Реферат по теме выпускной работы
Содержание
- Введение
- 1. Задачи технического диагностирования
- 2. Функции и параметры диагностирования
- 3. Методы диагностирования
- 3.1 Органолептический метод диагностирования
- 3.2 Вибрационный метод диагностирования
- 3.3 Акустический метод диагностирования
- 3.4 Тепловой метод
- 3.5 Трибодиагностический метод
- 3.6 Диагностика на основе анализа продуктов износа в продуктах сгорания
- 3.7 Метод акустической эмиссии
- 3.8 Радиографический метод
- 3.9 Магнитопорошковый метод контроля
- 3.10 Вихретоковый метод диагностирования
- 3.11 Ультразвуковой метод диагностирования
- 3.12 Капиллярный метод диагностирования
- 4. Диагностика состояния электрооборудования электростанций и подстанций с помощью средств инфракрасной техники на практике
- 5. Проблемы технической диагностики
- Выводы
- Список источников
Введение
Диагностика электрооборудования занимает все более важное место в современной электроэнергетической отрасли Украины и России, что диктуется, прежде всего, необходимостью продления срока службы или интервала времени безаварийной работы силового электрооборудования. Износ основных фондов электроэнергетики давно уже перевалил за 50%. В настоящее время отрасль не располагает ни финансовыми, ни техническими возможностями в кратчайшие сроки заменить оборудование, которое исчерпало свой нормативный ресурс. Ежегодный прирост парка электрооборудования со сверхнормативным сроком службы значительно превышает прирост вновь вводимого оборудования, ввиду этого использование системы планово-предупредительных ремонтов для поддержания необходимой эксплуатационной готовности оборудования становится все более затруднительным. К переходу к ремонту в зависимости от фактического состояния подталкивает бурное развитие средств и методов технической диагностики.
В электроэнергетической отрасли назрела проблема создания системы технической диагностики, которая позволила бы решить проблему организации ремонтов электрооборудования в соответствии с его состоянием. Кроме того, необходимость повышения эксплуатационной безотказности работающего электрооборудования, в сложившихся условиях, за счет выявления дефектов, прогнозирования их развития, представляется актуальной задачей [1].
В качестве фундамента для построения эффективной системы диагностирования должны применяться такие средства и методы диагностики, которые обладают достаточно высокой информативностью, техническим и нормативным обеспечением, а также имеют гибкую методологическую базу принятия решений. Наряду с традиционными методами контроля, за последнее десятилетие, нашли применение современные высокоэффективные способы диагностики, обеспечивающие выявление дефектов электрооборудования на ранней стадии их развития и позволяющие контролировать достаточно широкий перечень параметров.
1. Задачи технического диагностирования
В настоящее время на современных отечественных и зарубежных электростанциях, подстанциях и в электрических сетях эксплуатируется значительное количество изношенного электрооборудования. Например, в США по состоянию на 1997г. около 65% силовых трансформаторов отработали более 25 лет, в России износ основных фондов электроэнергетики составляет около 50% [2,3]. По состоянию на конец 2005 г. средний срок эксплуатации электрооборудования Украины уже превышает половину проектного, что приводит к снижению надежности его функционирования, возрастанию аварийности.
Существующая в отечественной электроэнергетике система планово-предупредительных ремонтов электрооборудования [2,3] не всегда оправдана, так как она не учитывает его реальное техническое состояние, и часто требует вывода из работы работоспособного оборудования.
Поэтому возникает необходимость разработки новых технологий и практических методов, обеспечивающих эффективное техническое обслуживание и ремонт электрооборудования по техническому состоянию. Это в свою очередь предопределяет развитие существующих методов и средств контроля для получения диагностической информации, разработки математических моделей и алгоритмов оценки технического состояния электрооборудования, составляющих основу экспертной системы принятия решений [2,4].
В общем случае экспертная система оценки технического состояния электрооборудования определяет следующее: находится ли оборудование в нормальном состоянии, не требующем какого-либо вмешательства; требуется ли дополнительное внимание со стороны персонала или учащенный контроль параметров оборудования; необходимо ли выполнение дополнительных измерений, испытаний и других профилактических мероприятий с отключением и без отключения; требуется ли проведение ремонтов, модернизации, облегчение режимов работы или вывод электрооборудования из работы.
Для оценки технического состояния электрооборудования можно использовать автоматический классификатор, построенный на основе нечетких алгоритмов и позволяющий на основе параметров состояния отнести объект диагностирования к одному из классов технического состояния [4].
Состояние силового электрооборудования характеризуется большим количеством параметров состояния (признаков), значения которых можно получить используя штатные средства измерения или же путем проведения дополнительных испытаний на работающем или отключенном оборудовании. При большом числе параметров состояния, построение нечеткой базы знаний экспертной системы становится трудновыполнимой задачей.
2. Функции и параметры диагностирования
Диагностика технического состояния электрооборудования может осуществляться как специальными приборами, которыми производятся прямые измерения электрических параметров контролируемых объектов традиционными методами, так и приборами для измерения косвенных характеристик электрооборудования, например температуры поверхности, на бесконтактном измерении который основан тепловой неразрушающий контроль – тепловизионная диагностика, но все процессы диагностирования технических объектов включает в себя следующие функции:
- оценка технического состояния объекта;
- обнаружение и определение места локализации неисправностей;
- прогнозирование остаточного ресурса объекта;
- мониторинг технического состояния объекта.
Под диагностическими параметрами понимают репрезентативные параметры, по которым можно судить о состоянии объекта. Различают прямые и косвенные диагностические параметры. Первые непосредственно характеризуют состояние объекта, а вторые связаны с прямыми параметрами функциональной зависимостью [4].
При функциональной диагностике объекта в процессе его работы – наряду с отдельно рассматриваемыми параметрами – могут использоваться также как признак состояния функциональные связи (функциональные зависимости) параметров.
3. Методы диагностирования
В зависимости от технических средств и диагностических параметров, которые используют при проведении диагностирования, можно составить следующий неполный список методов диагностирования:
- органолептические методы диагностирования;
- вибрационные методы диагностирования;
- акустические методы диагностирования;
- тепловые методы;
- трибодиагностика;
- диагностика на основе анализа продуктов износа в продуктах сгорания;
- метод акустической эмиссии;
- радиография;
- магнитопорошковый метод;
- вихретоковый метод;
- ультразвуковой контроль;
- капиллярный контроль;
- методы параметрической диагностики;
- электродиагностический контроль. Сфера применения – электродвигатели, электромагнитные клапаны, катушки, кабели, трансформаторы. Различают статические и динамические испытания электроагрегатов;
- специфические методы для каждой из областей техники (например, при диагностировании гидропривода широко применяется статопараметрический метод, основанный на анализе задросселированного потока жидкости; в электротехнике применяют методы, основанные на анализе параметров электрических сигналов, в сложных многокомпонентных системах применяют методы диагностирования по стохастическим отклонениям параметров от их осредненных значений и т. д.).
Рассмотрим более подробно все методы диагностирования.
3.1 Органолептический метод диагностирования
Органолептические методы диагностирования основаны на использовании органов чувств человека (осмотр, ослушивание).
Визуальный осмотр, контроль температуры и визуализация механических колебаний входят в список органолептических методов диагностирования и контроля работы оборудования. Они являются достаточно эффективными и не требуют материальных затрат, так как в роли диагностического «прибора» в данном случае выступает человек.
Контроль температуры является важным аспектом оценки технического состояния механического оборудования. До 95% всех форм энергии, создаваемой и передаваемой машинами прямо или частично, превращается в тепловую энергию. Параметром теплового диагностирования является температура, отражающая протекание рабочего процесса и развитие целого ряда неисправностей.
Температура нагрева корпусов механизмов как диагностический параметр имеет две особенности: появление некоторых видов неисправностей вызывает повышение температуры корпуса механизма; инерционность нагрева металлических деталей, корпусов и опор не позволяет использовать данный параметр для определения внезапных отказов и зарождающихся повреждений. Правила технической эксплуатации регламентируют предельную температуру корпусов подшипников, которая не должна превышать температуру окружающей среды более чем на 40°С и быть не выше 60-80°С. Для некоторых механизмов, имеющих циркуляционную систему смазки или охлаждения, оценивают разницу температур масла или воды на выходе и входе. Это позволяет контролировать тепловые процессы, общее состояние оборудования, а также степень его ухудшения. Обычно разница температур на выходе и входе не должна превышать 5-10°С.
3.2 Вибрационный метод диагностирования
Вибрационные методы диагностирования основаны на анализе параметров вибраций технических объектов.
Вибрационная диагностика – метод диагностирования технических систем и оборудования, основанный на анализе параметров вибрации, либо создаваемой работающим оборудованием, либо являющейся вторичной вибрацией, обусловленной структурой исследуемого объекта.
Вибрационная диагностика, как и другие методы технической диагностики, решает задачи поиска неисправностей и оценки технического состояния исследуемого объекта.
При вибрационной диагностике как правило исследуются временной сигнал или спектр вибрации того или иного оборудования. Также применяется кепстральный анализ (кепстр – анаграмма слова спектр).
При вибрационной диагностике анализируются виброскорость, виброперемещение, виброускорение [6].
В качестве диагностических параметров могут выступать следующие:
- ПИК – максимальное значение сигнала на рассматриваемом интервале времени;
- СКЗ – среднее квадратическое значение (действующее значение) сигнала для рассматриваемой полосы частот;
- ПИК-фактор – отношение параметра ПИК к СКЗ;
- ПИК-ПИК – (Размах) разница между максимальным и минимальным значением сигнала на рассматриваемом интервале времени;
- SPM – метод ударных импульсов, основанный на использовании специального датчика с резонансной частотой 32 кГц и алгоритма обработки ударных волн малой энергии, генерируемых подшипниками качения вследствие соударений и изменений давления в зоне качения этих подшипников (Эдвин Сёхль, SPM Instrument, Швеция, 1968г.);
- EVAM – Аббревиатура EVAM является сокращением от
Evaluated Vibration Analysis Method
, что в переводе означает «Метод анализа вибрации с оценкой состояния». Метод EVAM® объединяет в себе различные общепризнанные методики анализа вибросигналов вместе с программными средствами практической оценки состояния оборудования на основе результатов такого анализа. Поддерживается программно и аппаратно, как и метод SPM, оборудованием и ПО производства фирмы SPM Instrument AB (Швеция); - SPM-M: пик-фактор на резонансной частоте акселерометра (ООО Бифор) (1980г.);
- RPF: пик-фактор высших частот вибрации механизмов (1982г.);
- VСС – контроль степени кондиции смазки (1995г.);
- ARP: распределение амплитуд импульсов сухого трения в узлах машин (2001г.);
- Entropy – вибрационно-энтропийная оценка состояния узлов машин (2002г.).
Из датчиков вибрации наиболее часто применяются акселерометры (вибропреобразователи ускорения) пьезоэлектрические датчики.
Наибольшее развитие метод получил при диагностировании подшипников качения. Также вибрационный метод успешно применяется при виброиспытании изделий и диагностике колёсно-редукторных блоков на железнодорожном транспорте.
Заслуживают внимания виброакустические методы поиска утечек газа и в гидрооборудовании. Суть этих методов заключается в следующем. Жидкость или газ, дросселируя через щели и зазоры, создаёт турбулентность, сопровождающуюся пульсациями давления, и, как следствие, в спектре вибраций и шума появляются гармоники соответствующих частот. Анализируя амплитуду этих гармоник, можно судить о наличии (отсутствии) течей [7].
Интенсивное развитие метода в последние годы связано с удешевлением электронных вычислительных средств и упрощением анализа вибрационных сигналов [8].
Преимущества метода:
- метод позволяет находить скрытые дефекты;
- метод, как правило, не требует сборки-разборки оборудования;
- малое время диагностирования;
- возможность обнаружения неисправностей на этапе их зарождения;
- снижение ожидаемого риска возникновения аварийной ситуации при эксплуатации оборудования.
Недостатки:
- особые требования к способу крепления датчика вибрации;
- зависимость параметров вибрации от большого количества факторов и сложность выделения вибрационного сигнала обусловленного наличием неисправности, что требует глубокого применения методов корреляционного и регрессионного анализа;
- точность диагностирования в большинстве случаев зависит от числа сглаженных (осреднённых) параметров, например, числа оценок SPM.
3.3 Акустический метод диагностирования
Из датчиков сигналов (частичных разрядов) ЧР (электрические, электромагнитные, акустические) большое применение получили акустические. Акустический метод диагностирования, основанный на анализе параметров звуковых волн, генерируемых техническими объектами и их составными частями.
Электрические датчики способны дать приближенную локализацию источника сигналов ЧР, основанную только на сравнении интенсивностей сигналов в различных точках оборудования (трансформатора). Для локализации дефекта обычно используют акустические датчики, которые хотя и имеют значительно меньшую чувствительность, но, благодаря сравнительно низкой скорости распространения акустических сигналов (время прохождения звуковой волны значительно больше, чем длительность электрического импульса), позволяют провести довольно точную локализацию источника сигналов внутри трансформатора (в пространстве). Акустические датчики практически не подвержены внешним помехам на подстанции. Измерение сигналов ЧР в реальных условиях эксплуатации хотя и сталкивается с определенными трудностями, но является вполне решаемой задачей. В настоящее время успешно испытана на силовом оборудовании подстанций практически всех классов напряжений и мощностей система СКИ-2. Она использовалась как при однократных измерениях, так и в режиме непрерывного автоматического мониторинга. Аппаратура надежно регистрирует сигналы ЧР с уровнями 50-500 пКл даже в условиях очень сильных помех высокой интенсивности с амплитудой, достигающей 15 пКл. В России освоен комплект для акустического определения уровня частичных разрядов на базе акустического приемника LDA 5/S компании Intereng Messtechnik
. С помощью его определяются места частичных разрядов в трансформаторах, выключателях, преобразователях тока и напряжения. Лучшие результаты диагностирования можно получить при использовании метода ЧР и дефектоскопа «Филин-6».
3.4 Тепловой метод
Метод инфракрасной термографии. Потери электрической энергии на нагрев элементов и узлов электрооборудования в процессе эксплуатации зависят от их технического состояния. К тепловому методу так же относится метод диагностирования, основанный на использовании тепловизоров.
Измеряя инфракрасное излучение, обусловленное нагревом, можно сделать выводы о техническом состоянии электрооборудования. Невидимое инфракрасное излучение с помощью тепловизоров преобразуется в видимый человеком сигнал. Данный метод дистанционный, чувствительный, позволяющий регистрировать изменения температуры в доли градуса. Поэтому его показания сильно подвержены влияющим факторам, например, отражающей способности объекта измерения, температуре и состоянию окружающей среды, так как запыленность и влажность поглощают инфракрасное излучение, и др.
3.5 Трибодиагностический метод
Трибодиагностика – анализ состава масла (продуктов износа, окисления и загрязнения сторонними веществами). Это один из самых эффективных методов диагностики состояния трущихся деталей механизмов. Трибодиагностика применительно к машинному оборудованию представляет собой оценку его технического состояния по составу и концентрации продуктов износа в рабочем масле с помощью специальных приборов и оборудования (анализаторов масла, атомно-эмиссионных и ИК спектрометров, рентгено-флюорисцентных анализаторов и т.д.). Анализ проб масла на данном оборудовании позволяет определить концентрацию в нем того или иного элемента, из которого сделаны детали механизма, подвергающиеся трению. Зная эту величину, определяют усредненный износ соответствующей детали и делают вывод о необходимости проведения ремонтных работ.
Трибодиагностика – это перспективный превентивный метод оценки состояния машинного оборудования, дающий достоверные данные о его рабочем состоянии и степени износа. Однако на сегодняшний день данный метод не получил широкого распространения в промышленности. Трибодиагностика в качестве повседневной практики пока используется только для обслуживания газотурбинных двигателей. Но перспективно ее применение для оценки работоспособности подшипников качения и других узлов машин.
3.6 Диагностика на основе анализа продуктов износа в продуктах сгорания
Известно, что разрушение деталей проточной части ГПА, вызываемое перегревом, газовой коррозией, абразивным износом, сопровождается выносом из ГПА вместе с газовым потоком мельчайших частиц металла. Начало разрушения и его характер, можно определить, регистрируя наличие продуктов износа и их состав. Отсюда рассматриваемый метод аналогичен методу диагностики по анализу продуктов износа в масле. Решение этой задачи основано на применении импульсного метода с лазерным источником для определения концентрации в газовом турбулентном потоке. Экспериментально показано, что метод позволяет проводить мгновенные (в течение 10-14 с) и одновременные измерения локальных концентраций в смесях в многоатомных газах. Определение состава и концентрации продуктов износа проводят в процессе анализа состава проб продуктов сгорания, взятых из выхлопного тракта ГПА. Недостаток данного метода связан с его трудоемкостью и дискретностью контроля технического состояния. Перспективность же его связана с тем, что этот метод представляется весьма эффективным для диагностирования такого важного узла, как камера сгорания ГПА, в настоящее время наименее охваченного диагностированием.
3.7 Метод акустической эмиссии
Для контроля широко применяются все виды и диапазоны излучения. Метод акустической эмиссии работает в звуковом диапазоне. Известен метод контроля оптического излучения ПР с помощью электронно-оптического дефектоскопа. Он основан на регистрации пространственно временного распределения яркости свечения и определении по ее характеру дефектных изоляторов. Для этих же целей с разной эффективностью применяют радиотехнический и ультразвуковой методы, а также метод контроля ультрафиолетового излучения с помощью электронно-оптического дефектоскопа «Филин».
3.8 Радиографический метод
Контроль основан на проникании гамма и рентгеновских лучей сквозь материалы, метод широко применяется в неразрушающем контроле. Используется для определения внутренних дефектов в металле и оборудовании.
С помощью радиографических методов проверки распределительного устройства на наличие износа и дефектов компания ABB сэкономила американскому заказчику 38 суток простоя, требовавшихся на профилактическое обслуживание 26 автоматических выключателей, причем расходы на эту проверку составили менее половины обычной стоимости подобного техобслуживания. Например, при проверке автоматов на напряжение 35-145 кВ обычным методом требуется два дня, а радиографическая дефектоскопия позволяет выполнить эту работу за два часа. Если же взять автоматический выключатель на 550 кВ, то потребуется соответственно пять суток и четыре часа. Основным преимуществом радиографии является возможность оставить элегаз в распределительном устройстве, а не откачивать его, как это имеет место при обычной проверке.
3.9 Магнитопорошковый метод контроля
Магнитопорошковый метод – один из самых распространённых, надёжных и производительных методов неразрушающего контроля поверхностей изделий из ферромагнитных материалов в их производстве и эксплуатации.
МПК - один из четырех классических методов неразрушающего контроля, а также один из наиболее старых методов НК, связанных с применением приборов и дефектоскопических материалов для НК. Первые опыты описали феномен полей магнитного рассеяния и объяснили их значение. Впоследствии были предприняты попытки найти применение этому явлению и ввести его в техническую практику. В 1868 году англичанин Саксби применил компас для определения дефектов в пушечных стволах. В 1917 году американец Хок применил железные опилки для обнаружения трещин в стальных деталях.
Суть метода такова: магнитный поток в бездефектной части изделия не меняет своего направления; если же на пути его встречаются участки с пониженной магнитной проницаемостью, например, дефекты в виде разрыва сплошности металла (трещины, неметаллические включения и т.д.), то часть силовых линий магнитного поля выходит из детали наружу и входит в нее обратно, при этом возникают местные магнитные полюсы (N и S) и, как следствие, магнитное поле над дефектом. Так как магнитное поле над дефектом неоднородно, то на магнитные частицы, попавшие в это поле, действует сила, стремящаяся затянуть частицы в место наибольшей концентрации магнитных силовых линий, то есть к дефекту. Частицы в области поля дефекта намагничиваются и притягиваются друг к другу как магнитные диполи под действием силы так, что образуют цепочные структуры, ориентированные по магнитным силовым линиям поля.
Метод магнитопорошкового контроля предназначен для выявления тонких поверхностных и подповерхностных нарушений сплошности металла – дефектов, распространяющихся вглубь изделий. Такими дефектами могут быть трещины, волосовины надрывы, флокены, непровары, поры. Наибольшая вероятность выявления дефектов достигается в случае, когда плоскость дефекта составляет угол 90° с направлением намагничивающего поля (магнитного потока). С уменьшением этого угла чувствительность снижается и при углах, существенно меньших 90° дефекты могут быть не обнаружены.
3.10 Вихретоковый метод диагностирования
Вихретоковый метод основан на анализе взаимодействия внешнего электромагнитного поля с электромагнитным полем вихревых токов, наводимых возбуждающей катушкой в электропроводящем объекте контроля. Вихретоковый метод позволяет обнаруживать дефекты типа несплошностей, выходящих на поверхность или залегающих на небольшой глубине, а также трещины, расслоения, неметаллические включения и т.д.
Вихретоковый контроль находит применение для анализа электропроводящих материалов: металлы, полупроводники, графит, сплавы, а также неферромагнетики. Применяется, в основном, для поиска трещин и коррозионного растрескивания под напряжением (КРН) на газонефтепроводах.
3.11 Ультразвуковой метод диагностирования
Ультразвуковой контроль также наиболее распространенный метод, этот метод можно разделить на ультразвуковую дефектоскопию (УЗД) и ультразвуковою толщинометрию (УЗТ). Ультразвуковая дефектоскопия используется, как правило, для контроля сварных швов и основного металла оборудования с целью поиска различных дефектов как подповерхностных, так и внутренних. Используемая частота 2,5 или 5 МГц. Ультразвуковая толщинометрия используется для измерения толщины ферромагнитных материалов с помощью ультразвуковых волн. Существует также метод длинноволновой волны, но он действует на ограниченной дистанции и широкого применения не имеет.
3.12 Капиллярный метод диагностирования
Капиллярные методы контроля предназначены для обнаружения поверхностных дефектов в объектах контроля. Они основаны на капиллярном проникновении индикаторных жидкостей (пенетрантов) в полости дефектов материала объекта контроля и регистрации образующихся индикаторных рисунков.
Капиллярный метод основан на искусственном повышении свето- и цветоконтрастности дефектов относительно неповрежденного участка. Методы капиллярной дефектоскопии позволяют обнаруживать невооруженным глазом тонкие поверхностные трещины и другие несплошности материала, образующиеся при изготовлении и эксплуатации различных объектов.
4. Диагностика состояния электрооборудования электростанций и подстанций с помощью средств инфракрасной техники на практике
Оценка фактического состояния силового электрооборудования по результатам диагностических измерений – очень сложная и актуальная задача. Значительная часть электрического оборудования станций, подстанций, системы передачи и распределения электроэнергии выработала свой ресурс, но продолжает эксплуатироваться, так как на его замену требуются большие финансовые средства. В связи с этим с каждым годом возрастают затраты на проведение комплексных обследований и диагностики.
В последние десятилетия большое распространение получают методы контроля параметров силовых трансформаторов под рабочим напряжением. К методам непрерывного контроля и измеряемым on-line
параметрам силовых трансформаторов, которые могут быть реализованы в системах мониторинга, можно отнести контроль величины tgδ изоляции вводов; измерение температуры верхних слоев масла, тока нагрузки, напряжения с ПИН вводов, давления масла во вводе, влагосодержания масла, содержания растворенных в масле газов с помощью специальных датчиков; измерение уровня ви брации с целью оценки состояния запрессовки обмоток, состояния магнитопровода, системы охлаждения; мониторинг уровня частичных разрядов (ЧР) в изоляции вводов и обмоток и др. Вышеперечисленные методы имеют различную степень достоверности и информативности.
Метод тепловизионного контроля с помощью средств инфракрасной диагностики и хроматографический анализ газов, растворенных в трансформаторном масле (ХАРГ), выполняемые в соответствии с руководящими документами «Объем и нормы испытаний электрооборудования» (ОНИЭ), позволяют выявить целый ряд различных дефектов высоковольтного электрооборудования (ЭО). О тепловидении и его применении для контроля состояния электрооборудования известно несколько десятков лет [11, 12]. Тепловизионный контроль является одним из основных направлений развития высокоэффективной системы технической диагностики, которая обеспечивает возможность контроля теплового состояния оборудования и сооружений без вывода их из работы, выявления дефектов на ранней стадии развития, сокращения затрат на техническое обследование за счет прогнозирования сроков и объема ремонтных работ [13]. Тепловизионный контроль проводится для выяснения теплового состояния разъединителей, трансформаторов тока (ТТ) и напряжения (ТН), разрядников и ограничителей перенапряжения (ОПН), конденсаторов связи, масляных и воздушных выключателей, ошиновки распределительных устройств (РУ), качества пайки обмоток статора турбогенераторов при ремонтных работах, высоковольтных вводов силовых трансформаторов, систем охлаждения трансформаторов, электродвигателей, генераторов и др. Ведется также контроль состояния дымовых труб и газоходов на тепловых электростанциях, обнаружение мест присосов холодного воздуха и т.д. В энергосистеме Самараэнерго
тепловизионный контроль проводился с помощью средств инфракрасной техники типа
INFRAMETRIKS-740
и «Иртис». В [13] затронуты вопросы применения тепловизионных приемников для выявления дефектных паек соединительных головок стержней обмотки статора турбогенераторов (ТГ) в процессе эксплуатации. В данном разделе рассмотрены вопросы использования тепловизионных приемников как средства контроля качества пайки соединительных головок стержней статорных обмоток ТГ с применением твердых припоев при их ремонтах. Тепловизионный контроль проводится при открытых лобовых частях обмотки статора с выведенным ротором и предварительным нагревом от источника постоянного тока (например, резервного возбудителя) током величиной порядка 1000 А. При этом, необходимым условием эффективности обследования головок стержней обмотки статора является наличие превышения температуры обмотки генератора над температурой окружающей среды турбинного цеха.
Следует отметить следующий важный момент: для обеспечения возможности сопоставления результатов измерений величины избыточной температуры T, выполненных на ТГ различных типов и мощностей, необходимо выполнение требования по обеспечению одинаковой плотности тока в прогреваемой обмотке. Однако в рассмотренных в статье случаях ремонта ТГ этот параметр не контролировался. При дальнейших ремонтах ТГ это предполагается делать. Кроме тепловизионного контроля, существует и применяется для контроля паек гидрогенераторов (сотни головок) токовихревой метод, но в данной статье он не рассматривается.
Максимальное отличие величины сопротивления постоянному току между ветвями обмотки статора ТГ не должно превышать 5%, а отклонение от паспортного значения не более 2% [11]. Турбогенератор ТГ-6 Тольяттинской ТЭЦ типа ТВФ-60-2, (год выпуска 1967, капремонт с полной перемоткой обмоток 1991 г.) находился в длительном резерве. Результаты измерения сопротивления постоянному току обмоток статора показали, что максимальное отличие ΔRmax междуветвями составило 6,8% (между ветвями А1 и А2 фазы А). Таким образом, ΔRmax между ветвями А1 и А2 фазы А превышало допустимый ОНИЭ уровень в 5%. Тепловизионное обследование лобовых частей обмотки статора 17.03.2000 г. показало повышенный нагрев мест паек в семи точках с избыточной температурой ΔT в диапазоне от 4,1 до 6,6°С по сравнению с соседними «холодными» (реперными) точками (рис. 1, 2). Из семи точек две точки приходятся на ветвь А2 фазы А, которая имеет повышенное омическое сопротивление ΔRmax = 6,8% (между ветвями) (рис. 1).
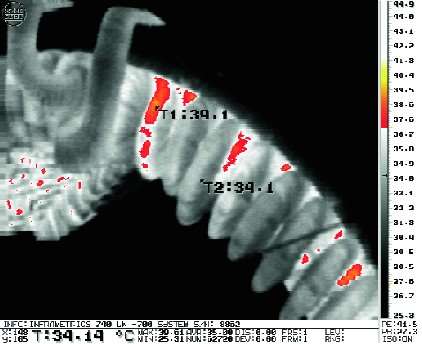
Рисунок 1 – Термограмма 17.03.2000 г. Генератора 6 ГТ То ТЭЦ. Вид со стороны возбудителя в районе 1-го часа (до 1-й перепайки), ΔT= 5°С (Rmax=6,8% между ветвями А1 и А2 фазы А)
На основании этих результатов проведена перепайка стержней ветви А2 фазы А обмотки статора ТГ в точках, указанных на рис. 1 и 2. ΔRmax между ветвями А1 и А2 фазы А составило 5,07 %. После 1-й перепайки отмечено снижение омического сопротивления ΔR на фазе А на 1,8 %. ΔRmax между ветвями А1 и А2 фазы А по-прежнему превышало допустимый ОНИЭ уровень в 5%.
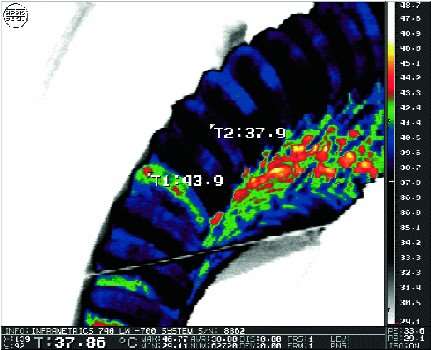
Рисунок 2 - Термограмма 17.03.2000 г. Генератора 6 ГТ То ТЭЦ. Вид со стороны турбины в районе 11-ти часов (до 1-й перепайки), ΔT = 6°С (Rmax = 6,8 % между ветвями А1 и А2 фазы А)
Повторное тепловизионное обследование 30.03.2000 г. показало повышенный нагрев двух головок в ветви А2, имеющей максимальное отклонение ΔRmax. Избыточная температура ΔT в районе этих двух точек составила от 5 до 7,6°С (рис. 3, 4). То есть, было обнаружено, что тепловое состояние головки ветви А2 на рис. 3 (до 1-й пайки на рис. 4.1), а соответственно и качество ее пайки, ухудшилось.
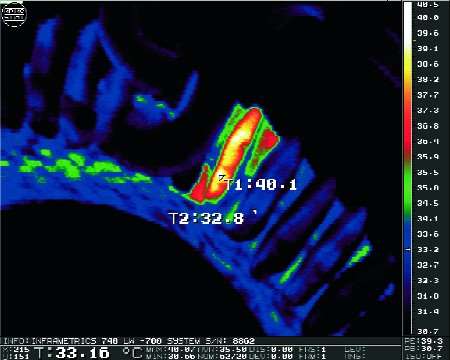
Рисунок 3 - Термограмма 30.03.2000 г. Генератора 6 ГТ То ТЭЦ. Вид со стороны возбудителя в районе 1-го часа (после 1-й перепайки), ΔT = 7,6°С (ΔRmax=5,07% между ветвями А1 и А2 фазы А)
Поэтому 3.04.2000 г. проведена перепайка двух соединительных головок в ветви А2 фазы А (см. рис. 3, 4). Обнаружен дефект пайки головки ветви А2 (см. рис. 4.3). Далее ΔRmax между ветвями А1 и А2 уменьшилось и составило 4,4%, что соответствует допустимым нормам по ОНИЭ [11].
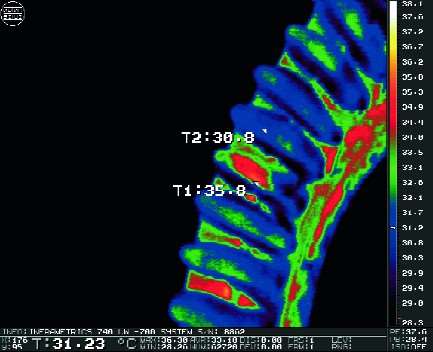
Рисунок 4 - Термограмма 30.03.2000 г. Генератора 6 ГТ То ТЭЦ. Вид со стороны турбины в районе 10-ти часов (после 1-й перепайки), ΔT=5°С (ΔRmax=5,07% между ветвями А1 и А2 фазы А)
Турбогенератор ТГ-4 ТЭЦ ВАЗ типа ТВФ-120-2 (год выпуска 1970) отключился от сети действием поперечной дифференциальной защиты генератора. Причиной срабатывания защиты явилось нарушение пайки соединительной головки ветви С2 фазы С обмотки статора (обрыв ветви). Предыдущее измерение сопротивления постоянному току обмоток статора показало, что максимальное отличие ΔRmax между ветвями составляет 3,49% . Максимальное отклонение от заводских данных составляло 2,2 % на ветви С2. После перепайки обмотки статора 3.03.2000 г. было проведено тепловизионное обследование состояния качества паек головок стержней обмотки статора. Результаты измерений указали на повышенный нагрев мест паек на ветви С2 в точках с ΔT в диапазоне от 3,6 до 3,9°С (рис. 5, 6). После перепайки максимальное отличие ΔRmax между ветвями составило 3,1 % , от заводских данных – 1,8% на ветви С1, что соответствует допустимым нормам по ОНИЭ [11]. По результатам тепловизионного обследования ТГ-6 ТоТЭЦ, ТГ-4 ТЭЦ ВАЗ и ТГ-2 Сызранской ТЭЦ была построена зависимость максимального отличия по сопротивлению постоянному току обмоток статора ΔRmax (между ветвями в %) от величины избыточной температуры ΔT (рис. 4.7). На рис. 7 выделена также пороговая граница в 5% для отклонения ?Rmax по ОНИЭ. Рассмотрение этой зависимости ΔRmax от ΔT позволило сделать вывод о величине порогового значения ΔT = 4-5°С, при превышении которого возможно наличие дефекта в пайке соединительных головок стержней обмотки статора турбогенераторов (ТГ) в процессе эксплуатации.Однако этот график носит приблизительный характер и нуждается в дальнейшем уточнении по мере накопления опыта тепловизионного контроля и статистических данных измерений. Пороговый критерий ΔT = 4-5 oС не является окончательным и будет уточняться.
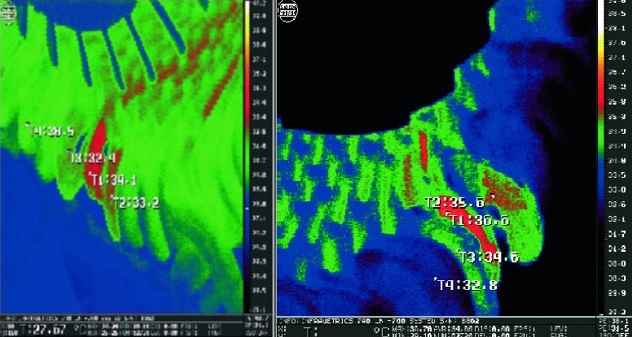
Рисунок 5, 6 - Термограммы 3.03.2000 г. генератора ТГ-4 ТЭЦ ВАЗа. Лобовая часть со стороны возбудителя T= 3,6-3,9°С (ΔRmax= 3,1% между ветвями)
Турбогенератор ТГ2-25-2 Сызранской ТЭЦ (год выпуска 1956) обследовался во время капитального ремонта при помощи тепловизионного контроля при открытых лобовых частях обмотки статора с выведенным ротором и предварительным нагревом от резервного возбудителя постоянным током величиной порядка 600 А. В ходе капитального ремонта проводилась полная перемотка обмотки статора турбогенератора; перепайка дефектных соединительных головок стержней проводилась с использованием циркониевого припоя марки ПМФОЦр 6-4-0,03.
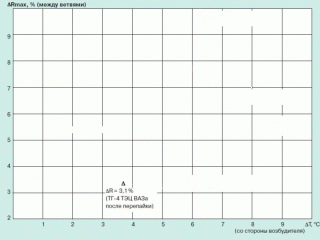
Рисунок 7 - Зависимость максимального отличия по сопротивлению постоянному току обмоток статора ΔRmax (между ветвями, в %) от величины избыточной температуры T (по сравнению с соседними «холодными» (реперными) точками. Вид со стороны возбудителя, ТГ ТЭЦ ВАЗа, ТоТЭЦ, СТЭЦ)(анимация: 6 кадров, 8 циклов повторений, 351 килобайт)
При первичном тепловизионном обследовании 27.10.2004 г. на термограмме со стороны возбудителя обнаружено превышение температуры дефектных головок стержней (точки №№ 1-7, 10) над температурой соседних «холодных» точек ΔT = от 3,1°С до 6,2°С при разнице величины омического сопротивления ΔRmax = 15% между фазами, что значительно превышает норму, указанную в ОНИЭ (рис. 8). После серии последовательных перепаек дефектных головок стержней обмотки статора турбогенератора 27.10, 28.10 и 29.10.2004 г. разница величин омического сопротивления ΔRомич. между фазами снизилась вначале с ΔRmax = 15 % до 7,6 %, а затем до 4,2 %.
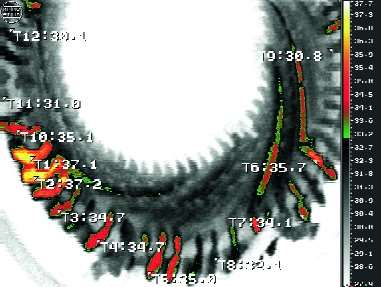
Рисунок 8 – Термограмма 27.10.04 г. турбогенератора типа ТГ2-25-2 Сызранской ТЭЦ, год выпуска 1956. Вид со стороны возбудителя, дефектные пайки головок стержней – точки № 1, № 2, № 3, № 4, № 5, №6, № 7, №10 (ΔT от 3,1°С до 6,2°С, ΔRомич. = 15 %)
Электрическая схема расположения фаз в обмотке статора турбогенератора (вид со стороны возбудителя) показана на рис. 9.
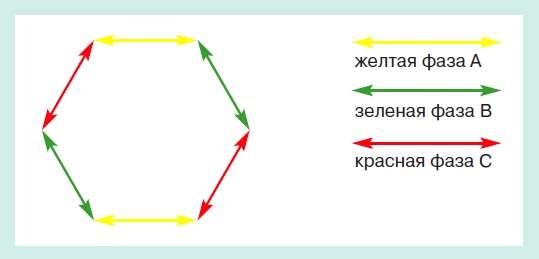
Рисунок 9 – Расположение фаз в обмотке статора
Тепловизионное обследование 29.10.2004 г. после очередной перепайки показало, что на термограмме, вид со стороны возбудителя, количество дефектных паек головок стержней уменьшилось с 8 до 2 – точки № 1, № 5 и ΔT составила от 3,3°С до 5,5°С при ΔRомич. = 3,2 % (рис. 10.). Это демонстрирует эффективность применения тепловизионного контроля качества пайки соединительных головок стержней статорных обмоток турбогенераторов в качестве инструмента последовательной оценки качества паек [14-16].
Тепловидение позволяет выявлять аварийные дефекты технического электрооборудования (ЭО) подстанций с сильными нагревами и значительными перепадами температур по сравнению с температурой окружающей среды (максимальная в данной статье ΔT=116°С). Кроме аварийных, в ходе тепловизионного обследования обнаруживаются нагревы болтовых соединений шинных и линейных разъединителей, которые могут устраняться по мере возможности отключений.
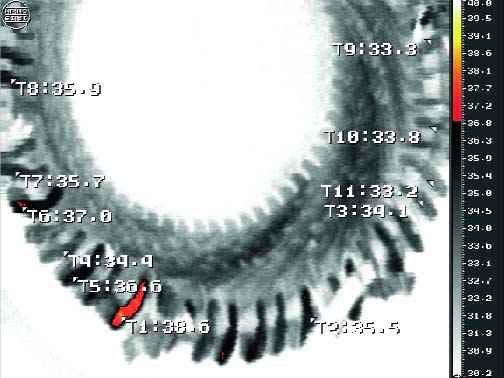
Рисунок 10 - Термограмма 29.10.04 г. турбогенератора типа ТГ2-25-2 Сызранской ТЭЦ, год выпуска 1956. Вид со стороны возбудителя, дефектные пайки головок стержней – точки № 1, № 5 (ΔT от 3,3°С до 5,5°С, ΔRомич.= 3,2 %)
На рис. 11 представлена термограмма опорного изолятора разъединителя 110 кВ подстанции «Новоспасская-1». Предположительная причина нагрева – увлажнение внутренней поверхности фарфора, увеличение тока утечки по внутренней поверхности (ΔT= 1,4°С). На рис. 12 – нагрев болтового соединения аппаратного зажима разъединителя 220 кВ в сторону линии «Просвет-2» подстанция «Томыловская» (губки ножа разъединителя, фаза В
(ΔT= 48°С)). На рис. 13 – нагрев болтового соединения гибкой связи шинного разъединителя 110 кВ в сторону масляного выключателя подстанции «Чапаевская» (фаза С
(ΔT = 116°С)).
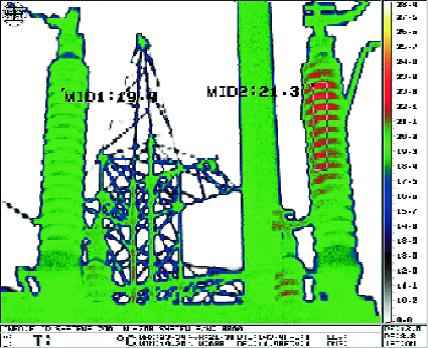
Рисунок 11 - Опорный изолятор разъединителя ШР-110 кВ подстанции «Новоспасская-1» в сторону ЛР. Фаза А
. Предположительно увлажнение внутренней поверхности фарфора, увеличение тока утечки по внутренней поверхности (ΔT=1,4°С)
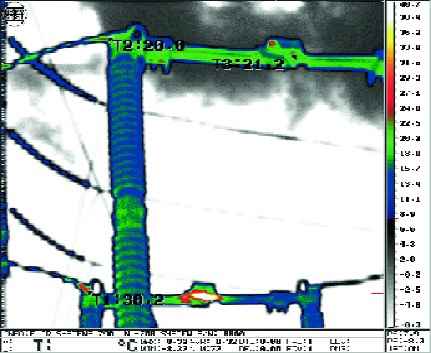
Рисунок 12 - ЛР-220 кВ линии «Просвет-2» подстанция «Томыловская». Нагрев болтового соединения аппаратного зажима разъединителя в сторону ЛЭП. Губки ножа разъединителя, фаза В
(ΔT= 48°С)
Дефекты болтовых соединений разъединителей не единственные обнаруживаемые тепловизорами. Возможно также выявление локальных нагревов на стенках бака высоковольтного маслонаполненного ЭО, связанных с дефектами обмоток встроенных ТТ или плохими контактами внутри масляного выключателя, которые скрыты толщей масла и трудно поддаются интерпретации. На рис. 14 хорошо виден нагрев фазы А
встроенного трансформатора тока 110 кВ (ΔT= 5,1°С) подстанция «ЗИМ 110/35/6 кВ». Предположительно возможны две причины: раскорачивание вторичных зажимов ТТ или витковое замыкание в обмотке ТТ. На рис. 15 изображен локальный нагрев на стенке бака масляного выключателя ВМ-35 кВ Т1Т
типа МКП-35 подстанции М. Ишуткино 35/10 кВ
, фаза А
(ΔT= 3,7°С), который может быть связан с плохим контактом в гибкой связи к токоведущему стержню или в контактной группе (розетка дугогасящего устройства) [14-16].
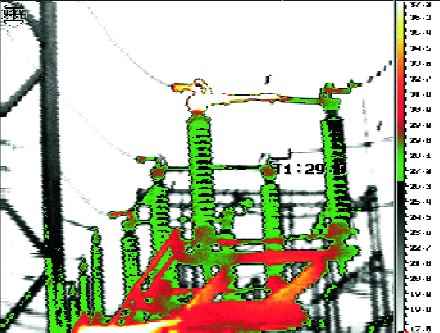
Рисунок 13 - ШР-1-110 кВ линии Гражданская
подстанции «Чапаевская». Нагрев болтового соединения гибкой связи в сторону МВ, фаза С
(ΔT=116°С)
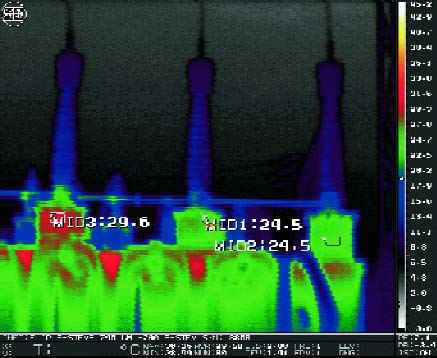
Рисунок 14 - Подстанция «ЗИМ 110/35/6 кВ», трансформатор С1Т. Нагрев фазы А
встроенного трансформатора тока 110кВ (ΔT = 5,1°С)
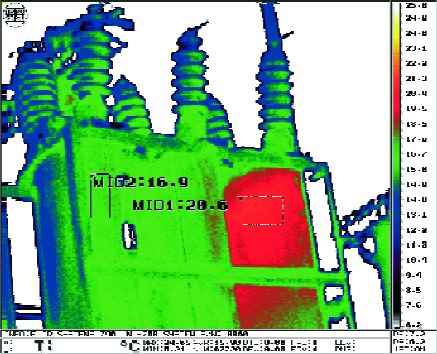
Рисунок 15 - Подстанция «М. Ишуткино 35/10 кВ» ВМ-35 кВ Т1Т
типа МКП-35. Локальный нагрев на стенке бака масляного выключателя, фаза А
. (ΔT = 3,7°С)
5. Проблемы технической диагностики
Общей проблемой технической диагностики является достижение адекватной оценки распознавания истинного состояния объекта и классификации этого состояния (нормального или аномального).
При проведении технического диагностирования для подтверждения нормального состояния объекта выделяют две основные задачи:
- обеспечение получения достоверной информации;
- обеспечение приемлемой оперативности получения информации.
При проведении технического диагностирования для выявления аномалий выделяют две основные проблемы:
- вероятность пропуска неисправности;
- вероятность «ложной тревоги», то есть вероятность ложного сигнала о наличии неисправности.
Чем выше вероятность «ложной тревоги», тем меньше вероятность пропуска неисправности, и наоборот. Задача технической диагностики неисправностей состоит в нахождении «золотой середины» между этими двумя проблемами.
Выводы
Диагностика технического состояния электрооборудования может осуществляться как специальными приборами, которыми производятся прямые измерения электрических параметров контролируемых объектов традиционными методами, так и приборами для измерения косвенных характеристик электрооборудования, например, температуры поверхности, на бесконтактном измерении который основан тепловой неразрушающий контроль - тепловизионная диагностика. Метод позволяет осуществлять высокопроизводительный бесконтактный контроль электрооборудования в процессе работы без обесточивания объекта и выявлять многие дефекты на ранней стадии их развития, предупреждая возникновение аварий и чрезвычайных ситуаций в системах энергоснабжения.
Разработанная методика в настоящее время успешно применена при натурных обследованиях более 50 объектов на практике.
Тепловизионный контроль стал важным инструментом для обследования состояния различного электротехнического оборудования энергосистемы: трансформаторов тока и напряжения, разъединителей, вентильных разрядников, высоковольтных вводов, силовых трансформаторов, масляных выключателей, качества пайки обмоток статора турбогенераторов при ремонтных работах электродвигателей, дымовых труб и газоходов и др.
Проблема обеспечения используемыми технологиями качества пайки соединительных головок статорных обмоток ТГ при проведении ремонтных работ на сегодняшний день достаточно актуальна. Необходима проверка качества пайки с помощью последовательного тепловизионного контроля и измерения сопротивления постоянному току обмоток статора ТГ.
Для объективного определения технического состояния оборудования электротехнических комплексов предлагается использовать программно-информационную диагностическую систему, которая позволяет осуществлять сбор и обработку первичной информации на работающем электрооборудовании при помощи современных, высокоэффективных диагностических средств, выдачу результатов обработки этой информации в удобной форме, передачу этой информации в архив; обращение в справочно-информационный массив; постановку предварительного диагноза; принятие решения о дальнейших диагностических операциях. Диагностическая система включает перечни контролируемых узлов различных типов электроустановок, выявляемых дефектов, методы контроля и параметры, характеризующие эксплуатационное состояние. Учтена метрологическая обеспеченность, необходимый уровень автоматизации и совместимость средств измерения с ПЭВМ, удобство и наглядность выходной информации.
Диагностическая система показала высокую эффективность при решении задач раннего выявления дефектов высоковольтного оборудования; прогнозирования развития дефектов, оценки их опасности; определения объема ремонтно-восстановительных работ; оптимизации ремонтно-технического обслуживания оборудования.
*При написании данного реферата магистерская работа еще не завершена. Полный текст работы и материалы по теме могут быть получены у автора или его руководителя в январе 2016 года.
Список источников
- Косолапов А.Б. Система технической диагностики электротехнических комплексов // Успехи современного естествознания. – 2005. – № 2
- Алексеев Б.Л. Контроль состояния крупных силовых трансформаторов. – М.: Издательство НЦ ЭНАС, 2002. – 216с.
- Назарычев А.Н. Основные принципы системы технического обслуживания и ремонта электрооборудования по техническому состоянию // Надежность либерализованых систем энергетики / Под ред. Н.И. Воропая, А.Д. Тевяшева. – Новосибирск: Наука, 2004. – с.173-189.
- Структура экспертно-диагностической и информационной системы оценки состояния высоковольтного оборудования /Давиденко И.В., Голубев В.П., Комаров В.И., Осотов В.Н. // Электрические станции. 1997. №6. – с.25-27.
- Ротштейн А.П. Медицинская диагностика на нечеткой логике. – Винница: Континент-ПРИМ, 1996. – 132с.
- Пархоменко П. П. О технической диагностике. М: Знание, 1969 – 90 с.
- Приборы и системы для измерения вибрации шума и удара. Справ. в 2 кн. под ред. В.В. Клюева. М: машиностроение, 1978 – 844 с.
- Вибрации в технике. Т. 5. Ред. совет: В. Н. Челомей и др. М: Машиностроение, 1981 – 496 с.
- Технические средства диагностирования: Справочник / В.В.Клюев, П.П.Пархоменко, В.Е.Абрамчук и др.; под общ. Ред. В.В.Клюева. – М.: Машиностроение, 1989. – 672 с.
- Костюков А. В., Костюков В. Н. Повышение операционной эффективности предприятий на основе мониторинга в реальном времени. – М.: Машиностроение, 2009. – 192 с.
- Обьeм и нормы испытаний электрооборудования РД 34.45-51.300 – 97 с.
- Поляков В.С. Применение тепловизионных приемников для выявления дефектов высоковольтного оборудования. – Л.: 1990.
- Бажанов С.А. Инфракрасная диагностика электрооборудования распределительных устройств. ИТФ «Энергопрогресс», Приложение к журналу «Энергетик». – М.: 2000.
- Григорьев А.В., Осотов В.Н. О совершенствовании и расширении методов контроля теплового состояния турбогенераторов. – Электpические станции, 1999, № 11.
- Хренников А.Ю., Еганов А.Ф., Смолин А.Ю., Щербаков В.В., Языков С.А. Тепловизионный контроль генераторов и импульсное дефектографирование силовых трансформаторов. – Электрические станции, № 8, 2001.
- Хренников А.Ю., Петров А.С., Цыгикало Г.В., ЩербаковтВ.В., Языков С.А. Cистемы мониторинга и опыт диагностики состояния электротехнического оборудования в ОАО
СамараЭнерго
. – Электро. Электротехника, электроэнергетика.