Реферат по теме выпускной работы
Содержание
- Введение
- 1. Актуальность темы
- 2. Цели и задачи исследования
- 3. Обзор существующих токарных станков и технологии обработки конических поверхностей
- 3.1 Обзор существующих разновидностей токарных станков
- 3.2 Радиометрическая схема, позволяющая контролировать толщину стенки заготовки
- 4. Алгоритмы работы прибора
- 4.1 Алгоритм проверки целостности изделия
- 4.2 Алгоритм обработки изделия
- Выводы
- Список источников
Введение
Известно, что сейчас на производстве стараются ограничивать ручной труд и по возможности отказываются от него – вместо людей начинают работать машины. И действительно, технологии не стоят на месте, оборудование позволяет производить работы более точно и с меньшим процентом брака. Более того, многие виды работ, раньше длившиеся очень долго теперь выполняются машинами с потрясающей точностью и за очень короткий промежуток времени.
Соответственно автоматизация производства является важной задачей для любого предприятия, которое идет в ногу со временем, однако этот процесс не всегда проходит легко и гладко. Для достижения наилучшего результата приходится применять новые методы и научные разработки. Процесс модификации и интеграции АСУ временами становится сложной и затратной задачей, однако при правильном подходе в большинстве случаев внедрение АСУ значительно улучшает показатели производства.
1. Актуальность темы
В настоящее время обработка заготовок сложной формы с точным контролем толщины стенки изделия в большой степени состоит из ручной работы, так как мастер должен снимать заготовку с токарного станка и производить соответствующие измерения микрометром. Это существенно увеличивает время на производство одной детали, так же данный способ не надежен с точки зрения человеческого фактора – мастер при измерениях может допустить ошибку. При данном способе существует большая вероятность брака – при обработке изделия мастер может не правильно выбрать момент, когда обработку следует остановить, в следствии этого повышается вероятность брака на производстве.
Эти причины и обуславливают необходимость автоматизации контроля на рабочем месте толщины стенки заготовок на производстве.
2. Цели и задачи исследования
Целью магистерской работы является разработка автоматизированной системы управления токарным станком с применением радиометрической системы.
В ходе выполнения работы планируется выполнение следующих задач:
1. Анализ существующих методов обработки изделий;
2. Выбор токарного станка и радиометрической системы, подходящих для задачи автоматизации;
3. Моделирование процесса измерения толщины стенки детали;
4. Разработка алгоритма проверки целостности и однородности заготовки с помощью электромагнитного КВЧ-излучения;
5. Разработка алгоритма функционирования автоматизированного фрезерного станка, позволяющего обрабатывать заготовки с требуемым значением толщины;
3. Обзор существующих токарных станков и технологии обработки конических поверхностей
На сегодняшний день существует несколько видов токарных станков, предназначенных для обработки деталей различного вида и имеющих разную производительность. Также их можно разделить на автоматизированные и не автоматизированные станки.
3.1 Обзор существующих разновидностей токарных станков[1-3]
Токарные станки, в зависимости от их конструкции и выполняемых функций, делятся на виды[1]:
- Токарно-винторезный станок;
- Токарно-револьверный станок;
- Настольные токарные станки;
- Токарно-карусельный станок;
- Автомат продольного точения;
- Станки с ЧПУ.
Различные станки выполняют специализированные задачи, однако для автоматизации производства заготовок конической формы наиболее подходит токарно-винторезный станок с ЧПУ[3], так как такой станок уже имеет в своем составе программируемый логический контроллер, который позволяет производить обработку детали согласно заданной программе.

Рисунок 3.1. – Токарно-винторезный станок с ЧПУ
Однако данный станок не позволяет производить оценку толщины стенки изделия[4], соответственно его необходимо дополнить системой, способной производить соответствующие измерения.
3.2 Радиометрическая схема, позволяющая контролировать толщину стенки заготовки[5]
Данная система используется для неразрушающего контроля технологических параметров объектов, которые определяются по изменению фазы отраженных от них электромагнитных колебаний КВЧ-диапазона. Это позволит контролировать толщину стенки изделия автоматически с высокой точностью.
В радиометрической системе для измерения толщины стенки детали антенны работают как на передачу, так и на прием сигнала, измерение осуществляется по очереди, количество антенн определяется характеристиками изделия – чем больше изделие – тем больше антенн требуется для точного измерения (необходимо чтобы вся поверхность изделия попадала в поле излучения антенн).
На рисунке 3.2 представлено расположение антенн относительно изделия
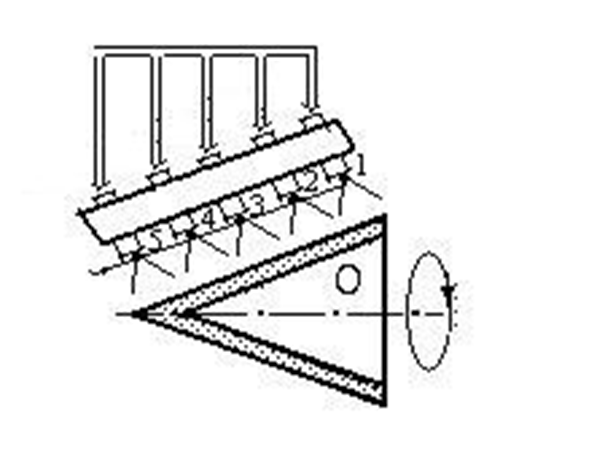
Рисунок 3.2. – Расположение антенн в радиометрической системе для измерения толщины стенки детали
На рисунке 3.2 позициями 1-5 обозначены антенны, направленные на внешнюю поверхность детали (изделия).
Управление передачей и приемом сигналов с антен, а так же их коммутация осуществляются с помощью контроллера станка с ЧПУ.
Полная радиометрическая схема представлена на рисунке 3.3
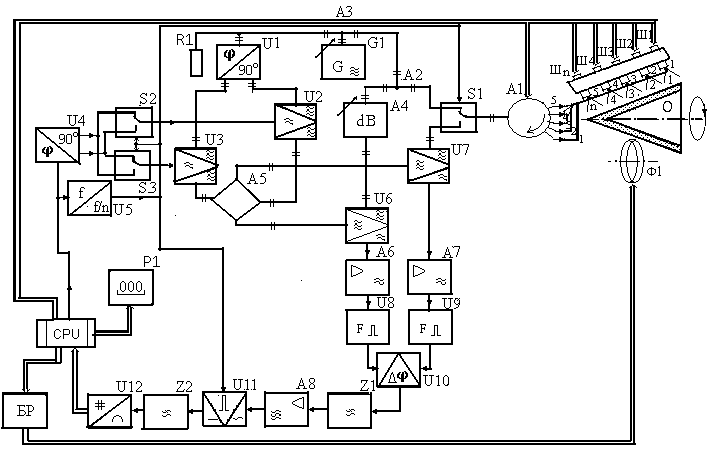
Рисунок 3.3. – Функциональная схема радиометрической системы для измерения толщины стенки изделия на рабочем месте при их механической обработке.
Схема содержит в себе генератор G1 гармонических колебаний КВЧ-диапазона, делители мощности A2 и А3, подключенные к генератору G1, автоматический переключатель S1 и циркулятор A1 с соединенными приемно-передающими антеннами 1 – n, закрепленными на соответствующих подвижных штоках Ш1 – Шn, расположенных на скобе, которая повторяет форму изделия и направленными на контролируемый объект О
, согласующий аттенюатор А4, подключенный к другому выходу делителя мощности А2, КВЧ-балансные смесители U6 и U7, к выходам которых подключены последовательно соединенные усилители промежуточной частоты A6 и A7, формировщики коротких импульсов U8 и U9 и линейный фазовый детектор U10 на триггерах. Ко второму выходу делителя мощности А3 подключен КВЧ-квадратурный фазоделитель U1, к выходам которого через КВЧ-балансные модуляторы U2 и U3 подключен двойной волноводный тройник А5, выходы которого соединены с другими входами КВЧ-балансных смесителей U6 и U7, низкочастотный гетеродин, встроенный в микроЭВМ cpu и соединенный с низкочастотным квадратурным фазоделителем U4, выходы которого через автоматические переключатели S2 и S3 соединены с модулирующими входами КВЧ-балансных модуляторов U2 и U3. Делитель частоты U5 соединяет управляющие входы автоматических переключателей S2 и S3 и выход низкочастотного гетеродина, встроенного в микроЭВМ cpu. К выходу триггерного фазового детектора U10 подлючены последовательно соединенные фильтр верхних частот Z1, усилитель низкой частоты A8, синхронный детектор U11, фильтр нижних частот Z2, аналогово-цифровой преобразователь U12, микроЭВМ cpu и цифровой индикатор P1. Управляющий вход синхронного детектора U11 соединен с управляющими входами автоматических переключателей S2 и S3. Цифровой выход микроЭВМ cpu соединен с кодоуправляемым блоком регулирования (БР) режимом механической обработки изделия фрезой Ф1.
4. Алгоритмы работы прибора
4.1Алгоритм проверки целостности изделия[6]:

Рисунок 4.1. – Алгоритм проверки целостности изделия.
A1c – начальное значение коэффициента затухания 1-го аттенюатора
А2с – начальное значение 2-го аттенюатора
Uцел – целевое значение коэффициента поглощения
U[i][j] – значение коэффициента поглощения в заданной точке
Af[i][j] – значение отклонения коэффициента затухания 1-го аттенюатора в заданной точке
ε – допустимое отклонение коэффициента поглощения
A1 – текущее значение коэффициента затухания аттенюатора А1
r – режим работы аппарата
t – текущая температура изделия
tc – целевая температура изделия
Lцел – целевое значение излучения объекта
L[i][j] – значение излучения объекта в заданной точке
As[i][j] – значение коэффициента затухания 2-го аттенюатора в заданной точке
ε1 – допустимое отклонение излучения объекта
A2 – текущее значение коэффициента затухания аттенюатора А2
Сначала происходит ввод эталонных значений, а также допустимых отклонений и целевой температуры. Далее происходит измерение коэффициента поглощения. Если уровень сигнала отличается от эталонного – изменяется значение затухания кодоуправляемого аттенюатора А1, пока значение не будет соответствовать эталонному. Величина изменения коэффициента затухания А1 и координаты зоны излучения запоминаются компьютером.
Далее происходит построение графика с заданным шагом коэффициентов поглощения материала по всей поверхности изделия (вывод коэффициентов поглощения и изменений коэффициентов затухания А1). Потом система переходит на другой режим излучения.
Производится нагревание материала до заданной температуры и ее поддержание в течении всего второго режима измерений. Потом происходит измерение излучения. Если значение входного сигнала отличается от эталонного, на аттенюатор А2 подается сигнал, изменяющий его затухание до значения, соответствующего эталонному значению сигнала Проведенные измерения также фиксируются и строится график (вывод значений излучения и коэффициентов затухания А2 во всех точках).
Далее происходит сравнение результатов первого и второго режимов работы и с эталонными показателями. (Еще один вывод коэффициентов, не соответствующих эталонным).
Места, где коэффициенты не соответствуют эталонным являются подозрительными на брак.
4.2 Алгоритм обработки изделия[7]
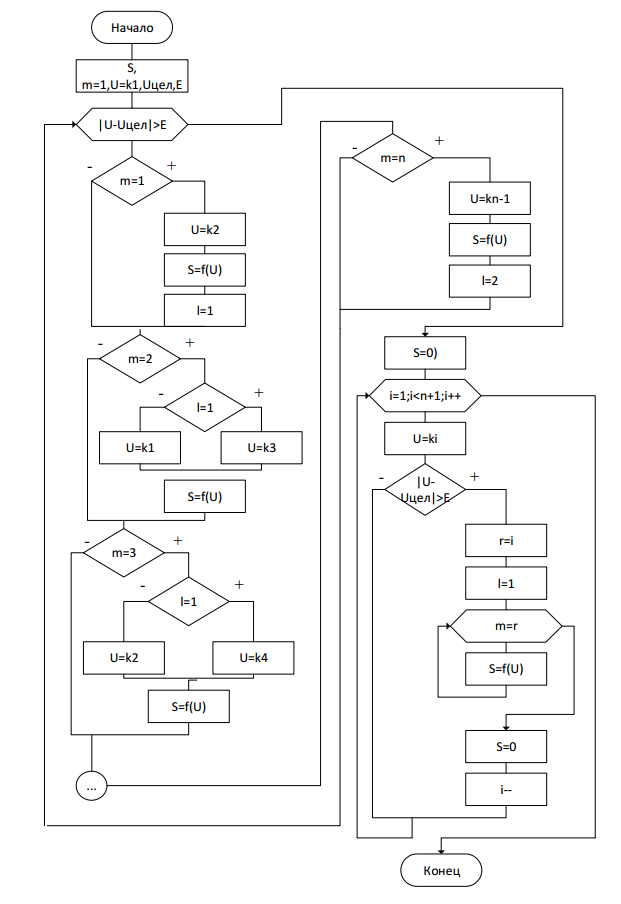
Рисунок 4.2. – Алгоритм обработки изделия
При разработке алгоритма были использованы такие условные обозначения:
m – положение фрезы относительно зоны приема отражения сигнала;
S – глубина подачи фрезы;
U – текущее значение фазы зондирующего сигнала;
Uцел – целевое значение фазы зондирующего сигнала;
E – допустимое значение разницы фаз зондирующего сигнала, согласно заданному значению толщины обрабатываемого изделия;
массив k – значения фаз зондирующего сигнала с антенн (количество элементов в массиве равняется количеству антенн);
l – направление движения фрезы;
r – управляемое положение относительно антенн (1–n).
Измерение коэффициента производится с опережением (коэффициент измеряется перед фрезой).
При количестве излучающих антенн равном n, изделие разбивается на n зон, в которых может находиться фреза. Текущее положение фрезы соответствует переменной m, в начале программы фреза располагается на начале изделия, соответственно m=1. Также в начале необходимо указать целевое значение фазы зондирующего сигнала, к которому мы будем стремиться при обработке изделия и E – допустимое значение разницы фаз, согласно заданному значению толщины стенки, оно будет использоваться для определения момента завершения обработки изделия. Текущее значение фазы зондирующего сигнала определяется по показаниям антенны.
Пока не выполнится условие |U-Uцел|> E, выполняется механическая обработка изделия. Изделие обрабатывается согласно с текущим значением фазы зондирующего сигнала U (регулируется глубина подачи фрезы). Текущее значение фазы зондирующего сигнала U определяется по положению фрезы с опережением – если фреза находится в первой зоне приема-отражения сигнала – текущее значение фазы зондирующего сигнала берется со 2-й антенны, U=k2, вычисляется глубина подачи фрезы S=f(U), направление движения фрезы устанавливается равным 1, l=1, если фреза находится во второй зоне и направление движения фрезы берется с антенны 3, U=k3, если же направление движения фрезы не равняется 1, текущее значение фазы берется с антенны 1, U=k1, вычисляется глубина подачи фрезы S=f(U), аналогично проводится определение текущего значения фазы зондирующего сигнала и глубины подачи фрезы вплоть до n-й зоны, при нахождении фрезы в n-й зоне, m=n, текущее значение фазы берется с антенны (n-1), U=kn-1, вычисляется глубина подачи фрезы S=f(U), направление движения фрезы устанавливается равным 2, l=2.
Когда достигается условие |U-Uцел|> E, механическая обработка изделия останавливается, S=0. Далее необходимо выполнить проверку, в каждой ли зоне достигнут желаемый результат? Для этого, работает цикл i = 1; i <n +1; i + +, проводится проверка: текущее значение фазы зондирующего сигнала присваивается антенне соответственно индексу i, U=ki, выполняется проверка |U-Uцел|> E, если результат сравнения положительный – заданная точность не достигнута, фреза перемещается в начало i-й зоны, r=i, направление движения фрезы устанавливается равным 1, l=1, пока фреза находится в необходимой зоне, m=r, определяется глубина подачи фрезы S=f(U), когда фреза выходит из заданной зоны, она перестает подаваться, S=0, так как целевая точность может быть не достигнута, производится уменьшение итератора i, i--.
По окончанию алгоритма необходимая точность будет достигнута на всех n участках.
Работу радиометрической схемы можно наблюдать на рисунке 4.3

Рисунок 4.3. – Работа схемы
Выводы
На основе поставленных целей и задач были проанализированы различные типы фрезерных станков и методов обработки изделий сложной формы. Был выбран тип станка наиболее подходящий для автоматизации, рассмотрена радиометрическая система, позволяющая осуществлять неразрушающий контроль изделия, были предложены алгоритмы проверки целостности и однородности заготовки с помощью электромагнитного КВЧ-излучения и функционирования автоматизированного фрезерного станка, позволяющего обрабатывать заготовки с требуемым значением толщины.
При написании данного реферата магистерская работа еще не завершена. Окончательное завершение: декабрь 2014 года. Полный текст работы и материалы по теме могут быть получены у автора или его руководителя после указанной даты.
Список источников
- Модзелевский А.А., Мущинкин А.А., Кедров С.С., Соболь А.М., Завгородний Ю.П. Токарные станки / А.А. Модзелевский // Машиностроение. – 1973. – 282с.
- Фещенко В.Н. Токарная обработка / В.Н.Фещенко – Высш. шк. – 2005. – 303 с.
- Панов Ф. С., Травин А. И. Работа на станках с числовым программным управлением / Ф.С Панов. – Л.:Лениздат – 1984. – 278с.
- Головко Д.Б., Скрипник Ю.О., Яненко О.П. Надвисокочастотні методи та засоби вимірювання фізичних величин. / Д.Б. Головко – К.: Либідь, 2003. – 328 с.
- Куценко В.П., Скрипник Ю.А., Трегубов Н.Ф., Шевченко К.Л., Яненко А.Ф. Методы и средства сверхвысоко-частотной радиометрии / В.П. Куценко – Донецк: ИИиИИ «Наука і освіта», 2011. – 324 с.
- Звіт про виконання науково-дослідної роботи „Розробка алгоритмів оптимального управління системами неруйнівного контролю в умовах технологічних процесів виробництва продукції на ККНВП „Кварсит” — Донецк: ДонНТУ, 2012. – 92 с.
- Довгопол В.А., Куценко В.П. Разработка алгоритма работы радиометрической системы контроля параметров диэлектрических изделий. / В.А. Довгопол – Матерiали IV мiжнародної науково-технiчної конференцiї студентiв, аспiрантiв та молодих вчених. — Донецьк, ДонНТУ — 2013, Том 1, с. 533–537.