Реферат по теме выпускной работы
ПРИМЕЧАНИЕ: Реферат носит постановочный характер, так как время его создания – апрель – май 2014 г., тогда как защита магистерской работы запланирована на январь 2015 г.
Содержание
- 1. Актуальность темы
- 2. Цель, методы и задачи исследования
- 3. Анализ современного состояния вопросов исследования
- 3.1. Анализ классификации соединения деталей по форме сопрягаемых поверхностей
- 3.2. Анализ использования разъемных соединений применяемых в машино – и приборостроении
- 3.3. Анализ использования не разъемных соединений применяемых в машино – и приборостроении
- 3.4. Анализ принципов компоновки роторных линий
1. Актуальность темы
Учитывая развитие производства в направлении к многономенклатурному разносерийному производству, необходимо повышать производительность за счет синтеза новых технологий путем применения расширенного числа новых машин и механизмов. Для сборочных работ в общем объеме машиностроительного производства характерна тенденция к постоянному повышению производства и производственных мощностей сборки в целом [1].
Сборка является заключительным этапом изготовления машины, в значительной степени определяющий ее эксплуатационные качества, так как в процессе сборки по разным причинам могут возникать погрешности взаимного расположения деталей и узлов. Одни и те же точно изготовленные детали при разных условиях соединения могут изменить долговечность машин в сотни раз [2].

Для повышения качества сборки, увеличения производительности труда и повышения экономической эффективности всего сборочного процесса должны быть найдены новые способы решения не стандартных задач. В этом принципе эффективно применяются такие виды сборки как узловая (сборочная единица или узел), при этом . по виду перемещению собираемого объекта не должно быть ограничений, а так же разбиваться на операции сборки узлов. Такой принцип был разработан и это модульный принцип.
С применением модульной технологии в сборке открываются новые возможности повышения не только производительности, но и на ряду с качеством сборки изделий – экономический эффект.
2. Цель, методы и задачи исследования
Цель магистерской работы – повышение производительности сборки изделий на роторных линиях на базе модульной технологии. Разработка средств технологического оснащения при сборке, основанное на применении модульной технологии.
Объектом исследования являются соединения с зазором, а также переходные посадки и форма сопрягаемых поверхностей.
Анализ использование соединений и посадок в машиностроении в мировом масштабе приведено ниже, на рисунке 2:
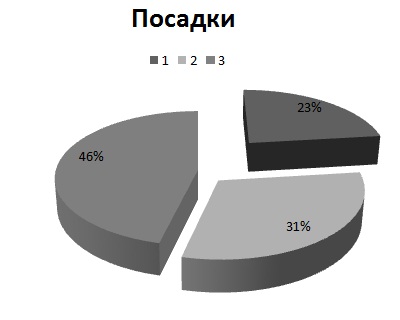
Предмет исследования – технологическое обеспечение сборки изделий , роторные автоматические линии а также характерные особенности осуществления процессов сборки с использованием модульной технологии.
Предлагаемый модульный принцип построения технологических процессов изготовления изделий, основанный на представлении изделия как структурированного множества модулей поверхностей и модулей соединения, открывает новые перспективы в решении проблемы совершенствования сборочного производства. Он позволяет выработать единый подход в разработке сборочных процессов, средств их осуществления широком внедрении типизации, унификации и стандартизации.
В основе технологического процесса сборки любого изделия лежит, прежде всего, процесс соединения его деталей, сборочных единиц. Этот процесс является неотъемлемой частью сборочного процесса и составляет его основу. Именно эта часть сборочного процесса в первую очередь определяй Эффективность всего технологического процесса и предъявляет требования к средствам механизации и автоматизации [1].
Соединение деталей, сборочных единиц происходит посредством совмещения их баз, в качестве которых выступают базирующие модули поверхностей (МПБ).
МПР же представляет собой совмещение двух МПБ – прямого и ответного ему, когда изделие не работает, т.е. подвижное соединение превращается в неподвижное. В этом случое при наличии относительного движения МПБ деталей, образовавших соединение (МС), переходят в категорию МПР.
Здесь надо отметить еще одно обстоятельство: изданная траектория движения одного модуля относительно другого обеспечивается соответствующими поверхностями у МПР, выполняющих роль баз, в задачу которых входит лишение деталей соответствующих степеней свободы.
Исходными же данными для разработки модульного технологического процесса изготовления делали, является ее чертеж в модульном представлении и объем выпуска. Поэтому, прежде чем разрабатывать модульный технологический процесс, надо деталь представить совокупностью МП. Однако МП, приведенные в классификации являются конструкторскими, так как своим конструктивно-геометрическим оформлением и характеристиками отражают требования служебного назначения детали.
В тоже время анализ различных деталей показывает, что у них встречаются поверхности, не принадлежащие к базирующим, рабочим или связующим МП. Объясняется это тем, что при изготовлении деталей действуют законы технологии, вследствие чего приходится предусматривать у детали различного рода дополнительные поверхности, облегчающие ее изготовление. Такие поверхности, улучшающие тех нелогичность детали, будем называть технологическими и условимся относить их к классу МПС.
Однако с позиций технологии изготовления детали в ряде случаев такие МП желательно объединять с другими МП в группы, получившие название интегральных модулей поверхностей (МПИ).
Поэтому в тех случаях, когда некоторые МП объединяют в МПИ, надо внести соответствующие коррективы в чертеж детали.
В соответствии с этим в общем случае чертеж детали в модульном исполнении может быть представлен совокупностью только МП или только МПИ или МП с МПИ [1].
3. Анализ современного состояния вопросов исследования
3.1 Анализ классификации соединения деталей по форме сопрягаемых поверхностей
Доля сборочных работ в общем объеме машиностроительного производства колеблется в пределах от 25 до 40%, а в отрасли приборостроения достигает 70%. В опытном производстве эти показатели возрастают вдвое [1].
Классификация соединения деталей, применяемых в машино-и приборостроении, принято делить на подвижные, обеспечивающие перемещение одной детали относительно другой, и неподвижные, в которых две или несколько деталей жестко скреплены друг с другом [3].
Виды соединений деталей (рисунок 3); Классификация соединений деталей (рисунок 4).
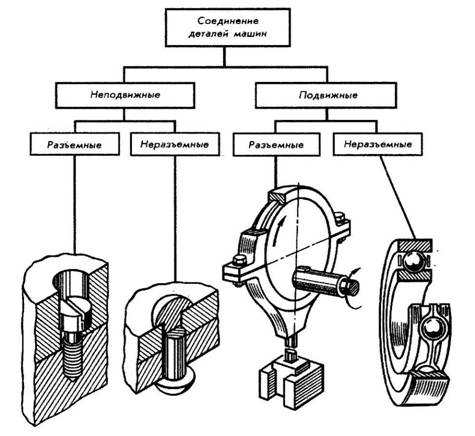
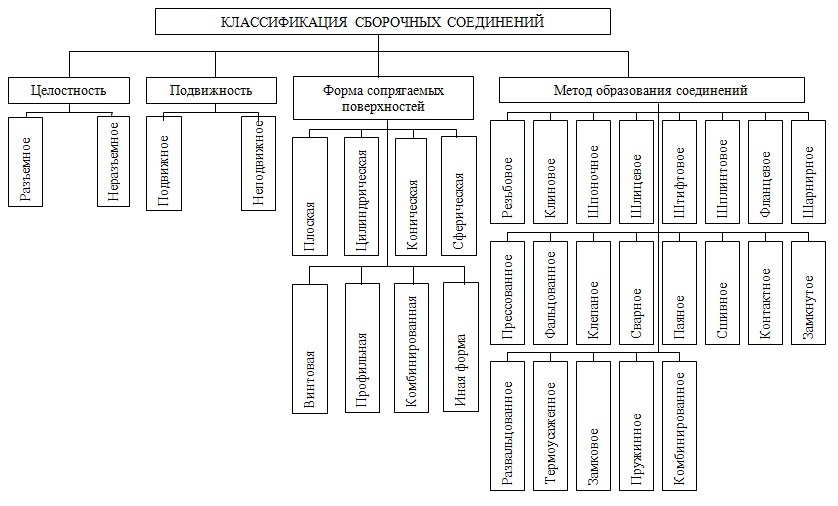
В свою очередь по схеме классификации сборочных соединений форма сопрягаемых поверхностей бывает:
– плоская
– цилиндрическая
– коническая
– сферическая
– винтовая
– профильная
Анализ по форме сопрягаемых поверхностей приводится ниже, на рисунке 5:
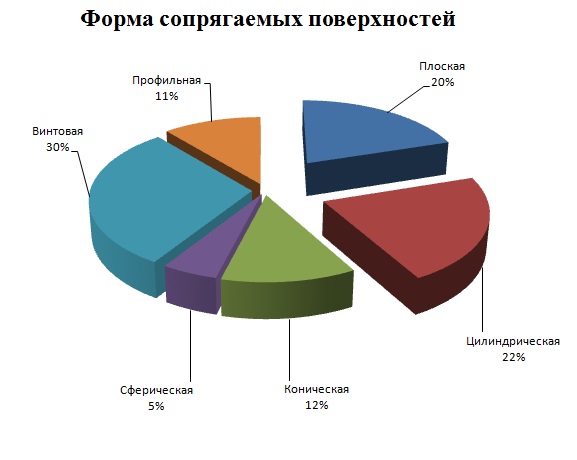
3.2. Анализ использования разъемных соединений применяемых в машино – и приборостроении
Каждый из этих двух типов соединений подразделяют на две основные группы: разъемные и неразъемные. Разъемными называются такие соединения, которые позволяют производить многократную сборку и разборку сборочной единицы без повреждения деталей. К разъемным неподвижным соединениям относятся резьбовые, штифтовые, шпоночные, шлицевые, а также соединения, осуществляемые переходными посадками. Разъемные подвижные соединения имеют подвижные посадки (посадки с зазором) по цилиндрическим, коническим, винтовым и плоским поверхностям [3].
Анализ использования разъемных соединений приводится ниже, на рисунке 6:
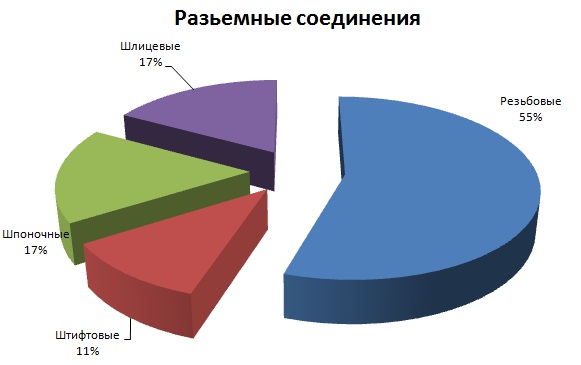
3.3. Анализ использования не разъемных соединений применяемых в машино – и приборостроении
Неразъемными называются такие соединения, которые могут быть разобраны лишь путем разрушения или недопустимых остаточных деформаций одного из элементов конструкции. Неразъемные неподвижные соединения осуществляются механическим путем (запрессовкой, склепыванием, загибкой, кернением и чеканкой), с помощью сил физико-химического сцепления (сваркой, пайкой и склеиванием) и путем погружения деталей в расплавленный материал (заформовка в литейные формы, в пресс-формы и т. п.) [4].
Процентное отношение применения данных соединений приведено ниже на рисунке 7:
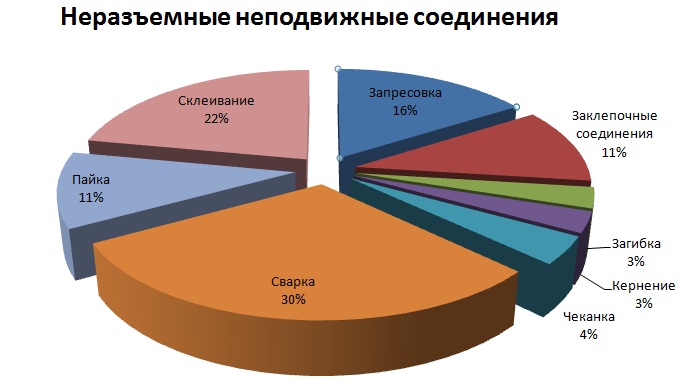
3.4. Анализ принципов компоновки роторных линий
Разновидностью автоматических линий являются роторные автоматические линии, разработанные инженером Л.Н.Кошкиным.
Роторные линии являются одной из высших форм автоматизации технологических процессов, так как межмашинное и внутри машинное транспортирование потока обрабатываемых деталей осуществляется непрерывно с постоянной скоростью, что облегчает управление производительностью и качеством обработки. Автоматизация производственных процессов включает комплекс научных и технических мероприятий по разработке интенсифицированных технологических операций и создания на их основе высокопроизводительного оборудования, выполняющего основные технологические и вспомогательные операции без участия человека. Уровни автоматизации отличаются степенью охвата основных и вспомогательных операций производственного процесса. На базе роторных линий осуществляется комплексная автоматизация производственных процессов, включающих обработку деталей штамповкой и резанием, сборку, расфасовку, комплектацию, маркировку и упаковку. Опыт показывает, что для отдельных видов производств создание цехов-автоматов, оснащенных только автоматическими роторными линиями, дает значительный экономический эффект [5].
Автоматическая роторная линия состоит из рабочих роторов и транспортных роторов, передающих заготовки с одного рабочего ротора на другой (рисунок 8).
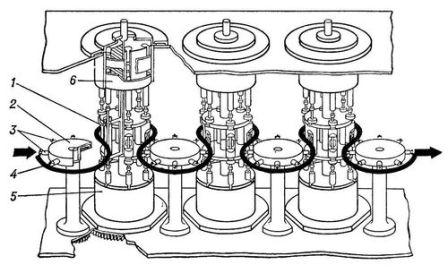
Рабочий ротор представляет собой жёсткую систему, на которой монтируется группа орудий, равномерно расположенных вокруг общего вращающего систему вала. Необходимые рабочие движения сообщаются этим орудиям исполнительными органами, для малых усилий применяются механические исполнительные органы, для больших — гидравлические (например, штоки гидравлических силовых цилиндров).
Инструмент, как правило, монтируется комплектно в предварительно налаживаемых (вне рабочих машин) блоках, сопрягаемых с исполнительными органами ротора преимущественно только осевой связью, что обеспечивает возможность быстрой замены блоков. Транспортные роторы принимают, транспортируют и передают изделия. Они представляют собой барабаны или диски, оснащенные несущими органами. Чаще применяются простые транспортные роторы, имеющие одинаковую транспортную скорость, общую плоскость транспортирования и одинаковую ориентацию предметов обработки. Для передачи изделий между рабочими роторами с различными шаговыми расстояниями или различным положением предметов обработки предназначены транспортные роторы, которые могут изменять угловую скорость и положение в пространстве транспортируемых предметов. Рабочие и транспортные роторы соединяются в линии общим синхронным приводом, перемещающим каждый ротор на один шаг за время, соответствующее темпу линии [7].
На автоматических роторных линиях можно выполнять операции, значительно различающиеся по продолжительности, например прессовые, контрольные, термические и химические. Автоматическая роторная линия может одновременно обрабатывать несколько различных изделий. Такие многономенклатурные автоматические роторные линии могут применяться в немассовых производствах (рисунок 9).
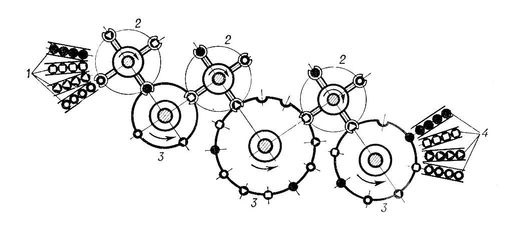
Автоматические роторные линии могут работать по так называемым рефлекторным циклограммам, обеспечивающим срабатывание каждого органа в соответствии с командой контроля по одному из нескольких предусмотренных законов (например, совершить рабочий ход или отказаться от него). Рефлекторные циклограммы позволяют машине реагировать без остановки на различные отклонения от нормального хода работы, например на поступление некондиционного предмета, прекращение подачи детали при сборке и т. п. [6].
4. Научная новизна полученных результатов
Получила дальнейшее развитие использования модульной технологии сборочных процессов в условиях систем непрерывного действия.
Выводы
Ведущиеся научные исследовательские работы по совершенствованию машиностроительного производства отличаются разрозненностью, отсутствием общей идеи, фрагментарностью и различием подходов, методов и средств в их решении.
Все это приводит к дублированию работ, распылению сил, отсутствию концентрации усилий на главных направлениях, в ряде случаев несовместимости разработок.
В итоге развитие машиностроительного комплекса как единого целого осуществляется во многом стихийно, нерационально, неравномерно, когда одни проблемы решаются достаточно полно, другие частично, а некоторые практически не решаются; с другой стороны, многочисленные разработки не поддаются учету, что делает машиностроение необозримым, а процесс его развития - неуправляемым.
Из изложенного следует, что сегодня главная задача заключается не сколько в поиске новых технологических и технических решений для обеспечения сборочного процесса на роторных линиях, сколько в не стандартном подходе при решении данных задач.
Решить эту проблему можно только с помощью новой идеи, способной обеспечить в себе все составляющие для решения данной проблемы. Такой идеей является применение модульной технологии в сборке на роторных линиях, так как данная технология обеспечивает повышение производительности, экономический эффект а также качественный скачек сборочного процесса деталей машин.