Summary on the theme of master's work
Contents
- Introduction
- 1. Relevance of the theme
- 2. The purpose and objectives of the study, expected results
- 3. Overview of Research and Development
- 3.1 Overview of international sources
- 3.2 Overview of national sources
- 3.3 Overview of local sources
- 4. Analysis of the existing management
- Conclusion
- Source List
Reducing the cost of electricity, for a given level of reliability is the main objective of energy. Therefore, the increased use of hydraulic requirements reliability their operation, for its efficiency to the number of revolutions per second turbine blades, constant frequency of the output current. Hydraulic power units are multimode hydro machines, in which there are non-linear dynamic processes. The existing system of automatic control of hydraulic power plant are based on linear models of hydraulic components and are equipped with PID controllers with constant parameters. Therefore, the automatic control of hydraulic units do not provide maximum efficiency and reliability their work. Full-scale hydroelectric power tests Dnieper HPP showed the following:
Exceeding the allowable value overshoot rotor speed hydraulic unit and the degree of opening of the guide apparatus;
Presence of a frequency deviation output current within 0.5%;
High inertia rotating turbine blades;
Reducing the efficiency near the hydroelectric operating limits the load on the generator, due to an increase in hydraulic losses in the impeller turbine.
This increases the dynamic loads on the hydraulic unit and the probability of its failure to overhaul period, due to the rapid deterioration of equipment. On the other hand, the development of technology and computer technology has led to the gradual replacement of analog systems, microprocessor-based control systems.
1. Relevance of the topic
Existing microprocessor control system of hydraulic implement control methods designed for analog systems, and therefore does not provide maximum efficiency and reliability of the hydraulic unit.
Besides the various hydroelectric plants differ from each other so there is a need for methods of adjustment knobs to whole class objects.
2. The purpose and objectives of the study, expected results
The aim of the study is to research and develop a method for tuning of the hydraulic unit, which in turn will impact on reducing management costs and increase efficiency object.
main objectives of the study:
- study of hydraulic automatic control system and its features.
- Analyze the object of research to justify the need for research in this area.
- Analyze existing methods of adjustment.
- identify problems in the use of existing methods.
- development of alternative methods and evaluation of its effectiveness.
object of study span>: Hydroelectric
subject of study span>: The study of management of hydraulic hydroelectric power.
As part of the master plan to get topical scientific results in the following areas:
- Investigation of plant automation units.
- analysis and feasibility study dominance of the developed method over existing.
- business case for the introduction of a new method of tuning the controller.
For experimental evaluation of the theoretical results and the formation of the relevant conclusions of the feasibility study conducted by planning the following:
-
Getting
- mathematical description of hydraulic units. Getting
- model of the automatic control.
- comparative analysis of the results.
3. Overview of Research and Development
Because of hydraulic automatic control is an important part of the task automation industry, the problem of finding the optimal method were widely investigated as American, European, Japanese scientists and domestic experts. This issue is devoted to a variety of articles and other scholarly works that need your attention.
3.1 Overview of international sources
Fundamentals of hydraulic control various powerful hydroelectric power have been described in the work of David Rushmore [ 1 ]. Also in this study were affected by the relevance of research in this area, the basics of the entire theoretical framework. Also of note is the work of E. Irvinga and A. Labo [ 2 3 ].
The problem of automation of power plant engaged in commission with the investigation of the accident at the Sayano-Shushenskaya HPP. This paper is an analysis of the existing problems. A. Mursaeva, E. Ugryumova [ 4 ].
The book Sekretarev J., S. Didenko, Caravan A., N. Moshkin [ 5 ] stated description of contingency management hydroelectricity. Stages of modeling and comparative analysis of the most commonly used methods.
Automatic speed control of hydraulic turbine blades as well as active power flows at different times occupied many famous scientists. Approaches to this problem have been developed at different times and improved Molkov S. and Y. Evdokimov [ 8 , 9 ]; Sherbina U., Molkov S., [ 10 ]; Batalov A. (The use of power flows in the automatic regulation) [ 11 ]; Zarembo V. (ACS to improve the reliability of computer-based) [ 12 ].
The reliability of the hydraulic units was investigated in Zhdanovich A., secretarev A. [ 6 ].
In Rui-Jung was considered best management practice. The study was actively used simulation package Matlab. In particular, the model was built oil pressure unit. [ 7 ].
3.2 Overview of national sources
A team of researchers led by Potashkin S. (Chairman of the Management Board of JSC "Ukrhydroenergo") are set out in detail the theoretical foundations of control of hydraulic, offers its automatic control system for DniproHES. This article is good because that it contains the fundamental and structural diagram of ACS. [ 13 ]
Kiev researchers (KPI) are also involved in the management of hydraulic units. Zaharchenko V. engaged in the evaluation of reliability of information support hydraulic control system on the basis of function-oriented fuzzy mathematical models [ 14 ]. Also conducted research in the management of hydropower stations based on fuzzy sets. [ 15 16 ]
3.3 Overview of local sources
In the Donetsk National Technical University undergraduates Voblikov S. conducted studies of reliability and performance of hydraulic malfunctions. [ 17 ]
The reports of student conference also raised the issue of management of hydraulic units. Performances of young professionals is clearly highlighted the problems in the field of automation. There have been some offer technical solutions [ 18 ].
control of hydraulic analysis methods.
Existing methods of control vanes of the impeller rotation bucket turbines are based on management for opening guide vanes with the correction of the pressure plant. Such management has a number of disadvantages.
Management is characterized by the pressure from the pressure of hydropower turbines that organically introduces an error which may be significant.
The signal for the pressure is determined by measuring the levels of the lower and the upper bay and transmitted over a long distance to units which introduces additional uncertainty and reduces the reliability of the control system.
It does not include losses in the intake grilles and conduits.
In this method, the basis for management control position for opening the guide vanes and active power hydraulic which eliminates the above drawbacks. At the same time, with the same values of pressure and speed the opening of each guiding unit corresponds to one of the universal characterization the optimal value of the angle of the blades working wheel and therefore one power value. Therefore for each head there is a plot of the optimal power from the opening of the guide vanes. The curve is shown in Figure 1:
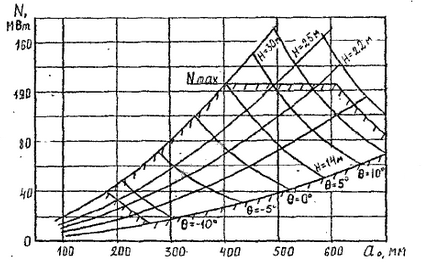
Figure 1 power versus the flap opening
Optimization of hydraulic unit when the load changes.
One of the advantages of the use of hydraulic units is undoubtedly high maneuverability, which in turn not only on the technical parameters of the used unit, but also of its automatic control and regulation In turn, in some cases need to configure the controller so that the speed at which the system was small Raise it is possible, if the control signal is pre-formed for a specific law. The need for optimal control is that the frequency generated by the current generators directly dependent on the rotation of the turbine. Thus neutralize the deviation of the turbine speed considerably we reduce the frequency produced by the current. Figure 2 shows the dependence of the output current from the turbine speed:
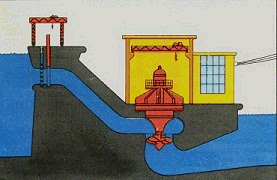
Figure 2 The Prince of hydraulic action (Animation: number of frames 5 Weight animation 150 kB, delay between shots 1c, the total number of reps 10, created by the software MP GIF Animator)
The method of proactive management
The construction of accurate predictive models for complex technological systems is quite voluminous and difficult problem to be solved. In reality, in many cases, these models are not sufficiently accurate assessment of performance required under with technological regulations. Therefore, the use of known control methods based on the construction of accurate predictive models Toy, for the efficient management of complex technological processes has certain limitations In this regard, the actual problem is to develop management approach, which is based on proactive assessments process efficiency received Nena predictive models defined on the basis of previous studies, but on the basis of direct measurements.
Evaluation of the effectiveness and efficiency of both existing and developing control algorithms, as well as optimization of system configuration management best conducted using mathematical modeling that will improve the informational content about the object and, thus increase the quality performance of products and the management of energy facilities. In this context, the task of developing algorithmic and hardware research, implementation and configuration of hydraulic unit is relevant. The aim is to develop algorithmic and hardware research, implementation and configuration of multi-function digital automatic control system Francis turbine, allowing to carry out preliminary configuration ACS at the factory, to reduce the time of commissioning and acceptance testing of the power plant.
The adaptive control
The adaptive control of the active power flow and power turbine speed can be attributed to the adaptive control methods. Management is performed by changing the value of opening guide vanes (HA) and the angle of turbine blades. Control effect on by enters the servomotors, which in turn is formed by active power control algorithm which is made with the use of mathematical Madeli unit. In the model include regression equations that describe the nonlinear dependence of the power turbine and the pressure drop in a flow alignment of the turbine on the value of the opening angle of the NA and the blades of the impeller. The model parameters are computed recursively using the method of least squares algorithm. This method is aimed at ensuring a minimum mean square error of the active management of hydroelectric power at a minimum flow of water and minimal power consumed to control. Control actions on the actuators of the opening of the guide unit and turn the impeller blade shape on algorithms that make use of a hydraulic model containing combinatorial dependence and major hydroelectric energy equation with the Kaplan turbine. Control action u_1 (t) servo mechanism to turn the blades of the impeller form in electronic or digital converter (combiners) for the same for all hydraulic units of the same type installed with many units plant, depending on the desired angle of the blades f_mpot H_cm static pressure and the magnitude of the opening of the guide vanes s (t) turbine ( combinatorial dependence):

Combinatorial dependence (1) is determined from the results of experimental studies of the layout of the Kaplan turbine. Flow rate Q is calculated by the equation:

where op-pressure drop in a flow alignment of the turbine; b_0 exponent whose value for the concrete spiral chambers of rectangular cross-section selected from the range (0,48-0,52); b_1 calibration factor, the value of which is determined by the similarity (index method) on factory performance. In equation (1) depending on the corrected combinatorial include combinations of the variables, ensure the maximum efficiency of the turbine, which is determined by calculation (the index method) in the main hydraulic unit of the energy equation with the Kaplan turbine:

where M_dv the moment of the driving forces generated by the flow of water on the blades of the impeller; n Hydraulic efficiency with which the estimated value of mechanical and electromagnetic losses in the turbine and generator;

a_1 the angle between the circumferential velocity and vector of absolute velocity of water flow at the leading edge of the blade of the impeller design section for a given value of opening the guide vanes s; b_p calculated angle of the blades of the impeller; Fa the angle of rotation of the blades of the impeller (the deflection angle of the blades of the impeller from the design angle setting); p density of water; D maximum diameter of the impeller; d diameter of the impeller hub.
Evaluation of the effectiveness and efficiency of both existing and developing control algorithms, as well as optimization of system configuration management best conducted using mathematical modeling that will improve the informational content about the object and, thus increase the quality performance of products and the management of energy facilities. In this context, the task of developing algorithmic and hardware research, implementation and configuration of hydraulic unit is relevant. The aim is to develop algorithmic and hardware research, implementation and configuration of multi-function digital automatic control system Francis turbine, allowing to carry out preliminary configuration ACS at the factory, to reduce the time of commissioning and acceptance testing of the power plant.
In writing this essay master's work is not yet complete. Final completion: December 2013. Full text of the and materials on the topic can be obtained from the author or his manager after that date.
References
- Rashmor D. HYDRO ELECTRIC POWER STATIONS / Rashmor D. / / NEW YORK, JOHN WILEY & SONS. - 1923. - 611 c.
- A. Gill, Introduction to the theory of finite state machines / A. Gill. - Moscow: Nauka, 1966. - 272.
- A. Laboratory Classical / advanced controls for hydraulicpower plants, 2004. - 414 c.
- Act of technical investigation of the accident that occurred on 17.08.2009 at OJSC "RusHydro" - "Sayano-Shushenskaya power plant named after PS Neporozhny ": Report of the Federal Service for Ecological, Technological and Nuclear Supervision (Rostekhnadzor) / / http://www.gosnadzor.ru/
- J. Hopcroft Introduction to Automata Theory, Languages, and Computation / J. Hopcroft, R. Motwani, J. Ullman. - Moscow: Publishing house "Williams", 2002. - 528 p.
- Zhdanovich A., secretary of the Y. Investigation of the parameters of operational reliability of hydroelectric using the theory of fuzzy sets / / Scientific Bulletin of the NSTU. 2010. No1. S. 145-159
- Rui Jun. Optimal regulation control system for cascade hydropower stations / Rui Jun. - 2009. - 358 sec.
- Brits S. Automatic control of active power flows in complex power systems / Malkov SA - K.: Publishing house "Williams", 1991. - 320.
- Ueykerli D. Design of Digital Devices / D. Ueykerli. - Moscow: postmarket, 2002. - Volume 2. - 528 p.
- Sherbina Y., S. Malkov Digital simulation model of the energy pool in the state space as an object of automatic frequency and active power flows. , Kiev, 1989. - 20c. - Dep. in UkrNShNTI 25.05.89 Ή 1379-UK89
- A. Batalov, Molkov A., Malkov SA Using the automatic adjustment of frequency and active power transfer units HPS as a generator / / Power plants. -1989. - | Ή 2 - P.63-66.
- Zarembo V., Molkov S. Improving the reliability of automatic frequency control and active power on the basis of computer / / Energy and Electrification. - 1990. -. Ή I. - P.40-42.
- Potashnik SI, Rassovsky VL, AP Zhuk, Martinchik VF Bondarenko, JN, start the first unit of the Dnieper HPP ., 2009. - 42.
- Nelson V. Digital logic circuit analysis and design / V. Nelson, H. Nagle, J. Irwin, B. Carroll. - Prentice Hall, 1995. - 842 pp.
- Shtovba S. Design of fuzzy systems by means of MATLAB., 2007. - 370S.
- Kalmyikov S., Shokii YI, Yuldashev ZK Methods of interval analysis, 2006. - 223 p.
- Voblikov S. Increase the wear resistance of machine parts by surface plastic deformation with the functionality of surfaces and surface areas [electronic resource]. - Mode of access: http://masters.donntu.ru ...
- Materials XII International Scientific and Technical Conference Speaker GWP [electronic resource]. - Mode of access: http://http://donntu.ru ...
- Serduk V. Develop an automated system of operational management of the power load in Kurakhovskaya TPP [electronic resource]. - Mode of access: http://http://masters.donntu.ru ...