Реферат за темою випускної роботи
Зміст
- Вступ
- 1. Актуальність теми
- 2. Мета і задачі дослідження та заплановані результати
- 3. Теплова постановка задачі
- 4. Опис енергозберігаючих режимів мікролегування сталі порошковим дротом з вмістом кальцію на основі комп'ютерної програми
- Висновки
- Перелік посилань
Вступ
У практиці сучасного металургійного виробництва одним з перспективних напрямів підвищення якості металу і поліпшення якості споживчих властивостей, які не потребують значних сировинних і енергетичних витрат є мікролегування сталей.
Під мікролегуванням прийнято розуміти введення окремих елементів або їх з'єднань, залишковий вміст яких не перевищує 0,1%, які суттєво впливають на процеси, що протікають в металі і визначають його фазовий склад, розмір структурних складових, будову і чистоту меж і прикордонних зон і, як наслідок, поліпшення фізичних властивостей металу.
Мікролегірующіе елементи здатні реагувати з киснем, азотом, сіркою, миш'яком і іншими домішками і утворювати відповідні з'єднання, що дозволяють нейтралізувати їхні негативні дії, що в кінцевому результаті позначається на поліпшенні фізичних властивостей металу.
1. Актуальність теми
На рис.1 представлена схема установки «ковш-піч» для позапічної обробки сталі, з можливістю мікролегування її порошковим дротом за допомогою трайб - апарату, встановленого на своді печі.
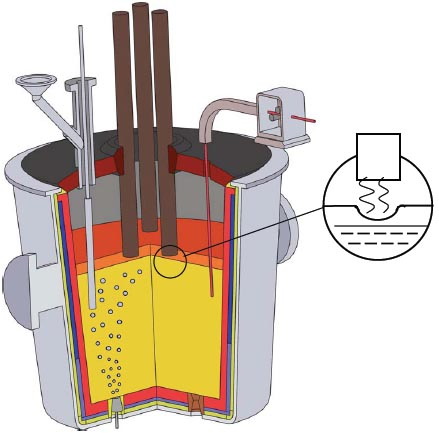
Рисунок 1 – Загальна схема установки «ковш-піч»
Застосування хімічно активних елементів в кусковому вигляді для позапічного мікролегування малоефективно. В останні роки набув поширення спосіб введення мікролегірующіх добавок в метал у вигляді порошкового дроту з відповідним наповнювачем.
Переваги введення легуючих добавок у вигляді порошкового дроту в порівнянні з традиційними способами легування:
- Більш висока ступінь засвоєння елементів;
- Можливість отримання сталей зі строго регламентованим вмістом активних елементів;
- Відтворюваність результатів;
- Можливість серійної безперервного розливання різних марок сталей;
- Отримання стабільних механічних властивостей;
- Висока технологічна і економічна ефективність процесу.
2. Мета і задачі дослідження та заплановані результати
Магістерська робота присвячена розробці енергоресурсозберігаючих режимів мікролегування рідкої сталі порошковим дротом на основі комп'ютерного моделювання процесів тепломасопереносу.
Це дозволить визначити оптимальну швидкість введення порошкового дроту, при якій буде досягнуто максимальний показник коефіцієнта засвоєння CaSi добавок, що в свою чергу призведе до зниження питомої витрати дорогого порошкового дроту.
3. Теплова постановка задачі
При позапічної мікролегуванні рідкої сталі найбільш важливим параметром є швидкість введення ПД(порошкового дроту) в розплав. Якщо вона низька, то це призводить до її плавлення і розчиненню наповнювача ПД у верхніх шарах ванни, що погіршує процес, призводить до нерівномірного розподілу введеного кальцію по висоті ковша. При надмірно високих швидкостях введення ПД, вона не встигає розплавитися і, досягаючи дна ковша, згинається і виходить у верхні шари розплаву і навіть в атмосферу.
Швидкість введення ПД необхідно вибирати таким чином, щоб її оболонка була розплавлена в нижніх обсягах ковша, у його днища. При цьому наповнювач ПД, спливаючи у вигляді крапель, буде максимально розчинятися в розплаві.
Для комплексної оцінки впливу різних чинників на час плавлення ПД доцільно використовувати залежність:
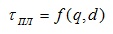
де d - діаметр дроту; q - щільність теплового потоку на її поверхні.
З урахуванням специфіки завдання, її математичну постановку можна описати рівнянням теплопровідності Фур'є в циліндричній системі координат для кожної області дроту:
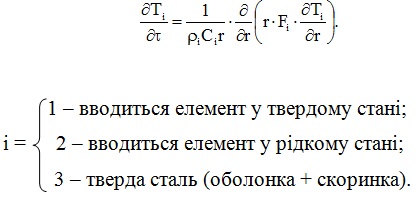
Отримаємо рівняння в узагальненому вигляді:
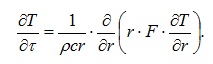
Крайові умови до рівняння теплопровідності мають вигляд:
1) Початкові умови:

Тут: Т0 – температура навколишнього середовища; R – радіус області, займаної наповнювачем ПД в початковий момент часу; δ – товщина сталевої оболонки в цей момент.
2) Граничні умови:
а) вісь симетрії (r = 0):

б) стик твердого наповнювача і сталевої оболонки Т1=Т3 (r = R):
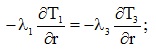
в) стик твердої і рідких фаз наповнювача ПД Т1=Тпн (r=R1):
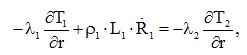
г) стик поверхні ПД з рідкою сталлю(r = R3):

Т3=T(R3) - наморажування скоринки при Т3< Тпс
Т3=Тпс - плавлення оболонки з скоринкою.
Тут:
Тпн, Тпс - температури ліквідусу наповнювача і стали;
Тс0, Тс - температура сталі в обсязі ковша і при r=R3;
ρ1, ρ3 - щільності наповнювача і стали;
L1, L3 - питомі теплоти фазових переходів;
R1, R3 - швидкості переміщення кордонів r=R1 и r=R3.
4. Опис енергозберігаючих режимів мікролегування сталі порошковим дротом з вмістом кальцію на основі комп'ютерної програми
Вибір оптимальної швидкості введення ПД в рідку сталь створює передумови вирішення питання про енергоресурсозберігання, пов'язаного з економією ПД.
Чисельне параметричне дослідження проводилося для силікокальцієвого дроту на базі СК 30, температури розплаву в сталерозливному ковші 1600°С, глибини рідкої ванни 4 м.
Як відомо, стадії плавлення ПД з силікокальцієвим, тобто легкоплавким, наповнювачем мають послідовність, показану на рис.2.
В початкові моменти часу, на стадії I, геометрія перетину ПД характеризується двома областями:
- Твердий наповнювач ПД;
- Сталева оболонка ПД з намерзлою на ній кіркою (на рис.2 не показана).
Потім, на стадії II, по мірі плавлення наповнювача формується третя область - розплав наповнювача ПД. І, нарешті, по завершенню розплавлення наповнювача, знову повертаємося до двох областей, одна з яких, замість твердої фази наповнювача ПД, перетворюється в його рідкий стан.
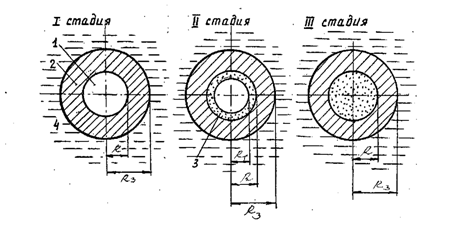
Рисунок 2 – Стадії плавлення ПД з силікокальцієвим наповнювачем
По мірі розплавлення оболонки ПД у днища ковша (при оптимальній швидкості введення ПД), тут формується очаг рідких крапель силікокальцію, які, спливаючи в розплаві сталі, розчиняються в ньому. p>
На рис.3 показана, отримана динаміка плавлення оболонки ПД діаметром 12 мм з сілікокальціевим (СК30) наповнювачем при температурі рідкої ванни 1600°С. Як видно з цього малюнка, кірка сталі на оболонці ПД спочатку зростає до деякої межі, а потім плавиться разом з оболонкою. Швидкість введення ПД в ванну визначає інтенсивність теплообміну між поверхнею дроту і рідкої сталлю в ковші. Внаслідок цього розглянутий параметр впливає на динаміку плавлення ПД.
Порівняння з аналогічними результатами інших робіт [16, 18] говорить про їх задовільне узгодження. При цьому на рис.3 крива 1 - відповідає роботі [18], 2 - результатами наведеної магістерської роботи, а крива 3 - оброблені методами інтерполяції та екстраполяції дані роботи [16]. p>
Як випливає з відносного порівняння кривих, використання автором більш точної емпіричної формули для безрозмірного коефіцієнта тепловіддачі (критерію Нуссельта) порівняно з роботою [16] дає результати, які наближають їх до дослідженням [18]. Разом з тим використана автором методологія стосовно до традиційної технології мікролегування металу в сталерозливному ковші порошковим дротом більш раціональна, ніж [18]. Це випливає з того, що розглянута технологія виключає як відхилення ПД від вертикалі при її введенні в сталерозливний ковш (за рекомендаціями авторів дослідно-промислових досліджень [15, 18] ), так і відсутність шлакового шару на поверхні ПД в глибинних шарах рідкої ванни. p>
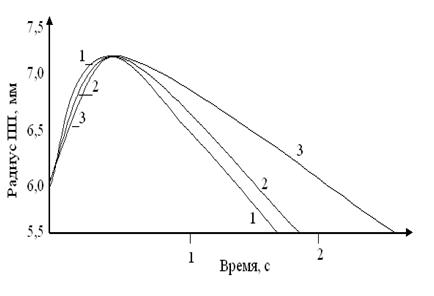
1 – за даними В.Ю.Болотова; 2 – результати даної роботи; 3 – за даними О.Е.Полозюка;
Наповнювач ПД - СК30; Швидкість введення ПД - 5м/с; Температура ванни - 1600°С; Глибина ванни - 4м.
Рисунок 3 – Діаграма плавлення ПД з кіркою сталі
Інформацію про вплив щільності теплового потоку, спрямованого на поверхню ПД, на час плавлення її оболонки з намерзлою кіркою представленна на рис.4. При визначенні q використаний знайдений коефіцієнт тепловіддачі α, а в якості температури поверхні ПД бралася температура ліквідусу сталі. Представлений графік дозволяє кількісно знайти розглядаємий час, тоді як монотонно спадаючий характер залежності тут очевидний. З рис.4 випливає, що найбільш динамічно плавиться дріт меншого діаметру . p>
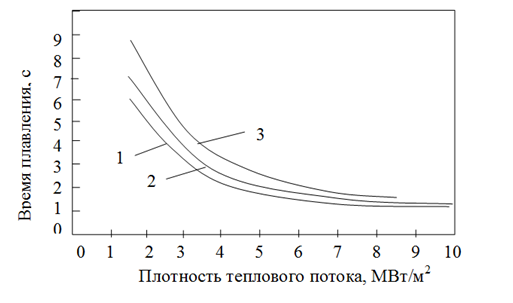
1 – діаметр 8мм; 2 – діаметр 10мм; 3 – діаметр 13мм;
Рисунок 4 – "Час розплавлення оболонки ПД і кірки сталі, намерзлої на ПД з силікокальцієм, залежно від щільності теплового потоку, спрямованого на поверхню ПД
Для розрахунку ступеня засвоєння наповнювача [17] залежно від параметрів технології введення дроту достатньо (з використанням розрахункових результатів по її плавленню) оцінити локальний дифузійний масообмін крапель наповнювача ПД з рідкою сталлю (що враховує процеси гідродинаміки і перенесення поблизу міжфазної границі), заснований на представленні про ідеальний перемішуванні металу в рідкій ванні. Останнє випливає з високих значень коефіцієнтів конвективної дифузії, які призводять до швидкого вирівнювання концентрації компонентів наповнювача ПД в розглянутій області . p>
Час плавлення наповнювачів ПД типу Al і Ca менше, ніж аналогічний час для намерзлої сталевої кірки і оболонки. Тому до моменту звільнення наповнювача від оболонки він є повністю рідким. P>
Поведінка рідких крапель наповнювача в деякому розумінні аналогічно міхурам аргону в умовах продувки ванни, тому що і щільність рідкого силікокальцію або алюмінію в 3-3,5 рази легше щільності стали при 1600°С, і динамічна в'язкість в 4-5 разів менше. p>
Кремній, з одного боку, добре розчинний у рідкому залізі, а з іншого боку, його коефіцієнт дифузії значно менше, ніж у кальцію. Кальцій, навпаки, слабо розчинний у розглянутому середовищі, проте його коефіцієнт дифузії вище.
Висновки
Таким чином, в даній роботі розглянуті актуальні питання енергоресурсозберігання при позапічному мікролегуванні стали порошковим дротом. Робота дозволить підібрати оптимальну швидкість введення порошкового дроту, що в свою чергу знизить її витрата і призведе до економії.
При написанні даного реферату магістерська робота ще не завершена. Остаточне завершення: січень 2016 року. Повний текст роботи та матеріали по темі можуть бути отримані у автора або його керівника після зазначеної дати.
Перелік посилань
- Троцан А.И. Теория и практика микролегирования с учетом межкристалитной внутренней адсорбции /А.И. Троцан, И.Л. Бродецкий, А.И. Ищенко. - К.: "КИМ" - 2009. - 272 с.
- Физическое металловедение / под ред. Р.У. Кана и П. Хаазена. - М.: Металлургия, 1987. - Т.1. - С. 111-137; Т.З. - С.5-112.
- Дамаск А. Точечные дефекты в металлах/ А. Дамаск, Дж. Дине. - М.: Мир, 1966. - 291с.
- Новиков И.И. Кристаллография и дефекты кристаллической решетки / И.И. Новиков, К.М. Розин. - М.: Металлургия, 1980. - 336с.
- Штремель М.А. Прочность сплавов. Дефекты решетки / М.А. Штремель. - М.: Металлургия, 1982. - 278с.
- Глейтер Г. Большеугловые границы зерен / Г. Глейтер, Б. Чалмерс. - М.: Мир, 1975. - 376с.
- Грабский М.В. Структура границ зерен в металлах / М.В. Грабский. - М.: Металлургия, 1972. - 160с.
- Атомная структура межзеренных границ сборник статей /[пер. с англ. В.Н. Перевезенцева, В.В. Рыбина ; ред. пер. и вступит, статья А.Н. Орлова]. - М.: Мир, 1978. - 290с.
- Орлов А.М. Границы зерен в металлах / А.М. Орлов, В.М. Перевезенцев, В.В. Рыбин. - М.: Металлургия, 1980 - 154с.
- Структура межкристаллитных и межфазных границ / В.М. Косевич, В.М. Невлев, JI.C. Палатник, А.И. Федоренко. - М.: Метал¬лургия, 1980. - 256с.
- Кайбышев О.А. Границы зерен и свойства металлов / О.А. Кайбышев, Р.З. Валиев. - М.: Металлургия, 1987. - 213с.
- Bollmann W. Crystal Defects and Crystal Interfaces / W. Bollmann. - Springer Verl.; Berlin, 1970. - 244 p.
- Goodhew P. Crain Boundary Structure and Kinetics / P. Goodhew. - 1SH, 355 Metals Park, OH, 1980 - 155 p.
- Ishida Y. Fild ion microscopy observations of ordered grain boundary structures in tungaten / Y. Ishida, D.A .Smith // Scripta Met. - 1974. - V.8, № 3. - P.293-298.
- Дюдкин Д.А., Кисиленко В.В., Павлюченков И.Л., Болотов В.Ю. Ковш-печь…
- Захаров Н. И., Полозюк О. Е. Исследование процессов теплообмена при обработке жидкой стали порошковой проволокой// Приднепр. науч. вестник. – Дн. – 1997. - №17. – С. 22-26.
- Полозюк О. Е., Захаров Н. И. Кинетика массопереноса элементов при внепечной обработке стали силикокальцием или алюминием// IV регион. научно-техн. конф. Апрель, 1997: Тез. докл. – Мариуполь. – 1997. – Т. 1 – С. 5.
- Исследование процессов плавления и траектории движения проволоки при вводе в сталь /Тимошпольский В.И., Болотов В.Ю., Павлюченков И.А. и др.// Литьё и металлургия. – 1999. – №2. – С. 21-23.