Abstract
Содержание
- Introduction
- 1. Analysis of the methods of investigation of the behavior of internal defects in the macrostructure of metal deformation
- 1.2. Defects of macrostructure of continuous billet
- 3. The analysis of existing methods of physical modeling of rolling out defects macrostructure
- 3. Development of research methodology and experimental design of physical models
- Findings
- References
Introduction
Currently in long products of increasingly high demands. There are two groups of long products: Group 1 - Private hire (is used for making non-critical structures); Group 2 - rental for machinery and critical structures.
However, in the case of production of rolled products for critical applications raises a number of problems caused by the use of continuous casting. This primarily concerns the problem of producing high-quality macro and microstructure of the cross section.
While the redistribution of unused bullion through blooming, this problem does not exist because the bar had an initial cross-section of at 750h900 mm, and the total was greater hood 100. Naturally, all internal defects could vykatat. But once started to produce similar products from continuously cast billets to 150x150 mm (125,135,150), respectively, then decreased hood. Due to the fact that the hood is reduced, the facts revealed neprorabotki metal structure.
The main types of marriage should be regarded as: violation of the geometry of continuous casting - 36.4%, defects in macrostructure - 17.2%, the crack - 31.9%, slag inclusions - 4.5%, as well as many of templates observed axial porosity, liquation strips and cracks developed columnar structure and the asymmetry of the zones of the ingot.
Particularly relevant to the problem of obtaining rental engineering of fine varietal continuous casting with the guaranteed parameters in the presence of a macrostructure in the initial procurement of axial defects such as pore piping.
Therefore, the work associated with the study of the behavior of axial macrostructure defects and their seals is undoubtedly relevant.
1. Analysis of the methods of investigation of the behavior of internal defects in the macrostructure of metal deformation
1.1 Defects of macrostructure of continuous billet
The quality of finished rolled products is largely determined by the quality of the original piece. This literature review examined the internal defects in continuously cast billets, the factors affecting the formation and development of defects, as well as their transformation during the rolling process.
Under defective understand discontinuity metalla.Defekty formed during solidification and may develop within the cast billet and the outer surface. In most cases, defects have a negative impact on production, causing rejection or increased production costs resulting from the need to bring the blanks in accordance with the required specifications prior to rolling.
Depending on the causes of the defects may be divided into two groups:
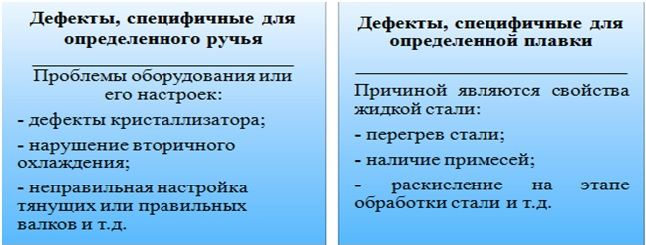
Each group of defects can be divided into four basic types:
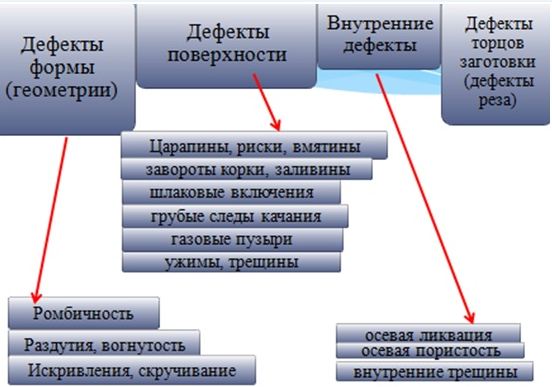
Some elements, unwanted and often present in the metal as impurities, may cause the formation of defects:
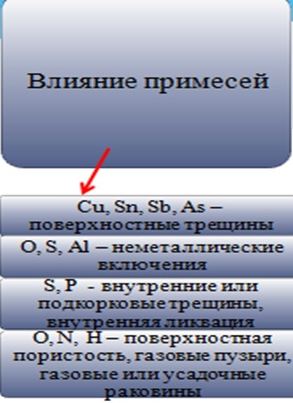
Consider the types of visual defects using the figure below.
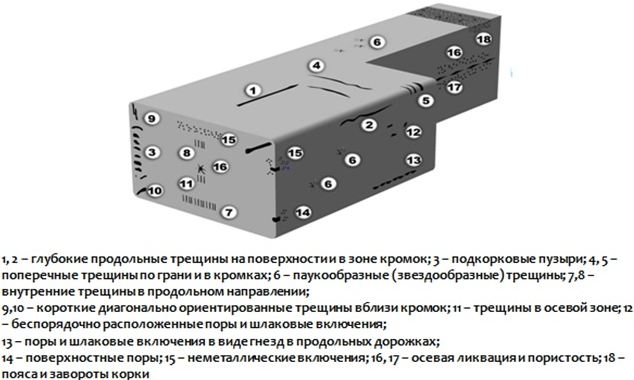
Defects in the internal structure of the workpiece to identify and evaluate the longitudinal and transverse of templates. The evaluation is carried out by comparing the macrostructure of templates etched or sulfur prints reference scale points. Axial chemical heterogeneity in some cases, the method was quantified. For this drill sampled for analysis of the axial zone, and an intermediate edge. Drill diameter - in the range of 5-10% of the size of the workpiece. For research purposes, use layered gouging crimped blanks with the analysis of the surface of each layer spectral and radiographically.
2. Analysis of the existing methods of physical modeling of rolling out the macrostructure defects.
There are physical and computer methods of research of the behavior of internal defects in the metal plastic deformation can be categorized in the following systems:
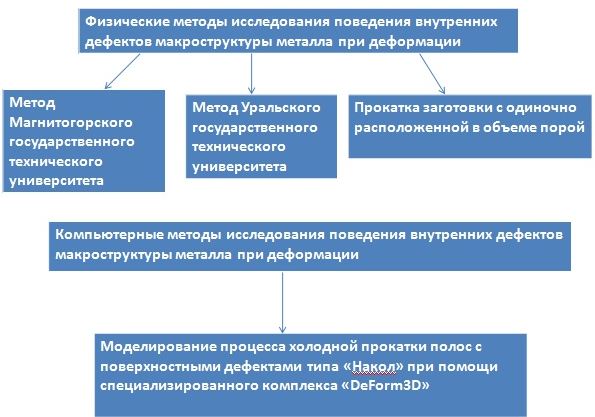
3. Development of research methodology and experimental design of physical models
The analysis published in the last decade of publications relating to the Conduct of continuous billet defects in rolling shows that prevail works which are used to study different kinds of mathematical models that are traditionally implemented using the finite element method. As shown by the analysis performed the literature data, the most difficult in the realization of using physical models of the behavior of the research process is seen internal defects macrostructure of continuous cast billet during rolling. The new approach was based on the following assumptions: - firstly, due to the fact that the axial macrostructure defects have significant length along the longitudinal axis, it is assumed that they are similar to surface defects and it applies to the term "roll-out"; - Secondly, the presence of a density gradient localization of defects per unit cross-sectional area to present this allows a layered model to the discrete nature of its change; - Thirdly, the process of changing the height is considered conditional metal layer with the already existing defect in the rolling process and new defects are formed; - Fourth, during rolling additional penetration defect by disrupting the continuity of the metal does not occur; - Fifthly, the roll-out of the defect is proportional to the change in height of the conditioned metal layer, and the angle of inclination of surface defects to the vertical symmetry axis of roll and rolling direction (longitudinal or transverse) and their position in the plane of the cross section profile during the rolling process can vary. In light of the above, for the study of the behavior of metal macrostructure defects axial region NLZ using physical models to be solved the problem associated with the development of the construction of the laboratory sample, which would allow it to track properly forming. Consider the application of this approach in our case specifically, when the defect is not the longitudinal axis but at an angle. Based on a study of existing approaches to the study of surface defects on rolling out physical models, it was suggested that the defect simulator in the form of 3-coal prism of a given length. The use of this form of the defect simulator will allow to determine the coefficients of deformation in each of the layers. Moreover, by varying its dimensions and the arrangement direction (lengthwise or transverse rolling) may significantly increase the initial information needed for subsequent analysis.
Conclusion
The paper presents the further development of methods for the study of metal forming processes using a layered physical models. Using a layered model in conjunction with the proposed method of application defects on the surface of the n-th layer and the method of processing information on the nature of its forming, allows to evaluate the effect of the degree of deformation in the process of "healing." Performed primary adaptation of the method applied to the conditions of modeling of the deformation process of continuous billet in the first three rectangular caliber crimp linear mill stand 500/370 PJSC "DMPZ." The experimental data have allowed to clarify the existing mechanism of "healing" of the axial defects discontinuity metal depending on the total stretching and deformation effects of the application schema.
References
1. Смирнов, Е.Н. Исследование процесса деформирования непрерывнолитой заготовки малого сечения с дефектом формы “ромбичность” в прямоугольных калибрах / Е.Н. Смирнов, С.А. Снитко, С.Ю. Красенков // Вісник Національного технічного університету України “Київський політехнічний інститут”; Сер., Машинобудування. - Київ: КПІ, 2012. - Вип. 64. - С. 214-220.
2. Смирнов, Е.Н. Компьютерное и физическое моделирование процесса прокатки непрерывнолитой заготовки с дефектом формы "ромбичность" в прямоугольных калибрах / Е.Н. Смирнов, С.А. Снитко, В.А. Скляр// Инновационные технологии в металлургии и машиностроении: Сб. науч. трудов. - Екатеринбург: унив. тип. «Альфа Принт», 2012. - С.392-396.
3. Сычков, А.Б. Трансформация дефектов непрерывнолитой заготовки в поверхностные дефекты проката / А.Б. Сычков, М.А. Жигарев, А.В. Перчатник и др. // Металлург. – 2006. - №2. – С. 60-64.
4. Кокшарев, Ю.М. Исследование заваривания внутренних дефектов в сортовых заготовках, полученных на МНЛЗ ОАО «ЗСМК» / Ю.М. Кокшарев, О.А. Лубяной // Металлургия: технологии, управление, инновации, качество: труды Всероссийской научно – практ. конф., Новокузнецк, 26-28 октября 2010. – Новокузнецк, 2010. – С.73-77.
5. Пат. на винахід 77283, Україна, МПК G01N3/28. Спосіб фізичного моделювання процесів пророблення структури в безперервнолитих зливках при пластичній деформації / О.А. Мінаєв, Є.М. Смирнов, А.П. Мітьєв, М.В., Григор’єв, І.А. Демідова, О.О. Слугін, В.М. Мягков: Донец. нац. техн. ун-т. - №20041008620; заявл. 22.10.2004, опубл.15.11.2006; Бюл.№11.
6. Minayev, A.A. Experimental investigation dynamics of condensation of axial zone continuous casting blooms and billets on physical models/ A.A. Minayev, E.N. Smirnov, A.N.Smirnov, M.V.Grigoriev // 11-th International Metallurgical & Materials Conference “METAL - 2002”, Hradec nad Moravicнi, 14 - 16 May 2002, Czech Republic. - Ostrava: VSB - Technical University, 2002. – B18. – Р.218-226.
7. Завьялов, А.А. Лабораторные методы моделирования ликвации при деформации непрерывно-литой сортовой заготовки / А.А. Завьялов, А. В. Логвинов, О.Н. Тулупов // Обработка сплошных и слоистых материалов: Межвузовский сборник научных трудов – Магнитогорск: МГТУ. - 2001. – С.66-71.
8. Tripathy, P.K. Migration of slab defects during hot rolling / P.K. Tripathy, S. Das, M.K. Jha and e.t.c. // Iron making and Steelmaking. – 2006. – v.33. - №6. – Р.447 – 483.
9. Tirosh, J. Evolution of anisotropy in the compliances of porous materials during plastic stretching or rolling – analysis and experiments / J. Tirosh, A.Shrizby, I. Rubinski // Mechanics of Materials. – July 1999. - v.31. – issue 7 .- Р. 449 – 460.
10.Минаев, А.А. Исследование и математическое моделирование формоизменения пор в непрерывнолитом металле при пластической деформации /А.А. Минаев, Е.Н. Смирнов, И.В. Лейрих, В.В. Зуб / Вестник Магнитогорского госуд. техн. ун-та им. Г.И.Носова: сб. науч. тр. – Магнитогорск: МГТУ, 2006. – Вып. 4. – С.47-52.