Реферат за темою випускної роботи
Зміст
- Вступ
- 1 Актуальність теми
- 2 Матеріали для виробництва плівки
- 2.1 Вимоги до ізоляційних покриттів
- 2.2 Класифікація покрить труб
- 2.2.1 Поліетиленове покриття
- 2.2.2 Поліпропіленові покриття
- 2.2.3 Комбіноване стрічково-поліетиленове покриття
- 2.2.4 Епоксидні покриття труб
- 2.2.5 Склоемалеве покриття труб
- 3 Опис конструкції черв'ячного екструдера і технологічної лінії
- 4 Огляд виробничого середовища і умов роботи екструдера
- 5 Основні проблеми при експлуатації екструдерів. Причини і способи їх усунення
- 6 Поопераційний контроль якості ізоляційних робіт
- Перелік посилань
Вступ
Для зведення до мінімуму корозійних пошкоджень, трубопроводи захищають антикорозійними покриттями. Для зовнішніх захисних покрить труб найбільш широко застосовуються полімерні плівки, виготовлені екструзією.
Виробництво труб з покриттям зовнішньої поверхні полімерною захисною плівкою є одним з найважливіших інноваційних напрямів промислового розвитку в сучасних умовах Донбасу.
У зв'язку з цим у даній роботі розглядаються питання, пов'язані з формулюванням вимог до покриттів труб, конструкціями покрить, описом конструкції і принципу роботи екструдера, можливими дефектами плівки.
1 Актуальність теми
Обробка сировини екструзією забезпечує великий обсяг виробництва, розмаїтність вироблюваної продукції і високий економічний ефект, обумовлений насамперед тим, що застосування екструдера дозволяє зробити процес безперервним, легко контрольованим, універсальним за видами перероблюваних матеріалів і готових виробів. При цьому актуальним є використання для їх виробництва не тільки поширеної сировини, але й вторинної сировини в поєднанні з різними добавками, що дозволяє отримувати нові продукти з унікальними наборами властивостей і структури.
Таким чином, виявлення закономірностей екструзії й обґрунтування раціональних режимів роботи машини для виробництва труб із зовнішнім захисним шаром є актуальною задачею, що має важливе теоретичне і народногосподарське значення.
2 Матеріали для виробництва плівки
2.1 Вимоги до ізоляційних покриттів
Для того щоб покриття виступали ізоляторами, вони повинні мати наступні властивості [1–4]:
- водонепроникність, що виключає можливість насичення пір покриття ґрунтовою вологою і тим самим перешкоджає контакту електроліту із поверхнею труби, яка захищається;
- добру адгезію покриття до поверхні труби, що запобігає відшаруванню ізоляції при місцевому руйнуванні її суцільності, а також виключає проникнення електроліту під покриття;
- суцільність, що забезпечує надійність покриття, бо навіть найдрібніша пористість в покритті призводить до створення електролітичних комірок і протікання корозійних процесів;
- хімічну стійкість, що забезпечує тривалу роботу покриття в умовах агресивних середовищ;
- електрохімічну нейтральність - окремі складові покриття не повинні брати участь у катодному процесі, бо це може призвести до руйнування ізоляції при електрохімічному захисті металевої споруди;
- механічну міцність;
- термостійкість, яка визначається необхідною температурою розм'якшення, що важливо при ізоляції
гарячих
об'єктів, і температурою настання крихкості, що має велике значення при проведенні ізоляційних робіт у зимовий час; - діелектрична стійкість, що визначають опір проходженню струму, що запобігають виникненню корозійних елементів між металом і електролітом і зумовлюють економічний ефект від застосування електрохімічного захисту;
- відсутність корозійного та хімічного впливу на об'єкт;
- можливість механізації процесу нанесення ізоляційного покриття, як в заводських, так і в трасових умовах;
- не дефіцитність;
- економічність (вартість ізоляційного покриття повинна бути на багато разів менше вартості об'єкта).
2.2 Класифікація покрить труб
Для зовнішньої ізоляції трубопроводів найбільш часто застосовуються наступні типи покрить:
- епоксидне;
- поліетиленове;
- поліпропіленове;
- комбіноване стрічково-поліетиленове;
- склоемалеве.
2.2.1 Поліетиленове покриття
Існує 4 варіанти конструкцій поліетиленових покрить труб:
- Поліетиленове покриття, що наноситься по бітумно-мастичному підшару (ГОСТ Р 51164–98).
- Поліетиленове покриття, що наноситься по ізоляційному підшару на основі липкої полімерної стрічки (ГОСТ Р 51164–98).
- Двошарове поліетиленове покриття, що складається з адгезійного підшару на основі термоплавкої полімерної композиції і зовнішнього поліетиленового шару (ГОСТ Р 51164–98).
- Тришарове поліетиленове покриття, що складається з шару епоксидної ґрунтовки (праймеру), адгезійного полімерного підшару і зовнішнього поліетиленового шару (ГОСТ Р 51164–98).
Труби з покриттям із екструдованого поліетилену мають такі переваги [5]:
- підвищений безремонтний термін експлуатації газопроводів;
- підвищена механічна міцність;
- якість покриття не залежить від температури навколишнього середовища;
- високий показник адгезії до матеріалу труб;
- високі діелектричні характеристики;
- широкий температурний діапазон застосування (від мінус 50 °С до +80 °С).
2.2.2 Поліпропіленові покриття
Поліпропіленове покриття має підвищену теплостійкість, високу механічну й ударну міцність, стійкість до продавлювання і абразивного зносу [6]. Але воно має один серйозний недолік – знижену морозостійкість.
Основна область застосування поліпропіленових покрить – протикорозійний захист "гарячих" (до 110–140 °С), морських і шельфових трубопроводів.
2.2.3 Комбіноване стрічково-поліетиленове покриття
Для протикорозійного захисту трубопроводів малих та середніх діаметрів (до 530 мм) досить широко використовується комбіноване стрічково-поліетиленове покриття. Основна перевага цього покриття полягає в можливості його нанесення на труби у заводських і в трасових умовах [7].
Температурний діапазон експлуатації трубопроводів з комбінованим покриттям – від мінус 20 до +40 °С, а прогнозований термін служби – 35–40 років.
2.2.4 Епоксидні покриття труб
Епоксидні покриття характеризуються підвищеною теплостійкістю, високою адгезією до сталі, відмінною стійкістю до катодного відшаровування, стійкістю до прорізання, абразивного зносу. Труби з епоксидним покриттям протягом тривалого часу можуть зберігатися під відкритим небом. Витрати на нанесення епоксидних покриттів значно нижче витрат на поліетиленові та поліпропіленові покриття труб (зі складу технологічних ліній виключаються енергоємні екструдери, системи завантаження і сушіння гранульованих композицій, зменшується витрата ізоляційних матеріалів тощо) [8].
Основними недоліками епоксидних покрить є їх недостатньо висока еластичність і низька міцність при ударі, особливо в області мінусових температур, що значною мірою ускладнює транспортування ізольованих труб і виконання будівельно-монтажних робіт в трасових умовах.
Даний тип покриття може бути використаний при будівництві морських, шельфових трубопроводів, при прокладці трубопроводів на ділянках під дорогами, при будівництві методом похило-спрямованого буріння.
2.2.5 Склоемалеве покриття труб
Склоемаль – це отримана плавленням скловидно застигла неорганічна маса, що складається переважно з оксидів і нанесена на метал в один або кілька шарів.
Склоемалеве покриття заводського нанесення застосовують для захисту трубопроводів від підземної й атмосферної корозії [9].
Аналіз представлених матеріалів захисних покрить показує, що повністю всім вимогам не відповідає жоден матеріал, тому для ізоляції підбирають матеріали, що відповідають ряду вимог, найбільш характерних для розглянутих умов спорудження й експлуатації трубопроводу.
У роботі, враховуючи підвищені вимоги до якості покриття підземних трубопроводів, доступність матеріалів покриття, технологічність і невисоку вартість, вибирається тришарове поліетиленове покриття, що складається з шару епоксидної ґрунтовки (праймеру), адгезійного полімерного підшару і зовнішнього поліетиленового шару (ГОСТ Р 51164–98).
3 Опис конструкції черв'ячного екструдера і технологічної лінії
Нанесення зовнішніх захисних покриттів на труби здійснюється з використанням обладнання потокових механізованих ліній. До складу таких ліній входять:
- роликові конвеєри;
- перекладники труб;
- вузли очищення (дробометна або дробострумна установки);
- печі технологічного нагріву труб (індукційні або газові);
- вузол напилювання порошкової епоксидної ґрунтовки;
- два екструдери – один для нанесення адгезійного підшару, а другий – зовнішнього шару покриття;
- притискні пристрої;
- камери водяного охолодження ізольованих труб;
- обладнання для контролю якості покриття.
У конструкції тришарового захисного покриття першим шаром наноситься епоксидна ґрунтовка на очищені і нагріті до необхідної температури труби методом напилювання, після цього послідовно наносяться экструдовані розплави термоплавкої композиції адгезиву і поліетилену [5].
Конструктивна схема технологічної лінії нанесення екструзією зовнішнього поліетиленового шару на підготовлені труби показана на рисунку 1.
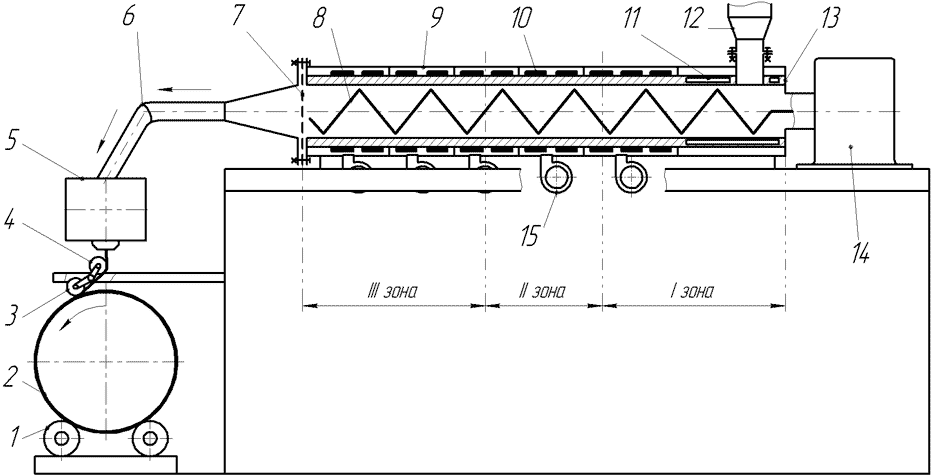
Рисунок 1 – Конструктивна схема технологічної лінії нанесення зовнішнього поліетиленового шару на труби екструзією
(анімація: 10 кадрів, 5 циклів повторення, 160 кілобайт)
Циліндричний корпус 13 екструдера умовно поділяють по довжині на три зони:
- 1 – зона прийому сировини;
- 2 – зона пластифікації (плавлення);
- 3 – зона гомогенізації.
Полімерний матеріал подається з бункера 12 в зону приймання сировини і шнеком 8 просувається уздовж корпуса 13. При цьому по мірі просування матеріал ущільнюється за рахунок зменшення глибини нарізки шнека [10].
У зоні пластифікації матеріал плавиться в місцях контакту з поверхнею корпуса за рахунок теплопередачі від нагрітих стінок, а також теплоти, що виникає при терті гранул полімеру по шнеку і стінкам корпуса. Нагрівання стінок корпуса здійснюється електричними кільцевими нагрівачами опору 10. Регулювання температури по довжині корпуса здійснюється повітрям, що подається вентиляторами 15 всередину знімних захисних огороджень 9 корпуса, а ділянка корпуса поблизу завантажувального отвору охолоджується водою, що проходить по каналах 11 корпуса. Обертальний рух шнеку 8 передається приводом, що складається з електродвигуна і двоступінчастого редуктора 14. Регулювання частоти обертання шнека здійснюється зміною частоти обертання ротора електродвигуна з використанням тиристорного перетворювача частоти.
Сітка 7 або пакет з декількох сіток, встановлюється на виході матеріалу з корпуса і створює опір, необхідний для підвищення тиску в зонах пластифікації та гомогенізації. Спресований матеріал утворює пробку. Тиск в пробці підвищується до величини, достатньої для подолання опору сіток 7 і формування профілю.
На початку 3-ї зони гомогенізації матеріал складається з твердих і розплавлених частинок. До кінця 3-ї зони сировина стає повністю гомогенною розплавленою масою. На виході з корпуса 13 екструдера розплав полімеру через перехідний пристрій 6 надходить на плоскощілинну головку 5 і продавлюється крізь неї.
На виході з плоскощілинної головки 5 плівка огинає направляючий ролик 4 і наноситься на поверхню труби 2 з притисненням до неї роликом 3. Плівка повинна мати суцільну гладку поверхню без бульбашок, смуг, гофр та включень [10].
Ізольовані труби роликовим конвеєром 1 подаються в тунель, де покриття охолоджується водою до необхідної температури, а потім труби з допомогою перекладників подаються на стелаж готової продукції.
4 Огляд виробничого середовища і умов роботи екструдера
Обладнання для нанесення поліетиленового покриття на труби не є пожежо - і вибухонебезпечним, однак його небажано встановлювати в приміщеннях з потенційно вибухонебезпечним середовищем, так як при піднесенні відкритого полум'я поліетилен спалахує без вибуху і тліє з утворенням розплаву і виділенням газоподібних продуктів горіння. В умовах нормальної роботи вібрація обладнання технологічної лінії відсутня [11].
Фактори ризику, що виникають при роботі обладнання:
- незахищені рухомі елементи обладнання;
- нагріті труби, що транспортуються по рольгангу;
- пил, до складу якого входять речовини, здатні викликати корозію;
- токсичні пари.
Виходячи з вищевказаного, постачальники сировини, добавок і витратних матеріалів зобов'язані надавати всю інформацію про пов'язані з їх продукцією потенційні небезпеки і про заходи безпеки, яких повинні дотримуватися при її зберіганні та використанні.
5 Основні проблеми при експлуатації екструдерів. Причини і способи їх усунення
Раціональні режими роботи екструдера при виробництві плівки для захисту трубопроводів від корозії безпосередньо залежать від вимог до якості одержуваної полімерної плівки.
Основними регульованими параметрами є:
- тиск;
- температура;
- швидкість обертання шнека.
Для своєчасного виявлення та усунення дефектів необхідно вимірювати наступні параметри:
- тиск в головці;
- частоту обертання шнека;
- температуру розплаву в головці;
- розподіл температури по довжині корпуса;
- швидкість охолодження кожної зони екструдера;
- швидкість руху плівки;
- геометричні розміри плівки;
- температуру води.
На роботу екструзійної лінії також впливають і зовнішні умови:
- температура навколишнього середовища;
- конвекція повітря;
- коливання напруги в електромережі.
Механічні зміни в екструдері (проблеми, пов'язані з обладнанням) тягнуть за собою зміни в технологічному процесі та можуть бути пов'язані з різними системами екструдера:
- із системою приводу (проявляються в зміні швидкості обертання шнека);
- із системою завантаження сировини в екструдер;
- із системою нагріву та охолодження.
Коливання продуктивності екструдера – це найпоширеніша проблема при екструзії, оскільки вона може викликатися різними причинами, головними з яких є [4, 13]:
- нерівномірність подачі матеріалу із завантажувального бункера і його подальшого транспортування в екструдері;
- недостатня потужність нагрівачів екструдера для плавлення полімеру;
- недостатня температура розплаву в головці;
- низька температура корпуса;
- порушення суцільності плівки;
- неправильно вибрана частота обертання шнека;
- коливання тиску в голівці.
Основні порушення режиму роботи екструдера [13]:
- захоплення повітря;
- наявність в екструдаті пустот;
- поява гелеобразних включень;
- поява поздовжніх смуг і рисок;
- сторонні включення;
- потемніння поверхні;
- відхилення товщини плівки (більше або менше) від заданого;
- низька механічна міцність плівки;
- складки і зморшки на плівці.
Неповне оснащення екструзійної лінії і, зокрема, екструдера контрольним устаткуванням може сильно заважати швидкому і точному виявленню несправностей.
6 Поопераційний контроль якості ізоляційних робіт
Контроль якості ізоляційних покрить здійснюється поопераційно. Придатність ізоляційних матеріалів визначає служба технічного нагляду [1, 3]. При цьому контролюється правильність технологічного процесу розігрівання бітумних матеріалів, відповідність фізико-механічних властивостей вихідних матеріалів і мастик вимогам ГОСТу та СНіП. Для цього не рідше одного разу на день проводять відбір контрольної проби мастики з метою визначення температури розм'якшення.
Для оперативного контролю процесу екструзії і підвищення якості одержуваної продукції виникає необхідність визначення фізико-механічних властивостей конкретної партії матеріалу, що переробляється, зокрема коефіцієнта зовнішнього тертя.
Відомі прилади для визначення коефіцієнта зовнішнього тертя гранульованих матеріалів при переміщенні відносно твердої поверхні [14] не враховують сил тертя матеріалу по стінках матриці, що призводить до зниження їх точності. Цей недолік усунений у приладі, розробленому на кафедрі машин та апаратів хімічних виробництв ДонНТУ [15].
Конструктивна схема приладу показана на рисунку 2.
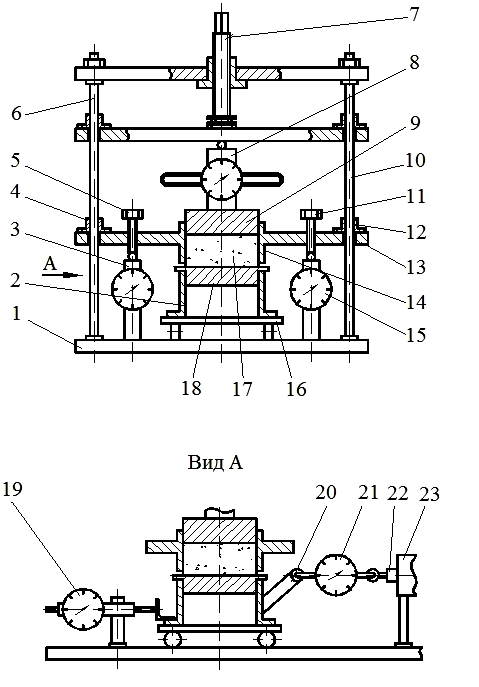
Рисунок 2 – Конструктивна схема приладу для визначення коефіцієнта зовнішнього тертя гранульованого матеріалу об робочі поверхні екструдера
Пристрій монтується на опорній плиті 1 і містить дві матриці. Нижня матриця 2 встановлюється на візок 16, а верхня 14 кріпиться до фланця 13. Фланець 13 встановлюється на два динамометра 3 і 15. Замість динамометрів можуть бути використані стрижні з тензометричними датчиками.
До нижньої матриці 2 кріпиться зразок 18 із досліджуваною поверхнею, зверненої в бік верхньої матриці 14. Досліджуваний гранульований матеріал 17 завантажується в порожнину верхньої матриці. Гвинтами 5 і 11 регулюється зазор між верхньою матрицею та досліджуваною поверхнею. Для запобігання перекосу верхнього матриці 14 до фланця 13 кріпляться втулки 4 та 12, які переміщаються по напрямних стійок 6 і 10.
Зусилля на пуансон 9 і гранульований матеріал створюється гвинтом 7 і вимірюється динамометром 8. Сили тертя матеріалу об стінки верхньої матриці реєструються динамометрами 3 і 15 та враховуються при визначенні середнього тиску досліджуваного матеріалу на досліджувану поверхню зразка 18.
Переміщення нижньої матриці здійснюється механізмом, виконавчою ланкою якого є шток 22 гвинтового редуктора 23.
Зусилля, необхідне для переміщення візка з нижньою матрицею 2 вимірюється динамометром розтягування 21, який кріпиться до тязі 20 нижньої матриці 2. Розміщення тяги 20 має бути таким, щоб лінія дії зусилля переміщення лежала в площині зсуву досліджуваного гранульованого матеріалу щодо досліджуваної твердої поверхні.
Для реєстрації початку переміщення нижньої матриці 2 до опорної плити 1 кріпиться мікрометричний індикатор годинникового типу 19.
Товщину шару захисного покриття визначають за допомогою ультразвукових товщиномерів у процесі виконання ізоляційних робіт через кожні 100 м труб, в місцях зупинки ізоляційної машини, не менше ніж у чотирьох точках по окружності труби або ємності і на кожній фасонній частини.
Суцільність покриття контролюють іскровим дефектоскопом.
Якість захисного покриття при приймально-здавальних випробуваннях перевіряють через кожні 500 м, а також вибірково на вимогу замовника.
Зчеплення покриття з мастик з поверхнею об'єкта, що захищається, контролюють адгезіметром або вручну надрізом захисного покриття під кутом 45-50° з відривом вершини кута надрізу.
При здачі захисного покриття трубопроводу замовнику пред'являють: паспорта на кожну партію матеріалів або результати лабораторних випробувань матеріалів; лабораторні аналізи проб бітумної мастики; журнал виробництва робіт; акт перевірки якості захисного покриття. Контроль якості ізоляційного покриття готових ділянок трубопроводу і засипаних ґрунтом здійснюється методом катодної поляризації.
При написанні даного реферату магістерська робота ще не завершена. Остаточне завершення: січень 2016 року. Повний текст роботи і матеріали по темі можуть бути отримані у автора після зазначеної дати.
Перелік посилань
- ГОСТ Р 51164-98 Трубопроводи сталеві магістральні. Загальні вимоги до захисту від корозії.
- ГОСТ 9.602-2005 Споруди підземні. Загальні вимоги до захисту від корозії.
- Протикорозійний захист трубопроводів і резервуарів/ М. В. Кузнєцов, В. Ф. Новоселів, П. І. Тугунов та ін.. - М: Надра, 1992.- 238 с.
- Крижанівський В.К., Кербер М.Л., Бурлов В.В., Паниматченко А.Д. Виробництво виробів з полімерних матеріалів. – С-П.: Професія, 2008. – 460 с.
- ТУ 1390-001-86695843-08. Труби сталеві діаметром 57-1420 з зовнішнім двошаровим і тришаровим поліетиленовим покриттям.
- ТУ 1394-010-17213088-03. Труби сталеві діаметром 57-1420 з зовнішнім покриттям на основі екструдованого поліпропілена для будівництва магістральних нафтопроводів.
- ТУ 1390-014-05111644-98. Труби діаметром 57-530 мм із зовнішнім комбінованим стрічково-поліетиленовим покриттям.
- ТУ 1390-014-86695843-2011. Труби і деталі трубопроводів сталеві з зовнішнім двошаровим епоксидним антикорозійним покриттям.
- ТУ 1396-001-12617190-95. Вузли сталевих трубопроводів з двостороннім склоемалевим покриттям. Технічні умови.
- Технологічна інструкція спеціального процесу зовнішнього антикорозійного покриття труб, 2014. – 14 с.
- Керівництво користувача екструдерів TR.100 і TR.200, редакція 1 від 26.10.2006. – 55 с.
- Лапшин В. В. Основи переробки термопластів литтям під тиском. - М.: Хімія, 1974. – 271 с., іл.
- Проблеми виявлення і усунення можливих дефектів у процесі отримання виробів з термопластів: навчальний посібник /А. Н. Садова, Т. Р. Дебердеєв, О. Н. Кузнєцова, О. В. Стоянов. – Казань: Вид-во Казан. держ. технол. ун-ту, 2009. – 123 с.
- Буличов В. Г. Механіка дисперсних грунтів. - М: Стройиздат, 1974. – 227 с., іл.
- А. С. СРСР №846637. Остапенко М. А., Рассказов М.І., Федоренко А.Д. Прилад для дослідження опору зсуву ґрунтів і сипких матеріалів. Б. І. №18, 1981.