Реферат по теме выпускной работы
Содержание
- Введение
- 1. Актуальность темы
- 2. Обзор существующих методов определения оптимальных режимов резания при шлифовании
- 3. Оптимизация режимов шлифования с использованием понятия "текущая лимитированная режущая способность круга"
- 3.1 Схемы обработки при внутреннем шлифовании
- 3.2 Введение понятия "текущая лимитированная режущая способность круга"
- 3.3 Ограничения, налагаемые на режимы обработки при шлифовании по схеме с постоянным усилием поджима
- 3.4 Методика определения усилия поджима
- 3.5 Устройство для внутреннего шлифования с постоянным усилием поджима РПК к заготовке
- 4. Разработка устройства автоматической подачи на глубину бабки изделия внутришлифовального станка модели 3А227П в соответствии с законом изменения режущей способности круга
- 4.1 Кинематическая схема устройства перемещения бабки изделия
- 4.2 Автоматическая система управления перемещением бабки изделия
- 4.3 Определение закона изменения текущей лимитированной режущей способности для программирования автоматической системы управления
- 4.4 Описание конструкции модернизированного привода подачи на глубину бабки изделия
- Выводы
- Список источников
Введение
1. Актуальность темы
В настоящее время, повышение производительности обработки при минимальных затратах на производство, с обеспечением требуемых показателей качества являются необходимыми условиями выпуска конкурентоспособной продукции. Решение этих задач возможно за счет оптимизации параметров режима обработки: скорости круга, скорости детали и глубины резания [1]. Скорость круга принято назначать максимальной исходя и технических возможностей станка с целью обеспечения максимальной производительности, скорость детали в наибольшей степени определяет шероховатость шлифованной поверхности, а глубина резания существенно влияет на производительность обработки и качество шлифованной поверхности [2].
В существующих исследованиях [1, 3], задача оптимизации глубины шлифования труднообрабатываемых материалов решается путем экспериментального ее определения с использованием многофакторных экспериментов. Этому способу решения характерна высокая трудоемкость исследований и большие временные затраты. В ряде работ [4, 5] данная задача решается с использованием схемы шлифования с постоянным усилием поджима рабочей поверхности круга (РПК) к заготовке. Данная схема позволяет исследовать процесс шлифования вне зависимости от текущего состояния РПК, тепловых и динамических процессов, сопровождающих резание. Схема шлифования с постоянным усилием поджима позволяет определить закон изменения режущей способности круга во времени, который дает возможность оптимизировать глубину шлифования при обработке по схеме с постоянной глубиной резания.
Поскольку в существующих исследованиях отсутствуют сведения по исследованию режущей способности алмазных шлифовальных кругов при внутреннем шлифовании образцов из твердого сплава по схеме с постоянным усилием поджима, а также сведения об определении рациональных режимов обработки, то целью работы является обоснование оптимальных режимов резания изделий из твердых сплавов при внутреннем шлифовании кругами из синтетических алмазов.
Объект исследования: изменение режущей способности рабочей поверхности алмазного круга, заправленного электроэрозионным способом, при внутреннем шлифовании твердого сплава.
Практическая ценность результатов работы.
- Разработка нового устройства, для обеспечения автоматической подачи бабки изделия внутришлифовального станка модели 3А227П в соответствии с законом изменения текущей лимитированной режущей способности круга, в котором за счет новых конструктивных элементов и системы управления обеспечивается возможность внутреннего шлифования отверстий с использованием в полной мере режущих свойств шлифовального круга;
- Определен закон изменения текущей лимитированной режущей способности круга для конкретных условий обработки, необходимый для программирования автоматической системы управления разработанного устройства;
- Полученный закон может быть использован для оптимизации процесса шлифования.
2. Обзор существующих методов определения оптимальных режимов резания при шлифовании
Входными данными для определения режимов резания при шлифовании являются:
- Информация об обрабатываемом материале и размеры шлифуемой поверхности;
- Припуск на обработку;
- Требования к точности, шероховатости обрабатываемых поверхностей и другим показателям качества;
- Информация о станке;
- Жесткость системы станок – деталь – устройство – круг;
- Характеристика круга, которым проводят обработку на данной операции.
Режимы резания при шлифовании могут быть определении расчетным путем или назначены на основе практических рекомендаций. Расчет режимов шлифования целесообразно проводить для условий массового производства, когда незначительные отклонения от оптимальных требований обработки могут привести к существенным потерям. Расчет режимов целесообразно также проводить при разработке различных нормативов и рекомендаций, относящихся к изготовления шлифовальных кругов.
Задача определения оптимального режима шлифования выполняется в три этапа:
- Составление системы уравнений, описывающих технические ограничения, налагаемые на режим резания требованиями к детали, станку, инструменту и требованиями производства.
- Математическое описание целевой функции, т.е. функции, выражающей цель оптимизации.
- Совместное рассмотрение технических требований и целевой функции и определение на этой основе оптимальных режимов шлифования [1].
Математическое выражение, описывающее технические ограничения, однотипны и могут быть представлены в виде неравенств, в левой части которых приведено заданное (предельное) значение какой-либо ограничивающей величины, или параметра, а в правой – фактическое значение этой величины или параметра при той или иной комбинации элементов режима резания и других заданных требований обработки.
Технические ограничения, налагаемые на режим резания требованиями к изделию, следующие:
- Предельно допустимая высота шероховатости Ra на обработанной поверхности;
- Необходимая точность детали после шлифования;
- Температура шлифуемой поверхности, предельно допустимая с точки зрения прижогов, остаточных напряжений или других показателей качества поверхностного слоя детали.
Технические ограничения, налагаемые на режимы резания станком, следующие:
- Мощность привода шлифовального круга;
- Наибольшие и наименьшие частоты вращения шпинделя и значение подач, которые предусмотрены кинематикой и конструкцией соответствующих механизмов станка (nmax, nmin, vmax и vmin и т.п.).
В связи с малыми значениями сил, возникающих при шлифовании, прочность механизма станка, как правило, не ограничивает режимы резания. Исключениями могут быть случаи чернового шлифования и обработки деталей на станках с одновременным шлифованием несколькими кругами.
Технические ограничения, налагаемые на режим резания шлифовальным кругом, следующие:
- Требуемая стойкость инструмента;
- Предельная температура на режущих зернах;
- Прочность круга.
Комплекс технических ограничений описывает область возможных режимов шлифования. Если оптимизации подвергается комплекс из двух элементов режима резания, а остальные элементы режима заданы, то упомянутая область изображает собой плоскую фигуру, очерченная соответствующими линиями. На рис. 2.1 в общем виде показана схема построения области возможных режимов резания в случае, когда находится оптимальное сочетание скорости детали и глубины резания (поперечная подача). Линиям на рисунке присвоены наименования ограничений ТО1 – ТК3, что упоминались выше. Если оптимизируется комплекс из трех элементов режима работы, то каждое ограничение описывается не линией, а поверхностью того или иного вида, а область возможных режимов шлифования превращается в трехмерное пространство. При большем количестве элементов, характеризующих режим резания, область возможных режимов вращается в четырех или более мерное пространство.
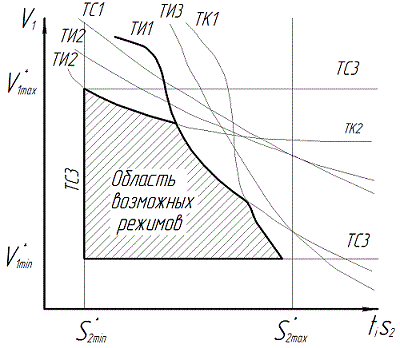
Рисунок 2.1 – Схема области возможных режимов
Целевые функции представляют собой математическое описание цели, с которой производят оптимизацию режима шлифования. В зависимости от конкретных условий производства при оптимизации можно обеспечить наименьшую себестоимость обработки на данной операции, достижение на данной операции наибольшей производительности, минимальные затраты на инструмент. Могут быть и другие конкретные цели оптимизации.
Таким образом, в области возможных режимов, описанных техническими ограничениями и графически изображенных на рис. 1.1, необходимо отыскать точку, для которой все ограничения будут удовлетворены при максимальных значениях режимов, отвечающих наибольшей производительности, она и будет отвечать оптимальному режиму шлифования.
Недостатком рассмотренного метода нахождения оптимальных режимов при шлифовании новых материалов или кругами с новыми характеристиками заключается в том, что он требует значительных затрат времени для нахождения зависимостей, описывающих технические ограничения. Кроме того, он дает результаты, которые невозможно использовать в случае, когда режимы при обработке выходит за пределы, в которых были найдены уравнения технических ограничений, а также не учитывает изменение режущей способности РПК при работе.
3. Оптимизация режимов шлифования с использованием понятия "текущая лимитированная режущая способность круга"
3.1 Схемы обработки при внутреннем шлифовании
Внутреннее шлифование применяется для обработки поверхностей цилиндрических, конических и фасонных отверстий на универсальных и специальных станках. Обработка металлических и неметаллических материалов при внутреннем шлифовании может выполняться по двум схемам: с постоянным усилием поджима и постоянной глубиной шлифования (рис. 3.1, 3.2).
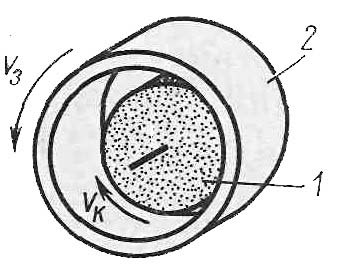
Рисунок 3.1 – Схема внутреннего врезного шлифования с постоянной глубиной резания: 1 – заготовка, 2 – шлифовальный круг
При шлифовании отверстий (рис 3.1) подача осуществляется только перпендикулярно оси отверстия, из-за чего форма рабочей поверхности круга переносится на обрабатываемую поверхность [6].
Врезное шлифование применяют для обработки поверхностей, длина которых не превышает ширину шлифовального круга. Его преимущество – большая производительность и простота наладки. Врезное шлифование широко применяют в массовом и крупносерийном производстве.
По сравнению с обычным шлифованием по схеме с постоянной глубиной резания, шлифование с определенным радиальным давлением (рис. 3.2), по мнению Л. А. Глейзера, представляет собой достаточно устойчивый процесс, обладающий большей степенью детерминированности [3]. Шлифование по схеме с постоянным усилием поджима Py шлифовального круга к заготовке позволяет исключить влияние на температуру шлифования, непостоянства припуска, нестабильности физико-механических свойств материала изделия и изменения режущей способности шлифовального круга за период его стойкости, что снижает опасность появления дефектов на шлифованной поверхности [7].
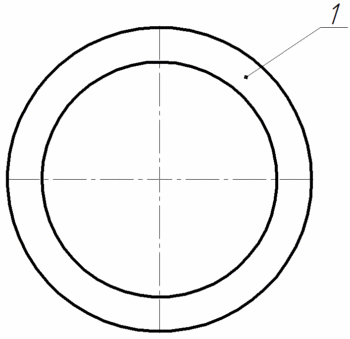
Рисунок 3.1 – Внутреннее шлифование по схеме с постоянным усилием поджима: 1 – заготовка, 2 – шлифовальный круг
Шлифование и заточка по схеме с постоянным усилием поджима позволяют наиболее полно проявить высокие режущие свойства алмазных кругов, так как глубина внедрения зерен в шлифуемое изделие определяется нормальной силой [8]. Постоянная нормальная сила прижима детали к кругу может быть реализована с помощью различных конструктивных решений, среди которых наиболее часто используются: создание постоянной силы с помощью пружины, с помощью рычажного механизма и путем применения гидравлического устройства [9].
3.2 Введение понятия "текущая лимитированная режущая способность круга"
Текущая лимитированная режущая способность алмазного круга – это объем обрабатываемого материала, удаляемый с заготовки рабочей поверхностью круга (РПК) за единицу времени при условии, что все требования, налагаемые на режим обработки техническими ограничениями, удовлетворены [5].
В качестве лимитирующего технического ограничения при обработке быстрорежущих сталей и твердых сплавов в основном выступают показатели качества обработанной поверхности или же показатели, характеризующие теплонапряженность процесса.
Текущая лимитированная режущая способность круга зависит от сочетания параметров РПК (зернистости, относительной концентрации алмазов, вида связки и ее механических характеристик, ориентации зерен и степени их выступания из связки, разновысотности зерен) и элементов режима резания. Вследствие непостоянства параметров РПК во время шлифования при любой схеме обработки текущая лимитированная режущая способность круга в процессе обработки постоянно изменяется.
Изменение текущей режущей способности круга явным образом проявляется при схеме обработки с постоянным усилием поджима в виде изменения в ходе процесса фактической глубины резания при условии постоянства остальных элементов режима.
3.3 Ограничения, налагаемые на режимы обработки при шлифовании по схеме с постоянным усилием поджима
Параметрами режима резания при внутреннем врезном шлифовании постоянным усилием поджима являются:
- Скорость шлифовального круга, Vк, м/с;
- Скорость детали, Vд, м/мин;
- Усилие поджима рабочей поверхности круга к заготовке, Рн, Н.
Скорость шлифовального круга Vк, назначают максимально возможной, исходя из условий обработки и технологических возможностей оборудования и инструмента, аналогично плоскому шлифованию.
Скорость детали Vд рассчитывают по заданному значению параметра шероховатости Ra шлифованной поверхности изделия, аналогично методике, применяемой при плоском шлифовании с учетом изменения длины дуги контакта изделия со шлифовальным кругом [13].
Усилие поджима Рп при шлифовании твердых сплавов алмазными кругами ограничено температурным порогом окисления алмазов. При внутреннем шлифовании – точностью обработки [14].
3.4 Методика определения усилия поджима по точности
Усилие поджима обрабатываемого образца из твердого сплава к рабочей поверхности алмазного круга при внутреннем врезном шлифовании имеет вид [13]:

где kш – коэффициент шлифования твердого сплава алмазным кругом;
Ток – температура окисления алмазного зерна, С;
l – длина дуги контакта зерна с обрабатываемой поверхностью, мм;
Vк – скорость круга, м/с;
b – ширина шлифуемой поверхности, мм;
d – диаметр основания цилиндрической модели зерна, мм;
λ1 – коэффициент теплопроводности алмаза, Вт/(м ⋅ C°);
ω1 – коэффициент температуропроводности алмаза, м2/с;
δ – коэффициент неравномерности нагрузки на зерно;
np – количество режущих зерен на одном квадратном метре поверхности круга.
Величина А∗определяется по формуле:

Здесь:
А1 – безразмерная функция учитывающая температуру рабочего торца зерна;
Аср – безразмерная функция, учитывающая среднюю температуру рабочего и не рабочего торца зерна;
F0 – безразмерное время контакта зерна с кругом, представленное с помощью критерия Фурье;
h – высота цилиндрической модели, мм;
λк – коэффициентом теплопроводности связки, Вт/м ⋅ C°.
Длина дуги контакта шлифовального круга с образцом равна:

где Rк – радиус шлифовального круга, мм;
RD – радиус шлифуемого отверстия, мм.
Установлено [14], что при внутреннем шлифования в качестве критерия, также лимитирующего усилие поджима РПК к заготовке, может быть использована точность обработки. В этом случае определяют упругое перемещение конца шпинделя (рис. 3.3).
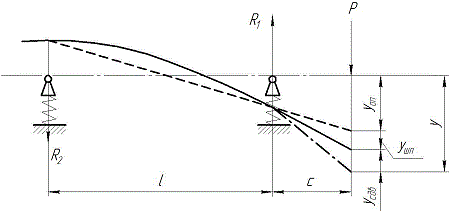
Рисунок 3.3 – Расчетная схема к определению упругого перемещения
Перемещение переднего конца шпинделя с учетом защемляющего момента в передней опоре:

где G – модуль сдвига материала шпинделя;
S1 и S2 – площади сечения переднего конца и межопорной части шпинделя;
δ1 – перемещение, вызванное изгибом тела шпинделя, мм;
δ2 – перемещение, вызванное жесткостью опор, мм;
δ3 – сдвиг, вызванный защемляющим моментом, мм;
l – расстояние между передней А и задней В опорами шпинделя, мм;
a – вылет переднего конца шпинделя, мм;
с – расстояние от приводного элемента до передней опоры, мм;
J1 – среднее значение осевого момента инерции сечения консоли, мм4;
J2 – среднее значение осевого момента инерции сечения шпинделя в пролете между опорами, мм4;
Е – модуль упругости материала, H/мм2;
jA и jB – радиальная жесткость передней и задней опор, H/мм;
ε – коэффициент защемления в передней опоре.
В итоге, допустимое усилие поджима будет представлять собой величину, которая вызывает деформацию рабочего конца шпинделя в пределах допустимой погрешности обработки.
3.5 Устройство для внутреннего шлифования с постоянным усилием поджима РПК к заготовке
Для осуществления внутреннего шлифования с постоянной силой поджима Рy было разработана специальная конструкция шлифовальной бабки внутришлифовального станка модели 3А227П.
Устройство для внутреннего шлифования с постоянным усилием поджима РПК к заготовке (рис. 3.4) [15] состоит из корпуса 1, который расположен на столе станка 2. Шлифовальная головка 3 со шлифовальным кругом 4 закреплена с двух сторон в обоймах 5, которые имеют сверху и снизу призматические пазы с установленными в них планками 6 с треугольными канавками, в которых расположены шарики 7. С шариками 6 находятся в контакте треугольные канавки регулируемых ответных планок 8, которые закреплены на торце стаканов 9, закрепленных в отверстии корпуса 1.
Канавки планок 6 и 8 образуют шариковые направляющие, которые в горизонтальном направлении дают возможность перемещения шлифовальной головки относительно стола, тем самым осуществляя поджим рабочей поверхности шлифовального круга 4 к обрабатываемой поверхности заготовки с постоянной силой, которую задают с помощью нагрузочного устройства (рис. 3.5) [16].
Конструкция устройства для внутреннего шлифования с постоянным усилием поджима РПК к заготовке обеспечивает возможность электроэрозионной правки шлифовального круга. Для изоляции шлифовального круга 4 шлифовальная головка 3 закреплена в обоймах 5 через диэлектрические кольца.
Токоподвод к шлифовальному кругу реализован через графитовую щетку 11, установленную в кронштейне 12 с торца шлифовальной головки. Кронштейн 12 закреплен на задней обойме 5 для постоянства контакта щетки с торцем шлифовальной головки в независимости от ее горизонтального перемещения. Надежность контакта щетки обеспечивается пружиной 13.
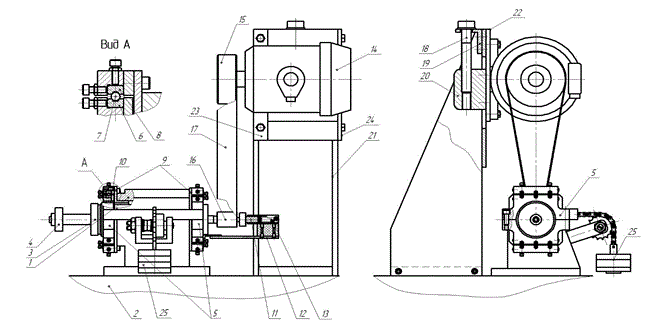
Рисунок 3.4 – Конструкция устройства для внутреннего шлифования с постоянной радиальной силой резания
Вращение шлифовальной головке передается от двигателя 14 через плоскоременную повышающую передачу. Ось вращения двигателя и шпинделя шлифовальной бабки расположены в вертикальной плоскости, что необходимо для обеспечения постоянства межосевого расстояния шкивов 15 и 16 при перемещении шлифовальной головки в горизонтальной плоскости. Регулировка усилия натяжения ремня 17 осуществляется винтовым механизмом, образованным винтом 18, упором 19 и гайкой 20.
Винт с упором установлен на неподвижной стойке 21. Гайка 20 закреплена на основании 22 двигателя и перемещается вместе с ним при вращении винта 18. Основание 22 заключено между двумя планками 23 и 24, служащими плоскими направляющими при его перемещении.
Нагрузочное устройство (рис. 3.5), состоит из пластинчатой цепи 1, расположенной на звездочке 2, которая закреплена на оси 3 на шариковых подшипниках 4 с возможностью вращения вокруг нее.
Один конец пластинчатой цепи закреплен на подвижной части 6 устройства для шлифования шлифовании с постоянной радиальной силой резания, а на другом конце цепи закреплен груз 7.
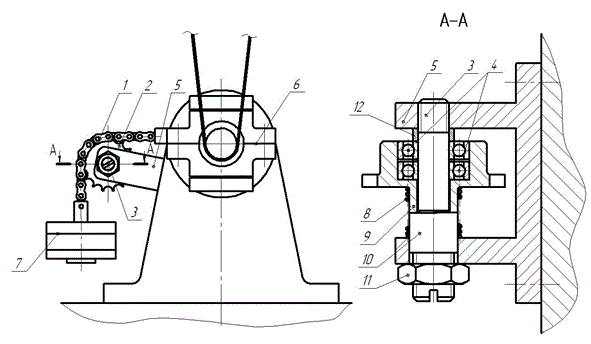
Рисунок 3.5 – Конструкция нагрузочного устройства шлифовальной бабки для внутреннего шлифования с постоянным усилием поджима РПК к заготовке.
На оси 3 расположена винтовая пружина 8, одна часть внутренней поверхности контактирует с внешней цилиндрической поверхностью ступицы 9 на звездочке 2, а другая часть внутренней поверхности винтовой пружины – с цилиндрической поверхностью 10 оси 3, при этом направление винта витка пружины является противоположным направлению вращения звездочки 2, обусловленной действием груза 7. Гайка 11 служит для закрепления оси 3 в проушине неподвижно, а втулка 12 – для регулирования положения звездочки 2 по отношению к пластинчатой цепи 1.
После включения вращения заготовки шлифовальный круг 10 подводится к обрабатываемой поверхности и подвижная часть шлифовальной бабки начинает перемещаться под действием груза 7. При этом направление вращения звездочки 2, является противоположным направлению винта витка винтовой пружины 8. В этом случае силы трения на внутренней поверхности винтовой пружины 8 с наружной цилиндрической поверхностью ступицы 9 на звездочке 2 с направлением винта витка пружины различны и разворачивают винтовую пружину 8, вследствие чего ее диаметр увеличивается, что обеспечивает свободное перемещение подвижной части шлифовальной бабки в направлении РПК. При обратном движении подвижной части шлифовальной бабки, вследствие радиального биения РПК, звездочка 2 будет пытаться вращаться в направлении, которое совпадает с направлением витка винтовой пружины 8. При этом силы трения на внутренний поверхности винтовой пружины 8 с наружной цилиндрической поверхностью ступицы 9 на звездочке 2 закручивают винтовую пружину и ее диаметр уменьшается, силы трения на внутренней поверхности винтовой пружины 12 и цилиндрической поверхности 10 оси 3 растут, что делает невозможным вращения звездочки 2, а следовательно и перемещения подвижной части 8 шлифовальной бабки в направлении от обрабатываемой поверхности образца. Таким образом, сила поджима РПК к образцу и сила, которая препятствует перемещению РПК от обрабатываемой поверхности, будут приложены в одном и том же месте, а именно, на звездочке. В связи с этим, сила поджима РПК к образцу будет обусловлена величиной груза 7, и не будет зависеть от возможных перекосов в направляющих подвижной части устройства для шлифования шлифовании с постоянной радиальной силой резания и обеспечивает отсутствие радиальных колебаний подвижной части устройства.
Такой способ реализации подачи шлифовального круга в соответствии с его режущей способностью имеет ряд существенных недостатков – необходимостью изменения конструкции шлифовальной бабки станка и компоновки ее привода; а также ограниченностью применения шлифовальной бабки врезным шлифованием, так как при шлифовании с подачей груз будет осуществлять колебательное движение.
Поэтому для осуществления подачи, изменяющуюся в соответствии с законом изменения ТЛРСК станок предлагается оснастить дополнительным устройством.
4. Разработка устройства автоматической подачи на глубину бабки изделия внутришлифовального станка модели 3А227П в соответствии с законом изменения режущей способности круга
4.1 Кинематическая схема устройства перемещения бабки изделия
Для осуществления подачи, изменяющейся в соответствии с законом изменения ТЛРСК во времени станок предлагается оснастить дополнительным устройством, кинематическая схема которого представлена на рис. 4.1. Задающим устройством привода перемещения бабки изделия в соответствии с законом изменения ТЛРСК, является вычислительный блок 1, который преобразует закон изменения текущей лимитированной режущей способности круга во времени в определенное количество импульсов в единицу времени, управляющих шаговым двигателем 2. От вала шагового двигателя 2 вращение передается через безлюфтовую упругую муфту 3 на вал 4, от вала 4 на вал 6 через беззазорную червячную передачу 5. От вала 6 вращение передается через беззазорную цилиндрическую зубчатую передачу 7 на вал ходового винта 8.
Беззазорные передачи практически исключают зазор в зубчатом зацеплении, тем самым увеличивают точность перемещения бабки изделия. От ходового винта 8 перемещение передается на гайку 9. Гайка 9 с регулируемым зазором в винтовой паре, жестко закреплена на корпусе бабке изделия 10. Перемещение бабки изделия 10 осуществляется по роликовым направляющим 11.

Рисунок 4.1 – Кинематическая схема устройства перемещения бабки изделия в соответствии с законом изменения ТЛРСК
4.2 Кинематическая схема устройства перемещения бабки изделия
Автоматическая система управления (рис. 4.2) перемещением бабки изделия осуществляется в соответствии с найденным законом изменения текущей лимитированной режущей способности круга во времени.
Задающее устройство 1 генерирует управляющие шаговым двигателем импульсы, в соответствии с заданным законом. Также устройство 1 задает начальное положение бабки изделия в зависимости от диаметра шлифуемого отверстия.
Управляющие импульсы, преобразованные в электрический сигнал, передаются в сравнивающее устройство 2, в котором происходит сопоставление сигнала текущего положения бабки изделия с заданным и, в случае необходимости, вырабатывается корректирующий сигнал. Фиксирование текущего положения бабки изделия происходит по цепи обратной связи, образованной датчиком 3, фиксирующим фактическое положение бабки изделия и усилителем сигнала 4. Полученный суммарный управляющий сигнал усиливается устройством 6 и подается на вход шагового двигателя 7, вращение от которого через беззазорный механизм 8, чей принцип работы описан выше, передается бабке изделия 9.
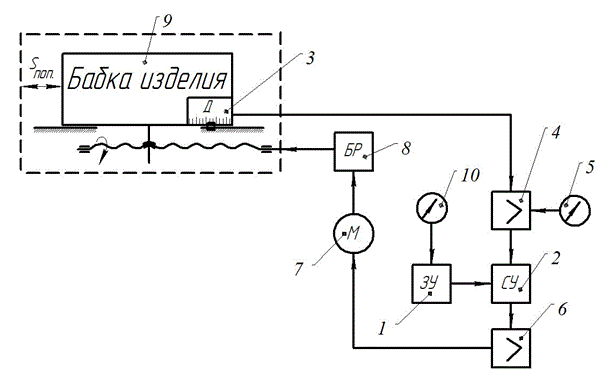
Рисунок 4.2 – Схема автоматической системы управления механизмом перемещением бабки изделия
Индикаторы 5 и 10 визуально фиксируют координаты текущего и заданного положения бабки изделия.
4.3 Определение закона изменения текущей лимитированной режущей способности для программирования автоматической системы управления
С целью программирования автоматической системы управления бабкой изделия, необходимо знать закон изменения ТЛРСК во времени для конкретных условий обработки, которую определяют экспериментально.
Текущую лимитированную режущую способность шлифовального круга 1А1 40×16×10×5 АС6 100/80-4-М2-01 определяли при шлифовании твердого сплава ВК15 с постоянной силой поджима на станке модели 3А227П, модернизированном для электроэрозионной правки [17].
Перед проведением экспериментов круг правили электроэрозионным способом по схеме внутреннего многопроходного шлифования до полного обновления рабочей поверхности круга. В качестве источника технологического тока использовали блок питания ИТТ-35. Правку РПК осуществляли шлифованием чугунного электрода на режимах: механических – Vк =26 м/с, Vэ =24 м/мин, глубина шлифования t =0,005 мм; электрических – средняя сила тока электроэрозионных воздействий Iср=10А, напряжение холостого хода Uxx=60 В.
Внутреннее врезное шлифование с постоянным усилием поджима образца из твердого сплава марки ВК15 в виде кольца, с диаметром отверстия Dо=40 мм и высотой В=10 мм, выполняли на режимах: Vк = 25,8 м/с, Vэ=24 м/мин (при заданном параметре шероховатости Ra=1,25 мкм). Усилие поджима образца к РПК составляло Pп= 20 Н, найденное исходя из точности обработки, которая является лимитированным техническим ограничением. Поджим образца к РПК осуществляли при помощи специального нагрузочного устройства, обеспечивающего стабильное усилие поджима в процессе обработки. Охлаждение при правке и шлифовании осуществляли 0,3%-ным водным раствором кальцинированной соды. Внутренний диаметр кольца измеряли в трех сечениях с помощью микрометром с ценою деления 10 мкм. Режущую способность оценивали объемом сошлифованного материала, удаленного за одну минуту. Измерение диаметра отверстия, а также шлифовального круга выполняли после 0,25; 0,5; 1; 2; 5; 10; 15; 30; 45 минут обработки.
Величину подачи Sп(τ), изменяющуюся в соответствии с законом изменения ТЛРСК Q(τ), определим используя ее значения в разные периоды шлифования по следующей формуле:

где Q(τ) – значения ТЛРСК в определенные периоды шлифования, мм3/мин;
Vд – скорость детали, м/мин;
τдис – время дискретизации процесса шлифования, мин;
Вд – высота обрабатываемой цилиндрической поверхности образца, мм.
Используя данные экспериментов, были построены график зависимости текущей лимитированной режущей способности круга от времени шлифования Q(τ) (рис. 4.3), а также найдены уравнения регрессии в виде:

где Q, Qисх, Qуст – соответственно текущая, исходная, установившаяся режущая способность круга, мм3/мин; ΔQ = Qисх − Qуст – амплитуда изменения режущей способности круга, мм3/мин; βQ – эмпирический коэффициент, 1/мин; τ – продолжительность шлифования, мин.
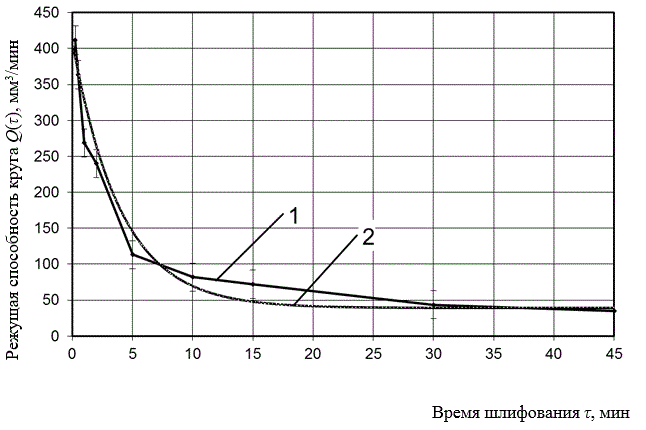
Рисунок 4.3 – Изменение текущей лимитированной режущей способности круга 1А1 40×16×10×5 АС6 100/80-4-М2-01 при шлифовании твердого сплава ВК15:1 – экспериментальная кривая; 2 – регрессионная кривая
За исходную режущую способность Qисх принимали режущую способность на первой минуте шлифования. За установившуюся принимали режущую способность круга после 15 минут обработки. Уравнение Q = ƒ(t), полученное методом наименьших квадратов, имеет вид:

Полученный закон изменения ТЛРСК во времени будет использован при программировании предложенной автоматической системы управления поперечной подачей бабки изделия внутришлифовального станка модели 3А227П в соответствии с найденным законом.
4.4 Описание конструкции модернизированного привода подачи на глубину бабки изделия
Конструкция привода для обеспечения автоматической поперечной подачи бабки изделия внутришлифовального станка модели 3А227П в соответствии с законом изменения режущей способности круга представлен на рис. 4.4.
Обеспечение заданной текущей глубины резания в модернизированном приводе осуществляется благодаря шаговому двигателю 1. От вала шагового двигателя вращение передается через муфту 3, соединяющая вал шагового двигателя 1 и вал 3. Через беззазорную передачу 4 вращение передается вал 5. На валу 5 закреплена электромагнитная муфта 6. Если муфта включена, то крутящий момент передается через беззазорную цилиндрическую передачу 7 на ходовой вал 8. Если муфта не включена, то перемещение бабки изделия в поперечном направлении осуществляется вручную.
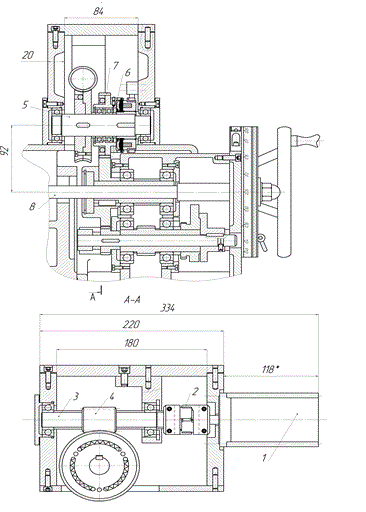
Рисунок 4.4 – Конструкция привода для обеспечения автоматической поперечной подачи бабки изделия внутришлифовального станка модели 3А227П в соответствии с ТЛРСК во времени
Конструктивная реализация беззазорных зубчатых передач заключается в следующем. В зубчатой или червячной передаче одно зубчатое (червячное) колесо делают разрезным. Зазор устраняется взаимным разворотом половинок, пружинами или последующим жестким закреплением половинок болтами. Устранение зазоров и создание предварительного натяга в передаче достигается взаимным разворотом его кинематических цепей специальным нагружающим устройством. В результате в каждой кинематической цепи получается однопрофильное зацепление, которое не нарушается и при реверсе движения.
При включении шагового электродвигателя, 0,06 мм, бабка перемещается автоматически по заданному закону с точностью 0,5 мкм.
Если электромагнитная управляемая муфта не включена, то движение осуществляется вручную с помощью рукоятки.
После этого, на станок устанавливается заготовка и начинается обработка. Движение поперечной подачи позволяет бабке с изделием перемещаться в широком диапазоне, достаточном для полной обработки детали на размер.
Выводы
В данной работе проведен анализ существующих методов оптимизации режимов шлифования и установлено, что использование обобщающих показателей режимов шлифования, обеспечивающих стабильные показатели качества, позволяют уменьшить трудоемкость поиска оптимальных режимов.
На основе анализа существующих конструкций устройств для шлифования по схеме с постоянным усилием поджима РПК к заготовке предложена конструкция бабки изделия внутришлифовального станка, которая может быть применена при внутреннем шлифовании по схеме с постоянным усилием поджима РПК к заготовке, которая обеспечит максимальное использование режущих свойств круга.
При написании данного реферата магистерская работа еще не завершена. Окончательное завершение: декабрь 2014 года. Полный текст работы и материалы по теме могут быть получены у автора или его руководителя после указанной даты.
Список источников
- Абразивная и алмазная обработка материалов. Справочник. Под ред. д-ра техн. наук проф. А. Н. Резникова. М.: Машиностроение, 1977. – 391 с.
- Матюха П.Г., Полтавець В. В. Алмазне шліфування з електроерозійними керуючими діями на робочу поверхню круга / Матюха П.Г. , Полтавець В. В.–Донецьк: ДонНТУ, 2006.–164с.
- Глейзер Л.А. О сущности процесса круглого шлифования// Вопросы точности в технологии машиностроения. – М.: Машгиз, 1959.– с.5-24.
- Матюха П.Г. Високопродуктивне шліфування ванадієвих штампових та інструментальних сталей / П.Г. Матюха. Донецьк: ДВНЗ «ДонНТУ», 2008. – 222 с.
- Жулин И.С., Полтавець В.В. Описание процесса алмазного шлифования по упругой схеме с использованием понятия текущей лимитированной режущей способности круга/ Прогрессивные направления развития машино-приборостроительных отраслей и транспорта. Материалы международной научно-технической конференции студентов, аспирантов и молодых ученых 14-17 мая 2007 г. в г. Севастополе. – Севастополь: Изд-во СевНТУ, 2007. – С. 97-98.
- Технология машиностроения. В 2 кн. Кн. 1. Основы технологии машиностроения. Кн. 2. Производство деталей машин: учебное пособие для вузов / Э. Л. Жуков, И. И. Козарь, С. Л. Мурашкин и др.; под ред. С. Л. Мурашкина. – М.: Высшая школа, 2003.
- Палей М.М. и др. Технология шлифования и заточки режущего инструмента. – М.: Машиностроение, 1988.– 288 с.
- Теория инженерного эксперимента: Учеб. Пособие / Г.М. Тимошенко, П.Ф. Зима. – К.:УМК ВО, 1991. – 124с.
- Математический анализ точности механической обработки деталей. Колкер Я.Д. “Техника”, 1976.– 200с.
- Попов С.А., Малевский Н.В., Терещенко Л.М. Алмазно-абразивная обработка металлов и твёрдых сплавов. – М.: Машиностроение, 1977. – 263 с.
- Основы алмазного шлифования/ Семко М.Ф., Грабченко А.И. Раб А.Ф. и др. – Киев: Техніка, 1978. –192 с.
- Матюха П.Г., Стрелков В.Б., Полтавец В.В. Определение режимов плоского шлифования твердых сплавов с использованием нового критерия о текущей лимитированной режущей способности круга/ Сверхтвердые материалы. Научно-теоретич. журнал. – Киев: 2004. – № 3. – С. 67-73.
- Матюха П.Г., Полтавец В.В. Режущая способность рабочей поверхности круга как ограничивающий параметр производительности шлифования. Надежность инструмента и оптимизация технологических систем. Сб. научных трудов. – Краматорск: ДГМА, вып. № 13, 2003. – С. 159-164.
- Габитов В.В. Определение оптимальных режимов внутреннего шлифования твёрдого сплава ВК15 по упругой схеме с периодическими электроэрозионными воздействиями / В.В. Габитов // Надежность инструмента и оптимизация технологических систем. Сборник научных трудов. – Краматорск, вып. №29, 2011. – С. 232-241.
- Шліфувальна бабка Патент України №94813 С2 МПК В24В41/00 Автори: Матюха П.Г., Габітов В.В., Войтов М.С., Благодарний А.О. Заявка а200911849 от 19.11.2009. Опубл 10.06.2011 бюл №11, 2011.
- Навантажувальний пристрій для шліфування ПАТЕНТ УКРАЇНИ №98857 С2 МПК В24В 41/00 Автори: Матюха П.Г., Габітов В.В., Благодарний А.О. Заявка а201012927 от 01.11.2010. Опубл 25.06.2012 бюл №12, 2011.
- Габитов В.В. Определение текущей лимитированой режущей способности алмазного шлифовального круга при шлифовании комбинированного образца «Сталь 45 – твердый сплав ВК8» / В.В. Габитов // Наукові праці Донецького національного технічного університету. Серія: Машинобудування і машинознавство. Випуск 6 (154). – Донецьк: ДонНТУ, 2009. С 35 – 40 с.