Реферат по теме выпускной работы
Важное замечание: При написании данного реферата работа еще не завершена. Планируемое завершение: декабрь 2014 г. – январь 2014 г. Полный текст работы и материалы по теме могут быть получены у автора или у научного руководителя после защиты дипломной работы магистра
Содержание
- 1. Актуальность темы
- 2. Цель и задачи работы
- 3. Краткое изложение результатов магистерской работы
- 4. Заключение
- Список источников
1. Актуальность темы
Угольная промышленность была и остается отраслью с наиболее вредными, тяжелыми и опасными условиями труда.
Современные способы добычи угля и проведения подготовительных выработок характеризуются образованием большого количества пыли и попаданием ее в атмосферу горных выработок, в которых работают люди.
Шахтная пыль – основная причина заболеваний горнорабочих пневмокониозами и бронхитами.
Борьба с пылью, как с профессиональной вредностью, предопределяющей возможность заболевания рабочих пневмокониозом и силикозом, представляет собой сложную инженерную, и организационно–техническую задачу. Решением этой задачи, т.е. снижением запыленности воздуха в шахте до уровня предельно–допустимых концентраций, возможно только при комплексном применении различных способов предотвращения, снижения пылеобразования, пылеподавления и обеспыливания рудничного воздуха.
Таким образом борьба со взрывами угольной пыли – одна из актуальнейших проблем обеспечения безопасных условий труда горнорабочих в шахтах, разрабатывающих пласты, опасные по взрывам пыли.
2. Цель и задачи работы
Целью работы является разработка эффективных мероприятий по снижению вредного влияния угольной пыли в условиях шахтыРоссия
ПО Селидовуголь
Задачи: провести анализ запыленности воздуха, пылевых нагрузок горняков при разных технологических процессах, фактических параметров и эффективности мероприятий, применяемых на шахте для борьбы с пылью; исследовать факторы, влияющие на пылевыделение и запыленность воздуха; разработать и обосновать комплекс эффективных мероприятий для снижения запыленности воздуха и предупреждения заболеваний горняков пневмокониозами.
3.Краткое изложение результатов магистерской работы
Общие сведения о шахте
ПО шахтаРоссия
ГП Селидовуголь
сдана в эксплуатацию в 1960 году с проектной мощностью 1800 тыс.т угля в год. В течение всего срока службы шахты производственная мощность ее неоднократно изменялась в сторону уменьшения. С 2002 года на шахте была установлена производственная мощность в объеме 700 тыс.т угля в год.
Поле шахты Россия
расположено в юго-восточной части Красноармейского района Донецкой области Украины.
У западной границы находится г. Селидово, в 3–4 км расположен г. Новогродовка, к востоку и югу – сельскохозяйственные земли.
В промышленном отношении шахта подчинена ГП Селидовуголь
и относится к Красноармейскому
горнопромышленному району Донбасса.
Категорийность:
- По газу: сверхкатегорийная.
- По гидрогеологическим условиям отработки – ІІ.
- По пыли: опасная.
- По выбросам: не опасная.
- По горным ударам: не опасная.
- По самовозгораемости: m3, l81, l3 – склонны к самовозгоранию; m42, m2, l8, l7, l6, l21, l1, k8 – не склонны.
Горно–геологические условия отработки сложные из–за слабой устойчивости вмещающих пород, наличия зон влияния тектонических нарушений, зон распространения ложной кровли, размывов пластов, зон распространения неустойчивой в условиях обводнения почвы. Промышленные запасы на 01.01.11 г. составляют – 64,7 млн.тонн угля. Шахтное поле вскрыто двумя стволами – главным и вспомогательным. Главный ствол оборудован двухскиповым подъёмом, обеспечивающим выдачу горной массы. Вспомогательный ствол оборудован двухклетевым и двухскиповым подъёмами. Клетевый подъём обеспечивает выполнение грузолюдских операций (при необходимости и выдачу породы), а скиповый – выдачу породы. Подъёмы обоих стволов обслуживают гор. 210 м.
В работе находятся 5 проходческих забоев: 1 южный конвейерный штрек северного уклона П ст. пл.11, монтажный ходок 1 южной лавы северного уклона П ст. пл.11 , 2 северный вентиляционный штрек северного уклона П ст. пл.11 и 2 северный конвейерный штрек северного уклона П ст. пл.11, южный уклон П ст. пл. 11.
На шахте прохождение подготовительных выработок осуществляется смешанными забоями по пластам с подрывкой почвы и кровли. Подготовительные выработки проводятся с помощью комбайнов КСП–32, КПД и при помощи БВР.
Крепление горных выработок, как правило, металлическое арочное. Исключение составляют выработки, которые крепятся смешанной крепью. В настоящее время в работе имеются два очистных забоя, оборудованных комбайном типа 1К–101 и комплексами типа 1КД–90 .
Способ управления кровлей по пластам - полное обрушение.
Способ проветривания шахты – всасывающий, схема – фланговая. Свежий воздух поступает в шахту по вспомогательному стволу (частично по главному) и выдается на поверхность вентиляторными установками № 2 и № 8.
Шурф № 1 используется для проветривания выработок северного крыла пл. l1 и оборудован вентиляторами ВОД–21 (2 шт.). Шурф № 7 – используется для проветривания выработок южного крыла пл. l21 и l1 -оборудован вентиляторами ВОД–21 (2 шт.). На вспомогательном стволе установлена вентиляторная установка, состоящая из двух вентиляторов ВОКД–3, которая в данное время используется для случаев реверсирования вентиляционной струи воздуха в шахте.
Для борьбы с пылью на участке следует применять следующие способы:
- увлажнение угля в массиве;
- применение оросительной системы, которой комплектуется комбайн;
- очистка исходящей вентиляционной струи водяными заслонами;
- орошение угля перед ручной выгрузкой его из ниши;
- орошение на погрузочном пункте;
- применение пылеулавливающей установки, поставляемой вместе с комбайном;
- орошение при погрузке горной массы на конвейер или вагоны
- применение средств индивидуальной защиты
Предварительное увлажнение угля в массиве
Предварительное увлажнение угля в массиве должно применяться при ведении очистных работ, а также при проведении выработок комбайнами избирательного действия по пластам средней мощности.
Предварительное увлажнение заключается в нагнетании воды в массив до его разрушения (наиболее распространено при разработке угольных месторождений). Осуществляется через скважины, пробуренные по пласту параллельно или перпендикулярно плоскости очистного забоя, в подготовительных забоях, как правило, в плоскости забоя. Основные параметры, от которых зависит эффективность этого способа – давление и темп нагнетания, расстояние между скважинами, глубина герметизации скважин, расход воды и время между нагнетанием воды и выемкой угля. Значения параметров зависят от свойств угольных пластов. Снижение запылённости воздуха при разработке увлажнённых массивов происходит вследствие увеличения общей влажности разрушаемого материала, его ослабления в результате физико-химических и гидродинамических процессов взаимодействия воды и массива и смачивания пыли, имеющейся в массиве до его разрушения [1].
Различают низконапорное (от водопроводной магистрали) и высоконапорное (от насоса) предварительное увлажнение. Использование кратковременного высоконапорного нагнетания воды в пласт основано на предположении, что вода, проникающая под давлением в угольный массив, увеличивает пластичность угля, снижает удельную энергию, накопленную углем при сжатии, вытесняет часть газа и приводит к перераспределению напряжений в призабойной зоне. Работы, проведенные в этом направлении, позволяют сделать вывод, что при кратковременном высоконапорном нагнетании вода не проникает в микропоры угля, а перемещается по крупным трещинам, способствует гидроразрыву пласта.) [1].
Низконапорное увлажнение, в отличие от высоконапорного, направлено не на разрушение обрабатываемого угля, а на нейтрализацию заключенного в нем газа и изменение прочностных свойств угля. Это достигается путем длительного нагнетания воды с добавками поверхностно-активных веществ, улучшающих смачиваемость угля и позволяющих максимально использовать капиллярные силы, которые возникают при проникновении раствора в тонкопористую структуру угля[2,4].
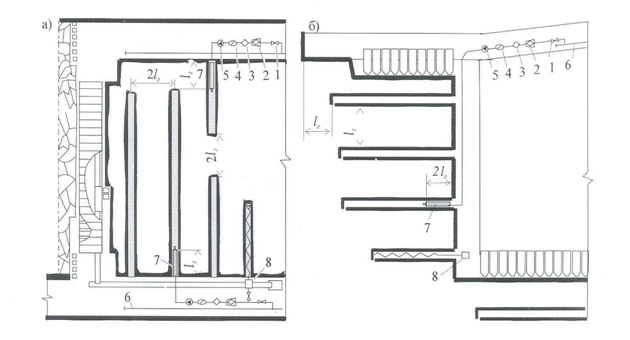
Рис. 1 – Технологические схемы нагнетания воды из подготовительных выработок в очистных забоях пологих пластов (а) и при щитовой выемке на крутых пластах (б)
1 – вентиль; 2 – фильтр штрековый; 3 – дозатор смачивателя; 4 – расходомер; 5 – насосная установка высоконапорная; 6 – штрековый трубопровод; 7 – герметизатор; 8 – буровой станок
Применение оросительной системы, которой комплектуется комбайн
В механизированных очистных забоях пологих и крутых пластов пылеподавление при выемки угля осуществляется с использованием средств орошения, которыми оснащаются выемочные машины (комбайны), механизированные крепи, струговые установки, фронтальные и щитовые агрегаты. На рис. 2 приведены технологические схемы пылеподавления орошением при выемке пологих пластов механизированным комплексом и струговой выемке.
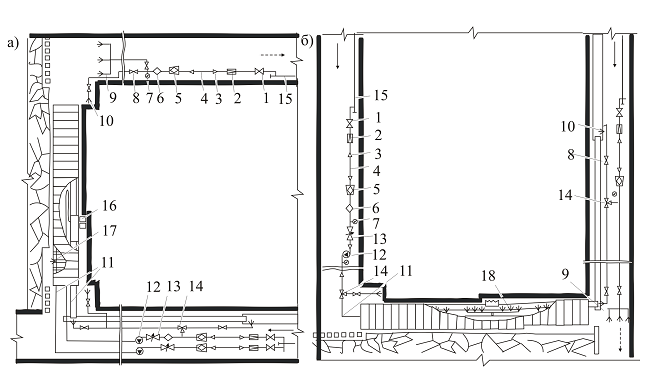
Рис. 2 – Технологические схемы пылеподавления орошением при выемке пологих пластов механизированным комплексом а) и при струговой выемке б)
1 – вентиль фланцевый; 2 – клапан редукционный; 3 – переходник; 4 – рукав напорный; 5 – фильтр штрековый; 6 – дозатор смачивателя; 7 – манометр; 8 – кран проходной муфтовый; 9 – водяная завеса; 10 – форсунка; 11 – водопровод забойный; 12 – насосная установка;13 – вентиль электромагнитный; 14 – кран трехходовой муфтовый; 15 – штрековый трубопровод; 16 и 17 – оросительные системы комбайна и крепи; 18 – автоматическое секционное орошение;
При работе выемочной машины на пластах с высокой категорией производственных процессов по пылевому фактору может применяться также отсос и улавливание пыли, если это предусмотрено технической документацией на машину. [3].
Применение пылеулавливающей установки, поставляемой вместе с комбайном
При проведении выработок комбайнами или применения погрузочных и буровых машин применяются средства пылеподавления, которыми комплектуются эти комбайны и машины. На пластах с высокой категорией пыльности проходческие комбайны по заявкам шахт могут дополнительно к орошению комплектоваться пылеуловителями или автономными пылеулавливающими установками (рис. 3).
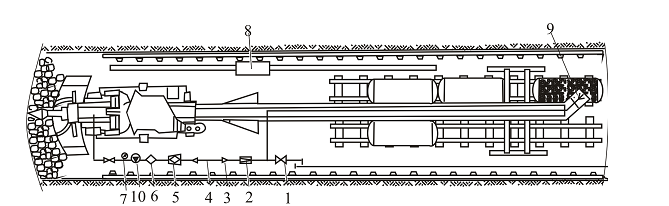
Рис. 3 – Технологическая схема обеспыливания в забое с комбайновой проходкой
1 – вентиль фланцевый; 2 – клапан редукционный; 3 – переходник; 4 - рукав напорный; 5 - фильтр штрековый; 6 – дозатор смачивателя; 7 – манометр; 8 – пылеулавливатель; 9 – водяная завеса; 10 – форсунка
При применении автономных пылеулавливающих установок проветривание тупиковой подготовительной выработки может быть нагнетательно–всасывающее и всасывающее. Всасывающее проветривание допускается применять в выработках не газовых шахт, нагнетательно–всасывающее проветривание с использованием автономных пылеулавливающих установок может быть применено в шахтах любой категории по метану, кроме выработок, опасных по внезапным выбросам угля и газа и суфлярам [3].
Водяные завесы
Остаточная запыленность воздуха по сети горных выработок, как правило, находится на относительно высоком уровне и воздушные потоки, исходящие из очистных и подготовительных выработок, а также проходящие по сети выработок, нуждаются в дополнительном обеспыливании. Для обеспыливания воздушных потоков применяем водовоздушные (туманообразующие) завесы.
Для создания водяных завес типа ВЗ–1 используют плоскоструйные форсунки .
Более эффективными являются туманообразующие завесы, создаваемые туманообразователями типа ОП–1 или ТЗ–1В. Диаметр капель образующегося тумана не превышает 10–50 микрон, поэтому распыленная вода длительное время удерживается в воздухе. Для образования водяного тумана в туманообразователи подводятся вода и сжатый воздух. При подаче сжатого воздуха и перемещения золотника вода и сжатый воздух поступают в смесительную камеру, в которой образуется водовоздушная смесь. Распыление последней происходит через кольцевую щель, при помощи которой регулируется степень дисперсности водяного тумана[4].
Орошение
Сущность пылеподавления орошением заключается в том, что при взаимодействии капли жидкости с частицей пыли происходит ее смачивание, захват каплей и осаждение получившегося агрегата – частица пыли – вода.
В системах орошения в качестве оросителей используют насадки, дающие компактную струю и универсальные форсунки, факел различной формы: конусные (КФ) – в виде сплошного конуса, зонтичные (ЗФ) – в виде полого конуса, плоскоструйные (ПФ) – в виде плоского веера. Обозначение форсунок указывает форму факела, коэффициент расхода воды и угол раствора факела. Например, форсунка КФ 1,6–75 является конусной форсункой с коэффициентом расхода воды 1,6 и углом раствора факела 750.
Эффективность Орошения зависит от удельного расхода жидкости, дисперсности капель, условий захвата каплями пылинок (скорости относительного движения частиц и капель, электрозаряженности капель), смачиваемости пыли и равномерности орошения.
При всех системах орошения обязательным является использование для очистки воды штрековых фильтров ФШ–1М, ФШ–200, ФК или ФКВ.
Для создания водовоздушных завес и с целью повышения эффективности орошения или необходимости уменьшения влажности угля и расхода воды в два и более раз может применяться пневмогидроорошение – смесь сжатого воздуха с водой. Подвод водовоздушной смеси к форсункам производится путем подачи воды и сжатого воздуха в смеситель. При пневмогидроорошении достигается тонкое диспергирование воды, а, следовательно, и осаждение тонко диспергированной пыли. Для того чтобы туман не рассеивался в выработке, а направлялся к источнику пыли, применяются форсунки, в которых формируется двойной факел диспергированной воды: наружный – грубодисперсный и внутренний – тонкодисперсный, а также форсунки с переменной дисперсностью тонкодиспергированной воды, которые ограждаются форсунками с равномерным распределением грубодиспергированной воды.
Орошение при работе добычных комбайнов и врубовых машин – воду подают непосредственно в место разрушения угля и равномерно распределяют по всему фронту разрушения; в местах, где пыль переходит во взвешенное состояние, производят дополнительное Орошение. При работе машин с плоским баром воду подают в зарубную щель с помощью оросителей, установленных на баре; при работе с кольцевым баром вода подается на входящую ветвь режущей цепи из насадок. Отбойные, погрузочные и отвальные устройства орошают из плоскоструйных форсунок, подающих воду на всю поверхность устройства. В барабанных исполнительных органах вода подается непосредственно через барабан или производится внешнее орошение.
Для эффективного подавления пыли (не менее 80–90 %) при работе выемочных машин при оптимальных режимах работы оросителей необходимо расходовать не менее 30–40 л воды на 1 т угля, а при работе врубовой машины – 80–100 л на 1 т штыба. Уменьшение расхода воды резко снижает эффективность орошения при выемке и транспортировании[2,4].
Эффективное пылеподавление, включающее одновременно очистку запыленного воздуха и орошение горной массы водой, достигается при применении цилиндрических и конических водовоздушных эжекторов ЭЦ–100, ЭЦ–250, ЭК–80, ЭК–1–110–500 и др. Принцип работы водовоздушного эжектора (рис. 4) заключается в том, что за счет разряжения, создаваемого водяным факелом форсунки, отсасывается запыленный воздух, образующий с диспергированной водой шламовидную смесь, которая, в свою очередь, направляется на подавление пыли.
Водовоздушные эжекторы применяются, в частности, для пылеподавления при передвижке секций механизированной крепи. На принципе эжектирования основано также пылеподавление на погрузочных и перегрузочных пунктах угля путем орошения его под укрытием с помощью конусных форсунок[3].
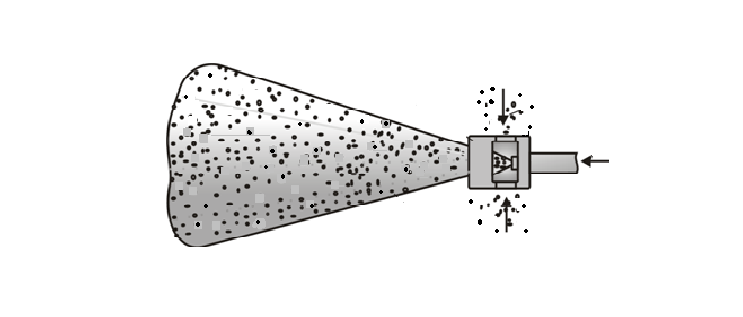
Рис. 4 –Принцип работы водовоздушного эжектора
(анимация: 5 кадров, 5 циклов повторения, 140 килобайт)
1 – форсунка; 2 – вода; 3 – запыленный воздух; 4 – шламовидная смесь
Применение средств индивидуальной защит
Индивидуальная защита органов дыхания шахтеров от угольной и породной пыли осуществляется с помощью противопылевых респираторов типа Ф–62Ш, которые обеспечивают очистку вдыхаемого воздуха от пыли до предельно допустимых концентраций.
Защита органов дыхания шахтеров будет надежной и эффективной только в том случае, если респиратор правильно выбран по размеру. Правильно выбранный и подогнанный респиратор должен плотно и равномерно прилегать к лицу[1].
4.Заключение
Снижение запыленности воздуха в шахте до уровня предельно допустимых концентраций, возможно только при комплексном применении различных способов предотвращения пылеобразования, снижения пылевыделения и обеспыливание рудничного воздуха. Основными средствами борьбы с пылью в очистных и подготовительных забоях в настоящее время являются предварительное увлажнение угля в массиве, эффективная вентиляция воздуха и орошение .
Список источников
- НПАОП 10.0–1.01–10, Правила безопасности в угольных шахтах, Киев – 2010 [Электронный ресурс]. – Режим доступа: http://ohranatruda.in.ua/pages/4955/
- Руководство по борьбе с пылью в угольных шахтах – 1979 год.
- Александров С.Н., Булгаков Ю.Ф., Яйло В.В., Охрана труда в угольной промышленности: Учебное пособие для студентов горных специальностей высших учебных заведений. – Донецк.: ДонНТУ. 2005., 520 с.
- «Инструкция по предупреждению и локализации взрывов угольной пыли способами, основанными на применении воды» – 2003 год.
- А.О. Бабокин, Сборник инструкций и других нормативных документов по технике безопасности в угольной промышленности. Москва,
- Ищук И.Г., Поздняков Г.А. Средства комплексного обеспыливания горных предприятий: Справочник. – М. : Недра, 1991. – 253 с.
- Артамонов В.Н., Николаев Е.Б. Способ увлажнения угольного пласта. Декларационный патент на полезную модель, (13)UА,(11)9320,(51) 7 Е21F5/05 від 15.09.2005 .