Зміст
- Вступ
- 1. Актуальність теми
- 2. Мета і задачі дослідження та заплановані результати
- 3. Огляд досліджень та розробок
- 3.1 Лазерний датчик РФ620
- 3.2 Автоматизований діагностичний комплекс контролю геометричних параметрів колісних пар вагонів
КОМПЛЕКС
- 3.3 Система автоматизованого контролю колісних пар
АУРА
- 4. Вибір методу
- Список джерел
Вступ
Залізничі дороги широко розповсюджені та мають багато переваг — високу вантажопідйомність, надійність, відносно високу швидкість. Залізницями перевозять найрізноманітніші вантажі (особливо масові: сировина, сільгосппродукція). Не варто забувати, що залізниця транспортує не лише сировину виробникам і товари споживачам, але і є транспортом для багатьох людей, як на малі (приміські залізниці), так і на великі відстані. Так само велика кількість людей щодня користується трамваями і метрополітеном.
Поїзд це не лише є частина минулого. Навпаки, це частина транспорту, яка розвивається. Спочатку в Японії, а тепер і в Європі створена система швидкісних залізниць, що допускають рух з швидкостями до трьохсот кілометрів на годину. Електрифіковані залізниці (в даний момент це більшість залізниць з інтенсивним рухом) набагато екологічніші від автомобільного транспорту.
Ці та багато інших чинників говорять про те, що залізничний транспорт дуже поширений і швидше за все не буде втрачати своїх позицій найближчим часом, а можливо і зміцнить їх. Тому дуже гостро постає питання забезпечення безпеки використання залізничних складів. У моїй роботі будуть проведені дослідження системи, яка сканує поверхню залізничного колеса.
1. Актуальність теми
Найменші відхилення параметрів залізничного колеса від номінальних ведуть до зниження ходових і динамічних характеристик локомотивів і вагонів, а отже і безпеки експлуатації складів. У зв’язку з цим в процесі виготовлення, а також експлуатації рухомого складу залізничного транспорту до залізничних коліс ставляться дуже високі вимоги щодо контролю і збереження геометричних параметрів.
Донедавна вимірювання параметрів коліс і розрахунок їх відхилень полягало у використанні контактних приладів (в основному шаблонів). Шаблонами вимірюють профіль катання,
товщину гребеня. Вимірювання жолоблення зазвичай здійснюється контрольною плитою або шаблоном типу павук
.
Дефектоскопист прикладає шаблон до колеса, після чого за допомогою щупа визначає максимальний зазор. Результат вимірювань дуже сильно залежить від рівня навичок дефектоскопіста, від правильності використання ним шаблону, щупів тощо. Природно, що людина вносить окрему похибку у результаті вимірювання.
Принцип застосування шаблонів взагалі має ще масу недоліків. Наприклад, якщо колеса починають проточувати за іншою методикою (наприклад з скошеним гребенем замість ГОСТ 9036-88), то виникне проблема контролю якості проточки, оскільки колишні шаблони вже не підходять для даної задачі, потрібно виготовляти нові.
Вага колеса складає 500 кг. При визначенні осьового викривлення колесо кладуть на контрольну плиту, а потім визначають зазор між плитою і колесом по всій довжині. Такий механізм неминуче призводить до появи вищербліни на контрольній плиті, а отже результат вимірювань залежить від плити, на якій вони проводяться.
Не слід забувати і про настільки важливий фактор як час. При дотриманні всіх вимог ГОСТ для повного вимірювання колеса контактними методами досвідченому дефектоскописту потрібно близько 20 хвилин, що істотно гальмує весь виробничий процес.
Приблизно 30 геометрчних параметрів залізничних коліс необхідно контролювати в процесі експлуатації та вимірювання. Більшість з них необхідно виміряти з високою точністю (максимальне осьове жолоблення не повинно перевищувати 0,1 мм). За допомогою шаблонів подібне завдання реалізувати важко, та забере велику кількість часу. У зв’язку з цим виникла необхідність створення високоякісних комплексів, які змогли б забезпечувати необхідну точність.
Недоліки контактного методу вимірів:
тривалість і трудомісткість процесу вимірювання;
залежність результатів вимірювань від людського фактора
;
залежність результатів вимірювань від деформації контактних приладів у процесі експлуатації;
неможливість перенастроювати контактні прилади відповідно до змін вимог до кінцевої продукції.
Позбутися цих недоліків можна при використанні безконтактних методів контролю. Як засіб вимірювання можна використовувати лазерні датчики-далекоміри (наприклад растрові далекоміри). Датчики такого роду за одне сканування знімають профіль (а не одну точку). Довжина поверхні сканування коливається (залежить від потужності лазера і похибки вимірювання).
2. Мета і завдання дослідження, плановані результати
Мета роботи: забезпечити метрологічні і геометричні характеристики заготівки залізничного колеса шляхом застосування оптичного методу контролю геометрії та компенсації динамічних збурень середовища, що впливають на результати вимірювань, а так само підвищення метрологічної надійності і зменшення матеріалоємності та енерговитратності при подальшій обробці заготовки колеса.
Для досягнення мети необхідно вирішити наступні завдання:
- Розробка системи спектральної взаємодії оптичного далекоміра і заготівки колеса високої температури.
- Розробка методики встановлення оптичних компонентів відносно заготівки в процесі прокатки.
- Аналіз факторів, що обурюють та їх впливу на результат вимірювання.
- Формування оцінки метрологічних параметрів і характеристик пристрою.
- Розробка первинного алгоритму відновлення геометрії заготівки колеса.
- Синтез структурної схеми системи узгодження частоти обертання валків колесопрокатного стану.
- ширина обіда колеса;
- виліт маточини;
- максимальне осьове жолоблення;
- діаметр по колу катання;
- еліптичність кола катання;
- внутрішній діаметр обіда з внутрішньої сторони;
- внутрішній діаметр обіда з зовнішньої сторони;
- товщина обіда з внутрішньої сторони;
- товщина обіда з зовнішньої сторони;
- довжина маточини;
- зовнішній діаметр маточини з зовнішнього боку;
- зовнішній діаметр маточини з внутрішньої сторони;
- діаметр отвору маточини;
- товщина маточини з внутрішньої сторони;
- товщина маточини з зовнішнього боку;
- різниця ширини обіда;
- різниця внутрішньої товщини обіда по периметру;
- різниця зовнішньої товщини обіда по периметру;
- різниця внутрішньої товщини маточини (разностенность маточини);
- різниця діаметрів внутрішніх поверхонь обіда;
- ексцентриситет отвори маточини щодо кола катання;
- найбільший зазор між реальним і теоретичним профілем катання;
- паралельність торцевих поверхонь маточини і бічній поверхні обіда з внутрішньої сторони колеса;
- товщина диска (перехід обід / диск);
- товщина диска (перехід диск / маточина);
- максимальний розвал;
- профіль катання, зазор у контрольних точках;
- різниця товщини диска по периметру радіусу (перехід обід / диск);
- різниця товщини диска по периметру радіусу (перехід диск / маточина).
- Компелкс [Электронный ресурс]. – Режим доступа: http://www.labracon.ru/ru/products/complex
- Дефектоскопия деталей подвижного состава железных дорог и метрополитенов / [ Ильин В. А., Кожевников Г. И., Левыкин Ф. В., Штремер Ю. Н.]; Под ред. Ильина В. А., М. Транспорт 198. – 318 стр.
- Мойкин Д. А. Неразрушающий контроль в вагонном хозяйстве. Учебное пособие, Петербургский Государственный Университет путей сообщения, Санкт-Петербург, 2001. – 87 стр.
- Компания ООО «Матириалз Лаб» [Электронный ресурс]. – Режим доступа: http://www.materials-lab.com.ua/...
- Андреев А. Н., Шерешев А. Б. Оптические измерения: Учебное пособие по курсу «Оптические измерения». М.,:Изд. МИИГАиК, 2002 г. –72 стр.
- Дефектоскопист.ру [Электронный ресурс]. – Режим доступа: http://defektoskopist.ru/showthread.php?t=606
- Справочник конструктора-машиностроителя. Анурьев В. И. Издательство «Машиностроение», 2001 год. – 920 стр.
3. Огляд досліджень та розробок
3.1 Лазерний датчик РФ620
Мають діапазон вимірювання по осі Х до 150 мм (рис. 1). По висоті такі датчики мають діапазон від 100 до 350 мм. Чим менший діапазон вимірювання приладу – тим вище його точність. Швидкість сканування таких датчиків вельми висока – близько 100 сканів в секунду. За одне сканування датчик може отримати до 1024 точок.
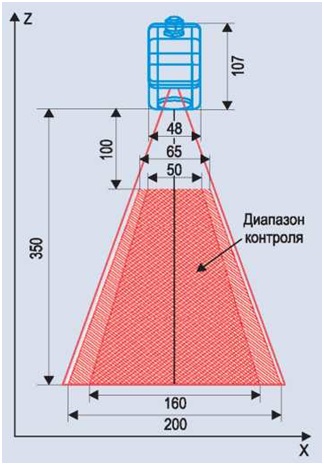
Рисунок 1 – Діапазон вимірювання растрового лазерного датчика РФ 620
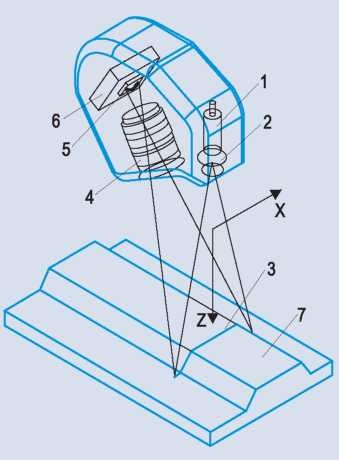
Рисунок 2 – Принцип дії растрового сканера-дальноміра
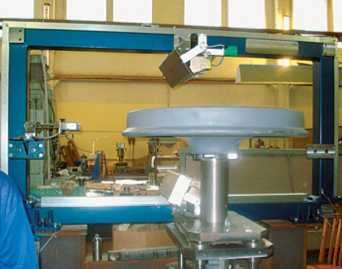
Рисунок 3 – Загальний вигляд комплексу
В основу роботи растрових сканерів-далекомірів покладено принцип оптичної тріангуляції (рис. 2).
Випромінювання напівпровідникового лазера 1 формується об’єктивом 2 у вигляді лінії 3 і проектується на об’єкт 7. Розсіяне на об’єкті випромінювання об’єктивом 4 збирається на двовимірній CMOS-матриці 5. Отримане зображення контуру об’єкта аналізується сигнальним процесором 6, який розраховує відстань до об’єкта (координата Z) для кожної з безлічі точок вздовж лазерної лінії на об’єкті (координата Х).
ЗАТ Віматек
(входить до ДП Юнітест
) розробило принципово новий комплекс для вимірювання ж.-д. коліс безконтактним методом (рис. 3).
В його основі лежить використання растрових лазерних датчиків. Установка була спроектована так, щоб уникнути всіх труднощів при контролі, описаних вище.
Механічна частина комплексу була гранично спрощена, що дозволило істотно підвищити надійність і зносостійкість обладнання.
Вимірювальна апаратура легко інтегрується в існуючу виробничу лінію. Колеса на пост контролю подаються безпосередньо з конвеєра заводу. За допомогою перекладчіка колесо встановлюється на спеціальну план-шайбу з прорізами. Здійснюється контроль. Після цього колесо знову повертається на конвеєр. Управління механічною частиною комплексу здійснюється за допомогою контролерів Siemens.
До складу комплексу входить 7 растрових лазерних датчиків (рис. 4). Три датчика розташовуються зверху, щоб вимірювати зовнішню поверхню колеса, три – знизу, вони знімають внутрішню поверхню, а сьомий датчик сканує поверхню катання. Діапазону трьох датчиків вистачає для того, щоб повністю виміряти профіль колеса по радіусу. У процесі контролю колесо обертається навколо осі установки, кут обертання вимірюється за допомогою високоточного енкодера. Таким чином, результатом вимірювань є набір профілів колеса і відповідний їм кут нахилу навколо осі обертання. Цієї інформації достатньо, щоб відновити тривимірну картину колеса.
Лазерні датчики зведені в єдину мережу, об’єднану на основі 485 інтерфейсу, по якому дані надходять на комп’ютер. Кут з енкодера, команди управління і контролю стану установки надходять на комп’ютер через інтерфейс мережевої карти. До складу комплексу входить комп’ютерна програма, яка встановлює зв’язок з контролером і датчиками. Вона отримує всі виміряні дані, аналізує їх і розраховує все необхідні характеристики колеса. По закінченні розрахунку на екран виводиться список виміряних параметрів і їх відповідність нормам ГОСТ. Результати контролю по локальній мережі передаються на сервер підприємства, де здійснюється автоматична архівація даних. За результатами вимірювання створюється протокол контролю та видається висновок про придатність колеса. Весь вимірювальний цикл займає 30 с!
Ще однією перевагою комплексу є автоматичне збереження результатів контролю в базу даних. Архівуються результати контролю, номер колеса, ПІБ дефектоскопіста, номер зміни, тощо. Є можливість здійснювати вибірку з бази даних за прізвищем дефектоскопіста, датою, номером зміни, тощо.
Комплекс вимірює наступні параметри колеса: p>
Необхідно особливо зупинитися на окремих найважливіших нюансах, які необхідно було врахувати при створенні комплексу та програмного забезпечення. Зважаючи спрощення механічної частини комплексу, колесо встановлювалося так, що його фізичний центр і центр обертання осі установки не збігаються. Більш того, площина колеса може не бути перпендикулярна площині сканування. Таким чином, всі обчислення вельми сильно ускладнилися, тому що довелося мати справу з даними в тривимірній системі координат. Наприклад, якби колесо було жорстко центровано і вирівняно на площині план-шайби, можна було б обійтися двома координатами з датчиків, енкодер був би не потрібен.
Але в цьому випадку термін експлуатації комплексу був би меншим, а час контролю більшим.
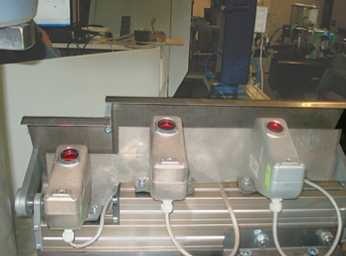
Рисунок 4 – Лінійка лазерних датчиків
Для обчислення всіх необхідних діаметрів (по колу катання, обіда з внутрішньої і зовнішньої сторін тощо) був застосований метод найменших квадратів.
Координати точок, що лежать на шуканій окружності, переводяться з циліндричної системи координат в декартову, потім проектуються на усереднену (також за методом
найменших квадратів) площину і підставляються в стандартний алгоритм апроксимації еліпсом. Тим самим відразу обчислюється середній
діаметр і еліптичність.
Для обчислення відхилення поверхні катання від теоретичного профілю була побудована аналітична функція, що задає профіль катання згідно ГОСТ 9036-88. Потім, згідно з тим же ГОСТ, функція програмно поєднувалася з бічною поверхнею обіда з внутрішньої сторони, і обчислювалися зазори по всьому периметру профілю. Виміряний і теоретичний профіль виводяться на монітор комп’ютера.
Іншим дуже важливим аспектом є калібрування і юстирування обладнання. Для того щоб отримувати коректні профілі колеса від сукупності датчиків, необхідно правильно виставити ці датчики по периметру вимірювальної лінійки. Промені сканування датчиків верхньої та нижньої лінійок повинні лежати в одній площині і мати однаковий нахил. Площина сканування повинна проходити через центр обертання установки. Це завдання було вирішене за допомогою юстувальні лазера.
Після виставлення датчиків необхідно провести калібрування, тобто визначити взаєморозташування систем координат кожного, а потім поєднати початку систем координат всіх датчиків з віссю обертання. Для калібрування був розроблений спеціальний високоточний шаблон. Він являє собою лінійку з еквідистантними насадками шириною і висотою 30 мм, розташованими на відстані 70 мм один від одного. Шаблон був виготовлений з високою точністю, всі розміри були заміряні за допомогою штангенциркуля, приладу, чия точність вище точності використовуваних датчиків. Шаблон встановлюється на вісь обертання замість колеса і сканується усіма датчиками. Таким чином, вимірявши шаблон, можна обчислити відстань від всіх датчиків до осі обертання, відстань між лінійками датчиків і взаєморозташування почав систем координат по осі Z.
Бічний датчик, який вимірює поверхню катання, може перебувати в трьох різних положеннях – залежно від діаметра колеса. Для всіх положень проводиться калібрування і зберігається на комп’ютері. При переході на інший типорозмір колеса досить завантажити файл з потрібною калібруванням.
Отже, комплекс фірми Віматек
дозволяє здійснити вимірювання геометричних параметрів колеса за 30 с, при цьому має дуже високу механічну надійність. Він є
відмінною альтернативою колишнім методам контролю розмірів коліс. У даний момент проходять пусконалагодження комплексу на Виксунському металургійному заводі [6].
3.2 Автоматизований діагностичний комплекс для контролю геометричних параметрів колісних пар вагонів КОМПЛЕКС
Призначення: виявлення на ходу поїзда зносів суцільнокатаних коліс. Передача отриманої інформації на найближчий пункт технічного обслуговування (ПТО).
Принцип дії системи заснований на лазерному безконтактному контролі геометрії рухомих тривимірних об’єктів за допомогою триангуляційних датчиків положення.
Відмінні особливості: безконтактне вимірювання геометричних параметрів колісних пар рухомого складу на ходу поїзда при швидкостях до 60 км / год в різних кліматичних умовах.
Застосування системи дозволяє підвищити надійність експлуатації рухомого складу і максимально усунути ймовірність виникнення аварійних ситуацій на залізниці, викликаних дефектами колісних пар.
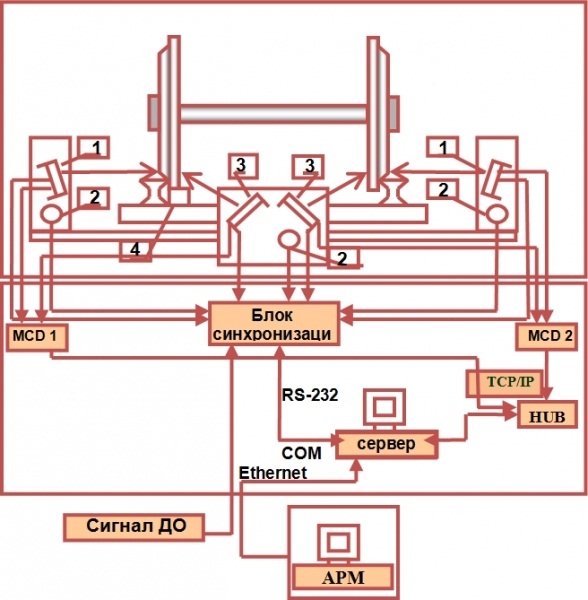
Рисунок 5 – Структурная схема системи Комплекс
3.3 Автоматизований діагностичний комплекс для контролю геометричних параметрів колісних пар вагонів КОМПЛЕКС
Призначення: виявлення на ходу поїзда зносів суцільнокатаних коліс. Передача отриманої інформації на найближчий пункт технічного обслуговування (ПТО).
Принцип дії системи заснований на лазерному безконтактному контролі геометрії рухомих тривимірних об’єктів за допомогою триангуляційних датчиків положення.
Відмінні особливості: безконтактне вимірювання геометричних параметрів колісних пар рухомого складу на ходу поїзда при швидкостях до 60 км/год в різних к ліматичних умовах.
Застосування системи дозволяє підвищити надійність експлуатації рухомого складу і максимально усунути ймовірність виникнення аварійних ситуацій на залізниці, викликаних дефектами колісних пар [1].
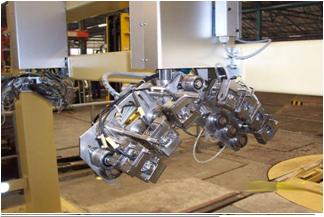
Рисунок 6 – Зовнішній вид комплекса контролю колісних пар АУРА
Конструкція і принцип дії. p>
Установка головним чином складається з трьох частин: стенду обертання КП, порталу та розміщеними на ньому сканерів коліс. Всі частини взаємопов’язані між собою за допомогою центральної системи управління.
У якості ультразвукового дефектоскопа використовується MODUS 03, а в якості вихретокового – Elotest Ms / IC. Для визначення координат дефектів від стенду обертання КП по шині Profibus в дефектоскопи надходить сигнал від датчика кута колеса.
Дефектоскопи володіють ЕОМ і можуть виконувати завдання контролю автономно і незалежно. Дефектоскопист працює за комп’ютером, який контролює як дефектоскопи, так і систему управління стендом (PLC). У керуючому комп’ютері вибирається програма (обсяг) контролю, за допомогою керуючого ПК ведеться контроль за процесом дефектоскопії, тут же зберігаються результати контролю, проводиться їх обробка та візуалізація. У завершення контролю дані зберігаються в банку даних і роздруковуються протоколи. Незважаючи на наявність різних дефектоскопів (УЗ, ВТ), дефектоскопист працює з однієї універсальної інтерфейсної програмою.
Банк даних має багатоступеневу систему доступу так, що звичайний оператор не може змінити/скорегувати результати контролю. Копія банку даних резервується на DVD-диску. Опціонально можлива зв’язка банку даних установки з банком даних депо, дороги [4].
4. Вибір методу
З наведених прикладів розробок можна зробити висновок, що при використанні в якості датчиків оптичних приладів ми отримуємо більш швидкий час сканування, що є дуже важливим фактором. Так само слід зазначити що оптичні датчики забезпечать необхідну точність при вирішенні даної задачі. Оскільки у виробництві швидкість відіграє дуже важливу роль, то для вирішення поставленого завдання було прийнято рішення використовувати саме оптичний метод.
При написанні даного реферату магістерська робота ще не завершена. Остаточне завершення: грудень 2015 року. Повний текст роботи та матеріали по темі можуть бути отримані у автора або його керівника після вказаної дати.