Реферат по теме выпускной работы
Содержание
- Введение
- 1. Актуальность темы
- 2. Цель и задачи исследования, планируемые результаты
- 3. Основные способы дробления. Классификация оборудования.
- 3.1 Щековые дробилки.
- 3.2 Конусные дробилки.
- 3.3 Валковые дробилки.
- 3.4 Молотковые дробилки и дезинтеграторы.
- 4. Предложенное гидравлическое дробление угля.
- Выводы
- Список источников
Введение
Обогащение полезных ископаемых – совокупность процессов первичной обработки минерального сырья, имеющая своей целью отделение всех ценных минералов от пустой породы, а также взаимное разделение ценных минералов.
При обогащении возможно получение как конечных товарных продуктов (известняк, асбест, графит и др.), так и концентратов, пригодных для дальнейшей химической или металлургической переработки. Обогащение – наиважнейшее промежуточное звено между добычей полезных ископаемых и использованием извлекаемых веществ. В основе теории обогащения лежит анализ свойств минералов и их взаимодействия в процессах разделения – минералургия.
Обогащение позволяет существенно увеличить концентрацию ценных компонентов. Содержание важных цветных металлов – меди, свинца, цинка – в рудах составляет 0,3–2%, а в их концентратах – 20–70%. Концентрация молибдена увеличивается от 0,1–0,05% до 47–50%, вольфрама – от 0,1–0,2% до 45–65%, зольность угля снижается от 25–35% до 2–15%. В задачу обогащения входит также удаление вредных примесей минералов мышьяк, сера, кремний и т.д.). Извлечение ценных компонентов в концентрат в процессах обогащения составляет от 60 до 95%.
Операции обработки, которым подвергают на обогатительной фабрике горную массу, подразделяют на: основные (собственно обогатительные); подготовительные и вспомогательные.
Все существующие методы обогащения основаны на различиях в физических или физико-химических свойствах отдельных компонентов полезного ископаемого. Существует, например, гравитационное, магнитное, электрическое, флотационное, бактериальное и др. способы обогащения.
Переработка полезных ископаемых на обогатительных фабриках включает ряд последовательных операций, в результате которых достигается отделение полезных компонентов от примесей. По своему назначению процессы переработки полезных ископаемых разделяют на подготовительные, основные (обогатительные) и вспомогательные (заключительные).
В данной работе будет акцентироваться внимание на подготовительной стадии обогащения каменного угля, а именно на процессе дробления.
Дробление проводят на специальных дробильных установках. Дроблением называется процесс разрушения твердых тел с уменьшением размеров кусков до заданной крупности, путем действия внешних сил, преодолевающих внутренние силы сцепления, связывающие между собой частицы твердого вещества.[1]
1. Актуальность темы.
Разрабатывающиеся в нынешнее время угольные пласты отличаются большой зольностью от 35 и более процентов. Использование таких углей в металлургии и энергетике требует дополнительных затрат.
Дробление в большинстве случаев – это основная и часто наиболее энергоёмкая операция, предназначенная для разрушения до требуемых размеров сырья, а также для раскрытия взаимно сросшихся агрегатов и образования частиц отдельных материалов.
В настоящее время обогащение угля осуществляется на обогатительных фабриках, которые применяют технически возможное оборудование. Разработка более экономичных и производительных способов обогащения угля на различных его этапах является очень актуальной.
2. Цель и задачи исследования, планируемые результаты.
Целью данной работы является разработка гидравлической дробилки для дробления угля на обогатительных фабриках, определение её технических параметров и основных конструктивных размеров.
Для достижения поставленной цели необходимо выполнить задачи:
- Рассмотреть и проанализировать эффективность применения имеющихся на данный момент дробилок на обогатительных фабриках;
- Определить особенности технологии дробления с использованием гидроимпульсной установки;
- Произвести аналитический расчет и конструкторские разработки по созданию гидроимпульсной дробилки.
Планируется разработать гидравлическую дробилку для дробления крепкого каменного угля на обогатительных фабриках.
3. Основные способы дробления. Классификация оборудования.
Основными способами дробления, осуществляемыми рабочими органами дробильных машин, являются раздавливание (сжатие), удар, истирание и раскалывание.
Часто эти способы сочетают друг с другом, например, раздавливание с ударом, удар с истиранием и т. п., при этом комбинируется действие сил изгибающих, срезающих и разрывающих.
Выбор способов дробления зависит от физико-механических свойств материала (твердости, хрупкости, вязкости, загрязненности глиной, склонности к замазыванию дробильной камеры), начальной величины кусков и требуемой степени измельчения.
Твердые материалы наиболее эффективно измельчаются ударом или раздавливанием, пластические (глина) – раздавливанием в сочетании с истиранием, хрупкие материалы (уголь) – раскалыванием.
От правильного выбора типа дробильной машины, а следовательно, и способа дробления в значительной степени зависят качество готового продукта и производительность агрегата. Никогда не надо стремиться осуществлять полное измельчение в одной машине, всегда выгоднее и целесообразнее стадийное дробление последовательно на нескольких соответствующих по размерам и конструкциям дробильных машинах.
В настоящее время созданы и успешно эксплуатируются дробилки различных конструкций. Основные требования, которым должна удовлетворять любая дробилка, сводятся к следующему.
1.Конструкция и размеры загрузочного отверстия должны соответствовать прочности дробимого материала и размерам его отдельных кусков: так, например, дробилка, измельчающая твердый материал, должна иметь достаточно большой запас прочности конструкции и ширина загрузочного отверстия должна быть больше размера наибольших кусков в поперечнике на 30–40%. Это предотвращает явление «зависания» кусков в приемном отверстии, снижает простои оборудования, связанные с извлечением «негабарита», и создает благоприятные условия для автоматизации технологического процесса.
2.Для технологической увязки последовательно работающих дробилок и надежной работы систем автоматизации необходимо, чтобы приемное отверстие дробилок последующей стадии было на 60–80% больше разгрузочной щели дробилок предыдущей стадии.
3.Дробилка должна иметь некоторый запас (15–20%) производительности, чтобы в случае увеличения количества поступающего материала не было перегрузки.
4.Дробление – весьма энергоемкий процесс, поэтому удельный расход энергии должен быть небольшим. Следует помнить общее свойство всех дробилок: при увеличении степени измельчения уменьшается производительность машины и увеличивается расход энергии.
5.Необходимо сводить к минимуму количество пыли, образующейся в процессе дробления. Пыль и каменная мелочь играют роль амортизатора (подушки). Заполняя пространство между крупными кусками, они смягчают удар и тем самым снижают эффективность дробления: уменьшается производительность, увеличиваются расход энергии и износ дорогостоящих деталей дробилок. Пыль вредна для здоровья обслуживающего персонала.
6.Раздробленный материал следует из дробилки выгружать быстро и непрерывно во избежание его переизмельчения, чрезмерного пылеобразования и усиления износа деталей.
7.Конструкция дробилки должна позволять быстро и легко заменять износившиеся или поломавшиеся детали.
8.Раздробленный материал должен состоять из кусков по возможности одного размера и кубообразной формы, что особенно важно при дроблении щебня для бетонных работ.
9.Дробилка должна иметь легкие и недорогие предохранительные детали. В случае попадания недробимых предметов (кусков рельсов, зубьев ковша экскаватора и др.) такие детали деформируются или ломаются, тем самым предохраняя основные дорогостоящие детали дробилки от поломки.
Как и всякая машина, дробилка должна быть прочной, дешевой, простой в изготовлении и эксплуатации, не требовать высококвалифицированного обслуживания и потреблять минимальное количество энергии.[2]
3.1 Щековые дробилки.
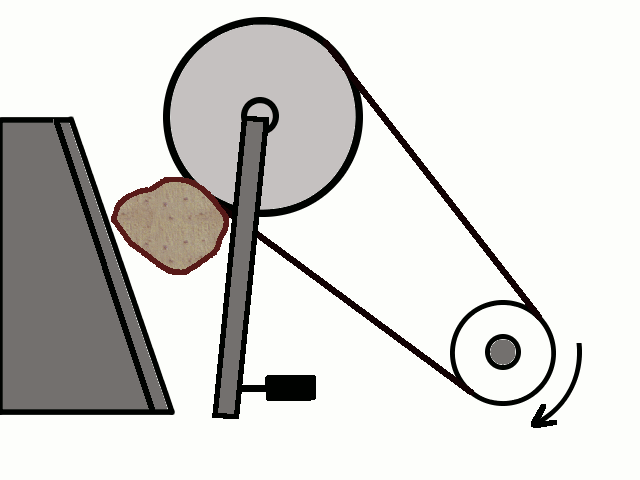
Рисунок 1 – Принципиальная схема щековой дробилки (293 кБ, 9 кадров)[3]
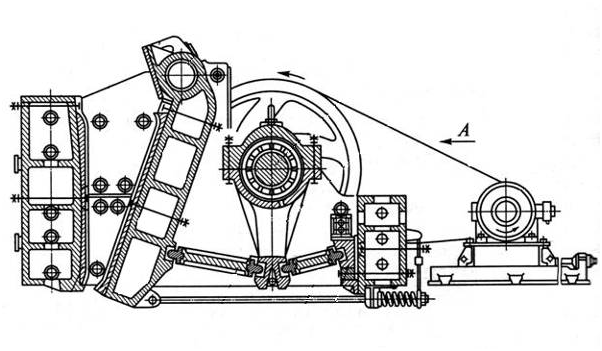
Рисунок 2 – Щековая дробилка с простым движением подвижной щеки
Щековые дробилки разделяются на два основных класса: с простым и сложным движением подвижной щеки. Дробилки с простым движением подвижной щеки различаются между собой способом ее крепления и приводным механизмом. Различают дробилки с верхним подвесом щеки, с нижней шарнирной опорой, с кулачковым приводным механизмом, с кривошипно-шарнирным приводным механизмом. В дробилках со сложным движением подвижной щеки, последняя шарнирно подвешена на эксцентриковом приводном валу. Значительное вертикальное перемещение щек, обусловливающее их истирающее действие на куски материала, приводят к повышенному износу дробящих плит. Поэтому дробилки со сложным движением применяют преимущественно для малоабразивных материалов. Достоинства: их простота конструкции, компактность и небольшая масса.[4]
На рис.3 изображена схема щековой дробилки со сложным движением щеки ЩДС. Станина дробилки сварная. Ее боковые стенки выполнены из стальных листов и соединены между собой передней стенкой 1 коробчатого сечения и задней балкой 2, являющейся одновременного корпусом регулировочного устройства 7. Над приемным отверстием укреплен защитный кожух 3. Подвижная щека 4 закреплена на эксцентриковой части приводного вала 5, в нижней части щеки имеется паз, куда вставляется вкладыш для упора распорной плиты 6. Другим концом распорная плита упирается во вкладыш регулировочного устройства, состоящего из ползуна 13 и двух винтов 14. Замыкающее устройство состоит их тяги 8 и цилиндрической пружины 9. Подвижная щека имеет в нижней части косой выступ, на который устанавливают дробящую футеровочную плиту 10. Неподвижная дробящая плита 11 опирается внизу на выступ передней стенки станины 1, а с боковых сторон зажата футеровочными плитами 12.
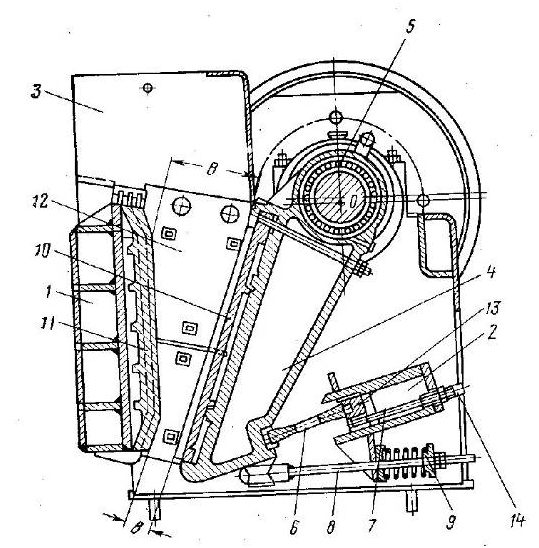
Рисунок 3 – Щековая дробилка со сложным движением щеки
3.2 Конусные дробилки.
Конусные дробилки разделяются на дробилки для крупного, среднего и мелкого дробления. Принцип действия всех конусных дробилок одинаков. Дробящий конус жестко крепится на валу, подвешенном к точке О, а нижним концом свободно вставлен в эксцентриковый стакан. Стакан устанавливается концентрично со станиной дробилки. Ось вала несколько наклонена к вертикальной оси корпуса дробилки. Эксцентриковый стакан получает вращение от электродвигателя. Жестко закрепленный на валу дробящий конус совершает круговые качания, последовательно приближаясь к стенкам конической чаши и удаляясь. Приближение дробящего конуса к чаше сопровождается дроблением кусков материала, поступающих в пространство между ними, а удаление – разгрузкой дробленого продукта. Дробление материала в конусных дробилках происходит непрерывно. При отсутствии холостого хода время дробления, а, следовательно, и производительность у конусных дробилок выше, чем у щековых.[5]
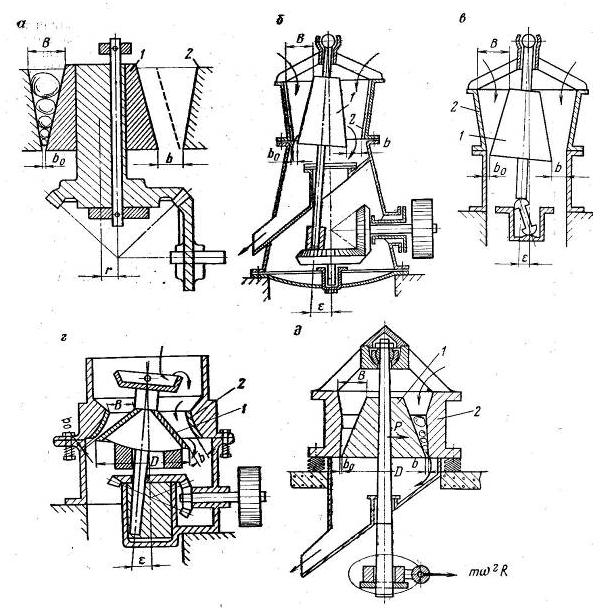
Рисунок 4 – Схема конусных дробилок.
а – с неподвижной осью, б – с подвесным валом (ККД гирационная), в – с валом, имеющим опору (ГРЩ), г – с консольным валом, опирающимся на шаровой подпятник (КСД и КМД), д – инерционная дробилка (вибрационная безэксцентриковая КИД).
Рабочие пространства конусных дробилок для крупного, среднего и мелкого дробления различается между собой конфигурацией. У дробилок для крупного дробления конус крутой (угол при вершине около 20о), а у дробилок для среднего и мелкого дробления – пологий (угол при вершине около 100о). Конусные дробилки для крупного дробления отличаются от дробилок для мелкого и среднего дробления величиной эксцентриситета стакана, определяющего амплитуду качания дробящего конуса. У дробилок для крупного дробления эксцентриситет стакана составляет не больше 25 мм, а у дробилок для среднего и мелкого дробления – больше 100 мм.[6]
3.3 Валковые дробилки.
Валковые дробилки с гладкими валками применяются для среднего и мелкого дробления твердых пород. Материал питателем подается в дробилку через загрузочную воронку, захватывается валками, вращающимися с одинаковой скоростью навстречу друг другу, дробятся и разгружаются вниз под дробилку.
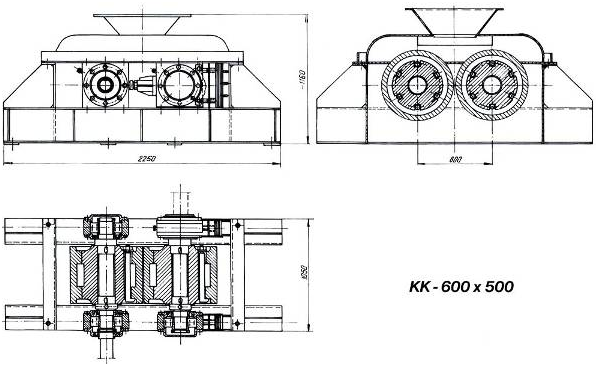
Рисунок 5 – Валковая дробилка КК 600 х 500.
Валки изготовляются из чугуна и футеруются по внешней поверхности бандажами из марганцовистой или углеродистой стали. Длина валков всегда в два-три раза меньше их диаметра. Валковые дробилки бывают одно- двух- и четырехвалковые с гладкими либо зубчатыми валками.
Расход стали при дроблении на валковых дробилках составляет от 0,016 до 0,06 кг на 1 т. дробленой руды и при бандажах из высокоуглеродистой стали.
На дробилках с гладкими валками, работающих в открытом цикле, достигается степень дробления от 3 до 4, а на дробилках с зубчатыми валками – от 4 до 6.
3.4 Молотковые дробилки и дизентиграторы.
Принято разделение ударных дробилок на две подгруппы: с ударным ротором и с безударным разгонным ротором (центробежным). К машинам с ударным ротором относятся:
- Молотковые, с шарнирно подвешенными молотками
- Роторные, с жестко закрепленными лопатками
- Стержневые дробилки (дезинтеграторы)
Дробилки ударного действия применяют для дробления мягких и средней крепости неабразивных материалов.
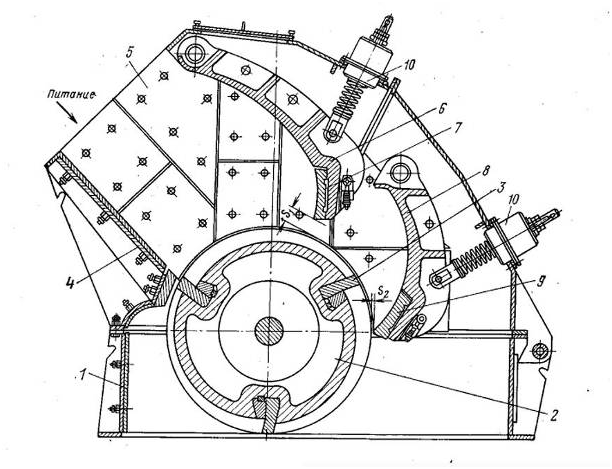
Рисунок 6 –Роторная дробилка ДРК (СМД)
1 – рама, 2 – ротор, 3 – била, 4 – верхняя часть корпуса для загрузки исходного материала, 5 – футеровка корпуса, 6 и 8 – соответственно верхняя и нижняя отражательные плиты, 7 и 9 – футеровка плит, 10 – механизм для регулирования зазора отражательных плит.[7]
4. Предложенное гидравлическое дробление угля.
В данной магистерской работе предлагается замена механического способа дробления угля на использование струи воды высокого давления, которое исключает в этом случае механическое воздействие на дробление горной массы и одновременно позволяет использование жидкой составляющей в технологическом процессе.
Выводы
В настоящее время на этапе дробления угля на обогатительных фабриках испульзуют дробилки механического типа, которые имеют ряд недостатков:
- Щековые дробилки: периодичность воздействия рабочего органа на материал, неполная уравновешенность движущихся масс. Для уменьшения шума и ударов, связанных с неуравновешенностью, дробилки устанавливают на тяжелых фундаментах и снабжают массивными маховиками.
- Конусные дробилки: большие габариты, повышенная энергоемкость.
- Основной недостаток валковых дробилок – возможность перекоса зубчатой передачи при неравномерной загрузке и пропуске недробимых тел.
- Недостаток молотковых дробилок: повышенная энергоемкость, быстрый износ пальцев, большое пылеобразование, отсутствие устройств, предотвращающих поломки при попадании недробимых тел.
- Научно-технический журнал «Обогащение руд»
- Строительный справочник [Электронный ресурс]. – Режим доступа: http://stroy-technics.ru/.
- . Свободная энциклопедия [Электронный ресурс]. – Режим доступа: http://ru.wikipedia.org/.
- Справочник по обогащению руд: Подготовительные процессы / Под ред. О.С. Богданова. - Изд. 2-е, перераб. И доп. - М.: Недра, 1982. - 366с.
- Зверевич В.В. Основы обогащения полезных ископаемых: Учеб. пособие для студентов вузов / В.В. Зверевич, В.А. Перов. - М.: Недра, 1971. - 216 с.
- Авдохин В.М. Основы обогащения полезных ископаемых. Том 2. Технология обогащения полезных ископаемыхУчебник для вузов: В 2 т. — М.: Издательство Московского государственного горного университета, 2006. — Т.2. — 417 с.
- Клушанцев Б.В., Косарев А.И., Муйземнек Ю.А. Дробилки. Конструкция, расчет, особенности эксплуатации. М.:Машиностроение, 1990. —320с
Разработанная гидравлическая дробилка будет иметь ряд преимуществ: высокую износостойкость и прозводительность, низкую энергоёмкость, компактность, возможность работы с углём высокой зольности и дробления его до различных размеров.
При написании данного реферата магистерская работа еще не завершена. Окончательное завершение: декабрь 2014 года. Полный текст работы и материалы по теме могут быть получены у автора или его руководителя после указанной даты.