Дослідження працездатного стану маханізму гидравлічних ножиць МБЛЗ
Зміст
- Вступ
- 1. Актуальність теми
- 2. Технологія розливання сталі на МБЛЗ
- 3. Способи порізки безперервнолитої заготовки і аналіз існуючих конструкцій ножиць
- 4. Патентний пошук
- 5. Призначення та конструкція гідравлічних ножиць МБЛЗ
- 6. Літературний огляд
- Перелік посилань
Вступ
Безперервне розливання сталі є найбільш ефективним металургійним процесом. Серед механізмів МБЛЗ особливу функцію виконують механізми порізки заготовки на мірні довжини, вони забезпечують зв’язок між безперервним процесом лиття та періодичним процесом пакетировки злитків. Забезпечення працездатного стану ножиць для різання заготовки є однією з першорядних завдань, що реалізуються в сталеплавильному цеху, оскільки затримка злитка або його зупинка можуть призвести до порушення роботи всього сталеразливного агрегату.
Метою даної роботи є дослідження працездатного стану гідравлічних летючих ножиць з шевронними ножами для різання заготовки на МБЛЗ.
У роботі проаналізовано процес порізки сталевої заготовки на гідравлічних ножицях, спосіб вогневої порізки, вивчена конструкція ножиць, розглянуті умови експлуатації, типові відмови, будуть виконані розрахунки напруженого стану деталей. Також буде зроблено фізичне і математичне моделювання роботи та зносу ножиць.
Результатом роботи будуть рекомендації для підтримки працездатного стану машини.
1. Актуальність теми
Сучасне виробництво вимагає забезпечення безперервного технологічного процесу через тісному зв’язку елементів процесу.
Працездатність кожного елемента є визначальним чинником у безперервній роботі всього технологічного циклу і безпосередньо впливає на можливість виконання планових замовлень у відповідності з графіком.
Одним з елементів процесу порізки прокату на мірні довжини в гарячому або холодному стані є гідравлічні ножиці. У процесі їх роботи зношується як гідравлічний привід, так і ножі, що призводить до відмов, позаплановим зупинкам і до необхідних замін ножів.
Виконання робіт з технічного обслуговування в плановому порядку дозволяє підтримувати або відновлювати працездатність даного механізму. Позапланові зупинки призводять до втрат у виробництві, прямим і непрямим витратам підприємства.
Тому метою даної магістерської роботи є дослідження працездатного стану гідравлічних летючих ножиць з шевронними ножами для різання заготовки на МБЛЗ.
2. Технологія розливання сталі на МБЛЗ
Принцип безперервного розливання полягає в тому, що рідку сталь з ковша заливають в інтенсивно охолоджувану форму прямокутного або квадратного перетину – кристалізатор, де відбувається часткове затвердіння злитка, що безперервно витягається, подальше його затвердіння відбувається при проходженні зони вторинного охолодження. Процес безперервного лиття дозволяє отримувати заготовки для прокатних станів, а також його можна поєднати з безперервною прокаткою в одному агрегаті.
Основні переваги безперервного лиття сталі в порівнянні з розливанням у виливниці полягають у наступному. Відпадає необхідність у великому парку виливниць і сталерозливних візків, у застосуванні стриперних кранів і стаціонарних машин для вилучення злитків з виливниць, установок для охолодження і підготовки складів з виливницями під розливання, в установці центрових і піддонів, а також блюмінгів і слябінгів, а в ряді випадків і заготівельних станів. Знижуються експлуатаційні витрати і витрати електроенергії, підвищується вихід придатного матеріалу внаслідок мінімальних втрат металу в скрап, ліквідації літників, різкого зменшення витрати металу на обріз в прокатних цехах і т. д. Значно підвищується якість металу внаслідок зменшення поверхневих дефектів і поліпшення структури злитка. Процес безперервного лиття піддається повної автоматизації.
Найбільш широке застосування отримали радіальні машини, що відрізняються від машин вертикального типу меншою висотою і підвищеною швидкістю лиття. Схема радіальної машини безперервного лиття заготовки приведено рисунку 1.
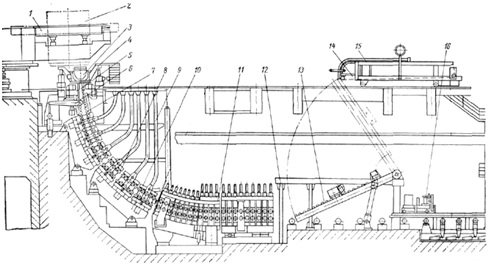
Рисунок 1 – Схема радіальної МБЛЗ
До складу машини входить сталерозливний стенд 1 для двох ковшів 2, проміжний ківш 3, встановлений на самохідному візку 4, мідний водоохолоджуваний кристаллизатор 5, механізм гойдання 6 кристаллизатора, неприводна роликовая проводка 7, радіальний ділянка 10, приводний роликової проводки з десятіроліковимі секціями 8, правильно-тягнучі ролики 11, машина 14 для введення в кристалізатор затравки 15 і рухома машина газового різання 16 [1].
3. Способи порізки безперервнолитої заготовки і аналіз існуючих конструкцій ножиць
Для різання безперервнолитої заготовки на мірні довжини в процесі руху застосовуються машини двох типів – пересувні газового різання і ножиці. Найбільш широко використовують машини газового різання, що володіють відносною простотою конструкції, малою металоємністю та можливістю швидкої заміни вузлів, що вийшли з ладу. Проте їх недоліками є значний відхід металу в шлам при різанні (1 – 2%) і велика витрата ацетилену і кисню. Поступаючись машинам газового різання по ряду показників (маса, вартість виготовлення, ремонтні витрати і т. д.), ножиці володіють перевагою, що полягає в безвідходної різанні металу.
4. Патентний пошук
Відомі різні конструкції ножиць для різання на мірні довжини безперервнолитого злитка. Нижче наведено опис конструкцій, спрямованих на забезпечення якісного різу.
У патенті № 2156676 [2] представлена конструкція летючих ножиць для різання безперервнолитого злитка (рисунки 2 і 3). Конструкція може бути використана в сталеплавильних цехах з машинами безперервного лиття заготовок (МБЛЗ) переважно радіального типу.
Дана конструкція ножиць вирішує технічну задачу маневреності летючих ножиць за рахунок можливості їх переміщення у вертикальному напрямку. Досягнутий при цьому технічний ефект – підвищення продуктивності як самих ножиць, так і МНЛЗ в цілому, підвищення якості різу.
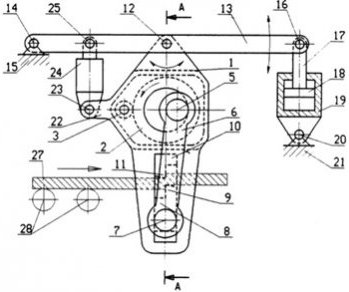
Рисунок 2 – Загальна компоновка ножиць
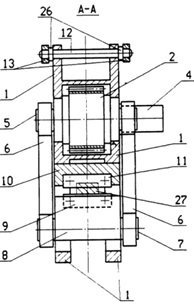
Рисунок 3 – Поперечний розріз ножиць
Летючі ножиці для різання безперервнолитого злитка являють собою корпус 1, у верхній частині якого розміщена зубчаста передача, що складається з відомою шестерні 2 і провідної шестерні 3, що приводиться в рух електроприводом 4, закріпленим безпосередньо на верхній частині корпусу 1 ножиць. На веденої шестірні 2 ексцентрично її осі встановлена верхня вісь 5 шатуна 6, його нижня вісь 7 встановлена в супорті 8 нижнього ножа 9.
Кріплення 10 верхнього ножа 11 виконано нерухомим щодо корпусу 1 ножиць. Своєю верхньою частиною ножиці підвішені за допомогою несучої шарнірної опори 12 до траверси 13, яка своїм одним кінцем за допомогою опорного шарніра 14 кріпиться на нерухомому елементі 15 конструкції МБЛЗ, а іншим кінцем – за допомогою осі-шарніра 16 з’єднана зі штоком 17 поршня 18 основного гідроциліндра 19 переміщення траверси. Сам же основний гідроциліндр 19 переміщення траверси за допомогою головного опорного шарніра 20 закріплений на нерухомій опорі 21.
Верхня частина корпусу має бічний приплив 22, який шарнірно з’єднаний з допомогою осі 23 з нижньою частиною гідроциліндра 24 переміщення ножиць, який в свою чергу також підвішений на траверсі 13 за допомогою шарніра переміщення 25. Позиції 12, 13, 14 і 25 кріпляться за допомогою обмежувальних шайб 26.
Запропоновані летючі ножиці для різання безперервнолитого злитка підвищують технологічні можливості процесу різання, знижують їх металоємність, виключають вплив процесу розрізання безперервнолитого злитка на сам процес безперервного лиття, підвищують якість поверхні різу і довговічність ножів. До недоліків ножиць можна віднести одночасне наявність електроприводу і гідроциліндрів, досить складна конструкція.
У патенті № 2033300 представлено пристрій для різання безперервнолитих зливків [3]. Цей пристрій направлено на усунення недоліків конструкції ножиць для різання безперервнолитих зливків в потоці, що включає хитну станину, встановлену в шарнірних опорах, нижній рухливий супорт, що охоплює своїми напрямними стійками станину, два гідроциліндра ріжучого механізму, два гідроциліндра зворотного ходу супорта, гідроциліндр механізму хитання станини, пов’язаний з нею шатуном, і два гідроциліндра притиску, з’єднаних з лапами. Ріжучий механізм забезпечений двома ножами, з яких один закріплений в супорті, а другий у верхній траверсі станини. Всі гідроциліндри плунжерного типу, за винятком гідроциліндра гойдання станини, двосторонньої дії. Плунжери гідроциліндрів з’єднані з нижнім супортом відповідно стійками з сферичними опорами.
При відхиленні станини від вертикального положення в процесі різання злитка гидроцилиндр гойдання повертає пристрій у вихідне положення.
Недоліком відомого пристрою є його складність. Це пояснюється необхідністю застосування гідроциліндра гойдання станини пристрої для її повернення у вихідне положення. У цих умовах необхідно застосування системи спостереження за переміщенням поршня гідроциліндра двосторонньої дії. При збої в роботі системи стеження гідроциліндра гойдання відбуваються недорези злитка або затримки в поверненні пристрою в початкове положення для початку нового різу.
Авторами патенту №2033300 запропоновано між корпусом станини і кожною стійкою встановити пружини в горизонтальному напрямку, що дозволить спростити конструкцію внаслідок усунення гідроциліндра гойдання станини разом з системою стеження за ходом поршня гідроциліндра, а також полегшити процесу її обслуговування за рахунок наявності пружин між стійками і корпусом станини . У цих умовах повернення пристрою у вихідне положення буде відбуватися автоматично під дією одних пружин.
Описаний пристрій для різання безперервнолитих зливків зображено на рисунках 4 і 5.
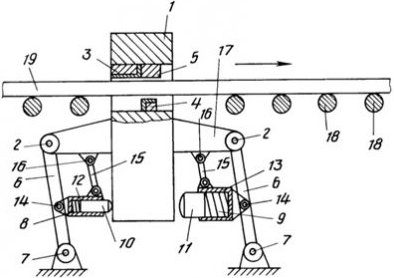
Рисунок 4 – Початкове положення пристрої для різання безперервнолитих зливків
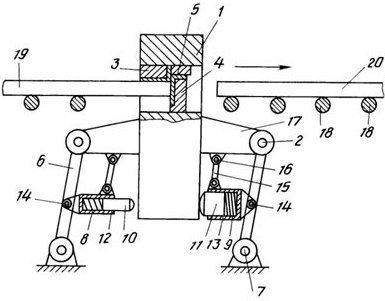
Рисунок 5 – Положення пристрою в момент закінчення різання злитка
Пристрій для різання безперервнолитих зливків складається з станини 1, шарнірних опор 2, ріжучого механізму з ножами 3 і 4, притиску 5 злитка, стійок 6, шарнірних опор 7, пружин 8 і 9, плунжеров 10 і 11, корпусів 12 і 13, шарнірів 14 , тяг 15, шарнірів 16, кронштейнів 17. Позицією 18 позначені ролики, 19 безперервнолитої злиток, 20 безперервнолита заготовка.
Застосування запропонованого пристрою спрощує конструкцію гідравлічних ножиць і полегшує процес їх обслуговування. При цьому вартість пристрою і експлуатаційні витрати зменшуються на 8%. Однак наявність великої кількості шарнірних з’єднань в конструкції буде в процесі експлуатації призводити до зниження якості різу через неминуче збільшення зазорів в результаті зношування шарнірів.
5. Призначення та конструкція гідравлічних ножиць МБЛЗ
Гідравлічні ножиці призначені для обрізання на ходу дефектних переднього і заднього кінців безперервнолитої заготовки та різання на мірні довжини. Ножиці встановлюються на кожен струмок МБЛЗ [4].
Загальний вигляд ножиць наведено на рисунку 6.
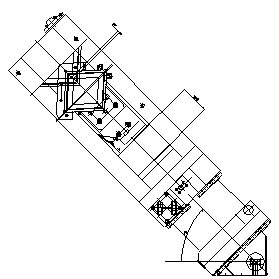
Рисунок 6 – Загальний вигляд механізму гідравлічних ножиць
Ножиці складаються зі зварного водоохолоджуваного корпусу, на верхній перемичці якого закріплений верхній нерухомий ніж, з’єднаний болтами з корпусом. На штоку гідроциліндра різу закріплений нижній ніж, рухливий.
Ножиці встановлюються під кутом 45° до горизонту в площині різу, вони спираються в нижній частині на циліндричні направляючі, а у верхній частині опорним роликом на направляючу планку, що знаходиться на порталі.
Направляючі для гідравлічних ножиць складаються з двох зварних стійок, що встановлюються на фундамент, циліндричної хромованої балки, що спирається на ці стійки і двох корпусів, що переміщаються по циліндричній поверхні балки, до яких у свою чергу кріпляться гідравлічні ножиці. Для захисту циліндричної напрямної від окалини, води і випадкових ударів на корпусах встановлюються кожуха.
Гідравлічний циліндр призначений для горизонтального переміщення ножиць по циліндричної напрямної (вперед і назад) при різанні заготовки в русі. Він встановлюється на рамі, а штоком шарнірно з’єднується з гідравлічними ножицями.
Для синхронізації переміщення гідравлічних ножиць і руху безперервнолитої заготовки в корпус гідроциліндра вмонтований спеціальний кодовий датчик, який регулює швидкість подачі робочої рідини в поршневу або штокову порожнини. Для плавної зупинки гідравлічних ножиць в крайніх положеннях в гидроцилиндре переміщення ножиць є гальма, регулюванням яких і здійснюється плавність зупинки.
Безперервнолита заготовка по подводящему рольгангу подається до ножиць, встановленим під кутом 45° на кожному струмку шестиструмкової МБЛЗ, і мають можливість переміщатися в напрямку руху заготовки і назад. При досягненні заданої довжини переднього кінця рухомій заготовки, по команді від датчика включаються одночасно гидроцилиндр переміщення ножиць і гідроциліндр різу, який піднімає супорт з нижнім ножем і заготівлею до верхнього нерухомого ножа. Заготівля в русі розрізається. За сигналом кінцевого вимикача гидроцилиндр різу реверсують, і ніж з відрізаним переднім кінцем опускається в нижнє положення. Ножиці, зробивши повний хід вперед, реверсують, тобто повертаються у вихідне положення. При цьому відрізаний передній кінець заготовки, що знаходиться на передавальному жолобі, що рухається заготівлею стикається з передавального жолоби в короб для обрізу.
Система вимірювання мірної довжини заготовки позиціонує заготовку на лінії різу і дає команду на включення механізмів ножиць. Порізка рухомої заготовки на мірні довжини здійснюється аналогічно обрізку переднього кінця з тією відмінністю, що відрізана частина транспортується роликами рольганга за ножицями із зони різання зі швидкістю більшою, ніж рухається заготовка.
На анімованому рисунку 7 зображена конструкція діючих ножиць, вироблених Новокраматорський машинобудівний завод, а так само фото готової продукції.
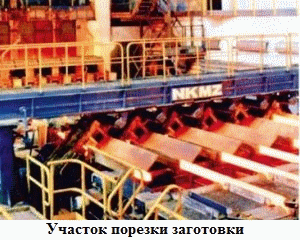
Рисунок 7 – Конструкція гідравлічних ножиць НКМЗ
(Анімація складається з 4 кадрів з затримкою 450 мс між кадрами;
кількість циклів відтворення 10)
6. Літературний огляд
Існує багато статей, присвячених роботі гідроциліндра при високій температурі, а також дослідженням процесу порізки сортових заготовок на МБЛЗ.
У статті Дослідження енергосилових параметрів процесу поперечного поділу безперервнолитих сортових заготовок на ножицях
[5]
проведені експериментальні дослідження процесу різання безперервнолитих сортових заготовок квадратного перетину на лабораторних ножицях, залежно від
форми ножів і розташування профілю та встановлено їх вплив на максимальну величину сили різання і роботу, расходуемую на поділ.
У статті Аналіз відмов вузлів приводу холодильника МБЛЗ
[6] наведені дані про відмови вузлів приводу холодильника
машини безперервного лиття заготовок. Розглянуто причини несправностей та ремонтні впливу стосовно гідравлічному приводу даного механізму.
У статті Чисельна методика розрахунку енергосилових параметрів процесу гарячої поперечного різання безперервнолитих сортових заготовок
[7]
на основі чисельного підходу, що полягає в розбитті поперечних перерізів на кінцеве безліч елементарних обсягів та організації
подальшого вирішення для кожного з них, розроблена математична модель енергосилових параметрів процесу поперечного різання безперервнолитих заготовок
на їх мірні довжини. Показаний складний характер розподілів сили різання в залежності від ходу ножів і температурно-деформаційних параметрів, дана
кількісна оцінка ступеня уточнення загальноприйнятих теоретичних рішень.
У статті Удосконалення режимів роботи гідравлічних пресів з насосно-акумуляторним приводом на холостому ході
[8]
розглянута математична модель холостого ходу, використання якої в системах автоматичного управління гідравлічними пресами забезпечується досягнення
оптимальних параметрів процесу наближення рухомого поперечки до поковки, виключаючи можливість виникнення рідинного голодування робочих циліндрів.
Виконано аналіз коефіцієнтів математичної моделі, що дозволяє на етапі проектування системи управління пресом підібрати оптимальні величини основних
параметрів і режими здійснення холостого ходу без побудови фізичної моделі. Розроблено нові технічні рішення, впровадження яких дозволить забезпечити
прискорений заповнення робочих циліндрів рідиною низького тиску. Наведено практичні рекомендації для їх реалізації у виробництві.
У статті Аналіз енергосилових параметрів процесу поділу на ножицях сортових профілів в гарячому стані
[9]
проведено аналіз енергосилових параметрів процесу поділу квадратної заготовки при різанні паралельними ножами і фасонними на кут. Запропоновано
методику розрахунку сили різання для цих схем реалізації процесу, яка дозволяє уточнити величину максимальної сили, а також отримати характер її
розподілу по ходу реалізації процесу. Виконано порівняння запропонованої методики з існуючими. Наведено результати експериментальних досліджень,
які добре узгоджуються з отриманими теоретичними рішеннями. Результати роботи можуть бути використані при подальших дослідженнях процесу гарячого
різання металу на ножицях з метою розширення уявлення про процес різання і підвищення ступеня точності енергосилових параметрів процесу.
У статті Математичне моделювання енергосилових параметрів процесу поперечного різання круглих сортових профілів
[10]
проведено аналіз енергосилових параметрів процесу поділу довгомірних круглих заготовок при їх поперечної різанні на ножицях з паралельними і фасонними ножами.
У статті Теоретичний аналіз процесу гарячого різання на ножицях
[11] виконано теоретичний аналіз процесу гарячого різання
на ножицях з паралельними ножами.
У статті Моделювання ударної різання злитка
[12] розглянуті процедура і результати математичного моделювання ударної
різання злитка. Представлена нова математична модель технологічної зони ударної різання, проаналізовано механічний стан об’єктів технологічної зони та
закономірності їх взаємодії.
У статті Теоретичний аналіз бічного зусилля при гарячої різанні паралельними ножами
[13] виконано теоретичний аналіз
процесу поділу металу в ході гарячої різання на ножицях з метою розширення уявлення про протікання процесу та оцінки бічного зусилля, що діє на ножі.
У статті Підвищення якості різання прокату шевронними ножами
[14] виконано теоретичний аналіз процесу різання
товстих листів шевронними ножами. В основу дослідження покладено метод кінцевих елементів, на базі якого було розроблено математичну 3D-модель процесу
різання товстих листів шевронними ножами.
У статті Аналіз напружено-деформованого стану металу при поділі квадратного профілю на ножицях
[15] виконані теоретичні
дослідження напружено-деформованого стану металу при поділі квадратних профілів на ножицях з метою розширення уявлення про протікання процесу шляхом аналізу
напружено-деформованого стану металу в осередку різання з урахуванням технологічних особливостей реалізації. В основу дослідження покладено метод кінцевих
елементів. Були розроблені математичні 3D моделі процесу різання квадратного профілю паралельними і фасонними ножами. Розглянуто особливості розподілу і
приведена якісна і кількісна оцінка розподілів інтенсивності пластичних деформацій, інтенсивності напружень і показника жорсткості напруженого стану. Розширено
уявлення про процеси, що протікають в металі при поділі його на ножицях. Вказується на можливість розвитку методу розрахунку сили різання і підвищення його
точності. Результати роботи можуть бути використані при подальших
У статті Імітаційне моделювання спектра робочого навантаження процесу поперечного різання сортових профілів на ножицях
[16]
проведено обґрунтування застосування імітаційного моделювання, зокрема методу Монте-Карло, для оцінки ступеня розкиду технологічних навантажень і урахування
реальної картини навантаження сортових ножиць. Виділено найбільш вагомі фактори варіювання, що дозволяють кількісно оцінити характер формування спектра
робочих навантажень. Вироблено моделювання спектра робочого навантаження для різних профілів в перерахунку на еквівалентний за площею квадрат. Отримані
результати можуть сприяти подальшим дослідженням процесу різання фасонних профілів на ножицях і підвищенню надійності їх роботи в реальних виробничих умовах.
При написанні даного реферату магістерська робота ще не завершена. Остаточне завершення: грудень 2015 року. Повний текст роботи та матеріали по темі можуть бути отримані у автора або його керівника після вказаної дати.
Перелік посилань
- Машины и агрегаты металлургических заводов. В 3-х томах. Т. 2. Машины и агрегаты сталеплавильных цехов. Учебник для вузов / Целиков А. И., Полухин П. И., Гребенник В. М. и др. 2-е изд., перераб. и доп. – М.:
Металлургия
. 1988., – 432 с. - Парент РФ № 2156676 Филатов А. А., Ванинский М. М., Середкин В. П., Жуков А. А. // Летучие ножницы для резки непрерывнолитого слитка // Патент России № 2156676.
- Патент РФ № 2033300 Рубинштейн Ю. Е., Бойко Ю. П., Лебедев В. И., Худанов В. К., Блинов А. П., Бояринцев А. В., Кузьменко С. Г. // Устройство для резки непрерывнолитых слитков // Патент России № 2033300.
- Установка ножниц. – Руководство по эксплуатации. – НКМЗ.
- Сатонин А. В. Исследование энергосиловых параметров процесса поперечного разделения непрерывнолитых сортовых заготовок на ножницах: Вып. 35, 2011. – (Сб. науч. тр. ДонГТУ) // Сб. науч. тр. ДонГТУ. – С. 131–137.
- Сидоров В. А. Анализ отказов узлов привода холодильника МНЛЗ / В. А. Сидоров // Металлургические процессы и оборудование. – 2009. – № 2 (16). – С. 28–33.
- Сатонин А. В. Численная методика расчета энергосиловых параметров процесса горячей поперечной резки непрерывнолитых сортовых заготовок / А. В. Сатонин, С. М. Стриченко, А. В. Завгородний, А. А. Житлова // Обработка материалов давлением: сборник научных трудов ДГМА. – Краматорск., – 2011. – № 2 (27). – С. 43–46.
- Шинкаренко О. М. Совершенствование режимов работы гидравлических прессов с насосно-аккумуляторным приводом на холостом ходе / Шинкаренко О. М., Корчак Е. С. // Обработка материалов давлением: Обработка материалов давлением: сборник научных трудов ДГМА. – Краматорск., – 2011. – № 2 (27). – С. 190–194.
- Денищенко П.Н. Анализ энергосиловых параметров процесса разделения на ножницах сортовых профилей в горячем состоянии / Денищенко П.Н., Боровик П.В., Петров П.А., Стриченко С.М. // Обработка материалов давлением: сборник научных трудов ДГМА. – Краматорск., – 2011. – № 4 (29).
- Петров П. А. Математическое моделирование энергосиловых параметров процесса поперечной резки круглых сортовых профилей / Петров П. А., Стриченко С. М., Бойко И. И., Сытник А. А. // Обработка материалов давлением: сборник научных трудов ДГМА. – Краматорск., 2012. – №1 (30). – С. 227–232.
- Боровик П. В. Теоретический анализ процесса горячей резки на ножницах / Боровик П. В. // Обработка материалов давлением: сборник научных трудов ДГМА. – Краматорск., 2012. – № 1 (30). – С. 218–222.
- Ворожко С. С. Моделирование ударной резки слитка / Ворожко С. С., Кладова О. Ю., Нарыжный А. Г., Слюсаренко Т. В. // Обработка материалов давлением: сборник научных трудов ДГМА. – Краматорск., 2012. – № 3 (32). – С. 185–191.
- Боровик П. В. Теоретический анализ бокового усилия при горячей резке параллельными ножами / Боровик П.В. // Обработка материалов давлением: сборник научных трудов ДГМА. – Краматорск., 2012. – № 4 (33). – С. 132–135.
- Боровик П. В. Повышение качества резки проката шевронными ножами / Боровик П.В. // Обработка материалов давлением: сборник научных трудов ДГМА. – Краматорск., 2013. – № 1 (34). – С. 245–250.
- Боровик П. В. Анализ напряженно-деформированного состояния металла при разделении квадратного профиля на ножницах // Обработка материалов давлением: сборник научных трудов ДГМА. – Краматорск., – 2014. – № 2 (39).
- Сатонин А. В. Имитационное моделирование спектра рабочей нагрузки процесса поперечной резки сортовых профилей на ножницах / Сатонин А. В., Боровик П. В., Петров П. А. // Обработка материалов давлением: сборник научных трудов ДГМА. – Краматорск., – 2014. – № 2 (39).
- Электронный ресурс www.findpatent.ru.