Реферат по теме выпускной работы
Содержание
- Введение
- 1. Проблема обеспечения надежности и безопасности химического оборудования
- 1.1. Актуальность проблемы
- 1.2. Технологическая схема улавливания и транспортирования коксового газа
- 2. Анализ конструкции и принцип работы оборудования системы
- 2.1. Коксовые печи
- 2.2. Газовый стояк и газосборник
- 2.3. Сепаратор
- 2.4. Первичный газовый холодильник
- 2.5. Нагнетатель
- 2.6. Анализ основных процессов, протекающих в оборудовании
- 2.7. Анализ деградационных процессов
- 2.8 Постановка задач исследования
- 3. Методы обеспечения техногенной безопасности химического оборудования
- 3.1 Теоретические основы расчета техногенной безопасности
- 3.1.1 Анализ предельных состояний в зоне улавливания и транспортирования коксового газа
- 3.1.2 Анализ технических рисков в зоне отвода и улавливания коксового газа
- 3.1.3 Анализ надежности системы улавливания и очистки коксового газа методом дерева отказов
- 3.2 Практические методы
- 3.2.1 Методы снижения коррозионной деградации
- 3.2.2 Методы снижения образования отложений
- Выводы
- Список источников
ВВЕДЕНИЕ
В печах в процессе коксования образуется кокс и химические продукты, выделяющиеся в виде весьма сложной смеси паров и газов, которую называют коксовым газом.
Коксовый газ является ценным сырьем, из которого получают смолу, аммиак, цианистый водород, сероводород, нафталин, сырой бензол и др.
В оборудовании систем улавливания и транспортирования коксового газа происходят различные технологические процессы. Такие как перемещение газа, его охлаждение, конденсация влаги из него. При этом протекают такие деградационные процессы:
- коррозия внутренних поверхностей соприкасающихся с веществом
- образование отложений на стенках трубопроводов вследствие конденсации, изменение свойства кирпича, и как следствие, изнашивание футеровки из-за насыщения его веществами из газопровода.
Эти деградационные процессы оказывают определяющее влияние на техническое состояние оборудования.
В данной работе рассмотрено оборудование системы улавливания и транспортирования коксового газа, выполнены материальный и теплой расчеты этого оборудования, рассмотрены основные деградационные процессы и способы борьбы с ними. Предложен метод расчета технического состояния коксохимического оборудования, позволяющий учесть деградацию оборудования, а также изменения оборудования в процессе работы.
1 ПРОБЛЕМА ОБЕСПЕЧЕНИЯ НАДЕЖНОСТИ И БЕЗОПАСНОСТИ ХИМИЧЕСКОГО ОБОРУДОВАНИЯ
1.1 Актуальность проблемы
Содержащееся в коксовом газе значительное количество паров смолы окрашивает его в темно-бурый или коричневый цвет.
Выделяющийся из печей коксовый газ называется прямым и содержит водяных паров 250-450м3, смоляных паров 80-120м3, бензольных углеводородов 30-40м3, аммиака 8-13м3, сероводорода 6-30м3, цианистых соединений 0,5-1,5м3.
Кроме того, в газе содержится незначительное количество легких пиридиновых оснований (0,4-0,6 г/м3), нафталин (до 10 г/м3), различные сероорганические (сероуглерод CS2, сероокись углерода COS, тиофен C4H4S и другие) (2-2,5 г/м3) и иные соединения.
После получения коксового газа в печах его необходимо уловить и выполнить над ним ряд технологических операций: охлаждение, конденсация смолы, транспортировка. Для этого используются системы улавливания и транспортирования газа, состоящие из стояка, газосборника, газопровода, сепаратора, первичного газового холодильника, газодувки (далее оборудование).
Из коксовой камеры горячий газ (t = 600—650°C) отводится через стояк, который чугунным коленом соединен с газопроводом, расположенным вдоль коксовой батареи. В стояк через форсунки подается барильетная вода с температурой 80°C, охлаждающая и увлажняющая газ. Затем газ попадает в сепаратор. Там влага со смолой конденсируется и подается в механизированный осветлитель, где очищают барильетную (надсмольную) воду.
После этого охлажденный до температуры в 85°C газ проходит через конечный газовый холодильник, еще раз охлаждаясь оборотной водой до 35°C. В таком виде коксовый газ подается в газодувку. Объем получаемого прямого коксового газа для всей батареи составляет 37 тыс. м3/ч.
Коксовый газ имеет сложный состав, содержит коррозионно-активные вещества и имеет высокую температуру. Он оказывает определяющее влияние на оборудование. Это приводит к относительно невысокой его надежности и долговечности.
К примеру, срок службы стояков 10 лет, капитальный ремонт проводят через 5 лет, при этом замена футеровки выполняется с периодичностью в 9 месяцев, очистка от отложений 1 раз в неделю.
Проблема надежности оборудования систем улавливания и транспортирования коксового газа носит особо важный характер, так как при его деградации возникают отказы, разрушения и как следствие происходят очень серьезные для окружающей среды выбросы, взрывы, пожары, за которыми следуют большие расходы.
В оборудовании систем улавливания и транспортирования коксового газа происходят различные технологические процессы. Такие как перемещение газа, его охлаждение, конденсация влаги из него. При этом протекают такие деградационные процессы:
- коррозия внутренних поверхностей соприкасающихся с веществом,
- образование отложений на стенках трубопроводов вследствие конденсации, изменение свойства кирпича, и как следствие, изнашивание футеровки из-за насыщения его веществами из газопровода.
Эти деградационные процессы оказывают определяющее влияние на техническое состояние оборудования.
К примеру, отложения, осаждающиеся на стенках газопровода, приводят к таким последствиям:
- уменьшается сечение труб;
- увеличивается давление;
- повышаются затраты на энергию;
- меняется гидравлический режим движения вещества по трубам;
- меняется шероховатость стенок трубопровода;
- ухудшается теплопередача;
- из-за коррозии уменьшается прочность трубопровода.
В каждый момент времени свойства оборудования и его технические характеристики подвергаются изменениям. То есть вместо исходного оборудования имеем несколько иное, с несколько другими свойствами.
Отсюда следует, что на этапе проектирования необходим прогноз технического состояния или изменения параметров в заданные моменты времени. Что возможно выполнить на основе моделирования изменения технического состояния оборудования.
Однако на практике получить точные данные о влиянии всех этих процессов очень сложно: скорость коррозии на разных участках оборудования различная, количество отложений также отличается, физико-механические свойства меняются по-разному. То есть все процессы, происходящие с оборудованием, имеют вероятностный характер и все свойства, как оборудования, так и технологических и деградационных процессов (размеры, шероховатость, физико-механические свойства, температура, давление, скорость коррозии и т.п.) необходимо описывать математическим ожиданием и дисперсией.
Для определения вероятности отказов системы необходимо учитывать множество факторов. Однако эти факторы, определяющие техническое состояние, являются вероятностными, то они представлены в виде интервала значений, и результаты расчетов также будут вероятностными. Использование такого подхода позволит значительно повысить точность определения показателей надежности в несколько раз.
Таким образом, вероятностные расчеты при проектировании являются конструктивным способом получения количественных оценок рабочих характеристик надежности изделия на различных этапах эксплуатации уже при проектирования. Поскольку при таком подходе рабочие характеристики изделия выражаются через статистические показатели, это помогает конструктору оценивать затраты на гарантийное обслуживание, разрабатывать программы технического обслуживания и планировать движение запасов.
1.2 Технологическая схема улавливания и транспортирования коксового газа
При нагревании угля без доступа воздуха до температуры 900-1100°C в камерах коксовых печей из него выделяются летучие продукты коксования. Из камер коксовых печей летучие продукты коксования по стоякам выходят в газосборники 1 (рисунок 1.1). Температура газов в стояке 750-800°C.
При охлаждении газа происходит частичная конденсация смолы и выпадение мелких частей каменного угля, отнесенных газом из печей.
За счет испарения части надсмольной воды (около 2-3% от подаваемой), коксовый газ охлаждается до 80-85°C, при этом, в виде тумана, из него конденсируется большая часть смолы (65-80% от той, которая содержится в коксовом газе). Под напором надсмольной воды (давление на газосборники не ниже 3кг/см2), которая подается через форсунки непосредственно в газосборник, сконденсировавшаяся смола и фусы смываются из днища последнего и отводятся с машинной стороны коксовой батареи через два переточных ящика в газопроводы коксового газа.
В отделении конденсации и первичного охлаждения коксового газа делают следующие технологические операции:
- первичное охлаждение коксового газа;
- очистка надсмольной воды от смолы и фусов;
- очистка смолы от воды и фусов;
- очистка охлажденного коксового газа от смолы;
- отсасывание коксового газа из коксовых батарей и транспортировка его через аппараты улавливания.
Охлажденный коксовый газ, пары воды и часть туманообразной смолы, а также сверхсмоляная вода, которая стекает из переточних ящиков по газопроводу, направляется в газовый сепаратор 2, где происходит разделение жидкой и газообразной фазы. Жидкая часть из газового сепаратора 2 отводится в механизированные осветители 10. Газовая часть, прямой коксовый газ, направляется под действием газодувки 8 к трубчатым газовым холодильникам 3.
Охлаждение коксового газа производится в трубчатых газовых холодильниках 3. Для охлаждения газа установлено 14 трубчатых газовых холодильников. Верхние две секции ПГХ орошаются поглощающим раствором цеха сероочистки. Другие секции холодильников охлаждаются оборотной технической водой, которая подается из насосной технической воды цеха водоснабжения.
Конденсат газа из холодильников 3 через гидрозатворы отводится в сборники 13, откуда насосами перекачивается в механизированные осветители и частично в отстойник 18.
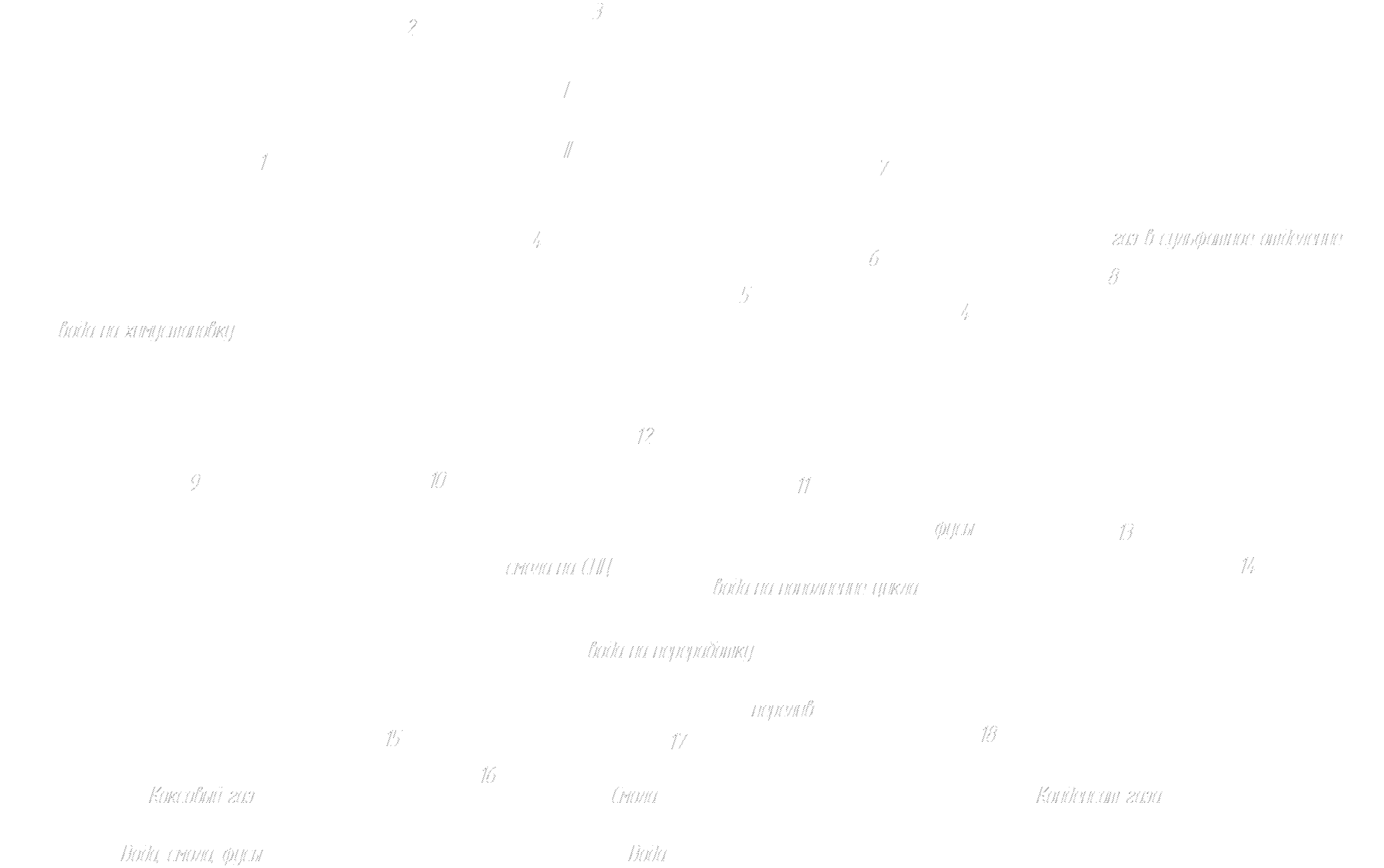
Рисунок 1.1 – Технологическая схема транспортировки коксового газа
Для отсасывания коксового газа из газосборников коксовых батарей установлены четыре газовых нагнетателя типа 1200-27-2, производительностью 72000 м3/ч.
В результате сжатия газа в нагнетателе выделяется тепло, что повышает температуру газа на выходе до 55-65°С.
Каждый нагнетатель оборудован стопорными задвижками на всасывающем 1 и нагнетательном 2 газопроводе, пусковым байпасом 3 и дроссельной заслонкой 4 на всасывающем газопроводе. Байпас диаметром 800 мм служит для грубой регулировки производительности нагнетателя в результате пропускания газа из нагнетательного трубопровода в газопровод перед трубчатыми газовыми холодильниками. Автоматическая регуляция отсасывания происходит с помощью дроссельной заслонки на всасывании нагнетателя.
2 Анализ конструкции и принцип работы оборудования системы
2.1 Коксовые печи
Современные печи для коксования углей представляют собой горизонтальные прямоугольные камеры, выложенные из огнеупорного материала. Камеры печей обогреваются через боковые стены. Печи располагаются в ряд и объединяются в батареи для уменьшения потери тепла и достижения компактности. В типовую батарею печей с шириной камер 410 мм входят обычно 65 печей, а в батарею большой емкости с камерами шириною 450 мм входят 77 печей. Обычные камеры имеют полезный объем 20—21,6 м3, а печи большой емкости—30 м3. Ширина печей более 450 мм нецелесообразна из-за ухудшения качества кокса (повышения истираемости). Для облегчения выталкивания кокса из камеры коксования ширину камеры со стороны выдачи кокса делают на 40—50 мм шире, чем с машинной стороны. Таким образом, камера имеет вид конуса. За основные элементы батареи надо принять следующие: фундамент, регенераторы, корнюрную зону, зону обогревательных простенков, перекрытия простенков и перекрытия камер.
Превращение угольной шихты в кокс является химическим процессом, проходящим без доступа воздуха. Этот процесс характеризуется сложными химическими, физическими и физико-химическими превращениями при термической деструкции угольной загрузки на отдельных стадиях процесса коксообразования.
2.2 Газовый стояк и газосборник
Стояк (рисунок 2.2) состоит из вертикальной трубы 2, тройника 3, крышки 5, колена 9, клапанной коробки 16 с тарельчатым клапаном 14, форсунки 8 для подачи надсмольной воды на орошение газа, форсунки (устанавливается в отверстие 4) для пароинжекции при бездымной загрузке и рычагов для управления крышкой и клапаном.
Стальная труба 2 устанавливается в гнездо 1, образованное в кладке печи над газоотводящим люком. После установки трубы гнездо уплотняется асбестовым шнуром и шамотным раствором. Внутри труба футерована шамотным кирпичом. Толщина футеровки 60 – 65 мм. Для защиты обслуживающего персонала от ожогов, сторона трубы, обращенная в сторону путей углезагрузочного вагона, закрывается стальным щитом. Поверхность щитка, обращенная к трубе, покрывается листовым асбестом.
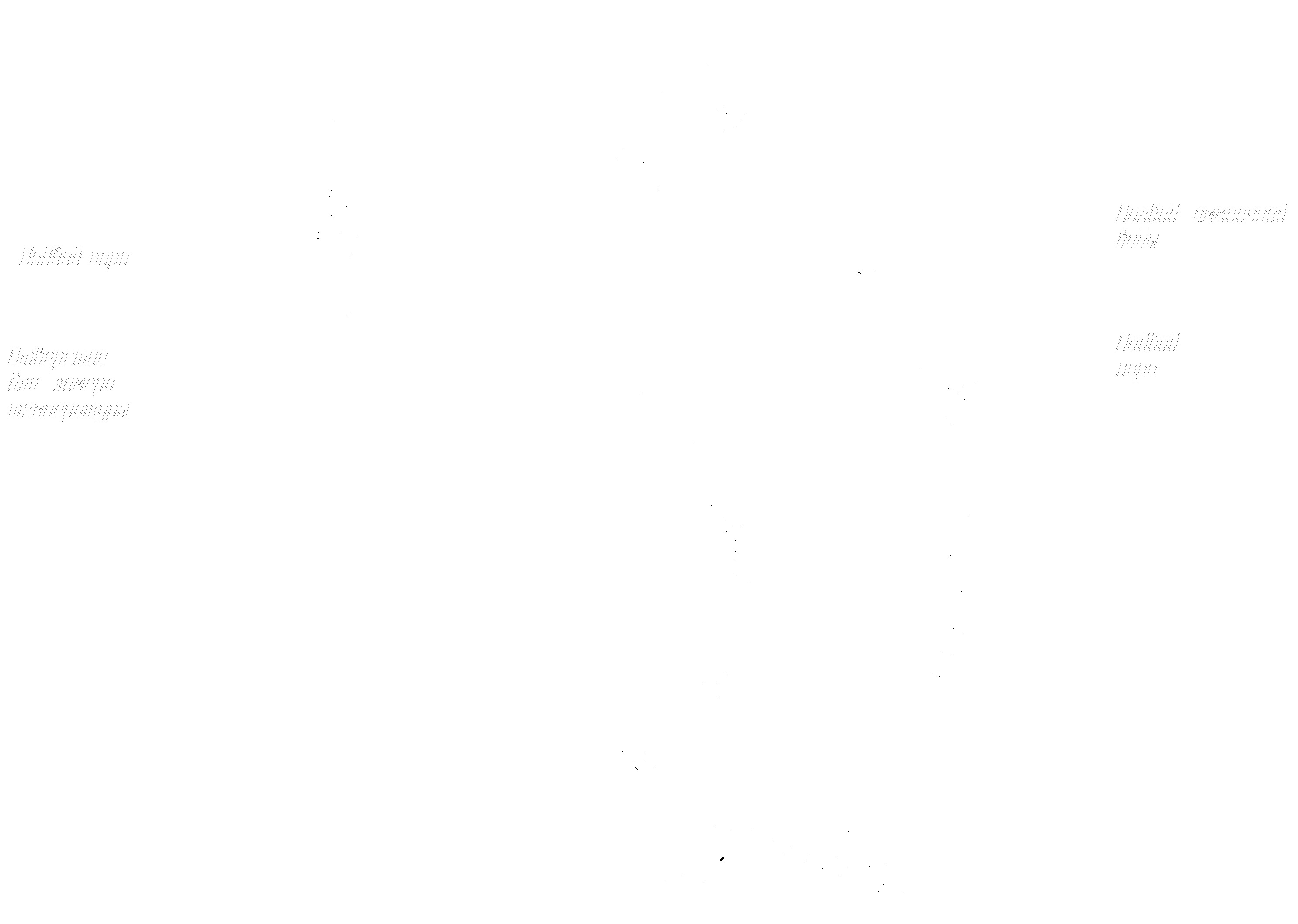
Рисунок 2.1– Стояк для отвода газа из коксовой печи
Тройник 3 с закрепленным на нем коленом 9, присоединяется к трубе фланцем. Сверху тройник закрывается крышкой 6. Между крышкой и съемным фланцем 5 тройника имеется уплотнение типа «железо по железу», при котором острие крышки устанавливается на обработанную поверхность съемного фланца.
Клапанная коробка 16 присоединена фланцем к газосборнику13. В клапанной коробке размещен вал 17, на котором монтируется тарельчатый клапан 14. При закрывании клапан поворачивается до соприкосновения с коническим седлом 15. Вода, подаваемая на орошение, заполняет тарелку клапана так, что конус оказывается погруженным в жидкость. При этом образуется гидрозатвор, отключающий стояк от газосборника. Высота гидрозатвора 40 мм. Закрывание клапана производится перед выдачей кокса. При коксовании клапан открыт, и газ из камеры коксования поступает в газосборник. При прохождении по стояку газ охлаждается при непосредственном контакте с водой, разбрызгиваемой форсункой 8, установленной на колене. Давление воды перед форсункой 0,3—0,35 МПа.
Форсунку орошения сырого коксового газа устанавливают таким образом, чтобы конус распыления аммиачной водой перекрывал все сечение потока газа и при этом, вода не могла попасть в коксовую камеру. Аммиачная вода орошения газа в стояке служит гидрозатвором при закрытии клапанной коробки, с помощью которой колено стояка соединяется с газосборником.
Тройники, колена и клапанные коробки изготавливают из (чугуна марки СЧ 21 — 40; крышки стояков и клапаны — из стали.
Из стояка через колено и клапанную коробку продукты коксования проходят в газосборники – стальные трубы, диаметром 1100 – 1600 мм, расположенные с машинной и коксовой стороны батареи, или только с машинной.
Колено и корпус стояка оборудованы рычажной системой, с помощью которой приводится в движение крышка и клапан. Обе кинематические цепи приводятся к действию одним рычагом, или гидроприводом.
2.3 Сепаратор
По принципу работы сепаратор относится к инерционным центробежным аппаратам вихревого типа. Разделение газожидкостного потока на составляющие в аппарате происходит под действием центробежных сил, направленных радиально по отношению к вертикальной оси сепаратора. Величина центробежной силы, действующей на каплю влаги или частичку механических примесей зависит от скорости потока на входе в сепаратор, плотности капельки (ее веса) и радиуса аппарата. Чем меньше радиус аппарата, тем больше возникающая центробежная сила.
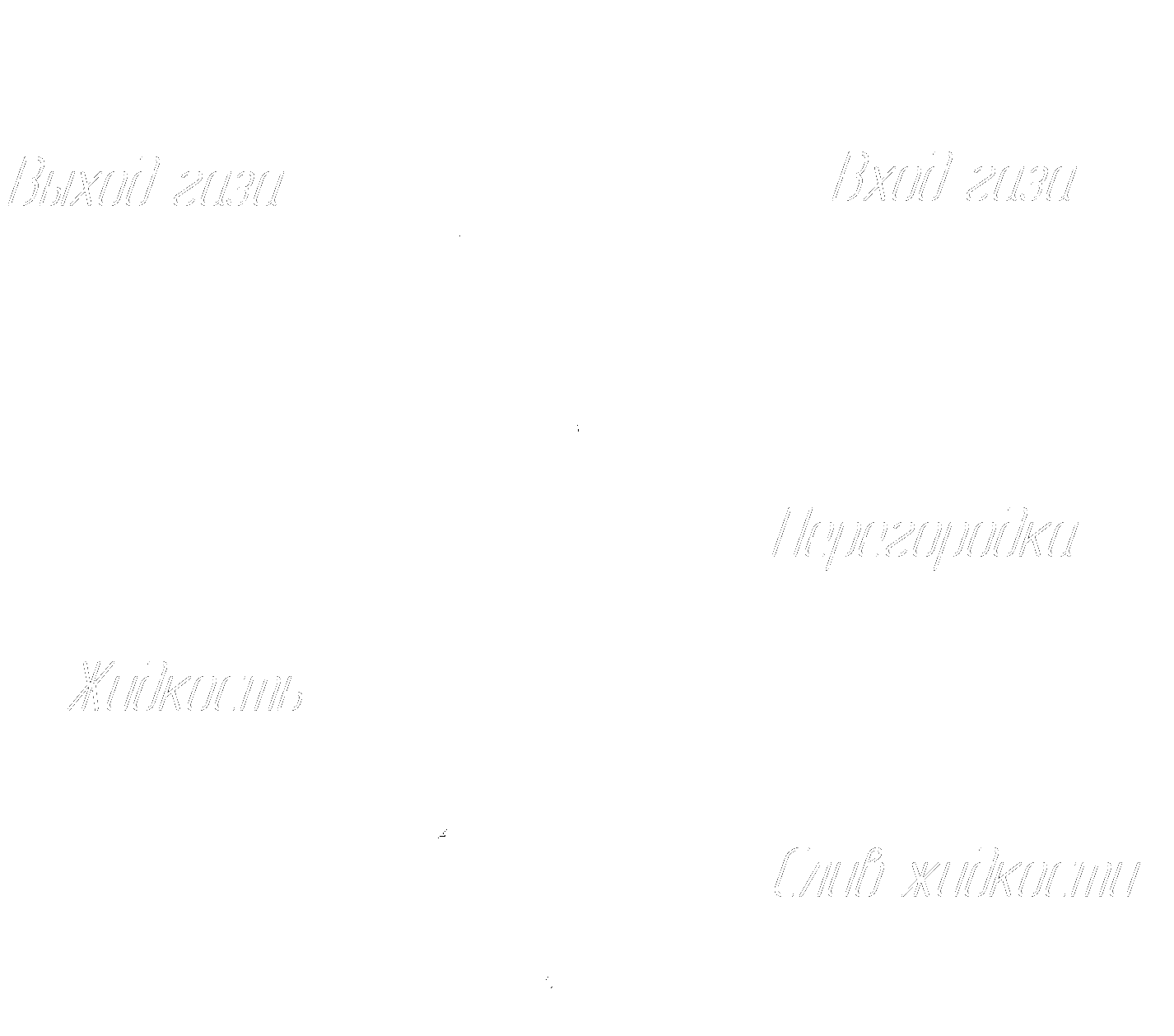
Рисунок 2.2 – Газовый сепаратор
Сепаратор содержит в своей конструкции 7 ступеней сепарации, одновременно являющимися конструктивными элементами, предназначенными для разделения газожидкостного потока.
Сепаратор работает следующим образом. Газожидкостный поток поступает в сепаратор через входной газовый патрубок 11, где приобретает вращательное движение вокруг вертикальной оси сепаратора благодаря конструкции дефлектора 5. Вращаясь вокруг вертикальной оси, жидкость и механические примеси, под действием центробежных сил отделяются от газожидкостного потока и прижимаются к корпусу сепаратора 4. Здесь происходит отделение примерно 80 % жидкости и механических примесей от газового потока.
Далее газожидкостный поток поступает через зазоры сепарационного пакета 6 во внутреннюю полость сепарационного пакета, продолжая вращение вокруг вертикальной оси сепаратора, направляется в выходной газовый патрубок 2. В сепарационном пакете происходит полная очистка газового потока от капельной влаги и мех. примесей.
Отделенная жидкость и механические примеси под действием силы гравитации стекают по стенкам корпуса сепаратора и по пластинам сепарационного пакета вниз к сливному патрубку 8.
2.4 Первичный газовый холодильник
Для первичного охлаждения газа устанавливаются горизонтальные трубчатые холодильники системы Гипрококса (рис.1.6) поверхностью охлаждения 2100 м2. Производительность этого холодильника по газу равна 10—11 тыс. м3/ч газа, приведенного к нормальным условиям.
Газ движется в межтрубном пространстве, охлаждающая вода — в трубах. Так как коэффициент теплопередачи возрастает с увеличением скорости движения газа и воды, то для увеличения этих скоростей холодильник разделен вертикальными перегородками на шесть секций.
Холодильник по высоте разделен тремя горизонтальными перегородками, образующими нижнюю камеру для воды, среднюю — камеру охлаждения, заполненную трубами, и верхнюю камеру для перелива воды.
Газ вступает в межтрубное пространство камеры охлаждения и последовательно проходит из одной секции в другую. Вода поступает в нижнюю камеру, разделенную также на секции, и поднимается по трубам шестой по ходу газа секции (первой по ходу воды) вверх, затем сливается по трубам вниз и т. д. Таким образом, во всех шести секциях соблюден полный противоток движения газа и воды.
Для поддержания постоянной скорости движения газа и воды и, следовательно, постоянства коэффициента теплопередачи от газа к воде секции, по которым движется газ, имеют переменное сечение: наибольшее у первой по ходу газа секции и наименьшее у последней по ходу газа секции. Для воды, движущейся в противоточном направлении, наименьшее сечение труб в первой по ходу воды секции и наибольшее в месте выхода ее из холодильника. Весьма важным фактором, в значительной мере определяющим эффективность работы трубчатых холодильников, является скорость газового потока. Она, естественно, будет тем выше, чем больше нагрузка холодильника по газу. Поэтому лучшее охлаждение газа при меньшем расходе охлаждающей воды получается при последовательном прохождении газа через ряд соединенных друг с другом холодильников. Однако при этом резко возрастает сопротивление газовому потоку, т. е. разность разрежения газа до и после холодильников увеличивается.
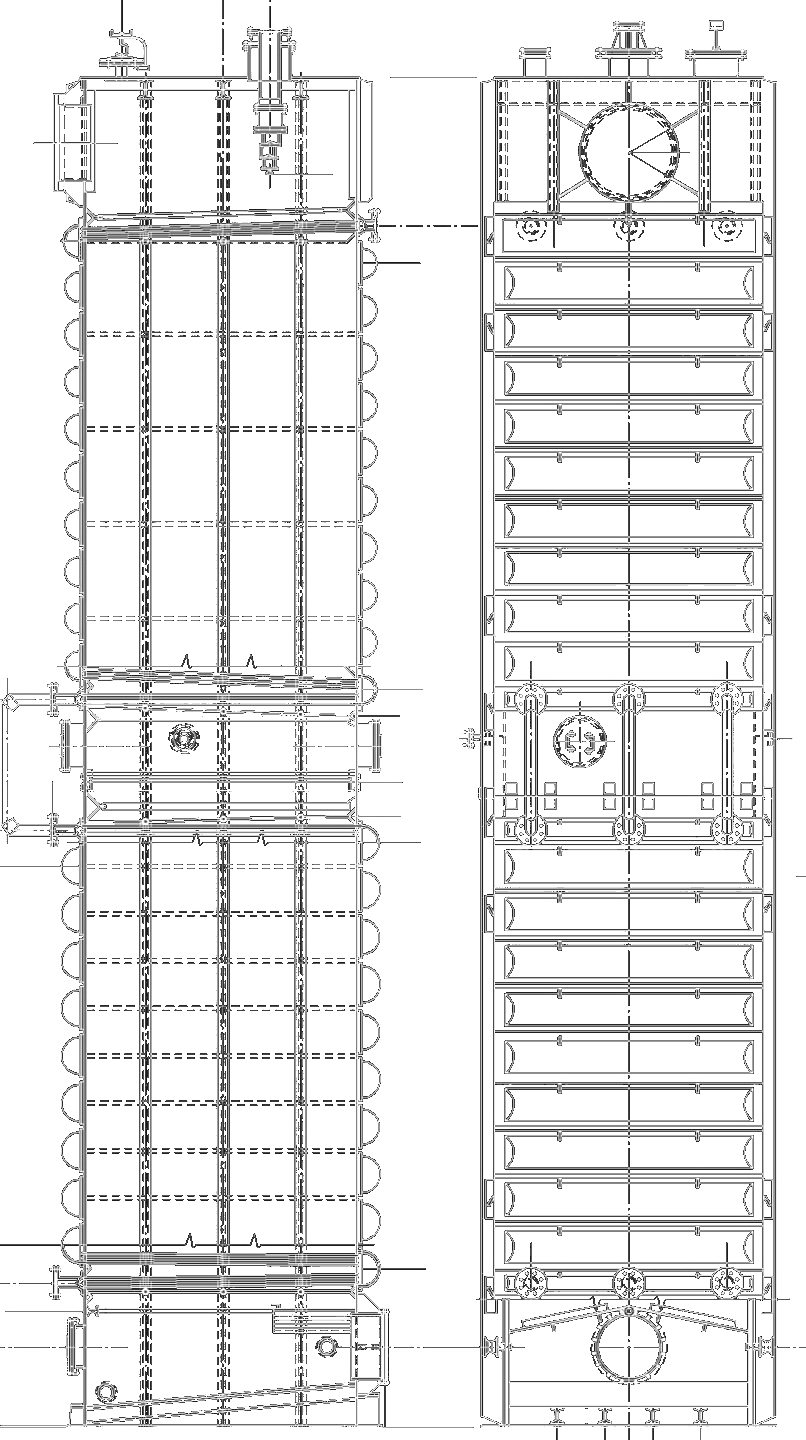
Рисунок 2.3 – Схема газового холодильника
2.5 Нагнетатель
Назначение нагнетателей – отсасывание коксового газа из коксовых печей, транспортирование его через аппаратуру цеха улавливания и подача после этого потребителям.
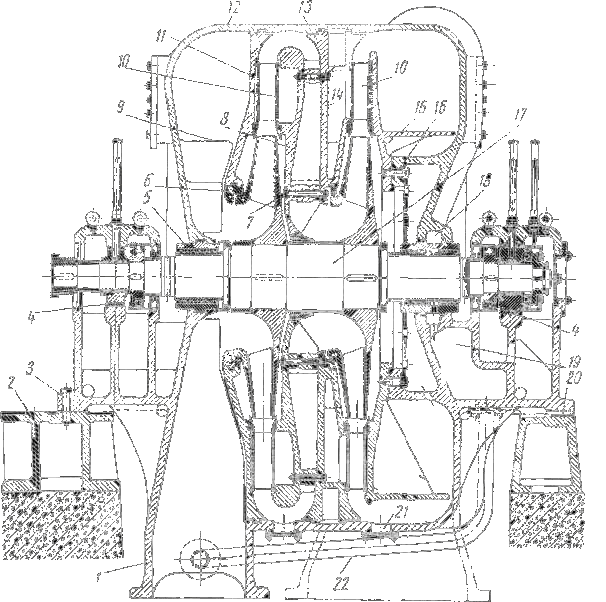
Рисунок 2.4 - Продольный разрез нагнетателя
Нагнетатели газа располагаются в машинном отделении цеха улавливания. Чаще всего они устанавливаются после первичных газовых холодильников. Газопровод и аппаратура, расположенные до нагнетателя, находятся под разрежением, а после нагнетателя – под давлением.
Газ из коксовых батарей, соединенных попарно, через первичные холодильники поступает в общий коллектор, расположенный перед машинным отделением. Из коллектора двумя нагнетателями газ подается в газопровод, идущий к отделениям цеха улавливания.
По пути следования коксовый газ испытывает сопротивление участков газопроводов и аппаратуры, которое вызывает изменение давления газа на отдельных участках газовой трассы.
На современных коксохимических заводах применяют нагнетатели центробежного типа, приводимые в движение паровой турбиной (3000–5000 об/мин) или от тихоходного высоковольтного электродвигателя (1450 об/мин) через зубчатый редуктор, увеличивающий скорость вращения до 3000–5000 об/мин.
На случай возможных перебоев в подаче электроэнергии один или два нагнетателя (из трех) должны иметь привод от паровой турбины. Как правило, в работе находится один нагнетатель с электроприводом и один с турбоприводом.
Нагрев газа в нагнетателях в зависимости от степени сжатия колеблется в пределах 10–15°С. Поэтому коксовый газ после нагнетателей имеет температуру 35–45°С.
2.6 Анализ основных процессов, протекающих в оборудовании
В печах в процессе коксования образуется кокс и химические продукты, выделяющиеся в виде весьма сложной смеси паров и газов, которую называют коксовым газом.
Коксовый газ является ценным сырьем, из которого получают смолу, аммиак, цианистый водород, сероводород, нафталин, сырой бензол и др.
Содержащееся в коксовом газе значительное количество паров смолы окрашивает его в темно-бурый или коричневый цвет.
Выделяющийся из печей коксовый газ называется прямым и содержит водяных паров 250-450 м3, смоляных паров 80-120 м3, бензольных углеводородов 30-40 м3, аммиака 8-13 м3, сероводорода 6-30 м3, цианистых соединений 0,5-1,5 м3.
Из коксовой камеры горячий газ (t=600-650°C) отводится через стояк, который чугунным коленом соединен с газосборником, расположенным вдоль коксовой батареи. В стояк через форсунки подается барильетная вода с температурой 80°C, охлаждающая и увлажняющая газ. Затем газ попадает в сепаратор. Там влага со смолой конденсируется и подается в механизированный осветлитель, где очищают барильетную (надсмольную) воду.
Взаимодействие газа и охлаждающей воды в газосборнике сопровождается процессами тепло- и массообмена.
Процесс теплообмена определяется разностью температур газа и воды. Так как температура газа выше температуры орошающей воды, то тепло передается от газа к воде, и он охлаждается.
Движущей силой второго процесса — массообмена является разность между упругостью паров воды при ее температуре и парциальным давлением водяных паров в газе. Так как упругость водяных паров над поступающей водой больше, чем парциальное давление их в газе, поступающем из камер коксовых печей, то происходит испарение воды.
Следовательно, тепло QГ, отдаваемое газом, частично переходит к образующемуся пару, смешивающемуся с газовым потоком, а остальное тепло охлаждения газа QГ — Qп идет на нагрев воды.
По мере охлаждения газа и нагрева воды разность температур между ними будет уменьшаться, а вместе с тем будет уменьшаться и количество передаваемого тепла от газа к воде. Очевидно, наступит момент, когда величина Qг станет равной Qи, после чего дальнейший нагрев воды станет невозможным, а все тепло, получаемое водой от газа, пойдет на ее испарение при постоянной температуре. Пределу охлаждения газа будет соответствовать температура мокрого термометра.
Затем газ попадает в сепаратор, где происходит отделение жидкой фазы и газа. В таком виде коксовый газ подается в газодувку, она же нагнетатель. Объем получаемого прямого коксового газа для всей батареи составляет 37 тыс. м3/ч. В нагнетателях происходит частичное выделение туманообразной смолы из газа до содержания 0.2-0.5 г/м3. Выделившаяся в нагнетателях смола стекает через специальные спускные линии в гидравлический затвор. Вследствие сжатия газа в нагнетателях выделяется тепло, которое повышает температуру выходящего газа. Некоторая часть тепла теряется через корпус, но она очень мала в сравнении с общим количеством выделяемого тепла. После нагнетателей температура газа повышается обычно на 15-25°С.
2.7 Анализ деградационных процессов
Коксовый газ имеет сложный состав, содержит коррозионно-активные вещества и имеет высокую температуру. Он оказывает определяющее влияние на оборудование. Это приводит к относительно невысокой его надежности и долговечности.
В оборудовании систем улавливания и транспортирования коксового газа происходят различные технологические процессы. Такие как перемещение газа, его охлаждение, конденсация влаги из него. При этом протекают такие деградационные процессы:
- коррозия внутренних поверхностей соприкасающихся с веществом
- образование отложений на стенках трубопроводов вследствие конденсации
- изменение свойства кирпича и, как следствие, изнашивание футеровки из-за насыщения его веществами из газопровода.
Эти деградационные процессы оказывают определяющее влияние на техническое состояние оборудования.
К примеру, отложения, осаждающиеся на стенках газосборника, приводят к таким последствиям:
- уменьшается сечение труб;
- увеличивается давление;
- повышаются затраты на энергию;
- меняется гидравлический режим движения вещества по трубам;
- меняется шероховатость стенок трубопровода;
- ухудшается теплопередача;
- из-за коррозии уменьшается прочность трубопровода.
В первичном газовом холодильнике наблюдаются подобные проблемы:
- из-за взаимодействия металлических конструкций с кислородом воздуха и влияния агрессивных рабочих сред развивается коррозия металлоконструкций;
- из-за трения жидкости, содержащей абразивные частички, при движении потока, об металл изнашивается поверхность ПГХ, а точнее крышки трубных решеток и переходные колена;
- при нагревании технической воды выше допустимого уровня на внутренней поверхности труб образуются соли жесткости (накипь);
- процесс адгезии - притяжение жидких или твердых тел при их молекулярном контакте, для нарушения которого необходимо внешнее воздействие возникает, в тех случаях, когда при охлаждении компоненты газа конденсируются на внешних поверхностях труб.
2.8 Постановка задач исследования
В каждый момент времени свойства оборудования и его технические характеристики подвергаются изменениям. То есть вместо исходного оборудования имеем несколько иное, с несколько другими свойствами.
Отсюда следует, что на этапе проектирования необходим прогноз технического состояния или изменения параметров в заданные моменты времени. Что возможно выполнить на основе моделирования изменения технического состояния оборудования.
Однако на практике получить точные данные о влиянии всех этих процессов очень сложно: скорость коррозии на разных участках оборудования различная, количество отложений также отличается, физико-механические свойства меняются по-разному. То есть все процессы, происходящие с оборудованием, имеют вероятностный характер и все свойства, как оборудования, так и технологических и деградационных процессов (размеры, шероховатость, физико-механические свойства, температура, давление, скорость коррозии и т.п.) необходимо описывать математическим ожиданием и дисперсией.
Для определения вероятности отказов системы необходимо учитывать множество факторов. Однако эти факторы, определяющие техническое состояние, являются вероятностными, т. е. они представлены в виде интервала значений, и результаты расчетов также будут вероятностными. Использование такого подхода позволит значительно повысить точность определения показателей надежности в несколько раз.
Таким образом, вероятностные расчеты при проектировании являются конструктивным способом получения количественных оценок рабочих характеристик надежности изделия на различных этапах эксплуатации уже при проектирования. Поскольку при таком подходе рабочие характеристики изделия выражаются через статистические показатели, это помогает конструктору оценивать затраты на гарантийное обслуживание, разрабатывать программы технического обслуживания и планировать движение запасов.
3 МЕТОДЫ ОБЕСПЕЧЕНИЯ ТЕХНОГЕННОЙ БЕЗОПАСНОСТИ ХИМИЧЕСКОГО ОБОРУДОВАНИЯ
Как установлено из раздела 1, оборудование под воздействием агрессивных сред неуклонно деградирует. И, к сожалению, остановить этот процесс полностью невозможно. Однако существуют различные методы для уменьшения интенсивности деградационного воздействия на конкретные объекты.
3.1 Теоретические основы расчета техногенной безопасности
3.1.1 Анализ предельных состояний в зоне улавливания и транспортирования коксового газа
Целью метода является не допускать с определенной вероятностью наступления предельных состояний при эксплуатации в течение всего заданного срока службы оборудования, а также при производстве работ.
Предельное состояние - состояния, при которых конструкции перестают удовлетворять заданным эксплуатационным требованиям или требованиям при производстве работ.
В расчетах оборудования на действие статических и динамических нагрузок и воздействий, которым они могут подвергаться в процессе эксплуатации и заданного срока службы, учитываются следующие предельные состояния первой и второй группы.
К первой группе относятся:
- общая потеря устойчивости формы;
- потеря устойчивости положения;
- разрушение любого характера;
- переход конструкции в изменяемую систему;
- качественное изменение конфигурации;
- состояния, при которых возникает необходимость прекращения - эксплуатации в результате текучести материала и т.д.
Ко второй группе относятся состояния, затрудняющие нормальную эксплуатацию или снижающие долговечность вследствие появления недопустимых перемещений (прогибов, осадок, углов поворота, колебаний, трещин и т.п.).
Предельные состояния первой группы проверяются расчетом на максимальные (расчетные) нагрузки и воздействия, возможные при нарушении нормальной эксплуатации, а предельные состояния второй группы - на эксплуатационные (нормативные) нагрузки и воздействия, отвечающие нормальной эксплуатации оборудования.
Надежность и гарантия от возникновения предельных состояний конструкции обеспечиваются надлежащим учетом возможных наиболее неблагоприятных характеристик материалов; перегрузок и наиболее невыгодного (но реально возможного) сочетания нагрузок и воздействий; условий и особенностей работы; надлежащим выбором расчетных схем и предпосылок расчета, учетом в необходимых случаях пластических свойств материалов.
Для первой группы условие по несущей способности может быть записано в общем виде
N≤Ф,
где N - усилие, действующее в рассчитываемом элементе конструкции (функция нагрузок и других воздействий);
Ф - предельное усилие, которое может воспринять рассчитываемый элемент (функция физико-механических свойств материала, условий работы и размеров элементов).
Для второй группы предельных состояний, связанных, как правило, с перемещениями, также можно записать предельное неравенство:
f≤[f],
где f – перемещение конструкции (функция нагрузок);
[f] – предельное перемещение, допустимое по условиям эксплуатации (функция конструкции и ее назначения).
В общем случае работа конструкций и переход их в предельное состояние зависят от нагрузок, свойств материала и условий работы. Рассмотрим учет этих факторов при расчете конструкции по предельным состояниям.
В процессе эксплуатации объекты подвергаются различным нагрузкам и воздействиям.
Работа объекта, а, следовательно, и особенности его расчета во многом зависят от природы, характера и продолжительности воздействий. Так, при взрыве следует учитывать влияние скорости нагружения на свойства материала; при воздействии низких температур - повышенную опасность хрупкого разрушения; при продолжительном воздействии – ползучесть материала.
Классификация нагрузок и воздействий.
По своей природе нагрузки и воздействия подразделяют на:
- нагрузки от собственного веса конструкций;
- технологические нагрузки (вес оборудования, складируемых материалов, людей, давление жидкостей, газов, сыпучих материалов и т.д.);
- атмосферные нагрузки (снег, ветер, гололед);
- температурные (технологические и климатические) воздействия;
- монтажные нагрузки;
- сейсмические и взрывные воздействия;
- аварийные нагрузки, возникающие при резком нарушении технологического процесса, поломках оборудования, обрывах проводов линий электропередачи и т.д.
Все эти нагрузки и воздействия вызывают в объекте усилия и перемещения и могут быть отнесены к прямым воздействиям. Кроме них на конструкции могут влиять химические (коррозия), радиационные и другие воздействия. Эти воздействия приводят к изменению свойств материала (снижению ударной вязкости при радиационном воздействии), меняют параметры работы элементов (уменьшение толщины элементов, повышение концентрации напряжений при коррозии) и в итоге влияют на несущую способность и долговечность конструкций. Такие воздействия называют косвенными.
Под характером воздействия понимают скорость и частоту приложения нагрузок. По этому признаку нагрузки подразделяют на статические, динамические и переменные многократно повторяющиеся.
При статических нагрузках скорость нагружения равна нулю и. только мала, что вызываемые ими инерционные силы в расчете можно не учитывать. При динамических нагрузках скорость нагружения высока и, вызываемые ими инерционные силы, необходимо учитывать при расчете объектов. При воздействии переменных многократно повторяющихся нагрузок в конструкциях могут возникнуть усталостные разрушения. В этом случае конструкции необходимо проверить на выносливость.
В зависимости от продолжительности действия нагрузки делят на постоянные и временные. Временные нагрузки в свою очередь подразделяют на длительные, кратковременные и особые.
Постоянными нагрузками называют такие, которые действуют на конструкцию постоянно: собственный вес, давление, воздействие предварительного напряжения конструкций и т.п.
Длительными нагрузками называют такие, которые действуют на конструкцию продолжительное время (но могут и отсутствовать): вес технологического оборудования, вес складируемых грузов, давление жидкостей и газов в резервуарах и трубопроводах.
Кратковременными нагрузками называют нагрузки, действующие непродолжительное время: снег, ветер, подвижные краны, нагрузки (возникающие при транспортировке, монтаже, ремонтах и испытаниях), температурные климатические воздействия и т.д.
Особые нагрузки – это нагрузки, которые могут появиться в исключительных случаях: сейсмические воздействия, аварийные нарушения технологического процесса, резкие просадки грунтов.
Нормативные и расчетные нагрузки. Все нагрузки в той или иной степени случайны и при математическом описании могут быть представлены в виде случайных величин (например, собственный вес конструкций) или случайных функций времени (например, ветер). Однако при расчете конструкций но предельным состояниям принимаем детерминированные значения нагрузок. Поэтому для обеспечения необходимого уровня надежности при расчете конструкций по первой группе предельных состояний следует принимать максимальные значения нагрузок с высокой степенью обеспеченности. При расчете по второй группе предельных состояний, т.е. в условиях нормальной эксплуатации. обеспеченность может быть ниже.
Основные положения по расчету устанавливают два значения нагрузок: нормативные и расчетные.
Нагрузки, отвечающие условиям нормальной эксплуатации, называют нормативными. Их величину устанавливают в нормах проектирования, обговаривают в техническом задании или определяют по проектным значениям геометрических параметров оборудования или конструкций.
Возможное отклонение нагрузок в неблагоприятную (большую пли меньшую) сторону от их нормативных значений, как вследствие естественной изменчивости нагрузок, так и отступлений от условий нормальной эксплуатации учитывается коэффициентом надежности по нагрузке γj. Значение этого коэффициента зависит от характера нагрузки и степени ее изменчивости. Так, нагрузки от собственного веса металлических конструкций могут отклоняться от нормативной в достаточно узких пределах (за счет допусков на размеры сечений, точности резки и т.п.), поэтому для этой нагрузки γj = 1,05.
Значения коэффициентов надежности по нагрузке определяют на основании статистической обработки результатов наблюдений, экспериментальных исследований или устанавливают на основании опыта проектирования.
Расчетные нагрузки представляют собой наибольшие в вероятностном смысле нагрузки и воздействия за время эксплуатации сооружения.
Коэффициенты надежности по нагрузке учитывают только изменчивость нагрузки и возможность превышения ею нормативных значений. Они не учитывают динамического характера нагрузки или перспективного возрастания нагрузки со временем, например при модернизации производства и смене оборудования. Эти факторы при необходимости учитывают отдельно.
3.1.2 Анализ технических рисков в зоне отвода и улавливания коксового газа
Под риском следует понимать ожидаемую частоту или вероятность возникновения опасностей определенного класса, или же размер возможного ущерба (потерь, вреда) от нежелательного события, или же некоторую комбинацию этих величин.
Применение понятия риск, таким образом, позволяет переводить опасность в разряд измеряемых категорий. Риск, фактически, есть мера опасности. Часто используют понятие "степень риска", по сути, не отличающееся от понятия риск, но лишь подчеркивающее, что речь идет об измеряемой величине.
Все названные (или подобные) интерпретации термина "риск" используются в настоящее время при анализе опасностей и управлении безопасностью (риском) технологических процессов и производств в целом.
Формирование опасных и чрезвычайных ситуаций - результат определенной совокупности факторов риска, порождаемых соответствующими источниками.
Применительно к проблеме безопасности производства таким событием может быть авария или катастрофа технической системы или устройства, загрязнения или разрушение экологической системы, гибель группы людей, материальный ущерб от реализовавшихся опасностей или увеличения затрат на безопасность.
Каждое нежелательное событие может возникнуть по отношению к определенной жертве - объекту риска. Соотношение объектов риска и нежелательных событий позволяет различать индивидуальный, технический, экологический, социальный и экономический риск. Каждый вид его обусловливают характерные источники и факторы риска, классификация и характеристика которого приведены в табл. 3.1
Таблица 3.1 – Классификация и характеристика видов риска
Вид риска | Объект риска | Источник риска | Нежелательное событие |
Индивидуальный |
Человек | Условия жизнедеятельности человека | Заболевание, травма, инвалидность, смерть |
Технический |
Технические системы и объекты | Техническое несовершенство, нарушение правил эксплуатации технических систем и объектов | Авария, взрыв, катастрофа, пожар, разрушение |
Экологический |
Экологические системы | Антропогенное вмешательство в природную среду, техногенные чрезвычайные ситуации | Антропогенные экологические катастрофы, стихийные бедствия |
Социальный |
Социальные группы | Чрезвычайная ситуация, снижение качества жизни | Групповые травмы, заболевания, гибель людей, рост смертности |
Экономический |
Материальные ресурсы | Повышенная опасность производства или природной среды | Увеличение затрат на безопасность, ущерб от недостаточной защищенности |
Индивидуальный риск может быть добровольным, если он обусловлен деятельностью человека на добровольной основе, и вынужденным, если человек подвергается риску в составе части общества (например, проживание в экологически неблагоприятных регионах, вблизи источников повышенной опасности).
Технический риск - комплексный показатель надежности элементов техносферы. Он выражает вероятность аварии или катастрофы при эксплуатации машин, механизмов, реализации технологических процессов, строительстве и эксплуатации зданий и сооружений:
где Rт - технический риск;
ΔT - число аварий в единицу времени t на идентичных технических системах и объектах;
T - число идентичных технических систем и объектов, подверженных общему фактору риска f.
Источники и факторы технического риска приведены в табл. 3.2
Таблица 3.2 – Источники и факторы технического риска
Источник технического риска | Наиболее распространенные факторы технического риска |
Низкий уровень научно-исследовательских работ | Ошибочный выбор направлений развития техники в технологии по критериям безопасности |
То же, опытно-конструкторских работ |
Выбор потенциально опасных конструктивных схем и принципов действия технических систем.
Ошибки в определении эксплуатационных нагрузок. Неправильный выбор конструкционных материалов. Недостаточный запас прочности. Отсутствие в проектах технических средств безопасности. |
Опытное производство новой техники | Некачественная доводка конструкций, технологии, документации по критериям безопасности |
Серийный выпуск небезопасной техники |
Отклонение от заданного химического состава конструкционных материалов.
Недостаточная точность конструкционных размеров. Нарушение режимов термической обработки деталей. Нарушение регламентов сборки и монтажа конструкций и машин. |
Нарушение правил безопасной эксплуатации технических систем |
Использование техники не по назначению.
Нарушение паспортных режимов эксплуатации. Несвоевременные профилактические осмотри и ремонты. Нарушение требований транспортирования и хранения. |
Ошибки персонала |
Слабые навыки действия в сложной ситуации.
Неумение оценивать информацию о состоянии процесса. Слабое знание сущности происходящего процесса. Отсутствие самообладания в условиях стресса. Недисциплинированность. |
3.1.3 Анализ надежности системы улавливания и очистки коксового газа методом дерева отказов
Наиболее используемым методом анализа возможных отказов оборудования является метод «дерева отказов». Он заключается в построении и анализе модели надежности (безопасности), представляющей собой логико-вероятностную модель причинно-следственных связей отказов исследуемой системы с отказами ее элементов и прочими воздействиями.
Основными достоинствами метода являются:
- высокая наглядность представления результатов анализа, что делает их доступными для широкого круга специалистов (не только в области безопасности);
- возможность выполнять как качественный, так и количественный анализ безопасности системы;
- позволяет показать в явном виде ненадежные места системы;
- обеспечивает глубокое представление о поведении системы и проникновение в процесс ее работы.
Недостатки «дерева отказов» состоят в следующем:
- реализация метода требует значительных затрат средств и времени;
- дерево отражает только два состояния системы: рабочее и отказавшее;
- дерево отказов описывает систему в определенный момент времени (обычно в установившемся режиме);
- требует от специалистов по надежности глубокого понимания системы и конкретного рассмотрения каждый раз только одного определенного отказа.
Несмотря на широкое освещение в научно-технической литературе, на практике специалисты допускают ряд методических и логических ошибок. Это приводит к некорректности результатов анализа безопасности.
Основными ошибками являются:
- несоответствие «дерева» иерархической структуре системы;
- упущение существенных факторов и придание избыточного веса несущественным;
- введение ложных операторов не несущих смысловой нагрузки, но участвующих в расчете;
- рассмотрение отказов, не влияющих на безопасность оборудования;
- некорректное использование логических символов;
- некорректное использование статистических данных.
Рассмотрим ключевые моменты построения «дерева отказов» в инженерной практике.
Прежде чем приступить к построению, необходимо проанализировать следующие источники информации об объекте:
- проектную документацию;
- документацию заводов-изготовителей оборудования;
- технологический регламент установки;
- эксплуатационную и ремонтную документацию.
На основании полученных данных проводится анализ процесса эксплуатации объекта, и разрабатываются перечни возможных отказов и их причин.
Анализ процесса эксплуатации позволяет получить необходимые сведения для выявления возможных отказов. Его проводят в следующем порядке:
- определяют назначение системы, особенности ее эксплуатации и перечень выполняемых задач;
- выделяют основные, обеспечивающие и вспомогательные функции изделия;
- для каждой выделенной функции определяют группы выходных параметров, номинальные и предельно допустимые значения каждого параметра;
- определяют виды элементов системы, их функциональные особенности и характер взаимодействия при эксплуатации, наличие резервных элементов, выявляют элементы, не имеющие аналогов;
- определяют особенности эксплуатации изделия (основные и резервные режимы эксплуатации, возможности работы с измененными выходными параметрами и т.д.);
- определяют продолжительность каждого периода эксплуатации.
Перечень возможных отказов должен обладать достаточной полнотой, определяемой наличием наиболее вероятных и критичных (приводящих к наиболее тяжелым последствиям) отказов, но не может быть избыточным из-за включения в него зависимых отказов. Отказы, возникающие по одной и той же причине, могут быть объединены. При составлении перечня анализируют ограничения на условия применения системы, нарушения которых рассматривают как возможные отказы.
Упрощенно структуру «дерева отказов» можно изложить в следующем виде:
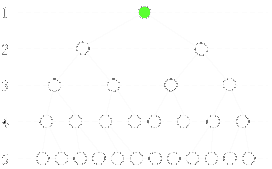
Рисунок 3.1 – Структура дерева отказов
Где
1) Отказ системы
2) Отказ составных частей
3) Отказ элементов
4) События, порождающие отказ
5) Виды воздействий
3.2 Практические методы
3.2.1 Методы снижения коррозионной деградации
Коррозия приводит ежегодно к миллиардным убыткам, и разрешение этой проблемы является важной задачей. Основной ущерб, причиняемый коррозией, заключается не в потере металла как такового, а в огромной стоимости изделий, разрушаемых коррозией. Вот почему ежегодные потери от неё в промышленно развитых странах столь велики. Истинные убытки от неё нельзя определить, оценив только прямые потери, к которым относятся стоимость разрушившейся конструкции, стоимость замены оборудования, затраты на мероприятия по защите от коррозии. Ещё больший ущерб составляют косвенные потери. Это простои оборудования при замене прокорродировавших деталей и узлов, утечка продуктов, нарушение технологических процессов.
Коррозия — это самопроизвольное разрушение металлов в результате химического или физико-химического взаимодействия с окружающей средой.
В зависимости от характера коррозионного процесса различают химическую и электрохимическую коррозию металлов.
При химической коррозии металл разрушается в агрессивных средах вследствие непосредственного соединения металла с агрессивными химическими агентами (например, железо окисляется).
При электрохимической коррозии разрушение металлов происходит вследствие их растворения в жидкой среде, являющейся электролитом, и заключается в образовании на их поверхности множества микрогальванических элементов.
Коррозия металлов может быть местная, при разрушении поверхности в определенных участках, и равномерная, когда металл разрушается по всей поверхности, а также межкристаллитная, когда разрушение происходит по границам зерен металла.
Прямые показатели коррозии
- убыль или увеличение массы, отнесенные к единице поверхности металла;
- глубина коррозии;
- доля поверхности, занятая продуктами коррозии;
- количество коррозионных язв или точек (очагов коррозии) на единице поверхности;
- объем выделившегося с единицы поверхности водорода или поглощенного кислорода;
- время до появления первого очага коррозии;
- время до появления коррозионной трещины или полного разрушения образца;
- сила тока коррозии;
Косвенные показатели коррозии
- изменение физико-механических свойств металла (предела прочности при испытаниях на сжатие и разрыв, относительного удлинения, отражательной способности и др.);
- изменение сопротивления;
Группа стойкости |
Глубинный показатель коррозии, мм/год |
Балл |
Совершенно стойкие |
0,001 | 1 |
Весьма стойкие |
0,001 ... 0,005 0,005 ... 0,010 |
2 3 |
Стойкие |
0,01 ... 0,05 0,05 ... 0,10 |
4 5 |
Пониженно стойкие |
0,1 ... 0,5 0,5 ... 1,0 |
6 7 |
Малостойкие |
1,0 ... 5,0 5,0 ... 10,0 |
8 9 |
Нестойкие |
10,0 | 10 |
Таблица 3.4 – Шкала грубой оценки коррозионной стойкости металлов
Существует несколько методов антикоррозионной защиты металлов. По механизму действия все методы антикоррозионной защиты можно разделить на две основные группы: электрохимические, оказывающие влияние на потенциал металла или его критические значения, и механические, изолирующие металл от воздействия окружающей среды созданием защитной пленки и покрытий.
К основным методам антикоррозионной защиты относятся:
- легирование металлов
- термообработка
- ингибирование окружающей среды
- деаэрация среды
- водоподготовка
- защитные покрытия
- создание микроклимата и защитной атмосферы.
Способы антикоррозионной защиты указываются в рабочих чертежах конструкций, в СНиП, технических условиях (ТУ). Простейшим и эффективным способом защиты металлических конструкций от коррозии является покрытие их поверхностей различными красками, лаками, эмалями.
Красочное покрытие, полимерное покрытие и эмалирование должны, прежде всего, предотвратить доступ кислорода и влаги. Часто также применяется покрытие, например, стали другими металлами, такими как цинк, олово, хром, никель. Цинковое покрытие защищает сталь даже когда покрытие частично разрушено. Цинк имеет более отрицательный потенциал и корродирует первым. Ионы Zn2+ токсичны. При изготовлении консервных банок применяют жесть, покрытую слоем олова. В отличие от оцинкованной жести, при разрушении слоя олова корродировать, притом усиленно, начинает железо, так как олово имеет более положительный потенциал.
Образующиеся на поверхности металлов окисные пленки разделяются на два вида: плотные и рыхлые. Плотные пленки окислов нарушают контакт окружающей среды с поверхностью металла и таким образом защищают последнюю от окисления. Рыхлые пленки не препятствуют окислению. Плотные пленки окислов образуются алюминием, свинцом, никелем, рыхлые окисные пленки — кальцием, магнием и др.
Современная химия дает возможность изготовлять высококачественные лакокрасочные материалы, обеспечивающие наряду с механической химическую (фосфатирующие грунты) и электрохимическую (протекторные грунты) защиту. Лакокрасочные материалы (по предъявляемым требованиям и свойствам входящих в их состав компонентов) различают: антикоррозионные, водостойкие — защищающие металл от коррозии в местах с высокой степенью влажности (ЭКЖС-40, ХС-78, грунты ВЛ-02, № 81,ФЛ-03Ж и др.); атмосферостойкие — защищающие от атмосферной коррозии (ПХВ-29, ПХВ-35, ХВ-124, ПФ-115, ХС-510 и др.); термостойкие — защищающие от коррозии поверхности металла, нагревающиеся свыше 100°С, и др.
Другая возможность защитить металл от коррозии — применение защитного электрода с большим отрицательным потенциалом, например, из цинка или магния. Для этого специально создаётся коррозионный элемент. Защищаемый металл выступает в роли катода, и этот вид защиты называют катодной защитой. Растворяемый электрод, называют, соответственно, анодом протекторной защиты. Этот метод применяют для защиты от коррозии морских судов, мостов, котельных установок, расположенных под землей труб. Для защиты корпуса судна на наружную сторону корпуса крепят цинковые пластинки.
3.2.2 Методы снижения образования отложений
Образующиеся на внутренней поверхности трубопроводов отложения являются продуктами сложных физико-химических процессов, происходящих на ней самой или на нанесённом защитном покрытии, а также в транспортируемой по трубопроводу среде.
Характер отложений в трубопроводах, как правило, определяется:
- физико-химическими свойствами транспортируемых сред;
- условиями эксплуатации сети;
- продолжительностью службы трубопроводов.
Предотвращение образования и удаление отложений, обусловленных жесткой водой или коррозионными процессами является актуальной задачей, что обусловлено следующими соображениями:
1. Наличие отложений значительно ухудшает теплообмен в теплообменных аппаратах, снижает пропускную способность трубопроводов. Теплопроводность отложений в зависимости от их состава в два и более раз меньше, чем теплопроводность конструкционных материалов;
2. Коррозионные повреждения поверхностей оборудования, в т.ч. запорно-регулирующей арматуры, существенно снижают их надежность работы и срок службы.
Солеотложение крайне негативно влияет на безопасность эксплуатации трубопроводов. Оно вызывает усиление локальной коррозии металла труб, что приводит к их ускоренному разрушению.
Механизм предотвращения образования отложений определяется отношением скорости протекания зародышеобразования кристаллов и ростом кристаллов. Термин «образование центров кристализации» относится к спонтанному формированию микроскопических частиц (микрокристаллитов) из растворенных ионов, например, кристаллитов карбоната кальция из растворенного кальция и карбонатных ионов. Эти крошечные кристаллы могут спонтанно распадаться или продолжать расти до определенного сверхкритического размера. При достижении этого размера они становятся макрокристаллами и переходят в устойчивое состояние. Распад прекращается, и постепенно формируются крупные кристаллические структуры, которые называют «отложениями».
Для того чтобы предметно и систематически решать проблемы, связанные с образованием отложений, рекомендуется придерживаться следующей процедуры:
Этап 1. Определить место образования отложений
Наиболее распространенные места образования отложений включают центрифуги и трубопроводы, а также насосы, теплообменники.
Этап 2. Определить тип отложений
Тип первичной очистки, выбор и дозирование продуктов зависят от типа отложений. Тип отложений может быть с достаточной степенью уверенности определен на месте с помощью несложных способов.
Соли углекислоты: образуются газовые пузырьки при обработке уксусной кислотой или лимонной кислотой.
Фосфаты: медленно растворяются в среднеконцентрированных неорганических кислотах или щелочах без образования пузырьков.
Окислы железа: определяются визуально, выглядят, как ржавчина. Более точное определение состава отложений возможно только в лабораторных условиях.
Этап 3. Выбрать оптимальный реагент
Оптимальный ингибитор образования отложений можно выбрать с помощью прибора P-MAC, используя для моделирования процесса образования отложений образец воды, взятый из места предполагаемого применения реагента. В случае очень высокого содержания железа достаточно эффективное ингибирование образования отложений может быть обеспечено применением полиакрилатов.
Этап 4. Определить точку ввода реагента
Общее правило:
Точка ввода реагента должна находиться как можно ближе к месту образования отложений, но при этом должен быть обеспечении равномерный ввод в смесь. С учетом химической природы ингибиторов образования отложений их эффективность может быть ослаблена под воздействием других веществ, содержащихся в воде. По этой причине не следует применять реагенты в жидкой фазе на большом удалении от места их непосредственного действия.
Этап 5. Выполнить первичную очистку
Реагенты, используемые для противодействия образованию минеральных отложений, не способны удалить отложения, которые уже присутствует. Поэтому перед началом использования реагента необходимо выполнить первичную очистку, для чего при необходимости можно привлечь квалифицированных специалистов специализированной организации.
Этап 6. Обеспечить дозирование и оперативный контроль
Определение доз продуктов для дозирования с помощью дозировочных насосов основывается на эмпирическом подборе или лабораторных рекомендациях. В большинстве случаев исходная доза соответствует концентрации 30 ppm. Эффективность действия реагента может быть проверена визуально, например, осмотром внутренней поверхности подверженных образованию отложений труб или отдельного трубопровода, специально установленного в контрольных целях.
Химическая очистка имеет ряд недостатков, основными из которых являются:
- Используемые реагенты имеют высокую токсичность, обладают высокой коррозионной активностью и являются едкими веществами;
- Необходимость утилизации больших объемов отработанных реагентов и их растворов. Расход моющих растворов составляет до 10% от объема теплоносителя – то есть примерно 1 м3 на 10м3 промываемого объема;
- Высокая вероятность повреждения конструкционных материалов оборудования вследствие высокой коррозионной активности промывочных растворов. Особенно это относится к таким конструкционным материалам как алюминий, бронза, черные металлы.
- Вероятность попадания агрессивных токсичных жидкостей в жилые и производственные помещения в случае появления течей;
- Необходимость отключения системы отопления при проведении промывки;
- Необходимость проведения дополнительных мероприятий по предотвращению коррозии оборудования после проведения промывки.
ВЫВОДЫ
В данной работе была описана система улавливания и транспортирования коксового газа, включающая в себя газосборник, сепаратор, первичный газовый холодильник с горизонтальными трубами, нагнетатель для коксового газа. Были проанализированы условия работы всех элементов системы улавливания и транспортирования коксового газа. Были исследованы процессы, происходящие в данном оборудовании.
В итоге из вышесказанного следуют такие выводы:
- Оборудование системы отвода и транспортирования коксового газа работает в тяжелых условиях (давление, температура, коррозионная среда).
- Такие условия работы приводят к интенсивному развитию деградационных процессов (коррозия, возникновение отложений, изменение свойств материала), снижающих надежность системы.
- Для обеспечения безопасной эксплуатации оборудования необходимо знать параметры его технического состояния в любой момент времени в процессе работы.
Используя вышеописанные методы мы можем рассчитать технические риски учитывая надежность и изменение технического состояния объекта. Ранее в подобных расчетах для коксохимического производства изменение технического состояния объекта не учитывалось. В предложенных же расчетах будет видно влияние отложений и деградационных процессов на надежность.
Для повышения надежности и безопасности предложено выполнять вероятностный расчет, который заключается в определении вероятности безотказной работы системы, в которой учитываются множество факторов. Однако, в связи с тем, что факторы определяющие прочность элементов и действующие нагрузки являются вероятностными, они представлены в виде интервала значений. С использованием данного метода появляется возможность:
- Прогнозирования изменения технического состояния оборудования для улавливания и транспортирования коксового газа с заданной вероятностью;
- Принимать для ответственного оборудования допустимыми наиболее опасные сочетания факторов, а для менее ответственных такой точностью можно пренебречь.
Для определения этих величин были произведены экспериментальные исследования свойств деталей особо сильно подверженных деградации, таких как футеровочный кирпич из газового стояка и образцы металла с разных участков технологического пути движения газа.
При написании данного реферата магистерская работа, в частности расчетная ее часть, еще не завершена. Окончательное завершение: декабрь 2014 года. Полный текст работы и материалы по теме могут быть получены у автора или его руководителя после указанной даты.
Список источников
- Коляндр Л.Я. Улавливание и переработка химических продуктов коксования. – Харьков, 1962. 22с.
- Коробчанский И.Е., Кузнецов М.Д. Расчеты аппаратуры для улавливания химических продуктов коксования. Харьков. Металлургия, 1952. - 55с.
- Александров К.И. Газодувки. - М.: Энергия, 1961. – 79с.
- Лебедев А.А., Ковальчук Б.И. Справочное пособие по расчету машиностроительных конструкций на прочность. – К., 1990. – 240с.
- Ковалев Г.М. Нагнетатели коксового газа. М.: Металлургия, 1972.–190с.
- Соколов Ю.Н. Основы единой теории лопастных машин. – Томск, 1973. – 218с.
- Юдин Е.М. Шестеренные насосы. – М.: Машиностроение, 1964. – 75с.
- Бондаренко М.С., Иванченко В.В. Справочник механика химических производств. – Донецк: Донбасс, 1988. - 208с.
- Хенли Э. Джм Кумамото X., Надежность технических систем и оценка риска: — М.: Машиностроение, 1984.
- Капур К., Ламберсон Л. Надежность и проектирование систем. – Москва, 1980.