Реферат по теме выпускной работы
Оглавление
- Введение
- 1 Актуальность темы
- 2 Материалы для производства пленки
- 2.1 Требования к изоляционным покрытиям
- 2.2 Классификация покрытий труб
- 2.2.1 Полиэтиленовое покрытие
- 2.2.2 Полипропиленовые покрытия
- 2.2.3 Комбинированное ленточно-полиэтиленовое покрытие
- 2.2.4 Эпоксидные покрытия труб
- 2.2.5 Стеклоэмалевые покрытия труб
- 3 Описание конструкции червячного экструдера и технологической линии
- 4 Обзор производственной среды и условий работы экструдера
- 5 Основные проблемы при эксплуатации экструдеров. Причины и способы их устранения
- 6 Пооперационный контроль качества изоляционных работ
- Перечень ссылок
Введение
Для сведения к минимуму коррозионных повреждений, трубопроводы защищают антикоррозионными покрытиями. В качестве наружных защитных покрытий труб наиболее широко применяются полимерные пленки, изготовленные экструзией.
Производство труб с покрытием внешней поверхности полимерной защитной пленкой является одним из важнейших инновационных направлений промышленного развития в современных условиях Донбасса.
В связи с этим в настоящей работе рассматриваются вопросы, связанные с формулировкой требований к покрытиям труб, конструкциями покрытий, описанием конструкции и принципа работы экструдера, возможными дефектами пленки.
1 Актуальность темы
Обработка сырья экструзией обеспечивает большой объем производства, разнообразие производимой продукции и высокий экономический эффект, обусловленный прежде всего тем, что применение экструдера позволяет сделать процесс непрерывным, легко контролируемым, универсальным по видам перерабатываемых материалов и готовых изделий. При этом актуальным является использование для их производства не только широко распространенного сырья, но и вторичного сырья в сочетании с различными добавками, что позволяет получать новые продукты с уникальными наборами свойств и структуры.
Таким образом, выявление закономерностей экструзии и обоснование рациональных режимов работы экструдера для производства труб с наружным защитным слоем является актуальной задачей, имеющей важное теоретическое и народнохозяйственное значение.
2 Материалы для производства пленки
2.1 Требования к изоляционным покрытиям
Для того чтобы покрытия выступали изоляторами, они должны обладать следующими свойствами [1–4]:
- водонепроницаемостью, исключающей возможность насыщения пор покрытия почвенной влагой и тем самым препятствующей контакту электролита с защищаемой поверхностью трубы;
- хорошей адгезией (прилипаемостью) покрытия к изолируемой поверхности трубы, что предотвращает отслаивание изоляции при местном разрушении ее сплошности, а также исключает проникновение электролита под покрытие;
- сплошностью, так как даже мельчайшая пористость в покрытии приводит к созданию электролитических ячеек и протеканию коррозионных процессов;
- химической стойкостью, обеспечивающей длительную работу покрытия в условиях агрессивных сред;
- электрохимической нейтральностью – отдельные составляющие покрытия не должны участвовать в катодном процессе, поскольку это может привести к разрушению изоляции при электрохимической защите металлического сооружения;
- механической прочностью;
- термостойкостью, определяемой необходимой температурой размягчения, что важно при изоляции
горячих
объектов, и температурой наступления хрупкости, что имеет большое значение при проведении изоляционных работ в зимнее время; - диэлектрическими свойствами, определяющими сопротивление прохождению тока, предотвращающими возникновение коррозионных элементов между металлом и электролитом и обусловливающими экономический эффект от применения электрохимической защиты;
- отсутствием коррозионного и химического воздействия на защищаемый объект;
- возможностью механизации процесса нанесения изоляционного покрытия как в заводских, так и в трассовых условиях;
- не дефицитностью;
- экономичностью (стоимость изоляционного покрытия должна быть во много раз меньше стоимости защищаемого объекта).
2.2 Классификация покрытий труб
Для наружной изоляции трубопроводов наиболее часто применяются следующие типы покрытий:
- эпоксидное;
- полиэтиленовое;
- полипропиленовое;
- комбинированное ленточно-полиэтиленовое;
- стеклоэмалевое.
2.2.1 Полиэтиленовое покрытие
Существует 4 варианта конструкций полиэтиленовых покрытий труб:
- Полиэтиленовое покрытие, наносимое по битумно-мастичному подслою (ГОСТ Р 51164–98).
- Полиэтиленовое покрытие, наносимое по изоляционному подслою на основе липкой полимерной ленты (ГОСТ Р 51164–98).
- Двухслойное полиэтиленовое покрытие, состоящее из адгезионного подслоя на основе термоплавкой полимерной композиции и наружного полиэтиленового слоя (ГОСТ Р 51164–98).
- Трехслойное полиэтиленовое покрытие, состоящее из слоя эпоксидной грунтовки (праймера), адгезионного полимерного подслоя и наружного полиэтиленового слоя (ГОСТ Р 51164–98).
Трубы с покрытием из экструдированного полиэтилена имеют следующие преимущества [5]:
- повышенный безремонтный срок службы газопроводов;
- повышенная механическая прочность;
- качество покрытия не зависит от температуры окружающей среды;
- высокий показатель адгезии к материалу труб;
- высокие диэлектрические характеристики;
- широкий температурный диапазон применения (от минус 50 °С до +80 °С).
2.2.2 Полипропиленовые покрытия
Полипропиленовое покрытие обладает повышенной теплостойкостью, высокой механической и ударной прочностью, стойкостью к продавливанию и абразивному износу [6]. Но оно имеет один серьезный недостаток – пониженную морозостойкость.
Основная область применения полипропиленовых покрытий – противокоррозионная защита "горячих" (до 110–140 °С), морских и шельфовых трубопроводов.
2.2.3 Комбинированное ленточно-полиэтиленовое покрытие
Для противокоррозионной защиты трубопроводов малых и средних диаметров (до 530 мм) довольно широко используется комбинированное ленточно-полиэтиленовое покрытие. Основное преимущество данного покрытия заключается в возможности его нанесения на трубы как в заводских, так и в трассовых условиях [7].
Температурный диапазон эксплуатации трубопроводов с комбинированным покрытием – от минус 20 до +40 °С, а прогнозируемый срок службы – 35–40 лет.
2.2.4 Эпоксидные покрытия труб
Эпоксидные покрытия характеризуются повышенной теплостойкостью, высокой адгезией к стали, отличной стойкостью к катодному отслаиванию, устойчивостью к прорезанию, сдиру, абразивному износу. Трубы с эпоксидным покрытием в течение длительного времени могут храниться под открытым небом. Затраты на нанесение эпоксидных покрытий значительно ниже затрат на полиэтиленовые и полипропиленовые покрытия труб (из состава технологических линий исключаются энергоемкие экструдеры, системы загрузки и сушки гранулированных композиций, уменьшается расход изоляционных материалов и т.д.) [8].
Основными недостатками эпоксидных покрытий являются их недостаточно высокая эластичность и низкая прочность при ударе, особенно в области минусовых температур, что в значительной степени осложняет транспортировку изолированных труб и выполнение строительно-монтажных работ в трассовых условиях.
Данный тип покрытия может быть использован при строительстве морских, шельфовых трубопроводов (в том числе, при производстве теплоизолированных и обетонированных труб), при прокладке трубопроводов на участках проколов под дорогами, при строительстве методом наклонно-направленного бурения.
2.2.5 Стеклоэмалевые покрытия труб
Стеклоэмаль – это полученная плавлением стекловидно застывшая неорганическая масса, состоящая преимущественно из окислов и нанесенная на металл в один или несколько слоев.
Стеклоэмалевые покрытия заводского нанесения применяют для защиты трубопроводов от подземной и атмосферной коррозии [9].
Анализ представленных материалов защитных покрытий показывает, что полностью всем требованиям не отвечает ни один материал, поэтому для изоляции подбирают материалы, отвечающие ряду требований, наиболее характерных для рассматриваемых условий сооружения и эксплуатации трубопровода.
В работе, учитывая повышенные требования к качеству покрытия подземных трубопроводов, доступность материалов покрытия, технологичность и сравнительно невысокую стоимость нанесения покрытия, выбирается трехслойное полиэтиленовое покрытие, состоящее из слоя эпоксидной грунтовки (праймера), адгезионного полимерного подслоя и наружного полиэтиленового слоя (ГОСТ Р 51164–98).
3 Описание конструкции червячного экструдера и технологической линии
Нанесение наружных защитных покрытий на трубы осуществляется с использованием оборудования поточных механизированных линий. В состав таких линий входят:
- роликовые конвееры;
- перекладчики труб;
- узлы очистки (дробеметная или дробеструйная установки);
- печи технологического нагрева труб (индукционные или газовые);
- узел напыления порошковой эпоксидной грунтовки;
- два экструдера – один для нанесения адгезионного подслоя, а второй – наружного слоя покрытия;
- прикатывающие устройства;
- камеры водяного охлаждения изолированных труб;
- оборудование для контроля качества покрытия.
В конструкции трехслойного защитного покрытия первым слоем наносится эпоксидная грунтовка на очищенные и нагретые до необходимой температуры трубы методом напыления, после этого последовательно наносятся экструдируемые расплавы термоплавкой композиции адгезива и полиэтилена [5].
Конструктивная схема линии нанесения экструзией внешнего полиэтиленового слоя на подготовленные трубы показана на рисунке 1.
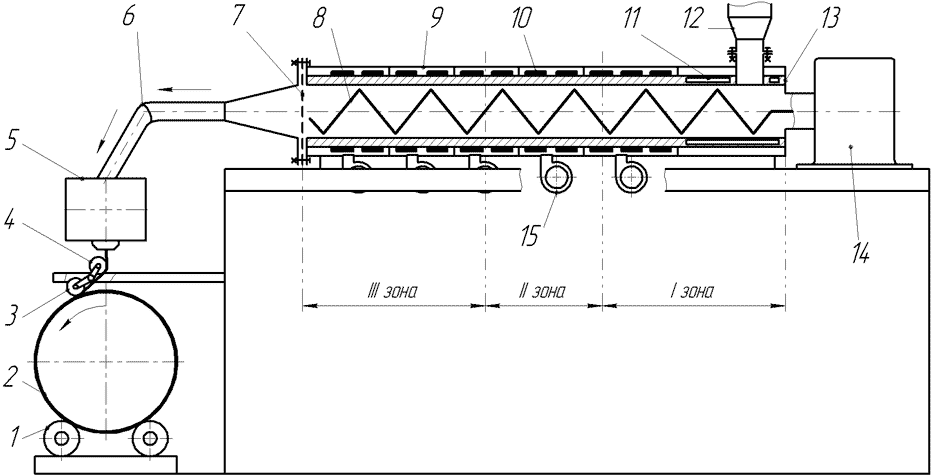
Рисунок 1 – Конструктивная схема технологической линии нанесения внешнего полиэтиленового слоя на трубы экструзией
(анимация: 10 кадров, 5 циклов повторения, 160 килобайт)
Цилиндрический корпус 13 экструдера условно разделяют по длине на три зоны:
- 1-я зона приема сырья;
- 2-я зона пластификации (плавления);
- 3-я зона гомогенизации.
Перерабатываемый полимерный материал подается из бункера 12 в 1-ю зону приема сырья и шнеком 8 продвигается вдоль корпуса. При этом по мере продвижения материал уплотняется за счет уменьшения глубины нарезки шнека [10].
В зоне пластификации материал плавится в местах контакта с поверхностью корпуса за счет теплопередачи от нагретых стенок, а также теплоты, возникающей при трении гранул полимера о шнек и стенки корпуса. Нагрев стенок корпуса осуществляется электрическими кольцевыми нагревателями сопротивления 10. Регулирование температуры по длине корпуса осуществляется воздухом, который подается вентиляторами 15 внутрь съемных защитных ограждений 9 корпуса, а участок корпуса вблизи загрузочного отверстия охлаждается водой, которая проходит по каналам 11 корпуса. Вращательное движение шнеку 8 сообщается приводом, состоящим из электродвигателя и двухступенчатого редуктора 14. Регулирование частоты вращения шнека осуществляется путем изменения частоты вращения ротора электродвигателя с использованием тиристорного преобразователя частоты.
Сетка 7 или пакет из нескольких сеток, устанавливается на выходе материала из корпуса и создает сопротивление, необходимое для повышения давления в зонах пластификации и гомогенизации. Спрессованный материал образует пробку (в зоне приема материал твердый, в зоне пластификации – плавящийся). Давление в пробке повышается до величины, достаточной для преодоления сопротивления сеток 7 и формования профиля.
В начале 3-й зоны гомогенизации материал состоит из твердых и расплавленных частиц. К концу 3-й зоны сырье становится полностью гомогенной расплавленной массой. На выходе из корпуса 13 экструдера расплав полимера через переходное устройство 6 поступает на плоскощелевую головку 5 и продавливается сквозь неё.
На выходе из плоскощелевой головки 5 пленка огибает направляющий ролик 4 и наносится на поверхность вращающейся и поступательно перемещающейся по линии трубы 2 путем ее спиральной намотки с прижатием к трубе эластичным роликом 3. Пленка должна иметь гладкую сплошную поверхность без пузырей, полос, гофр и включений [10].
Изолированные трубы при помощи роликового конвейера 1 поступают в тоннель водяного охлаждения. Затем зачищаются концы и при помощи перекладчиков трубы подаются на стеллаж готовой продукции.
4 Обзор производственной среды и условий работы экструдера
Оборудование для нанесения полиэтиленового покрытия на трубы не является пожаро- и взрывоопасным, однако его нежелательно устанавливать в помещениях с потенциально взрывоопасной средой, так как при поднесении открытого пламени полиэтилен загорается без взрыва и горит коптящим пламенем с образованием расплава и выделением газообразных продуктов горения. В условиях нормальной работы вибрация оборудования технологической линии отсутствует [11].
Факторы риска, возникающие при работе оборудования:
- незащищенные подвижные элементы оборудования;
- нагретые трубы, транспортируемые по рольгангу;
- пыль, в состав которой входят вещества, способные вызывать коррозию;
- токсичные пары.
Исходя из вышеперечисленного, поставщики сырья, добавок и расходных материалов обязаны предоставлять всю информацию о связанных с их продукцией потенциальных опасностях и о мерах безопасности, которые должны соблюдаться при ее хранении и использовании.
5 Основные проблемы при эксплуатации экструдеров. Причины и способы их устранения
Рациональные режимы работы экструдера при производстве пленки для защиты трубопроводов от коррозии напрямую зависят от требований к качеству получаемой полимерной пленки.
Основными регулируемыми параметрами являются:
- давление;
- температура;
- скорость вращения шнека.
Для своевременного выявления и устранения дефектов необходимо измерять следующие параметры:
- давление в головке;
- частоту вращения шнека;
- температуру расплава в головке;
- распределение температуры по длине корпуса;
- скорость охлаждения каждой зоны экструдера;
- скорость движения пленки;
- геометрические размеры пленки;
- температуру воды.
На работу экструзионной линии также оказывают влияние и внешние условия:
- температура окружающей среды;
- конвекция воздуха;
- колебания напряжения в электросети.
Механические изменения в экструдере (проблемы, связанные с оборудованием) влекут за собой изменения в технологическом процессе и могут быть связаны с различными системами экструдера:
- с системой привода (проявляются в изменении скорости вращения шнека);
- с системой загрузки сырья в экструдер;
- с системой нагрева и охлаждения.
Колебания производительности экструдера – это самая распространенная проблема при экструзии, поскольку она может вызываться самыми разными причинами, главными из которых являются [4, 13]:
- неравномерность подачи материала из загрузочного бункера и его последующей транспортировки в экструдере;
- недостаточная мощность нагревателей экструдера для плавления полимера;
- недостаточная температура расплава в головке;
- низкая температура корпуса;
- нарушение сплошности пленки;
- неправильно выбранная частота вращения шнека;
- колебания давления в головке.
Основные нарушения режима работы экструдера [13]:
- захват воздуха;
- образование в экструдате пустот;
- появление гелеобразных включений;
- появление продольных полос и рисок;
- посторонние включения;
- потемнение поверхности;
- тусклая поверхность;
- возникновение шероховатой поверхности;
- отклонение толщины пленки (больше или меньше) от заданного;
- низкая механическая прочность пленки;
- складки и морщины на пленке.
Неполное оснащение экструзионной линии и, в частности, экструдера контрольным оборудованием может сильно мешать быстрому и точному обнаружению неисправностей.
6 Пооперационный контроль качества изоляционных работ
Контроль качества изоляционных покрытий осуществляется пооперационно в процессе производства работ. Пригодность изоляционных материалов определяет служба технического надзора [1, 3]. При этом контролируется правильность технологического процесса разогревания битумных материалов, соответствие физико-механических свойств исходных материалов и мастик требованиям ГОСТа и СНиП. Для этого не реже одного раза в день проводят отбор контрольной пробы мастики с целью определения температуры размягчения.
Для оперативного контроля процесса экструзии и повышения качества получаемой продукции возникает необходимость определения физико-механических свойств конкретной партии перерабатываемого материала, в частности коэффициента внешнего трения.
Известные приборы для определения коэффициента внешнего трения гранулированных материалов при перемещении относительно твердой поверхности [14] не учитывают сил трения материала о стенки матрицы, что приводит к снижению их точности. Этот недостаток устранен в приборе, разработанном на кафедре машин и аппаратов химических производств ДонНТУ [15].
Конструктивная схема прибора показана на рисунке 2.
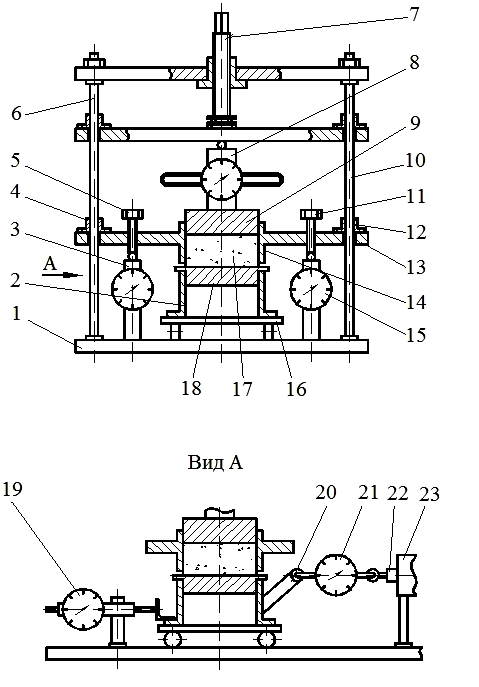
Рисунок 2 – Конструктивная схема прибора для определения коэффициента внешнего трения гранулированного материала о рабочие поверхности экструдера
Прибор монтируется на опорной плите 1 и содержит две матрицы. Нижняя матрица 2 устанавливается на тележку 16, а верхняя 14 крепится к фланцу 13. Фланец 13 устанавливается на два динамометра 3 и 15. Вместо динамометров могут быть использованы стержни с тензометрическими датчиками.
К нижней матрице 2 крепится образец 18 с исследуемой поверхностью, обращенной в сторону верхней матрицы 14. Исследуемый гранулированный материал 17 загружается в полость верхней матрицы. Винтами 5 и 11 регулируется зазор между верхней матрицей и исследуемой поверхностью. Для предотвращения перекоса верхней матрицы 14 к фланцу 13 крепятся втулки 4 и 12, которые перемещаются по направляющим стойкам 6 и 10.
Усилие на пуансон 9 и гранулированный материал создается винтом 7 и измеряется динамометром 8. Силы трения материала о стенки верхней матрицы регистрируются динамометрами 3 и 15 и учитываются при определении среднего давления исследуемого материала на исследуемую поверхность образца 18.
Перемещение нижней матрицы осуществляется механизмом, исполнительным звеном которого является шток 22 винтового редуктора 23.
Усилие, необходимое для перемещения тележки с нижней матрицей 2 измеряется динамометром растяжения 21, который крепится к тяге 20 нижней матрицы 2. Размещение тяги 20 должно быть таким, чтобы линия действия усилия перемещения лежала в плоскости сдвига исследуемого гранулированного материала относительно исследуемой твердой поверхности.
Для регистрации начала перемещения нижней матрицы 2 к опорной плите 1 крепится микрометрический индикатор часового типа 19.
Толщину слоя защитного покрытия определяют с помощью ультразвуковых толщиномеров в процессе выполнения изоляционных работ через каждые 100 м труб, в местах остановки изоляционной машины, не менее чем в четырех точках по окружности трубы или емкости и на каждой фасонной части.
Сплошность покрытия контролируют искровым дефектоскопом.
Качество защитного покрытия при приемосдаточных испытаниях проверяют через каждые 500 м, а также выборочно по требованию заказчика.
Сцепление покрытия из мастик с поверхностью защищаемого объекта контролируют адгезиметром или вручную надрезом защитного покрытия под углом 45-50° c отрывом вершины угла надреза.
При сдаче защитного покрытия трубопровода заказчику предъявляют: паспорта на каждую партию материалов или результаты лабораторных испытаний материалов; лабораторные анализы проб битумной мастики; журнал производства работ; акт проверки качества защитного покрытия. Контроль качества изоляционного покрытия готовых участков трубопровода и засыпанных грунтом осуществляется методом катодной поляризации.
При написании данного реферата магистерская работа еще не завершена. Окончательное завершение: январь 2016 года. Полный текст работы и материалы по теме могут быть получены у автора после указанной даты.
Перечень ссылок
- ГОСТ Р 51164-98 Трубопроводы стальные магистральные. Общие требования к защите от коррозии.
- ГОСТ 9.602-2005 Сооружения подземные. Общие требования к защите от коррозии.
- Противокоррозионная защита трубопроводов и резервуаров/ М. В. Кузнецов, В. Ф. Новоселов, П. И. Тугунов и др. – М.: Недра, 1992. – 238 с.
- Крыжановский В.К., Кербер М.Л., Бурлов В.В., Паниматченко А.Д. Производство изделий из полимерных материалов. – С-П.: Профессия, 2008. – 460 с.
- ТУ 1390-001-86695843-08. Трубы стальные диаметром 57-1420 с наружным двухслойным и трехслойным полиэтиленовым покрытием.
- ТУ 1394-010-17213088-03. Трубы стальные диаметром 57-1420 с наружным покрытием на основе экструдированного полипропилена для строительства магистральных нефтепроводов.
- ТУ 1390-014-05111644-98. Трубы диаметром 57-530 мм с наружным комбинированным ленточно-полиэтиленовым покрытием.
- ТУ 1390-014-86695843-2011. Трубы и детали трубопроводов стальные с наружным двухслойным эпоксидным антикоррозийным покрытием.
- ТУ 1396-001-12617190-95. Узлы стальных трубопроводов с двусторонним стеклоэмалевым покрытием. Технические условия.
- Технологическая инструкция специального процесса наружного антикоррозионного покрытия труб, 2014. – 14 с.
- Руководство пользователя экструдеров TR.100 и TR.200, редакция 1 от 26.10.2006. – 55 с.
- Лапшин В.В. Основы переработки термопластов литьем под давлением. - М.: Химия, 1974. – 271 с., ил.
- Проблемы выявления и устранения возможных дефектов в процессе получения изделий из термопластов: учебное пособие /А.Н. Садова, Т.Р. Дебердеев, О.Н. Кузнецова, О.В. Стоянов. – Казань: Изд-во Казан. гос. технол. ун-та, 2009. – 123 с.
- Булычев В.Г. Механика дисперсных грунтов. - М.: Стройиздат, 1974. – 227 с., ил.
- А.С. СССР №846637. Остапенко М.А., Рассказов Н.И., Федоренко А.Д. Прибор для исследования сопротивления сдвигу грунтов и сыпучих материалов. Б.И. №18, 1981.