Содержание
- Введение
- 1. Актуальность темы
- 2. Цель и задачи исследования, планируемые результаты
- 3. Обзор исследований и разработок
- 3.1 Лазерные датчики РФ620
- 3.2 Автоматизированный диагностический комплекс для контроля геометрических параметров колесных пар вагонов «КОМПЛЕКС»
- 3.3 Система автоматизированного контроля колесных пар «АУРА»
- 4. Выбор метода
- Список источников
Введение
Железные дороги широко распространены и имеют много преимуществ — высокую грузоподъёмность, надёжность, сравнительно высокую скорость. По железным дорогам перевозят самые разные грузы (особенно массовые: сырьё, сельхозпродукция). Не стоит забывать что железная дорога транспортирует не только сырьё производителям и товары потребителям, но и является транспортом для многих людей, как на малые (пригородные железные дороги), так и на большие расстояния. Так же масса людей ежедневно пользуется трамваями и метрополитеном.
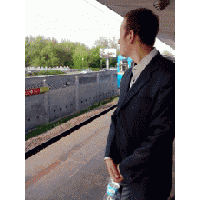
Анимация – Прибытие вагона метро на станцию. 10 кадров. Создана при помощи «GIF Animator». Задержка 0,5 с.
Поезд не являются лишь частью прошлого, которая не каналу в лету. Наоборот, это развивающаяся часть транспорта. Сначала в Японии, а теперь и в Европе создана система скоростных железных дорог, допускающих движение со скоростями до трёхсот километров в час. Электрифицированные железные дороги (в данный момент это большинство железных дорог с интенсивным движением) намного экологичнее автомобильного транспорта.
Эти и многие другие факторы говорят о том, что железнодорожный транспорт очень распространён и, скорее всего, не будет терять своих позиций в ближайшее время, а возможно и укрепит их. Поэтому очень остро встаёт вопрос обеспечения безопасности использования железнодорожных составов. В моей работе будут проведены исследования системы, сканирующей поверхность железнодорожного колеса.
1. Актуальность темы
Малейшие отклонения параметров железнодорожных колес от номинальных ведут к снижению ходовых и динамических характеристик локомотивов и вагонов, а следовательно, и безопасности эксплуатации составов. В связи с этим в процессе изготовления, а также эксплуатации подвижного состава железнодорожного транспорта к железнодорожным колесам ставятся очень высокие требования в отношении контроля и сохранения геометрических параметров.
До недавнего времени измерение параметров колёс и расчёт их отклонений заключалось к использовании контактных приборов (в основном шаблонов). Шаблонами измеряют профиль катания, толщину гребня. Измерение коробления обычно осуществляется контрольной плитой или шаблоном типа «паук».
Дефектоскопист прикладывает шаблон к колесу, после чего при помощи щупа определяет максимальный зазор. Результат измерений очень сильно зависит от уровня навыков дефектоскописта, от правильности использования им шаблона, щупов и т. д. Естественно, что человек вносит отдельную погрешность в измерения.
Принцип применения шаблонов вообще имеет ещё массу недостатков. Например, если колёса начинают протачивать по иной методике (например, со скошенным гребнем вместо ГОСТ 9036-88), то возникает проблема контроля качества проточки, поскольку прежние шаблоны уже не подходят для данной задачи, нужно изготавливать новые.
Вес колеса составляет 500 кг. При определении осевого коробления колесо кладут на контрольную плиту, а затем определяют зазор между плитой и колесом по всей длине. Такой механизм неизбежно приводит к появлению выщерблин на контрольной плите, а следовательно, результат измерений зависит от плиты, на которой они проводятся.
Не следует забывать и о столь важном факторе как время. При соблюдении всех требований ГОСТ для полного измерения колеса контактными методами опытному дефектоскописту потребуется порядка 20 минут, что существенно тормозит весь производственный процесс.
Порядка 30 геометрических параметров железнодорожных колес необходимо контролировать в процессе эксплуатации и измерения. Большинство из них необходимо измерить с высокой точностью (максимальное осевое коробление не должно превышать 0,1 мм). При помощи шаблонов подобную задачу реализовать затруднительно, и займёт определённо сравнительно большое количество времени. В связи с этим возникла необходимость создания высококачественных комплексов, которые смогли бы обеспечивать требуемую точность.
Недостатки контактного метода измерений:
длительность и трудоемкость процесса измерения;
зависимость результатов измерений от «человеческого фактора»;
зависимость результатов измерений от деформации контактных приборов в процессе эксплуатации;
невозможность перенастраивать контактные приборы в соответствии с изменениями требований к конечной продукции.
Избавиться от этих недостатков можно при использовании бесконтактных методов контроля. В качестве средства измерения можно использовать лазерные датчики-дальномеры (например, растровые дальномеры). Датчики такого рода за одно сканирование снимают профиль (а не одну точку). Длина поверхности сканирования колеблется (зависит от мощности лазера и погрешности измерения).
2. Цель и задачи исследования, планируемые результаты
Цель работы: обеспечить метрологические и геометрические характеристики заготовки железнодорожного колеса путем применения оптического метода контроля геометрии и компенсации динамических возмущений среды, влияющих на результаты измерений, а так же повышение метрологической надежности и уменьшение материалоемкости и энергозатратности при дальнейшей обработке заготовки колеса.
Для достижения цели необходимо решить следующие задачи:
- Разработка системы спектрального взаимодействия оптического дальномера и заготовки колеса высокой температуры.
- Разработка методики установки оптических компонентов относительно заготовки в процессе прокатки.
- Анализ возмущающих факторов и их влияния на результат измерения.
- Формирование оценки метрологических параметров и характеристик устройства.
- Разработка первичного алгоритма восстановления геометрии заготовки колеса.
- Синтез структурной схемы системы согласования частоты вращения валков колесопрокатного состояния.
- ширина обода колеса;
- вылет ступицы;
- максимальное осевое коробление;
- диаметр по кругу катания;
- эллиптичность круга катания;
- внутренний диаметр обода с внутренней стороны;
- внутренний диаметр обода с внешней стороны;
- толщина обода с внутренней стороны;
- толщина обода с внешней стороны;
- длина ступицы;
- наружный диаметр ступицы с наружной стороны;
- наружный диаметр ступицы с внутренней стороны;
- диаметр отверстия ступицы;
- толщина ступицы с внутренней стороны;
- толщина ступицы с наружной стороны;
- разность ширины обода;
- разность внутренней толщины обода по периметру;
- разность наружной толщины обода по периметру;
- разность внутренней толщины ступицы (разностенность ступицы);
- разность диаметров внутренних поверхностей обода;
- эксцентриситет отверстия ступицы относительно круга катания;
- наибольший зазор между реальным и теоретическим профилем катания;
- параллельность торцевых поверхностей ступицы и боковой поверхности обода с внутренней стороны колеса;
- толщина диска (переход обод/диск);
- толщина диска (переход диск/ступица);
- максимальный развал или поднутрение;
- профиль катания, зазор в контрольных точках;
- разность толщины диска по периметру радиуса (переход обод/диск);
- разность толщины диска по периметру радиуса (переход диск/ступица).
- Компактная и надежная конструкция
- Высокая надежность и точность
- Большой межсервисный интервал
- Проверенная конструкция УЗ сканеров для автоматизированной работы
- Простое управление и обслуживание
- УЗ и вихретоковый контроль
- Возможность наблюдения результатов контроля «он-лайн»
- Почти не требующая ухода конструкция
- Обслуживание установки одним оператором
- Малые эксплуатационные затраты
- Время такта около 5 мин
- Соответствие требованиям Deutsche Bahn
- Вопроизводимость результатов контроля
- Компелкс [Электронный ресурс]. – Режим доступа: http://www.labracon.ru/ru/products/complex
- Дефектоскопия деталей подвижного состава железных дорог и метрополитенов / [ Ильин В. А., Кожевников Г. И., Левыкин Ф. В., Штремер Ю. Н.]; Под ред. Ильина В. А., М. Транспорт 198. – 318 стр.
- Мойкин Д. А. Неразрушающий контроль в вагонном хозяйстве. Учебное пособие, Петербургский Государственный Университет путей сообщения, Санкт-Петербург, 2001. – 87 стр.
- Компания ООО «Матириалз Лаб» [Электронный ресурс]. – Режим доступа: http://www.materials-lab.com.ua/...
- Андреев А. Н., Шерешев А. Б. Оптические измерения: Учебное пособие по курсу «Оптические измерения». М.,:Изд. МИИГАиК, 2002 г. –72 стр.
- Дефектоскопист.ру [Электронный ресурс]. – Режим доступа: http://defektoskopist.ru/showthread.php?t=606
- Справочник конструктора-машиностроителя. Анурьев В. И. Издательство «Машиностроение», 2001 год. – 920 стр.
3. Обзор исследований и разработок
3.1 Лазерный датчик РФ620
Имеют диапазон измерения по оси Х до 150 мм (рис. 1). По высоте такие датчики захватывают диапазон от 100 до 350 мм. Чем меньше диапазон измерения прибора – тем выше его точность. Скорость сканирования таких датчиков весьма высока – порядка 100 сканов в секунду. За одно сканирование датчик может получить до 1024 точек.
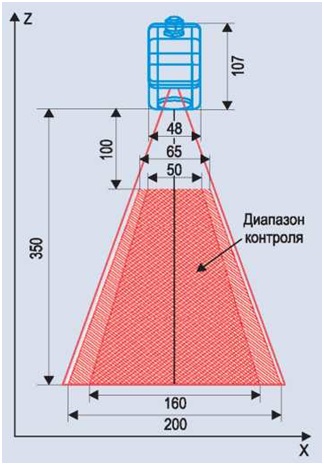
Рисунок 1 – Диапазон измерения растрового лазерного датчика РФ 620
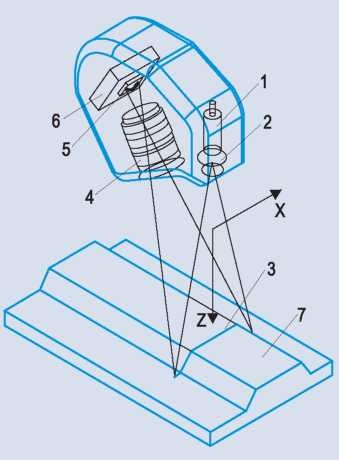
Рисунок 2 – Принцип работы растрового сканера-дальномера
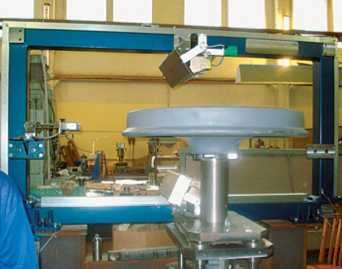
Рисунок 3 – Общий вид комплекса
В основу работы растровых сканеров-дальномеров положен принцип оптической триангуляции (рис. 2).
Излучение полупроводникового лазера 1 формируется объективом 2 в виде линии 3 и проецируется на объект 7. Рассеянное на объекте излучение объективом 4 собирается на двумерной CMOS-матрице 5. Полученное изображение контура объекта анализируется сигнальным процессором 6, который рассчитывает расстояние до объекта (координата Z) для каждой из множества точек вдоль лазерной линии на объекте (координата Х).
ЗАО «Виматек» (входит в ГП «Юнитест») разработало принципиально новый комплекс для измерения ж.-д. колес бесконтактным методом (рис. 3).
В его основе лежит использование растровых лазерных датчиков. Установка была спроектирована так, чтобы избежать всех трудностей при контроле, описанных выше.
Механическая часть комплекса была предельно упрощена, что позволило существенно повысить надежность и износостойкость оборудования.
Измерительная аппаратура легко интегрируется в существующую производственную линию. Колеса на пост контроля подаются непосредственно с конвейера завода. С помощью перекладчика колесо устанавливается на специальную план-шайбу с прорезями. Осуществляется контроль. После этого колесо вновь возвращается на конвейер. Управление механической частью комплекса осуществляется при помощи контроллеров Siemens.
В состав комплекса входит 7 растровых лазерных датчиков (рис. 4). Три датчика располагаются сверху, чтобы измерять внешнюю поверхность колеса, три – снизу, они снимают внутреннюю поверхность, а седьмой датчик сканирует поверхность катания. Диапазона трех датчиков хватает для того, чтобы полностью измерить профиль колеса по радиусу. В процессе контроля колесо вращается вокруг оси установки, угол вращения измеряется с помощью высокоточного энкодера. Таким образом, результатом измерений является набор профилей колеса и соответствующий им угол поворота вокруг оси вращения. Этой информации достаточно, чтобы восстановить трехмерную картину колеса.
Лазерные датчики сведены в единую сеть, объединенную на основе 485 интерфейса, по которому данные поступают на компьютер. Угол с энкодера, команды управления и контроля состояния установки поступают на компьютер через интерфейс сетевой карты. В состав комплекса входит компьютерная программа, которая устанавливает связь с контроллером и датчиками. Она получает все измеренные данные, анализирует их и рассчитывает все требуемые характеристики колеса. По окончании расчета на экран выводится список измеренных параметров и их соответствие нормам ГОСТ. Результаты контроля по локальной сети передаются на сервер предприятия, где производится автоматическая архивация данных. По результатам измерения создается протокол контроля и выдается заключение о годности колеса. Весь измерительный цикл занимает 30 с!
Еще одним существенным достоинством комплекса является автоматическое сохранения результатов контроля в базу данных. Архивируются результаты контроля, номер колеса, ФИО дефектоскописта, номер смены и т. д. Имеется возможность осуществлять выборку из базы данных по фамилии дефектоскописта, дате, номеру смены и т. п.
Комплекс измеряет следующие параметры колеса:
Хочется особо остановиться на ряде важнейших нюансов, которые необходимо было учесть при создании комплекса и программного обеспечения. Ввиду упрощения механической части комплекса, колесо устанавливалось так, что его физический центр и центр вращения оси установки не совпадают. Более того, плоскость колеса может не быть перпендикулярна плоскости сканирования. Таким образом, все вычисления весьма сильно усложнились, так как пришлось иметь дело с данными в трехмерной системе координат. Например, если бы колесо было жестко центрировано и выровнено на плоскости план-шайбы, можно было бы обойтись двумя координатами с датчиков, энкодер был бы не нужен.
Но в этом случае срок эксплуатации комплекса был бы меньше, а время контроля больше.
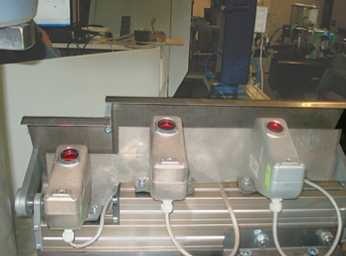
Рисунок 4 – Линейка лазерных датчиков
Для вычисления всех необходимых диаметров (по кругу катания, обода с внутренней и внешней сторон и т. д.) был применен метод наименьших квадратов. Координаты точек, лежащих на искомой окружности, переводятся из цилиндрической системы координат в декартову, затем проецируются на усредненную (также по методу наименьших квадратов) плоскость и подставляются в стандартный алгоритм аппроксимации эллипсом. Тем самым сразу вычисляется «средний» диаметр и эллиптичность.
Для вычисления отклонения поверхности катания от теоретического профиля была построена аналитическая функция, задающая профиль катания согласно ГОСТ 9036-88 (рис. 5). Затем, согласно тому же ГОСТ, функция программно совмещалась с боковой поверхностью обода с внутренней стороны, и вычислялись зазоры по всему периметру профиля. Измеренный и теоретический профиль выводятся на монитор компьютера.
Другим очень важным аспектом является калибровка и юстировка оборудования. Для того чтобы получать корректные профили колеса от совокупности датчиков, необходимо правильно выставить эти датчики по периметру измерительной линейки. Лучи сканирования датчиков верхней и нижней линеек должны лежать в одной плоскости и иметь одинаковый наклон. Плоскость сканирования должна проходить через центр вращения установки. Эта задача была решена с помощью юстировочного лазера.
После выставления датчиков необходимо произвести калибровку, т. е. определить взаиморасположение систем координат каждого, а затем совместить начала систем координат всех датчиков с осью вращения. Для калибровки был разработан специальный высокоточный шаблон. Он представляет собой линейку с эквидистантными насадками шириной и высотой 30 мм, расположенными на расстоянии 70 мм друг от друга. Шаблон был изготовлен с высокой точностью, все размеры были замерены с помощью штангенциркуля, прибора, чья точность выше точности используемых датчиков. Шаблон устанавливается на ось вращения вместо колеса и сканируется всеми датчиками. Таким образом, измерив шаблон, можно вычислить расстояние от всех датчиков до оси вращения, расстояние между линейками датчиков и взаиморасположение начал систем координат по оси Z.
Боковой датчик, который измеряет поверхность катания, может находиться в трех различных положениях – в зависимости от диаметра колеса. Для всех положений производится калибровка и сохраняется на компьютере. При переходе на другой типоразмер колеса достаточно загрузить файл с нужной калибровкой.
Еще одной важнейшей задачей является метрологическая аттестация установки. Так как комплекс является уникальным в своем роде, то как таковой методики для его аттестации не существует. Было принято решение произвести измерение всех параметров колеса с помощью высокоточного, сертифицированного оборудования фирмы CimCore (США), а затем по результатам сравнения с данными комплекса делать вывод о его точности. Данная процедура была успешно проведена. Стоит отметить, что на измерение одного колеса с помощью американской установки ушло порядка 8 ч (!).
Итак, комплекс фирмы «Виматек» позволяет осуществить измерение геометрических параметров колеса за 30 с, при этом имеет очень высокую механическую надежность. Он является отличной альтернативой прежним методам контроля размеров колес. В данный момент проходят пусконаладка комплекса на Выксунском металлургическом заводе [6].
3.2 Автоматизированный диагностический комплекс для контроля геометрических параметров колесных пар вагонов «КОМПЛЕКС»
Назначение: выявление на ходу поезда износов цельнокатаных колес. Передача полученной информации на ближайший пункт технического обслуживания (ПТО).
Принцип действия системы основан на лазерном бесконтактном контроле геометрии движущихся трехмерных объектов с помощью триангуляционных датчиков положения.
Отличительные особенности: бесконтактное измерение геометрических параметров колесных пар подвижного состава на ходу поезда при скоростях до 60 км/час в различных климатических условиях.
Применение системы позволяет повысить надежность эксплуатации подвижного состава и максимально устранить вероятность возникновения аварийных ситуаций на железной дороге, вызванных дефектами колесных пар [1].
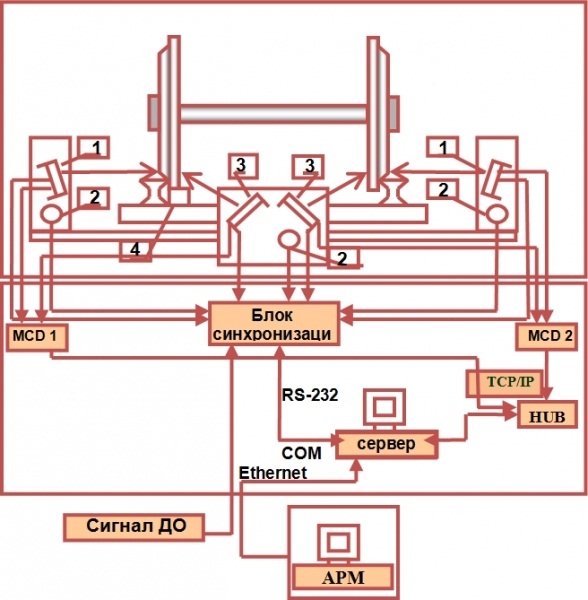
Рисунок 5 – Структурная схема системы «Комплекс»
3.3 Система автоматизированного контроля колесных пар «АУРА»
Установка предназначена для механизированной и автоматизированной дефектоскопии колес выкаченных колесных пар (КП) различных типов на продольные, поперечные и дефекты в объёме.
Преимущества:
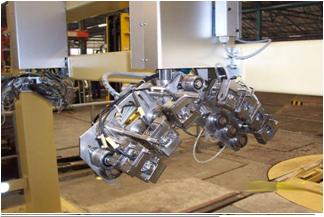
Рисунок 6 – Внешник вид комплекса контроля колесных пар «АУРА»
Конструкция и принцип действия.
Установка главным образом состоит из трех частей: стенда вращения КП, портала и размещенными на нём сканеров колес. Все части взаимосвязаны между обой посредством центральной системы управления (PLC).
В качестве ультразвукового дефектоскопа используется MODUS 03, а в качестве вихретокового – Elotest Ms/IC. Для определения координат дефектов от стенда вращения КП по шине Profibus в дефектоскопы поступает сигнал от датчика угла колеса.
Дефектоскопы обладают ЭВМ и могут выполнять задачу контроля автономно и независимо. Дефектоскопист работает за управляющим компьютером, который контролирует как дефектоскопы, так и систему управления стендом (PLC). В управляющем компьютере выбирается программа (объём) контроля, при помощи управляющего ПК ведется контроль за процессом дефектоскопии, здесь же сохраняются результаты контроля, проводится их обработка и визуализация. В завершения контроля данные сохраняются в банке данных и распечатываются протоколы. Несмотря на наличие различных дефектоскопов (УЗ, ВТ), дефектоскопист работает с одной универсальной интерфейсной программой.
Банк данных имеет многоступенчатую систему доступа так, что обычный оператор не может изменить/скорректировать результаты контроля. Копия банка данных резервируется на DVD- диске. Опционально возможно связка банка данных установки с банком данных депо, дороги [4].
4. Выбор метода
Из приведенных примеров разработок можно сделать вывод, что при использовании в качестве датчиков оптических приборов мы получаем более быстрое время сканирования, что является очень важным фактором. Так же следует отметить что оптические датчики обеспечат требуемую точность при решении данной задачи. Поскольку в производстве скорость играет очень важную роль, то для решения поставленной задачи было принято решение использовать именно оптический метод.
При написании данного реферата магистерская работа еще не завершена. Окончательное завершение: декабрь 2015 года. Полный текст работы и материалы по теме могут быть получены у автора или его руководителя после указанной даты.