Abstract
Содержание
- Introduction
- 1. Theme urgency
- 2. Goal and tasks of the research
- 3. Selection processing circuit
- 4. Mechanism for processing a spherical surface
- References
Introduction
In the world of modern ceramic materials has a prominent role, due to its wide range of physical and chemical properties. Ceramics are not oxidized and is stable in a high temperature region in comparison with metals. Modulus ceramic materials is much higher than for metals. Among the ceramic materials can be found both in large and small (even negative) values of the coefficient of thermal expansion. Wide range of ceramic materials with different physical properties, among which are insulators, and semiconductors and conductors (conductivity comparable to metals), and superconductors.
The major structural components of modern instrumental and ceramics are alumina, zirconia, silicon nitride, boron, alumina, silicon carbide and boron, their solid solutions and various composites.
The prospect of ceramics due to an exceptional variety of its properties in comparison with other types of materials, availability of raw materials, low energy technology, durability of ceramic structures in aggressive environments. Manufacture of pottery, usually, does not pollute the environment to such an extent as metallurgy. Ceramic materials are more biocompatible than metals and polymers, and this allows their use in medicine, for the implantation of artificial organs, and as constructional materials in biotechnology and genetic engineering.
1. Theme urgency
The development of modern engineering, productivity and quality of the surface requires improvement of technological processes of machine parts, increasing the share of finishing operations. It was on the final surface layer is formed transactions details, defining their operational properties [1].
The complexity of the processing of spherical surfaces necessitates thorough theoretical and experimental study of the physical nature of the phenomena and their impact on the accuracy and surface quality. One of the promising areas of manufacturing spherical parts are grinding operation through the development of new design and technology solutions. Widely known processes grinding plane and cylindrical surface, while grinding parts having a spherical surface has been little studied.
Increasing the accuracy of the spherical surfaces, improving roughness of the surface layer, giving the surface controlled micro-geometry is an important task of modern engineering. The need for mechanical engineering to provide a high quality of spherical surfaces of the parts especially of hard materials such as ceramics, and the creation of high-performance and competitive machining process on the one hand and insufficient knowledge of the spherical honing on the other hand emphasizes the timeliness of the research data and its impact on productivity, quality and accuracy the treated surface.
2. Goal and tasks of the research
The purpose of the study - to develop a method of controlling the quality of the ceramic surface using diamond grinding method for the treatment of spherical surfaces. The fulfillment of this goal is achieved by performing the following tasks:
- Make a comparative analysis of the main methods for processing diamond grinding ceramics, ceramic grinding characteristics, methods of control and measuring surface roughness of the cutting forces, namely, its components and determining their influence.
- Choose the most efficient processing circuit of a spherical surface
- Develop design a mechanism for handling the spherical surface by sanding.
- Conduct a kinematic analysis of the selected processing circuit and to determine the parameters and processing conditions that affect the accuracy and surface quality of the workpiece ball.
- Review and examine the basic laws, checks and other measures that will take place during processing.
- On the bases of the above study to develop a model parameter control surface quality of ceramics.
3. Select the processing circuit
The most promising processes of finishing and finishing treatment processes are part of the internal conical grinding wheel. This process is based on the use of a tube cutter cutting elements arranged on the inner surface. A generator of this surface coincides with the tangent to the image of a sphere on its border with the end planes limiting the scope [3,4].
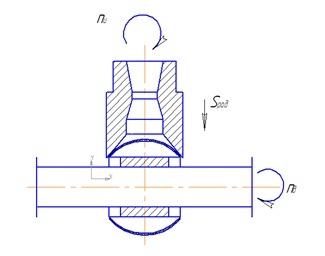
Picture 1 – The scheme grinding tapered round
This process of grinding tube grinding wheels can be attributed to the few cases in which the main motion are both rotational motion, which is determined in the aggregate required for the grinding of the resulting cutting speed. Specifically, the issue should be resolved feasibility of a constructive solutions. This process should ensure that stock removal, sufficient to achieve the required accuracy of the size, shape, as well as error compensation based.
Reducing the grain size of the circle, makes the process of grinding to finishing and finishing. But then the feasibility of its implementation on the hard axis tool and the tool is questionable. On the contrary, it is necessary to release one of the elements - the grinding head to give her the opportunity to self-aligning on the treated surface, which will ensure the process of honing and polishing..
Reducing the grain size of the circle, makes the process of grinding to finishing and finishing. But then the feasibility of its implementation on the hard axis tool and the tool is questionable. On the contrary, it is necessary to release one of the elements - the grinding head to give her the opportunity to self-aligning on the treated surface, which will ensure the process of honing and polishing.
Another advantage is the ability to install instead of the tool ring-saddle valve, but instead details - cast iron lap and make processing of the ring, and then grind the ball and the seat itself, using a fine abrasive free in paste form.
Conclusion
Thus, we have chosen the method of processing, implemented in legacy equipment that allows the processing of spherical ceramic products, with the required parameters of accuracy and quality.
In writing this essay master's work is not yet complete. Final completion: December 2013. Full text of the work and materials on the topic can be obtained from the author or his manager after that date.
References
- Горяинов Д.С. Повышение эффективности хонингования сферических поверхностей деталей из нержавеющих сталей, Самарский государственный технический университет, 2009 г.
- Меркушкин А. О. Керамика на основе алюминатов редкоземельных элементов. 2012 г.
- Управление формообразованием функциональных поверхностей из керамических композиционных материалов с использованием методов алмазной доводки. // Вестник МГТУ «Станки». 2011. № 1. С. 51 – 57.
- Особенности формирования функциональных свойств изделий из керамических материалов методами доводки // Вестник УГАТУ. 2009. т.12. №4 (33). С. 66 – 71.
- О Бахарев, В. П. Конструкторско-технологическое сопровождение производства изделий из керамических и композиционных материалов / В. П. Бахарев // Конструкции из композиционных материалов. М.: 2008 г. .
- А.Г. Ткачев, И.Н. Шубин, типовые технологические процессы изготовления деталей машин, 2007 г.
- Электронная библиотека. Исследование режущей способности алмазных шлифовальных кругов при плоском врезном шлифовании титановых сплавов
- Исследование режущей способности алмазных шлифовальных кругов при плоском врезном шлифовании титановых сплавов [электронный ресурс]. – Режим доступа: http://www.plasmacentre.ru/...