Abstract
Ñontents
- Introduction
- 1. Topicality
- 2. The purpose and objectives of the study, expected results
- 3. A review of research and development
- 3.1 Theoretical bases
- 3.2 Classification dryers
- Conclusions
- Source List
Introduction
In various sectors of the economy are widespread process of removing the liquid from the surface or from the inner layers of different materials. As retentate fluid may be water, methanol, gasoline and the like. N. Among the existing methods of particular materials dewatering takes place thermal drying. Drying of various materials and products in the industry is important, since on it depends largely on the quality of products. For example, buckets to be filled with liquid metal, their retainers, molds and cores are dried to remove the moisture introduced during manufacture, together with a binder solution and materials. In addition, pre-dried granular raw material for the manufacture of refractory molds and cores.
The drying is a process in which the moisture in the material changes from a liquid to gaseous state and is removed to the environment. To speed up this process to dry the material of heat. The application of heat may be performed by radiation, convection or thermal conduction and in accordance with this distinction tion radiative, convective and conductive drying, and drying under generation in the body of the dried material. The most widely used dryers (often called dryers or drying), in which the convective drying. In these plants, the gaseous medium not only allows removal of moisture from the surface of the dried material, but also serves as a coolant. This medium is referred to as a drying agent. During drying the moisture content varies, in the dried material, and a drying agent. Sushil to dry bulk materials are performed mainly as installation of continuous action. These include drum driers, driers for drying and drying installations pnevmopotoke fluidized bed. By the nature of heat transfer in the work area, these devices are very different among themselves that affects their design and performance parameters. P>
1. Relevance of the topic
In the foundry for the production of molds traditionally used silica sand. Drying of sand is a major process steps in the preparation of foundry molding mixtures. Quartz sand can be supplied to the production with 12% humidity and contain, as impurities, clay, dust particles and coarse inclusions. Therefore, quartz sand for use in foundry must possess certain properties humidity and temperature, especially for the manufacture of molds for casting of complex parts made of nonferrous metals. By molding sand special requirements. It should be dry and free of impurities (clay, silt) have a certain particle size distribution, and others. For the sand used in fomovanii, consider the following technological features: Sand humidity - no more than 0.5%; sand temperature - not more than 30 ° C, otherwise the dryer must be provided a refrigerator for cooling the sand; During the summer in the southern and eastern regions of Ukraine outside temperature often exceeds 40-50S so there is the problem of cooling the quartz sand to the desired temperature. Therefore, the main objective of this thesis is to improve the cooling efficiency of the molding sand in a hot summer temperatures Visoko region.
2. The purpose of the study
The aim is to improve the efficiency of cooling the molding sand at high tempera summer hot regions.
3. Overview of Research and Development
3.1 Theoretical Foundations
The intensity is determined by the speed of drying, drying, which is approaching a state of equilibrium and usually decreases to zero. The intensity of the drying depends on a number of factors indicating the real complexity of the drying process, especially in terms of production, the difficulty of obtaining for him adequate mathematical description. The greatest influence on the drying process have factors that determine the drying material as the object of drying. They characterize a material resistance to moisture transport within it from its surface to the environment, with the effect of moisture binding material, the material's ability to perceive the heat supplied to it. Such factors include the internal structure of the material, its thermal properties, and the size, shape and condition of the outer surface. The strongest influence on the drying process has the internal structure of the material. Significantly affect the drying process parameters of the drying agent (coolant) temperature, relative humidity (relative pressure), the speed of movement relative to the material pressure. P>
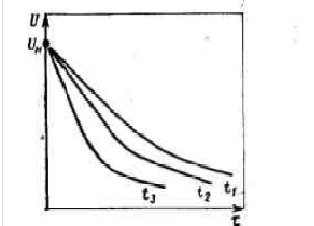
Figure 1. The dependence of the kinetic curve of the drying temperature of the coolant with respect to moist body t1> t2> t3. P>
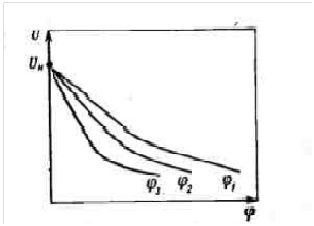
Figure 2 The dependence of the kinetic curve of the relative humidity of the drying coolant relatively moist body. P> div>
Among the factors influencing the drying are the concentration and composition of the impurities contained in the material is removed from the liquid. Impurities alter the thermophysical properties of the fluid (viscosity, thermal conductivity, etc.), Correct interaction with the liquid surface of solid skeleton and thereby affect the rate of migration of moisture from the interior of the body to the periphery. The drying of dispersed materials in the device layer on a weighted rate of drying affects the interaction of the material particles together. P>
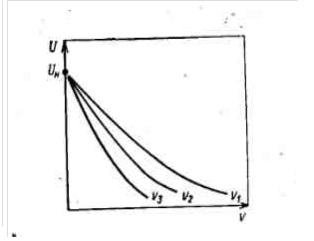
Figure 3 The dependence of the kinetic curve of the speed of drying the coolant with respect to the wet body. P> div>
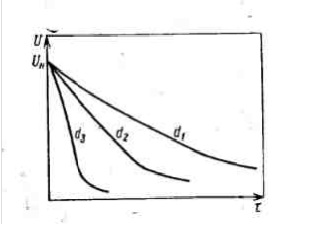
Figure 4 The dependence of the kinetic curve of the drying of the size of a dried body. P> div>
In its simplest form, the drying process is carried out such that the drying agent is heated to the maximum allowable temperature for the material to be dried, the drying apparatus used singly. This process is called the primary. In the process of drying wet material moisture is transferred as a liquid or as a vapor. The study of the laws of the transfer of moisture and heat can go two ways:
1) on the basis of molecular-kinetic method, ie, study the microscopic picture occurring in this process and comprehension of the physical essence of individual components of a complex phenomenon.
2) based on the concepts of thermodynamics process. Learning macroscopic properties of bodies and systems of bodies and processes of their interaction, not interested in the behavior of individual molecules.
The transfer of a gaseous substance may occur due to molecular by chaotic movement of individual molecules (diffusion) or by directed movement of molecules when each moving independently of each other (effusion), and the molar through when moving groups, clusters of molecules under a differential pressure at different points of the body. For the drying of materials that require high humidity of the drying agent and the low temperatures, the device used to ensure the recycling (recovery) of the exhaust air to the dryer and the dryer with an intermediate heated air between the individual stages (or zones), and a simultaneous recycling it. Convective drying mechanism can be summarized as follows. When administered to a moist body in the heated gas heat is transferred to the surface of the material due to the temperature difference therebetween, heat, and moisture evaporation. This increases the partial pressure near the surface of the body, which leads to the transfer of moisture vapor into the environment. As a result of the evaporation of moisture from the surface and removing the resulting vapor concentration gradient of moisture in the material, is the driving force of internal displacement it from deep layers to the surface evaporation. When moving violation occurs due to the moisture of a solid substance, which requires additional energy costs in excess of that required for vaporization. Therefore, the speed of the process depends on the nature or form of communication moisture with dry substance of the material.
3.2 Classification dryers
Industrial dryers are classified according to the following criteria:
1. By way of heat to the material: convection. conductive, radiation, electromagnetic, combined (convection, radiation, convection -radiatsionno - high - frequency, and so on. n.);
2. By the time the operation: continuous, batch, semi-continuous operation;
3. By design: chamber, shaft, tunnel, drum, tube, tape, weighted layer, spray, freeze, and others.
From the classification most widely convective dryers. These settings are divided into several groups:
1. As applicable to the drying agent: air, for combustion (flue) gases on the non-condensable gases in the process of drying (nitrogen, helium, superheated steam, etc.);
2. Under the scheme of movement of the drying agent to: single-band (with a single use of the drying agent, recirculation), multi-zone (an intermediate heated drying agent, in its recirculation zones, recirculation between zones and the like);
3. With the pressure in the drying chamber to: atmospheric, vacuum;
4. According to the direction of movement of the drying agent with respect to material: through-flow, counter-current, cross-flow, reversible.
Conclusions
Thus, this paper discussed topical issues of energy saving in the drying materials. Work for the best work of the technical installation, which in turn will reduce its consumption and lead to cost savings. In writing this essay master's work is not yet complete. Final completion: January 2016. The full text of work and materials on the topic can be obtained from the author or his manager after that date.
Source List
1. Kurbatov YL, Vasilenko Yu Metallurgical furnace metallurgical furnace: a tutorial / Donetsk: SHEI "DonNTU", 2013. - 388 p.
2. Kazantsev EI Industrial furnaces / Reference book for the calculation and design / Moscow "Metallurgy", 1975. 368 pp.
3. M. Glinka The general theory of operation of furnaces / Metallurgy, Moscow G-35, 1959. 416 pp.