Abstract
Содержание
- Introduction
- 1. Relevance compaction process
- 2. Negative influence particulate waste on human health and the environment
- 3. Equipment for compacting waste dispersed
- Conclusion
- References
Introduction
General principles of modern waste production include engineering, environmental criteria, which is an important area of waste management. Effective use of process waste. However, more than 70% of all man-made waste can not be recycled in the same undertakings in which they are formed. Recycle such materials will not businesses producing these wastes.
In Ukraine, the problem of waste is more acute than in other developed countries. Every year in our country produces about 7 billion tons of waste processed at the same time only 2 billion tons (about 28%) and these issues have been neglected.
Existing methods for processing of industrial and household waste (incineration, gasification, biochemical purification etc.) requires significant capital expenditures for the construction of recycling plants and thus generate secondary waste – gas, dust, sulfur and nitrogen oxides, which are also in need of disposal. However, processing of these mostly digital products requires additional preconditioning, one of the stages of preparation for which is compacting.
1. Relevance compaction process
Recycling waste dispersed, especially the fine fraction component of MSW is relevant and technically challenging due to significant uncertainty and instability of composition and properties of the waste, as well as the difficulty of handling the fine fraction because of its poor flowability, meterability and adhesive properties. Stabilizing composition and properties of the particulate waste can be ensured pre-treatment and processing, by averaging, followed by compaction or briquetting of the granulation methods [3].
Despite the many existing technologies and pelletizing, briquetting and a wide variety of designs of machines and apparatus for implementing these processes, there is a need to optimize them. This is due to the fact that the resource base is constantly changing and growing share in the feed raw materials occupy reuse – recycle, various industrial wastes.
Are the most common methods of granulation (briquetting) presses, rotating surfaces (sloshing) and in devices with boiling (fluidized) bed. Despite the difference in principle, they may be useful for the same materials.
2. Negative influence particulate waste on human health and the environment
Disperse waste called shredded or otherwise obtained by fine particles of solids, Vita (are in motion) sometime in the air. Such wool-occurs due to small size of the particles (dust particles) under the action of the movement of air.
Air in varying degrees soiled; even in those areas that are usually considered to be clean, not dusty, small amounts of dust is still there (sometimes it is even visible to the naked eye in passing sunbeam). However, in many industries because of the nature of the process, the applied methods of production, the nature of raw materials, intermediate and finished products, and many other reasons, there is an intense dust that pollutes the air of these rooms to a large extent. This may represent a risk to human [7].
Dust generated due crushing or attrition, evaporation followed by condensation into solid particles in the combustion air to form solid particles – products of combustion (smoke), a series of chemical reactions, etc.
In a production environment with the formation of dust is most commonly associated processes of crushing, grinding, sifting, turning, sawing, suction and other movements of bulk materials, combustion, fusion, etc.
Effect of the dust on the skin is reduced mainly to mechanical irritation. Due to this there is a little itchy irritation, discomfort, and when scratching, redness and some swelling of the skin, indicating that the inflammatory process.
Some toxic dust in contact with the skin it causes chemical irritation, manifested in the appearance of itching, redness, swelling, and sometimes ulcers. In most cases these properties have dust chemicals (chrome salts, lime, soda, arsenic, calcium carbide, etc.).
To avoid adverse effects on the environment, the human body and not waste valuable raw materials, it is proposed to use the method of compacting particulate waste and subsequent disposal.
3. Equipment for compacting waste dispersed
Compacting – receiving in the form of granules briquettes rings, tablets by compaction of waste particulate, sometimes followed by crushing the compacted material. Waste used to disperse and Roller roller press (Figure 3.1), tablet machine serrated rotary granulators, drums. For a continuous supply of material and its pre-compaction is often used helical screw [5].
УRoller presses the seal on a continuous process. Roller presses feature work is need for coherence between supply compressible material nip press with productivity. When reducing the supply of material to leave enough dense briquettes, while increasing the supply can come hang the charge to form the arch. Therefore, in all designs Roller presses use special devices different designs to ensure proper filing of the charge.
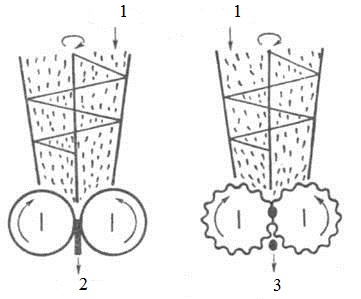
Figure 3.1 – swath (left) and roller (right) presses for consolidating powders
1 - powder 2 - tile; 3 - briquettes
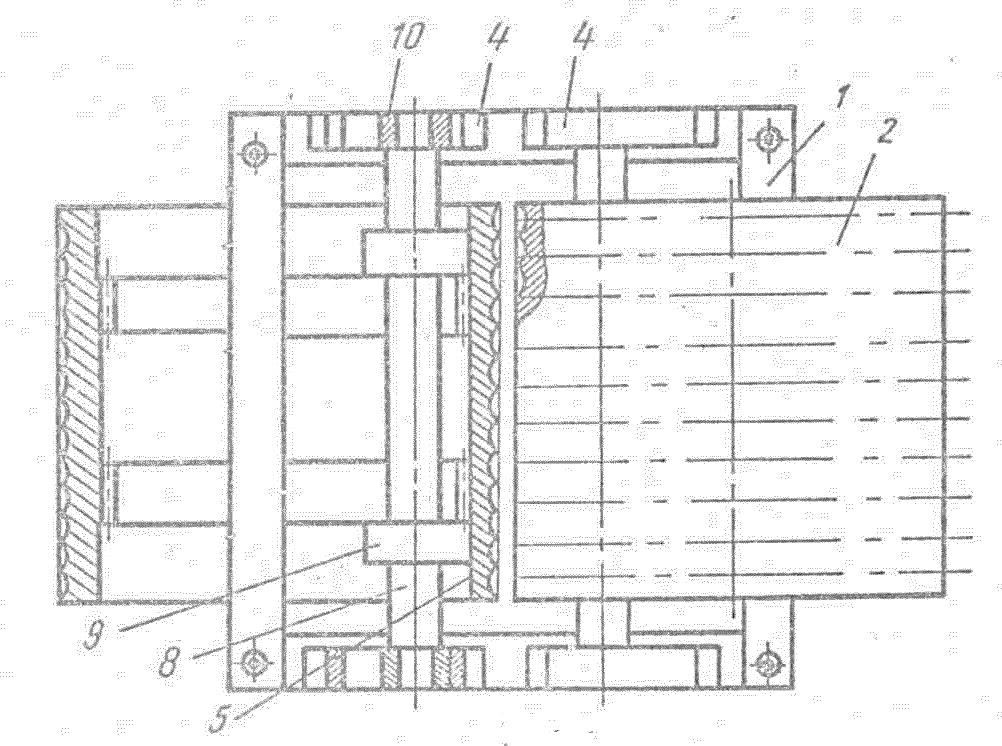
Figure 3.2a – Roller press for briquetting bulk materials
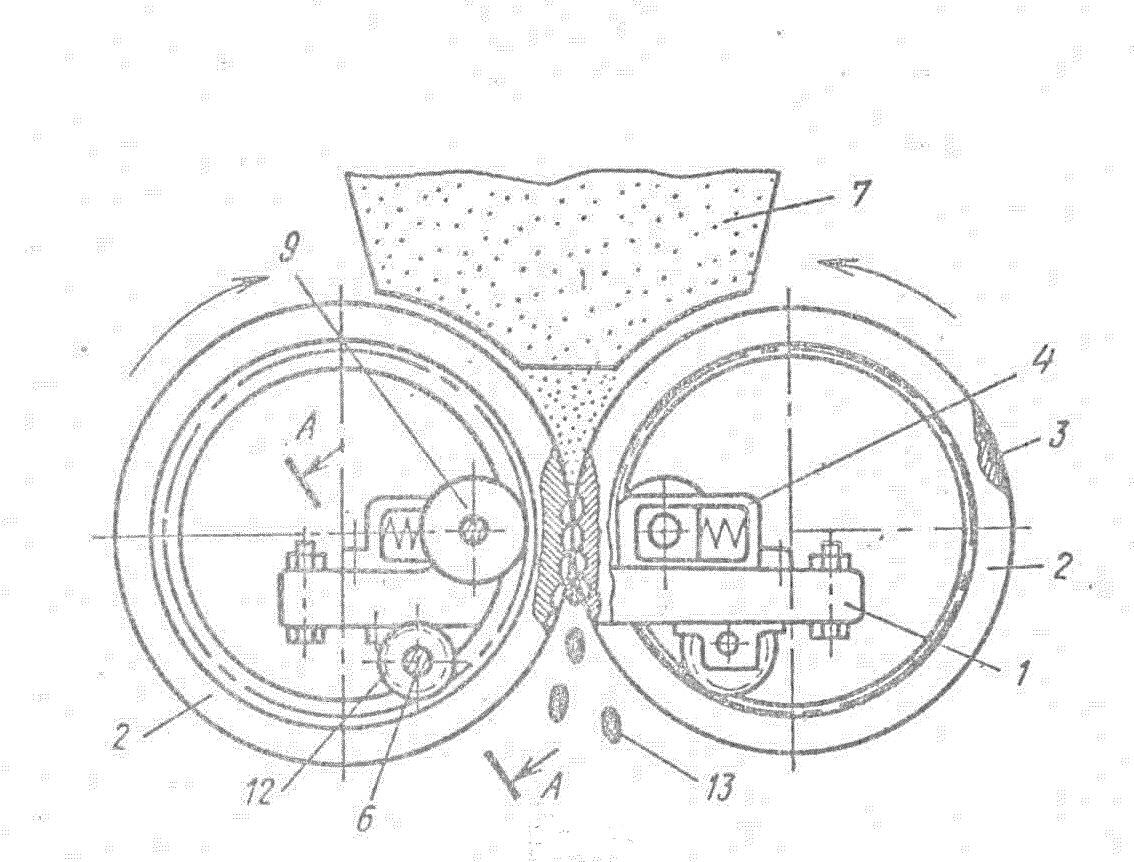
Figure 3.2b – Roller press. Side view
1 - frame, 2 - roller presses, 3 - cell 4 - elastic knots, 5 - inner surface, 6 - drive shafts, 7 - boot device (bunker), 8 - axis 9 - support rollers, 10 - support, 11 - ring gears, 12 - gears, 13 - briquettes.
The press comprises a frame 1 mounted on the driving roller presses 2. Rolls made in the form of hollow cylinders with the toothings on the inner surface. Inside the elastic roller assemblies 4 are installed. They are made in the form of axles with supporting rollers 9 and the spring-loaded supports. Supports mounted on the frame to move. Drive shafts have 6 gears 12. These gears are placed in windrows and 2 interact with the ring gear. With increasing compaction pressure bearing rollers 9 are displaced, the distance between the rollers increases, compressible material passes between the rollers without a sharp increase in load [2].
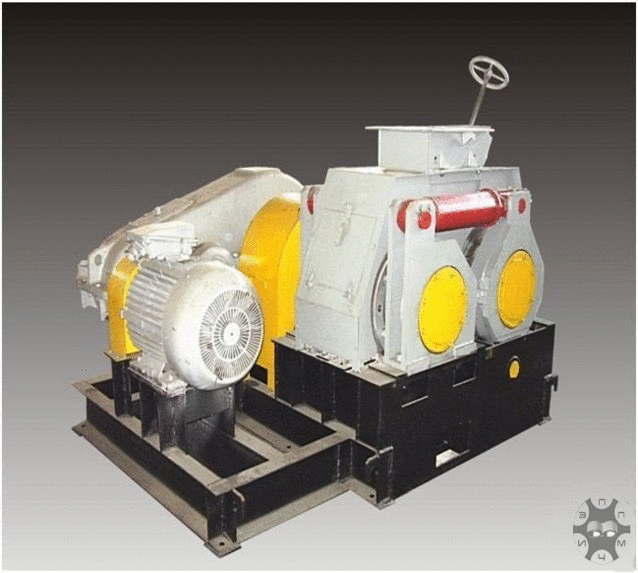
Figure 3.3 – Roller press type briquetting Housingless small fraction of raw materials and industrial waste
Tableting – forming particulate materials in the blanks of regular geometric shape, uniform in size and weight. Apply in cases where melting impossible or inappropriate material. The resulting tablets are generally cylindrical or rectangular in shape.
Sealing material occurs under the compressive forces, wherein the pressure depends on the nature of the material and up to 30 MPa. Pressure can be reduced by preheating the material, its hydrate, use of lubrication additives and binders [6].
Exercise automatic tableting in a tableting machine in which the process comprises the steps of dosing, compaction and ejection of tablets. By type of drive tablet machines are divided into mechanical (crank and rotor) and hydraulic [1].
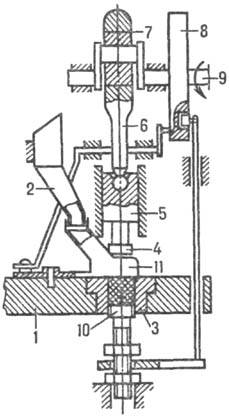
Figure 3.4 – Scheme crank tableting machine
1 - table; 2 - hopper; 3 - matrix; 4 - punch; 5 - slider; 6 - rod; 7, 8 - eccentrics; 9 - crankshaft; 10 - ejector; 11 - a boot device
Hydraulic machine is a horizontal press machine (Figure 3.5), consisting of two fixed plates. Pressing the feed hopper of the material to be processed is done by rolling on a stationary punch. In this tableting material dispensed by volume, which is controlled by the distance between the movable and stationary dies. The machine design allows for two-way pressing, change weight tablets, the dosing time, pressure and pressing time, ejection speed pills. Used for the manufacture of large (heavy) tablets with a minimum spread by weight [4].
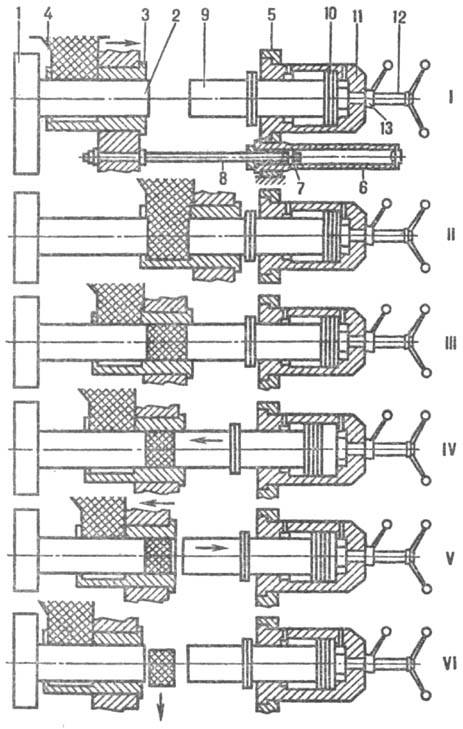
Figure 3.5 – Diagram of hydraulic tableting machine
I - start cycle; II - loading material to be processed; III - moving material in the matrix; IV - pressing; V - start pushing pills; VI - relief tablets in containers; 1,5 - fixed plate; 2 - fixed-punch; 3 - matrix; 4 - bin; 6 - cylinder auxiliary; 7,10 - pistons; 8 - Rod; 9 - movable punch; 11 - slave cylinder; 12 - screw; 13 - locknut.
Conclusion
It is shown that the compaction is thus a process that will allow us to most effectively prepare raw material for further processing. Thus, in addition to involvement in the further production of waste can be resolved issues related to improving the environmental situation in the workplace. Using such devices allows you to prepare for further processing even fine dust-like material. Waste thus prepared can be used for energy production.
In writing this essay master's work is not yet complete. The final results will be available after the completion of the work. Full text of the work and materials on the topic can be obtained from the author or his supervisor.
References
- Антонюк С. И. Оборудование технологии компаундирования твердых углеродистых отходов для экологически чистой термолизной переработки в камерных печах. Автореф. дисс. работы. – К., 2004
- АС 361899 СССР, кл. В 30 В 11/18 Пресс для брикетирования сыпучих материалов/С.П. Веретельник, А.С. Парфенюк, 1971.
- Классен П.В., Гришаев И.Г. «Основы техники гранулирования», М. 1982г.;
- Крохин В.Н. Брикетирование углей. Учебник для техникумов. – М.: Недра, 1984. С.224.
- Брагинский В.А. Прессование. – Л.: Химия, 1979. – 176 с
- Генералов М.Б. и др. Расчет оборудования для гранулирования минеральных удобрений [Электронный ресурс]. – Режим доступа: http://bookre.org/reader?file=475984
- Н.И., Николайкина Н.Е., Мелехова О.П. Экология. Учебник для вузов [Электронный ресурс]. – Режим доступа: Книги и журналы