Abstract
Содержание
- Introduction
- 1. Theme urgency
- 2. Goal and tasks of the research
- 3. An approach to the unification of synthesis of Moore FSM on FPGA
- Conclusion
- References
Introduction
Ukraine in the early twenty-first century was in a difficult economic situation. The aggravation of relations with Russia, the worldwide rise in price of energy processes, outdated, energy-intensive equipment - it constitutes a threat to the energy independence of our country.
Leaders of the state stakes in overcoming the energy crisis in the nuclear power industry and the development of alternative energy sources.
Both of these ways are wrong, require huge capital investments, and are not capable in the next few decades to provide an uninterrupted supply of cheap energy of the population and the national economy.
1. Theme urgency
Cooking tapiwa includes a set of pieces of equipment and transport mechanisms that provide a continuous supply of prepared for fuel combustion in the boiler burner. Preparation of the solid fuel occurs in two stages: first, crushing lumps Fuel crusher to a maximum particle size of 15-25 mm (Granulated) and then grinding coal mill to regrind to the smallest of the coal dust (dust preparation). The last stage is carried out directly for the boiler in the boiler room, and pulverizing equipment is included in the boiler plant. Fuel drying before grinding is beneficial to the operation of the mill. Performance hammer mills increased by 20% compared with mills operating on the wet fuel approximately 2-fold increased resource beat. Reduced grinding mill productivity by increasing the humidity of fuel can be explained by the fact that the fuel is wet milling in the presence of a large amount of plastic deformation, difficult to obtain finished coal dust. According VTI found that the larger the difference between fuel moisture milled hygroscopic humidity value, the greater the reduction in performance of the grinding mill. Preliminary drying of fuel with the removal of the external moisture by only 3-5% dramatically improves the free-flowing properties, eliminates difficulties transporting coal to fuel paths and movements in bunkers, increased heat of combustion of fuel. Thus, the preliminary drying coal is an integral part of its enrichment and issues, improve equipment reliability fuel supply, coal-pulverization systems and, ultimately, the entire boiler plant.
2. Goal and tasks of the research
The aim of the study is to analyze the work of pulverizing system of boilers TPP-312A for a 300 MW unit at Zuevskaya TPP in order to improve the technical and performance ekoneomicheskih station
Main tasks of the research:
- Analysis of the dust preparation system.
- Select ways to improve efficiency dust system.
- Select the method of research.
Research object: Pulverizing system
Research subject: Study modernization of pulverization, reducing fuel moisture.
3. Overview of Research and Development
The system pulverization Zuevskaya TPP.
The boiler is equipped with two individual systems pulverization with an industrial container (Figure 1.1). the supply of coal to the mill produced raw coal belt feeders belt width 2000 mm. Each dust system is equipped with a ball mill drum type W - 50A milling capacity of 80 t/h (with the subtleties of the dust of the separator R9o = 28%, ball load 80 tons and ventilation 170×103m3/h), a dust separator SPTSV-5500/2000, a cyclone type ZN-15-4250. Motor power 1600 kW mill.
dusty mixture is conveyed mill fan CF-180/1100, of 170×103m3/h, total head of 900 kg/m, speed 1480 rev/min. MB-Motor DAZO 2-16-59-4U1 power 1250 kW. To increase the explosion at the coal-pulverization systems provides supply of flue gases from DRG. Filing dust pyleprovody carried sixteen dust feeders type PIL-10, the maximum capacity of 14 t/h each. On one pyleprovod (burner) is installed on the two dust feeders.
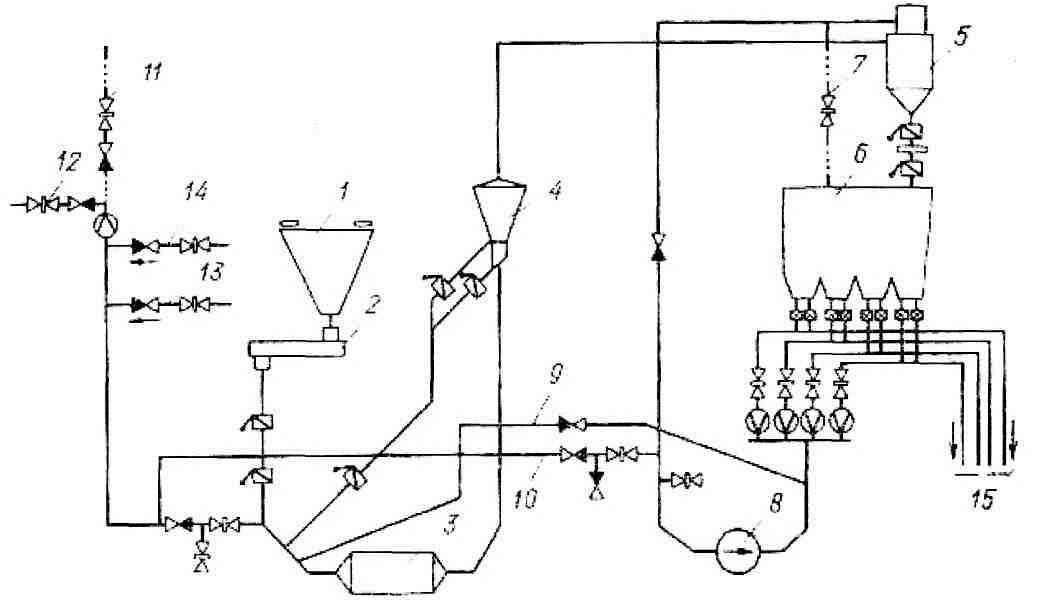
Figure 1.1. The system of the boiler pulverizing CCI - 312 A.
1 - bunker crude coal; 2 - belt feeder raw coal; 3 - Mill; 4 - separator; 5 - cyclone; 6 - dust hopper; 7 - vlagootsos dust from the hopper; 8 - fan mill; 9 - recirculation line; 10 - bypass dust system; 11 - hot air after the air heater; 12 - additive cold air blowing from the fan; 13 - hot flue gases from the flue after water economizer of smoke exhaust gas recirculation; 14 - cold flue gases from the flue after the axial smoke exhaust from the boiler smoke exhaust gas additive; 15 - pyleprovody to the burners.
The boiler is equipped with two two-speed blowers type VDN -32 B performance 45,6×103m3/h, total head of 475 kg/m2. Blower Motor Series DAZO 1916/10, 1100/625 kW capacity, speed 730/590 rev / min. Capacity control is performed axial guide vanes smoke exhausts recirculation duct to the mill.
Removing the products of combustion of fuel from the boiler and transport them to the chimney is made by two axial smoke exhausts type DOD - 31F Performance 9850×103m3/h, total head 480 kg/m2, when the flue gas temperature 100C and rotor speed 495 r/min. Exhauster asynchronous motor series DAZO 1910 - 12U1, 1700 kW power.
In order to reduce flue gas temperature at the inlet to screen to prevent slagging and KPPVD SPP. provided flue gas recirculation of the furnace up. The flue gases are fed through slots in the furnace with two smoke exhausts recirculation type DG - 200 - 500 of 200×103m3/h, total head of 480 kg/m2 and speed 985 r/min. The flue gases are selected and before the economizer after the smoke exhausts are cleaned from ash zolokontsentratorah.
The additive flue gases in coal-pulverization systems can be carried out by two types of smoke exhausts NAM\17 performance 74,5×103 pressure of 365 kg/m2 and a speed of 985 / min. The flue gases are selected for the additive after the main smoke exhausts. To clean the flue gases from the electrostatic precipitator ash are two types of HS-3-4-177.
gas path of the boiler is shown in Figure 1.2.
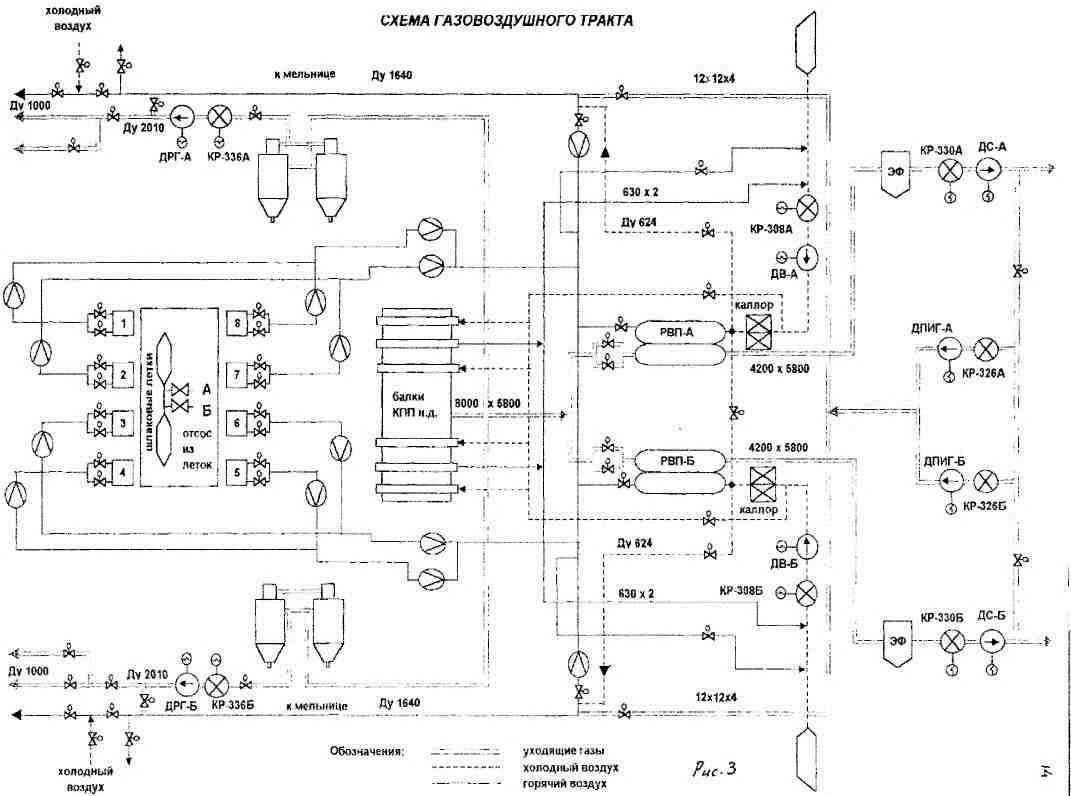
Conclusion
Toplivoprigotovleniya fuel system and provides continuous and uninterrupted supply of fuel to the power station, as well as preparing it for use. In assessing the effectiveness of technological schemes of preparation of fuel for combustion using thermodynamic method one of the main exponents of thermodynamic perfection of the system is the exergy efficiency (efficiency), defined as the ratio of useful to the technical effect of the expended. In this case, a useful technical effect can be considered to obtain the desired coal dust humidity and temperature. The paper discusses the system toplivoprigotovleniya with intermediate bunker coal dust and drying of fuel combustion products, are selected from the flues of the boiler unit. In systems of this type are most commonly used ball mill drum. Drying fuel combustion increases the temperature of the drying agent, while providing a fire and explosion safety system, which is explained by a low content of oxygen in the drying agent and dry coals allows virtually any moisture.
List of sources
- Коузов П.А., Скрябин Л.Я. Методы определения физико-химических свойств промышленных пылей/ Л.: Химия 1983 - 143 с.
- Белоусов В.Н., Смородин С.Н., Смирнова О.С. Топливо и теория горения/СПб., 2011 - 84 с.
- Лебедев Б.В. Технология сжигания органического топлива/ Томск: Изд-во Томского политехнического университете, 2012 - 148 с.
- Михайлов Н.М. Вопросы сушки топлива на электростанциях/ М.,Л: - 1957 - 153 с.
- Сажин Б.С. Основы техники сушки/ М.: Химия 1984 - 320 с.