Реферат за темою випускної роботи
Зміст
- Вступ
- 1. Актуальність теми
- 2. Мета і завдання дослідження, плановані результати
- 3. Структура і особливості редукторів
- 4. Особливості технології відновлення елементів редукторів (валів, зубчастих коліс, корпусів)
- 4.1 Основні види поломок елементів редукторів
- 4.2 Способи відновлення елементів редукторів
- 4.2.1 Зварювання
- 4.2.2 Наплавлення
- 4.2.3 Нанесення газотермических покриттів
- 4.2.4 Холодне пластичне деформування
- 4.2.5 Гаряче пластичне деформування
- 4.2.6 Гальванічні процеси
- 4.2.7 Нанесення полімерних матеріалів
- 4.2.8 Застосування ремонтних розмірів
- 4.2.9 Застосування додаткових деталей
- 4.2.10 Проведення хіміко-термічних процесів
- 4.2.11 Електромеханічна обробка
- 4.2.12 Електрофізична обробка
- 4.2.13 Електрохімічна обробка
- 4.2.14 Пайка
- 4.3 Технології ремонту елементів редукторів
- Висновки
- Список джерел
Вступ
Найважливішими факторами, що визначають експлуатаційну надійність і термін служби транспортних і технологічних машин і устаткування є експлуатаційні властивості поверхневого шару матеріалу і його міцність. При експлуатації нерідко зношуються робочі поверхні деталей, що вимагає їх повної заміни і, як наслідок, підвищення собівартості ремонту. У ряді випадків виготовлення деталей цілком взагалі нераціонально у зв'язку з високою вартістю матеріалів і трудністю обробки. Тому для вирішення завдань підвищення фізико-механічних показників робочих поверхонь деталей і збільшення їх терміну служби в машинобудуванні та підприємствах сервісу застосовують різні способи відновлення і поверхневого зміцнення.
Технологія ремонту редукторів має свої особливості і труднощі. Виготовлення нових редукторів зазвичай проводиться більш-менш великими серіями, що дозволяє застосовувати при виробництві їх спеціальні високопродуктивні пристосування і інструмент, що забезпечують високу точність обробки деталей і зводять до мінімуму слюсарні прігоночні роботи при складанні вузлів і редуктора. При ремонті же редукторів, внаслідок великої їх різноманітності, застосування дорогих пристосуванні та інструменту часто економічно не виправдовується, тому питома вага слюсарних прігоночних робіт вельми висока. Ця особливість і створює додаткові труднощі в технології та організації ремонтних робіт. Інша важлива особливість ремонтного виробництва полягає в наступному. При ремонті редукторів, залежно від стану та призначення, одні деталі вибраковуються і заміняються новими, інші відновлюються тим чи іншим методом, а треті - тільки зачищаються і в такому вигляді використовуються для подальшої роботи.
1. Актуальність теми
Для відновлення зношених деталей в основному застосовують зварювально-наплавочні методи. Недоліком цих методів є: значні термічні дії на деталь, виникнення в деталях залишкових напружень, деформацій, тріщин і, як наслідок, зниження терміну служби в порівнянні з новими деталями. Крім того, для наплавленого матеріалу характерний значний розкид фізико-механічних властивостей.
Великим резервом підприємств технічного сервісу є організація відновлення зношених деталей. Збільшення обсягів відновлення деталей дозволяє істотно знизити витрати на запасні частини, а, отже, вартість ремонту і сервісних послуг в цілому [1].
У результаті глобалізації та розвитку засобів CAD / CAE систем, термін служби редукторів є прогнозованим ще на етапі проектування. Також можливі випадки екстреного виходу з ладу редуктора, через це потрібний ремонт деяких елементів або заміна елементів редуктора, так як нові редуктора є значно дорожче.
2. Мета і завдання дослідження, плановані результати
Метою даної роботи є збільшення продуктивності, підвищення якості, зниження трудомісткості і собівартості при відновленні елементів редукторів (валів, корпусів, зубчастих коліс).
Для вирішення поставленої мети слід вирішити наступні завдання:
- Провести аналіз методів відновлення поверхні деталі для гірничо-металургійного комплексу.
- Визначити раціональні методи відновлення поверхонь деталей.
- Розробка технологічної оснастки.
Завдання роботи:
- Дослідження методів відновлення редукторів.
- Розробка методів відновлення редукторів.
- Разработка технології восстановления.
3. Структура і особливості редукторів.
Редуктором називається передача або поєднання передач, встановлених в картері або вписаних в інший агрегат.
Редуктор служить для зниження (редукування) кутової швидкості та підвищення крутного моменту. Він є основною частиною механічного передавального пристрою від двигуна до виконавчого механізму і входить до складу гідромеханічних, електромеханічних та інших складних передач. Принцип роботи редуктора представлений на рисунку 1.
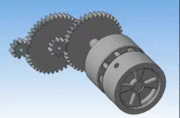
Рисунок 1 – Робота редуктора (анімація: кількість кадрів - 9, кількість повторень необмежена, розмір 122,0 КБ)
У загальному випадку редуктора складаються з корпусу, валів, зубчастих коліс і стандартизованих елементів (підшипників, шпонок і т.д.) .
4. Особливості технології відновлення елементів редукторів (валів, зубчастих коліс, корпусів).
4.1 Основні види поломок елементів редукторів
Освіта та розвиток несправностей в машині пояснюється дією об'єктивно існуючих закономірностей. Несправності машин з'являються в результате постійного або раптового зниження фізікомеханіческіх властивостей матеріалу деталей, їх стирання, деформування, смятия, корозії, старіння, перераспределенія залишкових напружень та інших причин, що викликають руйнування деталей. У більшості случаїв відбуваються зміни в сполученнях – порушення заданих зазорів в рухомих з'єднаннях або натягів в нерухомих. Практично будь-яка несправність являєтся наслідком зміни складу, структури або механічних властивостей матеріалу, конструктивних розмірів деталей і стану їх поверхонь.
Поява несправностей обумовлено конструктивними, технологічними та експлуатаційними чинниками.
До конструктивних факторів належать: розрахункові навантаження, швидкості відносного переміщення, тиску, матеріали, їх фізико-механічні характеристики і структура, конструктивне виконання деталей і сборочних одиниць, форма і величина зазорів або натягів в сполученнях, макрогеометрії, шорсткість і твердість поверхонь, умови змазування та охолодження деталей.
Технологічними факторами є прийоми, способи, точність і стабільність одержання заготовок, види механічної, термічної, упрочняющей і фінішної обробки при виготовленні деталей, правильність складання, регулювання, підробітки та випробування вузлів, агрегатів і машин [2].
Експлуатаційні фактори мають вирішальний вплив на збереження властивостей елементів машин, забезпечуваних їх конструкцією і технологією виготовлення.
Характерні несправності деталей
Несправності деталей машин можна розділити на три групи: знос, механічні пошкодження і хіміко-теплові пошкодження.
Зносу деталей машин визначаються тиском, циклічними навантаженнями, режимом змазування і ступенем його стабільності, швидкістю переміщення поверхонь тертя, температурним режимом роботи деталей, ступенем агресивності навколишнього середовища, якістю обробки і станом поверхонь тертя і т. д. [3]. Характерні несправності редукторів надані на рисунку 2.
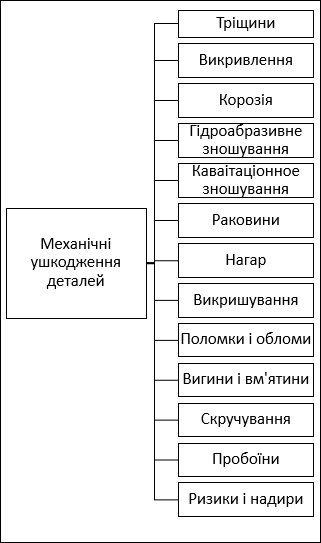
Рисунок 2 – Характерні механічні несправності деталей
4.2 Способи відновлення елементів редукторів
У виробничих умовах розроблені і реалізовані десятки різних способів відновлення деталей, які представлені на рисунку 3. Вибір найбільш прийнятного способу полягає в техніческому, економічному та організаційному аналізах вимог до відновлених деталей з урахуванням умов роботи їх в сполученнях, виробничої програми, оснащеності підприємств, забезпеченості матеріалами, енергією, робочою силою та інших конкретних заходів [2].
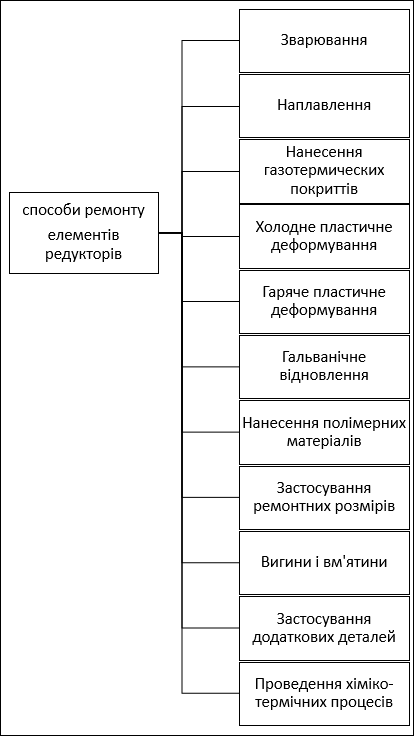
Рисунок 3 – Способи відновлення деталей
4.2.1 Зварювання
Зварювання – це процес утворення нероз'ємного з'єднання деталей або складальних одиниць шляхом їх місцевого нагріву та (або) спільного деформування, внаслідок чого виникають міцні зв'язки між атомами (молекулами) з'єднуються тел.
Застосовувані види зварювання для ремонту заготовок:
- ручна дугова – заварка тріщин, обломів, приварку накладок, вставок, латок, наплавка зносостійких матеріалів;
- автоматична і механізована дугова – заварка тріщин, обломів, приварку накладок, вставок, латок, зварювання тонколистового матеріалу;
- аргонодуговая – зварювання і наплавка алюмінію і коррозіонно-стійкої сталі;
- газова – заварка тріщин, приварювання обломів, зварювання тонколистового матеріалу;
- контактна – зварювання тонколистового матеріалу;
- тертям – стикова зварка деталей і їх елементів різної конфігурації при повишенних вимогах до якості сварного з'єднання;
- термитная – зварювання великогабаритних і масивних деталей;
- електрошлакове – приварку обломів, зварювання великогабаритних деталей;
- електро-променева – зварювання відповідальних деталей з високою точністю;
- ультразвукова – зварювання кольорових металів, сталі, негабаритних деталей;
- високочастотна магнітно-імпульсна зварка – корозійностійкої сталі;
- тиском – зварювання деталей та їх елементів, разлічних по конфігурації;
- диффузионная у вакуумі – зварювання дрібних відповідальних деталей з високою точністю;
- ковальська – зварювання невідповідальних деталей з невисокой точністю при підвищених требованіях до міцності зварного з'еднання.
4.2.2 Наплавлення
Наплавлення – процес нанесення відновно-зміцнюючого покриття шляхом розплавлення (теплом полум'я, дуги, струму, випромінювання та ін.) Присадочного металу, перенесення його на оплавлену відновлюють поверхню і кристалізацію шару.
Вживані види наплавлення для ремонту заготовок:
- дуговая під флюсом – наплавка деталей діаметром більше 50 мм при підвищених вимогах до якості наплавленого матеріалу з товщиною наплавленого шару більше 1 мм;
- дуговая у вуглекислому газі – наплавка сталевих деталей діаметром більше 16 мм широкої номенклатури, що працюють в різних умовах;
- дуговая з газополум'яної захистом - наплавка сталевих і чавунних деталей, що працюють в різних умовах;
- вибродуговая – наплавка сталевих деталей, що працюють в різних умовах при невисоких вимогах до опору втоми;
- дуговая порошковим дротом і стрічкою – наплавка зносостійких шарів на деталях, що працюють в умовах інтенсивного абразивного зношування, ударних навантажень, у вузлах тертя;
- дуговая в середовищі аргону – наплавка алюмінієвих деталей і деталей з корозійностійкої сталі;
- контактна – наплавка гладких циліндричних зовнішніх і внутрішніх поверхонь із зносом не більше 1 мм;
- газова – наплавка циліндричних і профільних поверхонь з місцевим зносом при підвищених вимогах до зносостійкості;
- плазмова – наплавка відповідальних деталей при підвищених вимогах до зносостійкості і опору втоми;
- багатоелектродні під флюсом – наплавка деталей зі значним зносом за величиною і площі;
- лежачим електродом – наплавка плоских поверхонь і поверхонь складної конфігурації зі значним зносом;
- електроімпульсна – наплавка зовнішніх циліндричних поверхонь із зносом до 0,5 мм з обмеженням температури нагріву деталі;
- електроіскрова – нарощування і зміцнення поверхонь із зносом до 0,2 мм при невисоких вимогах до складності покриття;
- електрошлакова – наплавка деталей зі значним зносом, що перевищують 6 мм по товщині;
- рідкий метал – наплавка деталей зі значним зносом (не менше 3 мм) при підвищених вимогах до зносостійкості і знижених вимогах до ударних навантажень;
- з одночасним деформуванням – наплавка деталей переважно із зовнішнім шліцьовим профілем;
- з одночасним різанням – наплавка та обробка зносостійких матеріалів в нагрітому стані, обробка яких в холодному стані утруднена;
- лазерна наплавка зносостійких матеріалів на відповідальні деталі і деталі зі складним профілем;
- високочастотна – наплавка зносостійких матеріалів на робочі органи і леза;
- високочастотна в вогнетривкої середовищі – наплавка вушок і цівок ланок гусениць.
4.2.3 Нанесення газотермических покриттів
Вживані види газотермических покриттів для ремонту заготовок:
- плазмове порошковими матеріалами без оплавленія (на ацетилені або пропан-бутан) – зовнішні і внутрішні циліндричні і профільні поверхні при підвищених вимогах до зносостійкості і міцності зчеплення з основним матеріалом
- плазмове порошковими матеріалами з оплавленіем (на ацетилені або пропан-бутан) – зовнішні та внутрішні циліндричні та профільні поверхні при підвищених вимогах до зносостійкості і міцності зчеплення з основним матеріалом
- плазмове порошкових матеріалів – зовнішні і внутрішні циліндричні поверхні
- плазмове дротом суцільного перерізу – зовнішні і внутрішні циліндричні поверхні
- іонно-плазмове – нанесення зносостійких і защітних покриттів з особливими властивостями товщиною до 0,02 мм
- детонаційне – нанесення зносостійких покриттів з особливими властивостями
- дугове – зовнішні і внутрішні ціліндріческіе поверхні з невисокими вимогами до міцності зчеплення
- високоточну – зовнішні і внутрішні ціліндріческіе поверхні з невисокими вимогами до міцності зчеплення
4.2.4 Холодне пластичне деформування
Застосовувані види холодної пластичного деформування для ремонту заготовок:
- роздача – відновлення зовнішніх поверхонь порожнистих деталей з нежорсткими вимогами до внутрішньому розміру;
- роздача з одночасною витяжкою – відновлення спеціальним деформуючим інструментом зовнішніх поверхонь і довжини порожнистих деталей з нежорсткими вимогами до внутрішньому розміру;
- витяжка – Відновлення довжини деталей з не жорсткими вимогами до зовнішніх розмірами;
- раскатка – Закріплення додаткових ремонтних деталей в отворах, наприклад, свертних кілець;
- дорновании і калібрування – відновлення поверхонь отворів після осідання або термічного впливу. Зміцнення і вигладжування;
- протягування – відновлення поверхонь отворів після осідання або термічного впливу. Зміцнення і вигладжування;
- осадка – відновлення зовнішніх і внутрішніх поверхонь деталей при нежорстких вимогах до довжини;
- правка – відновлення форми;
- накатка – відновлення поверхні невідповідальних деталей, відновлення рифленою і шліцьовій поверхонь;
- обжим – відновлення внутрішніх поверхонь деталей при нежорстких вимогах до зовнішніх;
- карбування – відновлення форми деталей, зміцнення зварних швів.
4.2.5 Гаряче пластичне деформування
Вживані види гарячого пластичного деформування для ремонту заготовок:
- тиск в закритому штампі – відновлення форми та елементів деталей за рахунок перерозподілу металу з неробочих поверхонь на робочі для компенсації зносу;
- гидротермічеськая роздача – відновлення зовнішніх поверхонь порожнистих деталей з нежорсткими вимогами до внутрішньому розміру;
- термоціклірованіе – відновлення, переважно внутрішніх поверхонь порожнистих деталей;
- термопластична обтиск – відновлення внутрішніх поверхонь порожнистих деталей;
- накатка – відновлення зубчастих профілів шестерень і зірочок;
- ротаційне деформування – відновлення зубчастих і шліцьових поверхонь;
- обжим – відновлення внутрішніх розмірів деталей при нежорстких вимогах до зовнішніх;
- правка – відновлення форми;
- витяжка – відновлення довжини деталей про нежорсткими вимогами до зовнішніх;
- осадка – відновлення зовнішніх і внутрішніх поверхонь деталей при нежорстких вимогах до довжини;
- роздача – відновлення зовнішніх поверхонь порожнистих деталей з нежорсткими вимогами до внутрішньому розміру;
- витискання – місцеве деформування з метою відновлення профілю і розмірів робочих поверхонь;
- відтягнення – відновлення форми робочих поверхонь і ріжучих кромок робочих органів;
- термомеханічна обробка – відновлення фізико-механічних характеристик, зміцнення.
4.2.6 Гальванічні процеси
Гальванічні процеси для ремонту заготовок:
- залізнення: на постійному і асиметричному токах, у спокійному або проточному електролітах; відновлення зовнішніх і внутрішніх поверхонь деталей переважно із зносом, що не перевищує 0,2-0,5 мм, високою поверхневою твердістю і при нежорстких вимогах до міцності зчеплення покриття з основним металом;
- хромування: при постійному струмі, в спокійному або проточному електроліті, розмірне – відновлення зовнішніх і внутрішніх поверхонь деталей із зносом, що не перевищує 0,2 мм, і високими вимогами по зносостійкості відновлених поверхонь
- хімічне і електролітичне нікелювання – відновлення зовнішніх і внутренніх поверхонь деталей із зносом, що не перевищує 0,05 мм;
- цинкування – захисне покриття від корозії;
- міднення – відновлення зовнішніх і внутрішніх поверхонь деталей, виготовлених з міді і її сплавів;
- електролітичне натирання цинком і железоцінковимі сплавами – відновлення зовнішніх і внутренніх циліндричних поверхонь деталей при нежорстких вимогах до твердості поверхневого шару;
- нанесення гальвано-полімерних покриттів – відновлення зовнішніх і внутренніх циліндричних поверхонь деталей;
- кадміювання – захисні антикорозійні покриття.
4.2.7 Нанесення полімерних матеріалів
- Напиленням: газополуменевим, в електростатичному полі, в псевдозрідженому шарі, відцентровим намазуванням: шпателем, пензлем, валиком - відновлення форми поверхонь облицювань і оперень, восстановленіе антифрикційних, електроізоляціонних і декоративних покриттів.
- Литтям: під тиском, обпресуванням – відновлення посадочних поверхностей нерухливих сполучень, заделка тріщин, пробоїн.
- Намазування рідких прокладок, герметиків – відновлення герметичності з'єднань.
4.2.8 Застосування ремонтних розмірів
- Індивідуальних – відновлення форми і посадок поверхонь обробкою більш дорогої деталі до зникнення слідів зносу і виготовленням, подгонкой менш дефіцитної і дорогої деталі за розмірами основний з обеспеченіем заданої посадки.
- Категорійності – обробка деталі під заданий ремонтний розмір сопрягаемой деталі з ремонтними стандартними розмірами.
4.2.9 Застосування додаткових деталей
- обрізка та приварку швидкозношуваних елементів – відновлення робочих органів грунтообробних, землерийних і меліоративних машин;
- бандажирование – відновлення зовнішніх поверхонь деталей з попередньою механічною обробкою і без неї;
- приварку елементів і вкладишів – відновлення розмірів профільних поверхонь (ведучі колеса тракторів та ін.);
- постановка втулок і компенсаційних шайб – відновлення отворів, розмірних ланцюгів;
- постановка свертних кілець з закріпляючу розкочуванням – відновлення отворів;
- постановка різьбових спіральних вставок – відновлення різьбових з'єднань;
- постановка фігурних вставок, стяжок і гуженів – усунення тріщин, відновлення герметичності;
- приварку і приклеювання накладок, латок, в тому числі і клеесварние способом – усунення тріщин, пробоїн, відновлення герметичності.
4.2.10 Проведення хіміко-термічних процесів
- цементація і нітроцементація;
- повторне азотування;
- диффузионное хромування у вакуумі і парогазових;
- сульфохромірованіе;
- диффузионное цинкування;
- диффузионное борирование.
4.2.11 Електромеханічна обробка
Електромеханічна обробка застосовується для відновлення нерухомих сполучень із зносом до 0,2 мм
- висаджування;
- вигладжування.
4.2.12 Електрофізична обробка
Електрофізичних обробка застосовується для обробки наплавлених поверхонь з високою твердістю і видаленню залишків обламаних інструментів.
- електроконтакта підводна;
- електроабразівная;
- анодно-механічна;
- електроерозійна;
4.2.13 Електрохімічна обробка
Електрохімічна обробка застосовується для обробки наплавлених поверхонь з високою твердістю.
- абразивним інструментом з примусовим подаванням електроліту;
- інструментом з примусовою подачею.
4.2.14 Пайка
До основними видами пайки є: пайка легкоплавкими припоями, тугоплавкими припоями, пайка-сварка. Застосовується для відновлення герметичності з'єднань і трубопроводів, відновлення інструменту.
4.3 Технології ремонту елементів редукторів
Зношена деталь ремонтного фонду на шляху свого перетворення придатну деталь в результаті технологічних впливів на неї виконавців і засобів ремонту проходить такі стадії. Вихідна заготовка, ремонтна заготівля, відновлена деталь. В результаті очищення від експлуатаційних забруднень і робіт з визначення технічного стану ремонтного фонду виявляють деталі які мають переборні ушкодження і підлягають відновленню. Такі деталі є вихідними заготовками, які збирають в групи з однаковими сполученнями усуваються пошкоджень і у вигляді партій направляють на відповідні ділянки відновлення. Таким чином, вихідна заготовка - це очищена деталь ремонтного фонду з усуненими пошкодженнями.
Вихідна заготовка в загальному випадку перетворюється на ремонтну заготовку шляхом створення припусків на відновлюваних поверхнях і нанесення швів на тріщини, а ремонтна заготівля в деталь - в результаті хіміко-термічної та механічної обробки.
Технологічні впливу на відновлювану деталь утворюють блоки операцій: підготовку зношених елементів під нанесення покриттів або установку додаткової ремонтної літали (ДРД); установку і закріплення на датчиках, зварювання тріщин. нанесення покриттів або перерозподіл матеріалу шляхом його об'ємного пластичного деформування: розмірну і структурну стабілізацію елементів; термічну обробку; механічну обробку чорнову і чистову; поверхнево пластичне деформування; обробку, урівноваження; чистку від технологічних забруднень; контроль і консервацію.
Попередня механічна обробка надає правильну геометричну форму відновлюваним елементам перед нанесенням покриттів або установкою датчиків.
Ремонтне виробництво розпорядженні добре вивченим безліччю способів створення припусків під механічну обробку на відновлюваних поверхнях. Це різні види наплавлень, напилювання, нанесення гальванічних покриттів, об'ємного пластичного деформування, установки датчиків.
Ряд деталей машин допускають відновлення під ремонтні розміри їх шийок, отворів і площинних елементів. У такому випадку ремонтні заготовки виходять з вихідних заготовок без нанесення або переміщення матеріалу. Для досягнення економічності процесу відновлення повинні бути використані всі передбачені ремонтні розміри заготовок шляхом:
- забезпечення виробництва сполучаються деталями всіх ремонтних розмірів;
- правки довгих деталей типу валів перед обробкою;
- рівномірного знята припуску при механічній обробці, чому сприяє поєднання осей оброблюваних отворів і шпинделя розточувального верстата, а також адаптивне базування деталей при обробці шийок. Якщо можливість використання ремонтних розмірів вичерпана, то ремонтну заготовку створюють шляхом нанесення відновного покриття або установкою і закріпленням датчиків або переміщенням матеріалу заготовки.
Необхідна зносостійкість відновлюваних поверхонь досягається вибором їх матеріалу, умов його нанесення, а також подальшої термічної, хіміко-термічної та механічної обробкою. Вигляд і властивості поверх кісткового шару повинні бути сумісні зі способом його обробки [4].
На стадії створення ремонтної заготовки в основному формуються матеріал і структура робочих поверхонь деталі, що визначає її післяремонтного надійність.
За форму і взаємне розташування поверхонь найбільшою мірою відповідають перші операції механічної обробки, за розміри і шорсткість - останні, за зносостійкість - матеріали, операції нанесення і термічної обробки, за втомну міцність і жорсткість термічні операції і поверхневе пластичне деформування.
Однотипні операції (попередню механічну обробку, нанесення покриттів, термічну і механічну обробку і ар.) При відновленні різних елементів деталі об'єднують в блоки операцій і виконують разом.
Призначення оздоблювальних операцій (полірування, суперфінішування, хонингования) полягає в знятті разупрочнения в результаті механічної обробки шару та забезпеченні необхідної шорсткості поверхні.
Операція контролю полягає у встановленні відповідності відповідно відновленої літали вимогам технічної документації (креслення або карти технічного контролю).
Консерваційний захист деталей до 3 ... 5 днів забезпечують технічні миючі засоби, що застосовуються для очищення деталей від техно логічних забруднень. Для більш тривалого зберігання (це відноситься до деталей, призначеним для продажу) необхідна спеціальна консервація. Загальний технологічний процес відновлення деталей показаний на малюнку 3.
Технологічні операції зазначених типів виконуються на будь-якому ремонтному підприємстві, проте число освоєних видів операцій кожного типу залежить від потужності і технічного рівня окремого заводу [5].
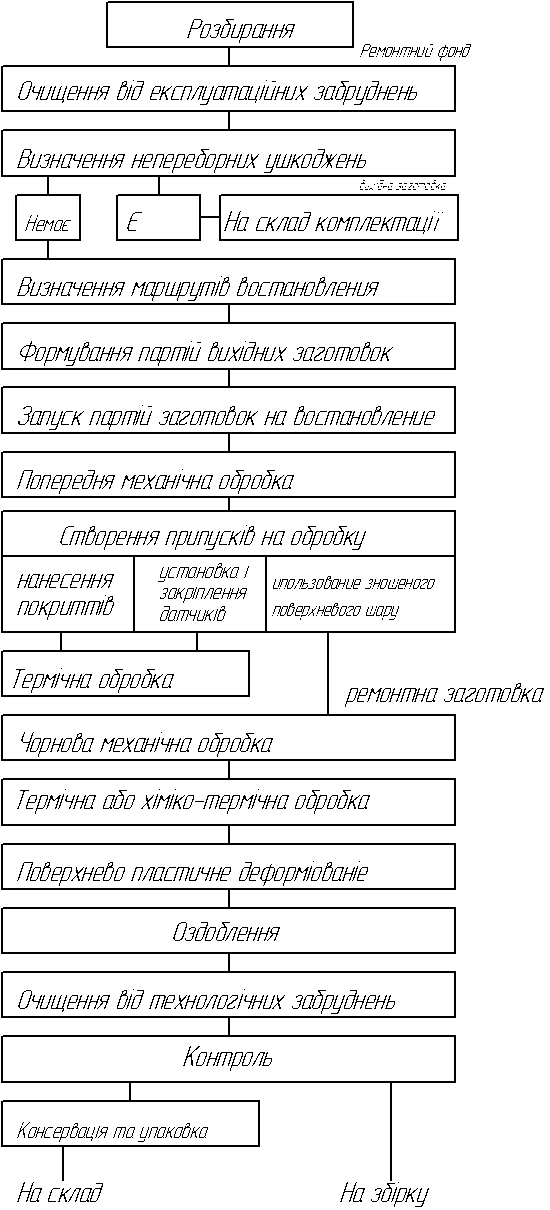
Рисунок 3 – Схема технологічного процесу відновлення деталей
Висновки
До основних способів відновлення деталей ставляться такі: відновлення ремонтних розмірів, використання додаткових деталей, тиску, зварювання та наплавлення, металізації, хромування, залізнення (відливання). Всі ці основні способи, хоча і не є рівнозначними, все ж використовуються в ремонтному виробництві в більшій чи меншій мірі залежно від його обсягу, оснащеності та іншого.
Щоб завоювати позиції на ринку товарів, відновне виробництво має досягти і підтримувати нормативний рівень якості випущених деталей, а для більшої ефективності своєї роботи безперервно зменшувати питому витрату виробничих ресурсів, забезпечується шляхом підвищення технічного рівня виробництва, а рахунок вдосконалення засобів відновлення деталей при їх завантаженні, впровадження нових ТП і передової організації праці.
Інформаційною базою для поліпшення виробництва служать відомостей про якість всієї відремонтованої (відновленої) продукції, в тому числі про її післяремонтного напрацюванні [6].
Якість ремонту (відновлення) виявляється за допомогою чотирьох груп відомостей:
- Результатів контролю ремонтованих об'єктів вчасно їх випробування і аналізу виявлених дефектів;
- Групування дефектів, виявлених користувачем техніки гарантійний період;
- Даних про післяремонтного напрацюванні і відмовах в подконтрольнойексплуатаціі;
- Вивчення пошкоджень ремонтного фонду, що надійшов ремонт
Директивне вимога до надійності відремонтованої техніки полягає в забезпеченні 80%-ної післяремонтного напрацювання цієї техніки в порівнянні з новими виробами. У свою чергу, надійність ремонтованого агрегату в значній мірі залежить від долговечней складових складальних одиниць і деталей.
Відремонтовані складальні одиниці і агрегати характеризуються: точністю замикаючих лінійних і кутових розмірів, определяющіх фактичні зазори, натяги та перекоси в сполученнях; складальними моментами і зусиллями; пропрацьованністю поверхонь; динамічної н змішаної врівноваженістю; функціональними вихідними параметрами (показниками призначення). Складальні моменти при затягуванні різьбових соедіненій знаходяться в нормативних межах тільки у 30 ... 70% сопряженій. Складальні зусилля, як правило, не контролюються.
Функціональні вихідні параметри (показники призначення) відремонтованих агрегатів (тиск і витрата середовищ, потужність, зростання та ін.) Відповідають нормативам, однак експлуатаційний темп їх зміни в гіршу сторону перевищує відповідний темп ізмененія в машинах, введених в експлуатацію після їх первинного виготовлення [7].
Перелік посилань
- Молодык Н. В., Зенкин А. С. Восстановление деталей машин / Н. В. Молодык, А. С. Зенкин. – М.: Машиностроение, 1989. – 480 с.: ил. – (Справочники для рабочих). – ISBN 5-217-00422-3.
- Пантелеенко Ф. И. Восстановление деталей машин / Ф. И. Пантелеенко. – М.: Машиностроение, 2003. – 672 с.
- Пекелис Г. Д., Гельберг Б. Т. Технология ремонта металлорежущих станков / Г. Д. Пекелис, Б. Т. Гельберг. – Л:,
Машиностроение
, 1970. - 320 с. - Гельберг Б. Т., Пекелис Г. Д. Ремонт промышленного оборудования / Б. Т. Гельберг, Г. Д. Пекелис – Л:,
Высшая школа
1965. – 410 с. - Муравьев К. Н., Мурзин И. К. Ремонт металлорежущих станков 3-е изд., перераб. и доп. / К.Н. Муравьев, И.К. Мурзин. – М.: Машгиз, 1963. – 280 с.
- Воловик Е. Л. Справочник по восстановлению деталей / Е. Л. Воловик. – М.:
Колос
1981. – 351 с. - Минкин А. С. Ремонт и обслуживание металлорежущих станков / А. С. Минкин. – М.: Машгиз, 1952. – 241 с.
- Макиенко В. М., Бидненко В. Е., Клиндух В. Ф. Технология сварочно-наплавочных работ / В.М. Макиенко, В.Е. Бидненко, В.Ф. Клиндух. – Хабаровск; изд-во ДВГУПС, 2006. – 125 с.
- ДонНТУ каф. ТМ [электронный ресурс]. — Режим доступа: http://iic.donntu.ru/...