Abstract
Content
- Introduction
- 1. The problem of ensuring safety and security of chemical equipment
- 1.1. Actuality of problem
- 1.2. Technological scheme of capturing and transportation coke oven gas
- 2. Analysis of the design and operating principles of the system
- 2.1. Coke ovens
- 2.2. Gas strut and gas collector
- 2.3. Separator
- 2.4. The primary gas cooler
- 2.5. Compressor
- 2.6. Analysis of the main processes that occur in equipment
- 2.7. Analysis of the degradation processes
- 2.8 Formulation of research problems
- 3. Methods technogenic safety of chemical equipment
- 3.1 The theoretical basis of calculating technological safety
- 3.1.1 Analysis of boundary conditions in the area of ??carbon capture and transportation of coke oven gas
- 3.1.2 Analysis of technical risks in the removal and capture of COG
- 3.1.3 Reliability analysis of capturing and purification of coke oven gas using fault tree
- 3.2 Practical methods
- 3.2.1 Methods of reducing corrosion degradation
- 3.2.2 Methods to reduce the formation of deposits
- Conclusion
- References
Introduction
In ovens during the coking formed coke and chemical products that stand out in a very complex mixture of gases and vapors, called coke oven gas.
Coke oven gas is a valuable raw material from which the tar, ammonia, hydrogen cyanide, hydrogen sulfide, naphthalene, benzene and others.
n the equipment of capturing and transporting COG held a variety of manufacturing processes. Such as moving gas cooling, condensation of moisture from it. Thus these degradation processes occur:
- Corrosion of internal surfaces in contact with the substance
- The formation of deposits on the pipe walls due to condensation, change the properties of a brick, and as a result, wear futerovalnoyi brick through saturation of substances from the pipeline.
These degradation processes have a decisive influence on the technical condition of equipment.
In this work the machinery system for capturing and transporting coke oven gas, made material and thermal calculations of this equipment, the basic degradation processes and ways of dealing with them. The method of calculating the technical condition of coke facilities that allow for the degradation machinery and equipment changes in the process.
1 THE PROBLEM OF ENSURING SAFETY AND SECURITY OF CHEMICAL EQUIPMENT
1.1 Actuality of problem
Coke oven gas contains large amounts of vapor resin painted it in dark brown or brown.
Coke oven gas emitted from furnaces called direct and contains water vapor 250-450m3, the resin fumes 80-120m3, benzene hydrocarbons 30-40m3, ammonia 8-13m3, hydrogen sulfide 6-30m3, cyanide compounds0,5-1,5 м3.
In addition, the gas contains a small amount of light pyridine bases (0.4-0.6 g/m3), naphthalene (up to 10 g/m3), different sulfur (disulfide CS2, oxysulfides carbon COS, thiophene C4H4 S and others) (2-2.5 g/m3) and other compounds.
After receiving the coke oven gas pichah it is necessary to grasp and vikonaty over it several operations: cooling, condensation resins transportation. This uses the capture and transport of gas, which consists of a riser, hazosbirnyka, pipeline, separator, primary gas cooler, Blower (later - the equipment).
With coke burning gas chamber (t = 600-650°C) is given through riser that cast iron knee connection to the gas pipeline, located along the coke oven battery. In the riser through nozzle fed bariletna water with a temperature of 80 ° C, which cools and humidifies the gas. Then the gas enters the separator. There wet resin is condensed and fed into mechanized clarifier where purified bariletnu (nadsmolyanu) water.
Then cooled to a temperature of 85 ° C gas passes through the gas cooler end, once cooled reversible water to 35 ° C. As such, the coke oven gas is supplied to the Blower. The amount received direct COG for the entire battery is 37 thousand. m3/h
Coke oven gas is rich composition containing corrosive agents and high temperatures. It has a decisive impact on the equipment. This leads to a relatively low its reliability and durability.
For example, the life of risers 10 years, major repairs carried out in 5 years, while replacing the lining is carried out at intervals of 9 months, removal of sediment 1 time per week.
The problem of the reliability of the equipment catching and transporting the coke oven gas is a particularly serious nature, since the degradation occurring failure, destruction and as a result there are very serious environmental emissions, explosions, fires, followed by high costs.
In the equipment of capture and transport COG held a variety of manufacturing processes. Such as moving gas cooling, condensation of moisture from it. Thus these degradation processes occur:
- Corrosion of internal surfaces in contact with the substance
- The formation of deposits on the pipe walls due to condensation, change the properties of a brick, and as a result, wear futerovalnoyi brick through saturation of substances from the pipeline.
For example, sediments are deposited on the walls of the pipeline, lead to the following consequences:
- Reduces the pipe section;
- Increasing pressure;
- Rising energy costs;
- Changing hydraulic regime of motion of matter through the pipes;
- Changing the roughness of the walls of the pipeline;
- Deteriorating heat transfer;
- Reduced strength due to corrosion of the pipeline.
At any given time properties of equipment and its specifications are subject to change. That is, instead of the original equipment have something different, with slightly different properties.
It follows that the design phase is required technical condition or prognosis of parameters at a given time. What may perform simulations based on changes in the technical condition of equipment.
However, in practice, to obtain accurate data on the effect of all these processes is difficult: the rate of corrosion in different parts of the equipment is different, the amount of deposits as different physical and mechanical properties change in different ways. That is, all processes of equipment are probabilistic in nature and all property, both equipment and technology and degradation processes (size, roughness, physical and mechanical properties, temperature, pressure, corrosion rate, etc.) are required to describe the expectation and variance.
To determine the probability of system failure must consider many factors. However, the factors determining the technical state is probabilistic, they are presented as a range of values and calculation results will also be probabilistic. Using this approach will significantly improve the accuracy of the reliability parameters several times.
So probability calculations when designing a constructive way to obtain quantitative estimates of performance reliability products at various stages of operation for the design. Since in this approach the performance of the product expressed in terms of statistics, it helps the designer to estimate warranty costs, develop a maintenance program and schedule the movement of stocks.
1.2 Technological scheme of capturing and transportation coke oven gas
When heated coal without air temperature 900-1100 ° C in cells coke out of his volatile coking products. With cameras coke coking volatile products by gas collector risers out of 1 (Figure 1.1). Temperature of gas in the riser 750-800°C.
Upon cooling gas is a partial condensation resin and loss of small pieces of coal with gas stoves assigned.
Due to the evaporation of over resin water (about 2-3% of fed), coke oven gas is cooled to 80-85°C, while in a fog of it condenses much of the resin (65-80% from that found in coke oven gas). Under pressure over resin water (gas collector pressure not lower 3kh/sm 2), which is fed through a nozzle directly into the gas collector, resin and condensation formed on the bottom fusy washed and drained the last of the machine-side coke oven battery in two peretochni box in coke oven gas pipelines.
The department condensation and initial cooling of coke oven gas make such technological operations:
- Initial cooling of coke oven gas;
- Over resin clean water from the resin and fusiv;
- Resin purification of water and fusiv;
- Cleaning chilled coke oven gas from the resin;
- Sucking coke oven gas from coke oven batteries and transporting it through the trap apparatus.
The cooled coke oven gas, water vapor and some tumanoobraznoy resin and nadsmolyana water that flows from peretochnyh boxes in the pipeline, is sent into the gas separator 2, where the separation of liquid and gaseous phases. The liquid portion of the gas separator 2 is given in motorized clarifier 10. Portion of gas, coke oven gas direct, routed under Blower 8 to pipe gas cooler 3.
The cooling of coke oven gas produced in the tube gas cooler 3. Cooling gas is set to 14 tubular gas refrigerators. The top two sections UGS irrigated plant desulfurization absorbing solution. Other sections are cooled refrigerators recycled industrial water, which is supplied from the pumping plant service water supply.
Condensate gas refrigerators 3 through the water seal is given in 13 collections, from pumps pumped in mechanical clarifiers and partly in the sump 18.
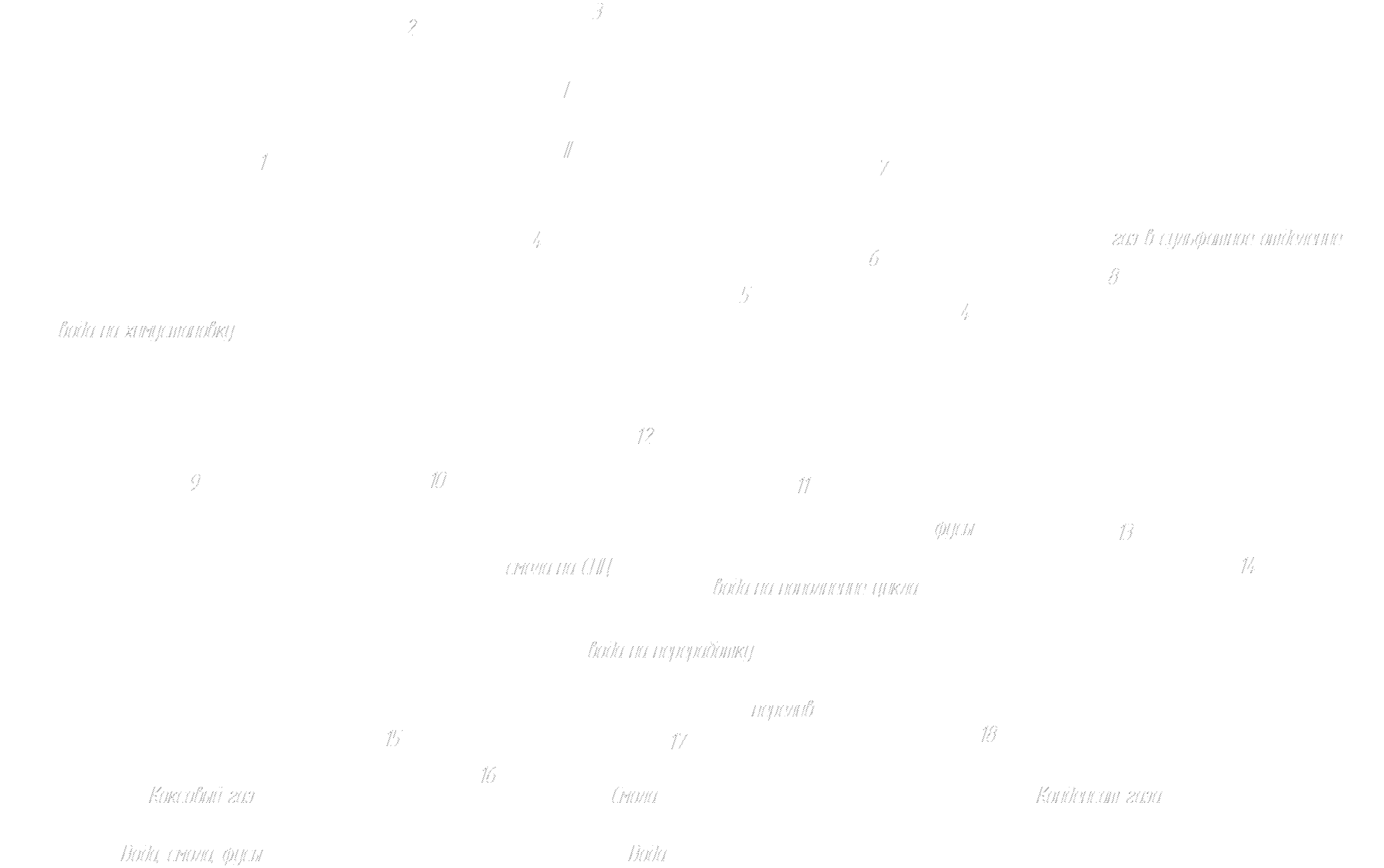
Figure 1.1 - Technological scheme of transportation COG
For extraction of gas collector COG coke batteries installed four gas blower type 1200-27-2, performance 72,000 m3/h
As a result of compression of gas blowers generates heat that increases the temperature of the gas at the outlet to 55-65°С.
Each blower is equipped with locking valves on the suction 1 and discharge 2 pipeline, starting bypass throttle 3 and 4 on the suction pipeline. Bypass with a diameter of 800 mm is used for coarse adjustment supercharger resulting in transmission of gas from the discharge pipe to the gas pipeline to the tubular gas refrigerators. Automatic suction regulation occurs through throttle suction blower.
2 Analysis of the design and operating principles of the system
2.1 Coke ovens
Modern furnace coking coal is a horizontal rectangular chamber, lined with refractory material. Cameras furnaces heated through the side wall. Furnaces are arranged in series and integrated in the battery to reduce heat loss and achieving compactness. In a typical battery furnaces with a width of 410 mm cameras typically consists of 65 ovens, and large capacity battery with a width of 450 mm camera consists of 77 ovens. Conventional cameras are useful volume 20-21,6 m3, and large capacity oven - 30 m3. Width 450 mm furnaces more feasible because of the deterioration of coke quality (increased abrasion). To facilitate the pushing of coke from coking chamber width of the camera from the issuance of coke make 40-50 mm wider than the machine-side. Thus, the camera looks like a cone. According to the basic elements of the battery must agree to the following: foundation, regenerators, kornyurnuyu zone, zone heating piers, piers overlapping and overlapping cameras.
Converting coal into coke charge is a chemical process that takes place without air. This process is characterized by complex chemical, physical and physico-chemical transformations during thermal decomposition of coal loading at certain stages of coke formation.
2.2 Gas strut and gas collector
Riser (Figure 2.2) consists of a vertical pipe 2, tee 3, cap 5, knees 9, valve box 16 of the poppet valve 14, 8 nozzles for supplying water for irrigation over vapor gas injectors (set of 4 hole) for loaded with smokeless and levers to control and valve cover.
Steel pipe 2 is installed in slot 1, formed in the masonry over furnace gas operated hatch. After installing pipe socket sealed asbestos cord and fireclay mortar. Inside the tube lined with fireclay bricks. Lining thickness 60-65 mm. To protect service personnel from burns, side pipes, reciprocal ways uhlezahruzochnaya toward the car, locked steel shield. The surface of the shield facing the tube is covered with sheet asbestos.
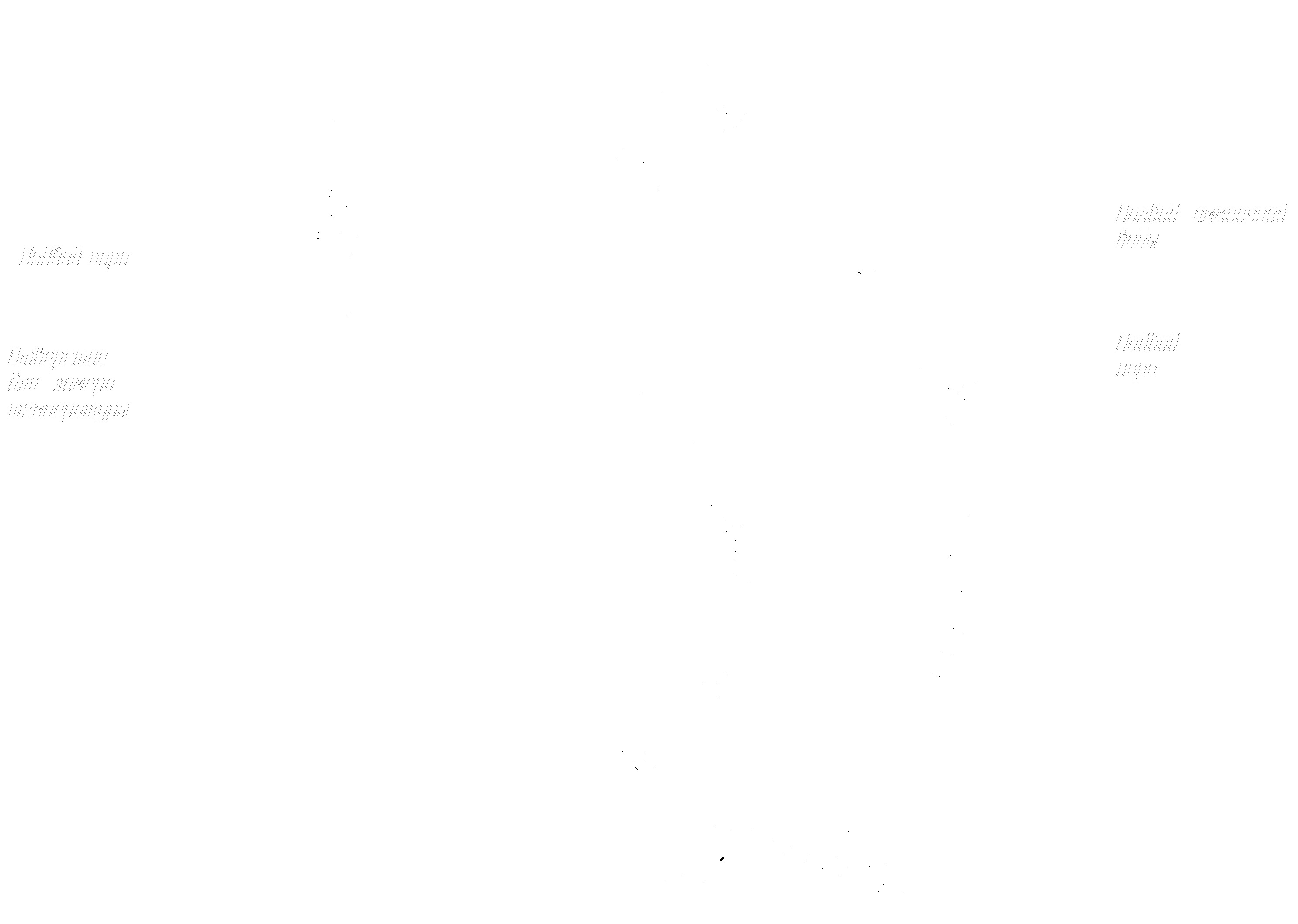
Figure 2.1 - Stands for removal of gas from the coke oven
Tee 3 with secured to the knee 9, joins pipe flange. Tee top closed by a cover 6. Between the lid and a removable flange 5 tee sealing means of the "iron on iron", in which the edge of the cover is installed on the finished surface removable flange.
Valve box 16 is attached to flange gas collector 13. In the valve box is shaft 17 on which is mounted tarilchaste valve 14. When closing the valve returns to the fray with a tapered saddle 15. Water supplied for irrigation, filling valve plate so that the cone turns out to be immersed in liquid. When forming a water seal that disables the riser of gas collector. Height 40 mm water seal. Closing the valve is held before issuing coke. When coking valve open, gas and coking chamber enters the gas collector. When passing through the riser gas is cooled by direct contact with water, spray nozzle 8 mounted on the knee. The water pressure to the nozzle 0,3-0,35 МПа.
Irrigation nozzles raw coke oven gas set so that the cone spraying ammonia water blocking all cross section of the gas flow and thus, the water could not get into the coke chamber. Ammonia water for irrigation riser gas is water seal when closing the valve box, through which the knee riser is connected to the gas collector.
Tees, elbows and valve boxes are made of (Iron brands СЧ 21-40; cover risers and valves - Steel.
With the riser through the knee and valve box products are in coking gas collector - steel pipes with a diameter of 1100 - 1600 mm, located on the machine and the coke side of the battery, or just with machine.
Knee and building riser equipped with a lever by which is driven by a cap and valve. Both kinematic chains are one-to-action lever or hydraulic drive.
2.3 Separator
According to the principle of the inertial separator refers to a centrifugal vortex type aids. Separation of the components of the gas-liquid flow in the device under the action of centrifugal force directed radially with respect to the vertical axis of the separator. The value of the centrifugal force acting on a drop of water or particle solids depends on the flow rate at the inlet of the separator, the density drops (its weight) and the radius of the device. The smaller the radius of the system, the greater the centrifugal force arising.
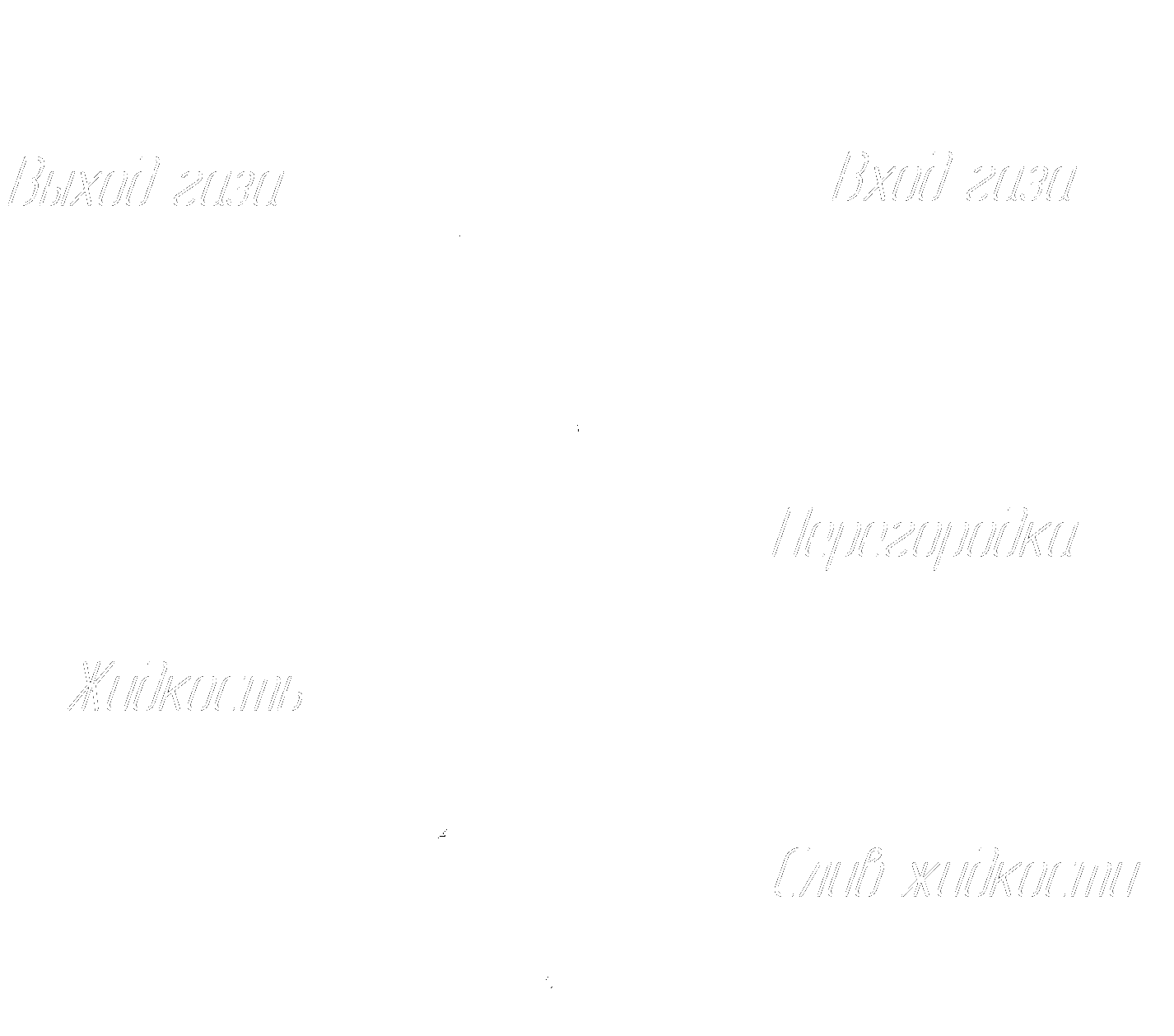
Figure 2.2 - Gas separator
The separator includes in its design 7 degrees of separation, while structural elements can be designed to separate gas-liquid flow.
Separator works as follows. Gas-liquid stream enters the separator through the gas inlet pipe 11, which takes rotational movement around the vertical axis through the separator design deflector 5. Rotating around a vertical axis, fluid and mechanical impurities by centrifugal force separated from the gas-liquid flow and pressed to the body of the separator 4. Here separation occurs approximately 80% solids and liquids from the gas stream.
Further gas-liquid flow coming through the gaps separatsyonnoho package 6 in the inner cavity separatsyonnoho package, continuing the rotation around the vertical axis of the separator is sent to the output gas pipe 2. B separation package is a complete cleaning of the gas flow from a drop of moisture and impurities.
Isolated fluid and mechanical impurities under the force of gravity flow down the walls of the housing and the separator plates in separate package down to the drain pipe 8.
2.4 The primary gas cooler
For primary gas cooling set horizontal tubular coolers of Giprokoks (pic.1.6) surface cooling 2100m2. The performance of this appliance for gas is 10-11 thousand m3/h of gas reduced to standard conditions.
The gas moves in the annulus, cooling water - in tubes. Since the heat transfer coefficient increases with increasing gas velocity and water, then increase these rates divided by vertical partitions refrigerator for six sessions. P>
Fridge height divided by three horizontal partitions that form the lower chamber for water, high - cooling chamber filled tubes, and the upper chamber to the overflow of water.
Gas enters the cooling chamber mezhtrubnyy space and passes successively from one section to another. Water enters the lower chamber also divided into sections, and rises through the pipes along the gas sixth section (first along the water) up, then piped down merges , etc. Thus, in all six sections observed complete reverse flow of the gas and water.
To maintain a constant gas velocity and water and hence the sustainability coefficient of heat transfer from the gas to the water section, which moves gas with variable cross-section: the largest in the course of the first gas used and the least in the last section along the gas. For water that moves in countercurrent direction, the lowest section of the pipe in the ground along the water section and the largest in the place of its exit from the appliance. A very important factor that largely determines the efficiency of the tube refrigerators is the rate of gas flow. It is, of course, is the higher, the greater the load the fridge on gas. So better cooling gas with less cooling water is obtained by passing the gas through a sequential series connected to each other refrigerators. However, it dramatically increases resistance to gas flow, is the difference liquefaction of the gas before and after coolers increases.
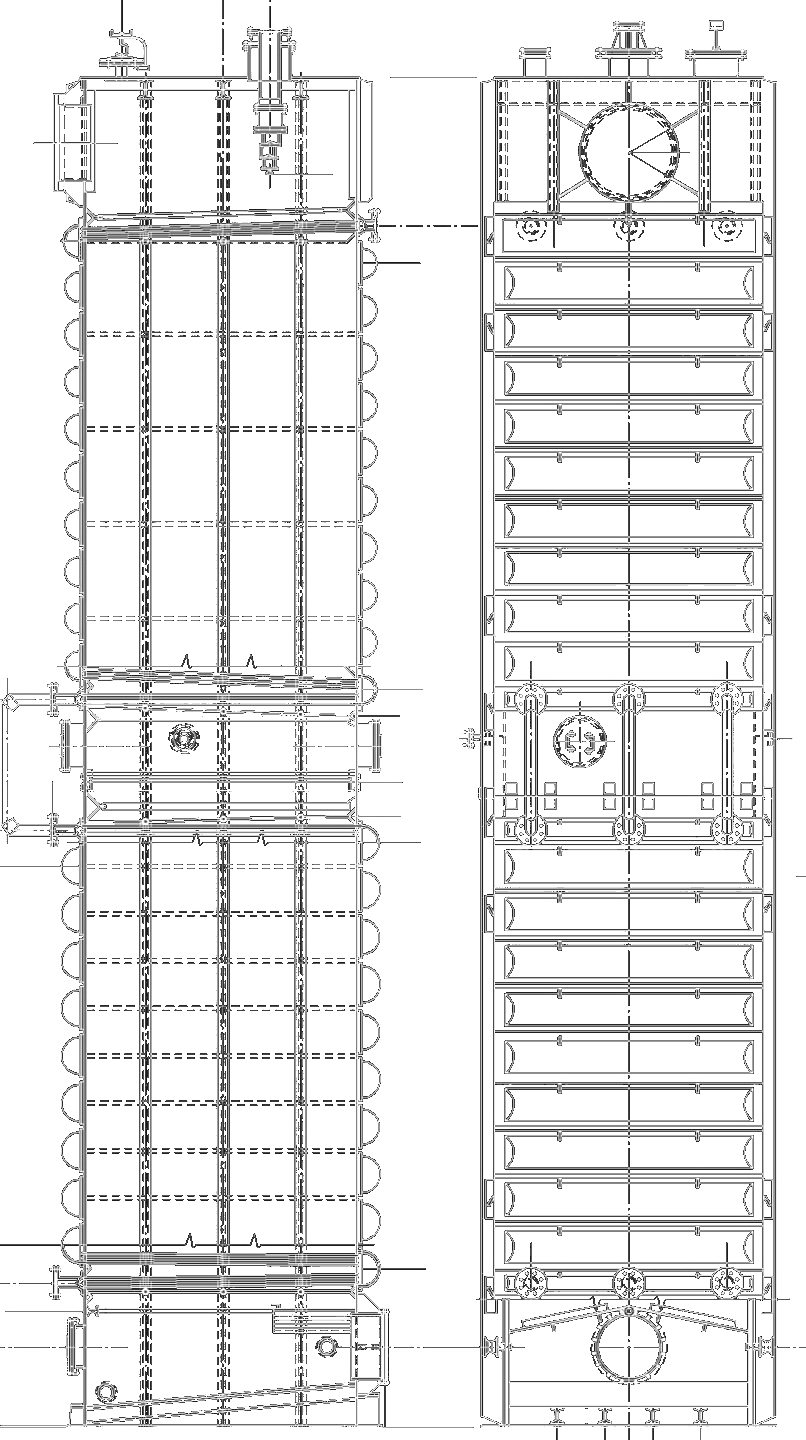
Figure 2.3 - Scheme of the gas cooler
2.5 Compressor
Purpose pumps - suction coke oven gas from coke ovens, transport it through recovery shop equipment and then supply to consumers.
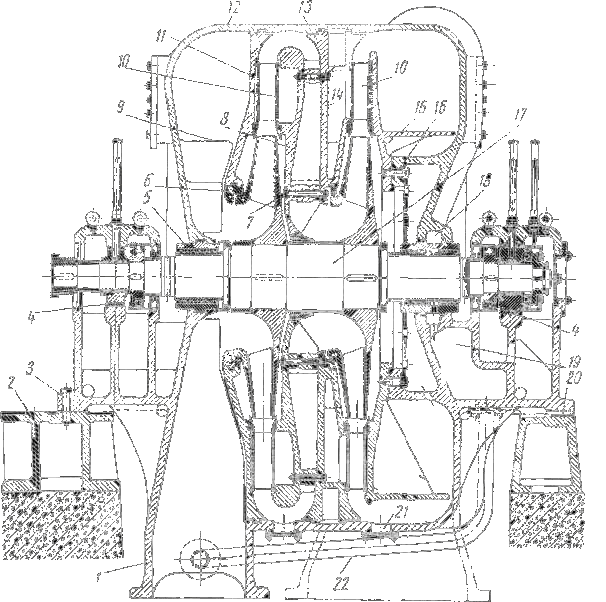
Figure 2.4 - Longitudinal section supercharger
Superchargers gas located in the engine room of recovery shop. Often they are installed after the primary gas coolers. Pipeline and hardware are located to the supercharger, under vacuum, and after supercharger - under pressure.
Gas from coke oven batteries, connected in pairs through primary coolers enters the general collector, located in front of the engine room. With two collector blowers gas is supplied to the gas pipeline, which runs to outlets recovery shop.
In the path of the coke oven gas pipelines experiencing resistance areas and equipment, which causes a change in the gas pressure in certain areas of the gas route.
In modern coke plants used blowers centrifugal type driven by a steam turbine (3000-5000 r/min) or low-speed high-voltage electric motor (1,450 rev/min) through a gear reducer that increases the rotational speed to 3000-5000 r/min.
In case of possible power outages one or two supercharger (of three) should have to drive a steam turbine. Typically, the work is one of the electric supercharger and turbo drive one.
Heating gas supercharger depending on the degree of compression varies between 10-15°C. Therefore, coke oven gas pumps after a temperature 35-45°С
2.6 Analysis of the main processes that occur in equipment
In ovens during the coking formed coke and chemical products that stand out in a very complex mixture of gases and vapors, called coke gas.
Coke oven gas is a valuable raw material from which the resin is obtained, ammonia, hydrogen cyanide, hydrogen sulfide, naphthalene, crude benzene, and others.
Coke oven gas contains large amounts of vapor resin paints it in dark brown or brown.
Coke oven gas emitted from furnaces called direct and contains water vapor 250-450 m3, resin vapors 80-120 m3, benzene hydrocarbons 30-40 m3, ammonia 8-13 m3, hydrogen sulfide 6-30 m3, cyanide compounds 0,5-1,5 м 3.
With the coke chamber hot gas (t = 600-650°C) is given through the riser, which is connected to the knee cast iron gas collector located along the coke oven battery. In the riser through nozzle fed water with a temperature of 80°C, cooling and humidifying gas. Then the gas enters the separator. There wet resin is condensed and fed into mechanized clarifier where purified water.
The interaction of gas and cooling water in the gas collector is accompanied by heat and mass transfer.
The process of heat transfer is determined by the temperature difference between the gas and water. Since the gas temperature above the temperature oroshayuschey water, the heat is transferred from the gas to the water and it cools.
The driving force of the second process - the mass transfer is the difference between the elasticity of water vapor at the temperature and partial pressure of water vapor in the gas. Since the elasticity over steam enters the water more than the partial pressure of the gas coming from the coke oven chambers, the water evaporates.
So, the heat Qг, given that gas is partially transferred to obrazuyuschemusya couple mixes with the gas flow, heat and other gas cooling Qг - Q SPAN>п goes to heating water.
During the cooling gas and heating water temperature difference between them will be reduced, but at the same time will be reduced and the amount of heat transferred from the gas to the water. Clearly, the time comes when the magnitude Qг becomes equal Qі, followed by further heating the water becomes impossible, and all the heat received water from the gas goes to evaporation at a constant temperature. The limits of the cooling gas temperature correspond wet thermometer.
Then the gas enters the separator where the separation of the liquid phase and gas. As such, the coke oven gas is supplied Blower, she supercharger. The amount received direct COG for the entire battery is 37 thousand m3/ч. In a supercharger is a partial selection tumanoobraznoy resin with gas content 0.2-0.5 g/m3. Released into the supercharger resin flows through a special drain line hydraulic valve. As a result of the compression of gas in the supercharger generates heat that increases the temperature of the gas that comes out. Some of the heat is lost through the building, but it is very small compared to the total amount of heat released. After blowers gas temperature increases usually 15-25°С.
2.7 Analysis of the degradation processes
Coke oven gas has a broad composition containing corrosive agents and high temperatures. It has a decisive impact on the equipment. This leads to a relatively low its reliability and durability.
In the equipment of capture and transportation COG held a variety of manufacturing processes. Such as moving gas cooling, condensation of moisture from it. Thus these degradation processes occur:
- corrosion of internal surfaces in contact with the substance
- deposits on the pipe walls due to condensation
- change the properties of brick and the resulting deterioration of the lining through its agents saturation of the pipeline.
These degradation processes have a decisive influence on the technical condition of the equipment.
For example, sediments are deposited on the walls of the gas collector, lead to the following consequences:
- reduced section of the pipe;
- Increasing pressure;
- Rising energy costs;
- Changing hydraulic regime of motion of matter through the pipes;
- Changing the roughness of the walls of the pipeline;
- Worse heat transfer;
- Reduced strength due to corrosion of the pipeline.
In the primary gas cooler observed similar problems:
- through the interaction of metal structures with oxygen and corrosive working environments develops corrosion of metal ;
- Through friction fluid containing abrasive particles , the motion flow on metal wear surface UGS , but rather cover tube sheets and transitional knees
- When heated process water above the acceptable level on the inner surface of the tube formed salt hardness ( scale );
- Process of adhesion - attraction of liquid or solids at their molecular contact, which is necessary for initiation of external influence occurs in cases when the component cooling gas condenses on the outer surfaces of the tubes.
2.8 Formulation of research problems
At any given time properties of equipment and its specifications are subject to change. That is, instead of the original equipment have something different, with slightly different properties.
It follows that the design phase is required technical condition or prognosis of parameters at a given time. What may perform simulations based on changes in the technical condition of the equipment.
However , in practice, to obtain accurate data on the effect of all these processes is difficult : the rate of corrosion in different parts of the equipment is different , the amount of deposits as different physical and mechanical properties change in different ways. That is, all processes of equipment are probabilistic in nature and all property, both equipment and technology and degradation processes (size, roughness , physical and mechanical properties, temperature, pressure, corrosion rate , etc. ) are required to describe the expectation and variance.
To determine the probability of system failure must consider many factors. However, the factors determining the technical state is probabilistic, ie they are presented as a range of values and calculation results will also be probabilistic. Using this approach will significantly improve the accuracy of the reliability parameters several times.
So probability calculations when designing a constructive way to obtain quantitative estimates of performance reliability products at various stages of operation for the design. Since in this approach the performance of the product expressed in terms of statistics, it helps the designer to estimate warranty costs, develop a maintenance program and schedule the movement of stocks.
3 METHODS TECHNOGENIC SAFETY OF CHEMICAL EQUIPMENT
As stated in Section 1, the equipment under the influence of aggressive media has been steadily deteriorating. And, unfortunately, stop the process completely impossible. However, there are different methods for reducing the intensity of degradation effects on specific objects.
3.1 The theoretical basis of calculating technological safety
3.1.1 Analysis of boundary conditions in the area of ??carbon capture and transportation of coke oven gas
The purpose of this method is to avoid a certain probability of boundary conditions in a given operation throughout the life of the equipment, and the production of works.
The limiting condition - a condition in which the design fail to meet specified performance requirements or the requirements of the production work.
In calculating the effect of equipment static and dynamic loads and effects which they may be subjected in service and given life time, takes into account the boundary conditions of the first and second group.
The first group includes:
- overall buckling shape;
- Buckling position;
- Destruction of any nature;
- Transition structures in changeable system;
- Qualitative change configuration;
- State in which it is necessary to cease - operation resulting fluidity of the material, etc.
The second group includes conditions that impede the normal operation or reduce longevity due to the appearance of unacceptable displacements (deflections, sediment, rotation angles, vibrations, cracks, etc.).
Boundary conditions of the first group are checked expectation maximum (calculated) loads and impacts, there may be in violation of normal operation, and the boundary conditions of the second group - the operational (legal) burden and impacts that correspond to the normal operation of the equipment.
Reliability and warranty from the occurrence of limit states design provided with due regard to possible adverse characteristics of most materials; overload and the most unfavorable (but actually possible) link loads and impacts; conditions and characteristics of the work; proper selection of design schemes and assumptions settlement account, where appropriate, the plastic properties of materials.
For the first group of terms on the bearing capacity can be written in the general form
N≤Ф,
where N - force acting in the calculated structural elements (function loads and other effects);
Ф - marginal effort that can perceive calculated element (function of physical and mechanical properties of the material conditions of work and size of elements).
For the second group of boundary conditions associated usually with the movement, you can also record limit inequality:
f≤[f],
где f – The transfer structure (function loads);
[f] – boundary displacement allowed by the operating conditions (feature construction and its purpose).
In general, work structures and transition them into the ultimate state dependent loads, material properties and operating conditions. Consider the account of these factors when calculating the design for the boundary conditions.
During the operation of objects subjected to various loads and impacts.
Of the object, and, consequently, the features of the estimation depends much on the nature, scale and duration of exposure. Thus, the explosion should take into account the impact of loading rate on the properties of the material; when exposed to low temperatures - increased risk of brittle fracture; with prolonged exposure - the creep of the material.
Classification of loads and impacts.
The nature of the load and the effects are divided into:
- gravity load structures;
- Technological load (weight of the equipment is stored, the people, the pressure of liquids, gases, bulk materials, etc.);
- Atmospheric loads (snow, wind, ice);
- Temperature (technological and climatic) effects;
- Mounting pressure;
- Seismic and explosive effects;
- Emergency load arising from the severe disturbance of the process, equipment breakdowns, breakages wire transmission lines, etc.
All of these effects cause stress and in house efforts and move and can be attributed to the direct effects. In addition to these structures can affect the chemical (corrosion), radiation and other effects. These actions lead to changes in the material properties (toughness decrease in radiation exposure), change the parameters of the elements (elements thinning, increased stress concentration at corrosion) and eventually affect the bearing capacity and durability of structures. Such effects are called indirect.
Under the influence of nature to understand the rate and frequency of application of loads. On this basis the load is divided into static and dynamic variables repetitive.
Static Loaded loading rate is zero. It is so small that they cause inertial forces in the calculation can not be ignored. Under dynamic loading loading rate is high and the resulting inertia forces must be considered when calculating objects. Under the influence of variable repetitive stress in structures can be fatigue fracture. In this case, the design should check endurance.
Depending on the length of the load is divided into permanent and temporary. Temporary load in turn are divided into long, short and specific.
Call such a constant load acting on the structure constant: weight, pressure, impact prestressing of structures, etc.
Call such prolonged stress acting on the structure for a long time (but may not be): the weight of technological equipment, the weight of stocked goods, the pressure of liquids and gases in tanks and pipelines.
Intermittent load is called the load acting briefly: snow, wind, mobile cranes, load (arising during transportation, installation, repair, and testing), temperature climate action, etc.
Special load - a load that may occur in exceptional cases: seismic, accidental infringement process, sudden subsidence.
Regulatory and computational load. All load in one way or another at random and mathematical description can be represented as random variables (eg own weight structures) or random functions of time (eg, wind ). However, when calculating the limit state designs but take loads determined value. Therefore, to ensure the required level of reliability in the calculation of structures for the first group of limit states should take the maximum values of loads with a high degree of security. In the calculation of the second group of boundary conditions, ie in normal operation. Provision may be lower.
The main provisions of the rate set two values of stress: regulatory and settlement.
The load corresponding to normal operation, called normative. Their value is set in the standards of design, discussed in the specifications or design values determined by the geometrical parameters of the equipment or structures.
Possible deviations loads in unfavorable (more Fire smaller) side of their normative values as a result of natural variability of loads and deviations from normal operation takes into account the reliability factor of the load γj. The value of this coefficient depends on the nature of the load and its degree of variability. Thus, the gravity load of metal structures may deviate from normative in a fairly narrow range (due to tolerances on dimensions of sections, precision cutting, etc.), so that the load γj = 1,05.
The coefficients of reliability of the load is determined through a statistical analysis of the results of observations, experimental studies, or established on the basis of experience design.
Calculated loads are the largest in terms of probability and impact loads during operation of facilities.
Safety factor for load only take into account the variability of the load and the possibility of exceeding its legal values. They do not take into account the dynamic nature of the load or load promising growth over time, such as modernization and changing facilities. These factors are taken into account separately if necessary.
3.1.2 Analysis of technical risks in the removal and capture of COG
At risk should understand the expected frequency or probability of the dangers of a certain class or size of possible damage (loss, damage) of adverse events, or some combination of these variables.
Applying the concept of risk, thus allowing to transfer risk in the category of measurable categories. The risk, in fact, is a measure of risk. Often use the term "risk" is essentially no different from the concept of risk, but only emphasizes that it is a measured value
All these (or similar) interpretation of the term "risk" is currently used in the analysis of hazards and safety management (risk management) processes and industries as a whole.
Formation of hazardous and emergency situations - the result of a specific set of risk factors, generated by reliable sources.
With respect to security problems producing such an event can be an accident or a disaster of a technical system or device, pollution or destruction of the ecological system, the death of a group of people, material loss is realized hazards or increased spending on security.
Any adverse events may occur in relation to certain victims - Object risk. Value objects risks and adverse events allows us to distinguish individual, technical, environmental, social and economic risk. Each type is characterized by its source and determine the risk factors, classification and characteristics are presented in Table. 3.1
Table 3.1 - Classification and description of types of risk
Types of risk | Object risk | Source of risk | Adverse events |
Individual |
Person | Conditions of human life | Disease, injury, disability, death |
Technical |
Technical systems and facilities | Technical imperfections rules violation technical systems and facilities | The accident, explosion, accident, fire, destruction |
Ecological |
Ecological systems | Anthropogenic interference with the natural environment, man-made emergencies | Anthropogenic interference with the natural environment, man-made emergencies |
Social |
Social Groups | Emergency, decreased quality of life | Group of injury, illness, loss of life, increased mortality |
Economic |
Material Resources | Increased danger of production or environment | The increase in security expenses, loss of insufficient protection |
Individual risk can be voluntary if it is caused by human activity on a voluntary basis and enforced if a person is at risk as a part of society (eg, living in ecologically unfavorable regions near sources of high risk).
Technical risk - a composite index nadezhnostielementov technosphere. He vyrazhaetveroyatnost accident or disaster in the operation of machines, implementation of processes, construction and operation of buildings and structures:
where Rт - technical risk;
ΔT - number of accidents per unit of time t for identical technical systems and facilities;
T - number of identical technical systems and facilities exposed to common risk factors f.
Sources and technical risk factors listed in the table. 3.2
Table 3.2 - Sources and technical risk factors listed in the table.
Source of technical risk | The most common technical risk factors |
The low level of scientific research | Wrong choice of directions of technological development in technology for security criteria |
Same, development work |
Choosing a potentially dangerous design scheme and the principle of technical systems.
Errors in determining the operating loads. Wrong choice of construction materials. Insufficient margin. Lack of draft technical security measures. |
Experimental production of new technology | Poor proof construction, technology, documentation of the safety criteria |
Serial production of dangerous machinery |
Deviations from the desired composition of construction materials.
Lack precision structural dimensions. Violation of heat treatment details. Violation of the rules of addition and installation of structures and machines. |
Faulty safe operation of technical systems |
The use of technology for other purposes.
Violation of the passport regime of operation. Untimely preventive inspection and repair. Violations of transport and storage. |
Human error |
Weak skills performance in a difficult situation.
Inability to evaluate information about the process. Poor knowledge of the essence of the process is going on. Lack of self-control under stress. Indiscipline. |
3.1.3 Reliability analysis of capturing and purification of coke oven gas using fault tree
The most used method of analysis of possible equipment failures is the method of "fault tree". It is to construct and analyze models of reliability (security), which is a logical-probabilistic model of causality failures of the system failures of its elements, and other influences.
Main advantages of the method are:
- The high visibility of the presentation of the results of analysis, making them accessible to a wide audience (not just the security);
- Ability to perform both qualitative and quantitative analysis of security systems;
- Lets show explicitly unsafe locations of the system;
- Provides insight into the behavior of the system and its penetration into the process of work.
Disadvantages of "fault tree" are as follows:
- Implementation of the method requires a significant investment of money and time;
- Tree displays only two states of the system: working and otkazavshee;
- Fault tree describes the system at a certain time (usually in steady state);
- Requires professionals with a deep understanding of the reliability of the system and specific consideration whenever only one particular failure.
Despite extensive coverage in the scientific and technical literature, in practice, the specialists allow a number of methodological and logical errors. This leads to incorrectness of the results of safety analysis.
The main error is:
- Inconsistency of "tree" hierarchy of the system;
- Omission of significant factors and provide overweight irrelevant;
- Introduction false operators are not bearing meaning, but are involved in the calculation;
- Consideration of failures that do not affect the safety equipment;
- Improper use of logical symbols;
- Incorrect use of statistics.
Consider the key points of building a "fault tree" in engineering practice.
Before the construction necessary to analyze such sources of information about the object:
- Project documentation;
- Documentation manufacturers of equipment;
- Production schedules installation;
- Operational and repair records.
Based on these data the analysis process of operating the facility, and developed a list of possible failures and their causes.
Analysis of the process operation allows to obtain the necessary information to identify possible failures. It is conducted as follows:
- Determine the purpose of the system , especially its operation and for the tasks ;
- There are basic and auxiliary functions interim products;
- For each selected function determine the group of initial parameters , nominal and maximum allowable values ??for each parameter;
- Determine the types of system elements, their functional characteristics and the interaction of the operation , availability of reserve elements reveal elements that are unique ;
- Defines the features of the product ( primary and backup modes of operation, ability to work with modified output parameters , etc.);
- Determine the length of each period of operation.
List of possible failures should have sufficient detail due to the presence of the most probable and critical (that lead to the most serious consequences of) failures, but can not be over because of the inclusion of dependent failures. Failures that occur for the same reason, can be combined. In compiling the list of restrictions analyze the conditions of use, violation of which is considered as the possible rejection.
Simplified structure of "fault tree" can be represented as follows:
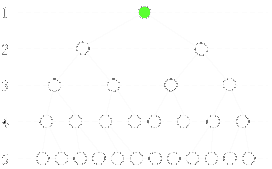
Figure 3.1 - Structure fault tree
Where
1) System failure
2) Disclaimer parts
3) Sailures of
4) Events that generate rejection
5) Types of effects
3.2 Practical methods
3.2.1 Methods of reducing corrosion degradation
Corrosion leads to billions in losses annually , and resolution of the problem is an important task. The main damage that caused by corrosion , is not the loss of the metal itself, and in the huge cost of merchandise destroyed by corrosion . That is why the annual loss of it in the industrialized world are so great . These losses it can not be determined , assessing only the direct losses , which include the cost of the destroyed structures, equipment replacement costs , the cost of measures to protect against corrosion. Even more damage make consequential loss. This downtime when replacing parts and components prokorrodirovavshih leaked product infringement processes.
Corrosion - a spontaneous fracture of metals as a result of chemical or physico-chemical interactions with the environment.
Depending on the nature of the corrosion process distinguish between chemical and electrochemical corrosion of metals.
The chemical corrosion destroyed in hostile environments due to the direct connection of the metal with aggressive chemical agents (eg iron oxidized).
In electrochemical corrosion fracture of metals is due to their dissolution in a liquid medium, which is the electrolyte, and is the formation on the surface of the many mikrohalvanichnyh items.
Corrosion of metals can be local, in the destruction of the surface in some areas, and even, when a metal is destroyed over the entire surface, and mezhkrystallytnaya when a failure occurs at the grain boundaries of the metal.
Direct indicators of corrosion
- Decline or increase in weight per unit surface of the metal;
- Depth of corrosion;
- Proportion of surface occupied by corrosion products;
- Number corrosive ulcers or points (foci corrosion) per unit surface area;
- Volume released per unit surface absorbed oxygen or hydrogen;
- Time before the first focus of corrosion;
- Time to occurrence of corrosion cracks or complete fracture of the specimen;
- Amperage corrosion;
Indirect indicators of corrosion
- Changing the physical and mechanical properties of the metal (tensile strength when tested in compression and tear, elongation, reflectivity, etc.);
- Change of resistance;
There are several methods of corrosion protection of metals. On the mechanism of action of all methods of corrosion protection can be divided into two main groups: electrochemical, influencing the potential of the metal or its critical value, and mechanical isolating metal from the environment and creating a protective film coating.
The main methods of corrosion protection include:
- Alloying metals
- Heat
- Inhibition environment
- Aeration environment
- Water treatment
- Protective Coatings
- Conditioning and protective atmosphere.
Methods of corrosion protection specified in working drawings of structures, snip, technical specifications (TU). A simple and effective way to protect metal structures from corrosion by coating their surfaces are different paints, varnishes, enamels.
Colorful coating, polymer coating and enamel must, above all, to prevent the access of oxygen and moisture. Often used as coatings, for example, were other metals such as zinc, tin, chromium, nickel. Zinc coating protects the steel even when the coating partially destroyed. Zinc has a negative potential and korrodiruyet first. Zn2 + ions are toxic. In the manufacture of tin cans used, covered with a layer of tin. Unlike galvanized gesture, in the destruction layer of tin korrodyrovat, though strenuously begins iron, because tin has a positive potential.
Formed on the surface of metal oxide films are divided into two types: tight and loose. Thick films of oxides violate environmental contact with the metal surface and thus protect the last of oxidation. Chubby films do not prevent oxidation. Thick oxide films formed by aluminum, lead, nickel, loose oxide film - calcium, magnesium, and others.
Modern chemistry makes it possible to produce high-quality paint materials, along with providing a chemical mechanical (fosfatyruyuschye soils) and electrochemical (protective ground) protection. Paints and coatings (for the proposed requirements and properties of their constituent components) are distinguished: anti-corrosion, water-resistant - protects metal from corrosion in areas with high humidity (ЕКЖС-40, ХС-78, soils ВЛ-02, №81, ФО-03Ж etc); Weatherproof - protect against atmospheric corrosion (ПХВ-29, ПХВ-35 , ХВ-124, ПФ-115, ХС-510 etc); heat-resistant - protects against corrosion of metal surfaces that are heated above 100°С, etc.
Another possibility to protect the metal from corrosion - use protective electrode with a high negative potential , such as zinc or magnesium. For this specially created corrosive element. The protected metal acts as a cathode, and this type of protection is called cathodic protection. Dissolved electrode, called, respectively, the sacrificial anode protection. This method is used for corrosion protection of marine vessels , bridges and boilers located underground pipes. To protect the hull on the outside of the shell are fixed zinc plate.
3.2.2 Methods to reduce the formation of deposits
The deposits formed on the inner surface of the pipeline are products of complex physical and chemical processes occurring on itself or on the deposited protective coatings, as well as transported by pipeline environment.
The nature of the deposits in the pipes is usually determined by:
- Physico-chemical properties of transported media;
- Operating conditions of the network;
- Service life of pipelines.
Preventing the formation and removal of sediments caused by hard water or corrosion is an important task, because of the following considerations:
1. The presence of sediments significantly affects heat transfer in heat exchangers, reduces bandwidth pipes. Thermal conductivity of sediments depending on their composition two or more times smaller than the thermal conductivity of construction materials;
2. Corrosive damage to equipment surfaces, including valves, greatly reducing their reliable performance and durability.
Salt sediments negatively affect the safe operation of pipelines. It causes increased local corrosion of metal pipes, which leads to rapid destruction.
Mechanisms to prevent the formation of deposits is determined by the ratio of the speed of crystal nucleation and crystal growth. The term "education centers krystalyzatsyy "refers to the spontaneous formation of microscopic particles (mikrokristalls) of dissolved ions, such as calcium carbonate crystallites of dissolved calcium and carbonate ions. These tiny crystals can spontaneously disintegrate or continue to grow to a certain size supercritical. Upon reaching this size they become makrokristallami and move in a stable state. The collapse stops and gradually formed large crystalline structures called "deposits".
In order to objectively and systematically solve problems associated with the formation of deposits, it is recommended to adhere to the following procedure:
Step 1. Define deposit formation
The most common place of deposit formation include centrifuges and piping, and pumps and heat exchangers.
Step 2. Determine the type of sediment
Type of initial cleaning, the choice and dosage of the products depend on the type of sediment. Type deposits can be with reasonable certainty to a certain place by using simple methods.
The salts of carbonic acid: formation of gas bubbles in the processing of acetic acid or citric acid.
Phosphates: slowly soluble in concentrated inorganic acids or alkalis without air bubbles.
Iron oxides : determined visually look like rust. A more precise determination of the composition of deposits is only possible in the laboratory.
Step 3. Choose the best reagent
Optimal inhibitor deposit formation can be selected with the aid of P-MAC, using simulations of the formation of sediment sample of water taken from the site of the alleged use of the reagent. In the case of very high iron content is quite effective inhibition of deposit formation can be achieved using polyacrylates .
Step 4. Determine the point of entering reactant
General rule :
Point input reagent should be as close as possible to the place of deposit formation , but must ensure uniform introduction to the mixture. Given the nature of chemical inhibitors of the formation of deposits their effectiveness may be weakened under the influence of other substances contained in the water. For this reason, you should not use reagents in the liquid phase at a large distance from the place of direct action .
Step 5 . Perform initial cleaning P>
Agents used to counteract the formation of mineral deposits are not able to remove deposits that are already present. Therefore, before using this reagent must perform initial cleaning , which if necessary can attract skilled professionals specialized organization .
Step 6 . Provide operational control and dosage
Of dosages products for dosing pumps using dosages based on empirical selection or laboratory recommendations. In most cases, the starting dose corresponds to the concentration of 30 ppm. The effectiveness of the reagent can be checked visually , for example, inspection of the inner surface deposit formation exposed pipes or pipe separate specially installed in the control purposes.
Dry cleaning has several disadvantages, the main ones are:
- Used reagents are highly toxic, with high corrosion activity and is caustic substances;
- The need for disposal of large volumes of spent reagents and their solutions. Consumption of detergents up to 10% of the carrier - which is about 1 m3 at 10m3 flushing volume;
- High risk of damage to equipment construction materials due to the high corrosive activity of drilling fluids. This applies to such construction materials as aluminum, bronze and steel.
- SW hit corrosive toxic liquids in residential and industrial premises in the event of leakage;
- Need heating system shut down during cleaning;
- The need for additional measures to prevent corrosion of equipment after cleaning.
CONCLUSION
This work has been described system catching and transportation coke oven gas includes gas collector, separator, primary gas cooler with horizontal pipes, supercharger for coke oven gas. Were analyzed working conditions of all elements of capture and transportation coke oven gas. We investigated the processes occurring in this equipment.
As a result of the foregoing, the following conclusions arising:
- Equipment removal and transportation of coke oven gas works in difficult conditions (pressure, temperature, corrosive environment).
- Such working conditions lead to the development of intensive degradation processes (erosion, sediment origin, changing material properties) that reduce system reliability.
- To ensure the safe operation of equipment should know the parameters of the technical state at any time in the process.
Using the above methods, we can calculate the technical risks given the reliability and maintenance of the object change. Previously, similar calculations for coke production technological change of the object is not taken into account. The proposed calculations are visible impact sediments and degradation processes in reliability.
To improve the reliability and security offered to perform a probabilistic calculation, which is to determine the probability of failure of the system, which takes into account many factors. However, due to the fact that the factors that determine the strength of the elements and the load is probabilistic, they are presented as a range of values??. Using this method it is possible to:
- Forecasting changes in the technical condition of equipment to capture and transport the coke oven gas with a given probability;
- accept responsibility for equipment acceptable combination of factors, the most dangerous and least responsible for such precision can be neglected.
To determine these quantities were made experimental studies of the properties of components most strongly exposed to degradation, such as the brick lining of the gas riser and metal samples from different parts of the technological path of the gas.
When writing this master's work, including design of it is not yet complete. Final completion: December 2014. Full text of the materials can be obtained from the author or his manager after that date.
References
- Коляндр Л.Я. Улавливание и переработка химических продуктов коксования. – Харьков, 1962. 22с.
- Коробчанский И.Е., Кузнецов М.Д. Расчеты аппаратуры для улавливания химических продуктов коксования. Харьков. Металлургия, 1952. - 55с.
- Александров К.И. Газодувки. - М.: Энергия, 1961. – 79с.
- Лебедев А.А., Ковальчук Б.И. Справочное пособие по расчету машиностроительных конструкций на прочность. – К., 1990. – 240с.
- Ковалев Г.М. Нагнетатели коксового газа. М.: Металлургия, 1972.–190с.
- Соколов Ю.Н. Основы единой теории лопастных машин. – Томск, 1973. – 218с.
- Юдин Е.М. Шестеренные насосы. – М.: Машиностроение, 1964. – 75с.
- Бондаренко М.С., Иванченко В.В. Справочник механика химических производств. – Донецк: Донбасс, 1988. - 208с.
- Хенли Э. Джм Кумамото X., Надежность технических систем и оценка риска: — М.: Машиностроение, 1984.
- Капур К., Ламберсон Л. Надежность и проектирование систем. – Москва, 1980.