Abstract
- 1. Theme urgency
- 2. The purpose and research problems
- 3. Review of research and development
- 4. Improving calibration for forming pipes with diameter 508×16mm steel 10G2FB
- Conclusions
- The list of the used litterature
1. Theme urgency
Extraction and processing of oil and gas are directly related to their transportation and, therefore, require the production of large volumes of welded pipes a wide assortment.
Improving the quality of pipes in part improve the performance of strength properties of metal, and in terms of increasing the dimensional accuracy is significant reserve enhancing their performance. Therefore, when the Welding Shop №2 JSC "HTZ" was put into operation bending machine «Haeusler», great importance was attached to it to ensure the dimensional accuracy of the finished tubes. Improving the method for calculating rational modes of forming tubular billets is an urgent task .
An urgent task is also a science-based definition of the parameters that require installation of supporting bridges, as well as the improvement of conditions forming tubular billets for welded pipes with diameter 450-700 mm in the three-roll bending machine «Haeusler» JSC HTZ.
2. The purpose and research problems
The aim is the improvement of labor conditions, bnyh molding blanks for welded pipes with diameter of 508×16mm and 660×15mm steel 10G2FB on a triple roll bending machine «Haeusler» JSC HTZ. Accordingly, the following tasks:
- determination of the parameters that require the installation of support bridges when forming tubular billets for welded pipes with diameter 450-700 mm.
3. Review of research and development
Tube blank is made from one sheet to the three-roll bending machine. Then she goes to doformovochny gauge where carried hem edges. The operation is performed in a single pass tubular blank.
Forming sheet on a triple roll bending machine is carried out between the upper push shaft having a diameter of 200 mm (when you install the support bridges) and two lower support shafts. Supporting bridges are used to eliminate bending of the upper shaft of the pressure [1]
Auxiliary bearing bridges are only used for bending small-diameter pipes. Wherein the upper shaft is removed and the usual auxiliary bearing mounted to the upper gangways shaft having a diameter of 200 mm.
Auxiliary bearing bridges installed between two support walkways. Smoothing upper shaft diameter of 200 mm is produced on the supporting trestle by means of upper rollers 22, spaced along the shaft. Supporting shaft diameter of 200 mm is also driven by a conventional drive to the upper rollers.
4. Improving calibration for forming pipes with diameter 508×16mm steel 10G2FB
Research and development were carried out using a computer program «Bending Set v7 Haeusler AG», which provides simulation of the forming process of pipe billets in the three-roll bending machine. The main window of the computer program is shown in figure 1.
The upper part of the window is for setting initial information by: the outer diameter of the pipe wall thickness, yield strength steel sheet, the parameters characterizing the type of steel, as well as the length and width of the sheet. There is also defined the parameters of the upper and lower forming rolls and chooses flexible.
Yield stress is determined depending on the steel grade. The distance between the lower support shafts is selected depending on the thickness of the sheet.
At the bottom of the window provides the results of calculations that include the value of the displacement of the upper shaft in each pass that affect the molding; tension cylinder pressure; the pressure in the support cylinder and the bending stress at the upper roller, which must not exceed the permissible value.
During calculations the outer radius of the tube was determined in dependence on the width of the bridge plate
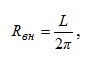
wherein L - the width of the sheet, in millimeters;
The distance between lower supporting shafts Xuw can be determined according to the passport data of the machine, and in case of their absence – calculate using the formula
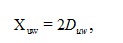
wherein Duw - the diameter of the lower roll, mm;
The relative distance between the lower support shafts can be determined as the ratio
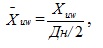
wherein Da - the outer tube diameter, mm;
Figure 1 shows the results of calculations of the regime molding pipe diameter 508×16mm steel 10G2FB mm. We obtained the following ra-tional molding parameters:
- the value of the top shaft to pass each subject in lnogo elastic recovery of the band: the first aisle - 90.4 mm, the second - 136.1 mm, the third - 168.0 mm, on the fourth - 184.4 mm;
- the diameter of the workpiece after the first pass of 1669 mm, after the second - 818 mm after the third - 585 mm; after the final fourth pass obtain diameter of the finished pipe - 508 mm.
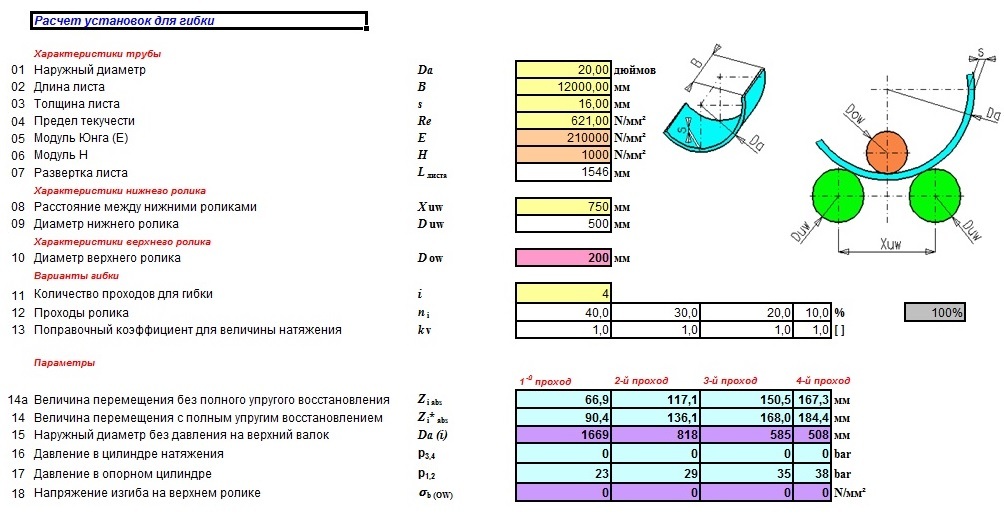
Figure 1. Window mode of the computer program for calculating forming billets for pipe diameter 508×16mm steel 10G2FB
Conclusions
On the basis of a specialized computer program usovershenst-tence modes forming tubular billets for welded pipes with diameter 508×16 mm and 660×15 mm steel 10G2FB on a triple roll plate bending ma-bus «Haeusler» JSC HTZ.
1. The rational parameters of molding sheets:
- the value of the top shaft to pass each subject in lnogo elastic recovery of the band: the first aisle - 90.4 mm, the second - 136.1 mm, the third - 168.0 mm, on the fourth - 184.4 mm;
- the diameter of the workpiece after the first pass of 1669 mm, after the second - 818 mm after the third - 585 mm; after the final fourth pass obtain diameter of the finished pipe - 508 mm.
2. provide additional fourth pass when forming billets, which provides a more uniform deformation of the sheet within the operating cycle of LGM.
The list of the used litterature
- Друян В.М., Гуляев Ю.Г., Чукмасов С.А. Теория и технология трубного производства Днепропетровск: Днепр-ВАЛ, 2001. — 544 с.
- Данченко В.Н. и др. Технология трубного производства М.: Интерметин-жиниринг, 2002 год, 640 стр.
- Осадчий В.Я., Вавилин А.С. - Технология и оборудование трубного производства - Москва, Интермет инженеринг, 2001 - 607с.
- Коликов А.П., Романенко В.П., Самусев С.В., и др. Машины и агрегаты трубного производства М.: МИСиС, 1998. - 536 с.