Abstract
Contents
- Introduction
- 1. The purpose and objectives of the study
- 2. Structure and gearboxes.
- 3. Features of technology of restoration of gear elements (shafts, gears, housings).
- 3.1 The main types of gear breakages elements
- 3.2 How to restore elements gearboxes
- 3.3 Technology components gear repairs
- Conclusion
- References
Introduction
The most important factors determining the operational reliability and service life of transport and technological machines and equipment are operational properties of the surface layer of the material and its durability. In operation, workers often wear surface parts, which requires their complete replacement and consequently increase the cost of repairs. In some cases, the entire production of all parts is irrational due to the high cost of materials and the difficulty of processing. Therefore, to solve problems of increasing physical and mechanical properties of working surfaces of parts and increase their service life in mechanical engineering and service companies use different methods of recovery and surface hardening.
Repair technology gear has its own peculiarities and difficulties. Production of the new gear is usually done more or less in large quantities, it can be used in the manufacture of special high-performance devices and tools for high accuracy machining and minimize locksmith fitting works in the assembly of units and gear. When repairing the gearbox due to their great diversity, the use of expensive tools and instruments are often not economically justified, so the proportion of plumbing fitting works is quite high. When repairing gearboxes, depending on the condition and use, some parts are discarded and replaced with new ones, while others are reduced by some method, and others - only stripped and used in this form for further work [1].
As a result of globalization and the development of means of CAD / CAE systems, gear life is more predictable in the design phase. Also available in case of emergency failure gear, because it requires repair or replacement of certain elements of the gear elements, as the new gear is much more expensive.
1. The purpose and objectives of the study
The aim of this work is to increase productivity, improve quality, reduce labor intensity and cost of the reduction gear elements (shafts, housings, gears).
To address this goal should be to solve the following problems:
- Analyze methods of restored eniya workpiece surface to Mining - Metallurgical complex.
- Determine the rational method of s Voss tanovlenii surfaces of the parts.
- To develop tooling.
Objectives of the work:
- Research methods of recovery gear.
- Development of methods for recovery gear.
- Development of technology for repairing.
2. Structure and gearboxes.
It called gear transmission or a combination of gears mounted in the crankcase or entered in other units.
Reducer serves to reduce (reduction) of the angular velocity and torque boost. It is the main part of the mechanical transmission device from the motor to the actuator and a part of the hydromechanical, electromechanical, and other complex transmission.
In the general case it consists of a gearbox housing, shafts, gears and standardized elements (bearings, keys, etc.).
3. Features of technology of restoration of gear elements (shafts, gears, housings).
3.1 The main types of gear breakages elements
Education and development of faults in the car is attributable to objectively existing laws. Faults machines are the result of constant or sudden decrease physical and mechanical properties of the parts, their abrasion deformation, crushing, corrosion, aging, redistribution of residual stresses and other causes of the destruction of parts. In most cases, there are changes in the pairings - violation of the given gaps in movable joints, or tightness in motionless. The appearance of faults due to the structural, technological and operational factors.
Operational factors have a decisive effect on the conservation of properties of machine elements, provided their design and manufacturing technology. Specific details of the fault[2].
Malfunctions of machine parts can be divided into three groups: wear, mechanical damage and chemical-heat injury.
3.2 How to restore elements gearboxes
In a production environment designed and implemented dozens of different ways to restore details. Drawing 1 methods of details Choosing the most appropriate method is in the technical, economic and organizational analysis requirements for the restoration of parts subject to the conditions of their work in the pairing of the production program, equipment companies, provision of materials, energy, labor and other specific activities [2].

Drawing - 1. Methods of details
3.3 Technology components gear repairs
Technological operations of these types are performed at any repair shop, but the number of cultivated species of each type of operation depends on the capacity and the technical level of the individual plant. Drawing 2 process Flow Diagram of details
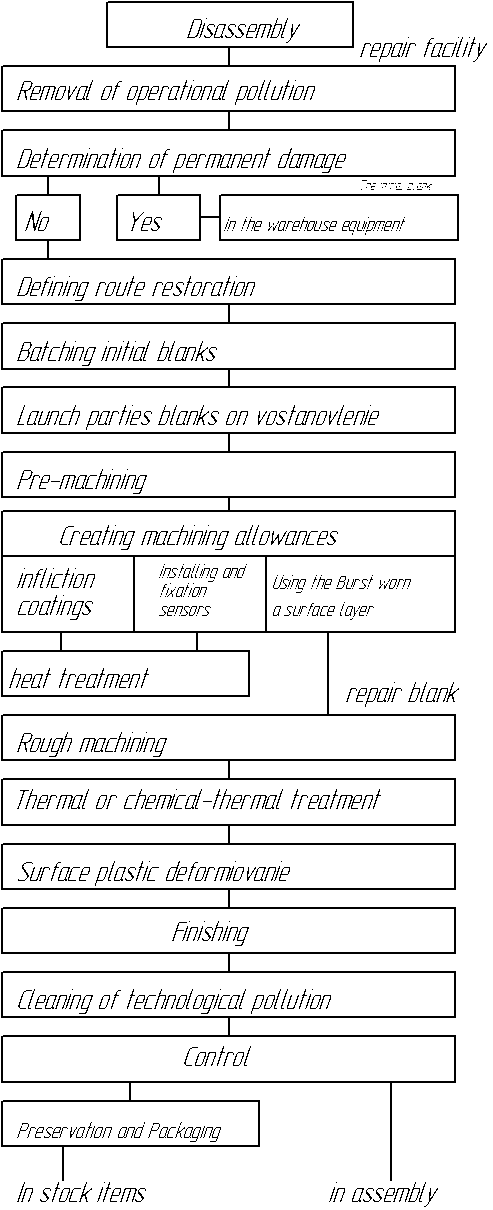
Drawing - 2. Process Flow Diagram of details
Conclusion
The main methods of details are as follows: recovery of the repair sizes, the use of additional components, pressure welding and cladding, plating, chrome plating, zheleznenija (by injection).
To win the position on the market of goods, reductive production must achieve and maintain a standard level of quality of the parts and for greater efficiency of its work continuously to reduce the specific consumption of production resources is achieved by raising the technical level of production, and by improving the means of details when fully loaded, the introduction of new and advanced TA Labour Organization [6].
The quality of the repair (restoration) is detected by the four groups of information:
- The results of monitoring of repaired facilities in time of testing and analysis of detected defects;
- Grouping the defects found by the user equipment warranty period;
- Data Cleanup operating time and failures in controlled operation;
- Studying damage repair fund incoming repair.
Legislative requirements for reliability repaired equipment is to ensure that 80% posleremontnogo developments of this technique as compared to the new products. In turn, the reliability of the repair the unit largely depends on the durability constituent assembly units and parts [7.
References
- Молодык Н. В., Зенкин А. С. Восстановление деталей машин / Н. В. Молодык, А. С. Зенкин. – М.: Машиностроение, 1989. – 480 с.: ил. – (Справочники для рабочих). – ISBN 5-217-00422-3.
- Пантелеенко Ф. И. Восстановление деталей машин / Ф. И. Пантелеенко. – М.: Машиностроение, 2003. – 672 с.
- Пекелис Г. Д., Гельберг Б. Т. Технология ремонта металлорежущих станков / Г. Д. Пекелис, Б. Т. Гельберг. – Л:,
Машиностроение
, 1970. - 320 с. - Гельберг Б. Т., Пекелис Г. Д. Ремонт промышленного оборудования / Б. Т. Гельберг, Г. Д. Пекелис – Л:,
Высшая школа
1965. – 410 с. - Муравьев К. Н., Мурзин И. К. Ремонт металлорежущих станков 3-е изд., перераб. и доп. / К.Н. Муравьев, И.К. Мурзин. – М.: Машгиз, 1963. – 280 с.
- Воловик Е. Л. Справочник по восстановлению деталей / Е. Л. Воловик. – М.:
Колос
1981. – 351 с. - Минкин А. С. Ремонт и обслуживание металлорежущих станков / А. С. Минкин. – М.: Машгиз, 1952. – 241 с.
- Макиенко В. М., Бидненко В. Е., Клиндух В. Ф. Технология сварочно-наплавочных работ / В.М. Макиенко, В.Е. Бидненко, В.Ф. Клиндух. – Хабаровск; изд-во ДВГУПС, 2006. – 125 с.
- ДонНТУ каф. ТМ [электронный ресурс]. — Режим доступа: http://iic.donntu.ru/...