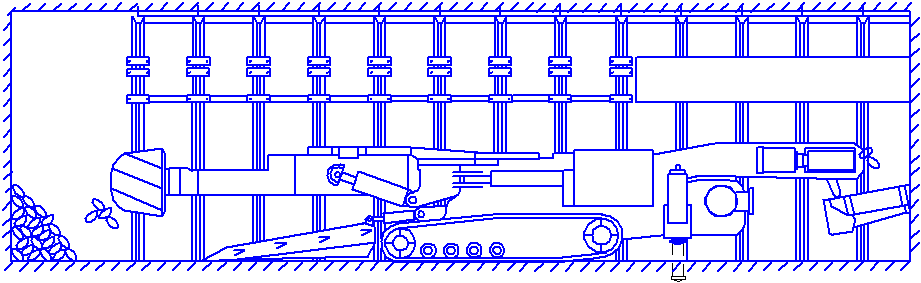
Содержание
- Введение
- 1. Актуальность, состояние, цель и задачи
- 2. Анализ систем перемещения проходческого комбайна
- 2.1. Анализ конструкции системы перемещения проходческого комбайна
- 2.2. Структурная схема системы перемещения проходческого комбайна
- 2.3. Выбор блока исполнительного органа
- 3. Повышение эффективности работы
- 3.1. Анализ структурных схем отработки тонкого пласта
- Выводы
- Список источников
Введение
Объектом исследования является система перемещения проходческого комбайна для проведения подготовительных выработок при интенсивной выемке тонких пластов.
В настоящее время развитие добычи угля в Украине характеризуется постоянным ростом нагрузки на добычной забой. Основными способами проведения подготовительных выработок являются буровзрывной и комбайновый. Уровень механизации основных технологических операций по проведению подготовительных выработок (разрушение горного массива и погрузка горной массы) на угольных шахтах Украины составляет 80–85%. Рассмотрим комбайновый способ проведения подготовительных выработок. [1]
Использование ПК позволяет совместить во времени основные, наиболее трудоемкие операции, что дает возможность повысить в 2–2,5 раза производительность труда и темпы проведения выработок, снизить стоимость проходческих работ и значительно обезопасить труд рабочих подготовительного забоя в сравнении с буровзрывным способом. Кроме того, при комбайновом способе проведения существенно повышается устойчивость гонных выработок, так как связанность пород в массиве нарушается в меньшей степени, чем при буровзрывных работах. Последнее обстоятельство позволяет снизить расходы на поддержание выработок. Среднемесячные темпы проведения выработок проходческими комбайнами в среднем в 2,7 раза больше, а производительность труда проходчиков в 1,6 раза выше, чем при проведении выработок буровзрывным способом.
1. Актуальность, состояние, цель и задачи
Эффективность работы горнодобывающей промышленности, являющейся основной сырьевой и энергетической базой для всех отраслей народного хозяйства, определяется техническим уровнем средств механизации и автоматизации технологического процессов добычи. В условиях рыночных экономических отношений, основными требованиями для горно–шахтного оборудования становятся:
–повышение эффективности и безопасности эксплуатации;
–снижение металлоемкости машины и энергоемкости разрушения горной массы;
–уменьшение экологической вредности горных работ.
Одним из факторов, наиболее сдерживающих рост нагрузки на современные добычные комплексы, является отставание в подготовке нового фронта очистных работ. Эта задача реально выполнима при проходке горных выработок с темпами 400–600 м/месяц. Такие темпы проходки может обеспечить только комбайновая технология проведения выработок, которая наиболее полно отвечает требованиям экономической эффективности горно-подготовительных работ. В настоящее время все больше широкое применение на шахтах Украины и за рубежом получают проходческие комбайны со стреловидными исполнительными органами, оснащенными коронками различной конфигурации.[2-6]
Применение проходческих комбайнов избирательного действия по горно–геологическим и горно-техническим условиям возможно в 60–65% проходческих забоев. Вместе с тем до настоящего времени уровень механизации проведения горных выработок комбайновым способом составляет всего 30–35 %. Малые фактические объемы проведения выработок проходческими комбайнами вызваны следующими причинами:
недостаточным объемом поставок этих комбайнов шахтам;
–вновь получаемые комбайны идут на замену старых (прирост комбайнового парка на действующих шахтах Украины прекратился с 1986 г.);
–технический уровень используемого на шахтах проходческого оборудования и его надежность не обеспечивают возможности дальнейшего существенного повышения темпов проходки, производительности труда проходчиков и уровня механизации процесса крепления.
Целью данной работы является – обоснование структуры и параметров предложенной структуры системы перемещения проходческого комбайна для проведения подготовительных выработок при интенсивной выемке тонкого пласта
Задачи для решения:
1) Сокращение времени затрачиваемого на проведение маневровых операций.
2) Анализ систем перемещения и предложение новой структуры системы перемещения
3) Обоснование структуры и параметров системы перемещения ПК.
2. Анализ систем перемещения проходческого комбайна
2.1. Анализ конструкции системы перемещения ПК
Мировая практика ведения горных работ имеет тенденцию к постоянному увеличению числа проходческих комбайнов избирательного действия наряду с необходимостью расширения области их применения. Все более широко на шахтах Украины и за рубежом применяются проходческие комбайны со стреловидным исполнительным органом, оснащенным аксиальными коронками. Эти комбайны используются при проходке подготовительных выработок на угольных шахтах, строительстве туннелей, а также для выемки при подземной разработке соляных и рудных месторождений. Прилагаемые в последнее время усилия, направленные на дальнейшее расширение области применения и повышение производительности проходческих комбайнов избирательного действия все чаще не дают ожидаемых результатов. Именно это определяет актуальность поиска путей и методов совершенствования и оптимизации этих машин и их подсистем, в частности, системы подачи исполнительного органа.
Основные показатели технического уровня горных машин – производительность, надежность и металлоемкость. Определяющее влияние на эти показатели оказывает процесс разрушения массива исполнительным органом, причем его система подачи принимает в этом процессе самое непосредственное участие. Это, в конечном счете, определяет техническую производительность комбайнов и эффективность ведения подготовительных работ.
Ходовое оборудование проходческих комбайнов предназначено для:
- создания напорного усилия на забой при разрушении горного массива и при погрузке отбитого материала;
- маневрирования комбайном в забое во время работы;
- транспортирования комбайна при перегонах по горным выработкам.
В зависимости от горнотехнических условий применяют гусеничное или шагающее ходовое оборудование. Причем наибольшее распространение получило гусеничное ходовое оборудование из–за высокой маневренности и удобства в эксплуатации.
Сравнение систем перемещения проходческих комбайнов
Гусеничное ходовое оборудование
В зависимости от типа привода различают гусеничное ходовое оборудование с электрическим и гидравлическим приводом. Приводы гусеничных ходов бывают двух типов: общий на две гусеницы и раздельный на каждую гусеницу. Один привод на две гусеницы в проходческих комбайнах применяют редко, обычно применяются раздельные как электрические, так и гидравлические приводы. При раздельном электрическом приводе редукторы приводов двух гусениц выполняются в одном корпусе или в самостоятельных корпусах.
Центральная рама, к которой крепятся две ходовые тележки, обычно служит базой машины и на ней же монтируются все исполнительные механизмы и узлы. Каждая гусеничная тележка состоит из рамы, гусеничной цепи, опорных катков, ленивца и натяжного устройства.
Мощность привода ходовой части должна обеспечивать движение комбайна при заданных углах наклона выработки со скоростью 0,08–0,11 м/с.
Шагающее ходовое оборудование
Предназначено в основном для создания напорного усилия на забой и не приспособлено для маневрирования комбайном, шагающее ходовое оборудование создает цикличное движение с помощью четырех гидродомкратов. Два распорных гидродомкрата встроены в балку и производят распор балки в боковые стенки выработки. Два подающих гидродомкрата, цилиндры которых прикреплены к корпусу главного двигателя, а штоки к балке, подают комбайн на забой при распертой балке. После этого давление в гидродомкрате снимается и балка с помощью вспомогательных гидродомкратов подается вперед. Шаг подачи обычно составляет 0,7 м.
2.2. Структурная схема систем перемещения ПК
Проанализировав вышеизложенное, предоставим усовершенствование шагающего ходового оборудования. Для повышения маневренности и упрощения конструкции ходового оборудования проходческого комбайна используем механизированную крепь поддерживающего типа. Механизированная крепь в составе проходческого комбайна предоставляет возможность решения задачи с металлоемкостью так, как рама крепи заменяет корпус и ходовое оборудование проходческого комбайна.
Ходовая часть гусеничных ПК представляет собой самоходную гусеничную тележку и предназначена для движения, поворотов и разворотов комбайна. Привод гусениц осуществляется от общего электродвигателя через коническую передачу и кинематические цепи, включающие в себя два рабочих и два тормозных фрикциона.
Давление на почву должно быть не более 0,05–0,1 МПа. У тяжелых мощных комбайнов оно может достигать 0,2 МПа. В тех случаях, когда для работы комбайнов требуются большие напорные усилия (при работе по крепким породам), применяется распорно-шагающее гидравлическое ходовое оборудование, которое является ходовым оборудованием цикличного действия.[12,14]
Перевод комбайнов с шагающим ходовым оборудованием в другие выработки не может осуществляться своим ходом, как комбайнов на гусеничном ходу, и требует дополнительных транспортных средств.
Основной вид энергии проходческих комбайнов – электрическая энергия. В состав электрооборудования комбайнов входят: электрические двигатели для привода исполнительных органов, органов погрузки, перегружателей и органов перемещения (кроме шагающе–распорного ходового оборудования и некоторых гусеничных ходов, оснащенных гидродвигателями), а также для привода насосов маслостанций комбайнов; магнитные станции с аппаратурой управления и защиты; электрические пульты управления; аппаратура сигнализации и освещения; кабельная сеть и электрическая арматура. В проходческих комбайнах получили также широкое распространение системы силового объемного гидропривода типа насос – силовой гидроцилиндр и насос – гидромотор.
В качестве рабочей жидкости гидросистем комбайнов можно применять минеральное масло, но в целях предотвращения пожаров правилами безопасности требуется применение огнестойкой нетоксичной рабочей жидкости. Такая жидкость представляет собой мелкодисперсную эмульсию воды и минерального масла (46 % воды и 50 % масла) с добавлением 4 % антизадирных, антикоррозионных и противопенных присадок.[5-10]
При интенсификации выемки тонких пластов необходимыми требованиями к ПК являются: высокая производительность; скорость перемещения ПК; усилия, приложенные к массиву для его разрушения; температура нагрева элементов приводов и рабочих органов; действующие нагрузки в приводах исполнительных механизмов.
Предлагаемая система перемещения проходческого комбайна состоит из трех секций механизированной крепи поддерживающего типа, таким образом, перемещение проходческого комбайна производится путем передвижки секций крепи, что одновременно позволяет передвижку конвейера. В процессе работы произведена поддержка породы кровли, что позволяет повысить устойчивость проходческого комбайна. Управление такой системой перемещения проходческого комбайна значительно упрощается тем, что для передвижки комбайна требуется только управление механизированной крепью, не включая дополнительно никаких электроприводов.
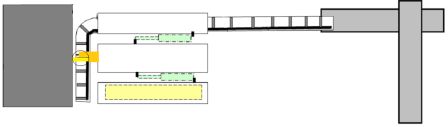
Рисунок 1 – Структура ходовой части ПК вид сверху
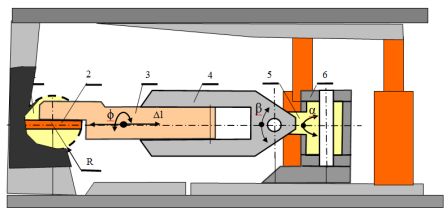
Рисунок 2 – Структура проходческого комбайна для проведения подготовительных выработок при интенсивной выемке тонких пластов
2.3. Выбор блока исполнительного органа
Стреловидный исполнительный орган комбайна представляет собой блок редукторов с электродвигателем и режущей коронкой, установленный в направляющей П–образной раме. С помощью двух гидроцилиндров, вмонтированных в раму, блок может выдвигать по ее направляющим на 900 мм, что позволяет проводить выработки сечением вчерне до 35 м^2 и производить до двух зарубок коронки в забой без включения гусеничного хода и подъема аутригеров.
Гидроцилиндры поворотов стрелы комбайна в горизонтальной и вертикальной плоскостях за счет ступенчатого изменения расхода поступающей в них рабочей жидкости обеспечивают перемещение стрелы в указанных плоскостях с тремя рабочими скоростями.
Для интенсификации отработки забоя и более точной формы сечения выработки , устанавливается блок исполнительного органа от погрузочно–поддирочной машины МПР. Использование такого блока исполнительного органа основывается на его структуре так, как на П–образной раме установлена телескопическая стрела с возможностью поворота исполнительного органа вокруг своей оси. Что позволяет отрабатывать забой под любым углом и разнообразной формы сечения выработки. В качестве инструмента для разрушения горного массива используется дисковый исполнительный орган.[15,13]
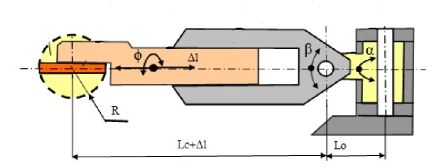
Рисунок 3 – Схема блока исполнительного органа машины МПР с использованием диска
3. Повышение эффективности работы
3.1. Анализ структурных схем отработки тонкого пласта
Для анализа влияния интенсивности выемки тонкого пласта на темпы был произведен расчет длины суточной проходки зависящей от суточной производительности на пластах различной мощности m=(0,5;0,7)м.
Приведем расчетную формулу:
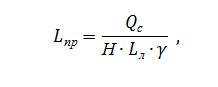
где:
Lпр – суточная длина проходки, м/сут;
Qc – суточная производительность комбайна, т/сут;
Lл – длина лавы, м;
Н – мощность отрабатываемого пласта, м;
v – плотность угля, т/м^3.
Для оценки требуемых темпов проходки были рассчитаны их значения в зависимости от суточной производительности комбайна (Рис 4 и Рис.5) при выемке пластов мощностью Н =0,5 м и Н=0,7м для длин лавы Lл =100м и Lл =200 м.[3,4]
Представим расчет по большей суточной производительности:
При Qc = 3000,т/сут; Lл=100,м; v=1,3; Н=0,5 ,м, получаем Lпр=46.15,м, а при Qc = 3000,т/сут; Lл=200,м; v=1,3; Н=0,5 ,м; Lпр=23.07,м.
При Qc = 3000,т/сут; Lл=100,м; v=1,3; Н=0,7 ,м, получаем Lпр=32.97,м, а при Qc = 3000,т/сут; Lл=200,м; v=1,3; Н=0,7 ,м; Lпр=16.48,м.
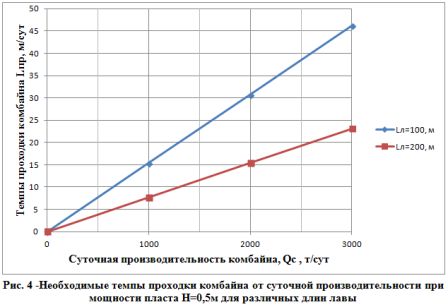
Рисунок 4 – Необходимые темпы проходки комбайна от суточной производительности при мощности пласта Н=0,5м для различных длин лавы
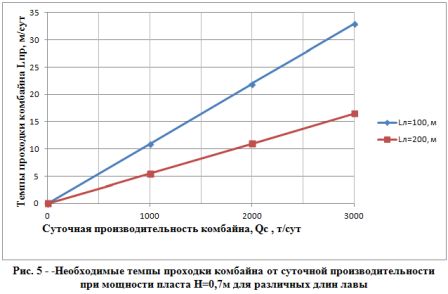
Рисунок 5 – Необходимые темпы проходки комбайна от суточной производительности при мощности пласта Н=0,7м для различных длин лавы
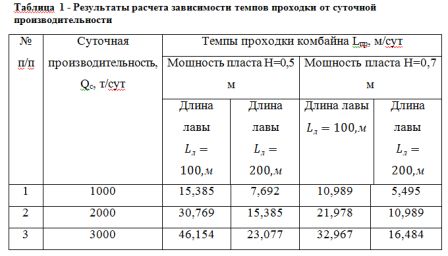
Из приведенного расчета видно, что при одинаковых значениях суточной производительности Qc и длине лавы Lл на пластах различной мощности существенно будут отличаться значения темпов проходки Lпр. На основании этого можно сказать, что для интенсивной выемки тонких пластов эффективнее применять лавы длиной Lл=200,м. Так как время на монтаж и демонтаж оборудования занимает большой срок, порядка одного месяца, отсюда видно, что при сегодняшних суточных производительностях и скоростях перемещения очистных комбайнов, необходимая суточная производительность проходческого комбайна должна превышать 2000–3000 т/сут и приемлемыми темпами проходки являются Lпр = 23,077 м для пласта Н=0,5м и Lпр = 16,484м на пластах Н=0,7м.[8,7]
На основе проведенного анализа предложим возможные технологические схемы для выемки тонкого пласта:
На Рис. 6 (а) представлена технологическая схема для интенсивной выемки тонкого пласта с опережением лавы проведением подготовительной выработки, проходка выработки осуществляется на 20–30 м вперед от лавы вдоль линии вынимаемого столба полезного ископаемого. Отбитая порода транспортируется скребковым конвейером и производится закладка бутовой полосы для временного поддержания породы кровли выработанного пространства вдоль ново–проходящей выработки на ширину 5м. По мере продвижения лавы, в ремонтные смены, производится ревизия конвейера, разбирают часть конвейера транспортном штреке и наращивают ее к конвейеру в проводимой подготовительной выработке (после проходческого комбайна).
Возможна и закладка бутовых полос вдоль лавы по выработанному пространству для более надежного крепления пород кровли.
На Рис.6 (б) представлена технологическая схема для интенсивной выемки тонкого пласта с проведением подготовительной выработки с отставанием на 20–30 м от проведения лавы. Также закладывая бутовую полосу вдоль линии забоя.
Для удобства крепления и проведения, выработку проводим прямоугольного сечения площадью 8–10 м^2.[11-18]
Рассчитаем длительность выемки столба по формуле:
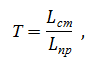
где:
Lст =2000 – дина вынимаемого столба, м;
Lпр – темп проходки, м/сут.
Для пласта мощностью Н=0,5м и длинной лавы Lл=200 м при суточной производительности Qс=3000т/сут:
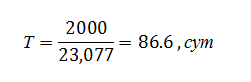
Для пласта мощностью Н=0,7м и длинной лавы Lл=200 м при суточной производительности Qс=3000т/сут:
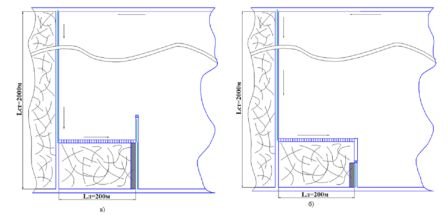
Рисунок 6 – Технологические схемы для интенсивной выемки тонкого пласта
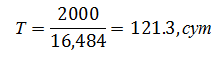
По полученным максимальным (для данной работы) результатам длительности выемки столба можно сказать, что время на монтаж и демонтаж занимает для первого случая 1/3 времени выемки столба, а во втором случае – 1/4 часть времени. Исходя из этого, необходимо уменьшить металлоемкость комбайна, что сократит время, затраченное на монтаж и демонтаж ПК. Для решения этой задачи необходимо упростить структуру комбайна, путем применения новой структуры системы перемещения проходческого комбайна, роль которой будет выполнять механизированная крепь.
Проанализировав данные работы комбайна типа КПД (экспериментальная работа Степаненко Е. Ю.) при проведении подготовительной выработки, получили, что время, затраченное на маневровые операции, занимает 85,86% времени работы комбайна.
В связи с такой ситуацией, возникает необходимость сокращения времени маневровых операций, что повысит скорость проходки. Путем достижения этой цели является повышение технического уровня ПК.
Одним из направлений повышения эффективности работы ПК является увеличение их технической производительности за счет сокращения потерь времени на простои и холостой ход привода резания, что может быть достигнуто при оснащении комбайна мехатронной системой подачи ИО, реализующей совмещение во времени двух его движений во взаимно перпендикулярных направлениях, с адаптивным компьютерным управлением процесса обработки забоя.[9,16]
Выводы
Одним из возможных направлений обеспечения высоких темпов проходки, является сокращение времени затрачиваемого на маневровые операции путем повышения технического уровня проходческого комбайна.
Способность комбайна обеспечить совмещение операций во времени позволяет значительно сократить длительность рабочего цикла прохождения выработки и сокращение времени затрачиваемого на монтаж и демонтаж комбайна, а возможность прохождения выработок с высоким качеством боковых поверхностей и почвы – значительно повысит эффективность его работы за счет снижения объема забутовки. Возможность работы комбайна по крепким породам с меньшей энергоемкостью и более высокой производительностью.
Для повышения технического уровня проходческого комбайна для эффективной проходки подготовительных выработок при интенсивной выемке тонких пластов была предложена структура системы перемещения ПК, в которой исключается ходовая часть ПК. Предлагаемая структура системы перемещения значительным образом изменяет и всю конструкцию проходческого комбайна. В данной схеме (Рис.2) показано, что исполнительный орган устанавливается на корпус механизированной крепи, что упрощает конструкцию комбайна, снижает металлоемкость и позволяет сократить время, затраченное на маневровые операции. Система перемещения комбайна состоит из трех секций механизированной крепи, что обуславливает перемещение ПК вдоль линии забоя за счет передвижки крепи межсекционными гидродомкратами и передвижку скребкового конвейера. Механизированная крепь обеспечивает поддержку породы кровли забоя, тем самым повышается устойчивость комбайна. Для простоты крепления кровли и боковых поверхностей подготовительных выработок, выемка разрушаемого массива производится прямоугольным сечением выработок.
Список источников
- Комплексная механизация и автоматизация очистных работ в угольных шахтах. Под общей ред. Б.Ф. Братченко. М., "Недра", 1977. с. 415.
- Горбатов П. А. Гірничі машини для підземного видобування вугілля. – Донецьк, 2006.
- Шабаев О.Е., Семенченко А.К., Хиценко Н.В., Семенченко Д.А., Степаненко Е.Ю. Повышение ресурса проходческих комбайнов с аксиальными коронками на основе регулятора нагрузки в системе подачи исполнительного органа // Наукові праці Донецького національного технічного університету, Вип. 16 (142), Серія: Гірничоелектромеханічна, Донецьк, 2008. – С. 265–274.
- Семенченко А.К., Шабаев О.Е., Семенченко Д.А., Хиценко Н.В. Принципы создания проходческих комбайнов как мехатронных систем // Наукові праці Донецького національного технічного університету. Серія: Гірничо-електромеханічна. Випуск 113. – Донецьк, 2006. – С. 238–243.
- Проектирование и конструирование горных машин и комплексов: Учебник для вузов / Малеев Г. В.; Гуляев В. Г.; Бойко Н.Г. и др. – М.: Недра, 1989.
- Семенченко Д.А. Обоснование параметров исполнительного органа проходческих комбайнов с аксиальными коронками: Дис. ... канд. техн. наук: 05.05.06. – Донецк, 2003. – 158 с.
- Горные машины для подземной добычи угля / П.А. Горбатов, Г.В.Петрушкин, Н.М. Лысенко, С.В. Павленко, В.В. Косарев. – Донецк: ДонНТУ, 2006. – 669с.
- Малевич Н. А. Горнопроходческие машины и комплексы. – М.: Недра, 1980. – 384с.
- Машины и оборудование для проведения горизонтальных и наклонных горных выработок. Под. pед. Братченко Б. Ф. – М: Недра, 1975. – 416с.
- Перспективы создания проходческих комбайнов нового технического уровня / Семенченко А. К., Шабаев О. Е., Семенченко Д. А., Хиценко Н. В. (Донецкий национальный технический университет) // Каталог-справочник "Горная техника – 2005"http://library.stroit.ru/articles/combain2/index.html.
- Ржевский В.В. Открытые горные работы. Часть 1 и 2. М., Недра.2005.
- Анистратов Ю.И. Технология открытой добычи руд редких и радиоактивных металлов.М.,Недра,2008.
- Брюховецкий О.С., Бунин Ж.В., Ковалев И.А. Технология и комплексная механизация разработки месторождений полезных ископаемых. М.,Недра,2009.
- Фомин С.И. Основы технологии горного производства.СПб.,2004.
- Справочник открытые горные работы. М., Недра, 2005.
- Кулешов А.А. Проектирование и эксплуатация карьерного автотранспорта. Справочник. Часть 1 и 2. СПб., изд. СПГГИ, 2005.
- Единые правила безопасности при разработке месторождений полезных ископаемых открытым способом. М., Недра, 2004.
- Вернер И.В., Мороз А.И., Симанович Г.А., Тарасенко А.А., 2000 г.