Abstract
Content
- Introduction
- 1. Theme urgency
- 2.Purpose and tasks of the research results
- 3. Basic methods of crushing, classification machines.
- 3.1 Jaw Crushers .
- 3.2 Cone Crusher .
- 3.3 Roller crusher.
- 3.4 Hammer crushers and disintegrating.
- 4. Proposed hydraulic crushing coal.
- Conclusion
- References
Introduction
Mineral - a set of processes of primary processing of mineral raw materials, which is aimed at all separation of valuable minerals from waste rock, as well as the mutual separation of minerals.
When enrichment may receive as a finite commodity products (limestone, asbestos, graphite, etc.) and concentrate suitable for further chemical or metallurgical processing. Enrichment - an essential intermediate between mining and the use of recovered materials. The theory is beneficiation analysis of the properties of minerals and their interaction in the process of division - mineralurhiya.
Enrichment can significantly increase the concentration of the components. Summary of important non-ferrous metals - copper, lead, zinc - in the ores is 0,3-2% and concentrates - 20-70%. Molybdenum concentration increases from 0,1-0,05% to 47-50% tungsten - from 0.1-0.2% to 45-65%, ash content of coal is reduced from 25-35% to 2-15%. The purpose of enrichment is also removing mineral contaminants arsenic, sulfur, silicon, etc.). Extract of the components in the concentrate in the process of enrichment from 60 to 95%.
Processing operations, which are subjected to mining concentration plant mass, divided into: main (actually dressing);preparation and support.
All existing enrichment methods based on differences in physical or physico-chemical properties of the individual components of minerals. There is, for example, gravity, magnetic, electrical, flotatsyonnoe, bacterial and other methods of enrichment.
Processing of minerals enrichment plants involves a series of successive operations that result is achieved separation of valuable components from domishok.Za his appointment processes mineral processing is divided into preparatory, basic (enrichment) and secondary (final).
This paper will accentuate attention to the preparatory phase enrichment of coal, namely the fragmentation process.
Splitting is performed on special crushing plant. Crushing is the process of fracture of solids with decreasing size of the pieces to the desired size by the action of external forces that overcome the internal strength of coupling, which connects particles of solid matter. [ 1 ]
1. Theme urgency
Developed at the present time coal seams are very ash content of 35 percent or more. The use of such coal industry and energy is costly.
Chipping in most cases - is the main and often the most energy-intensive operation, designed for destruction of raw materials to the required size, as well as the disclosure of mutually interlocking units and the formation of particles of some materials.
Currently, the enrichment is carried out on the concentration plants that employ technically possible equipment. Development of more efficient and productive ways enrichment at different stages is very important.
2. Purpose and tasks of the research results
The aim of this work is to develop a hydraulic crusher for crushing coal enrichment plants, determination of technical parameters and basic structural dimensions.
To achieve this goal it is necessary to do the job:
- To consider and analyze the effectiveness of currently available crushers enrichment plants;
- Identify the features of the technology using Hydro-crushing plant;
- Perform analytical calculation and design work on the creation of Hydro-crusher.
It is planned to develop a hydraulic crusher for crushing sound of coal enrichment plants.
3.Crushing main ways. Classification of equipment.
The main methods of crushing, crushing carried out by the working machine is crushing (compression) stroke, abrasion and cracking.
Often these methods combine with one another, such as from crushing blow, blow from abrasion, etc., with the combined effect of bending forces that cut and tear.
The methods of fragmentation depends on the physical and mechanical properties of materials (hardness, brittleness, viscosity, contamination of the clay, inclination to zamazuvannya crushing chamber), the initial value of the pieces and the required degree of grinding.
Solid materials are crushed most effective blow or crushing, plastic (clay) - crushing in combination with abrasion, brittle materials (coal) - splitting.
The correct choice of the type of crushing machine, and hence splitting method is largely dependent on the quality of the finished product and the performance of the unit. Never should strive for full grinding in one machine is always cheaper and more effective stadyynoe crushing consistently across multiple corresponding in size and design of crushing machines.
Currently established and successfully operated crushers different designs. The basic requirements that must satisfy any crusher, are as follows.
1.Konstruktsiya sizes and boot openings shall comply with the strength of crushed material and the size of the individual pieces: for example, crusher, crushing solid material should have a large enough margin structure and the loading slot width must be larger than the largest pieces across 30 - 40%. This prevents the phenomenon of "hang" pieces in the receiving aperture reduces downtime associated with removing the "bulky", and creates favorable conditions for process automation.
2.For technological linkage consistently working crushers and reliable automation systems necessary to receiving hole crushers next stage was 60-80% higher discharge gap crushers previous stage.
3.Drobilka must have a certain margin (15-20%) performance to increase when the number of incoming material was not an overload.
4.Droblenie - very energy-intensive process, so specific energy consumption should be small. It should be remembered common feature of all mills with increasing degree of grinding machines reduces productivity and increases energy expenditure.
5.Neobhodimo to minimize the amount of dust generated during crushing. Dust and rock fines act as a shock absorber (cushion).Filling the space between the large pieces, they soften the blow and thus reduce the efficiency of fragmentation: reduced productivity, increased energy consumption and wear expensive parts of crushers. The dust is harmful to health service staff.
6.Razdroblennyy material from the crusher should unload quickly and continuously to prevent it pereizmelcheniya, excessive dust formation and strengthening of wear parts.
7.Konstruktsiya crusher should allow to quickly and easily replace worn or broken parts.
8.Razdroblennyy material shall consist of pieces as possible the same size and shape kuboobraznoy, especially for crushing gravel for concrete work.
9.Drobilka should be easy and inexpensive safety details. If a nedrobimyh items (pieces of rails, excavator bucket teeth, etc.) are deformed or broken parts, thus protecting the main road crusher parts from damage.
Like any machine, the crusher must be strong, cheap, easy to manufacture and use, do not require highly skilled service and consume minimal energy. [ 2 ]
3.1 Jaw Crusher
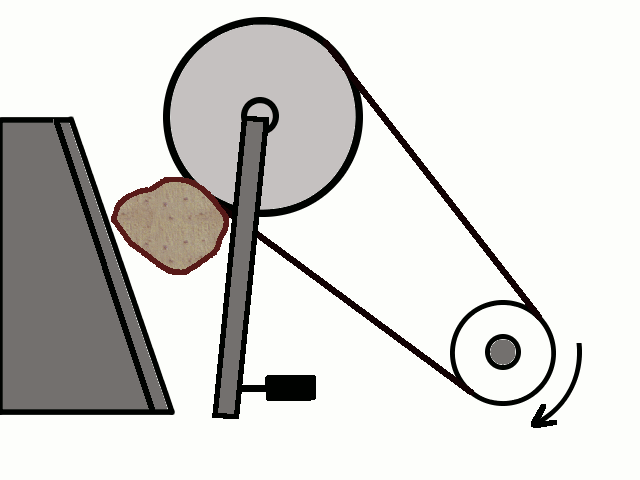
Figure 1 - Schematic diagram of jaw crusher (293 kB, 9 frames)[ 3 ]
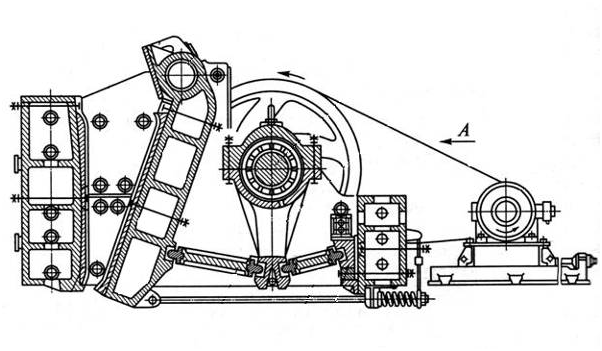
Figure 2 - Jaw crusher with a simple movement of the movable cheek
Jaw crusher is divided into two main classes: with simple and complex motion of the movable cheek. Crushers with a simple movement of the movable cheeks are different way of mounting and drive mechanism. There crusher suspension with upper cheeks, the bottom of the rocker bearing from the drive cam mechanism with crank-articulated drive mechanism. In the crusher with complex traffic moving cheeks, the latter is pivotally suspended on eccentric drive shaft. Significant vertical movement of the cheeks, which makes them ystyrayuschym effect on pieces of material, leading to increased wear crushing plates. Because of the complicated motion of the crusher are mainly used for maloabrazyvnyh materials. Benefits of design simplicity, compact and light weight. [ 4 ]
Figure 3 shows a diagram of jaw crushers with complex motion SCHDS cheeks. Crusher frame welded. Its side walls are made of sheet steel and connected by a front wall 1 box section and rear beam 2, which is also housing the control unit 7. Adopted over the hole fortified guard 3. Movable jaw 4 is fixed to the drive shaft of the orbit 5 the bottom of the cheek is a groove where liner is inserted to stop raspornoy plate 6. raspornaya other end rests on the liner plate control unit, consisting of the slider 13 and two screws 14. locking device consists of thrust cylindrical springs 8 and 9. movable jaw has the bottom of the oblique projection, which set drobyaschyhsya lining plate 10. Fixed crushing plate 11 rests on a ledge at the bottom of the front wall of the frame 1, and the sides sandwiched lining plates 12.
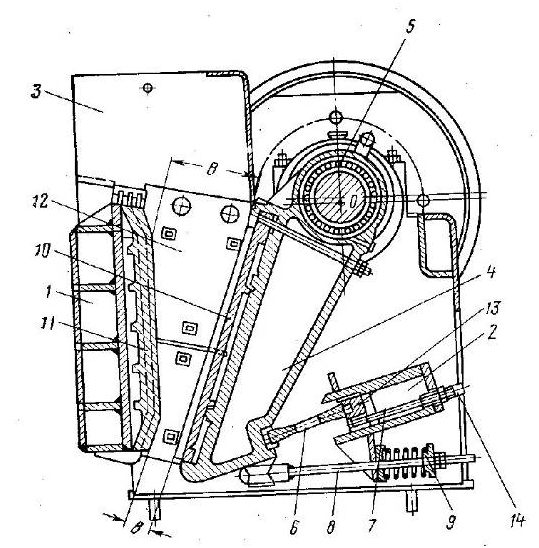
Figure 3 - Jaw crusher with complex motion cheeks
3.2 Cone Crusher
Cone crusher is divided into the crusher for coarse, medium and fine crushing. The principle of operation of all cone crushers same. Fractions cone rigidly attached to the shaft is suspended from point O, and the lower end is inserted into the eccentric free glass. Glass set of concentric Bed Type crusher. The axis of the shaft slightly inclined to the vertical axis of the shell crusher.Eccentric glass gets rotated by the motor. Rigidly mounted on the shaft of crushing cone has a circular swing consistently closer to the walls and conical bowl away. Approaching drobyascheho cone to bowl accompanied by crushing pieces of material entering the space between them, and removal - discharge of crushed product. Crushing the material in the cone crusher is continuous. In the absence of idling time of fragmentation and, consequently, performance cone crushers higher than the jaw. [ 5 ]
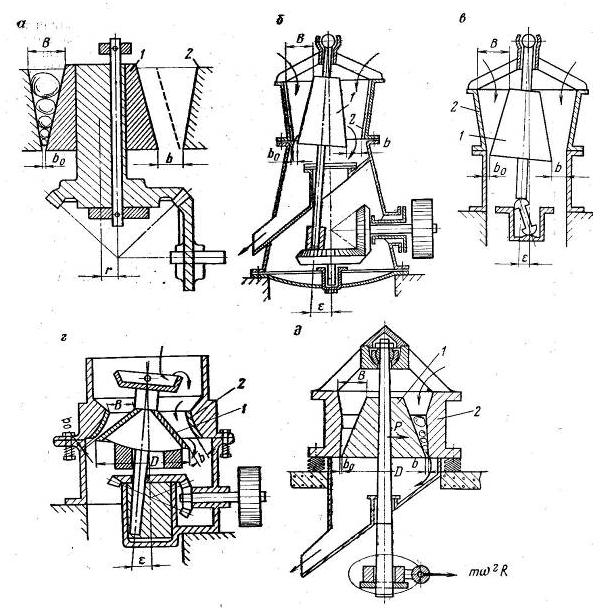
Figure 4 - Diagram of cone crushers.
Workspace cone crushers for large, medium and fine crushing varies between a configuration. In large crushers for crushing cone cool (the apex angle of about 20o), and crushers for secondary and fine crushing - flat (the apex angle of about 100o). Cone crusher for crushing big different from crushers for crushing small and medium size glass of eccentricity, determining the amplitude of swing drobyascheho cone. In crushers for crushing large eccentricity cup is not more than 25 mm, while the crushers for secondary and fine crushing - more than 100 mm. [ 6 ]
3.3 Roller Crusher
Roller crusher with smooth rollers are used for secondary and fine crushing of hard rocks. The material is fed into the crusher feeder through hopper, enjoys rolls rotating at the same speed in opposite directions, are broken down and unloaded under the crusher.
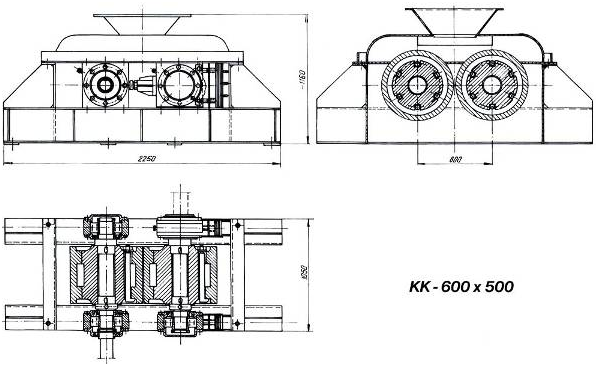
Figure 5 - roller crusher CC 600 x 500
Rolls are made of cast iron and futeruyutsya on the outer surface of the tires of marhantsovystoy or carbon stali.Dovzhyna rolls are always two to three times smaller than their diameter. Roller crushers are one-and two-chotyryvalkovi with smooth or toothed rollers.
Fuel began crushing on roller crusher is from 0.016 to 0.06 kg per 1 ton of crushed ore with bandages of high carbon steel.
On crusher with smooth rollers operating in open loop, achieved the degree of fragmentation of 3 to 4, and the crusher with serrated rollers - 4 to 6.
3.4 Hammer crushers and dizentihratory.
Accepted drum crushers division into two subgroups: with the hammer rotor and unstressed upper stage rotor (centrifugal). To the machine with the hammer rotor are:
- Hammer with hammers pivotally suspended
- Rotor with rigidly fixed blades
- Core cutters (disintegrants)
Impact Crushers are used for crushing of soft and medium bodied neabrazivnyh materials.
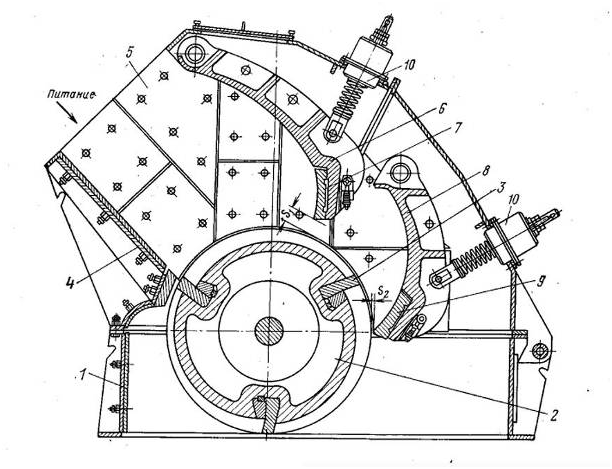
Figure 6 - Rotary Crusher DRC (SMD)
1 - Frame 2 - rotor, 3 - beat 4 - the upper part of the body to load the starting material, 5 - the shell lining, 6 and 8 - respectively the upper and lower plates of chops, 7 and 9 - lining plates, 10 - a mechanism for regulating gap reflective plates. [ 7 ]
4. Proposed hydraulic crushing coal.
This paper proposes a replacement master mechanically crushing coal for the use of high pressure water jet, which excludes this case, the mechanical effect on the fragmentation of the rock mass, while allowing the use of the liquid component in the process.
Conclusions
Now on stage crushing coal enrichment plants yspulzuyut mechanical crusher, which have several disadvantages:
- Jaw crusher: the frequency of the action of the working body of the material, incomplete mass balance moving. To reduce noise and shock associated with neurivnovazhenistyu cutters set on heavy foundation and provide massive torque.
- Cone crusher: large size, high power consumption.
- The main disadvantage of roll crushers - the possibility of a distortion of the gear in uneven loading and crossing nedroblenyh phone.
- Lack of hammer mills increased energy, rapid wear fingers, large pыleobrazovanye, no devices to prevent breakage when hit nedroblenyh phone.
Developed hydraulic crusher have several advantages: high durability and performance, low power consumption, compact size, ability to work with high-ash coals and splitting it into different sizes.
In writing this master's work is not yet complete. Final completion: December 2014. Full text of the work and materials can be obtained from the author or his manager after that date.
References
- Научно-технический журнал «Обогащение руд»
- Строительный справочник [Электронный ресурс]. – Режим доступа: http://stroy-technics.ru/.
- Свободная энциклопедия [Электронный ресурс]. – Режим доступа: http://ru.wikipedia.org/.
- Справочник по обогащению руд: Подготовительные процессы / Под ред. О.С. Богданова. - Изд. 2-е, перераб. И доп. - М.: Недра, 1982. - 366с.
- Зверевич В.В. Основы обогащения полезных ископаемых: Учеб. пособие для студентов вузов / В.В. Зверевич, В.А. Перов. - М.: Недра, 1971. - 216 с.
- Авдохин В.М. Основы обогащения полезных ископаемых. Том 2. Технология обогащения полезных ископаемыхУчебник для вузов: В 2 т. — М.: Издательство Московского государственного горного университета, 2006. — Т.2. — 417 с.
- Клушанцев Б.В., Косарев А.И., Муйземнек Ю.А. Дробилки. Конструкция, расчет, особенности эксплуатации. М.:Машиностроение, 1990. —320с