Содержание
Introduction
One of the most loaded subsystems combine mission is the executive body of the drive. Its loading is formed as a result of an "external" disturbance - a system of cutting forces of the rock on the core bit. Obviously, the state of the cutting tool and, particularly, breakage of the individual cutters, affect the load of the transmission. However, breaking the cutter does not lead to failure of the whole harvester and often can not be detected before stopping combine visual inspection executive. Prolonged operation with the tunnel boring machine out of service cutter can lead to a significant reduction of the resource elements of transmission of the executive body. Therefore, the development of technical means of diagnosing the technical condition of the cutting tool.
1. Theme urgency
At the beginning of 2012 in Ukraine there are 20 mining companies and 145 mines. Coal mining in Ukraine in 2011 in Europe, ranks third after Poland - 81.991 million tons.
Ukraine has about 4 % of global coal reserves. The main mineral extraction is carried out in Lugansk, Donetsk and Dnipropetrovsk regions. And at the Lugansk region accounts for 43 % of production. Donetsk region ranked second with 27 percent . On the Dnipropetrovsk region accounted for 23 %, and the Lviv and Volyn - 7% of total coal production.
Over the past 12 years coal production in Ukraine ranged from 73.8 million tons in 2009 to 86.8 million tons in 2011. Domestic consumption of coal has remained relatively stable at over 50% of total production. Domestic coal market consists of two key segments: thermal coal, which is mainly used for electricity production and coking coal, which is mainly used in metallurgy. Ukrainian coal market is characterized by shortage of coking coal and steam coal oversupply anthracite group, along with the lack of lean coal brand "T" in the power required. As for the supply of coal the defining feature of the Ukrainian coal market is the dominance in this market SKM Holding. The share of its subsidiary DTEK accounts for about 90% of thermal coal mined part of the company.
The share of another subsidiary of Metinvest, accounting for about 22% of coking coal produced by private companies. Steam coal plays a significant role in the Ukrainian energy sector. Coal used Ukrainian TPP is the only reliable fossil fuels, which do not need to import and which can fully provide the necessary amounts of electricity with the flexibility needed to industry and individual consumers in Ukraine.
Effect of Ukrainian coal to the European market slightly due to large high-quality coal reserves in Germany and Poland. Supply of quality coal from the United States is also a determining factor in this market.
The main factors affecting the domestic coal market:
- Negative factors - significant stockpiles of high concentration of the market, unregulated mining, falling global demand for steel, the boom in shale gas production, the planned commissioning of the LNG terminal, the installation of equipment on Ukrainian steel mills;
- Positive factors - a gradual transition for thermal coal as an energy source, the construction of a coal gasification plant, the Ukrainian government policies aimed at reducing dependence on Russian natural gas.
Ukraine's needs for energy resources is largely met by natural gas imported from Russia, despite the fact that Ukraine has rich reserves of fossil fuels of various kinds. "Energy Strategy of Ukraine 2030" is based on the declared intention of the government to reduce the country's dependence on imported fuels, including simultaneous increase in coal production. Ukrainian coal industry has recently undergone significant changes, including the privatization of the mines, closing unproductive mines and, in some cases, equipment upgrades and increased security.
Energy is an area of the economy, which is of great importance in the public planning. Instead, resource-intensive energy development, to which Ukraine relied on for decades, energy must go to the efficient use of energy resources to support economic development. To this end in the middle of 2012, the Ukrainian government has initiated Energy Strategy Update. Renewed Energy Strategy addresses the development of key sectors of energy, and aims to achieve significant energy savings in the industry until 2030. According to the Strategy, coal remains a major source of energy supply in Ukraine, and continues to be the main guarantor of security of the Ukrainian state from excessive dependence on energy imports.
Now becoming more widely used in mines in Ukraine and abroad receive roadheaders swept executive body, equipped with various configuration bits.
Executive part harvesting has the form of a drum or the screw on which are fixed cutters[1]. As an executive body also used drilling or CHIPPING - incisal crown. In tunneling machines Continuous executive bodies are in the form milling cutters discs[2]. Load on the executive body of the combine is formed under the influence of forces generated during cutting mineral separate cutters and harvesters with drum or screw executive body and also by transporting chipped fossil. Because of the fragility of the array cutting process is accompanied by cleavage of individual elements of different size, which leads to a change in the cutting force over a wide range[3]. Thus the heterogeneity of the structure and mechanical properties of rock is a major cause random changes in the character of effort in cutting.
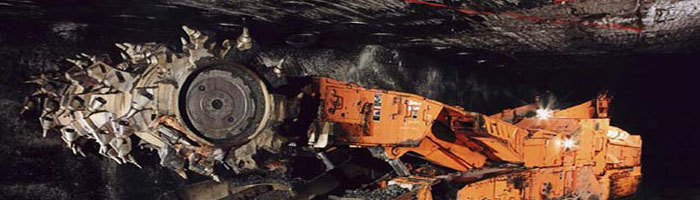
Figure 1 – Roadheader
One of the most important criteria for the effectiveness of rotary cutters, as well as other mining and cutting tools, is their durability under which refers to the ability to maintain its long-term instrument before limit state under certain conditions[4]. When this limit state is characterized not only further the ability to perform specified functions for the implementation of the process of destruction , but also a decrease in operational performance tool below specified limits. Estimate of how long the tool is its MTBF is the volume (V, m 1 pcs.) or weight ( g, r 1 pc.) muck, specific way of friction ( cutting ) a cutter. Its definition is usually made as a result of model acceptance tests of prototypes in real-life conditions. At the same time the application of computational methods to set as a result of research strength and durability characteristics that will determine the expected level of MTBF at the design stage of the tool. This approach seems to be more rational about creating new sizes of cutters with balanced performance, however, requires a certain amount of research and development of appropriate techniques.
Due to the fact that the nature of each type of mining and cutting tool has its own specific features you must first consider himself a physical process output rotary cutters out of action and analyze the causes of this phenomenon.
2. Overview and analysis of test results
As you know, during the operation incisors roadheaders perceive significant compressive and bending loads with the cyclical nature of the action as well as subject to intensive abrasion. Combined effect of these factors leads to the gradual exhaustion of the resource rock cutting tool and ultimately to its failure. This may be seen as a gradual failures limit is reached due to the amount of wear and sudden (emergency, instant ) failures breakage or carbide insert toolholder. Moreover, sudden failures can occur for two reasons - as a result of peak load exceeding the permissible level of strength tool or as a result of the accumulation of fatigue damage and wear which help to reduce the strength characteristics of the cutter elements.
On the subject were tested incisors on the executive board tunnel boring machine. Harvesters participating tests were combine harvester brand Sandvik and "КСП"- 42. Tests were conducted in order to know that the efficiency of the incisors and show the amount of replacement cutters after the mine workings. During inspection were also taken into account the characteristics of the breed. Combine Sandvik worked up to 100% of the breed. At the same processor "КСП"- 42 was operated at 2 characteristics. One had a content of 75 % rock and 25 % coal. The second characteristic combine work with 50% rock and 50% coal.
The results were promising. In one month, we have been able to see what Sandvik harvester with his trademark cutters good job with their work. For a month of tests on the combine was replaced by 317 pieces incisors holding production in 1295 m3, which means 0.1 un/m3. On the processor "КСП" - 42, at the same formulation was replaced by 279 and 420 units respectively, which represents a 0.06 and 0.14 un/m3 .
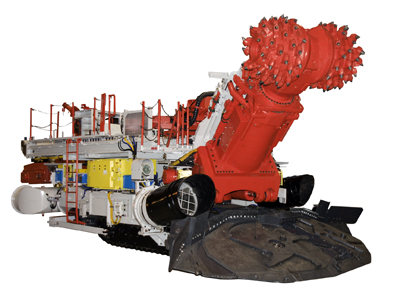
Figure 2 – Sandvik MR620
It is possible to distinguish the following three typical case of failure of cutters:
- Achieving limit the amount of wear of the cutting tool which corresponds to the point in time when as a result of wear head toolholder fully bared carbide insert and its loss will. Refusal tool occurs gradually thereby maximize the resource consumed by the design tool[5].
- Breakage of the weakest element of the tool as a result of the peak load exceeding the strength characteristics of the material. Such failures are usually the result of errors in the design or operation of the tool cutting edges in more severe conditions for which they were not intended.
- Faulty cutting part of the tool as a result of wear and the action of variable loads and accumulation of fatigue damage in the material[6]. In this scheme, the formation of the initial failure strength level of the weakest element cutter exceeds possible peak loads . However, the accumulation of fatigue damage and wear after a certain period of time ( or cutting path ) strength characteristics of the cutter will be commensurate with the applicable loads. Then broken tool failure can occur at any major cleavage breed.
Often during tunnel works further operation worn incisors when gutting carbide insert or absent. When this Cutting by means of the toolholder whereby the force acting on the tool is increased to two times . In turn, this leads to such negative phenomena as increasing energy intensity of the process of breaking rocks, strengthening the dynamics of the executive body, reduced productivity and resource tunneling machine. Therefore, the incisors have reached such a state obviously should be considered already out of service and require immediate replacement .
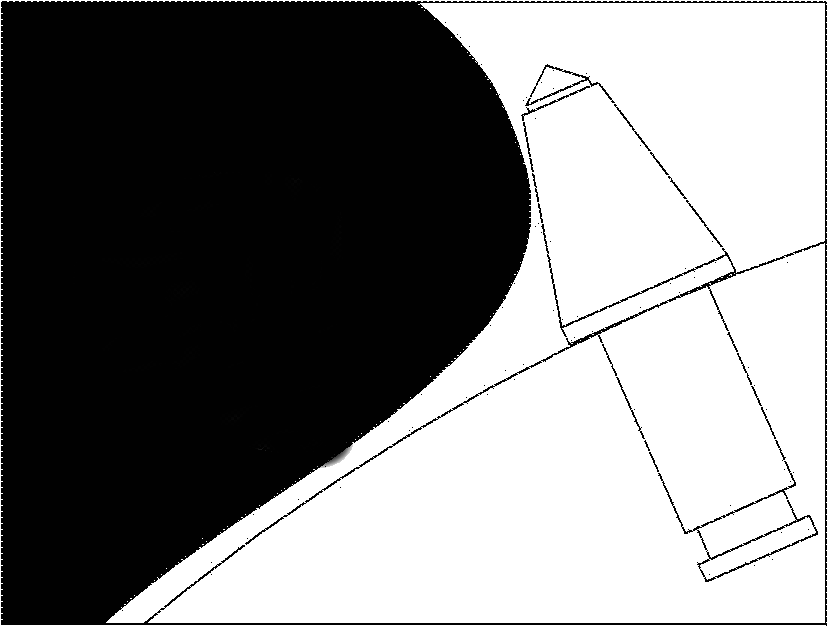
Figure 3 – Broken ground (103 kB, 14 frames, 0,5 s delay between frames, 4 cycling)
Sandvik company at work and combine this brand incisors requires always adhere to the instruction manual which states that after each generation should be measured on a workspace tool wear. If this reaches the value more than 15 mm, the cutter must be routinely replaced.
Conclusions and directions for further research
Conclusion of this work is such that the cutting tool on the executive board tunnel boring machine , it does not say , but is not always the most reliable part of the machine . In all this there is a fault , as miners and producers incisors. Not the proper use , over load , reduction of material from which made the cutter, not timely replacement , are all factors that can later lead to large losses.Next, I will conduct research about diagnosis tool breakage . Solutions will be identified and the conditions under which we can assess the situation for replacement or further continue.
References
- Классификация по сопротивляемости резанию углей и угольных пластов основных бассейнов СССР. Краткий научный отчет. – М.: ИГД им. А.А.Скочинского, 1970. – 40 с.
- Тон В.В. Исследование нагрузок на резцах для узкозахватных угледобывающих комбайнов: Автореф. дис. канд. техн. наук. – М.: Ин-т горн. дела им. А.А.Скочинского,1971 . – 18 с.
- Бойко М.Г. Експериментальні дослідження роботи очисних комбайнів. – Донецьк: ДВНЗ "ДонНТУ", 2011. – 252с.
- ОСТ 12.44.258-84. Комбайны очистные. Выбор параметров и расчет сил резания и подачи на исполнительных органах. Методика. Введен с 01.01.1986. – М.: Минуглепром СССР, 1984. – 107 с.
- ОСТ 12.44.197-81. Комбайны проходческие со стреловидным исполнительным органом. Расчет эксплуатационной нагруженности трансмиссии исполнительного органа. Введен с 01.07.1982. – М.: Минуглепром СССР, 1981. – 48 с.
- Кунтыш М.Ф. Методы оценки свойств угольных пластов сложного строения / М.Ф. Кунтыш, Э.И. Баронская – М.: Наука. 1980. – 143 с.
- Докукин А.В. Статистическая динамика горных машин / А.В. Докукин, Ю.Д. Красников, З.Я. Хургин – М.: Машиностроение, 1978. – 239 с.
- Бойко Н.Г. Формирование мгновенных усилий на передних гранях резцов / Н.Г. Бойко, В.И. Игнатов // Известия вузов. Горный журнал, 1983. – №7. – С.77-79.
- Бойко М.Г. Очисні комбайни для тонких пологих пластів. - Донецьк: ДВНЗ "ДонНТУ", 2010. – 476с
- Гуляев В.Г. Математическая модель и метод оптимизации параметров аксиальной коронки проходческого комбайна / В.Г. Гуляев, Д.А. Семенченко // Наукові праці ДонДТУ. Серія гірничо-електромеханічна. Донецьк – 2002. – Вип.42. - С.74-83.
- Семенченко Д.А. Обоснование параметров оптимизации аксиальной коронки проходческого комбайна. // Прогрессивные технологии и системы машиностроения. Сб. науч. трудов. – Донецк: ДонНТУ. – 2003. – Вып. 26. – С.65-69.