Реферат по теме выпускной работы
Содержание
- Введение
- 1. Актуальность темы
- 2. Цель и задачи исследования, планируемые результаты
- 3. Выбор схемы обработки
- 4. Механизм для обработки сферической поверхности
- Выводы
- Список источников
Введение
В мире современных материалов керамике принадлежит заметная роль, обусловленная широким диапазоном ее физических и химических свойств. Керамика не окисляется и устойчива в более высокотемпературной области в сравнении с металлами. Модуль упругости керамических материалов на порядок выше, чем у металлов. Среди керамик можно найти материалы как с большими, так и малыми (даже отрицательными) значениями коэффициента термического расширения. Широк спектр керамических материалов с разнообразными электрофизическими свойствами, среди которых есть и диэлектрики, и полупроводники, и проводники (сравнимые по проводимости с металлами), и сверхпроводники.
Важнейшими компонентами современной конструкционной и инструментальной керамики являются оксиды алюминия, циркония, нитриды кремния, бора, алюминия, карбиды кремния и бора, их твердые растворы и разнообразные композиты.
Перспективность керамики обусловлена исключительным многообразием ее свойств по сравнению с другими типами материалов, доступностью сырья, низкой энергоемкостью технологий, долговечностью керамических конструкций в агрессивных средах. Производство керамики, как правило, не загрязняет окружающую среду в такой мере, как металлургия. Керамические материалы обладают большей биологической совместимостью, чем металлы и полимеры, и это позволяет использовать их в медицине, как для имплантации искусственных органов, так и в качестве конструкционных материалов в биотехнологии и генной инженерии.
1. Актуальность темы
Развитие современного машиностроения, повышение производительности и качества поверхности требует совершенствования технологических процессов обработки деталей машин, увеличения доли чистовых операций. Именно на окончательных операциях формируется поверхностный слой детали, определяющий их эксплуатационные свойства[1].
Сложность процесса обработки сферических поверхностей вызывает необходимость глубокого теоретического и экспериментального изучения физической сущности явлений и их влияние на точность и качество поверхностей. Одним из перспективных направлений изготовления сферических деталей являются операции шлифования на основе разработки новых конструкторских и технологических решений. Широко известны процессы шлифования плоских и цилиндрических поверхностей, в то же время шлифование деталей, имеющих сферическую поверхность мало изучено.
Повышение точности сферических поверхностей, улучшение параметров шероховатости поверхностного слоя, придание поверхности управляемой микрогеометрии является актуальной задачей современного машиностроения. Потребность машиностроения в обеспечении высокого качества сферических поверхностей деталей особенно из труднообрабатываемых материалов, таких как керамика, и создание высокопроизводительного и конкурентного процесса обработки с одной стороны и недостаточная изученность сферического хонингования с другой стороны подчеркивает своевременность проведения данных исследований и его влияние на производительность, качество и точность обработанной поверхности.
2. Цель и задачи исследования, планируемые результаты
Цель исследования – разработать метод управления качеством поверхности керамики при использовании метода алмазного шлифования для обработки сферических поверхностей. Выполнение этой цели достигается путём выполнения следующих заданий:
- Провести сравнительный анализ основных методов обработки керамики алмазным шлифованием, особенностей шлифования керамики, методов контроля шероховатости поверхности и измерении сил резания, а именно, её составляющих и установление их влияния.
- Выбрать наиболее рациональную схему обработки сферической поверхности.
- Разработать конструкцию механизма для обработки сферической поверхности путём шлифования.
- Провести кинематический анализ выбранной схемы обработки и определить параметры и условия обработки, которые влияют на точность и качество поверхностного шара обрабатываемой детали.
- Рассмотреть и изучить основные закономерности, взаимозависимости и другие показатели, которые будут иметь место в процессе обработки.
- На основании вышеуказанного исследования разработать модель управления параметрами качества поверхности керамики.
3. Выбор схемы обработки
Наиболее перспективными процессами чистовой и отделочной обработки являются процессы шлифования внутренней конической частью шлифовального круга. Этот процесс основан на использовании режущего инструмента с трубчатыми режущими элементами, расположенными на внутренней поверхности. Образующая этой поверхности совпадает с касательной к образующей сферы на ее границе с торцовыми плоскостями, ограничивающими сферу[3,4].
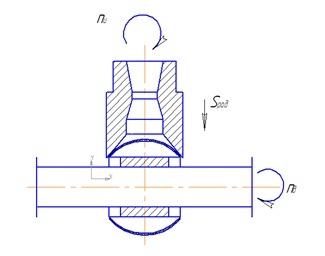
Рисунок 1 – Схема шлифования коническим кругом
Такой процесс шлифования трубчатыми шлифовальными кругами можно отнести к тем немногим случаям, когда главным движением являются оба вращательных движения, которые определяют в совокупности необходимую для осуществления шлифования результирующую скорость резания. Конкретно вопрос должен решаться целесообразностью того или иного конструктивного решения. Данный процесс должен обеспечить съем припуска, достаточный для достижения требуемой точности размера, формы, а так же компенсации погрешностей базирования.
Уменьшая зернистость круга, приближаем процесс шлифования к чистовому и отделочному. Но тогда целесообразность его осуществления на жестких осях приспособления и инструмента становится сомнительной. Наоборот, необходимо освободить один из элементов – шлифовальную головку предоставить ей возможность самоустанавливаться по обрабатываемой поверхности, что обеспечит процесс хонингования и доводки.
Данная схема обработки позволяет использовать в качестве инструмента конические алмазные круги с разной зернистостью, что необходимо при обработке керамических шаров, поэтому именно такая схема обработки будет положена в основу специализированного оборудования для производства шаровых клапанов промышленных кранов.
Еще одним преимуществом является возможность установить вместо инструмента кольцо-седло крана, а вместо детали – чугунный притир и произвести обработку кольца, после чего притереть непосредственно шар и седло, применив мелкодисперсный свободный абразив в виде пасты.
4. Механизм для обработки сферической поверхности
В работе было спроектировано специальное оборудование для обработки сферической поверхности деталей из керамики. Приспособление предназначено для шлифования сферической поверхности диаметром 20-50 мм. Данное приспособление устанавливается на поперечный суппорт станка плитой. Люфт выбирается клином, плита фиксируется винтами с контргайками. На плиту устанавливается сварной корпус, в который вварен стакан. В стакане на четырёх шариковых подшипниках смонтирован шпиндель. На одном конце шпинделя гайками закреплена шлифовальная головка, на другом - приводной шкив. На верхней плите корпуса расположен электродвигатель с ведущим шкивом. Вращение от ведущего шкива к ведомому передаётся через клиновой ремень. Натяжение клинового ремня осуществляется при помощи болта и двух гаек. Корпус может поворачиваться вокруг оси пальца на 360, болты и гайки закрепляют его в заданном положении. Врезание шлифовального инструмента в изделие происходит при продольном и поперечном перемещении суппорта[5,6].
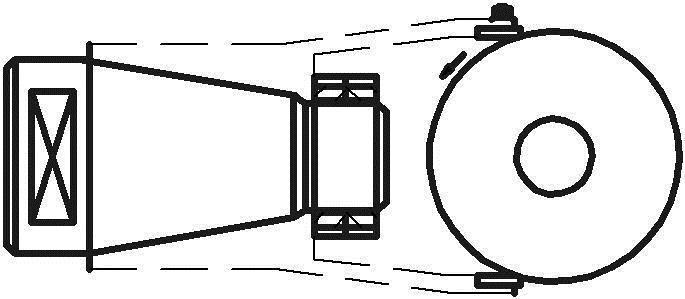
Рисунок 2 – Процесс шлифования детали сферической формы (5 кадров, 1 кадр/с, объем 170 кб)
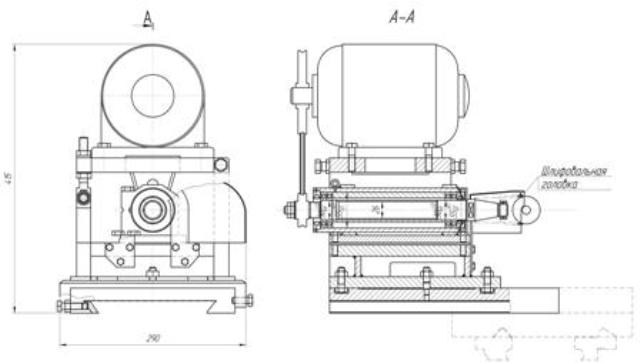
Рисунок 3 – Приспособление для шлифования деталей сферической формы
Выводы
Таким образом, выбранный нами метод обработки, реализованный в спроектированном специальном оборудовании, позволяет производить обработку сферических керамических изделий, с требуемыми параметрами точности и качества.
При написании данного реферата магистерская работа еще не завершена. Окончательное завершение: декабрь 2013 года. Полный текст работы и материалы по теме могут быть получены у автора или его руководителя после указанной даты.
Список источников
- Горяинов Д.С. Повышение эффективности хонингования сферических поверхностей деталей из нержавеющих сталей, Самарский государственный технический университет, 2009 г.
- Меркушкин А. О. Керамика на основе алюминатов редкоземельных элементов. 2012 г.
- Управление формообразованием функциональных поверхностей из керамических композиционных материалов с использованием методов алмазной доводки. // Вестник МГТУ «Станки». 2011. № 1. С. 51 – 57.
- Особенности формирования функциональных свойств изделий из керамических материалов методами доводки // Вестник УГАТУ. 2009. т.12. №4 (33). С. 66 – 71.
- О Бахарев, В. П. Конструкторско-технологическое сопровождение производства изделий из керамических и композиционных материалов / В. П. Бахарев // Конструкции из композиционных материалов. М.: 2008 г. .
- А.Г. Ткачев, И.Н. Шубин, типовые технологические процессы изготовления деталей машин, 2007 г.
- Исследование режущей способности алмазных шлифовальных кругов при плоском врезном шлифовании титановых сплавов [электронный ресурс]. – Режим доступа: http://www.plasmacentre.ru/...