Реферат за темою дипломної роботи
Зміст
- Вступ
- 1. Актуальність теми
- 2. Цілі і завдання дослідження
- 3. Огляд існуючих токарних верстатів і технології обробки конічних поверхонь
- 3.1 Огляд існуючих різновидів токарних верстатів
- 3.2 Радіометрична схема, що дозволяє контролювати товщину стінки заготівки
- 4. Алгоритми роботи приладу
- 4.1 Алгоритм перевірки цілісності виробу
- 4.2 Алгоритм обробки виробу
- Висновки
- Перелiк посилань
Вступ
Відомо, що зараз на виробництві намагаються обмежувати ручну працю і по можливості відмовляються від неї – замість людей починають працювати машини. І дійсно, технології не стоять на місці, устаткування дозволяє проводити роботи більш точно і з меншим відсотком браку. Більше того, багато видів робіт, які раніше тривали дуже довго, тепер виконуються машинами з приголомшливою точністю і за дуже короткий проміжок часу.
Відповідно автоматизація виробництва є важливим завданням для будь-якого підприємства, яке йде в ногу з часом, однак цей процес не завжди проходить легко і гладко. Для досягнення найкращого результату доводиться застосовувати нові методи і наукові розробки. Процес модифікації та інтеграції АСУ часом стає складним і витратним завданням, проте при правильному підході в більшості випадків впровадження АСУ значно покращує показники виробництва.
1. Актуальність теми
На сьогодні обробка матеріалів складної форми з точним контролем товщини стінки виробу у великій мірі складається з ручної роботи, так як майстер повинен знімати заготівлю з токарного верстата і проводити відповідні вимірювання мікрометром. Це істотно збільшує час на виробництво однієї деталі, так само даний спосіб не надійний з точки зору людського фактору – майстер при вимірах може допустити помилку. При даному способі існує велика ймовірність браку – при обробці виробу майстер може не правильно вибрати момент, коли обробку слід зупинити, в наслідок цього підвищується ймовірність браку на виробництві.
Ці причини і обумовлюють необхідність автоматизації контролю товщини стінки заготовок на виробництві.
2. Цілі і завдання дослідження
Метою магістерської роботи є розробка автоматизованої системи управління токарним верстатом із застосуванням радіометричної системи.
У ході виконання роботи планується виконання наступних завдань:
1. Аналіз існуючих методів обробки виробів;
2. Вибір токарного верстата і радіометричної системи, відповідних для завдання автоматизації;
3. Моделювання процесу вимірювання товщини стінки деталі;
4. Розробка алгоритму перевірки цілісності та однорідності заготовки за допомогою електромагнітного НВЧ-випромінювання;
5. Розробка алгоритму функціонування автоматизованого фрезерного верстата, що дозволяє обробляти заготовки з необхідним значенням товщини;
3. Огляд існуючих токарних верстатів і технології обробки конічних поверхонь
На сьогоднішній день існує декілька видів токарних верстатів, призначених для обробки деталей різного виду, що мають різну продуктивність. Також їх можна розділити на автоматизовані і не автоматизовані верстати.
3.1 Огляд існуючих різновидів токарних верстатів[1-3]
Токарні верстати, в залежності від їх конструкції і виконуваних функцій, поділяються на види[1]:
- Токарно-гвинторізний верстат;
- Токарно-револьверний верстат;
- Настільні токарні верстати;
- Прокатні верстати;
- Автомат поздовжнього точіння;
- Верстати з ЧПК.
Різні верстати виконують спеціалізовані завдання, однак для автоматизації виробництва заготовок конічної форми найбільш підходить токарно-гвинторізний верстат з ЧПК[3], так як такий верстат вже має у своєму складі програмований логічний контролер, який дозволяє проводити обробку деталі згідно з заданою програмою.

Рисунок 3.1. – Токарно-гвинторізний верстат з ЧПК
Однак даний верстат не дозволяє робити оцінку товщини стінки виробу[4], відповідно його необхідно доповнити системою, здатною проводити відповідні вимірювання.
3.2 Радіометрична схема, що дозволяє контролювати товщину стінки заготівки[5]
Дана система використовується для неруйнівного контролю технологічних параметрів об'єктів, які визначаються по зміні фази відбитих від них електромагнітних коливань НВЧ-діапазону. Це дозволить контролювати товщину стінки виробу автоматично з високою точністю.
У радіометричній системі для вимірювання товщини стінки деталі антени працюють як на передачу, так і на прийом сигналу, вимірювання здійснюється по черзі, кількість антен визначається характеристиками виробу – чим більше виріб – тим більше антен потрібно для точного виміру (необхідно щоб вся поверхня виробу потрапляла в поле випромінювання антен).
На рисунку 3.2 представлено розташування антен щодо виробу
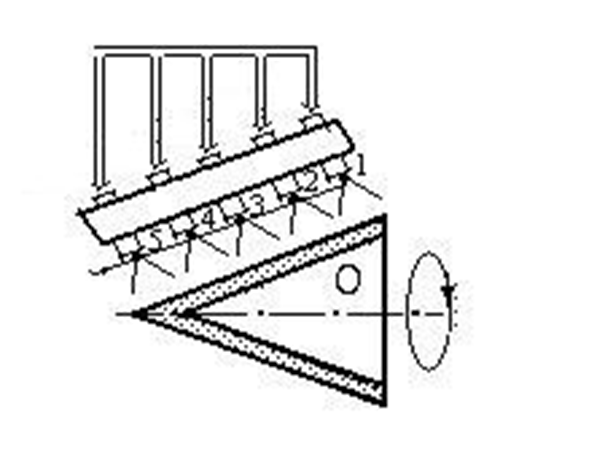
Рисунок 3.2. – Розташування антен в радіометричній системі для вимірювання товщини стінки деталі
На рисунку 3.2 позиціями 1-5 позначені антени, спрямовані на зовнішню поверхню деталі (виробу).
Управління передачею і прийомом сигналів з антен, а так само їх комутація здійснюються за допомогою контролера верстата з ЧПК.
Повна радіометрична схема представлена на рисунку 3.3
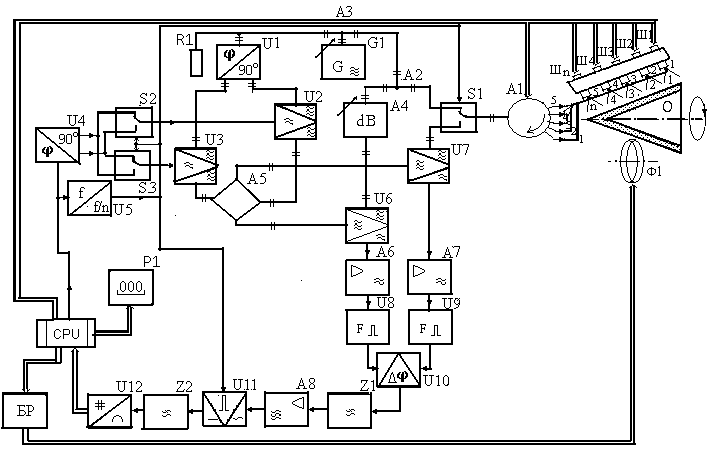
Рисунок 3.3. – Функціональна схема радіометричної системи для вимірювання товщини стінки виробу на робочому місці при його механічній обробці.
Схема містить у собі генератор G1 гармонійних коливань НВЧ-діапазону, подільники потужності A2 і А3, підключені до генератора G1, автоматичний перемикач S1 і циркулятор A1 із сполученими приймально-передавальними антенами 1 – n, закріпленими на відповідних рухомих штоках Ш1 – Шn, розташованих на скобі, яка повторює форму виробу і спрямованими на контрольований об'єкт О, узгоджувальний атенюатор А4, підключений до іншого виходу дільника потужності А2, КВЧ-балансні змішувачі U6 і U7, до виходів яких підключені послідовно з'єднані підсилювачі проміжної частоти A6 і A7, Формувальник коротких імпульсів U8 і U9 і лінійний фазовий детектор U10 на тригерах. До другого виходу дільника потужності А3 підключений НВЧ-квадратурний фазоделітель U1, до виходів якого через НВЧ-балансні модулятори U2 і U3 підключений подвійний хвилеводний трійник А5, виходи якого з'єднані з іншими входами НВЧ-балансних змішувачів U6 і U7, низькочастотний гетеродин, вбудований в мікроЕОМ cpu і сполучений з низькочастотним квадратурних фазоделітелем U4, виходи якого через автоматичні перемикачі S2 і S3 з'єднані з модулюючим входами НВЧ-балансних модуляторів U2 і U3. Дільник частоти U5 з'єднує керуючі входи автоматичних перемикачів S2 і S3 і вихід низькочастотного гетеродина, вбудованого в мікроЕОМ cpu. До виходу тригерного фазового детектора U10 подлючен послідовно з'єднані фільтр верхніх частот Z1, підсилювач низької частоти A8, синхронний детектор U11, фільтр нижніх частот Z2, аналогово-цифровий перетворювач U12, мікроЕОМ cpu і цифровий індикатор P1. Керуючий вхід синхронного детектора U11 з'єднаний з керуючими входами автоматичних перемикачів S2 і S3. Цифровий вихід мікроЕОМ cpu з'єднаний з кодокерованим блоком регулювання (БР) режимом механічної обробки виробу фрезою Ф1.
4. Алгоритми роботи приладу
4.1Алгоритм перевірки цілісності виробу[6]:

Рисунок 4.1. – Алгоритм перевірки цілісності виробу.
A1c – початкове значення коефіцієнта загасання 1-го атенюатора
А2с – початкове значення 2-го атенюатора
Uцел – цільове значення коефіцієнта поглинання
U[i][j] – значення коефіцієнта поглинання в заданій точці
Af[i][j] – начення відхилення коефіцієнта загасання 1-го атенюатора в заданій точці
ε – допустиме відхилення коефіцієнта поглинання
A1 – поточне значення коефіцієнта загасання атенюатора А1
r – режим роботи апарату
t – поточна температура виробу
tc – цільова температура виробу
Lцел – цільове значення випромінювання об'єкта
L[i][j] – значення випромінювання об'єкта в заданій точці
As[i][j] – значення коефіцієнта загасання 2-го атенюатора в заданій точці
ε1 – допустиме відхилення випромінювання об'єкта
A2 – поточне значення коефіцієнта загасання атенюатора А2
Спочатку відбувається введення еталонних значень, а також допустимих відхилень і цільової температури. Далі відбувається вимір коефіцієнта поглинання. Якщо рівень сигналу відрізняється від еталонного – змінюється значення загасання кодоуправляемого атенюатора А1, поки значення не буде відповідати еталонному. Величина зміни коефіцієнта загасання А1 і координати зони випромінювання запам'ятовуються комп'ютером.
Далі відбувається побудова графіка з заданим кроком коефіцієнтів поглинання матеріалу по всій поверхні виробу (виведення коефіцієнтів поглинання і змін коефіцієнтів загасання А1). Потім система переходить на інший режим випромінювання.
Проводять нагрівання матеріалу до заданої температури і її підтримку на протязі всього другого режиму вимірювань. Потім відбувається вимір випромінювання. Якщо значення вхідного сигналу відрізняється від еталонного, на атенюатор А2 подається сигнал, що змінює його затухання до значення, відповідного еталонного значення сигналу Проведені вимірювання також фіксуються і будується графік (виведення значень випромінювання і коефіцієнтів загасання А2 у всіх точках).
Далі відбувається порівняння результатів першого і другого режимів роботи і з еталонними показниками. (Ще один вивід коефіцієнтів, що не відповідають еталонним).
Місця, де коефіцієнти не відповідають еталонним є підозрілими на брак.
4.2 Алгоритм обробки виробу[7]
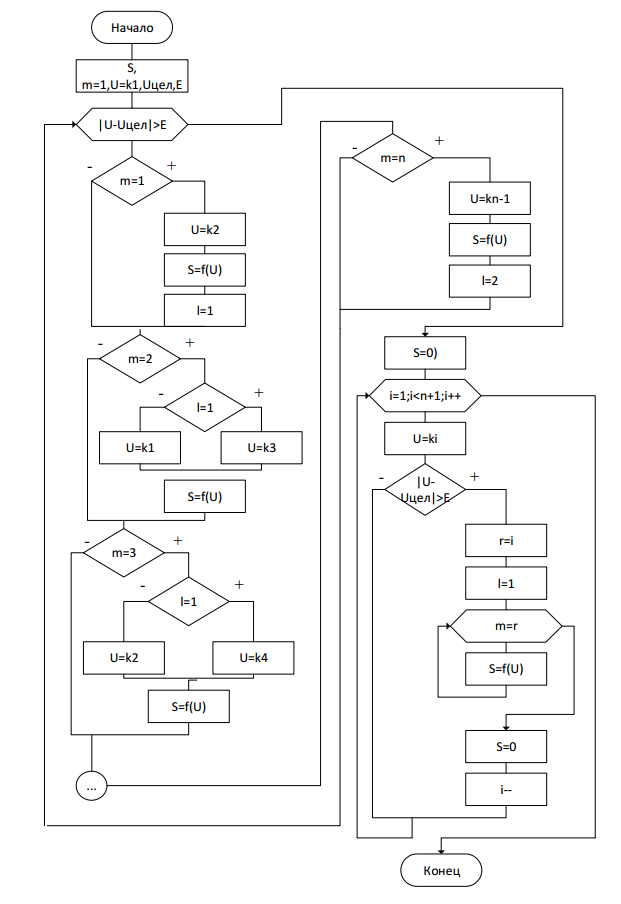
Рисунок 4.2. – Алгоритм обробки виробу
При розробці алгоритму були використані такі умовні позначення:
m – положення фрези щодо зони прийому відображення сигналу;
S – глибина подачі фрези;
U – поточне значення фази зондуючого сигналу;
Uцел – цільове значення фази зондуючого сигналу;
E – допустиме значення різниці фаз зондуючого сигналу, згідно заданому значенню товщини оброблюваного виробу;
массив k – значення фаз зондуючого сигналу з антен (кількість елементів у масиві дорівнює кількості антен);
l – напрямок руху фрези;
r – кероване положення щодо антен (1–n).
Вимірювання коефіцієнта здійснюється з випередженням (коефіцієнт вимірюється перед фрезою).
При кількості випромінюючих антен рівній n, виріб розбивається на n зон, в яких може перебувати фреза. Поточне положення фрези відповідає змінній m, на початку програми фреза розташовується на початку виробу, відповідно m = 1. Також на початку необхідно вказати цільове значення фази зондуючого сигналу, до якого ми будемо прагнути при обробці виробу і E – допустиме значення різниці фаз, згідно заданому значенню товщини стінки, воно буде використовуватися для визначення моменту завершення обробки виробу. Поточне значення фази зондуючого сигналу визначається за показаннями антени.
Доки не виконається умова|U-Uцел|> E, виконується механічна обробка виробу. Виріб обробляється згідно з поточним значенням фази зондуючого сигналу U (регулюється глибина подачі фрези). Поточне значення фази зондуючого сигналу U визначається за положенням фрези з випередженням – якщо фреза знаходиться в першій зоні прийому-відображення сигналу - поточне значення фази зондуючого сигналу береться з 2-й антени, U = k2, обчислюється глибина подачі фрези S = f (U), напрямок руху фрези встановлюється рівним 1, l = 1, якщо фреза знаходиться в другій зоні і напрямок руху фрези береться з антени 3, U = k3, якщо ж напрямок руху фрези НЕ дорівнює 1, поточне значення фази береться з антени 1, U = k1, обчислюється глибина подачі фрези S = f (U), аналогічно проводиться визначення поточного значення фази зондуючого сигналу і глибини подачі фрези аж до n-ї зони, при знаходженні фрези в n-й зоні, m = n, поточне значення фази береться з антени (n-1), U = kn-1, обчислюється глибина подачі фрези S = f (U), напрямок руху фрези встановлюється рівним 2, l = 2.
Коли досягається умова |U-Uцел|> E, механічна обробка виробу зупиняється, S = 0. Далі необхідно виконати перевірку, в кожній Чи зоні досягнутий бажаний результат. Для цього, працює цикл i = 1; i
По закінченню алгоритму необхідна точність буде досягнута на всіх n ділянках.
Роботу радіометричної схеми можна спостерігати на рисунку 4.3

Рисунок 4.3. – Робота схеми
Висновки
На основі поставлених цілей і завдань були проаналізовані різні типи фрезерних верстатів і методів обробки виробів складної форми. Був обраний тип верстата найбільш відповідний для автоматизації, розглянута радіометрична система, що дозволяє здійснювати неруйнівний контроль виробу, були запропоновані алгоритми перевірки цілісності та однорідності заготовки за допомогою електромагнітного КВЧ-випромінювання та функціонування автоматизованого фрезерного верстата, що дозволяє обробляти заготовки з необхідним значенням товщини.
При написанні даного реферату магістерська робота ще не завершена. Остаточне завершення: грудень 2013 року. Повний текст роботи та матеріали по темі можуть бути отримані у автора або його керівника після зазначеної дати.
Перелiк посилань
- Модзелевский А.А., Мущинкин А.А., Кедров С.С., Соболь А.М., Завгородний Ю.П. Токарные станки / А.А. Модзелевский // Машиностроение. – 1973. – 282с.
- Фещенко В.Н. Токарная обработка / В.Н.Фещенко – Высш. шк. – 2005. – 303 с.
- Панов Ф. С., Травин А. И. Работа на станках с числовым программным управлением / Ф.С Панов. – Л.:Лениздат – 1984. – 278с.
- Головко Д.Б., Скрипник Ю.О., Яненко О.П. Надвисокочастотні методи та засоби вимірювання фізичних величин. / Д.Б. Головко – К.: Либідь, 2003. – 328 с.
- Куценко В.П., Скрипник Ю.А., Трегубов Н.Ф., Шевченко К.Л., Яненко А.Ф. Методы и средства сверхвысоко-частотной радиометрии / В.П. Куценко – Донецк: ИИиИИ «Наука і освіта», 2011. – 324 с.
- Звіт про виконання науково-дослідної роботи „Розробка алгоритмів оптимального управління системами неруйнівного контролю в умовах технологічних процесів виробництва продукції на ККНВП „Кварсит” — Донецк: ДонНТУ, 2012. – 92 с.
- Довгопол В.А., Куценко В.П. Разработка алгоритма работы радиометрической системы контроля параметров диэлектрических изделий. / В.А. Довгопол – Матерiали IV мiжнародної науково-технiчної конференцiї студентiв, аспiрантiв та молодих вчених. — Донецьк, ДонНТУ — 2013, Том 1, с. 533–537.