Abstract
Contents
- Introduction
- 1. The topical issue of thermal insulation
- 2. Properties of insulating materials and designs
- 3. Thermal insulation materials
- 3.1 Mineral wool, and articles thereof
- 3.2 Glass fiber and articles thereof
- 3.3 Diatomite, tripoli and their products
- 3.4 Lime-siliceous products
- 3.5 Vulcanite products
- 3.6 Expanded perlite and glassware
- 3.7 Expanded vermiculite and glassware
- 4. Methods for measuring the thermal conductivity of materials
- 4.1 Fixed-line method is a flat layer
- 4.2 Method of longitudinal heat flow
- References
Introduction
Thermal insulation in modern industry plays an important role. With its help resolve issues of life support, the organization process, energy saving. Thermal insulation design are an integral part of the protective elements of industrial equipment, pipes, parts of industrial buildings. Due to its isolation is greatly improved reliability, durability and efficiency of buildings, structures and equipment. P>
Insulation performs the following functions:
- reduces heat loss to the environment from facilities (buildings, structures, equipment, piping, etc.);
- provides standard practice in the apparatus;
- maintain the desired temperature of components in industrial processes;
- creates a normal temperature conditions for staff;
- reduces thermal stress in metal structures, the refractory lining, etc.;
If the insulation is to prevent heat loss from the insulated surface to the environment, it is called heat.
Due to the extensive development of industrial processes that take place at high temperatures and pressures of the role and importance of thermal insulation is continuously increasing.
insulation works are completed in the course of construction of facilities, and so on fast and quality of their performance depends not only on terms of delivery of those facilities, but also the quality of its products, economic and technical characteristics of the objects, the comfort of the workplace.
How abroad and in our country, the development of production of thermal insulation works follows the path of industrialization with the use of modern insulating materials and structures, highly mechanized tools and devices, as well as prefabricated scaffolding tools (forests, scaffolding). In practice, thermal insulation works are increasingly used design full operational readiness, supplied by enterprises in the form of finished complex elements consisting of thermally insulating and coating layers, equipped with a set of fasteners. Production of thermal insulation work is reduced to the installation of prefabricated elements to be insulated.
1. The topical issue of thermal insulation
Thermal insulation of piping and equipment determines the technical feasibility and cost-effectiveness of the implementation of most manufacturing processes. It is widely used in the energy, utilities, chemicals, oil refining, metallurgy, food and other industries.
Energy conservation is an urgent problem, especially in countries with temperate and cold climates, since a significant part of the energy consumed in the production, transfer and heat retention. Loss of heat is dependent mainly on the thermal conductivity of materials that are used for insulation and heat dissipation. The use of the respective materials can significantly reduce energy costs for production, transmission and heat retention, and reduce environmental pollution, which is always true in the production of thermal energy.
Materials used for thermal insulation properties are characterized primarily by conduction. The smaller (larger) the thermal conductivity of the material, the better it keeps (conducts) heat. Therefore, the thermal conductivity is a characteristic of their passport, and the need for its measurement is correct.
Main way to obtain information about the thermal properties of materials remains the same experiment.
2. Properties of insulating materials and designs
In order to successfully meet the challenge posed by the creation and construction of thermal insulation design, it is necessary that the selected insulation materials to meet certain requirements. Among the most important requirements - low and constant throughout the entire life of the thermal conductivity, the ability not to collapse under the influence of atmospheric conditions and temperature of the isolated object, do not cause corrosion and damage the isolated object, not to prevent thermal deformation of an isolated object. Lifetime insulation typically not be lower lifetime isolated object. P>
Judgment on these and other properties of insulating materials can be taken after considering the totality of properties defined by conventional methods. p>
Allocate properties such insulating materials: p>
- density;
- porosity;
- thermal conductivity and heat capacity;
- Thermal stability;
- humidity and water absorption;
- vapor permeability, water resistance, water resistance;
- chemical and biological stability;
- strength, compressibility, elasticity, flexibility and consolidation;
- linear thermal shrinkage, the average fiber diameter and content of organic substances;
- fire resistance;
- sound absorption and sound insulation;
- environmental and technological safety insulation materials and designs.
3. Thermal insulation materials
3.1 Mineral wool, and articles thereof
Among the rather wide range of insulation materials first in the volume of production in Ukraine and abroad, take the product based on mineral fibers. They are non-flammable, are not exposed to microorganisms and rodents, frost-resistant, for their production does not require scarce raw materials.
Insulating materials based on mineral fibers allow you to create different versions of lightweight structures.
Mineral wool used for production of heat and sound insulation products as well as an insulating material in the construction industry and at the insulated surface to +600°C.
For the production of mineral wool products are used relatively small number of basic materials. However, existing significant technological developments make it possible to receive insulation products fairly wide range. Properties of the products can be controlled by varying the processing technology, the material composition and the nature of porosity. This allows to produce different products with predetermined properties for different operating conditions.
3.2 Glass fiber and articles thereof
Glass fiber (fiberglass) - a kind of mineral fiber. It is a semi-finished product in the production of thermal insulation and acoustic products. The raw material is glass batch consisting of silica sand, limestone (dolomite) and soda (sodium sulfate), mixed in a certain proportion. The charge is melted in the melting tank furnace, and then processed into fiber.
Depending on the average diameter of the glass fibers are distinguished: an ultrathin (UTV) with a diameter of less than 1 micron, superfine (ETS) - 1-3 microns thin - 4-12 microns, thickened -12-25 mm and thicker - more than 25 microns.
Fiber length divided by the continuous (3 m or more) and the staple (length 30-50 mm).
Continuous glass fibers are produced by drawing through a die. For this batch is melted in a tank furnace. Molten glass flows into the feeder, which is mounted in the bottom of the platinum-rhodium plate (bushing) with holes 1-2 mm in diameter. Through these holes molten glass flows streams, which are wound onto a rotating drum with great frequency. Thus streams drawn into fibers and cools. In this way, produce glass with a diameter of 4 to 25 microns.
After pulling glass fibers are passed through a sizing device, where they are wetted bystrozastyvayuschimi emulsions made paraffin-based or aqueous adhesives (starch, dextrin, gelatin) with plasticizers. Lubricants used for dusting glass and giving it flexibility in downstream processing.
Manufactured from continuous glass fiber insulating mats, strips.
3.3 Diatomite, tripoli and their products
Diatomites and tripoli - porous sedimentary rock composed mainly of amorphous silica, SiO2 (diatomite in 90-95% SiO2, tripoli contain more impurities). The chemical composition of diatomite and tripoli is almost the same, but different microstructure. This is explained by the difference in the geological age of the sediments. Diatomites refer to later, and tripoli - to the earlier deposits. Diatomites consist of fragments of diatom shells of crustaceans, almost completely preserved its structure. Tripoli - denser rock in which the starting material is completely lost its original shape. Diatomites more porous than tripoli. Depending on the amount of organic impurities and the presence of iron oxide and rottenstone diatomite color changes from white to pale yellow.
High porosity and low average density (porosity diatomite in a piece of 85% porosity tripoli below) has identified the use of tripoli and diatomite for thermal insulation. Plasticity and tripoli diatomite depends on the content of clay impurities. Diatomite (tripoli) is mined in open pit mines.
Density diatomite depending on the field ranges from 380 to 1000 kg/m3.
Diatomite com bubble, intended for the manufacture of insulating materials (TU 5761-001-25310144-93) must have an average density of not more than 800 kg/m3 and the humidity is 50%, the thermal conductivity at high temperature of 323 K - 0.181 W / (m • K) at 573 K - 0.195 W / (m • K), temperature resistance of 900 °C.
Diatomaceous baked chips (TU 36-888-83) - a material of different grain composition produced by burning, crushing and screening raw material. The chips produced an average density of 350 kg/m3 and is used as a lightweight heat-resistant additives in the manufacture of heat-resistant lightweight concrete as backfill for the thermal insulation of hot surfaces of industrial furnaces and process equipment at isolated surfaces up to 900 °C . Thermal chips with an average bed temperature of 298 to not more than 0.1 W / (m • K), at a temperature of 573 K-0, 16 W / (m • K). Most of diatomite (tripoli) manufactures and diatomite diatomite insulation products, in addition, they are used as part of the fabrication of rigid insulation products (lime-siliceous, vulcanite, perlitodiatomitovyh) or powders for thermal insulation mastic insulation and fire-resistant and heat-resistant plaster concrete.
Diatomite and diatomite products (GOST 2694-78) differ in the way of education in their porosity. In the porosity diatomite products prepared by the process of burning out of additives (sawdust) in diatomite - a way of pricing. Method pricing products obtained with smaller average density and heat conductivity.
Penodiatomitovyy and diatomite products are used for thermal insulation of industrial equipment and pipelines, as well as the furnace at a temperature of insulated surface to 900 °C.
3.4 Lime-siliceous products
Lime-siliceous products (GOST 24748-81) is made from finely ground mixture of lime, silica material (tripoli, diatomite, silica sand) with a silica content of SiO2 is not less than 75% of asbestos and 5 - th or 6 th group of semirigid structure by thermal-treatment in an autoclave.
At an average density of siliceous lime-brand products are divided into 200 (highest quality) and 225 (first class quality). Products manufactured in the form of rectangular plates (PRP) and the keystone (PKP) sections, half-cylinders (C) and segments (S).
Plate size (mm): PRP-length 1000, width 500, PKP-length 1025, width 525 (at the lower base) Length 1000 mm Width 500 (top base). The thickness of both types of plates 75 and 100 mm. Physical and mechanical properties of the products are shown in Table. 3.1.
The average density in the dry state (mark), kg/m3, not more | 200 | 225 |
Thermal conductivity, W / (m • K), not more, at a temperature, K 298 ± 5 398 ± 5 573 ± 5 |
0,058 0,070 0,104 |
0,065 0,077 0,112 |
Flexural strength in the dry state, MPa, not less than | 0,35 | 0,35 |
Linear thermal shrinkage at 600 °C,%, no more than | 1,8 | 2,0 |
Humidity,%, not more | 65 | 70 |
Temperature resistance, °C | 600 | 600 |
Products used for thermal insulation of piping and equipment surfaces at a temperature of insulated surfaces up to 600 °C. Products have gained widespread use in ovenbuilding, insulation of boiler equipment. The advantages of the product should include the complete absence of organic matter.
3.5 Vulcanite products
Vulcanite products - kind of lime-silica products. Such products are made of diatomaceous earth, lime and asbestos-6 group by autoclaving.
Vulcanite products differ from lime-silica ratio of the components and the method of hydrothermal treatment. In the production of lime-heat treatment of siliceous product is carried out in an autoclave. In the production of vulcanite park the products takes place in an autoclave and drying - in tunnel kilns.
At an average density vulcanite products separated by marks 300, 350 and 400 (Table 3.2).
Index | Mark 300 | Mark 350 | Mark 400 |
Average density, kg/m3, not more | 300 | 350 | 400 |
Thermal conductivity, W / (m • K), not more, with an average temperature, K: 298 ± 5 398 ± 5 |
0,076 0,088 |
0,081 0,092 |
0,087 0,099 |
Flexural strength, MPa, not less than | 0,3 | 0,35 | 0,4 |
Linear temperature shrinkage products at 600 °C shall not exceed 2%. Humidity product by weight is 30%. Dimensions vulcanite products are the same as in sovelite. Industry produces only a slab products.
Vulcanite products used for thermal insulation of equipment and pipelines of industrial installations at the insulated surface to 600 °C.
Packaging, storage and transportation of products. Sovelite, lime-siliceous and vulcanite products are wrapped in waterproof paper or plastic wrap and placed on edge in wooden boxes, crates, boxes or bags. Store the product in closed warehouses.
3.6 Expanded perlite and glassware
Expanded perlite (GOST 10832-91) - a porous material in the form of sand or gravel, obtained by heat treatment of crushed volcanic glasses - perlite and obsidian. Perlite - an igneous rock, which is the product of a volcanic eruption. Perlite deposits are located in the North Caucasus, Buryatia, Kamchatka, Magadan region. Abroad, the most significant reserves of perlite are in Armenia, Georgia, Turkey and Greece.
Main feature of volcanic glass behind them porization - the content of the so-called dissolved water. With a sharp heated volcanic glass softens and swells by converting the contained water vapor.
Expanded perlite is prepared by calcination of natural crushed perlite in special furnaces. Low swelling perlite depends on the natural properties and is in the range of from 850 to 1250 °C. The best raw material for the expanded perlite - rock intumescent temperature to 1050 °C in one step. Expanded perlite, depending on the grain size is separated into sand (grain size less than 5 mm) and crushed stone (grain size of 5 to 20 mm).
3.7 Expanded vermiculite and glassware
Expanded vermiculite - free-flowing granular material flake structure that results from burning natural vermiculite.
Natural vermiculite - mineral from the group consisting of hydrated micas which contain not only a water-absorbing, but the crystallization water, which is in the mineral lattice. Therefore, when heated vermiculite swells due to explosion-allocation of water. Thus it is split into individual plates of mica partially interconnected. Swelling of the vermiculite increases its volume by 15-20 times. Rock density vermiculite 2,05-2,71 g/cm3; melting point 1300 °C.
Expanded vermiculite (GOST 12865-67) for bulk density is divided into grade 100,150 and 200.
Vermiculite brilliant color, gold. By grain size of vermiculite is divided into three fractions: close - with a grain size of 5 to 10 mm, with an average - a grain size of from 0.6 to 5 mm; fine - grain size up to 0.6 mm. Thermal conductivity of expanded vermiculite varies depending on the brand of 0.064 to 0.075 W/(m • K) (at 298 K), moisture content not exceeding 3% by weight.
Due to ease and high temperature resistance (up to 1100 °C) exfoliated vermiculite used as loose-fill insulation for the manufacture of insulation products, and as filler in acoustic lightweight concrete and plaster. Furthermore, it is used to isolate the equipment surface temperature from -260 to +900 °C.
4. Methods for measuring the thermal conductivity of materials
Study heat materials at a wide temperature range. To investigate the use of two methods: stationary and non-stationary. Stationary methods based on the study of the time constant of temperature fields usually simpler and thus improved.
Unsteady methods are based on a study of time-varying according to a certain law of temperature fields. They are more complicated to implement. The main difficulty lies in the fact that the experiment is difficult to realize the conditions inherent in the theory of the method. However, the time-dependent methods allow in addition to data on the thermal conductivity to obtain information about the thermal diffusivity and specific heat of a substance.
4.1 Fixed-line method is a flat layer
To determine the coefficient of thermal conductivity of solid materials using the method of dynamic calorimeter with a heat and adiabatic shell. Setup is shown in Fig. 4.1. The test sample is placed between the reference 4 copper rod 5 and the copper contact plate 3. Some of the incoming heat flux through the heat meter Qt(τ) for heating of the sample (Qo(τ)).
Temperature field in the sample plate 4 and 2 can be considered linear. The thermal conductivity of the sample is determined by the formula:

where h, S, R - height cross-sectional area and the thermal resistance of the sample.
value of R is calculated as follows:
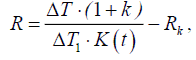
where ΔT, ΔT 1 - temperature gradient on the sample plate and 2; K (T) - the thermal conductivity of the heat meter; Rk - correction due to the thermal contact resistance between the rod and the plate 5 3, as well as contact with the surfaces of thermocouples; k - correction due to the influence of the heat capacity of the sample.
correction Rk and thermal conductivity of the heat meter K (T) is determined using the gradation reference samples of quartz glass and copper.
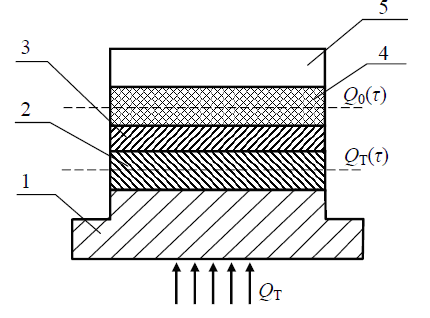
To improve the accuracy of their determination shall be held not less than five duplicate experiments. The thermal conductivity of the heat meter is determined by the formula:
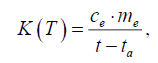
Where to ce, me - specific heat and mass of the reference sample.
Value of k is determined by the formula:
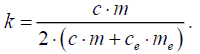
4.2 Method of longitudinal heat flow
Longitudinal heat flow method commonly used in the study of metals and other materials with relatively high thermal conductivity. At one end of a long sample with a cross-section S creates a uniform heat flux Q. Between two sections of the sample, located at a distance l from each other, measure the temperature difference Δt 1 = t1 - t2. In the absence of lateral conductivity of the sample heat loss is calculated as:
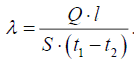
The main difficulty of the method is to create a one-dimensional axial heat flow, its measurement and recording of heat loss from the side surface of the sample. Protection of the cylindrical sample from the lateral heat losses can be carried out with the help of security cylinder (Figure 4.2) along which creates a thermal field, repeating field sample. The successful application of the method of longitudinal heat flow found in the study of the thermal conductivity of composite materials in the field of cryogenic temperatures (below 80 K). In this case, the heat loss from the side surface of the sample (Fig. 4.3) in a vacuum and are determined only by radiation at temperatures below 80 K is a small fraction of the main heat flow.
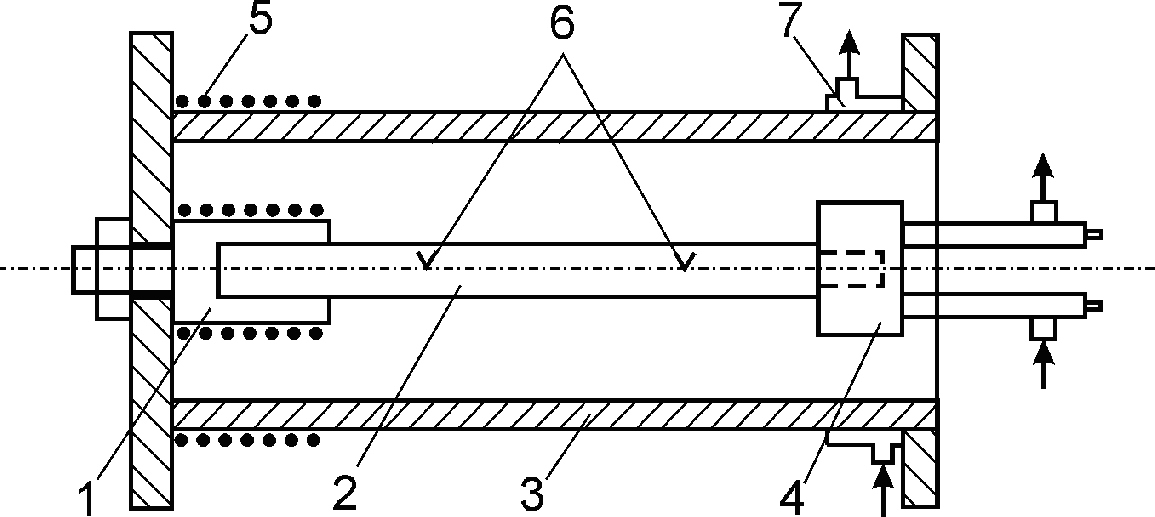
4, 7 - refrigerators, 5 - heater protective cylinder, 6 - thermocouple

1 - isolation, 2 - heater, 3 - sample 4 - differential thermocouple, 5 - copper block
In determining the thermal conductivity of metals and other conductive materials may be used in the method of Jaeger and Disselhorsta based on the solution of one-dimensional heat equation with internal heat sources for the rod heated by an electric current.
In the absence of heat transfer from the side surface of the rod (Fig. 4.4), the calculated formula is:
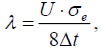
where σ e - electrical conductivity of the sample: U - voltage drop across the sample: Δt - temperature difference between the middle and end of the rod provided symmetrical along the length of the temperature distribution. If the experiment to measure the strength of the current design formula then I will take the form of:
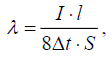
where l, S - length and cross-sectional area of the rod, respectively
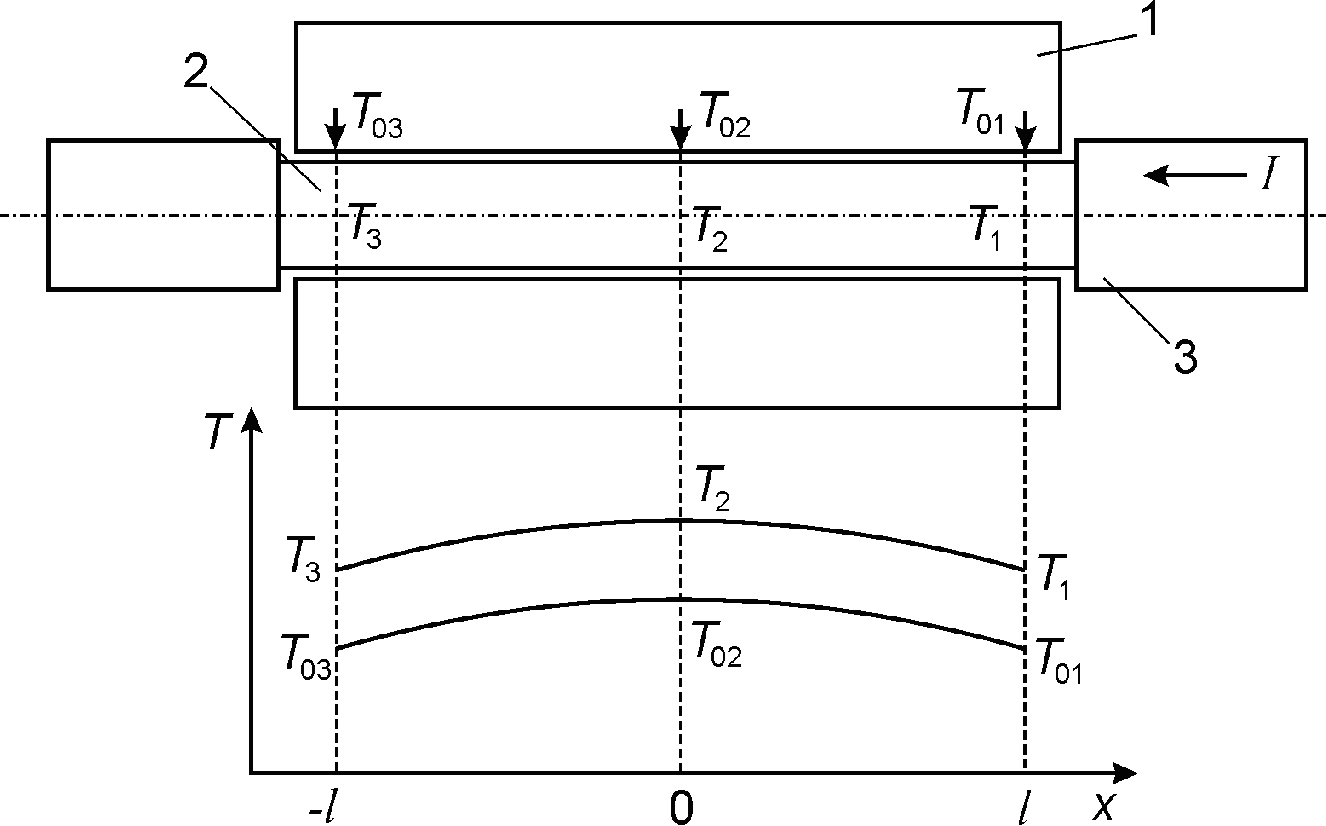
T10, T20, T0, T1, T2, T3 - places termination of thermocouples and measured their temperature
If heat from the side surface in the formula (4.7) to use the refined value Δt given heat loss.
References
- Бобров Ю.Л., Гранев В.В. Теплоизоляционные минераловатные материалы повышенной прочности в современном строительстве: Учеб. пособие. —М.: МИСИ им. В.В. Куйбышева, 1980.
- Воронков С.Т., Исэров Д.З. Тепловая изоляция энергетических установок. —М., 1982.
- Горлов Ю.П., Меркин А.П., Устенко А.А. Технология теплоизоляционных материалов: Учебник. —М.: Стройиздат, 1990.
- Горчаков Г.И. Специальные строительные материалы для теплоэнергетического строительства. — М.: Издательство литературы по производству, 1972.
- Горяйнов К.Э. Технология теплоизоляционных материалов и изделий. —М.: Стройиздат, 1982.
- Горяйнов К.Э., Коровникова В.В. Технология производства полимерных и теплоизоляционных изделий: Учебник. —М.: Высшая школа, 1985.
- Китайцев В.А. Технология теплоизоляционных материалов. — М.: Издательство литературы по строительству, 1970.
- Майзель И.Л., Сандлер В.Г. Технология теплоизоляционных материалов. —М.: Высшая школа, 1988.
- Михеев М.А., Михеева И.М. Основы теплопередачи. —М.: Энергия, 1977.
- Правдин Б.Н. Индустриальные способы изоляции теплопроводов. —Л.: Энергия, 1979.
- Сухарев М.Ф. Производство теплоизоляционных материалов и изделий. —М.: Высшая школа, 1973.
- Текунов Ю.Н., Блох Э.И., Пушкарский А.С, Растяпин В.В., Богданова Н.Н. Теплоизоляция промышленного оборудорания и трубопроводов. —М.: Стройиздат, 1985.
- Факторович Л.М. Тепловая изоляция. —Л.: Недра, 1966
- Хижняков С.В. Практические расчеты тепловой изоляции. — М.: Энергия, 1976.
- Шойхет Б.М., Ставрицкая Л.В.,Липовских В.М., Кашинский В.И. Тепловая изоляция промышленных трубопроводов//Энергоснабжеие, №3,2000.