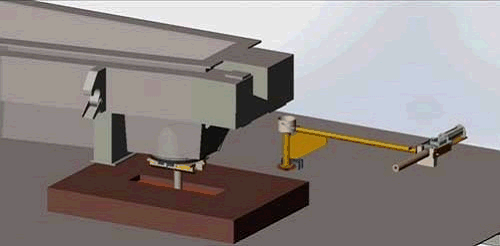
Рисунок 6.2 – Принцип работы системы быстрой замены погружных стаканов
(анимация: 5 кадров, 5 циклов повторения, 160 килобайт)
Тестирование физического аналога и 3D модели системы быстрой смены погружных стаканов для серийной разливки стали на слябовых МНЛЗ подтвердило работоспособность всех ее структурных элементов; манипулятор позволяет реализовать заданную траекторию движения в пространстве сменного огнеупорного стакана из исходной позиции в рабочую и осуществить механизированное выполнение операции по его быстрой смене.
Выводы
Таким образом, разработки, направленные на создание систем быстрой смены погружных стаканов, использование которых позволит исключить проблемы, вызванные прерыванием струи металла, истекающей из промежуточного ковша в кристаллизатор МНЛЗ во время разливки, являются наиболее перспективными.
Предлагаемая комплексная система является более универсальной в сравнении с известными отечественными и зарубежными аналогами, так как позволяет осуществлять быструю замену погружных стаканов на слябовой МНЛЗ при любом числе ручьев и различном типе устройств, осуществляющих транспортировку промежуточного ковша из рабочей позиции в резервную.
Разработанная методика расчета позволяет обосновать и рационализировать конструктивные и энергосиловые параметры комплексной системы быстрой смены погружных стаканов, в частности, сократить общее время проведения технологической операции, минимизировать энергетические затраты на ее выполнение, и рационально использовать свободное место на рабочей площадке.
С внедрением системы быстрой смены погружных стаканов сокращается время проводимой технологической операции по замене на 42% с 1,2 мин до 0,7 мин, при этом замену осуществляет один оператор (вместо 2-3 человек), физический труд которого в тяжелых и условиях сведен к минимуму.
При написании данного реферата магистерская работа еще не завершена. Окончательное завершение: январь 2014 года. Полный текст работы и материалы по теме могут быть получены у автора или его руководителя после указанной даты.
Перечень использованной литературы
- Процессы непрерывной разливки / А.Н. Смирнов, В.Л. Пилюшенко, А.А. Минаев и др. – Донецк: ДонНТУ, 2002. – 536 с.
- Смирнов А.Н., Куберский С.В., Штепан Е.В. Непрерывная разливка стали. – Донецк: ДонНТУ, 2011. – 482 с.
- Jungreithmeier A., Pessenberger E., Burgstaller K/ Production of UL CIF Steel Gradies at Voest-Alpine Stahl GmbH // Iron and Steel Technology. – 2004. – Vol. 1. №4. – P. 41-48.
- Еронько С.П., Быковских С.В. Разливка стали: Оборудование. Технология. – К.: Техніка, 2003. – 216 с.
- Металлургические мини-заводы / А.Н. Смирнов, В.М. Сафонов, Л.В. Дорохова и др. – Донецк: НОРД-ПРЕСС, 2005. – 469 с.
- New generation ladle slide gate system for performance improvement / J. Chaudhuri, G. Choudhury, S. Kumar, V. Rajgopalan // MPT International. – 2007. – Vol.30, №6. – pp. 38- 42.
- Mutsaarts P. Submerged entry nozzle exchange system for tundishes / Millennium Steel. – 2006. –pp. 143-146.
- Achieving higher perfomance & longer service life of Slide Plate / J. Chaudhuri, G. Choudhury, S. Kumar et. al. // Iron & Steel Review. – 2007. – June. – pp. 86-91.
- Еронько С.П., Сотников А.Л., Ткачев М.Ю. Совершенствование системы быстрой смены погружных стаканов для серийной разливки стали на слябовых МНЛЗ // Металлургические процессы и оборудование. – 2012. – №3. – С. 26-38.
- Разработка эффективных разливочных систем промежуточных ковшей МНЛЗ / С.П. Еронько, Д.А. Яковлев, И.А. Орлов и др. // Металлургические процессы и оборудование. – 2009. – №2. – С. 39-48.
- Исследование и разработка системы быстрой замены погружных стаканов при непрерывной разливке стали / С.П. Еронько, Е.В. Ошовская, Д.А. Яковлев и др. // Металлургическая и горнорудная промышленность. – 2009. – №4. – С. 105-108.
- Совершенствование разливочных систем промежуточных ковшей МНЛЗ / С.П. Еронько, А.Ю. Цупрун, К.В. Дубойский и др. // Электрометаллургия. – 2009. – №7. – С. 37-43.
- Еронько С.П. Разработка отечественного конкурентоспособного оборудования для дозированного перелива стали // Металлургическая и горнорудная промышленность. – 2010. – №2. – С. 180-185.
- Аксельрод Л.М., Паршин В.М., Мазурок Е.Ф. Механизм зарастания погружных стаканов при непрерывной разливке стали // Сталь. – 2007. – №4. – С.30-33.
- Патент 96891 Україна, В22D41/56, В22D11/106. Маніпулятор для заміни занурювального стакана на слябовій машині безперервного лиття заготовок / С.П. Єронько, М.Ю. Ткачов, К.В. Дубойський; Донец. нац. техн. ун-т. №2010155511; заявлено 23.12.2010; опубл. 12.12.2011. Бюл. №23. – 5 с.
- Заявка на винахід а 2012 08740, Україна, В22D41/56 (2006.01). Пристрій для заміни занурювального стакана проміжного ковша машини безперервного лиття заготовок / С.П. Єронько, М.Ю. Ткачов; Донец. нац. техн. ун-т; заявлено 16.07.2012.
- Расчет и конструирование системы быстрой замены погружных стаканов при непрерывной разливки стали / С.П. Еронько, А.Л. Сотников, М.Ю. Ткачев и др. // Металл и литье Украины. – 2011. - №12. С. 36-44.