Реферат за темою випускної роботи
Зміст
- Вступ
- 1. Актуальність теми
- 2. Огляд існуючих методів визначення оптимальних режимів різання при шліфуванні
- 3. Оптимізація режимів шліфування з використанням поняття "поточна лімітована різальна здатність круга"
- 3.1 Схеми обробки при внутрішньому шліфуванні
- 3.2 Введення поняття "поточна лімітована різальна здатність круга"
- 3.3 Обмеження, що накладаються на режими обробки при шліфуванні за схемою з постійним зусиллям підтиску
- 3.4 Методика визначення зусилля підтиску
- 3.5 Пристрій для внутрішнього шліфування з постійним зусиллям підтиску РПК до заготовки
- 4. Розробка пристрою автоматичної подачі на глибину бабки виробу внутрішньошліфувального верстата моделі 3А227П відповідно до закону зміни різальної здатності круга
- 4.1 Кінематична схема пристрою переміщення бабки виробу
- 4.2 Автоматична система управління переміщенням бабки виробу
- 4.3 Визначення закону зміни поточної лімітованої різальної здатності для програмування автоматичної системи управління
- 4.4 Опис конструкції модернізованого приводу подачі на глибину бабки виробу
- Висновки
- Перелік посилань
Вступ
1. Актуальність теми
В даний час, підвищення продуктивності обробки при мінімальних витратах на виробництво, із забезпеченням необхідних показників якості є необхідними умовами випуску конкурентоспроможної продукції. Вирішення цих завдань можливе за рахунок оптимізації параметрів режиму обробки: швидкості круга, швидкості деталі і глибини різання [1]. Швидкість круга прийнято призначати максимальної виходячи і технічних можливостей верстата з метою забезпечення максимальної продуктивності, швидкість деталі найбільшою мірою визначає шорсткість шліфованої поверхні, а глибина різання істотно впливає на продуктивність обробки і якість шліфованої поверхні [2].
В існуючих дослідженнях [1, 3], задача оптимізації глибини шліфування важкооброблюваних матеріалів вирішується шляхом експериментального її визначення з використанням багатофакторних експериментів. Цьому способу вирішення характерна висока трудомісткість досліджень і великі часові витрати. У ряді робіт [4, 5]. Дане завдання вирішується з використанням схеми шліфування з постійним зусиллям підтиску робочої поверхні круга (РПК) до заготовки. Дана схема дозволяє досліджувати процес шліфування незалежно від поточного стану РПК, теплових і динамічних процесів, що супроводжують різання. Схема шліфування з постійним зусиллям підтиску дозволяє визначити закон зміни різальної здатності круга в часі, який дає можливість оптимізувати глибину шліфування при обробці за схемою з постійною глибиною різання.
Оскільки в існуючих дослідженнях відсутні відомості з дослідження ріжучої здатності алмазних шліфувальних кругів при внутрішньому шліфуванні зразків із твердого сплаву за схемою з постійним зусиллям підтиску, а також відомості про визначення раціональних режимів обробки, то метою роботи є обгрунтування оптимальних режимів різання виробів з твердих сплавів при внутрішньому шліфуванні кругами із синтетичних алмазів.
Об'єкт дослідження: зміна ріжучої здатності робочої поверхні алмазного круга, заправленого електроерозійним способом, при внутрішньому шліфуванні твердого сплаву.
Практична цінність результатів роботи.
- Розробка нового пристрою, для забезпечення автоматичної подачі бабки вироби внутрішньошліфувального верстата моделі 3А227П відповідно до закону зміни поточної лімітованої різальної здатності круга, в якому за рахунок нових конструктивних елементів і системи управління забезпечується можливість внутрішнього шліфування отворів з використанням повною мірою різальних властивостей шліфувального круга.
- Визначено закон зміни поточної лімітованої різальної здатності круга для конкретних умов обробки, необхідний для програмування автоматичної системи управління розробленого пристрою.
- Отриманий закон може бути використаний для оптимізації процесу шліфування.
2. Огляд існуючих методів визначення оптимальних режимів різання при шліфуванні
Вхідними даними для визначення режимів різання при шліфуванні є:
- Інформація про оброблюваний матеріал і розміри поверхні, що шліфуються;
- Припуск на обробку;
- Вимоги до точності, шорсткості оброблюваних поверхонь та іншим показникам якості;
- Інформація про верстат;
- Жорсткість системи верстат – деталь – пристрій – круг;
- Характеристика круга, яким проводять обробку на даній операції.
Режими різання при шліфуванні можуть бути визначенні розрахунковим шляхом або призначені на основі практичних рекомендацій. Розрахунок режимів шліфування доцільно проводити для умов масового виробництва, коли незначні відхилення від оптимальних вимог обробки можуть привести до істотних втрат. Розрахунок режимів доцільно також проводити при розробці різних нормативів і рекомендацій, що відносяться до виготовлення шліфувальних кругів.
Завдання визначення оптимального режиму шліфування виконується в три етапи:
- Складання системи рівнянь, що описують технічні обмеження, що накладаються на режим різання вимогами до деталі, верстата, інструменту та вимогами виробництва.
- Математичний опис цільової функції, тобто функції, що виражає мету оптимізації.
- Спільне розгляд технічних вимог і цільової функції, і визначення на цій основі оптимальних режимів шліфування [[1].
Математичний вираз, що описує технічні обмеження, однотипні і можуть бути представлені у вигляді нерівностей, в лівій частині яких наведено задане (граничне) значення будь-якої величини, що обмежує, або параметра, а в правій – фактичне значення цієї величини або параметра при той чи іншій комбінації елементів режиму різання та інших заданих вимог обробки.
Технічні обмеження, що накладаються на режим різання вимогами до виробу, наступні:
- Гранично допустима висота шорсткості Ra на обробленій поверхні;
- Необхідна точність деталі після шліфування;
- Температура поверхні, що шліфується, гранично допустима з точки зору прижогів, залишкових напружень або інших показників якості поверхневого шару деталі.
Технічні обмеження, що накладаються на режими різання верстатом, наступні:
- Потужність приводу шліфувального круга;
- Найбільші і найменші частоти обертання шпинделя і значення подач, які передбачені кінематикою і конструкцією відповідних механізмів верстата (nmax, nmin, vmax и vmin та т.п.).
У зв'язку з малими значеннями сил, що виникають при шліфуванні, міцність механізму верстата, як правило, не обмежує режими різання. Винятками можуть бути випадки чорнового шліфування та обробки деталей на верстатах з одночасним шліфуванням декількома кругами.
Технічні обмеження, що накладаються на режим різання шліфувальним кругом, наступні:
- Необхідна стійкість інструменту;
- Гранична температура на ріжучих зернах;
- Міцність круга.
Комплекс технічних обмежень описує зона можливих режимів шліфування. Якщо оптимізації піддається комплекс з двох елементів режиму різання, а інші елементи режиму задані, то згадана зона зображує собою плоску фігуру, яка окреслена відповідними лініями. На рис. 2.1 у загальному вигляді зображена схема побудови зони можливих режимів різання у випадку, коли знаходиться оптимальне поєднання швидкості деталі і глибини різання (поперечна подача). Лінії, які зображені на малюнку, присвоєні найменування обмежень ТО1 – ТК3, що згадувалися вище. Якщо оптимізується комплекс з трьох елементів режиму роботи, то кожне обмеження описується не лінією, а поверхнею того чи іншого виду, а зона можливих режимів шліфування перетворюється в тривимірний простір. При великій кількості елементів, що характеризують режим різання, зона можливих режимів обертається у чотирьох або більш мірний простір.
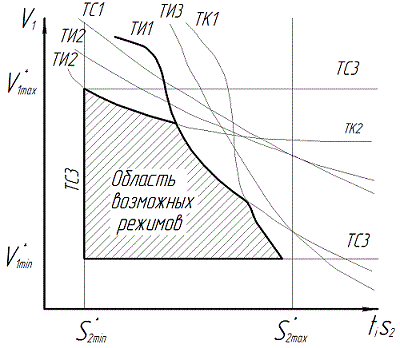
Рисунок 2.1 – Схема зони можливих режимів
Цільові функції являють собою математичний опис мети, з якої виробляють оптимізацію режиму шліфування. Залежно від конкретних умов виробництва при оптимізації можна забезпечити найменшу собівартість обробки на даній операції, досягнення на даній операції найбільшої продуктивності, мінімальні витрати на інструмент. Можуть бути й інші конкретні цілі оптимізації.
Таким чином, у зоні можливих режимів, які описані технічними обмеженнями і графічно зображені на рис. 1.1, необхідно відшукати точку, для якої всі обмеження будуть задоволені при максимальних значеннях режимів, що відповідають найбільшої продуктивності, вона і буде відповідати оптимальному режиму шліфування.
Недоліком розглянутого методу знаходження оптимальних режимів при шліфуванні нових матеріалів або кругами з новими характеристиками полягає в тому, що він вимагає значних витрат часу для знаходження залежностей, що описують технічні обмеження. Крім того, він дає результати, які неможливо використовувати у випадку, коли режими при обробці виходять за межі, в яких були знайдені рівняння технічних обмежень, а також не враховує зміну ріжучої здатності РПК при роботі.
3. Оптимізація режимів шліфування з використанням поняття "поточна лімітована різальна здатність круга"
3.1 Схеми обробки при внутрішньому шліфуванні
Внутрішнє шліфування застосовується для обробки поверхонь циліндричних, конічних і фасонних отворів на універсальних і спеціальних верстатах. Оброблення металевих і неметалевих матеріалів при внутрішньому шліфуванні може виконуватися за двома схемами: з постійним зусиллям підтиску і постійною глибиною шліфування (рис. 3.1, 3.2).
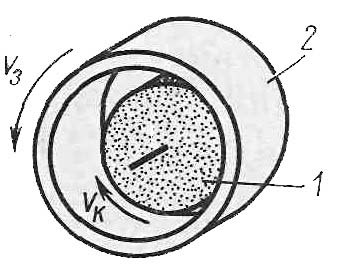
Рисунок 3.1 – Схема внутрішнього врізного шліфування з постійною глибиною різання: 1 – заготовка, 2 – шліфувальный круг
При шліфуванні отворів (рис 3.1) подача здійснюється тільки перпендикулярно осі отвору, через що форма робочої поверхні круга переноситься на оброблювану поверхню [6].
Врізне шліфування застосовують для обробки поверхонь, довжина яких не перевищує ширину шліфувального круга. Його перевага – велика продуктивність і простота наладки. Врізне шліфування широко застосовують у масовому і великосерійному виробництві.
У порівнянні з звичайним шліфуванням за схемою з постійною глибиною різання, шліфування з певним радіальним тиском (рис. 3.2 ), на думку Л. А. Глейзера, являє собою досить стійкий процес, що володіє більшим ступенем детермінованості [3]. Шліфування за схемою з постійним зусиллям підтиску Py шліфувального круга до заготовки дозволяє виключити вплив на температуру шліфування, непостійності припуску, нестабільності фізико-механічних властивостей матеріалу виробу та зміни ріжучої здатності шліфувального круга за період його стійкості, що знижує небезпеку появи дефектів на шліфованої поверхні [7].
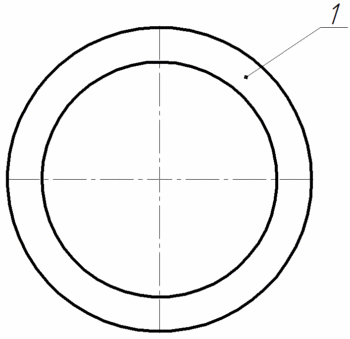
Рисунок 3.2 – Внутрішнє шліфування за схемою з постійним зусиллям підтиску : 1 – заготовка, 2 – шліфувальный круг
Шліфування та заточування за схемою з постійним зусиллям підтиску дозволяють найбільш повно проявити високі ріжучі властивості алмазних кругів так, як глибина впровадження зерен у шліфоване виріб визначається нормальною силою [8]. Постійна нормальна сила притиску деталі до круга може бути реалізована за допомогою різних конструктивних рішень, серед яких найбільш часто використовуються: створення постійної сили за допомогою пружини, за допомогою важільного механізму та шляхом застосування гідравлічного пристрою [9].
3.2 Введение понятия "текущая лимитированная режущая способность круга"
Поточна лімітована різальна здатність алмазного круга – це обсяг оброблюваного матеріалу, що видаляється з заготовки робочою поверхнею круга (РПК) за одиницю часу за умови, що всі вимоги, які накладаються на режим обробки технічними обмеженнями, задоволені [5].
В якості лімітованого технічного обмеження при обробці швидкорізальних сталей і твердих сплавів в основному виступають показники якості обробленої поверхні або ж показники, що характеризують теплонапруженість процесу.
Поточна лімітована різальна здатність круга залежить від поєднання параметрів РПК (зернистості, відносної концентрації алмазів, виду зв'язки і її механічних характеристик, орієнтації зерен і ступеня їх виступання з зв'язки, різновисотних зерен) та елементів режиму різання. Внаслідок непостійності параметрів РПК під час шліфування при будь-якій схемі обробки поточна лімітована різальна здатність круга в процесі обробки постійно змінюється.
Зміна поточної ріжучої здатності круга явним чином проявляється при схемі обробки з постійним зусиллям підтиску у вигляді зміни в ході процесу фактичної глибини різання за умови сталості інших елементів режиму.
3.3 Обмеження, що накладаються на режими обробки при шліфуванні за схемою з постійним зусиллям підтиску
Параметрами режиму різання при внутрішньому врізному шліфуванні з постійним зусиллям підтиску є:
- Швидкість шліфувального круга, Vк, м/с;
- Швидкість деталі, Vд, м/хв.;
- Зусилля підтиску робочої поверхні круга до заготовки, Рн, Н.
Швидкість шліфувального круга Vк, призначають максимально можливою, виходячи з умов обробки та технологічних можливостей обладнання та інструменту, аналогічно плоскому шліфуванню.
Швидкість деталі Vд розраховують за заданим значенням параметра шорсткості Ra шліфованої поверхні виробу, аналогічно методиці, застосовуваної при плоскому шліфуванні з урахуванням зміни довжини дуги контакту виробу зі шліфувальним кругом [13].
Зусилля підтиску Рп при шліфуванні твердих сплавів алмазними кругами обмежено температурним порогом окислення алмазів. При внутрішньому шліфуванні – точністю обробки [14].
3.4 Методика визначення зусилля підтиску
Зусилля підтиску оброблюваного зразка з твердого сплаву до робочої поверхні алмазного круга при внутрішньому врізному шліфуванні має вигляд [13]:

де kш – коефіцієнт шліфування твердого сплаву алмазним кругом;
Ток – температура окислення алмазного зерна, С;
l – довжина дуги контакту зерна з оброблюваної поверхні, мм;
Vк –швидкість круга, м/с;
b – ширина шліфованої поверхні, мм;
d – діаметр основи циліндричної моделі зерна, мм;
λ1 – коефіцієнт теплопровідності алмазу, Вт/(м⋅С°);
ω1 – коефіцієнт температуропровідності алмазу, м2/с;
δ – коефіцієнт нерівномірності навантаження на зерно;
np – кількість ріжучих зерен на одному квадратному метрі поверхні круга.
Величина А∗визначається за формулою:

Тут:
А1 – безрозмірна функція, що враховує температуру робочого торця зерна;
Аср – безрозмірна функція, що враховує середню температуру робочого і не робочого торця зерна;
F0 – безрозмірний час контакту зерна з кругом, представлене за допомогою критерію Фур'є;
h – висота циліндричної моделі, мм;
λк – коефіцієнтом теплопровідності зв'язки, Вт/м⋅С°.
Довжина дуги контакту шліфувального круга із зразком дорівнює:

де Rк – радіус шліфувального круга, мм;
RD – радіус отвору, що шліфується, мм.
Встановлено [14], що при внутрішньому шліфуванні у якості критерія, також лімітованого зусилля підтиску РПК до заготовки, може бути використана точність обробки. У цьому випадку визначають пружне переміщення кінця шпинделя (рис.3.3).
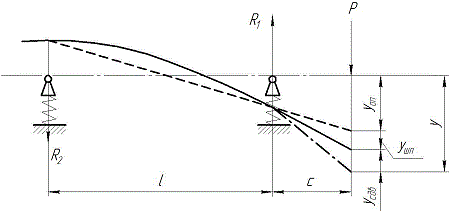
Рисунок 3.3 – Розрахункова схема до визначення пружного переміщення
Переміщення переднього кінця шпинделя з урахуванням затискного моменту у передній опорі:

де G– модуль зсуву матеріалу шпинделя;
S1 и S2 – площі перетину переднього кінця і межопорної частини шпинделя;
δ1 – переміщення, викликане згинанням тіла шпинделя, мм;
δ2 – переміщення, викликане жорсткістю опор, мм;
δ3 – зсув, викликаний затискним моментом, мм;
l – відстань між передньою А і задньою В опорами шпинделя, мм;
a – виліт переднього кінця шпинделя, мм;
с – відстань від приводного елемента до передньої опори, мм;
J1 – середнє значення осьового моменту інерції перерізу консолі, мм4;
J2 – середнє значення осьового моменту інерції перерізу шпинделя в прольоті між опорами, мм4;
Е – модуль пружності матеріалу, H/мм2;
jA та jB – радіальна жорсткість передньої і задньої опор, H/мм;
ε – коефіцієнт затиску у передній опорі.
У підсумку, допустиме зусилля підтиску представлятиме собою величину, яка викликає деформацію робочого кінця шпинделя в межах допустимої похибки обробки.
3.5 Пристрій для внутрішнього шліфування з постійним зусиллям підтиску РПК до заготовки
Для здійснення внутрішнього шліфування з постійною силою підтиску Рy була розроблена спеціальна конструкція шліфувальної бабки внутрішньо-шліфувального верстата моделі 3А227П.
Пристрій для внутрішнього шліфування з постійним зусиллям підтиску РПК до заготовки (рис. 3.4) [15] складається з корпусу 1, який розташований на столі верстата 2. Шліфувальна головка 3 з шліфувальним кругом 4 закріплена з двох сторін в обоймах 5, які мають зверху і знизу призматичні пази з встановленими в них планками 6 з трикутними канавками, в яких розташовані кульки 7. З кульками 6 знаходяться в контакті трикутні канавки регульованих відповідних планок 8, які закріплені на торці стаканів 9, закріплених в отворі корпусу 1.
Канавки планок 6 і 8 утворюють кулькові напрямні, які в горизонтальному напрямку дають можливість переміщення шліфувальної головки щодо столу, тим самим здійснюючи підтиск робочої поверхні шліфувального круга 4 до оброблюваної поверхні заготовки з постійною силою, яку задають за допомогою навантажувального пристрою (рис. 3.5) [16].
Конструкція пристрою для внутрішнього шліфування з постійним зусиллям підтиску РПК до заготовки забезпечує можливість електроерозійної правки шліфувального круга. Для ізоляції шліфувального круга 4 шліфувальна головка 3 закріплена в обоймах 5 через діелектричні кільця.
Струмопідвід до шліфувального круга реалізований через графітову щітку 11, встановлену в кронштейні 12 з торця шліфувальної головки. Кронштейн 12 закріплений на задній обоймі 5 для сталості контакту щітки з торцем шліфувальної головки в незалежності від її горизонтального переміщення. Надійність контакту щітки забезпечується пружиною 13.
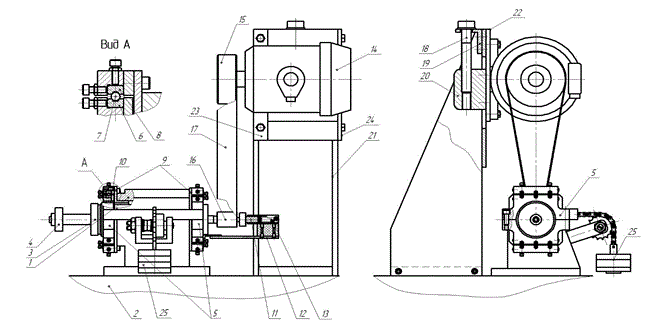
Рисунок 3.4 – Конструкція пристрою для внутрішнього шліфування з постійною радіальної силою різання
Обертання шліфувальної голівці передається від двигуна 14 через плоскопасову підвищувальну передачу. Вісь обертання двигуна і шпинделя шліфувальної бабки розташовані у вертикальній площині, що необхідно для забезпечення сталості міжосьової відстані шківів 15 і 16 при переміщенні шліфувальної головки у горизонтальній площині. Регулювання зусилля натягу ременя 17 здійснюється гвинтовим механізмом, утвореним гвинтом 18, упором 19 і гайкою 20.
Гвинт з упором встановлений на нерухомій стійці 21. Гайка 20 закріплена на підставі 22 двигуна і переміщується разом з ним при обертанні гвинта 18. Підстава 22 укладено між двома планками 23 і 24, службовцями плоскими направляючими при його переміщенні.
Навантажувальний пристрій (рис. 3.5), складається з пластинчастого ланцюга 1, розташованого на зірочці 2, яка закріплена на осі 3 на кулькових підшипниках 4 з можливістю обертання навколо неї.
Один кінець пластинчастого ланцюга закріплений на рухомій частині 6 пристрою для шліфування шліфуванні з постійною радіальної силою різання, а на іншому кінці ланцюга закріплений вантаж 7.
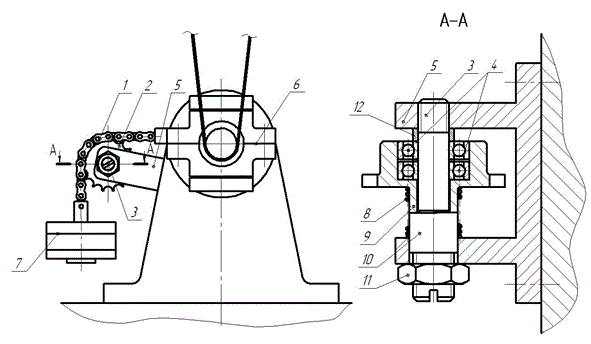
Рисунок 3.5 – Конструкція навантажувального пристрою шліфувальної бабки для внутрішнього шліфування з постійним зусиллям підтиску РПК до заготовки.
На осі 3 розташована гвинтова пружина 8, одна частина внутрішньої поверхні контактує із зовнішнім циліндричною поверхнею маточини 9 на зірочці 2, а інша частина внутрішньої поверхні гвинтовий пружини – з циліндричною поверхнею 10 осі 3, при цьому напрямок гвинта витка пружини є протилежним напрямку обертання зірочки 2 , зумовленої дією вантажу 7. Гайка 11 служить для закріплення осі 3 в вушку нерухомо, а втулка 12 – для регулювання положення зірочки 2 по відношенню до пластинчастої ланцюга 1.
Після включення обертання заготовки шліфувальний круг 10 підводиться до оброблюваної поверхні і рухома частина шліфувальної бабки починає переміщатися під дією вантажу 7. При цьому напрямок обертання зірочки 2, є протилежним напрямку гвинта витка гвинтової пружини 8. У цьому випадку сили тертя на внутрішній поверхні гвинтової пружини 8 з зовнішньою циліндричною поверхнею маточини 9 на зірочці 2 з напрямком гвинта витка пружини різні і розгортають гвинтову пружину 8, внаслідок чого її діаметр збільшується, що забезпечує вільне переміщення рухомої частини шліфувальної бабки у напрямку РПК. При зворотному русі рухомої частини шліфувальної бабки, внаслідок радіального биття РПК, зірочка 2 намагатиметься обертатися в напрямку, який збігається з напрямком витка гвинтової пружини 8. При цьому сили тертя на внутрішній поверхні гвинтовий пружини 8 зовнішньою циліндричною поверхнею маточини 9 на зірочці 2 закручують гвинтову пружину і її діаметр зменшується, сили тертя на внутрішній поверхні гвинтовий пружини 12 і циліндричної поверхні 10 осі 3 ростуть, що робить неможливим обертання зірочки 2, а отже і переміщення рухомої частини 8 шліфувальної бабки в напрямку від оброблюваної поверхні зразка. Таким чином, сила підтиску РПК до зразка і сила, яка перешкоджає переміщенню РПК від оброблюваної поверхні, будуть прикладені в одному і тому ж місці, а саме, на зірочці. У зв'язку з цим, сила підтиску РПК до зразка буде обумовлена величиною вантажу 7, і не залежатиме від можливих перекосів в напрямних рухомої частини пристрою для шліфування шліфуванні з постійною радіальної силою різання і забезпечує відсутність радіальних коливань рухомої частини пристрою.
Такий спосіб реалізації подачі шліфувального круга відповідно до його ріжучої здатністю має ряд істотних недоліків – необхідність зміни конструкції шліфувальної бабки верстата і компонування її приводу; а також обмеженість застосування шліфувальної бабки врізним шліфуванням, так як при шліфуванні з подачею вантаж буде здійснювати коливальний рух.
Тому для здійснення подачі, що змінюється відповідно до закону зміни ТЛРСК верстат пропонується оснастити додатковим пристроєм.
4. Розробка пристрою автоматичної подачі на глибину бабки виробу внутрішньо-шліфувального верстата моделі 3А227П відповідно до закону зміни різальної здатності круга
4.1 Кінематична схема пристрою переміщення бабки виробу
Для здійснення подачі, що змінюється відповідно до закону зміни ТЛРСК в часі верстат пропонується оснастити додатковим пристроєм, кінематична схема якого представлена на рис. 4.1. Задавач приводу переміщення бабки виробу відповідно до закону зміни ТЛРСК, є обчислювальний блок 1, який перетворює закон зміни поточної лімітованої різальної здатності круга в часі в певну кількість імпульсів в одиницю часу, керуючих кроковим двигуном 2. Від вала крокового двигуна 2 обертання передається через безлюфтову пружну муфту 3 на вал 4, від валу 4 на вал 6 через беззазорну черв'ячну передачу 5. Від вала 6 обертання передається через беззазорну циліндричну зубчасту передачу 7 на вал ходового гвинта 8.
Безпроміжкові передачі практично виключають зазор у зубчатому зачепленні, тим самим збільшують точність переміщення бабки виробу. Від ходового гвинта 8 переміщення передається на гайку 9. Гайка 9 з регульованим зазором у гвинтовій парі, жорстко закріплена на корпусі бабки виробу 10. Переміщення бабки виробу 10 здійснюється по роликових напрямних 11.

Рисунок 4.1 – Кінематична схема пристрою переміщення бабки виробу відповідно до закону зміни ТЛРСК
4.2 Автоматична система управління переміщенням бабки виробу
Автоматична система управління (рис. 4.2) переміщенням бабки виробу здійснюється відповідно до знайденого закону зміни поточної лімітованої різальної здатності круга у часі.
Завдач 1 генерує керуючі кроковим двигуном імпульси, відповідно до заданого закону. Також пристрій 1 задає початкове положення бабки виробу у залежності від діаметра отвору, що шліфується.
Керуючі імпульси, які перетворені в електричний сигнал, передаються до порівняльного пристрою 2, у якому відбувається зіставлення сигналу поточного становища бабки виробу з заданим і, в разі потреби, виробляється коригувальний сигнал. Фіксування поточного становища бабки виробу відбувається по ланцюгу зворотного зв'язку, утвореного датчиком 3, фіксуючим фактичне положення бабки виробу і підсилювачем сигналу 4. Отриманий сумарний керуючий сигнал підсилюється підсилювачем 6 і подається на вхід крокового двигуна 7, обертання від якого через безпроміжковий механізм 8, чий принцип роботи описано вище, передається бабці виробу 9.
Індикатори 5 і 10 візуально фіксують координати поточного та заданого положення бабки виробу.
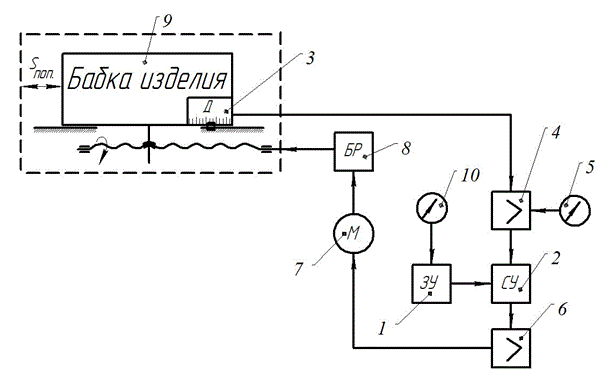
Рисунок 4.2 – Схема автоматичної системи управління механізмом переміщенням бабки виробу
4.3 Визначення закону зміни поточної лімітованої різальної здатності для програмування автоматичної системи управління
З метою програмування автоматичної системи управління бабкою виробу, необхідно знати закон зміни ТЛРСК у часі для конкретних умов обробки, яку визначають експериментально.
Поточну лімітовану ріжучу здатність шліфувального круга 1А1 40×16×10×5 АС6 100/80-4-М2-01 визначали при шліфуванні твердого сплаву [17].
Перед проведенням експерименту круг правили електроерозійним способом за схемою внутрішнього багатопрохідного шліфування до повного оновлення робочої поверхні круга. Як джерело технологічного струму використовували блок живлення ІТТ-35. Правку РПК здійснювали шліфуванням чавунного електрода на режимах: механічних – Vк =26 м/с, Vэ =24 м/хв., глибина шліфування t =0,005 мм; електричних – середня сила струму електроерозійних впливів Iср=10А, напруга холостого ходу Uxx=60 В.
Внутрішнє врізне шліфування з постійним зусиллям підтиску зразка з твердого сплаву марки ВК15 у вигляді кільця, з діаметром отвору Dо=40 мм та висотою В =10 мм, виконували на режимах: Vк = 25,8 м/с, Vэ=24 м/хв.(при заданому параметрі шорсткості Ra=1,25 мкм). Зусилля підтиску зразка до РПК становило Pп= 20 Н, знайдене виходячи з точності обробки, яка є лімітованим технічним обмеженням. Підтиск зразка до РПК здійснювали за допомогою спеціального навантажувального пристрою, що забезпечує стабільне зусилля підтиску в процесі обробки. Охолодження при правці і шліфуванні здійснювали 0,3%-ным ним водним розчином кальцинованої соди. Внутрішній діаметр кільця вимірювали в трьох перетинах за допомогою мікрометра з ціною поділки 10 мкм. Ріжучу здатність оцінювали об'ємом сошлифованого матеріалу, вилученого за одну хвилину. Вимірювання діаметра отвору, а також шліфувального круга виконували після 0,25; 0,5; 1; 2; 5; 10; 15; 30; 45 хвилин обробки.
Величину подачі Sп(τ), яка змінюється відповідно до закону зміни ТЛРСК Q(τ), визначимо використовуючи її значення у різні періоди шліфування за такою формулою:

де Q(τ) – значення ТЛРСК у певні періоди шліфування, мм3/хв.;
Vд – швидкість деталі, м/хв.;
τдис – час дискретизації процесу шліфування, хв.;
Вд – висота оброблюваної циліндричної поверхні зразка, мм.
Використовуючи дані експериментів, був побудован графік залежності поточної лімітованої різальної здатності круга від часу шліфування Q(τ) (рис. 4.3), а також знайдені рівняння регресії у вигляді:

где Q, Qисх, Qуст – відповідно поточна, вихідна, що встановилася ріжуча здатність круга, мм3/хв.; ΔQ = Qисх − Qуст – амплітуда зміни різальної здатності круга, мм3/хв.; βQ – емпіричний коефіцієнт, 1/хв.; τ – тривалість шліфування, хв.
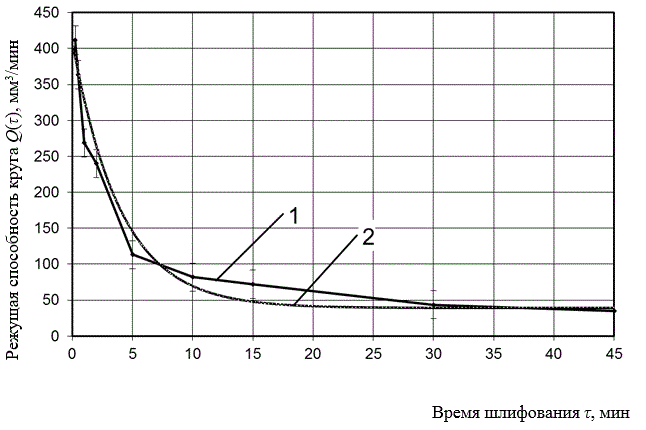
Рисунок 4.3 – Зміна поточної лімітованої різальної здатності круга 1А1 40×16×10×5 АС6 100/80-4-М2-01 при шліфуванні твердого сплаву ВК15:1 – експериментальна крива; 2 – регресійна крива
За вихідну ріжучу здатність Qисх брали ріжучу здатність на першій хвилині шліфування. За сталу брали ріжучу здатність круга після 15 хвилин обробки. Рівняння Q = ƒ(t), отримане методом найменших квадратів, має вигляд:

Отриманий закон зміни ТЛРСК у часі буде використаний при програмуванні запропонованої автоматичної системи управління поперечною подачею бабки виробу внутрішньо-шліфувального верстата моделі 3А227П відповідно до знайденого закону.
4.4 Опис конструкції модернізованого приводу подачі на глибину бабки виробу
Конструкція приводу для забезпечення автоматичної поперечної подачі бабки вироби внутрішньо-шліфувального верстата моделі 3А227П відповідно до закону зміни різальної здатності круга представлений на рис. 4.4.
Забезпечення заданої поточної глибини різання в модернізованому приводі здійснюється завдяки шаговому двигуну 1. Від вала крокового двигуна обертання передається через муфту 3, що з'єднує вал крокового двигуна 1 і вал 3. Через безпроміжкову передачу 4 обертання передається вал 5. На валу 5 закріплена електромагнітна муфта 6. Якщо муфта включена, то крутний момент передається через безпроміжкову циліндричну передачу 7 на ходовий вал 8. Якщо муфта не включена, то переміщення бабки виробу в поперечному напрямку здійснюється вручну.
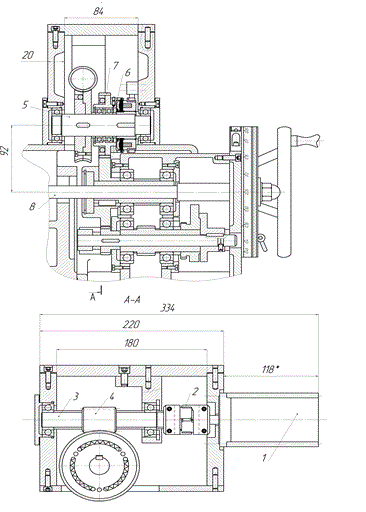
Рисунок 4.4 – Конструкція приводу для забезпечення автоматичної поперечної подачі бабки виробу внутрішньо-шліфувального верстата моделі 3А227П відповідно до ТЛРСК у часі
Конструктивна реалізація безпроміжкових зубчатих передач полягає в наступному. У зубчатої або черв'ячної передачі одне зубчате (черв'ячне) колесо роблять розрізним. Зазор усувається взаємним розворотом половинок, пружинами або по наступним жорстким закріпленням половинок болтами. Усунення зазорів і створення попереднього натягу в передачі досягається взаємним розворотом його кінематичних ланцюгів спеціальним навантажувальним пристроєм. У результаті в кожній кінематичного ланцюга виходить однопрофільне зачеплення, яка не порушується і при реверсі руху.
При включенні крокового електродвигуна, 0,06 мм, бабка переміщується автоматично за заданим законом з точністю 0,5 мкм.
Якщо електромагнітна керована муфта не включена, то рух здійснюється вручну за допомогою рукоятки.
Після цього, на верстат встановлюється заготовка і починається обробка. Рух поперечної подачі дозволяє бабці з виробом переміщатися у широкому діапазоні, достатньому для повної обробки деталі на розмір.
Висновки
У даній роботі проведено аналіз існуючих методів оптимізації режимів шліфування та встановлено, що використання узагальнюючих показників режимів шліфування, що забезпечують стабільні показники якості, дозволяють зменшити трудомісткість пошуку оптимальних режимів.
На основі аналізу існуючих конструкцій пристроїв для шліфування за схемою з постійним зусиллям підтиску РПК до заготовки запропонована конструкція бабки вироби внутрішньошліфувального верстата, яка може бути застосована при внутрішньому шліфуванні за схемою з постійним зусиллям підтиску РПК до заговки, яка забезпечить максимальне використання ріжучих властивостей круга.
При написанні даного реферату магістерська робота ще не завершена. Остаточне завершення: грудень 2014 року. Повний текст роботи та матеріали по темі можуть бути отримані у автора або його керівника після зазначеної дати.
Перелік посилань
- Абразивная и алмазная обработка материалов. Справочник. Под ред. д-ра техн. наук проф. А. Н. Резникова. М.: Машиностроение, 1977. – 391 с.
- Матюха П.Г., Полтавець В. В. Алмазне шліфування з електроерозійними керуючими діями на робочу поверхню круга / Матюха П.Г. , Полтавець В. В.-Донецьк: ДонНТУ, 2006.-164с.
- Глейзер Л.А. О сущности процесса круглого шлифования// Вопросы точности в технологии машиностроения. – М.: Машгиз, 1959.– с.5-24.
- Матюха П.Г. Високопродуктивне шліфування ванадієвих штампових та інструментальних сталей / П.Г. Матюха. Донецьк: ДВНЗ «ДонНТУ», 2008. – 222 с.
- Жулин И.С., Полтавець В.В. Описание процесса алмазного шлифования по упругой схеме с использованием понятия текущей лимитированной режущей способности круга/ Прогрессивные направления развития машино-приборостроительных отраслей и транспорта. Материалы международной научно-технической конференции студентов, аспирантов и молодых ученых 14-17 мая 2007 г. в г. Севастополе. – Севастополь: Изд-во СевНТУ, 2007. – С. 97-98.
- Технология машиностроения. В 2 кн. Кн. 1. Основы технологии машиностроения. Кн. 2. Производство деталей машин: учебное пособие для вузов / Э. Л. Жуков, И. И. Козарь, С. Л. Мурашкин и др.; под ред. С. Л. Мурашкина. – М.: Высшая школа, 2003.
- Палей М.М. и др. Технология шлифования и заточки режущего инструмента. - М.: Машиностроение, 1988.– 288 с.
- Теория инженерного эксперимента: Учеб. Пособие / Г.М. Тимошенко, П.Ф. Зима. – К.:УМК ВО, 1991. – 124с.
- Математический анализ точности механической обработки деталей. Колкер Я.Д. “Техника”, 1976.- 200с.
- Попов С.А., Малевский Н.В., Терещенко Л.М. Алмазно-абразивная обработка металлов и твёрдых сплавов. – М.: Машиностроение, 1977. – 263 с.
- Основы алмазного шлифования/ Семко М.Ф., Грабченко А.И. Раб А.Ф. и др. – Киев: Техніка, 1978. –192 с.
- Матюха П.Г., Стрелков В.Б., Полтавец В.В. Определение режимов плоского шлифования твердых сплавов с использованием нового критерия о текущей лимитированной режущей способности круга/ Сверхтвердые материалы. Научно-теоретич. журнал. – Киев: 2004. – № 3. – С. 67-73.
- Матюха П.Г., Полтавец В.В. Режущая способность рабочей поверхности круга как ограничивающий параметр производительности шлифования. Надежность инструмента и оптимизация технологических систем. Сб. научных трудов. – Краматорск: ДГМА, вып. № 13, 2003. – С. 159-164.
- Габитов В.В. Определение оптимальных режимов внутреннего шлифования твёрдого сплава ВК15 по упругой схеме с периодическими электроэрозионными воздействиями / В.В. Габитов // Надежность инструмента и оптимизация технологических систем. Сборник научных трудов. – Краматорск, вып. №29, 2011. – С. 232-241.
- Шліфувальна бабка Патент України №94813 С2 МПК В24В41/00 Автори: Матюха П.Г., Габітов В.В., Войтов М.С., Благодарний А.О. Заявка а200911849 от 19.11.2009. Опубл 10.06.2011 бюл №11, 2011.
- Навантажувальний пристрій для шліфування ПАТЕНТ УКРАЇНИ №98857 С2 МПК В24В 41/00 Автори: Матюха П.Г., Габітов В.В., Благодарний А.О. Заявка а201012927 от 01.11.2010. Опубл 25.06.2012 бюл №12, 2011.
- Габитов В.В. Определение текущей лимитированой режущей способности алмазного шлифовального круга при шлифовании комбинированного образца «Сталь 45 – твердый сплав ВК8» / В.В. Габитов // Наукові праці Донецького національного технічного університету. Серія: Машинобудування і машинознавство. Випуск 6 (154). – Донецьк: ДонНТУ, 2009. С 35 – 40 с.