Реферат за темою випускної роботи
Зміст
- Вступ
- 1. Проблема забезпечення надійності та безпеки хімічного обладнання
- 1.1. Актуальність проблеми
- 1.2. Технологічна схема вловлювання та транспортування коксового газу
- 2. Аналіз конструкції та принцип роботи обладнання системи
- 2.1. Коксові печі
- 2.2. Газовий стояк та газосбірник
- 2.3. Сепаратор
- 2.4. Первинний газовий холодильник
- 2.5. Нагнітач
- 2.6. Аналіз основных процесів, що протікають в обладнанні
- 2.7. Аналіз деградаційних процесів
- 2.8 Постановка задач дослідження
- 3. Методи забезпечення техногенної безпеки хімічного обладнання
- 3.1 Теоретичні основи розрахунку техногенної безпеки
- 3.1.1 Аналіз граничних станів в зоні уловлювання та транспортування коксового газу
- 3.1.2 Аналіз технічних ризиків в зоні відводу та вловлювання коксового газу
- 3.1.3 Аналіз надійності системи вловлювання та очищення коксового газу методом дерева відмов
- 3.2 Практичні методи
- 3.2.1 Методи зниження коррозійної деградации
- 3.2.2 Методы зниження утворення відкладень
- Висновки
- Перелік посилань
ВСТУП
У печах в процесі коксування утворюється кокс і хімічні продукти, що виділяються у вигляді вельми складної суміші парів і газів, яку називають коксовим газом. P>
Коксовий газ є цінною сировиною, з якої отримують смолу, аміак, ціаністий водень, сірководень, нафталін, бензол та ін. P>
В обладнанні систем вловлювання та транспортування коксового газу відбуваються різні технологічні процеси. Такі як переміщення газу, його охолодження, конденсація вологи з нього. При цьому протікають такі деградаційні процеси:
- Корозія внутрішніх поверхонь, що контактують з речовиною
- Утворення відкладень на стінках трубопроводів внаслідок конденсації, зміна властивості цегли, і як наслідок, зношування футеровальної цегли через насичення її речовинами з газопроводу.
Ці деградаційні процеси мають визначальний вплив на технічний стан обладнання.
В даній роботі розглянуто обладнання системи вловлювання та транспортування коксового газу, виконані матеріальний і теплою розрахунки цього обладнання, розглянуті основні деградаційні процеси і способи боротьби з ними. Запропоновано метод розрахунку технічного стану коксохімічного устаткування, що дозволяє врахувати деградацію обладнання, а також зміни обладнання в процесі роботи.
1 ПРОБЛЕМА ЗАБЕЗПЕЧЕННЯ НАДІЙНОСТІ ТА БЕЗПЕКИ ХІМІЧНОГО ОБЛАДНАННЯ
1.1 Актуальність проблеми
У коксовому газі міститься значна кількість парів смоли, що забарвлюють його в темно-бурий або коричневий колір.
Коксовий газ, що виділяється, з печей називається прямим і містить водяної пари 250-450м3, смоляних парів 80-120м3, бензольних вуглеводнів 30-40м3, аміаку 8-13м3, сірководню 6-30м3, ціанистих сполук 0,5-1,5 м3.
Окрім того, у газі міститься невелика кількість легких піридинових основ (0,4-0,6 г/м3), нафталін (до 10 г/м3), різні сіркоорганічні (сірковуглець CS2, оксисульфід вуглецю COS, тіофен C4H4S та інші) (2-2,5 г/м3) і інші з'єднання.
Після отримання коксового газу в пічах його необхідно вловити та віконати над ним ряд операцій: охолодження, конденсація смоли, транспортування. Для цього використовуються системи вловлювання та транспортування газу, яка складається зі стояка, газосбірника, газопроводу, сепаратора, первинного газового холодильника, газодувки (далі обладнання).
З коксової камери горячий газ (t = 600—650°C) відводиться через стояк, який чавунним коліном з'єднанний з газопроводом, розташованим уздовж коксової батареї. У стояк через форсунки подається барільетна вода з температурою 80°C, яка охолоджує і зволожує газ. Потім газ потрапляє в сепаратор. Там волога зі смолою конденсується і подається в механізований освітлювач, де очищають барільетну (надсмоляну) воду.
Після цього охолоджений до температури в 85°C газ проходить через кінцевий газовий холодильник, ще раз охолоджуючись оборотною водою до 35°C. У такому вигляді коксовий газ подається до газодувки. Обсяг одержуваного прямого коксового газу для всієї батареї становить 37 тыс. м3/ч.
Коксовий газ має багатий склад, містить корозійно-активні речовини і має високу температуру. Він має визначальний вплив на обладнання. Це призводить до відносно невисокої його надійності і довговічності.
Наприклад, термін служби стояків 10 років, капітальний ремонт проводять через 5 років, при цьому заміна футеровки виконується з періодичністю в 9 місяців, очищення від відкладень 1 раз на тиждень.
Проблема надійності обладнання систем уловлювання та транспортування коксового газу носить особливо важливий характер, тому що при його деградації виникають відмови, руйнування і як наслідок відбуваються дуже серйозні для навколишнього середовища викиди, вибухи, пожежі, за якими йдуть великі витрати.
В обладнанні систем уловлювання та транспортування коксового газу відбуваються різні технологічні процеси. Такі як переміщення газу, його охолодження, конденсація вологи з нього. При цьому протікають такі деградаційні процеси:
- корозія внутрішніх поверхонь, що стикаються з речовиною,
- утворення відкладень на стінках трубопроводів внаслідок конденсації, зміна властивості цегли, і як наслідок, зношування футеровки через насичення її речовинами з газопроводу.
Наприклад, відкладення, осаждающиеся на стінках газопроводу, призводять до таких наслідків:
- Зменшується перетин труб;
- Збільшується тиск;
- Підвищуються витрати на енергію;
- Змінюється гідравлічний режим руху речовини по трубах;
- Змінюється шорсткість стінок трубопроводу;
- Погіршується теплопередача;
- Через корозію зменшується міцність трубопроводу.
У кожен момент часу властивості обладнання та його технічні характеристики піддаються змінам. Тобто замість вихідного обладнання маємо дещо інше, з дещо іншими властивостями.
Звідси витікає, що на етапі проектування необхідний прогноз технічного стану або зміни параметрів в задані моменти часу. Що можливо виконати на основі моделювання зміни технічного стану обладнання.
Однак на практиці отримати точні дані про вплив всіх цих процесів дуже складно: швидкість корозії на різних ділянках обладнання різна, кількість відкладень також відрізняється, фізико-механічні властивості змінюються по-різному. Тобто всі процеси, що відбуваються з обладнанням, мають імовірнісний характер і всі властивості, як обладнання, так і технологічних і деградаційних процесів (розміри, шорсткість, фізико-механічні властивості, температура, тиск, швидкість корозії тощо) необхідно описувати математичним очікуванням і дисперсією.
Для визначення ймовірності відмов системи необхідно враховувати безліч чинників. Однак ці фактори, що визначають технічний стан, є імовірнісними, то вони представлені у вигляді інтервалу значень, і результати розрахунків також будуть імовірнісними. Використання такого підходу дозволить значно підвищити точність визначення показників надійності в кілька разів.
Таким чином, імовірнісні розрахунки при проектуванні є конструктивним способом отримання кількісних оцінок робочих характеристик надійності виробу на різних етапах експлуатації вже при проектуванні. Оскільки при такому підході робочі характеристики виробу виражаються через статистичні показники, це допомагає конструктору оцінювати витрати на гарантійне обслуговування, розробляти програми технічного обслуговування і планувати рух запасів.
1.2 Технологічна схема вловлювання та транспортування коксового газу
При нагріванні вугілля без доступу повітря до температури 900-1100°C в камерах коксових печей з нього виділяються летючі продукти коксування. З камер коксових печей летючі продукти коксування по стояках виходять в газозбірники 1 (малюнок 1.1). Температура газів в стояку 750-800°C.
При охолодженні газу відбувається часткова конденсація смоли і випадіння дрібних частин кам'яного вугілля, віднесених газом з печей.
За рахунок випаровування частини надсмольної води (близько 2-3% від подається), коксовий газ охолоджується до 80-85°C, при цьому, у вигляді туману, з нього конденсується велика частина смоли (65-80% від тієї, яка міститься в коксовому газі). Під напором надсмольної води (тиск на газозбірники не нижче 3кг/см2), яка подається через форсунки безпосередньо в газозбірник, сконденсувалася смола і фуси змиваються з днища останнього і відводяться з машинною боку коксової батареї через два переточні ящика в газопроводи коксового газу.
У відділенні конденсації і первинного охолодження коксового газу роблять такі технологічні операції:
- первинне охолодження коксового газу;
- очищення надсмольної води від смоли і фусів;
- очищення смоли від води і фусів;
- очищення охолодженого коксового газу від смоли;
- відсмоктування коксового газу з коксових батарей і транспортування його через апарати уловлювання.
Охолоджений коксовий газ, пари води і частина туманообразной смоли, а також надсмоляна вода, яка стікає з переточних ящиків по газопроводу, направляється в газовий сепаратор 2, де відбувається поділ рідкої і газоподібної фази. Рідка частина з газового сепаратора 2 відводиться в механізовані освітлювачі 10. Газова частина, прямий коксовий газ, направляється під дією газодувки 8 до трубчастих газових холодильників 3.
Охолодження коксового газу виробляється в трубчастих газових холодильниках 3. Для охолодження газу встановлено 14 трубчастих газових холодильників. Верхні дві секції ПГХ зрошуються поглинає розчином цеху сіркоочищення. Інші секції холодильників охолоджуються оборотної технічною водою, яка подається з насосної технічної води цеху водопостачання.
Конденсат газу з холодильників 3 через гідрозатвори відводиться в збірники 13, звідки насосами перекачується в механізовані освітлювачі і частково у відстійник 18.
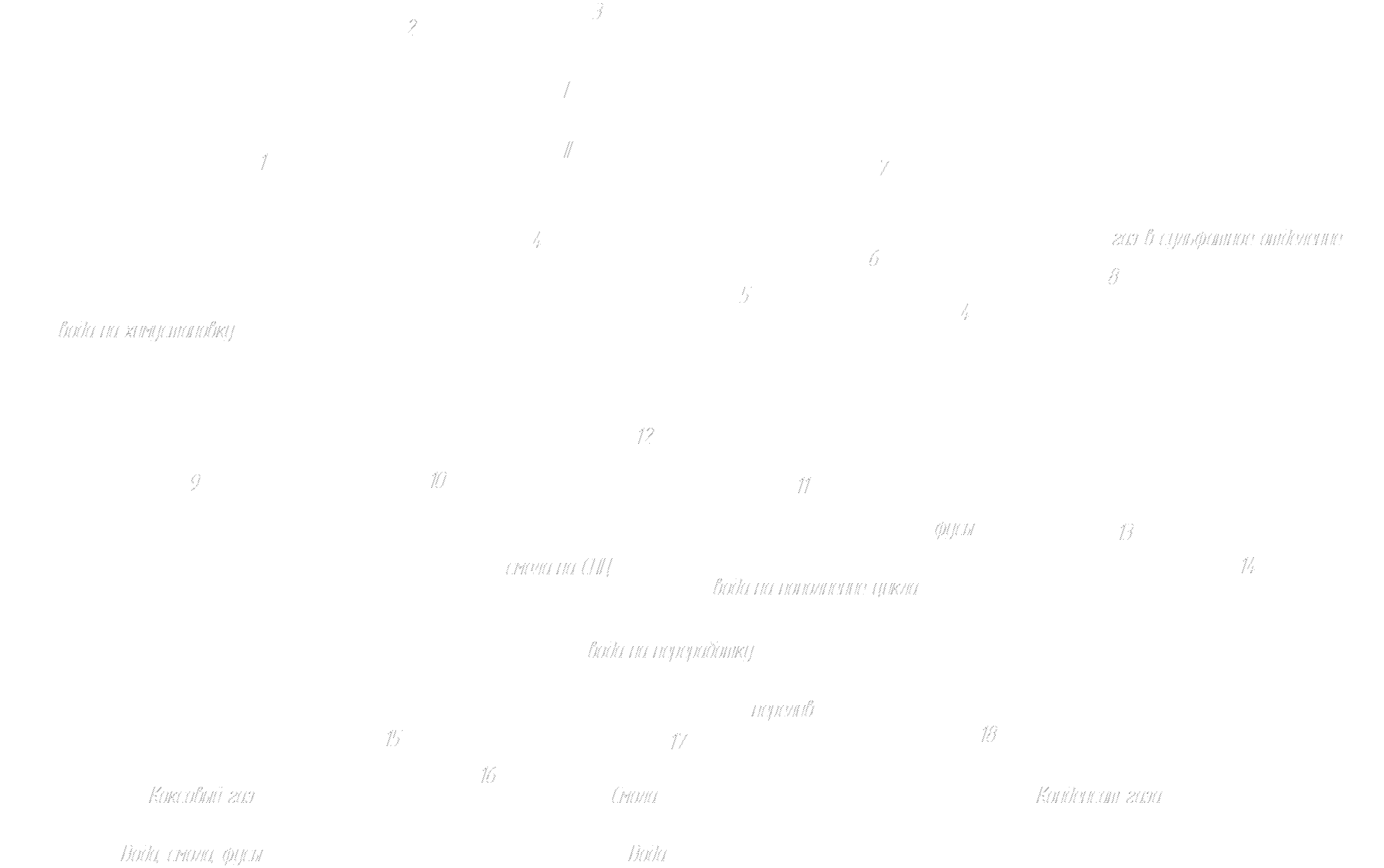
Малюнок 1.1 - Технологічна схема транспортування коксового газу
Для відсмоктування коксового газу з газозбірників коксових батарей встановлено чотири газових нагнітача типу 1200-27-2, продуктивністю 72000 м3/ч.
У результаті стиску газу в нагнітачі виділяється тепло , що підвищує температуру газу на виході до 55-65°С.
Кожен нагнітач обладнаний стопорними засувками на всмоктуючому 1 і нагнітальному 2 газопроводі, пусковим байпасом 3 і дросельною заслінкою 4 на всмоктуючому газопроводі. Байпас діаметром 800 мм служить для грубого регулювання продуктивності нагнітача в результаті пропускання газу з нагнітального трубопроводу в газопровід перед трубчастими газовими холодильниками. Автоматична регуляція відсмоктування відбувається за допомогою дросельної заслінки на всмоктуванні нагнітача.
2 Аналіз конструкції та принцип роботи обладнання системи
2.1 Коксові печі
Сучасні печі для коксування вугілля являють собою горизонтальні прямокутні камери, викладені з вогнетривкого матеріалу. Камери печей обігріваються через бічні стіни. Печі розташовуються в ряд і об'єднуються в батареї для зменшення втрати тепла і досягнення компактності. У типову батарею печей з шириною камер 410 мм входять зазвичай 65 печей, а в батарею великої ємності з камерами шириною 450 мм входять 77 печей. Звичайні камери мають корисний об'єм 20-21,6 м3, а печі великої ємності - 30 м3. Ширина печей більше 450 мм недоцільна через погіршення якості коксу (підвищення стиранням). Для полегшення виштовхування коксу з камери коксування ширину камери з боку видачі коксу роблять на 40-50 мм ширше, ніж з машинною сторони. Таким чином, камера має вигляд конуса. За основні елементи батареї треба прийняти наступні: фундамент, регенератори, корнюрную зону, зону обігрівальних простінків, перекриття простінків і перекриття камер.
Перетворення вугільної шихти в кокс є хімічним процесом, що проходить без доступу повітря. Цей процес характеризується складними хімічними, фізичними та фізико-хімічними перетвореннями при термічній деструкції вугільного завантаження на окремих стадіях процесу коксоутворення.
2.2 Газовий стояк та газозбірник
Стояк (рисунок 2.2) складається з вертикальної труби 2, трійника 3, кришки 5, коліна 9, клапанної коробки 16 з тарілчастим клапаном 14, форсунки 8 для подачі надсмольной води на зрошення газу, форсунки (встановлюється в отвір 4) для пароінжекціі при бездимної завантаженні і важелів для управління кришкою і клапаном.
Сталева труба 2 встановлюється в гніздо 1, утворене в кладці печі над газовідвідним люком. Після установки труби гніздо ущільнюється азбестовим шнуром і шамотним розчином. Усередині труба футерована шамотним цеглою. Товщина футеровки 60 - 65 мм. Для захисту обслуговуючого персоналу від опіків, сторона труби, обернена в бік шляхів углезагрузочная вагона, закривається сталевим щитом. Поверхня щитка, звернена до труби, покривається листовим азбестом.
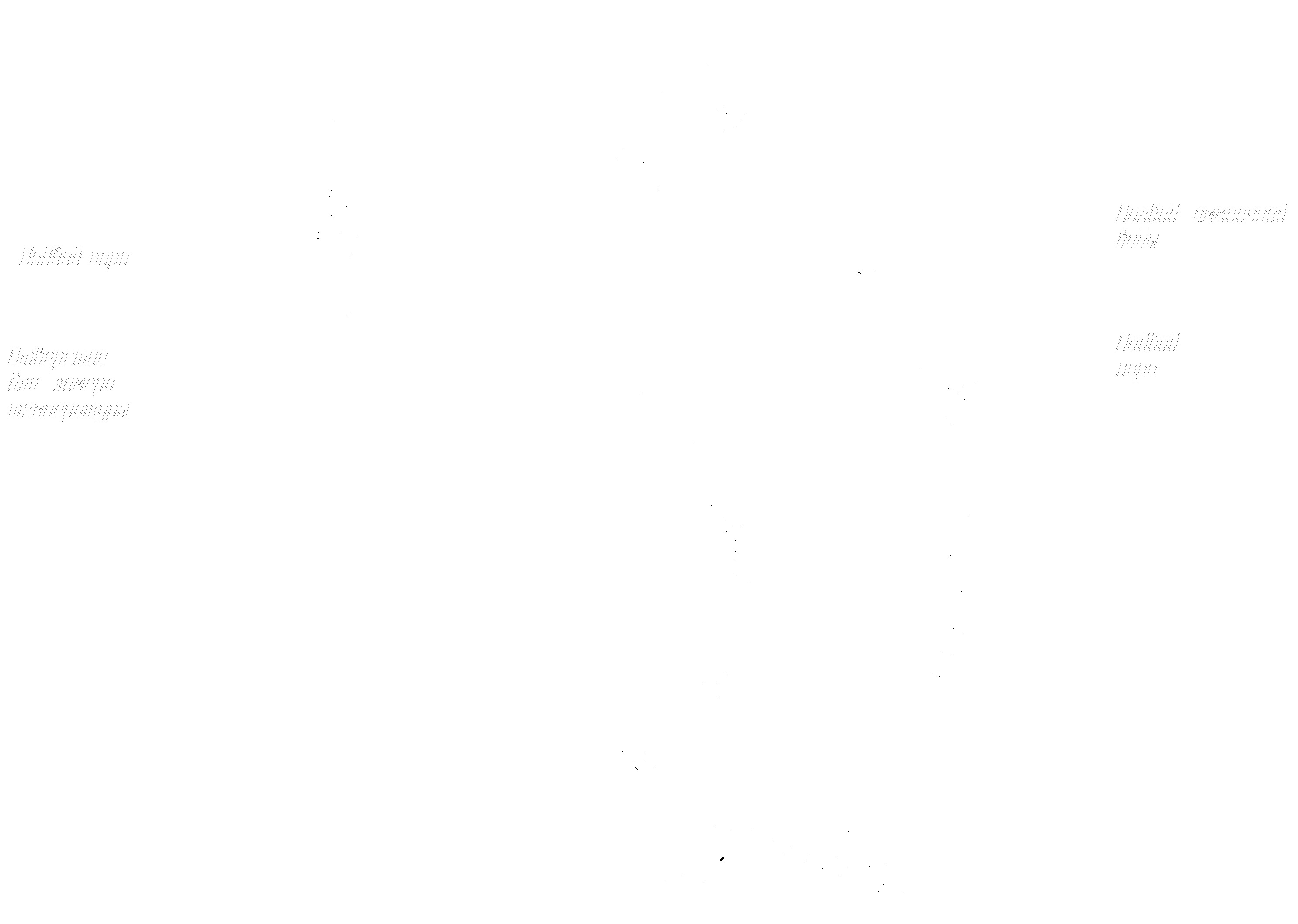
Малюнок 2.1 - Стояк для відводу газу з коксової печі
Трійник 3 із закріпленим на ньому коліном 9, приєднується до труби фланцем. Зверху трійник закривається кришкою 6. Між кришкою і знімним фланцем 5 трійника мається ущільнення типу «залізо по залізу», при якому вістря кришки встановлюється на оброблену поверхню знімного фланця.
Клапанна коробка 16 приєднана фланцем до газосборніку13. У клапанної коробці розміщений вал 17, на якому монтується тарільчасте клапан 14. При закриванні клапан повертається до зіткнення з конічним сідлом 15. Вода, що подається на зрошення, заповнює тарілку клапана так, що конус виявляється зануреним в рідину. При цьому утворюється гідрозатвор, що відключає стояк від газозбірника. Висота гідрозатвори 40 мм. Закривання клапана проводиться перед видачею коксу. При коксуванні клапан відкритий, і газ з камери коксування надходить в газозбірник. При проходженні по стояку газ охолоджується при безпосередньому контакті з водою, розбризкується форсункою 8, встановленої на коліні. Тиск води перед форсункою 0,3-0,35 МПа.
Форсунку зрошення сирого коксового газу встановлюють таким чином, щоб конус розпилення аміачною водою перекривав всі перетин потоку газу і при цьому, вода не могла потрапити в коксову камеру. Аміачна вода для зрошення газу в стояку служить гідрозатворів при закритті клапанної коробки, за допомогою якої коліно стояка з'єднується з газосборником.
Трійники, коліна і клапанні коробки виготовляють з (чавуну марки СЧ 21 - 40; кришки стояків і клапани - зі сталі.
З стояка через коліно і клапанну коробку продукти коксування проходять в газозбірники - сталеві труби, діаметром 1100 - 1600 мм, розташовані з машинного й коксової сторони батареї, або тільки з машинною.
Коліно і корпус стояка обладнані системою важеля, за допомогою якої приводиться в рух кришка і клапан. Обидві кінематичні ланцюги наводяться до дії одним важелем, або гідроприводом.
2.3 Сепаратор
За принципом роботи сепаратор відноситься до інерційним відцентровим апаратам вихрового типу. Поділ газорідинного потоку на складові в апараті відбувається під дією відцентрових сил, спрямованих радіально по відношенню до вертикальної осі сепаратора. Величина відцентрової сили, що діє на краплю вологи або частинку механічних домішок залежить від швидкості потоку на вході в сепаратор, щільності крапельки (її ваги) і радіусу апарату. Чим менше радіус апарату, тим більше виникає відцентрова сила.
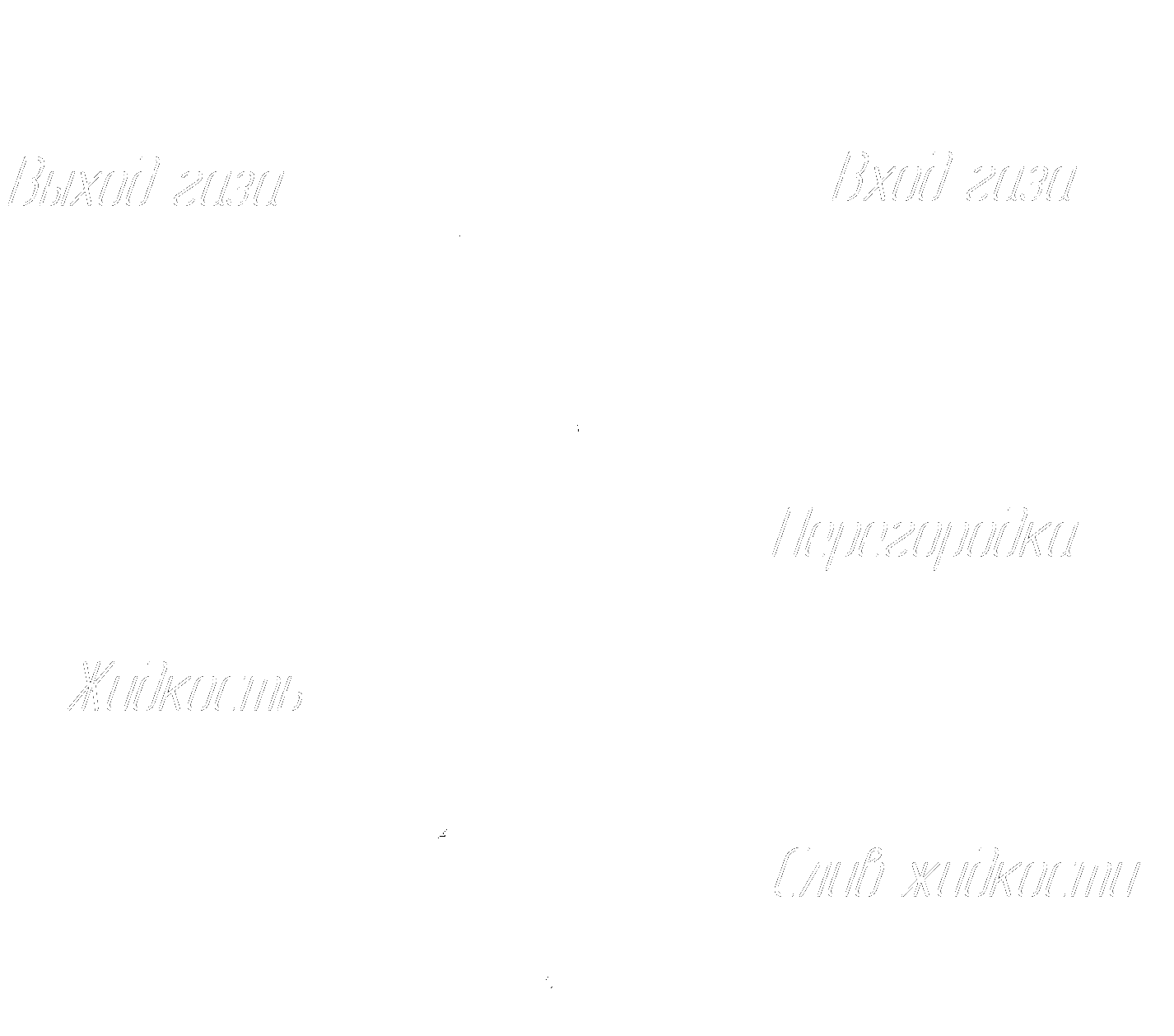
Малюнок 2.2 – Газовий сепаратор
Сепаратор містить в своїй конструкції 7 ступенів сепарації, водночас можуть бути конструктивними елементами, призначеними для розділення газорідинного потоку.
Сепаратор працює таким чином. Газорідинний потік надходить у сепаратор через вхідний газовий патрубок 11, де набуває обертальний рух навколо вертикальної осі сепаратора завдяки конструкції дефлектора 5. Обертаючись навколо вертикальної осі, рідина і механічні домішки, під дією відцентрових сил відокремлюються від газорідинного потоку і притискаються до корпусу сепаратора 4. Тут відбувається відділення приблизно 80% рідини і механічних домішок від газового потоку.
Далі газорідинний потік надходить через зазори сепарационного пакета 6 у внутрішню порожнину сепарационного пакета, продовжуючи обертання навколо вертикальної осі сепаратора, направляється у вихідний газовий патрубок 2. В сепараційному пакеті відбувається повне очищення газового потоку від краплинної вологи і механічних домішок.
Відокремлена рідина і механічні домішки під дією сили гравітації стікають по стінках корпусу сепаратора і по пластинах сепарационного пакета вниз до зливного патрубку 8.
2.4 Первинний газовий холодильник
Для первинного охолодження газу встановлюються горизонтальні трубчасті холодильники системи Гипрококсу (рис.1.6) поверхнею охолодження 2100 м2. Продуктивність цього холодильника по газу дорівнює 10-11 тис. м3/год газу, приведеного до нормальних умов.
Газ рухається в міжтрубному просторі, охолоджуюча вода - в трубах. Так як коефіцієнт теплопередачі зростає із збільшенням швидкості руху газу і води, то для збільшення цих швидкостей холодильник розділений вертикальними перегородками на шість секцій.
Холодильник по висоті розділений трьома горизонтальними перегородками, що утворюють нижню камеру для води, середню - камеру охолодження, заповнену трубами, і верхню камеру для переливу води.
Газ вступає в межтрубний простір камери охолодження і послідовно проходить з однієї секції в іншу. Вода надходить у нижню камеру, розділену також на секції, і піднімається по трубах шостий по ходу газу секції (перша по ходу води) вгору, потім зливається по трубах вниз і т. д. Таким чином, у всіх шести секціях дотриманий повний протитечія руху газу і води.
Для підтримки постійної швидкості руху газу та води і, отже, сталості коефіцієнта теплопередачі від газу до води секції, по яких рухається газ, мають змінне перетин: найбільша у першому по ходу газу секції і найменше у останньої по ходу газу секції. Для води, що рухається в протиточному напрямку, найменший переріз труб в першому по ходу води секції і найбільшу в місці виходу її з холодильника. Дуже важливим фактором, значною мірою визначає ефективність роботи трубчастих холодильників, є швидкість газового потоку. Вона, звісно, буде тим вище, чим більше навантаження холодильника по газу. Тому краще охолодження газу при меншій витраті охолоджуючої води виходить при послідовному проходженні газу через ряд з'єднаних один з одним холодильників. Однак при цьому різко зростає опір газовому потоку, тобто різниця розрідження газу до і після холодильників збільшується.
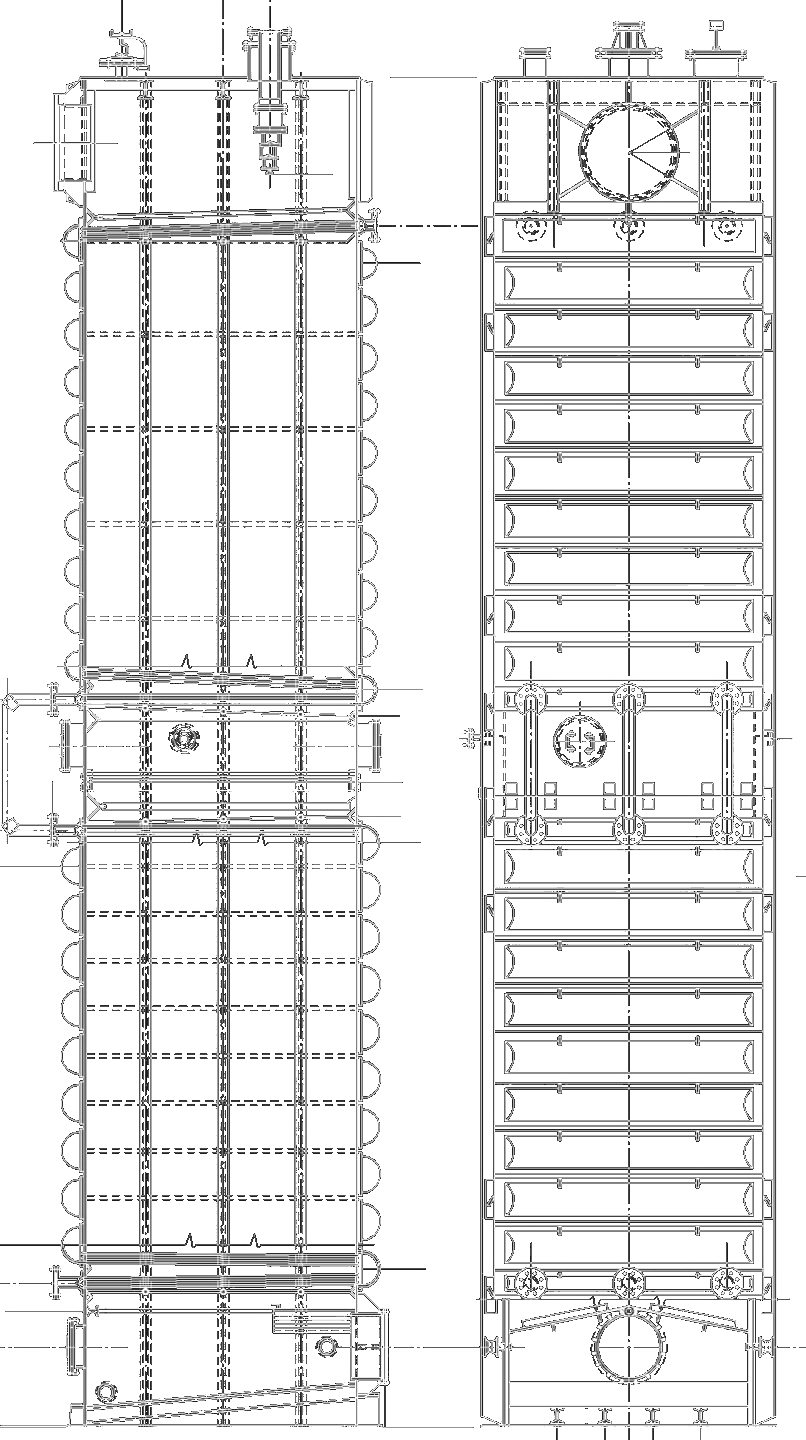
Малюнок 2.3 – Схема газового холодильника
2.5 Нагнітач
Призначення нагнітачів - відсмоктування коксового газу з коксових печей, транспортування його через апаратуру цеху уловлювання та подача після цього споживачам.
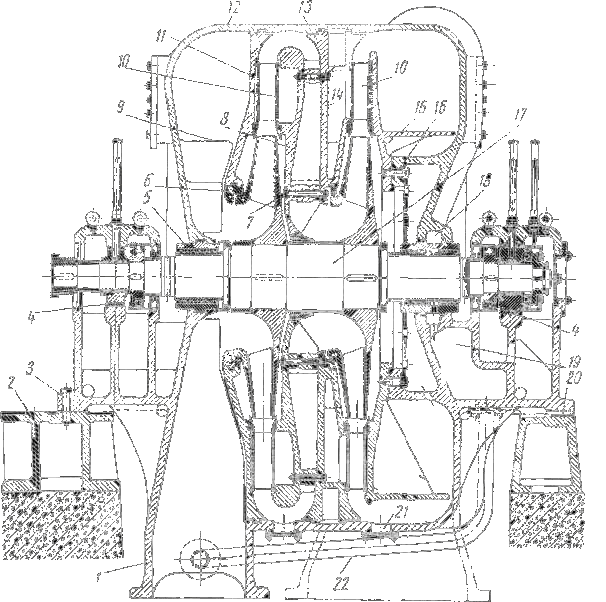
Рисунок 2.4 - Поздовжній розріз нагнітача
Нагнітачі газу розташовуються в машинному відділенні цеху уловлювання. Найчастіше вони встановлюються після первинних газових холодильників. Газопровід та апаратура, розташовані до нагнітача, знаходяться під розрідженням, а після нагнітача - під тиском.
Газ з коксових батарей, з'єднаних попарно, через первинні холодильники надходить у загальний колектор, розташований перед машинним відділенням. З колектора двома нагнітачами газ подається в газопровід, що йде до відділень цеху уловлювання.
По шляху проходження коксовий газ відчуває опір ділянок газопроводів і апаратури, яке викликає зміну тиску газу на окремих ділянках газової траси.
На сучасних коксохімічних заводах застосовують нагнітачі відцентрового типу, що приводяться в рух паровою турбіною (3000-5000 об / хв) або від тихохідного високовольтного електродвигуна (1450 об / хв) через зубчастий редуктор, що збільшує швидкість обертання до 3000-5000 об / хв.
На випадок можливих перебоїв в подачі електроенергії один або два нагнітача (з трьох) повинні мати привід від парової турбіни. Як правило, в роботі знаходиться один нагнітач з електроприводом і один з турбоприводів.
Нагрівання газу в нагнітачах залежно від ступеня стиснення коливається в межах 10-15°С. Тому коксовий газ після нагнітачів має температуру 35-45°С
2.6 Аналіз основних процесів, що протікають в обладнанні
У печах в процесі коксування утворюється кокс і хімічні продукти, що виділяються у вигляді вельми складної суміші парів і газів, яку називають коксівним газом.
Коксовий газ є цінною сировиною, з якого отримують смолу, аміак, ціаністий водень, сірководень, нафталін, сирої бензол та ін.
У коксовому газі міститься значна кількість парів смоли забарвлює його в темно-бурий або коричневий колір.
Коксовий газ, що виділяється з печей називається прямим і містить водяної пари 250-450 м3, смоляних парів 80-120 м3, бензольних вуглеводнів 30-40 м3, аміаку 8-13 м3, сірководню 6-30 м3 , ціаністих сполук 0,5-1,5 м 3.
З коксової камери гарячий газ (t = 600-650°C) відводиться через стояк, який чавунним коліном з'єднаний з газосборником, розташованим уздовж коксової батареї. У стояк через форсунки подається барільетная вода з температурою 80°C, охолоджуюча і зволожуюча газ. Потім газ потрапляє в сепаратор. Там волога зі смолою конденсується і подається в механізований освітлювач, де очищають барільетную (надсмольная) воду.
Взаємодія газу і охолоджуючої води в газозбірнику супроводжується процесами тепло-і масообміну.
Процес теплообміну визначається різницею температур газу і води. Так як температура газу вище температури орошающей води, то тепло передається від газу до води, і він охолоджується.
Рушійною силою другого процесу - масообміну є різниця між пружністю парів води при її температурі і парціальним тиском водяної пари в газі. Так як пружність водяної пари над надходить водою більше, ніж парціальний тиск їх в газі, що надходить з камер коксових печей, то відбувається випаровування води.
Отже, тепло Qг, що віддається газом, частково переходить до образующемуся пару, змішує з газовим потоком, а інше тепло охолодження газу Qг - Q SPAN>п йде на нагрів води.
Під час охолодження газу та нагріву води різниця температур між ними буде зменшуватися, а разом з тим буде зменшуватися і кількість переданого тепла від газу до води. Зрозуміло, що настане момент, коли величина Qг стане рівною Qі, після чого подальше нагрівання води стане неможливим, а все тепло, що отримується водою від газу, піде на її випаровування при постійній температурі. Межі охолодження газу відповідатиме температура мокрого термометра.
Потім газ потрапляє в сепаратор, де відбувається відділення рідкої фази і газу. У такому вигляді коксовий газ подається в газодувки, вона ж нагнітач. Обсяг одержуваного прямого коксового газу для всієї батареї становить 37 тис. м3/ч. У нагнітачах відбувається часткове виділення туманообразной смоли з газу до вмісту 0.2-0.5 г/м3. Виділилася в нагнітачах смола стікає через спеціальні спускні лінії в гідравлічний затвор. Внаслідок стиснення газу в нагнітачах виділяється тепло, яке підвищує температуру газу, що виходить. Деяка частина тепла втрачається через корпус, але вона дуже мала в порівнянні з загальною кількістю тепла, що виділяється. Після нагнітачів температура газу підвищується зазвичай на 15-25°С.
2.7 Аналіз деградаційних процесів
Коксовий газ має широкий склад, містить корозійно-активні речовини і має високу температуру. Він має визначальний вплив на обладнання. Це призводить до відносно невисокої його надійності і довговічності.
В обладнанні систем уловлювання та транспортування коксового газу відбуваються різні технологічні процеси. Такі як переміщення газу, його охолодження, конденсація вологи з нього. При цьому протікають такі деградаційні процеси:
- корозія внутрішніх поверхонь дотичних з речовиною
- утворення відкладень на стінках трубопроводів внаслідок конденсації
- зміна властивості цегли і, як наслідок, зношування футеровки через насичення його речовинами з газопроводу.
Ці деградаційні процеси мають визначальний вплив на технічний стан обладнання.
Наприклад, відкладення, що відкладаються на стінках газозбірника, призводять до таких наслідків:
- зменшується переріз труб;
- збільшується тиск;
- підвищуються витрати на енергію;
- змінюється гідравлічний режим руху речовини по трубах;
- змінюється шорсткість стінок трубопроводу;
- погіршується теплопередача;
- через корозію зменшується міцність трубопроводу.
У первинному газовому холодильнику спостерігаються подібні проблеми:
- через взаємодію металевих конструкцій з киснем повітря і впливу агресивних робочих середовищ розвивається корозія металоконструкцій;
- через тертя рідини, що містить абразивні частинки, при русі потоку, об метал зношується поверхню ПГХ, а точніше кришки трубних решіток та перехідні коліна;
- при нагріванні технічної води вище допустимого рівня на внутрішній поверхні труб утворюються солі жорсткості (накип);
- процес адгезії - тяжіння рідких або твердих тіл при їх молекулярному контакті, для порушення якого необхідно зовнішній вплив виникає, в тих випадках, коли при охолодженні компоненти газу конденсуються на зовнішніх поверхнях труб.
2.8 Постановка задач дослідження
У кожен момент часу властивості обладнання та його технічні характеристики піддаються змінам. Тобто замість вихідного обладнання маємо дещо інше, з дещо іншими властивостями.
Звідси витікає, що на етапі проектування необхідний прогноз технічного стану або зміни параметрів в задані моменти часу. Що можливо виконати на основі моделювання зміни технічного стану обладнання.
Однак на практиці отримати точні дані про вплив всіх цих процесів дуже складно: швидкість корозії на різних ділянках обладнання різна , кількість відкладень також відрізняється , фізико -механічні властивості змінюються по- різному. Тобто всі процеси , що відбуваються з обладнанням , мають імовірнісний характер і всі властивості , як обладнання, так і технологічних і деградаційних процесів (розміри , шорсткість , фізико -механічні властивості , температура , тиск , швидкість корозії тощо) необхідно описувати математичним очікуванням і дисперсією.
Для визначення ймовірності відмов системи необхідно враховувати безліч чинників. Однак ці фактори, що визначають технічний стан, є імовірнісними, тобто вони представлені у вигляді інтервалу значень, і результати розрахунків також будуть імовірнісними. Використання такого підходу дозволить значно підвищити точність визначення показників надійності в кілька разів.
Таким чином, імовірнісні розрахунки при проектуванні є конструктивним способом отримання кількісних оцінок робочих характеристик надійності виробу на різних етапах експлуатації вже при проектування. Оскільки при такому підході робочі характеристики виробу виражаються через статистичні показники, це допомагає конструктору оцінювати витрати на гарантійне обслуговування, розробляти програми технічного обслуговування і планувати рух запасів. разів.
3 МЕТОДИ ЗАБЕЗПЕЧЕННЯ ТЕХНОГЕННОЇ БЕЗПЕКИ ХІМІЧНОГО ОБЛАДНАННЯ
Як встановлено з розділу 1, обладнання під впливом агресивних середовищ неухильно деградує. І, на жаль, зупинити цей процес повністю неможливо. Однак існують різні методи для зменшення інтенсивності деградаційного впливу на конкретні об'єкти.
3.1 Теоретичні основи розрахунку техногенної безпеки
3.1.1 Аналіз граничних станів в зоні уловлювання та транспортування коксового газу
Метою методу є не допускати з певною ймовірністю настання граничних станів при експлуатації протягом усього заданого терміну служби устаткування, а також при виробництві робіт.
Граничний стан - стани, при яких конструкції перестають задовольняти заданим експлуатаційним вимогам або вимогам при виробництві робіт.
У розрахунках обладнання на дію статичних і динамічних навантажень і впливів, яким вони можуть піддаватися в процесі експлуатації і заданого терміну служби, враховуються такі граничні стани першої та другої групи.
До першої групи відносяться:
- загальна втрата стійкості форми;
- втрата стійкості положення;
- руйнування будь-якого характеру;
- перехід конструкції в змінювану систему;
- якісна зміна конфігурації;
- стану, при яких виникає необхідність припинення - експлуатації в результаті плинності матеріалу і т.д.
До другої групи належать стани, що утруднюють нормальну експлуатацію або знижують довговічність внаслідок появи неприпустимих переміщень (прогинів, осад, кутів повороту, коливань, тріщин і т.п.).
Граничні стани першої групи перевіряються розрахунком на максимальні (розрахункові) навантаження і впливи, можливі при порушенні нормальної експлуатації, а граничні стани другої групи - на експлуатаційні (нормативні) навантаження і впливи, що відповідають нормальній експлуатації обладнання.
Надійність і гарантія від виникнення граничних станів конструкції забезпечуються належним урахуванням можливих найбільш несприятливих характеристик матеріалів; перевантажень і найбільш невигідного (але реально можливого) сполучення навантажень і впливів; умов і особливостей роботи; належним вибором розрахункових схем і передумов розрахунку, обліком в необхідних випадках пластичних властивостей матеріалів.
Для першої групи умова по несучої здатності може бути записано в загальному вигляді
N≤Ф,
де N - зусилля, що діє в розраховується елементі конструкції (функція навантажень та інших впливів);
Ф - граничне зусилля, яке може сприйняти розраховується елемент (функція фізико-механічних властивостей матеріалу, умов роботи і розмірів елементів).
Для другої групи граничних станів, пов'язаних, як правило, з переміщеннями, також можна записати граничне нерівність:
f≤[f],
где f – перемещение конструкции (функция нагрузок);
[f] – граничне переміщення, допустиме за умовами експлуатації (функція конструкції і її призначення).
У загальному випадку робота конструкцій і перехід їх в граничний стан залежать від навантажень, властивостей матеріалу і умов роботи. Розглянемо облік цих факторів при розрахунку конструкції за граничними станами.
У процесі експлуатації об'єкти піддаються різним навантажень і впливів.
Робота об'єкта, а, отже, і особливості його розрахунку багато у чому залежать від природи, характеру та тривалості впливів. Так, при вибуху слід враховувати вплив швидкості навантаження на властивості матеріалу; при впливі низьких температур - підвищену небезпеку крихкого руйнування; при тривалому впливі - повзучість матеріалу.
Класифікація навантажень і впливів.
За своєю природою навантаження і впливи підрозділяють на:
- навантаження від власної ваги конструкцій;
- технологічні навантаження (вага обладнання, що складуються, людей, тиск рідин, газів, сипучих матеріалів і т.д.);
- атмосферні навантаження (сніг, вітер, ожеледь);
- температурні (технологічні та кліматичні) впливу;
- монтажні навантаження;
- сейсмічні й вибухові впливи;
- аварійні навантаження, що виникають при різкому порушенні технологічного процесу, поломки устаткування, обриви проводів ліній електропередачі тощо
Всі ці навантаження і впливи викликають в об'єкті зусилля і переміщення і можуть бути віднесені до прямих впливів. Крім них на конструкції можуть впливати хімічні (корозія) , радіаційні та інші впливи. Ці дії приводять до зміни властивостей матеріалу (зниження ударної в'язкості при радіаційному впливі), змінюють параметри роботи елементів (зменшення товщини елементів, підвищення концентрації напружень при корозії) і в підсумку впливають на несучу здатність і довговічність конструкцій. Такі впливи називають непрямими.
Під характером впливу розуміють швидкість і частоту прикладання навантажень. За цією ознакою навантаження поділяють на статичні, динамічні та змінні багаторазово повторювані.
При статичних навантаженнях швидкість навантаження дорівнює нулю. Вона настільки мала, що викликаються ними інерційні сили в розрахунку можна не враховувати. При динамічних навантаженнях швидкість навантаження висока і, викликані ними інерційні сили, необхідно враховувати при розрахунку об'єктів. При впливі змінних багаторазово повторюваних навантажень в конструкціях можуть виникнути втомні руйнування. У цьому випадку конструкції необхідно перевірити на витривалість.
Залежно від тривалості дії навантаження ділять на постійні і тимчасові. Тимчасові навантаження в свою чергу підрозділяють на тривалі, короткочасні і особливі.
Постійними навантаженнями називають такі, які діють на конструкцію постійно: власна вага, тиск, вплив попереднього напруження конструкцій і т.п.
Тривалими навантаженнями називають такі, які діють на конструкцію тривалий час (але можуть і не бути): вага технологічного обладнання, вага складованих вантажів, тиск рідин і газів в резервуарах і трубопроводах.
Короткочасними навантаженнями називають навантаження, що діють нетривалий час: сніг, вітер, рухливі крани, навантаження (що виникають при транспортуванні, монтажі, ремонтах і випробуваннях), температурні кліматичні дії і т.д.
Особливі навантаження - це навантаження, які можуть з'явитися у виняткових випадках: сейсмічні впливи, аварійні порушення технологічного процесу, різкі осідання грунтів.
Нормативні та розрахункові навантаження. Всі навантаження в тій чи іншій мірі випадкові і при математичному описі можуть бути представлені у вигляді випадкових величин (наприклад, власну вагу конструкцій) або випадкових функцій часу (наприклад, вітер). Однак при розрахунку конструкцій але граничним станам приймаємо детерміновані значення навантажень. Тому для забезпечення необхідного рівня надійності при розрахунку конструкцій за першою групою граничних станів слід приймати максимальні значення навантажень з високим ступенем забезпеченості. При розрахунку за другою групою граничних станів, тобто в умовах нормальної експлуатації. Забезпеченість може бути нижчою.
Основні положення з розрахунку встановлюють два значення навантажень: нормативні та розрахункові.
Навантаження, що відповідають умовам нормальної експлуатації, називають нормативними. Їх величину встановлюють у нормах проектування, обговорюють в технічному завданні або визначають за проектним значенням геометричних параметрів обладнання або конструкцій.
Можливе відхилення навантажень в несприятливу (більшу пли меншу ) сторону від їх нормативних значень, як внаслідок природної мінливості навантажень, так і відступів від умов нормальної експлуатації враховується коефіцієнтом надійності за навантаженням ?j. Значення цього коефіцієнта залежить від характеру навантаження і ступеня її мінливості. Так, навантаження від власної ваги металевих конструкцій можуть відхилятися від нормативної в досить вузьких межах (за рахунок допусків на розміри перерізів, точності різання і т.п.), тому для цього навантаження ?j = 1,05.
Значення коефіцієнтів надійності за навантаженням визначають на підставі статистичної обробки результатів спостережень, експериментальних досліджень або встановлюють на підставі досвіду проектування.
Розрахункові навантаження являють собою найбільші в ймовірносно сенсі навантаження і впливи за час експлуатації споруди.
Коефіцієнти надійності за навантаженням враховують тільки мінливість навантаження і можливість перевищення нею нормативних значень. Вони не враховують динамічного характеру навантаження або перспективного зростання навантаження з часом, наприклад при модернізації виробництва та зміні устаткування. Ці фактори при необхідності враховують окремо.
3.1.2 Аналіз технічних ризиків в зоні відводу та вловлювання коксового газу
Під ризиком слід розуміти очікувану частоту або ймовірність виникнення небезпек певного класу, або ж розмір можливого збитку (втрат, шкоди) від небажаної події, або ж деяку комбінацію цих величин.
Застосування поняття ризик, таким чином, дозволяє переводити небезпеку в розряд вимірюваних категорій. Ризик, фактично, є міра небезпеки. Часто використовують поняття "ступінь ризику", по суті, не відрізняється від поняття ризик, але лише підкреслює, що мова йде про вимірювану величину
Всі названі (або подібні) інтерпретації терміну "ризик" використовуються в даний час при аналізі небезпек та управлінні безпекою (ризиком) технологічних процесів і виробництв в цілому.
Формування небезпечних і надзвичайних ситуацій - результат певної сукупності факторів ризику, породжуваних відповідними джерелами.
Стосовно проблеми безпеки виробництва такою подією може бути аварія чи катастрофа технічної системи або пристрою, забруднення або руйнування екологічної системи, загибель групи людей, матеріальний збиток від реалізувалися небезпек або збільшення витрат на безпеку.
Кожна небажана подія може виникнути по відношенню до певної жертви - об'єкту ризику. Співвідношення об'єктів ризику і небажаних подій дозволяє розрізняти індивідуальний, технічний, екологічний, соціальний та економічний ризик. Кожен вид його обумовлюють характерні джерела та фактори ризику, класифікація і характеристика якого наведено в табл. 3.1
Таблиця 3.1 – Класифікація і характеристика видів ризику
Види ризику | Об'єкт ризику | Джерело ризику | Небажана подія |
Індивидуальний |
Людина | Умови життєдіяльності людини | Захворювання, травма, інвалідність, смерть |
Технічний |
Технічні системи та об'єкти | Технічна недосконалість, порушення правил експлуатації технічних систем та об'єктів | Аварія, вибух, катастрофа, пожежа, руйнація |
Екологічний |
Екологічні системи | Антропогенне втручання в природне середовище, техногенні надзвичайні ситуації | Антропогенне втручання в природне середовище, техногенні надзвичайні ситуації |
Соціальний |
Соціальні групи | Надзвичайна ситуація, зниження якості життя | Групові травми, захворювання, загибель людей, зростання смертності |
Економічний |
Матеріальні ресурси | Підвищена небезпека виробництва або природного середовища | Збільшення витрат на безпеку, збиток від недостатньої захищеності |
Індивідуальний ризик може бути добровільним, якщо він обумовлений діяльністю людини на добровільній основі, і вимушеним, якщо людина піддається ризику у складі частини суспільства (наприклад, проживання в екологічно несприятливих регіонах, поблизу джерел підвищеної небезпеки).
Технічний ризик - комплексний показник надежностіелементов техносфери. Він виражаетвероятность аварії або катастрофи при експлуатації машин, механізмів, реалізації технологічних процесів, будівництві та експлуатації будівель і споруд:
где Rт - технічний ризик;
ΔT - число аварій в одиницю часу t на ідентичних технічних системах та об'єктах;
T - число ідентичних технічних систем та об'єктів, схильних до загального фактору ризику f.
Джерела і фактори технічного ризику наведені втабл. 3.2
Таблиця 3.2 - Джерела і фактори технічного ризику
Джерело технічного ризику | Найбільш поширені фактори технічного ризику |
Низький рівень науково-дослідних робіт | Помилковий вибір напрямків розвитку техніки в технології за критеріями безпеки |
Те ж, дослідно-конструкторських робіт |
Вибір потенційно небезпечних конструктивних схем і принципів дії технічних систем.
Помилки у визначенні експлуатаційних навантажень. Неправильний вибір конструкційних матеріалів. Недостатній запас міцності. Відсутність в проектах технічних засобів безпеки. |
Експериментальне виробництво нової техніки | Неякісна доведення конструкцій, технології, документації по критеріям безпеки |
Серійний випуск небезпечною техніки |
Відхилення від заданого хімічного складу конструкційних матеріалів.
Недостатня точність конструкційних розмірів. Порушення режимів термічної обробки деталей. Порушення регламентів складання і монтажу конструкцій і машин. |
Порушення правил безпечної експлуатації технічних систем |
Використання техніки не за призначенням.
Порушення паспортних режимів експлуатації. Несвоєчасні профілактичні огляди та ремонти. Порушення вимог транспортування і зберігання. |
Помилки персоналу |
Слабкі навички дії у складній ситуації.
Невміння оцінювати інформацію про стан процесу. Слабке знання сутності процесу, що відбувається. Відсутність самовладання в умовах стресу. Недисциплінованість. |
3.1.3 Аналіз надійності системи вловлювання та очищення коксового газу методом дерева відмов
Найбільш використовуваним методом аналізу можливих відмов обладнання є метод «дерева відмов». Він полягає в побудові та аналізі моделі надійності (безпеки), що представляє собою логіко-імовірнісну модель причинно-наслідкових зв'язків відмов досліджуваної системи з відмовами її елементів та іншими впливами.
Основними перевагами методу є:
- Висока наочність представлення результатів аналізу, що робить їх доступними для широкого кола фахівців (не тільки в області безпеки);
- Можливість виконувати як якісний, так і кількісний аналіз безпеки системи;
- Дозволяє показати в явному вигляді ненадійні місця системи;
- Забезпечує глибоке уявлення про поведінку системи і проникнення в процес її роботи.
Недоліки «дерева відмов» полягають у наступному:
- Реалізація методу вимагає значних витрат коштів і часу;
- Дерево відображає тільки два стани системи: робочий і отказавшее;
- Дерево відмов описує систему в певний момент часу (зазвичай в сталому режимі);
- Вимагає від фахівців з надійності глибокого розуміння системи і конкретного розгляду щоразу лише одного певного відмови.
Незважаючи на широке висвітлення в науково-технічній літературі, на практиці фахівці допускають ряд методичних та логічних помилок. Це призводить до некоректності результатів аналізу безпеки.
Основними помилками є:
- Невідповідність «дерева» ієрархічній структурі системи;
- Упущення істотних факторів і надання надмірної ваги несуттєвим;
- Введення помилкових операторів не несучих смислового навантаження, але беруть участь у розрахунку;
- Розгляд відмов, які не впливають на безпеку обладнання;
- Некоректне використання логічних символів;
- Некоректне використання статистичних даних.
Розглянемо ключові моменти побудови «дерева відмов» в інженерній практиці.
Перш ніж приступити до побудови, необхідно проаналізувати такі джерела інформації про об'єкт:
- проектну документацію;
- Документацію заводів-виготовлювачів обладнання;
- Технологічний регламент установки;
- Експлуатаційну і ремонтну документацію.
На підставі отриманих даних проводиться аналіз процесу експлуатації об'єкта, і розробляються переліки можливих відмов та їх причин.
Аналіз процесу експлуатації дозволяє отримати необхідні відомості для виявлення можливих відмов. Його проводять у наступному порядку:
- Визначають призначення системи, особливості її експлуатації та перелік виконуваних завдань;
- Виділяють основні, забезпечувальні та допоміжні функції вироби;
- Для кожної виділеної функції визначають групи вихідних параметрів, номінальні і гранично допустимі значення кожного параметра;
- Визначають види елементів системи, їх функціональні особливості та характер взаємодії при експлуатації, наявність резервних елементів, виявляють елементи, що не мають аналогів;
- Визначають особливості експлуатації виробу (основні та резервні режими експлуатації, можливості роботи з зміненими вихідними параметрами і т.д.);
- Визначають тривалість кожного періоду експлуатації.
Перелік можливих відмов повинен володіти достатньою повнотою, обумовленою наявністю найбільш ймовірних і критичних (що призводять до найбільш тяжких наслідків) відмов, але не може бути надмірною через включення до нього залежних відмов. Відмови, що виникають за однією і тією ж причини, можуть бути об'єднані. При складанні переліку аналізують обмеження на умови застосування системи, порушення яких розглядають як можливі відмови.
Спрощено структуру «дерева відмов» можна уявити в наступному вигляді:
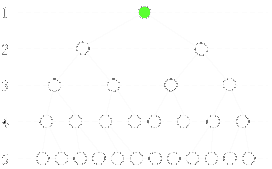
Малюнок 3.1 - Структура дерева відмов
Де
1) Відмова системи
2) Відмова складових частин
3) Відмова елементів
4) Події, які породжують відмова
5) Види впливів
3.2 Практичні методи
3.2.1 Методи зниження корозійної деградації
Корозія призводить щорічно до мільярдних збитків, і дозвіл цієї проблеми є важливим завданням. Основний збиток , що заподіюється корозією, полягає не у втраті металу як такого, а у величезній вартості виробів, що руйнуються корозією. Ось чому щорічні втрати від неї в промислово розвинених країнах настільки великі. Справжні збитки від неї не можна визначити, оцінивши лише прямі втрати, до яких відносяться вартість зруйнованої конструкції, вартість заміни обладнання, витрати на заходи по захисту від корозії. Ще більший збиток становлять непрямі втрати. Це простої обладнання при заміні прокорродіровавшіх деталей і вузлів, витік продуктів, порушення технологічних процесів.
Корозія - це мимовільне руйнування металів в результаті хімічного або фізико-хімічної взаємодії з навколишнім середовищем.
Залежно від характеру корозійного процесу розрізняють хімічну і електрохімічну корозію металів.
При хімічній корозії метал руйнується в агресивних середовищах внаслідок безпосереднього з'єднання металу з агресивними хімічними агентами (наприклад, залізо окислюється).
При електрохімічній корозії руйнування металів відбувається внаслідок їх розчинення в рідкому середовищі, що є електролітом, і полягає в утворенні на їх поверхні безлічі мікрогальванічних елементів.
Корозія металів може бути місцева, при руйнуванні поверхні в певних ділянках, і рівномірна, коли метал руйнується по всій поверхні, а також межкристаллитная, коли руйнування відбувається по межах зерен металу.
Прямі показники корозії
- спад або збільшення маси , віднесені до одиниці поверхні металу;
- Глибина корозії;
- Частка поверхні , зайнята продуктами корозії;
- Кількість корозійних виразок або точок ( вогнищ корозії) на одиниці поверхні ;
- Обсяг виділився з одиниці поверхні водню або поглиненого кисню ;
- Час до появи першого вогнища корозії;
- Час до появи корозійної тріщини або повного руйнування зразка;
- Сила струму корозії;
Непрямі показники корозії
- Зміна фізико-механічних властивостей металу (межі міцності при випробуваннях на стиск і розрив, відносного подовження, відбивної здатності та ін);
- Зміна опору;
Група стійкості |
Глибинний показник корозії, мм/рік |
Бал |
Абсолютно стійкі |
0,001 | 1 |
Вельми стійкі |
0,001 ... 0,005 0,005 ... 0,010 |
2 3 |
Стійкі |
0,01 ... 0,05 0,05 ... 0,10 |
4 5 |
Понижено стійкі |
0,1 ... 0,5 0,5 ... 1,0 |
6 7 |
Малостійкі |
1,0 ... 5,0 5,0 ... 10,0 |
8 9 |
Нестійкі |
10,0 | 10 |
Таблиця 3.4 – Шкала грубої оцінки корозійної стійкості металів
Існує кілька методів антикорозійного захисту металів. По механізму дії всі методи антикорозійного захисту можна розділити на дві основні групи: електрохімічні, що роблять вплив на потенціал металу або його критичні значення, і механічні, ізолюючі метал від впливу навколишнього середовища створенням захисної плівки і покриттів.
До основних методів антикорозійного захисту належать:
- легування металів P>
- Термообробка P>
- Інгібування навколишнього середовища P>
- Деаерація середовища P>
- Водопідготовка P>
- Захисні покриття P>
- Створення мікроклімату і захисної атмосфери.
Способи антикорозійного захисту вказуються в робочих кресленнях конструкцій, в СНиП, технічних умовах (ТУ). Найпростішим і ефективним способом захисту металевих конструкцій від корозії є покриття їх поверхонь різними фарбами, лаками, емалями.
Барвисте покриття, полімерне покриття і емалювання повинні, насамперед, запобігти доступ кисню і вологи. Часто також застосовується покриття, наприклад, стали іншими металами, такими як цинк, олово, хром, нікель. Цинкове покриття захищає сталь навіть коли покриття частково зруйнована. Цинк має більш негативний потенціал і корродіруєт першим. Іони Zn2+ токсичні. При виготовленні консервних банок застосовують жесть, покриту шаром олова. На відміну від оцинкованої жесті, при руйнуванні шару олова корродировать, притому посилено, починає залізо, так як олово має більш позитивний потенціал.
Утворені на поверхні металів окисні плівки поділяються на два види: щільні і пухкі. Щільні плівки окислів порушують контакт навколишнього середовища з поверхнею металу і таким чином захищають останню від окислення. Пухкі плівки не перешкоджають окисленню. Щільні плівки окислів утворюються алюмінієм, свинцем, нікелем, пухкі окисні плівки - кальцієм, магнієм і ін.
Сучасна хімія дає можливість виготовляти високоякісні лакофарбові матеріали, що забезпечують поряд з механічною хімічну (фосфатирующие грунти) і електрохімічний (протекторні грунти) захист. Лакофарбові матеріали (по пропонованим вимогам і властивостями входять до їх складу компонентів) розрізняють: антикорозійні, водостійкі - захищають метал від корозії в місцях з високим ступенем вологості (ЕКЖС-40, ХС-78, грунти ВЛ-02, №81, ФО-03Ж та ін); атмосферостійкі - захищають від атмосферної корозії (ПХВ-29, ПХВ-35 , ХВ-124, ПФ-115, ХС-510 та ін); термостійкі - захищають від корозії поверхні металу, що нагріваються понад 100°С, та ін
Інша можливість захистити метал від корозії - застосування захисного електрода з великим негативним потенціалом, наприклад, з цинку або магнію. Для цього спеціально створюється корозійний елемент. Захищуваний метал виступає в ролі катода, і цей вид захисту називають катодного захистом. Розчинялася електрод, називають, відповідно, анодом протекторного захисту. Цей метод застосовують для захисту від корозії морських суден, мостів, котельних установок, розташованих під землею труб. Для захисту корпусу судна на зовнішню сторону корпусу кріплять цинкові пластинки.
3.2.2 Методи зниження утворення відкладень
Відкладення, що утворюються на внутрішній поверхні трубопроводів є продуктами складних фізико-хімічних процесів, що відбуваються на ній самій або на нанесеному захисному покритті, а також в транспортується по трубопроводу середовищі.
Характер відкладень в трубопроводах, як правило, визначається:
- Фізико-хімічними властивостями транспортуються середовищ;
- Умовами експлуатації мережі;
- Тривалістю служби трубопроводів.
Попередження утворення і видалення відкладень, обумовлених жорсткою водою або корозійними процесами є актуальним завданням, що обумовлено такими міркуваннями:
1. Наявність відкладень значно погіршує теплообмін у теплообмінних апаратах, знижує пропускну здатність трубопроводів. Теплопровідність відкладень залежно від їх складу в два і більше разів менше, ніж теплопровідність конструкційних матеріалів;
2. Корозійні пошкодження поверхонь обладнання, в т.ч. запірно-регулюючої арматури, істотно знижують їх надійність роботи і термін служби.
Солевідкладення вкрай негативно впливає на безпеку експлуатації трубопроводів. Воно викликає посилення локальної корозії металу труб, що призводить до їх прискореного руйнування.
Механізм запобігання утворення відкладень визначається відношенням швидкості протікання зародкоутворення кристалів і зростанням кристалів. Термін «освіта центрів кристализации» відноситься до спонтанного формування мікроскопічних частинок (мікрокрісталлітов) з розчинених іонів, наприклад, кристаллитов карбонату кальцію з розчиненого кальцію і карбонатних іонів. Ці крихітні кристали можуть спонтанно розпадатися або продовжувати рости до певної надкритичного розміру. При досягненні цього розміру вони стають макрокрісталламі і переходять у стійкий стан. Розпад припиняється, і поступово формуються великі кристалічні структури, які називають «відкладеннями».
Для того щоб предметно і систематично вирішувати проблеми, пов'язані з утворенням відкладень, рекомендується дотримуватися наступної процедури:
Етап 1. Визначити місце утворення відкладень
Найбільш поширені місця утворення відкладень включають центрифуги і трубопроводи, а також насоси, теплообмінники.
Етап 2. Визначити тип відкладень
Тип первинного очищення, вибір і дозування продуктів залежать від типу відкладень. Тип відкладень може бути з достатнім ступенем упевненості визначений на місці за допомогою нескладних способів.
Солі вуглекислоти: утворюються газові бульбашки при обробці оцтовою кислотою або лимонною кислотою.
Фосфати: повільно розчиняються в среднеконцентрірованних неорганічних кислотах або лугах без утворення бульбашок.
Окисли заліза: визначаються візуально, виглядають, як іржа. Більш точне визначення складу відкладень можливо тільки в лабораторних умовах.
Етап 3. Вибрати оптимальний реагент
Оптимальний інгібітор утворення відкладень можна вибрати за допомогою приладу P-MAC, використовуючи для моделювання процесу утворення відкладень зразок води, взятий з місця передбачуваного застосування реагенту. У випадку дуже високого вмісту заліза досить ефективне інгібування утворення відкладень може бути забезпечено застосуванням поліакрилатів.
Етап 4. Визначити точку введення реагенту
Загальне правило:
Точка введення реагенту повинна знаходитися якомога ближче до місця утворення відкладень, але при цьому повинен бути забезпеченні рівномірний введення в суміш. З урахуванням хімічної природи інгібіторів утворення відкладень їх ефективність може бути ослаблена під впливом інших речовин, що містяться у воді. З цієї причини не слід застосовувати реагенти в рідкій фазі на великому видаленні від місця їх безпосередньої дії.
Етап 5. Виконати первинну очистку
Реагенти, використовувані для протидії утворенню мінеральних відкладень, не здатні видалити відкладення, які вже присутня. Тому перед початком використання реагенту необхідно виконати первинну очистку, для чого при необхідності можна залучити кваліфікованих фахівців спеціалізованої організації.
Етап 6. Забезпечити дозування і оперативний контроль
Визначення доз продуктів для дозування за допомогою насосів дозувань грунтується на емпіричному підборі або лабораторних рекомендаціях. У більшості випадків вихідна доза відповідає концентрації 30 ppm. Ефективність дії реагенту може бути перевірена візуально, наприклад, оглядом внутрішньої поверхні схильних утворення відкладень труб або окремого трубопроводу, спеціально встановленого в контрольних цілях.
Хімічне очищення має ряд недоліків, основними з яких є:
- Використовувані реагенти мають високу токсичність , мають високу корозійну активністю і є їдкими речовинами;
- Необхідність утилізації великих обсягів відпрацьованих реагентів і їх розчинів. Витрата миючих розчинів становить до 10% від обсягу теплоносія - тобто приблизно 1 м3 на 10м3 промивного об'єму;
- Висока ймовірність пошкодження конструкційних матеріалів обладнання внаслідок високої корозійної активності промивних розчинів. Особливо це відноситься до таких конструкційних матеріалів як алюміній, бронза, чорні метали.
- Ймовірність влучення агресивних токсичних рідин в житлові та виробничі приміщення у разі появи течі;
- Необхідність відключення системи опалення при проведенні промивки;
- Необхідність проведення додаткових заходів щодо запобігання корозії устаткування після проведення промивки.
ВИСНОВКИ
У даній роботі була описана система уловлювання та транспортування коксового газу, що включає в себе газозбірник, сепаратор, первинний газовий холодильник з горизонтальними трубами, нагнітач для коксового газу. Були проаналізовані умови роботи всіх елементів системи уловлювання та транспортування коксового газу. Були досліджені процеси, що відбуваються в даному обладнанні.
У підсумку з вищесказаного випливають такі висновки :
- Устаткування системи відводу і транспортування коксового газу працює у важких умовах (тиск, температура, корозійне середовище) .
- Такі умови роботи призводять до інтенсивного розвитку деградаційних процесів (корозія, виникнення відкладень, зміна властивостей матеріалу), що знижують надійність системи.
- Для забезпечення безпечної експлуатації обладнання необхідно знати параметри його технічного стану в будь-який момент часу в процесі роботи.
Використовуючи вищеописані методи ми можемо розрахувати технічні ризики враховуючи надійність і зміну технічного стану об'єкта. Раніше в подібних розрахунках для коксохімічного виробництва зміна технічного стану об'єкта не враховувалась. У запропонованих ж розрахунках буде видно вплив відкладень і деградаційних процесів на надійність.
Для підвищення надійності та безпеки запропоновано виконувати імовірнісний розрахунок, який полягає у визначенні ймовірності безвідмовної роботи системи, в якій враховуються безліч чинників. Однак, у зв'язку з тим, що фактори, які визначають міцність елементів і діючі навантаження є імовірнісними, вони представлені у вигляді інтервалу значень. З використанням даного методу з'являється можливість:
- Прогнозування зміни технічного стану обладнання для уловлювання та транспортування коксового газу із заданою вірогідністю;
- Приймати для відповідального обладнання допустимими найбільш небезпечні поєднання чинників, а для менш відповідальних такою точністю можна знехтувати.
Для визначення цих величин були зроблені експериментальні дослідження властивостей деталей особливо сильно піддаються деградації, таких як футеровочна цегла з газового стояка і зразки металу з різних ділянок технологічного шляху руху газу.
При написанні даного реферату магістерська робота, зокрема розрахункова її частина, ще не завершена. Остаточне завершення: грудень 2014 року. Повний текст роботи та матеріали по темі можуть бути отримані у автора або його керівника після зазначеної дати.
Перелік посилань
- Коляндр Л.Я. Улавливание и переработка химических продуктов коксования. – Харьков, 1962. 22с.
- Коробчанский И.Е., Кузнецов М.Д. Расчеты аппаратуры для улавливания химических продуктов коксования. Харьков. Металлургия, 1952. - 55с.
- Александров К.И. Газодувки. - М.: Энергия, 1961. – 79с.
- Лебедев А.А., Ковальчук Б.И. Справочное пособие по расчету машиностроительных конструкций на прочность. – К., 1990. – 240с.
- Ковалев Г.М. Нагнетатели коксового газа. М.: Металлургия, 1972.–190с.
- Соколов Ю.Н. Основы единой теории лопастных машин. – Томск, 1973. – 218с.
- Юдин Е.М. Шестеренные насосы. – М.: Машиностроение, 1964. – 75с.
- Бондаренко М.С., Иванченко В.В. Справочник механика химических производств. – Донецк: Донбасс, 1988. - 208с.
- Хенли Э. Джм Кумамото X., Надежность технических систем и оценка риска: — М.: Машиностроение, 1984.
- Капур К., Ламберсон Л. Надежность и проектирование систем. – Москва, 1980.