Реферат по теме выпускной работы
Содержание
- Введение
- 1. Актуальность темы
- 2. Анализ особенностей устройства и эксплуатации объекта исследований
- 3. Цели и задачи исследования
- 4. Теоретический анализ свойств устройств ускоренного торможения АД
- Выводы
- Перечень ссылок
Введение
Основой технического процесса на угольных шахтах является широкое использование высокопроизводительных добычных комплексов, оснащенных современным взрывобезопасным электрооборудованием. Их внедрение обеспечивает значительное повышения производительности работы предприятия. Высокая эффективность угледобычи в значительной мере зависит от эффективной работы шахтного транспорта, в частности конвейерного, значение которого становиться все более важным в связи с увеличением мощности угледобывающих машин. В настоящее время в качестве забойных повсеместно используются скребковые конвейеры, которые наиболее адаптированы к условиям функционирования очистного механизированного комплекса. Для ведущих угледобывающих шахт характерно повышение степени концентрации горных работ, рост погрузки на очистной забой, при сокращении их числа и одновременном увеличении длины и скорости подвигания. Все эти причины обуславливают повышение нагрузки на забойный скребковый конвейер. Как следствие, разрабатываются и внедряются в производство скребковые конвейеры все большой длины и с более мощными приводами.
1. Актуальность темы
Из анализа конструкции и условий эксплуатации скребковых конвейеров следует, что пуск их сопровождается высоким моментом сопротивления, который создается цепью со скребками и перемещаемой горной массой. Кроме этого конструкция скребкового конвейера допускает заштыбовку и заклинивание тягового органа, что является критичной порывов скребковой цепи. С целью осуществления снижения перегрузов привода они оснащены нерегулируемой гидромуфтой. Опыт эксплуатации показывает, что свои пускозащитные функции гидромуфта выполняет неудовлетворительно, имеет малый фактический срок службы, низкую надежность. Обладая значительным моментом инерции, вращающая часть муфты повышает растягивающее усилие в скребковой цепи в момент заклинивания, чем способствует не защите, а порыву последней.
Срабатывание защиты гидромуфты сопряжено с простоями скребкового конвейера, обусловленными временем на повторную заливку в нее эмульсии, установку новой плавкой пробки. Это влечет и дополнительные материальные затраты.
Этим обусловливается актуальность создания более эффективного метода защиты скребкового конвейера от стопорения.
2. Анализ особенностей устройства и эксплуатации объекта исследований
В настоящее время скребковые конвейеры остаются самым многочисленным видом транспортных средств на шахтах, ленточных конвейеров меньше, чем скребковых в 1,6 раза, электровозов – в 2,5 раза (рис. 1) [5].
Привод конвейера состоит из рамы привода, одного или двух приводных блоков (двигатель – гидромуфта – редуктор) и двух приводных звездочек, передающих тяговое усилие на скребковую цепь конвейера.
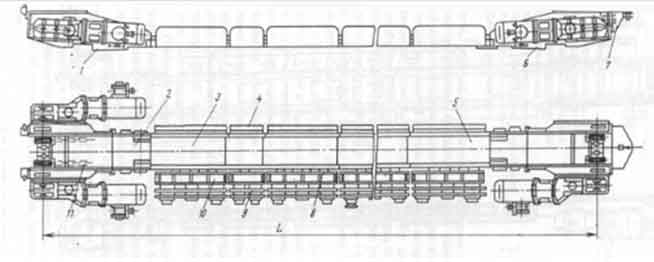
Рисунок 1 – Типовая конструкция шахтного скребкового конвейера: привод головной 1, переходные секции 2 у головного и концевого приводов, переходные рештаки 3 и 5, лемеха 4, привод концевой 6 (или концевой головки) линейный рештак, отклоняющий ролик 7 для направления каната предохранительной лебедки комбайна, направляющие комбайна 8, борта кабелеукладчика 9, борта 10, скребковая цепь 11, кронштейны для размещения кабелей, кронштейны светильников [5]
Функциональным элементом привода конвейера, специально предназначенным для замедления разгона, является гидромуфта, содержащая оребренные насосные и турбинное колеса, полость между которыми заполнена эмульсией. Влияние гидромуфты на динамику пуска электропривода скребкового конвейера объясняются ее механической характеристикой (рис. 2):
Mm = a1vн2 + a2vн vm + a3vm2 , (1)
где а1, а2, а3 – постоянные для отдельных зон семейства механических характеристик; Мm – момент на валу турбинного колеса гидромуфты; vн, vm – угловые скорости насосного и турбинного колес [5].
Близкий к номинальному момент на валу турбинного колеса гидромуфты в процессе пуска может быть получен при угловой скорости насосного колеса, близкой к номинальной. Поэтому, в начале пуска двигатель конвейера разгоняется почти без нагрузки, а в конце разгона ротора движение рывком передается к скребковой цепи, что является фактором повышения динамических нагрузок в трансмиссии конвейера.
Резкое торможение, вызванное внезапным стопорением тягового органа, является наиболее опасным режимом работы конвейера, поскольку его подвижные элементы, кроме статических сил, которые развиваются двигателем за счет электромагнитного момента, находятся под влиянием динамических сил, вызванных замедлением движущихся масс.
При условии, что стопорение тягового органа происходит мгновенно (сечение, которое заклинило, остается неподвижным), и в случае пренебрежения массой заклиненного участка тягового органа и упругостью трансмиссии, т.е. считая, что масса частей привода, которые движутся, является сосредоточенной в одной точке, модель конвейера, будет иметь вид [6].
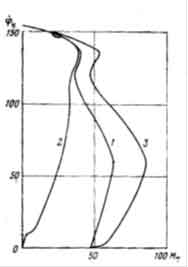
Рисунок 2 – Совокупность механических характеристик гидромуфты: 1 – рабочая, 2 – пусковая, 3 – при работе на стопорение
Характер движения конвейера и величины возникающих усилий после стопорения определяются во времени упругой деформацией u заклиненного участка тягового органа длиной l как невесомого упругого тела с твердостью с = E0 / l :
md2u/dt2 + cu - Fдв(v) = 0 , (2)
где m – суммарная приведенная масса привода; Fдв – усилие в тяговом органе, развиваемый двигателем за счет электромагнитного момента; v – скорость массы поводу.
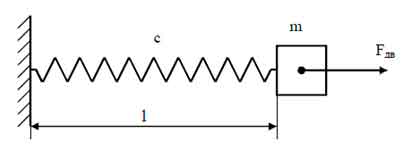
Рисунок 3 – Расчетная схема процесса стопорения конвейера
Определение максимального усилия в тяговом органе, развиваемый двигателем за счет электромагнитного момента при стопорении скребковой цепи выполняется по формуле:
Fmax = Fкр + √(F0 - Fкр) + cmvн2 , (3)
где Fкр – усилие, при критическом моменте двигателя F0 – усилие, развиваемое двигателем в начале торможения; vн – номинальная скорость тягового органа.
Из выражения (3) следует, что в момент стопорения скребковой цепи до остановки турбинного колеса гидромуфты вся ее вращающаяся масса, складываясь с массой ротора АД, вызывает значительное дополнительное растягивающее усилие, повышая общее растягивающее усилие в цепи.
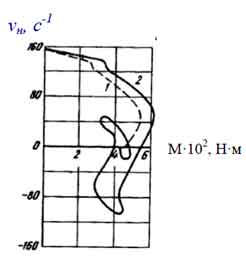
Рисунок 4 – Экспериментальная переходная характеристика гидромуфты ГПЭ-345 при стопорении конвейера [5]
Исследованиями установлено, что при стопорении тягового органа в приводе конвейера, оснащенного гидромуфтой, возникают колебания нагрузки и скорости вращения турбинного колеса муфты (рис. 4). Это обусловлено тем, что динамические нагрузки при стопорении приводят к значительным деформациям растяжения цепей. Упругая реакция цепей после остановки турбинного колеса раскручивает его в обратном направлении, и гидромуфта работает некоторое время в режиме противовключения, пока цепи не потратят определенную часть запасенной потенциальной энергии. После этого снова начинается движение турбинного колеса и последующее стопорение (рис. 5). В маломощных конвейерах колебания достаточно быстро затухают, однако, при увеличении мощности приводов до 55 кВт колебания могут носить стационарный характер при очень больших амплитудах до выплавки предохранительных пробок гидромуфт. Таким образом, защитное действие гидромуфты заключается в кинематическом отделении валов двигателя и редуктора путем слияния под давлением во внешнюю среду эмульсионной жидкости (что, как правило, разогрета до температуры, большей по 100 ºС) через выплавки плавкой пробки. Это действие происходит в случае остановки турбинного колеса при условии, что в начале стопорение не произошло порыва скребковой цепи конвейера.
Простои из-за отказа конвейера составляют 5-6% общего времени добычных смен. Статистические исследования, проведенные на 18 вахтах различных производственных объединений Донбасса показывают, что удельный вес простоев, связанных с отысканием и устранением порыва скребковых цепей составляет, в среднем, 59,3% от общего времени прос-тоев скребковых конвейеров. Наибольшее количество простоев конвейеров из–за порывов верхних ветвей их цепей составляют получасовые и часовые простои – соответственно, 25,8% и 23%. Наиболее часто встречающиеся простои скребкового конвейера из-за порывов нижних ветвей скребковой цепи составляют 2-2,5 часа, но много также простоев продолжительностью 6-8 час (рис. 1.1) [5].
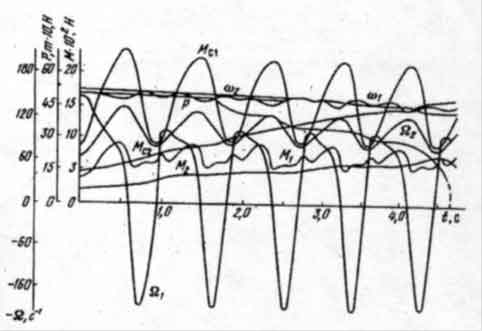
Рисунок 5 – Осциллограммы параметров привода двоприводного скребкового конвейера, оснащенного гидромуфтами, при стопорении:Мс1, Мс2 – приведены к турбинным колесам гидромуфты моменты сопротивления главного и хвостового приводов, Нм;М1, М2 – гидродинамические моменты, приложенные к турбинным колесам главного и хвостового приводов, Нм; Р – максимальные усилия в скребковых цепях, Н; ω1, ω2 – угловые скорости двигателей, с-1 [5]
Особенностью гидромуфты является низкий уровень технологич-ности, обусловленный тем, что срабатывание ее защиты предопределяет длительную остановку конвейера на время, необходимое для повторной заливки гидромуфты эмульсией и установки новой предохранительной плавной вставки (рис. 6). Интенсивность выплавления вставок зависит от загруженности конвейера, уровня жидкости в гидромуфте, качества гидромуфты и самой вставки, и в ряде случаев достигает 3–4 раз в смену.
Таким образом, использование гидромуфт в приводах конвейеров ставит в зависимость работу последних и очистных комплексов в целом от наличия плавких вставок на добычном участке. Отсутствие таковых вынуждает обслуживающий персонал устанавливать вместо плавких вставок стальные болты, т.е. идти на нарушение требований по эксплуатации конвейеров. В этом случае при перегрузе конвейера либо срабатывает вторая степень защиты гидромуфты, либо гидромуфта от избыточного давления разрывается, разрушая, как правило, и приводной двигатель. Это создает опасность травматизма людей [4].
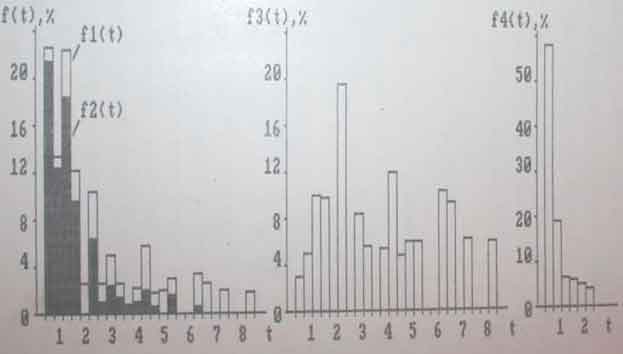
Рисунок 6 – Гистограммы распределения простоев добычных участков из-за отказов скребковых конвейеров: f1(t) – порывы скребковых цепей, в том числе: f2(t) – порывы в верхней ветви, f3(t) – порывы в нижней ветви; f4(t) – выплавление плавких вставок гидромуфт (t, час.)
Практическое применение гидромуфты в составе привода забойных конвейеров показывает что она плохо справляется со своими функциями. Также остается нерешенным вопрос низкого уровня технологичности, связанного со срабатыванием ее защит которые сопровождаются остановками конвейера для замены предохранительной плавкой вставки, а также низкая надежность гидромуфты. Простои связанные с заменой плавких вставок, а также устранением прочих неисправностей гидромуфт существенно замедляют работу всего очистного участка.
Особенности конструкции гидромуфты позволяют судить о том, что она является не только морально устаревшим пусковым и защитным средством из–за громоздкости работ при монтаже и ремонте, низкой надежности и как следствие малым сроком службы, но и является не эффективным средством пуска и защиты скребкового конвейера [4].
3. Цели и задачи исследования
Целью исследования является повышение производительности работы шахтного скребкового конвейера путем предотвращения порыва скребкового цепи при стопорении на основе обоснования параметров, структуры и технической реализации средств быстродействующей защиты от динамических перегрузок.
Для достижения этой цели должны быть решены следующие задачи:
- Выполнен аналитический обзор исследований и технических решений по проблематике обеспечения безаварийной эксплуатации шахтных скребковых конвейеров.
- Разработать математическую модель исследования процессов в приводе скребкового конвейера при стопорении с целью определения информационного параметра для применения в средстве защиты.
- Обосновать алгоритм и разработать структурную и принципиальную схемы средства автоматической защиты скребкового цепи от порывов при стопорении.
- Обосновать требования по безопасной и безаварийной эксплуатации разработанного средства автоматизации.
4. Теоретический анализ свойств устройств ускоренного торможения АД
Специфические условия эксплуатации конвейера вызывают частые стопорения его тягового органа, что приводит к порывам цепи и обусловливает необходимость создания соответствующей защиты. При этом, защитное устройство не должно существенно усложнять конструкцию электропривода [2].
В связи с изложенным, практический интерес представляет выяснение свойств известных способов выявления стопорения привода конвейера:
- по интенсивности изменения угловой скорости двигателя;
- по интенсивности изменения тока потребляемая двигателем.
Начальным состоянием любого процесса торможения является движущий режим работы двигателя. Признаком тормозного процесса является формирование двигателем электромагнитного момента, направление которого является обратным относительно направления угловой скорости вала двигателя. Одним из вариантов обеспечения защиты скребкового конвейера от стопорения может быть выключение и последующее торможение электропривода.
Принцип индукционно–динамического торможения асинхронного двигателя.
Эффективность процесса динамического торможения асинхронного двигателя значительной мере определяется величиной постоянного (выпрямленного) тока в фазах его статора. С другой стороны, величина этого тока определяется напряжением подведенная к статору величиной ЭДС вращения, индуцируемая в обмотках статора вращающимся полем токов ротора. В случае, если ЭДС вращения по своей полярностью будет совпадать с полярностью подведенной напряжения, ее действие будет направлена на уменьшение величины тока торможения. Это будет определяться разностью потенциалов мгновенных значений подведенного напряжения и ЭДС вращения и приводить к уменьшению интенсивности торможения двигателя. Таким образом, эффективное динамическое торможение асинхронного двигателя может происходить при отсутствии в его статорных обмотках обратной ЭДС вращения.
Эффективность способа индукционно-динамического торможения асинхронного двигателя заключается в устранении указанной ЭДС вращения (в начале тормозного процесса), которое сопровождается созданием значительных по амплитуде импульсов тормозного тока. В горной промышленности режим индукционно–динамического торможения используется для медленной остановки электроприводов бремсберговых ленточных конвейеров, экстренной остановки электроприводов других горных машин. Процесс индукционно–динамического торможения создается в силовой тиристорной схеме в цепи статора асинхронного двигателя в соответствии с рис. 7 и предполагает чередование состояний динамического (ДТ), индукционного (ИТ) и, собственно, индукционно-динамического (ИДТ) торможение двигателя.
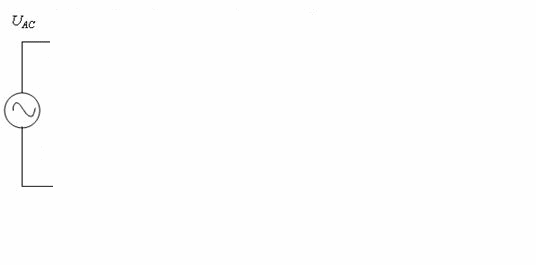
Рисунок 7 – Расчетная схема проведения анализа исследования процесса индукционно–динамического торможения асинхронного двигателя (анимация: 11 кадров, 5 циклов повторения, 24 килобайта)
Ток динамического торможения создается с помощью подачи на статор через тиристор VS1 и VS2 полуволн линейного напряжения UАВ сети. Эффект индукционного торможения создается при замыкании через тиристор VS3 ЭДС вращения ротора АД:
eоб = (1/√3)pωb(L0(2Is(k+1) + Isk) + Lr(2Ir(k+1) + Irk)) , (4)
где p – число пар полюсов асинхронного двигателя; Is; Ir – токи статора и ротора; L0 - индкутивность главного магнитного поля в расчете на фазу асинхронного двигателя.
Процесс индукционно–динамического торможения иллюстрируется диаграммами соответствующих параметров асинхронного двигателя и питающей сети (рис. 8). На интервалах динамического торможения полярности UAB и eоб совпадают. UAB > eоб. Начало ДГ определяется углом отпирание a тиристоров VS1 и VS2, а окончание – углом их проводимости β. Тормозной ток I определяется различием между мгновенными значениями UAB и eоб.
IТrн + LнdIТ/dt = UAB - eоб(АВ) , (5)
где rн; Lн – общие активное сопротивление и индуктивность цепи протекания тормозного тока. На интервале ИТ тиристор VS3 находится в проводящем состоянии, в то время как, тиристоры VS1 и VS2 – в не ведущему. Величина тормозного тока IТ определяется мгновенными значениями ЭДС вращения двигателя (eоб).
IТrн + LнdIТ/dt = |eоб(АВ)| , (6)
На каждом из интервалов ДТ и ИТ величина ЭДС вращения определяется соответствующими ее амплитудой (Евр mi) и начальной фазой (γ):
Eоб = I′Тr′Т((1 - s)/s) , (7)
eобi = Eобmi sin(ωbit + γ) , (8)
где ωbi = ω0(1 - s) – угловая частота ЭДС вращения, соответствующей i-му интервалу торможения, уменьшается, окончательно, до нуля. По мере уменьшения угловой скорости асинхронного двигателя уменьшаются амплитуда и частота его ЭДС вращения, и наступает состояние, когда полярности UAB и eоб будут отличными друг от друга. В этом случае тиристоры VS1; VS2; VS3 находиться в открытом состоянии, а тормозной ток двигателя IТ определяться суммой абсолютных величин мгновенных значений UAB и eоб (интервал ИДТ):
IТrн + LнdIТ/dt = UAB + |eоб(АВ)| , (9)
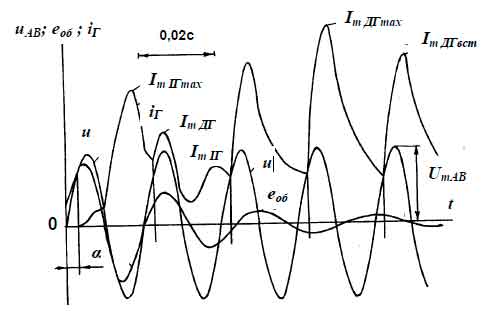
Рисунок 8 – Диаграммы формирования тока статора асинхронного двигателя в процессе его индукционно–динамического торможения
Выражения (1.52; 1.53; 1.56) решаются поэтапно в порядке появления интервалов с характерными, рассмотренными выше состояниями торможения. При этом учитываются соответствующие начальным условиям, величина и частота ЭДС вращения асинхронного двигателя. Их решением является следующее выражение:
Ir(t) = e-t/Tn(c + tk∫tn(U(t)/Lн)) e-t/Tn dt , (10)
где tn; tk – моменты начала и окончания соответствующего тормозного интервала, c = U(tн) / zн; Тн – постоянная времени обмоток ротора двигателя (Тн = Lн/rн).
При отсутствии тока через VS1 и VS2 ток в тиристоре VS3 определяется величиной ЭДС самоиндукции асинхронного двигателя:
Ir(t) = Ir(tni) e-t/Tn , (11)
где tni – момент начала указанного выше i-го состояния;
Тормозной ток существенно зависит от величины углов α отпирание тиристоров VS1; VS2. Его величина определяет уровень тормозного момента (МТ), что влияет на интенсивность торможения двигателя:
Mг = 2Ir2r21 / ω0Sнач , (12)
где ω0 и Sнач – соответственно, синхронная частота вращения ротора асинхронного двигателя и его скольжение в начале ИДТ.
Ir(t) = Irначe-t/Tn , (13)
где Irнач – начальная величина тормозного тока соответствующего интервала. По окончании тушения обратной ЭДС вращения асинхронного двигателя его тормозной ток будет определяться только ведущим состоянию тиристоров VS1; VS2 с учетом угла α их фазового регулирования [2].
Выводы
Таким образом, процесс индукционно-динамического торможения асинхронного двигателя позволяет получить высокий тормозной ток АД в установленном режиме за счет эффективного подавления ЭДС вращения, при этом в процессе подавления ЭДС вращения для получения начальных всплесков тока индукционного торможения. В зависимости от углов отпирания тиристоров, интенсивность торможения АД средней мощности находиться в пределах 0,3-6 с. Такой результат делает систему индукционно-динамического торможения АД допустимой относительно к электроприводу горных машин.
Перечень ссылок
- Чугреев Л. И. Динамика конвейеров с цепным тяговым органом / Л. И. Чугреев – М.: Недра, 1976. – 256 с.
- Маренич К. М. Автоматизований електропривод машин і установок шахт и рудників: навч. посібник для вузів [Під загальною редакцією К. М. Маренича] / К. М. Маренич, Ю. В. Товстик, В. В. Турупалов, С. В. Василець, І. Я. Лізан – Донецьк: ДонНТУ, Харків: УІПА, 2011. – 245 с.
- Маренич К. Н. Асинхронный электропривод горных машин с тиристорными коммутаторами / К. Н. Маренич – Донецк : ДонДТУ, 1997. – 64 с.
- Маренич К. Н. Асинхронный электропривод подземного скребкового конвейера с тиристорным пуско-защитным аппаратом [Дис. канд. техн. наук: 05.09.03] / К. Н. Маренич – Донецк., ДПИ, 1991. – 238с.
- Лаусенко А. В. Скребковые конвейеры. Справочник [Под ред. А. В. Леусенко] / А. В. Лаусенко – М.: Недра, 1992. – 221 с.
- Штокман И. Г. Расчёт и конструирование горных транспортных машин и комплексов: учебник [для студ. высших учебных заведений] под ред. И. Г. Штокмана. / И. Г. Штокман, П. М. Кондрахин, В. Н. Маценко и др. – М.: Недра, 1975. – 464 с.