Реферат за темою випускної роботи
ПРИМІТКА: Реферат носить постановочний характер, так як час його створення – квітень – травень 2014 р. Тоді як захист магістерської роботи запланований на січень 2015 р.
Зміст
- 1. Актуальність теми
- 2. Мета, методи та завдання дослідження
- 3. Аналіз сучасного стану питань дослідження
- 3.1. Аналіз класифікації з'єднання деталей за формою сполучених поверхонь
- 3.2. Аналіз використання роз'ємних з'єднань що застосовуються в машино – і приладобудуванні
- 3.3. Аналіз застосування не рознімних з'єднань що застосовуються в машино – і приладобудуванні
- 3.4. Аналіз принципів компонування роторних ліній
1. Актуальність теми
Враховуючи розвиток виробництва в напрямку до багатономенклатурного різнострійного виробництва, необхідно підвищувати продуктивність за рахунок синтезу нових технологій шляхом застосування розширеного числа нових машин і механізмів. Для складальних робіт у загальному обсязі машинобудівного виробництва характерна тенденція до постійного підвищення виробництва і виробничих потужностей збірки в цілому [1].
Збірка є заключним етапом виготовлення машини, в значній мірі визначає її експлуатаційні якості, так як в процесі складання з різних причин можуть виникати похибки взаємного розташування деталей і вузлів. Одні й ті ж точно виготовлені деталі за різних умов з'єднання можуть змінити довговічність машин в сотні разів [2].

Для підвищення якості збірки, збільшення продуктивності праці та підвищення економічної ефективності всього складального процесу повинні бути знайдені нові способи вирішення не стандартних завдань. У цьому принципі ефективно застосовуються такі види збірки як вузлова (складальна одиниця чи вузол), при цьому по виду переміщенню збираного об'єкта не повинно бути обмежень, а так само розбиватися на операції складання вузлів.
Такий принцип був розроблений і це модульний принцип.
Із застосуванням модульної технології в збірці відкриваються нові можливості підвищення не тільки продуктивності, але і на ряду з якістю збірки виробів – економічний ефект.
2. Мета і завдання дослідження
Мета магістерської роботи підвищення продуктивності складання виробів на роторних лініях на базі модульної технології. Розробка засобів технологічного оснащення при складанні, засноване на застосуванні модульної технології.
Об'єктом дослідження є з’єднання з зазором, а також перехідні посадки і форма сполучених поверхонь.
Аналіз використання з'єднань і посадок в машинобудуванні в світовому масштабі наведено нижче, на рисунку 2:
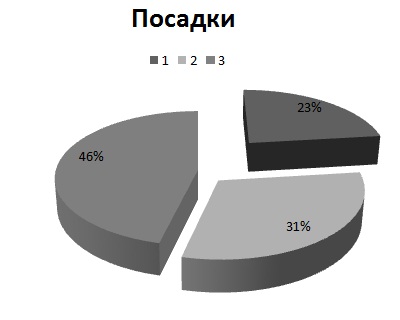
Предмет дослідження – технологічне забезпечення складання виробів на роторній автоматичній лінії а також характерні особливості здійснення процесів складання з використанням модульної технології.
Пропонований модульний принцип побудови технологічних процесів виготовлення виробів, заснований на представленні вироби як структурованого безлічі модулів поверхонь і модулів з'єднання, відкриває нові перспективи у вирішенні проблеми вдосконалення складального виробництва. Він дозволяє виробити єдиний підхід у розробці складальних процесів, засобів їх здійснення широкому впровадженні типізації, уніфікації та стандартизації.
В основі технологічного процесу складання будь-якого виробу лежить, перш за все, процес з'єднання його деталей, складальних одиниць. Цей процес є невід'ємною частиною складального процесу і становить його основу. Саме ця частина складального процесу в першу чергу визначає ефективність всього технологічного процесу і висуває вимоги до засобів механізації та автоматизації [1].
З'єднання деталей, складальних одиниць відбувається за допомогою поєднання їх баз, в якості яких виступають модулі поверхонь (МПБ).
МПР ж являє собою поєднання двох МПБ – прямого і відповідного йому, коли виріб не працює, тобто рухоме з'єднання перетворюється на нерухоме. У цьому випадку, при наявності відносного руху МПБ деталей, що утворили з'єднання (МС), переходять у категорію МПР.
Тут треба відзначити ще одна обставина: видана траєкторія руху одного модуля щодо іншого забезпечується відповідними поверхнями у МПР, що виконують роль баз, у завдання яких входить позбавлення деталей відповідних ступенів свободи.
Вихідними ж даними для розробки модульного технологічного процесу виготовлення робили, є її креслення в модульному поданні та обсяг випуску. Тому, перш ніж розробляти модульний технологічний процес, треба деталь представити сукупністю МП. Однак МП, наведені в класифікації є конструкторськими, так як своїм конструктивно - геометричним оформленням і характеристиками відображають вимоги службового призначення деталі.
У той же час аналіз різних деталей показує, що у них зустрічаються поверхні, які не належать до базуючи, робочих чи сполучною МП. Пояснюється це тим, що при виготовленні деталей діють закони технології, внаслідок чого доводиться передбачати біля деталі різноманітних додаткові поверхні, що полегшують її виготовлення. Такі поверхні, що поліпшують технологічність деталі, будемо називати технологічними та домовимося відносити їх до класу МПС.
Однак з позицій технології виготовлення деталі в ряді випадків такі МП бажано поєднувати з іншими МП в групи, що отримали назву інтегральних модулів поверхонь (МПІ).
Тому в тих випадках, коли деякі МП об'єднують в МПІ, треба внести відповідні корективи в креслення деталі.
Відповідно до цього в загальному випадку креслення деталі в модульному виконанні може бути представлений сукупністю тільки МП або тільки МПІ або МП з МПІ [1].
3. Аналіз сучасного стану питань дослідження
3.1 Аналіз класифікації з'єднання деталей за формою сполучених поверхонь
Частка складальних робіт у загальному обсязі машинобудівного виробництва коливається в межах від 25 до 40%, а в галузі приладобудування досягає 70 %. У дослідному виробництві ці показники зростають удвічі [1].
Класифікація з'єднання деталей, застосовуваних у машино- та приладобудуванні, прийнято ділити на рухливі, що забезпечують переміщення однієї деталі щодо іншої, і нерухомі, в яких дві або кілька деталей жорстко скріплені один з одним [3].
Види з'єднань деталей (рисунок 3) ; Класифікація з'єднань деталей (рисунок 4).
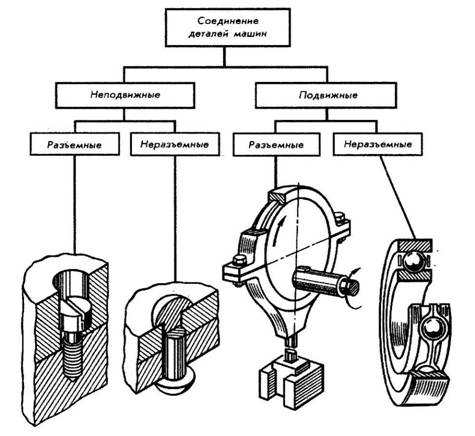
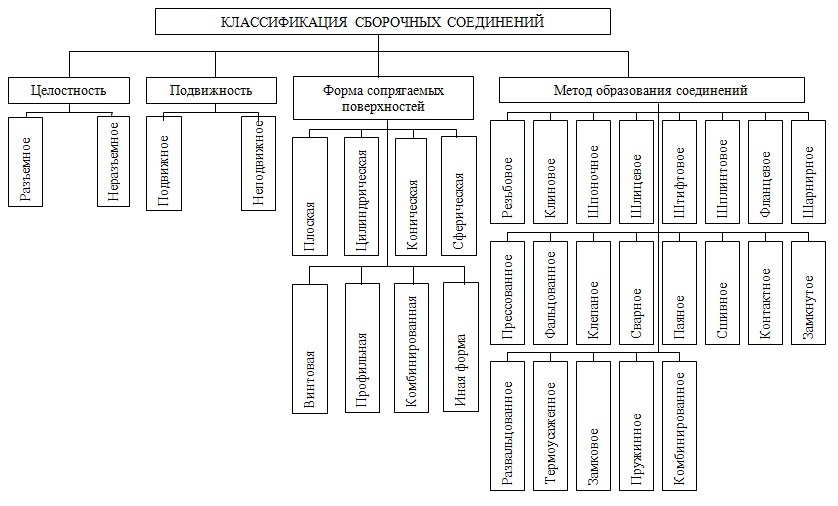
У свою чергу за схемою класифікації складальних з'єднань форма сполучених поверхонь буває:
– плоска
– циліндрична
– конічна
– сферична
– гвинтова
– профільна
Аналіз за формою сполучених поверхонь наводиться нижче, на рисунку 5:
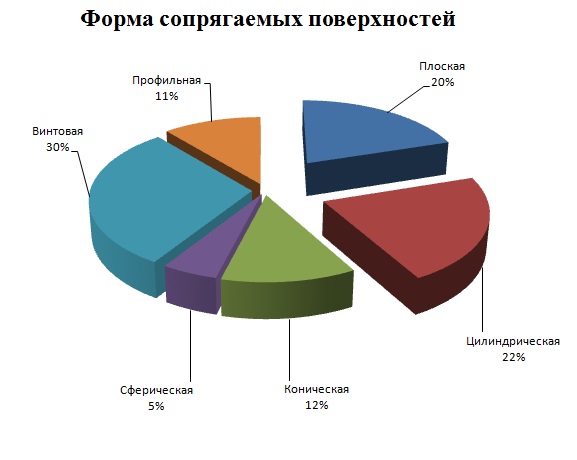
3.2. Аналіз використання роз'ємних з'єднань що застосовуються в машино – і приладобудуванні
Кожен з цих двох типів з'єднань поділяють на дві основні групи: роз'ємні і нероз'ємні. Роз'ємними називаються такі сполуки, які дозволяють виробляти багаторазову складання та розбирання складальної одиниці без пошкодження деталей. До рознімним нерухомим сполук відносяться різьбові, штифтові, шпонкові, шліцьові, а також сполуки, здійснювані перехідними посадками. Роз'ємні рухливі з'єднання мають рухливі посадки (посадки з зазором) по циліндричним, конічним, гвинтовим і плоским поверхням [3].
Аналіз використання роз'ємних з'єднань наводиться нижче, на рисунку 6:
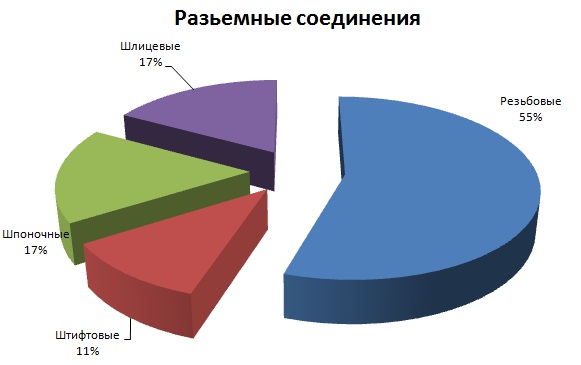
3.3. Аналіз використання не роз'ємних з'єднань що застосовуються в машино – і приладобудуванні
Нероз'ємними називаються такі сполуки, які можуть бути розібрані лише шляхом руйнування або неприпустимих залишкових деформацій одного з елементів конструкції. Нероз'ємні нерухомі з'єднання здійснюються механічним шляхом (запресовкою, склепкою, загинанням, керненням і карбуванням), за допомогою сил фізико -хімічного зчеплення (зварюванням, паянням і склеюванням) і шляхом занурення деталей в розплавлений матеріал (заформовка в ливарні форми, в прес-форми й т. п.) [4].
Аналіз застосування з'єднань наведено нижче на рисунку 7:
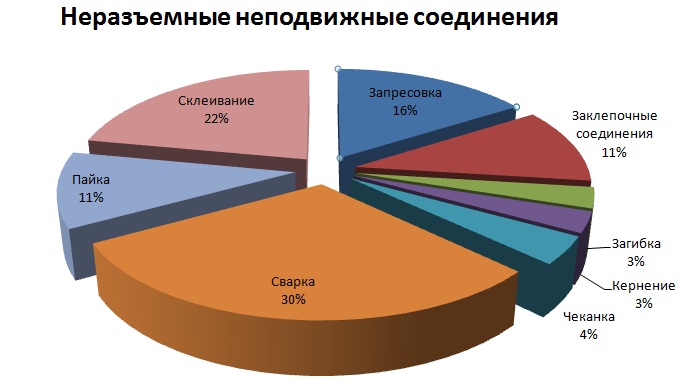
3.4. Анализ принципов компоновки роторных линий
Різновидом автоматичних ліній є роторні автоматичні лінії, розроблені інженером Л.Н.Кошкіним.
Роторні лінії є однією з вищих форм автоматизації технологічних процесів, зовнішнього та внутрішнього транспортування потоку оброблюваних деталей здійснюється безперервно з постійною швидкістю, що полегшує управління продуктивністю і якістю обробки. Автоматизація виробничих процесів включає комплекс наукових і технічних заходів з розробки інтенсифікованих технологічних операцій і створення на їх основі високопродуктивного устаткування, що виконує основні технологічні та допоміжні операції без участі людини. Рівні автоматизації відрізняються ступенем охоплення основних і допоміжних операцій виробничого процесу. На базі роторних ліній здійснюється комплексна автоматизація виробничих процесів, що включають обробку деталей штампуванням і різанням, складання, розфасовку, комплектацію, маркування та упаковку. Досвід показує, що для окремих видів виробництв створення цехів – автоматів, оснащених тільки автоматичними роторними лініями, дає значний економічний ефект [5].
Автоматична роторна лінія складається з робочих роторів і транспортних роторів, передавальних заготовки з одного робочого ротора на інший (рисунок 8).
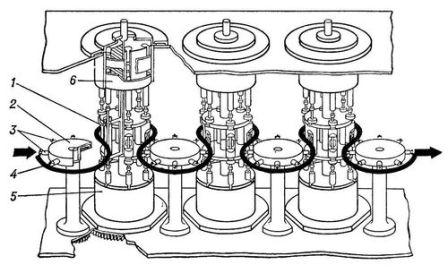
Робочий ротор являє собою жорстку систему, на якій монтується група знарядь, рівномірно розташованих навколо загального обертаючого систему валу. Необхідні робочі руху повідомляються цим знаряддям виконавчими органами, для малих зусиль застосовуються механічні виконавчі органи, для великих – гідравлічні (наприклад, штоки гідравлічних силових циліндрів).
Інструмент, як правило, монтується комплектно в попередньо налгоджується (поза робочих машин) блоках, сполучених з виконавчими органами ротора переважно тільки осьовим зв’язком забезпчує ожливість швидкої заміни блоків. Транспортні ротори приймають, транспортують і передають вироби. Вони являють собою барабани або диски, оснащені несучими органами. Найчастіше застосовуються прості транспортні ротори, що мають однакову транспортну швидкість, загальну площину транспортування і однакову орієнтацію предметів обробки. Для передачі виробів між робочими роторами з різними кроковими відстанями або різним становищем предметів обробки призначені транспортні ротори, які можуть змінювати кутову швидкість і положення в просторі транспортуються предметів. Робітники і транспортні ротори з'єднуються в лінії загальним синхронним приводом, що переміщує кожен ротор на один крок за час, відповідне темпу лінії [7].
На автоматичних роторних лініях можна виконувати операції, які відрізняються за тривалістю, наприклад пресові, контрольні, термічні та хімічні. Автоматична роторна лінія може одночасно обробляти кілька різних виробів. Такі багатономенклатурними автоматичні роторні лінії можуть застосовуватися в немасових виробництвах (рисунок 9).
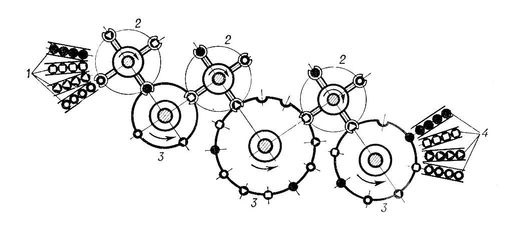
Автоматичні роторні лінії можуть працювати за так званими рефлекторним циклограми, що забезпечує спрацьовування кожного органу відповідно з командою контролю по одному з декількох передбачених законів (наприклад, здійснити робочий хід або відмовитися від нього). Рефлекторні циклограми дозволяють машині реагувати без зупинки на різні відхилення від нормального ходу роботи, наприклад на надходження некондиційного предмета, припинення подачі деталі при збірці і тощо [6].
4. Наукова новизна
Отримала подальший розвиток використання модульної технології складальних процесів в умовах систем безперервної дії.
Висновки
Наукові дослідницькі роботи, що ведуться з удосконалення машинобудівного виробництва відрізняються розрізненістю, відсутністю загальної ідеї, фрагментарністю і відмінністю підходів, методів і засобів у їх вирішенні.
Все це призводить до дублювання робіт, розпорошення сил, відсутності концентрації зусиль на головних напрямках, в ряді випадків несумісності розробок.
У підсумку розвиток машинобудівного комплексу як єдиного цілого здійснюється багато в чому стихійно, нераціонально, нерівномірно, коли одні проблеми вирішуються досить повно, інші частково, а деякі практично не вирішуються; з іншого боку, численні розробки не піддаються обліку, що робить машинобудування безмежним, а процес його розвитку – некерованим.
З викладеного випливає, що сьогодні головне завдання полягає не скільки в пошуку нових технологічних і технічних рішень для забезпечення складального процесу на роторних лініях, скільки в не стандартних підході при вирішенні даних завдань.
Вирішити цю проблему можна тільки за допомогою нової ідеї, здатної забезпечити в собі всі складові для вирішення даної проблеми.
Такою ідеєю є застосування модульної технології в збірці на роторних лініях, так як дана технологія забезпечує підвищення продуктивності, економічний ефект а також якісний скачок складального процесу деталей машин.