Реферат по теме выпускной работы
Содержание
- Введение
- 1. Актуальность темы
- 2. Цель и задачи исследования
- 3. Автоматическая газовая защита в структуре АСУ ТП горного предприятия
- 4. Моделирование события
Взрыв метановоздушной смеси
- 5. Оптимизация систем автоматической газовой защиты
- 6. Работа АГЗ при нестационарных процессах метанообразования
- 7. Борьба со слоевыми скопления метана
- Выводы
- Перечень ссылок
Введение
Взрывы газа и угольной пыли относятся к авариям с наиболее тяжкими последствиями в социальном и экономическом плане. Взрыв метановоздушной смеси и угольной пыли в шахте, сопровождающийся формированием и распространением по сети горных выработок ударных волн – очень опасный вид подземной аварии. Угрожая жизни и здоровью горнорабочих, взрыв всегда приводит к разрушению выработок и повреждению расположенного в них горного оборудования. При этом социальные, материальные и финансовые потери могут достигать катастрофических размеров.
Несмотря на то, что автоматические системы газовой защиты не один десяток лет эксплуатируются в условиях шахт, они не могут обеспечить гарантированной безопасности, а потому вопросы их совершенствования по‑прежнему остаются актуальными. Современные тенденция развития систем автоматической газовой защиты состоят в преобразовании данных систем в системы мониторинга, прогнозирования состава и защиты рудничной атмосферы, для чего необходим комплексный контроль ряда параметров. Также важным направлением развития данных систем является повышение их надежности, зарубежные производители предлагают полностью дублированные системы автоматической газовой защиты добычных участков.
Очевидно, что требуется применение на горных предприятиях Украины систем нового поколения, со схемотехническими решениями повышенной надежности, возможностью сбора и обработки большего количества параметров рудничной атмосферы, возможностью защиты от опасных ситуаций, возникающих при нестационарных процессах метанообразования.
1. Актуальность темы
В ходе расследования причин возникновения крупных аварий на угольных шахтах Украины [1], было установлено, что в подавляющем большинстве случаев контроль содержания метана в атмосфере горных выработок осуществлялся неудовлетворительно. Причинами взрывов на шахтах оборудованных системами АГЗ являются газодинамические явления или возникновение слоевых скоплений метана в неконтролируемых пространствах. Данные факты указывают на необходимость дальнейшего совершенствования систем автоматической газовой защиты.
2. Цель и задачи исследования
Целью научной работы является повышение надежности функционирования и выполнения защитных функций системой автоматической газовой защиты при стационарных и нестационарных процессах метанообразования, за счет изменения структуры и архитектуры системы автоматической газовой защиты. Для достижения поставленной цели необходимо выполнить следующие задачи:
- произвести анализ современных систем АГЗ;
- разработать математическую модель, связывающие структуру и архитектуру системы АГЗ с вероятностью возникновения события
взрыв метановоздушной смеси
; - на основании результатов моделирования разработать оптимальную архитектуру системы автоматической газовой защиты;
- исследовать работу системы автоматической газовой защиты при нестационарных процессах метановыделения;
- на основании исследования разработать усовершенствованную структуру системы АГЗ.
3. Автоматическая газовая защита в структуре АСУ ТП горного предприятия
Автоматическая газовая защита – обеспечение защитных мер, исключающих возможность загазирования горных выработок свыше допустимой
концентрации метана и взрыва метановоздушной смеси на шахтах [2]. Газовая защита основана на непрерывном контроле содержания метана
в горных выработках шахт, фиксировании момента достижения предельно допустимой концентрации газа и автоматической выдаче защитных команд на обесточивание
всего электрооборудования, попавшего в опасную зону, включении аварийной сигнализации, введении в действие дополнительных средств для интенсивного проветривания
и разгазирования аварийного участка. Газовая защита распространяется на отдельные технологические участки, часть его, камеру или ограничивается районом действия
горной машины. Газовая защита реализуется на шахтах с помощью отдельных средств и систем. Данные системы могут быть независимыми, либо входить в качестве подсистем
в АСУ ТП Проветривание
или Добыча угля
(см. рис. 1), либо как составная составной частью унифицированных телекоммуникационных автоматизированных систем
диспетчерского контроля и управления.
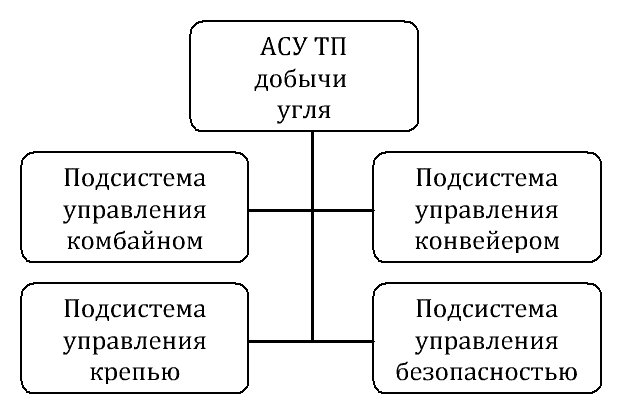
Рисунок 1 – Структура АСУ ТП добычи угля
Структурно АГЗ представляет собой распределенную в пространстве систему, состоящую из первичных преобразователей (датчиков), линий связи и телемеханики, устройств обработки измерительной информации (анализаторов и регистраторов, сигнализаторов, устройств защитного отключения). К конструктивным особенностям АГЗ следует отнести значительную удалённость элементов системы, искробезопасное исполнение цепей питания, сигнальных и измерительных цепей. Режим работы АГЗ непрерывный. Условия эксплуатации характеризуются потенциальной взрывоопасностью окружающей среды, ее повышенной влажностью, температурой, атмосферным давлением; наличием в атмосфере токопроводящей пыли, механическими вибрациями, низкой квалификацией обслуживающего персонала [3].
У большинства существующих систем АГЗ можно выделить следующие недостатки:
- релейный принцип действия, не учитывающий динамики процесса метанообразования;
- контроль недостаточного количества параметров рудничной атмосферы;
- недостаточно высокая надежность;
- невозможность идентификации слоевых скоплений метана;
- неэффективная работа при возникновении ГДЯ.
4. Моделирование события Взрыв метановоздушной смеси
Для того чтобы произошло событие взрыв метановоздушной смеси
необходимо выполнение ряда условий, каждое из которых является необходимым, но не достаточным.
Используя элементы теории графов и алгебры логики, приведем упрощенную структуру события взрыв
(рис. 2).
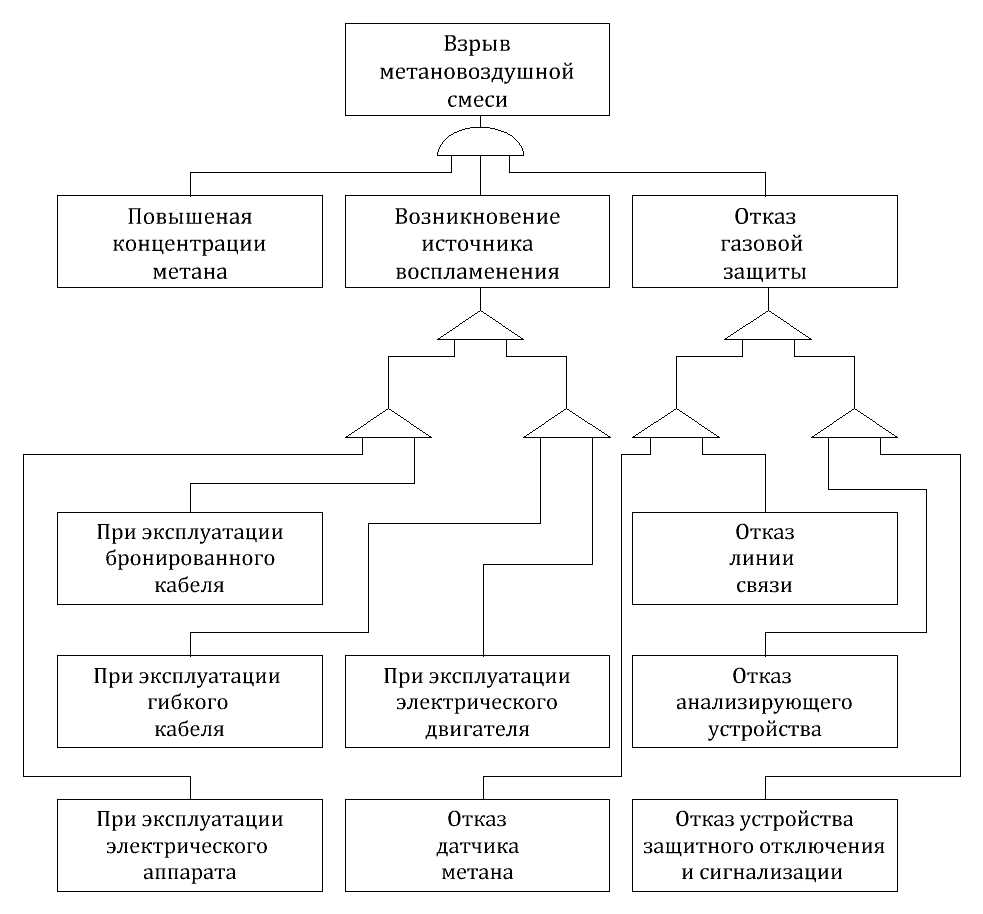
Рисунок 2 – Дерево события Взрыв метановоздушной смеси
Событие взрыв является конъюнкцией следующих состояний: повышенная концентрация метана
, наличие источника воспламенения
, отказ АГЗ
[4]. Все
данные условия являются необходимыми, но ни одно из них не является достаточным. Так для взрыва необходима строго определённая концентрация метана.
При концентрации метана менее 5 % (по объему) метан не взрывается, а горит, сгорая полностью с образованием СО2 и Н2О; при концентрации выше 16 % он также
горит, но при этом возможно неполное сгорание с образованием Н2О и ядовитого СО. Таким образом взрывоопасная концентрация метана С[СН4] ∈ (5,15) %. Однако
наличие взрывоопасной концентрации не является достаточным для возникновения события взрыв. Необходим инициирующий фактор, которым является источник воспламенения
электрического, механического или химического характера. При этом источник воспламенения должен иметь достаточную для детонации метановоздушной смеси мощность.
Так как возникновение источника воспламенения механического или химического характера в шахтах опасных по газу и пыли организационными мероприятиями сводится
на нет, то основным инициирующим фактором является электрическая дуга или искра критической (достаточной) мощности. Источником разряда необходимой мощности в
подземной выработке может служить повреждение бронированного или гибкого кабеля, электрического двигателя, электрического аппарата. Сигнальные цепи и цепи
управления при условии их искробезопасного исполнения не могут служить источником искры достаточной мощности. Третьим необходимым фактором является отказ
системы АГЗ. Это объясняется тем, что по своему функциональному назначению АГЗ должна нейтрализовать возможность взрыва. Все многообразие отказов можно
разделить их по пространственному признаку: отказ датчика, отказ в линии связи, отказ анализирующего устройства, отказ схемы (устройства) защитного отключения.
Обозначим событие взрыв
– В, событие опасная концентрация метана
– С, событие источник воспламенения – I,
событие отказ АГЗ – Ā,
тогда формализуем событие взрыв:
![]() | (1) |
Концентрация метановоздушной смеси является случайной величиной, зависит от газоносности пласта, горного давления, скорости воздуха в выработке
(а, следовательно, и от общешахтной депрессии), конфигурации выработки, наличия мероприятий по дегазации и пр. При этом процесс метановыделения
не стационарный а, следовательно, и не эргодичный. Событие источник воспламенения
также является не детерминированным. При этом данное событие
исследовано, и существуют формулы для расчета вероятности возникновения данного события [5].
Система АГЗ является восстанавливаемой системой без резервирования при последовательном соединении устройств и при наличии их профилактики [6]. Элементы устройства приняты последовательно соединенными, т. к. при выходе из строя любого из них вся система выходит из строя. Составим граф состояний системы (рис. 3).
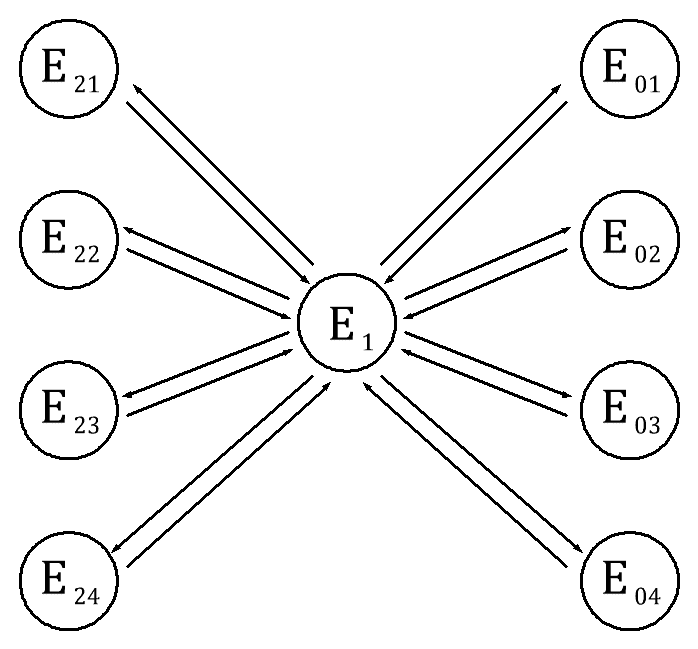
Рисунок 3 – Граф состояния АГЗ
На данной схеме состояние Е1 соответствует работоспособному состоянию системы АГЗ, состояние Е0i – аварийный простой по причине отказа i‑го элемента (i=1..n) и его восстановление, Е2j – профилактическое обслуживание и плановый простой j‑го элемента системы (j=1..k). λ – интенсивность отказа, μ – интенсивность восстановления. Индексу 1 соответствует датчик метана, 2 – линия связи, 3 – анализатор, 4 – устройство защитного отключения. Интенсивность отказа λ – условная плотность вероятности возникновения отказа объекта, определяемая при условии, что до рассматриваемого момента отказ объекта не возникает. Интенсивность восстановления μ имеет тот же математический смысл.
При моделировании вероятности отказа АГЗ используем правило Колмогорова, для составления аналитической модели,
описывающей граф состояния некой системы.
Согласно данному правилу: система содержит столько дифференциальных уравнений, сколько состояний содержит граф; левая часть всех уравнений содержит
производную от вероятности i‑го состояния; правая часть уравнений содержит столько слагаемых, сколько ветвей графа связано с данным состоянием,
если ветвь направлена в данное состояние, то перед слагаемым ставиться +
, если из данного состояния, то −
, каждое слагаемое правой
части представляет собой произведение
интенсивности перехода из одного состояния в другое и вероятности того состояния, из которого исходит стрелка.
В соответствии с формулой (1) для наступления события B (взрыв), необходимо одновременное наступление событий С, I, А̄. Поскольку данные события независимые, т. е. наступление одного из них не изменяет вероятность наступления другого, то вероятность возникновения события В равна произведению вероятностей возникновения событий С, I, А̄: PB = PC ⋅ PI ⋅ PĀ
Примем допущение о том, что в рассматриваемой нами выработке всегда взрывоопасная концентрация метана, т. е. PC = 1, для того чтобы смоделировать наихудшее развитие событий, тогда: PB = PI ⋅ PĀ
Известно [6], что даже при полной безотказности защитное оборудование (защита от утечек), не может предотвратить появление взрывоопасного источника от электрооборудования участка, таким образом PI ≥ 0,036.
Под состоянием А̄ подразумевается неработоспособное состояние АГЗ, что может быть связано не только с отказом системы, но и с выполнением профилактических работ. В соответствии с графом состояния АГЗ (рис. 3) состояние А̄ соответствует любому состоянию за исключением состояния E1. Так как все состояния, приведенные на рис. 3 образуют полную группу событий, то: PĀ = 1 − P1. Где P1 – вероятность того, что система находится в состоянии Е1.
Для выражения P1 составим уравнения относительных вероятностей перехода системы из одного устойчивого состояния в другое, используя правило Колмогорова:
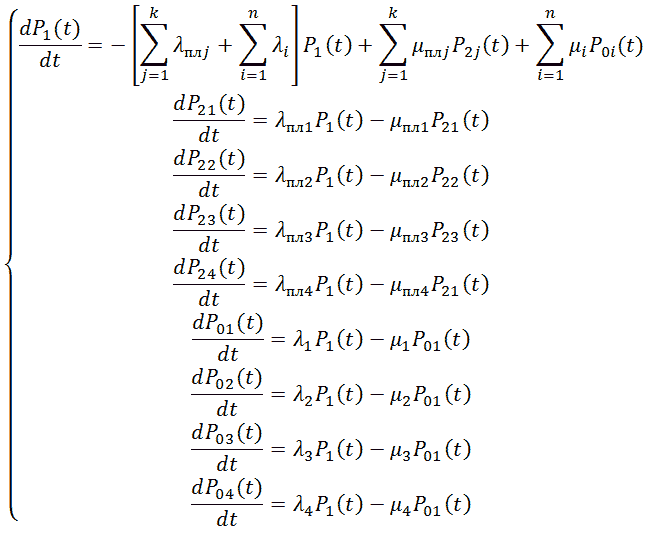
Интенсивность отказа λ в общем случае является функцией от времени, т. е. λ = f(t), по определению – условная плотность вероятности возникновения отказа объекта, определяемая при условии, что до рассматриваемого момента отказ объекта не возникнет. При практических расчетах принимается расчетное значение, полученное на основании испытаний и эксплуатации оборудования, являющиеся константой. При этом введением поправочных коэффициентов учитываются условия эксплуатации. Интенсивность отказов зависит от применяемого оборудования, его элементной базы, способы соединения элементов и т. д. и является уникальным для каждой конфигурации системы.
После параметрической идентификации разработанной, и решения уравнений модели численными методами для интервала времени в 1 год, были получены следующие
результаты: вероятность появления события взрыв
как функция времени быстро достигает установившегося значения РB = 6,6 ⋅ 10‑4. Динамика изменения
вероятности незначительна и представлена на рис. 4, где время выраженно в днях.

Рисунок 4 – Вероятность события Взрыв метановоздушной смеси
как функция времени
По результатам моделирования вероятность возникновения события взрыв
в горной выработке превышает допустимую вероятность события взрыв
(согласно ГОСТ 12.1.010‑76 Взрывобезопасность. Общие требования
, вероятность возникновения взрыва на любом взрывоопасном участке в течении года не выше 10−6)
на 2 порядка.
5. Оптимизация систем автоматической газовой защиты
Повышения надежности системы можно достичь двумя путями: снижением интенсивности отказов и снижением интенсивности профилактических простоев. При моделировании системы без выполнения профилактических работ полученные результаты на 1 порядок превосходят допустимые (рис. 5), следовательно, данный путь не достаточный.
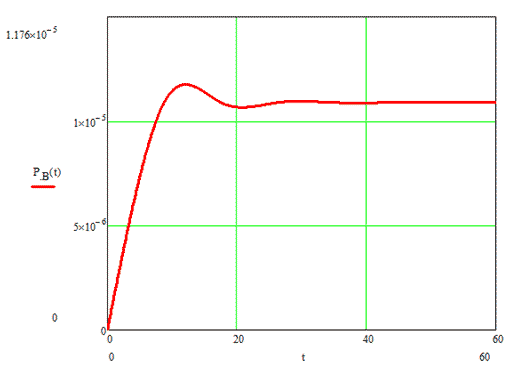
Рисунок 5 – Вероятность события Взрыв метановоздушной смеси
как функция времени для системы без профилактики
Разработка принципиально новой системы с полным дублированием датчиков и линий связи нецелесообразна, так как ее применение трудно обосновать экономически. Для соответствия вероятности взрыва требуемым значениям необходимо снизить на порядок вероятность отказа элементов системы, что возможно при применении ненагруженного резерва с автоматическим устройством переключения. Для того чтобы отказы устройства отключения, датчика и линии связи не создавали опасных состояний предлагается: питать катушку контактора, подающего напряжение на участок, через нормально разомкнутый контакт системы АГЗ; использовать интерфейсы передачи данных от датчика к анализаторам позволяющие организовать функцию самодиагностики, например аналоговая токовая петля 4..20 мА или передачу данных в виде цифрового кода.
Наличие резервного контроллера позволяет не прерывать технологический процесс для замены отказавшей аппаратуры [7]. Резервный микроконтроллер должен выполнять тот же набор инструкций, что и основной, однако иметь другой адрес в промышленной сети, чтобы переключение на резервный МК фиксировалось концентратором информации вышестоящего уровня АСУ ТП. Целесообразно применить ненагруженный резерв. Наиболее ответственным узлом в такой структуре является устройство, осуществляющее автоматическое переключение питания с основного на резервный МК. На вход данной схемы поступают контрольные импульсы от основного МК, наличие которых свидетельствует о штатном режиме работы устройства. Отсутствие указанных импульсов свидетельствует об отказе основного МК и необходимости включения в работу резервного контроллера. Периодичность контрольных импульсов задается сторожевым таймером основного МК.
На принципиальной схеме устройства переключения (рис. 6) генератор G представляет собой внешний вывод сторожевого таймера основного МК. Цепочка R1, C1 сглаживает
импульсный сигнал. В качестве ключевых элементов используются MOSFET‑транзисторы с каналом n‑типа, которые в установившемся режиме потребляют достаточно
малую мощность. Поскольку MOSFET‑транзисторы имеют паразитную емкость по каналу затвор‑сток, то на их входе включен повторитель на операционном усилителе,
исключающий влияние емкости транзистора на данную цепь [8]. Сигнал с выхода операционного усилителя поступает на затворы транзисторов VT1 и VT2. VT1
используется в качестве ключа, через который подается питание на основной МК. До тех пор, пока на затворе транзистора VT1 напряжение выше потенциала
земли – он открыт. Транзистор VТ2 и резистор R2 образуют логический элемент НЕ. Пока сигнал подаётся на затвор VТ2 – VТ3 закрыт.
В случае, если основной МК перестает подавать контрольные импульсы, потенциал затвора VТ2 равен 0
, он закрывается и через резистор R2 открывается
транзистор VT3, создающий цепь питания резервного МК. Кнопка S1 служит для запуска основного МК, замыкаясь, она шунтирует VТ1, образуя цепь питания
основного МК. Параметры R1 и C1 рассчитываются исходя из амплитуды и скважности контрольного сигнала, которые определяются напряжением питания и частотой
тактового генератора МК.

Рисунок 6 – Принципиальная схема устройства переключения
Работа рассмотренной схемы моделировалась с использованием пакета MicroCAP. На рис. 7 представлены графики переходного процесса в схеме при подаче питания.
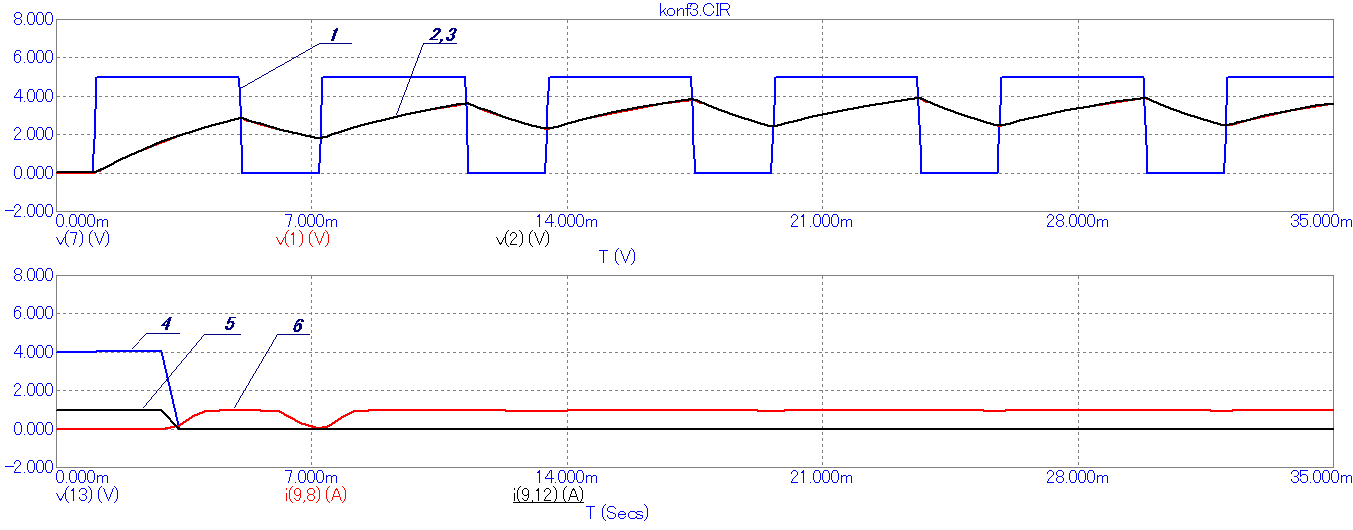
Рисунок 7 – Графики переходного процесса в схеме при подаче питания: 1 – контрольный импульс, 2 – напряжение на выходе RC‑цепи, 3 – напряжение на выходе повторителя на операционном усилителе, 4 – напряжение на затворе транзистора VT3, 5 – ток по каналу исток‑сток транзистора VT3, 6 – ток по каналу исток‑сток транзистора VT1
При подаче питания транзистор VT1 закрыт, VT3 – открыт. После первого контрольного импульса VТ3 запирается, после второго – VТ1 полностью открыт. Таким образом, длительность переходного процесса отпирания VT1 составляет 12 мс. После третьего контрольного импульса RC‑цепочка переходит в квазиустановившейся режим. Следует отметить, что увеличение скважности контрольных импульсов и снижение их амплитуды приводит к увеличению длительности переходного процесса.
На рис. 8 представлены графики переходного процесса в схеме при отказе основного микроконтроллера.
При отсутствии контрольного импульса RC‑цепь разряжается, потенциал на выходе повторителя становится равным нулю, VT1 и VТ2 запираются, появляется положительный потенциал на затворе VТ3 и начинает протекать ток в цепи питания резервного МК. Длительность переходного процесса составляет 16 мс.
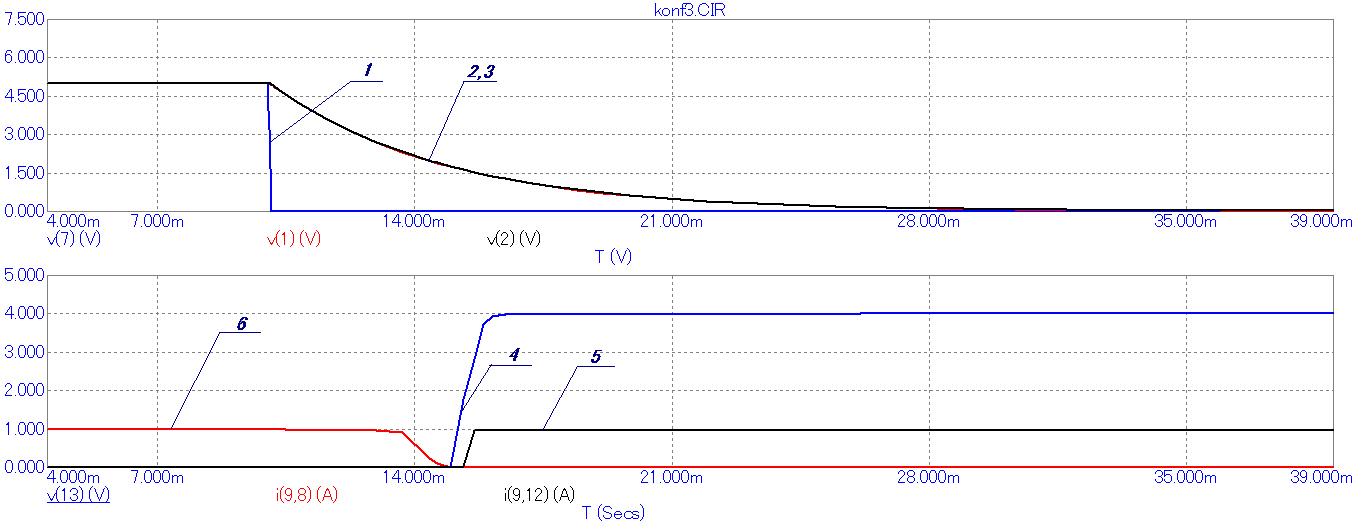
Рисунок 8 – Графики переходного процесса в схеме при отказе основного микроконтроллера: 1 – контрольный импульс, 2 – напряжение на выходе RC‑цепи, 3 – напряжение на выходе повторителя на операционном усилителе, 4 – напряжение на затворе транзистора VT3, 5 – ток по каналу исток‑сток транзистора VT3, 6 – ток по каналу исток‑сток транзистора VT1
Таким образом, повысить надежность мониторинга состояния рудничной атмосферы возможно за счет пассивного резервирования микропроцессорного устройства защиты.
6. Работа АГЗ при нестационарных процессах метанообразования
При расчетах расхода воздуха на проветривание выработок, принимается допущение, что каждая единица площади угольного массива выделяет равное объемное количество метана, т. е. считается, что метановыделение стационарно. В таком случае концентрация метана в рудничном воздухе, по мере его продвижения по выработкам, увеличивается нарастающим итогом. Однако существует ряд процессов, именуемых газодинамическими явлениями, при которых с незначительной площади угольного массива, за короткий промежуток времени, выделяется количество метана достаточное для образования взрывоопасных концентраций.
Сложность защиты от ГДЯ, состоит в наличии транспортного запаздывания, которое определяется скоростью движения воздуха и длиной выработки. Согласно Правил безопасности [9], допустимая скорость движения воздуха по выработкам vдоп = 0,25..4 м/с. При длине очистного забоя от 200 до 250 м, транспортная составляющая запаздывания может составлять от 50 до 1000 с (рис. 9), что является недопустимым.
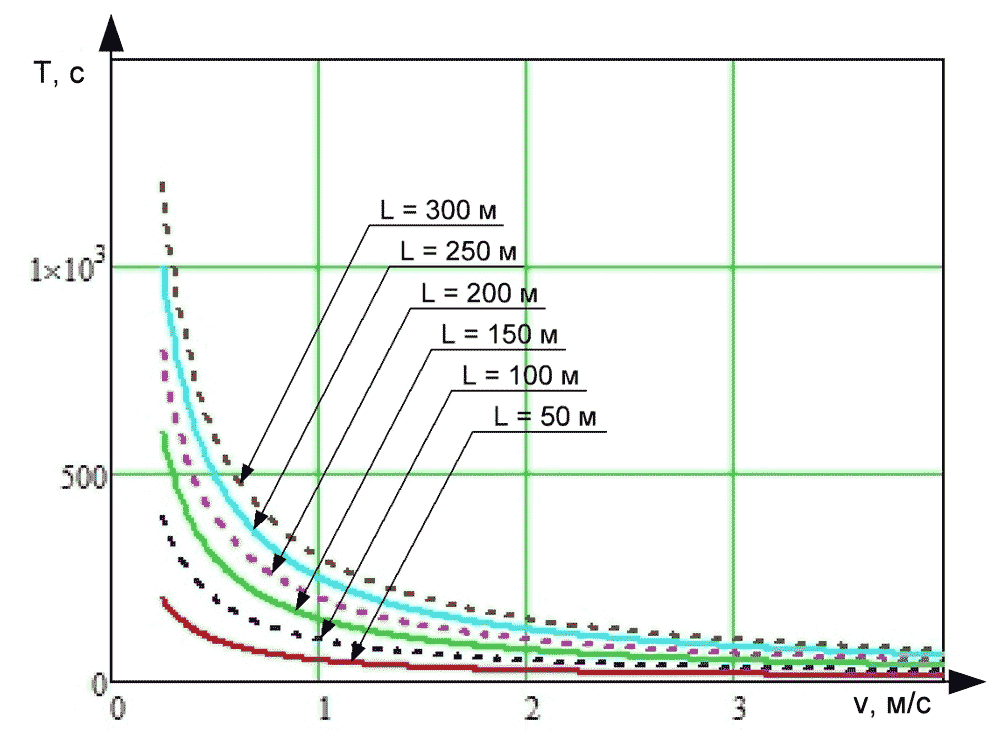
Рисунок 9 – Графики зависимостей транспортного запаздывания измерения концентрации метана от скорости воздуха и длины очистной выработки для датчика, расположенного на вентиляционном штреке
Имеющиеся методы текущего прогноза различных типов ГДЯ были предложены и обоснованы несколько десятилетий назад, и основаны на использовании первичных
физических величин, характеризующих разрушение газонасыщенного угольного массива: действующих механических напряжений, прочностных характеристик угля и
вмещающих пород, давления газа в пласте, газоносности угля, его влажности и т. п. [10]. Эти величины измерялись, так называемыми, инструментальными
методами, заключающимися в экспресс‑анализе проб газа и угля, взятых при бурении передовых разведочных скважин. В целях обеспечения безопасности необходим
непрерывный контроль фактора развязывания ГДЯ. Отдельные методы непрерывного мониторинга: спектрально‑акустический, акустической эмиссии, по температуре
забоя и прочие, помимо низкой точности требуют проектирования, создания, монтажа и эксплуатации принципиально новых систем в условиях очистного забоя.
При этом, информацию о начале ГДЯ можно иметь, обрабатывая показания датчиков существующих систем. Покажем, что с помощью аппаратуры АГЗ можно контролировать
газовый фактор выбросоопасности, характеризующий давление газа в пласте и его газофильтрационную способность. Известно [11], что давление свободного газа Р,
направленное в сторону горной выработки, на расстоянии х от обнаженной поверхности выработки может быть описано следующей полуэмпирической формулой:
![]() | (2) |
где m – константа, характеризующая влияние на давление газа пористости угля; G – расход газа с забоя выработки, м3/с; k0 – коэффициент, характеризующий газопроницаемость пласта, м−3; ψ = 1/xст – константа, определяемая расстоянием xст от забоя до участка массива, где давление газа стабилизируется, м−1:
![]() | (3) |
Sз – площадь поверхности забоя выработки, м2; η – коэффициент динамической вязкости метана, Па⋅с; Pат – давление газа на плоскости забоя, Па.
Попадая в выработку, газ смешивается с воздухом, в результате чего концентрация метана снижается. Газовыделение в выработку Хв складывается из газовыделения с поверхности забоя, бортов выработки и отбитого угля:
![]() | (4) |
где Gб и Gо.у. – расход газа с поверхности соответственно бортов выработки и отбитого угля, м3/с⋅м2; Sб и Sо.у. – соответственно, поверхность бортов выработки и отбитого угля на участке от забоя до места установки датчика метана (например, ДМТ‑4) аппаратуры автоматической газовой защиты, м2.
Это газовыделение можно определить через текущее значение Cт концентрации метана в атмосфере выработки:
![]() | (5) |
где Q – расход воздуха вентилятора местного проветривания (ВМП), проветривающего выработку, м3/с; Cт – текущее значение концентрации метана, замеренное датчиком метана, %; C0 – концентрация метана в свежей струе, поступающей в выработку.
Тогда расход газа с забоя выработки:
![]() | (6) |
где Cф – фоновая концентрация метана, замеренная до начала работы комбайна, и характеризующая газовыделение из бортов выработки и отбитого, но не отгруженного угля, %, при условии, что C0 = 0 в момент замера фоновой концентрации.
Искомое давление газа на некотором критическом
расстоянии от забоя выработки хкр, где начинается выбросоопасная зона, определится подстановкой (6) в (2):
![]() | (7) |
Таким образом, концентрация метана в выработке, замеренная аппаратурой контроля метана, характеризует давление свободного газа в призабойной зоне угольного пласта и его газофильтрационную способность – параметры, определяющие газовый фактор выбросоопасности.
Для повышения быстродействия АГЗ предлагается установка стационарных датчиков на секциях крепи забоя. Данное решение позволит сократить время транспортного запаздывания при возникновении газодинамических явлений. Количество дополнительных датчиков определяет время транспортного запаздывания:
![]() | (8) |
где L – длина выработки между датчиками метана, v – скорость воздуха в выработке.
Так как скорость воздуха в очистном забое величина нерегулируемая, то для снижения величины запаздывания необходимо уменьшить расстояние между соседними датчиками. Если принять оптимальное значение величины транспортного запаздывания, то необходимое количество датчиков метана в очистном забое составляет:
![]() | (9) |
7. Борьба со слоевыми скопления метана
Аппаратура автоматической газовой защиты контролирует концентрацию метана в местах регламентированных правилами безопасности в угольных шахтах. Однако ввиду того что скорость и расход воздуха не равномерен для всех выработок возможны слоевые скопления метана во взрывоопасных концентрациях в местах не контролируемых аппаратурой АГЗ. Очевидно, что невозможно установить датчики во всех местах предполагаемого скопления метана. Поэтому предлагается интеграция мобильного компонента в систему автоматической газовой защиты. В настоящее время распространены шахтные головные светильники со встроенным датчиком концентрации метана, в частности СМГВ.1А.Р.05, KLW4LMX и пр. Перспективным направлением в развитии шахтных информационно управляющих систем являются системы позиционирования горнорабочих, типа СПГТ‑41. Вполне логичным является объединение этих технологий в одну.
Результаты измерения со встроенного в головной светильник датчика будут использоваться не только для сигнализации аэрогазовой обстановки горнорабочему, но и вместе с персональным идентификатором будут транслироваться в систему позиционирования. Структурная схема предлагаемого портативного блока измерения концентрации метана и позиционирования приведена на рисунке 10. Датчик метана, через блок согласования подает результаты измерений на вход встроенного в МК АЦП. Выборка результатов измерений сохраняется во внутренней памяти МК. В случае, если микроконтроллер через приемник получает сигнал от метки системы позиционирования, он передает в систему позиционирования не только идентификатор, но и усредненное и максимально зарегистрированное с момента последнего обращения значение концентрации метана. При этом функция оповещения горнорабочего миганием лампы сохранена (блок сигнализации). Таким образом, имеется возможность контролировать значение концентрации метана во всех выработках, в которых находится персонал. Данная технология позволит дополнить стационарные системы газовой защиты на добычных и подготовительных участках, а также контролировать значительное пространство горных выработок, без внедрения дорогостоящей и требующей постоянного обслуживания инфраструктуры стационарных систем.
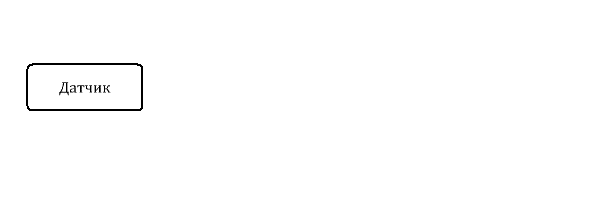
Рисунок 10 – Структурная схема портативного блока измерения концентрации метана и позиционирования. Анимация состоит из 6 кадров с задержкой в 1 с между кадрами; задержка до повторного изображения составляет 6 с; количество циклов воспроизведения ограничено 7‑ю
Выводы
Данная работа посвящена повышению надежности автоматической газовой защиты шахты. В ней рассмотрены современные тенденции развития систем АГЗ,
и перспективы ее совершенствования. В работе рассмотрены причины возникновения такого состояния как взрыв метановоздушной смеси
и составлена
вероятностная модель данного события. В результате моделирования наихудшего
состояния была выявлена недостаточная надежность газоанализаторов систем
АГЗ. Для устранения выявленного недостатка была разработана и исследована схема пассивного резервирования микроконтроллера газоанализатора.
При рассмотрении работы АГЗ при возникновении ГДЯ, а также слоевых скоплений метана, указано, что АГЗ не в состоянии нивелировать данные опасные состояния, ввиду особенностей структуры построения данных систем. Для устранения данных недостатков:
- Указано на возможность контролировать параметры, определяющие газовый фактор выбросоопасности с помощью данных о концентрации метана.
- Предложена интеграция мобильного компонента в структуру АГЗ.
- Предложен способ сокращения времени транспортного запаздывания.
Важно! При написании данного реферата магистерская работа еще не завершена. Окончательное завершение: декабрь 2014 года. Полный текст работы и материалы по теме могут быть получены у автора после указанной даты.
Перечень ссылок
- Кашуба И. О. Оценка эффективности контроля содержания метана в рудничной атмосфере при крупных авариях в угольных шахтах / О. И. Кашуба, В. Н. Медведев, О. А. Демченко // Науковий вісник УкрНДІПБ, 2012, № (25). – с. 68‑78.
- Басовский Б. И. Автоматическая газовая защита и контроль рудничной атмосферы / Басовский Б.И., Биренберг И.Э., Карпов Е.Ф.; – М.: Недра, 1984 – 284 с.
- Курносов В. Г. Научные основы автоматизации в угольной промышленности: опыт и перспективы развития: монография / Курносов В. Г., Силаев В. И.; Международный институт независимых педагогических исследований МИНПИ – ЮНЕСКО, ОАО
Автоматгормаш им. В.А. Антипова
. – Донецк: изд‑воВебер
(Донецкое отделение), 2009. – 422 с. - Федорченко А. А. Микропроцессорное устройство прогнозирования опасности взрыва метановоздушной смеси в шахте / А. А. Федорченко, С. В. Василец // Автоматизація технологічних об’єктів та процесів. Пошук молодих. Збірник наукових праць ХІII науково‑технічної конференції аспірантів та студентів в м. Донецьку 14‑17 травня 2013 р. – Донецьк, ДонНТУ, 2013. – с. 369–371
- Надежность электрооборудования угольных шахт / Б. Н. Ванеев, В. М. Гостищев, В. С. Дзюбан и др.; Под ред. А. И. Пархоменко. – М.: Недра, 1994. – 255 с.
- Колосюк В.П. Защитное отключение рудничных электроустановок / Колосюк В. П. – М: Недра, 1980 – 334 с.
- Федорченко А.А. Повышение надежности мониторинга состояния рудничной атмосферы за счет резервирования микропроцессорного устройства защиты / А.А. Федорченко // Севергеоэкотех‑2013. Сборник научных работ XIV международной молодежной научной конференции в г. Ухте 20‑22 марта 2013 г. – Ухта, УГТУ, 2013. – с. 117–120.
- Хилл У. Искусство схемотехники / Хилл У., Хоровиц П. – М.: Мир, 1998. – 704 с.
- НПАОП 10.0‑1.01‑10. Правила безпеки у вугільних шахтах. Наказ Державного комітету України з промислової безпеки, охорони праці та гірничого нагляду № 62 від 23.03.2010. – 150 с.
- Шадрин А. В., Шадрина О.Я. Сравнительный анализ известных критериев текущего прогноза выбросоопасности угольных пластов // Информационные недра Кузбасса: Труды IV Всероссийской научно‑практической конференции. ‑ Кемерово: ООО
ИНТ
, 2005. – с. 84–86. - Глушко В. Т. Геофизический контроль в угольных шахтах. / Глушко В. Т., Ямщиков В. С., Яланский А. А.; Киев: Наукова думка, 1978. – 224 с.