Содержание
- Введение
- 1. Общая характеристика игольной проволоки и игл из нее
- 2. Особенности термообработки заготовки для игольной проволоки и игл из нее
- 3. Постановка задачи и цели исследований
- 4. Материалы, методика, оборудование для исследования
- 5. Результаты исследований
- Выводы
- Список источников
Введение
Проволока является универсальным конструкционным материалом. Она применяется во всех без исключения отраслях материального производства, этим обуславливается многообразие свойств и размеров, а массовость потребления требует технологичности и экономически обоснованных схем изготовления [1].
Одними из изделий массового потребления, изготовляемых из проволоки, являются иглы. Иглы подразделяются на швейные и медицинские, изготовляемые из высокоуглеродистых и нержавеющих марок стали соответственно. К иглам как медицинского, так и швейного типа, предъявляются высокие технологические требования. Изготовление игольной проволоки требуемого качества осуществимо при условии устойчивого и качественного технологического процесса на всех этапах производства. Наиболее важная роль в производстве готовых изделий из игольной проволоки отведена термической обработке. Получение требуемых физико-механических характеристик достигается за счет получения оптимальной структуры материала игольной проволоки.
В связи с быстрым развитием техники, в том числе и производства швейных машин, а также обрабатываемого ими материала, возникает необходимость создания более качественной игольной продукции. Следует отметить, что в Украине ассортимент швейных игл достаточно ограничен. Отечественные производители бытовых и промышленных швейных игл вынуждены конкурировать с зарубежными производителями, которые выпускают более качественную, но и вместе с тем, более дорогостоящую, продукцию. В попытках уменьшить затраты на производство, отечественные производители в тоже время уменьшают показатели механических характеристик готового изделия из игольной проволоки.
Таким образом, проблемы в области производства игольной продукции отечественного производства являются актуальными, что безусловно свидетельствует о важности проведения исследования по разработке и усовершенствованию существующих способов проведения термической обработки изделий, как предварительной, так и окончательной. При этом стоит учитывать лимитированный бюджет отечественных предприятий, который не позволяет проводить дорогостоящих обработок игольной продукции.
1. Общая характеристика игольной проволоки и игл из нее
Игольная проволока используется для изготовления игл различного назначения. Наиболее известные – это иглы для шитья вручную (существует 8 видов [2]), машинные (15 видов по типу исполнения стержня и более 50 – по виду исполнения острия [3]). Для производства игольной проволоки и швейных игл в основном используют инструментальную углеродистую сталь, содержащую от 0,65 до 1,29 % углерода. Такая сталь имеет маркировку У7А-У12А, где цифры означают количество углерода в стали в десятых долях, а буква «А» означает высокое качество стали.
Швейные иглы производятся на так называемом игольно-платинном производстве. Ассортимент крупных предприятий может насчитывать несколько тысяч различных наименований игл различной толщины, формы острия и вида покрытия поверхности [4]. Машинная игла имеет более сложную конструкцию по сравнению с обычной бытовой иглой (рис. 1). Ручная бытовая игла представляет собой гладкий тонкий цилиндрический стержень, заостренный на одном конце, а на другом имеющий ушко для продевания нитки. Машинная игла имеет более сложную конструкцию, отвечающую специальным условиям ее работы [5].
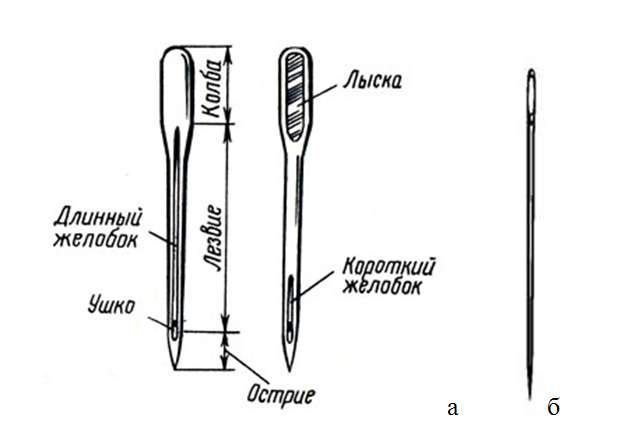
Рисунок 1 - Игла машинная (а) и бытовая (б)
В скоростных машинах во время прокалывания ткани иглой за счет сил трения игла нагревается до 350-400°С с выделением большого количества тепла. Нагрев иглы особенно опасен для материалов содержащих химические волокна. В процессе скоростного шитья игла нагревается выше температуры плавления химических волокон, поэтому при соприкосновении с нагретой иглой эти волокна расплавляются и забивают ушко и длинный желобок иглы.
Для снижения температуры нагрева иглы применяют: редуцирование лезвия, изменение геометрии поперечного сечения иглы, охлаждение воздухом или воздушно-водяной смесью, использование в качестве теплоотдатчиков различных жидкостей, предварительное проделывание в материале отверстия для прохода иглы электрическим методом и др. [6]. Также для борьбы с нагреванием игл, в процессе работы, некоторые производители используют покрытия. Покрытия для игл выполняют из нитрида титана; фосфор + тефлон; фосфатные смолы; хромовое; сочетание титанового или керамического в сочетании с карбоновым[7].
Коэффициент трения является важной характеристикой при изучении швейных игл, поскольку, чем выше коэффициент трения, тем сильнее нагреваются поверхности, как иглы, так и сшиваемого материала, что в свою очередь влечет за собой образования брака. Коэффициент трения в швейном производстве может варьироваться в пределах от 0,15 до 0,65 [7].
Таким образом, при производстве игольной продукции необходимо соблюдать жесткие требования, установленные к иглам, но серийное производство должно осуществляться с минимальными затратами. Важным показателем, который необходимо учитывать при разработке способа предотвращающего нагрев иглы в процессе работы, является коэффициент трения.
2. Особенности термообработки заготовки для игольной проволоки и игл из нее
Основным процессом для получения требуемых механических свойств и микроструктуры игольной проволоки и швейных игл является термообработка. Классический способ термообработки катанки – это патентирование и отжиг на зернистый перлит [8]. Патентирование происходит по следующему режиму: аустенизация стали при 920-950°С и охлаждение в расплаве свинца или соли при 480-550°С [8]. Однако патентирование значительно снижает прочностные характеристики, но повышает пластичность. В работе [9] взамен патентированию предложен кратковременный отжиг в селитровой ванне при температуре 520 ± 5°С и электротоком. Согласно проведенным исследованиям, такой отжиг несколько повышает прочностные характеристики и показатели удлинения. Отжиг на зернистый перлит проводится при температуре 680°С с последующим охлаждением на воздухе [9].
Существуют технологические схемы, исключающие процесс патентирования [10]. Данные технологические схемы включают в себя скоростную термообработку током высокой плотности (ТВП). Суть такой технологии заключается в кратковременном тепловом воздействии до температур 500-600°С. Длительность воздействия тока (0,5 – 4 с) зависит от плотности пропускаемого тока (35 – 80 А/мм2 – для углеродистых сталей [10]). Такая технология термообработки позволяет повысить прочностные характеристики стали, не понижая пластических свойств, и процесс формирования благоприятной структуры протекает значительно быстрее, в сравнении с классическими видами термической обработки.
Таким образом, основной термообработкой проволоки из высокоуглеродистой стали является патентирование. Готовые швейные иглы подвергают закалке и отпуску с целью достижения необходимых механических свойств. Следует отметить, что иглы производственного типа после заключительной термообработки должны иметь структуру состоящую из мелкоигольчатого мартенсита с равномерно распределенными карбидами (рис. 2). Твердость ручных и машинных игл должна быть в интервале 54...62 HRC [2, 5].
3. Постановка задачи и цели исследований
В нашем регионе ассортимент швейных игл достаточно ограничен. Размеры игл колеблются в пределах 35 – 80 мм по длине и 0,6 – 1,8 мм по диаметру [2]. Отечественные производители бытовых и промышленных швейных игл вынуждены конкурировать с крупнейшими производителями. Качественные швейные иглы производятся и импортируются в нашу страну из стран Европы (Германия, Великобритания, Франция), Японии, Китая. Большинство отечественных компаний предпочитают не производить иглы самостоятельно, а размещать заказы на их изготовление на китайских заводах. Они расфасовывают готовую продукцию в собственную упаковку и реализуют ее под своей торговой маркой [4].
Таким образом, целью данной работы является усовершенствование производства машинных швейных игл путем совершенствования технологического процесса их изготовления, а именно улучшение классических способов термической обработки, а именно разработка нетрадиционных способов.
Коэффициент трения, как указывалось выше, это важная характеристика, которую необходимо учитывать при разработке способов улучшения игольной продукции. Использование различных покрытий для снижения коэффициента трения является дорогостоящим процессом, поэтому данная работа посвящена изучению графитизации игольной проволоки из эвтектоидной стали, с целью использования графита в качестве смазочного материала, понижающего адгезию поверхности иглы со сшиваемым материалом.
4. Материалы, методика, оборудование для исследования
Для исследования влияния графитизации использовали проволоку диаметром 2 мм из эвтектоидной стали (сталь 85), недеформированной и со степенями деформации 27% и 75% . Химический состав стали приведен в таблице 1.
C | Si | Mn | Ni | S | P | Cr | Cu |
0.82-0.9 | 0.17-0.37 | 0.5-08 | <0.25 | <0.035 | <0.035 | <0.25 | <0.2 |
Данную проволоку резали на образцы длинной по 30 мм. Образцы подвергали графитизирующему отжигу и графитизирующему отжигу совмещенному с термоциклической обработкой.
Графитизирующий отжиг проводили следующим образом.
Образцы помещали в тигель и засыпали карбюризатором. Тигель с образцами помещали в печь (Тпеч = Тком ≈ 18°С) и нагревали до 750-760°С. Выдержка при данной температуре составила 5 часов. После чего замедленно охлаждали в течении 1 часа до 690-700°С; выдержка при данной температуре 2 ч. Дальнейшее охлаждение образцов производили вместе с печью. Режим графитизирующего отжига представлен на рисунке 3.
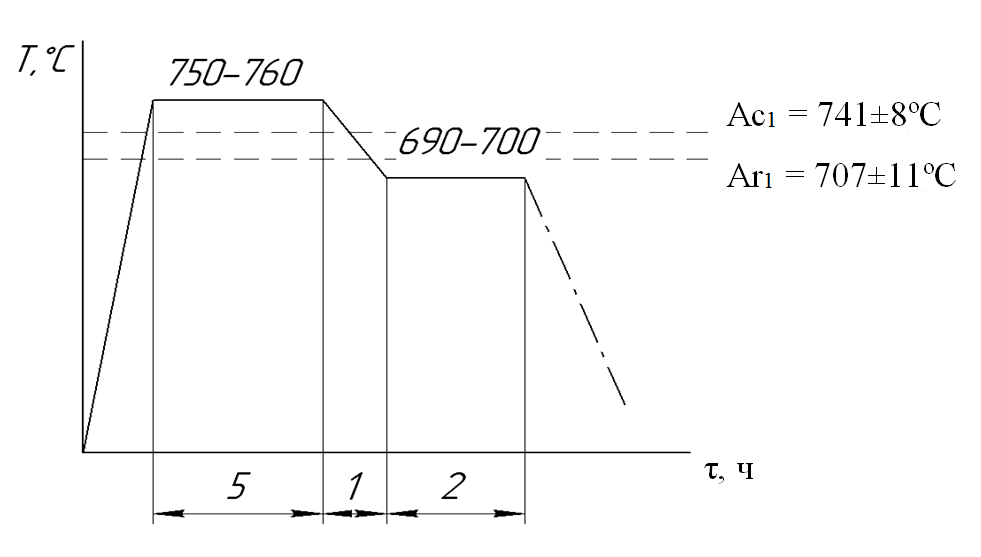
Рисунок 3 - Режим графитизирующего отжига образцов из стали 85
После проведения термической обработки образцы монтировали в оправки с эпоксидным клеем и изготавливали шлифы по стандартной технологии. Шлифы травили в 6%-ом растворе йода в спирте. Исследование структуры проводили на микроскопе МИМ-7. Для усиления яркости и расширения пределов увеличения изображения использовали иммерсионный метод микроскопического наблюдения. В качестве иммерсионной жидкости использовали касторовое масло. В результате, на микроскопе МИМ-7 было получено увеличение 1350.
Влияние графитизации и термоциклической обработки проводили на образцах длинной 30 мм, недеформированные и со степенями деформации 27% и 75%. Термоциклическая обработка проводилась по типу маятникового отжига. Тигель с образцами помещали в печь и нагревали до 750-760°С. Выдерживали при данной температуре 1 час. После этого охлаждали с печью до температуры 670-680°С и выдерживали при данной температуре 1 час. Затем производится вновь нагрев (с печью) до температуры 750-760°С и выдержка при данной температуре 1 час. Таким способом производится еще одно охлаждение и один нагрев, с выдержками по одному часу, с последующим охлаждением в печи. Таким образом, имеем три выдержки в течение часа при температуре 750-760°С и две выдержки в течение часа при температуре 670-680°С. Режим термоциклической обработки представлен на рисунке 4.
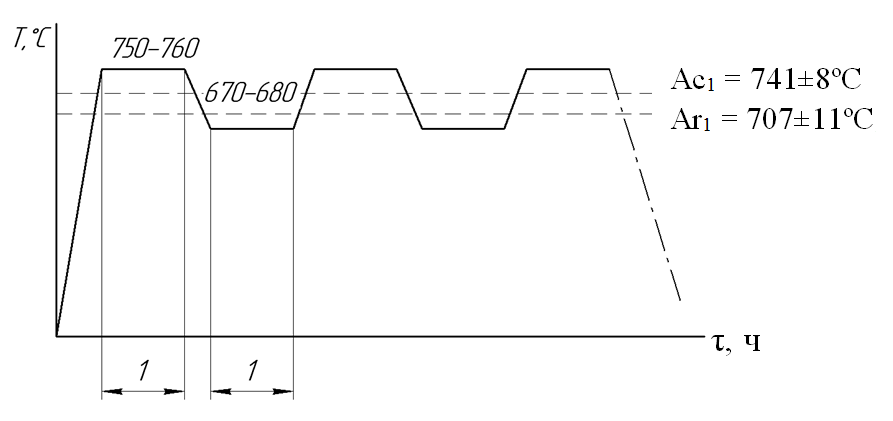
Рисунок 4 - Режим графитизирующего отжига совмещенного с термоциклической обработкой
Для сравнения влияния на свойства эвтектоидной стали графитизирующего отжига и совмещения графитизирующего отжига с последующей ТЦО были проведены некоторые исследования для образцов трех видов: 1) без термической обработки; 2) после графитизирующего отжига; 3) после графитизирующего отжига и ТЦО.
- Производился замер электросопротивления четырехзондовым методом.
- Определение плотности методом гидростатического взвешивания.
- Производили испытание на износ и анализировали полученные данные посредством рассчитаных коэффициентов истирания: массового (КΔm) и размерного (КΔd).
5. Результаты исследований
Микроструктура образцов после графитизирующего отжига представлена на рисунке 5. Как видно из фотографий микроструктуры, после отжига удалось получить графитные включения. Графитные включения имеют шаровидную форму. Однако графитизация стали не произошла на образце, не подвергавшегося холодной пластической деформации. По мере увеличения степеней обжатия образцов, видим, что и увеличивается количество графитных включений. Однако на образцах со степенью деформаций 25 и 75 % графитные включения распределены неравномерно по всей длине образца.
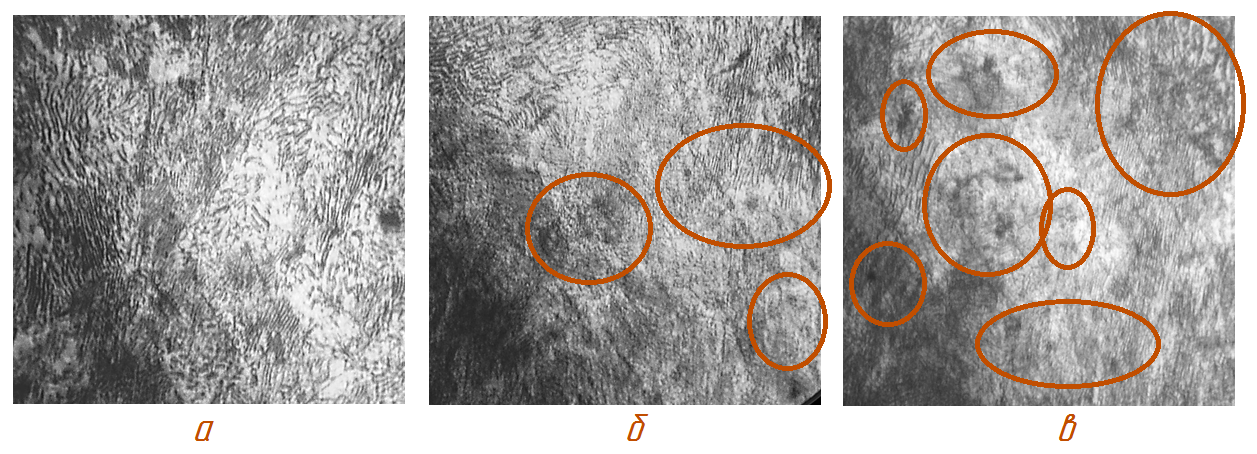
Рисунок 5 - Микроструктура образцов (включения графита обведены) со степенями обжатия, х1350:
а) не деформированный; б) 27%; в) 75%
Таким образом, увеличение степени деформации интенсифицирует графитизацию цементита в стали: это обусловлено возникшими дефектами (микротрещины, искажения кристаллической решетки), деформирующимися в структуре при предварительной деформации. Аналогичный вывод был сделан в работе [12]. Данный метод графитизации эвтектоидной стали был запатентован [13].
Влияние степени деформации на электросопротивление, в зависимости от термической обработки, представлено на рисунке 6.
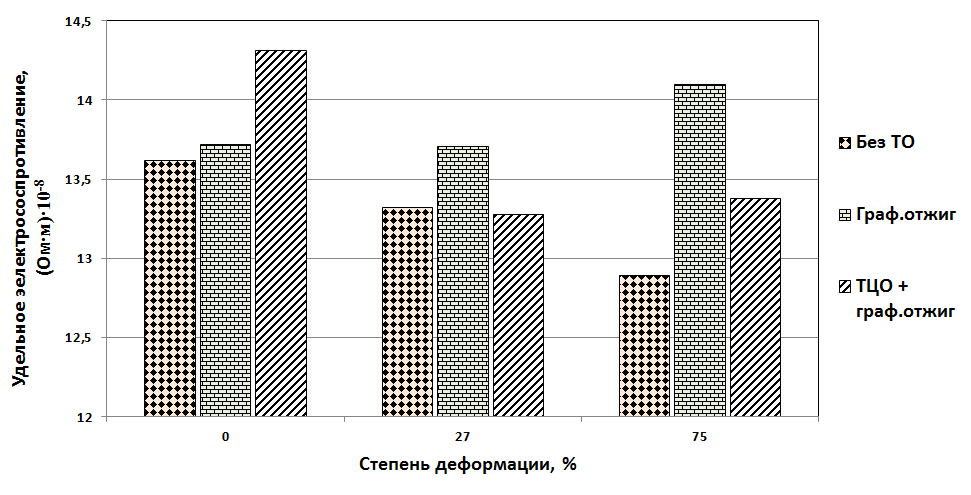
Рисунок 6 - Влияние термической обработки и степени предварительной холодной деформации на удельное сопротивление стали 85
Изменение плотности стали, в зависимости от степени деформации и термической обработки стали представлено на рисунке 7.
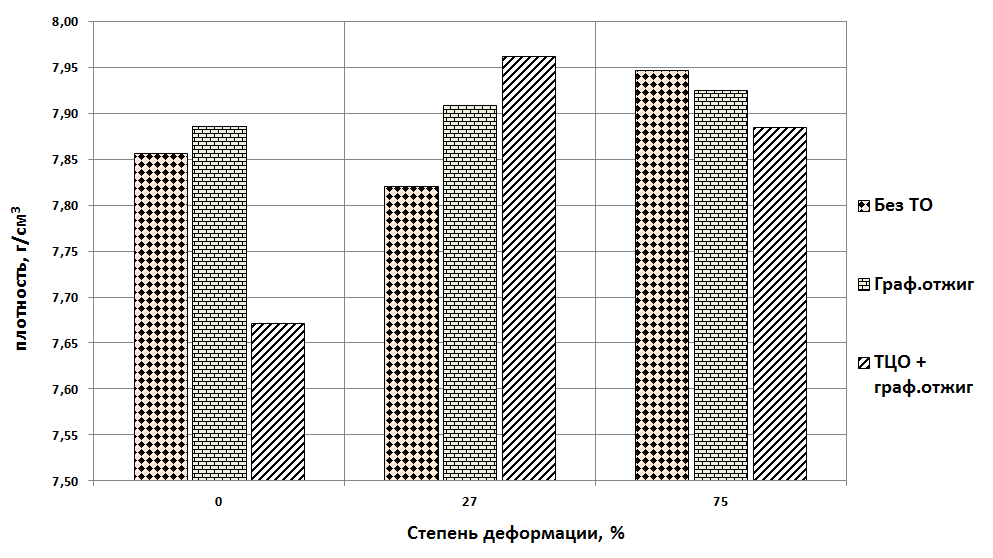
Рисунок 7 – Влияние термической обработки и степени предварительной холодной деформации на плотность стали 85
На рисунках 8 и 9 представлены влияние степени деформации и термической обработки на коэффициенты истирания.
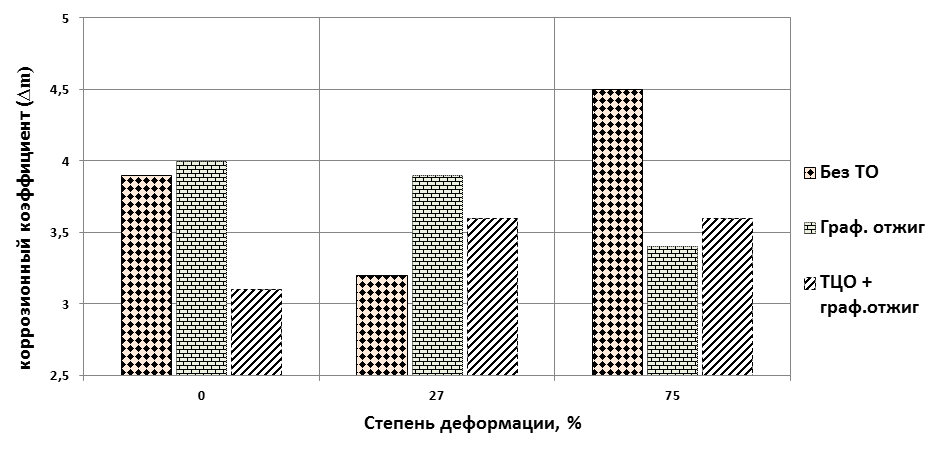
Рисунок 8 – Влияние термической обработки и степени предварительной холодной деформации на массовый коэффициент истирания
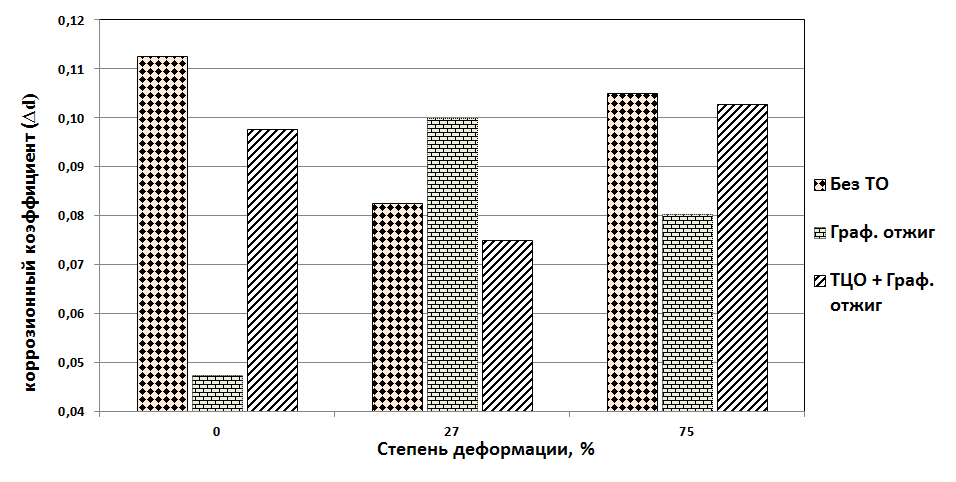
Рисунок 9 – Влияние термической обработки и степени предварительной холодной деформации на размерный коэффициент истирания
Выводы
- Увеличение степени деформации на образцах из стали 85 интенсифицирует графитизацию цементита в стали: это обусловлено возникшими дефектами (микротрещины, искажения кристаллической решетки), деформирующимися в структуре при предварительной деформации.
- При наличии графита в микроструктуре стали 85 удельное электросопротивление должно увеличиваться. Однако сопротивление деформированных образцов после графитизирующего отжига с ТЦО меньше сопротивления тех же образцов после только графитизирующего отжига, но превышает значения образцов, не подвергавшихся термической обработке. Таким образом, наилучшее и стабильное значение удельного электросопротивления достигнуто при графиизирующем отжиге: ρ0% = 13,72•10-8 Ом•м; ρ27% = 13,71•10-8 Ом•м; ρ75% = 14,10•10-8 Ом•м.
- Плотность стали 85 при наличии графитных включений должна уменьшиться. Но, из приведенных данных видно, что данное условие соблюдается лишь при высокой степени деформирования образцов: без термической обработки плотность стали равна 7,9463 г/см3, графитизирующий отжиг – 7,9243 г/см3, графитизирующий отжиг с последующей термоциклической обработкой – 7,8839 г/см3.
- Данные полученные при испытании на износ указывают, что коэффициенты истирания в сталях подвергавших термической обработке, в целом, превышают значения, полученные у образцов без термической обработки, что свидетельствует о большей склонности к износу образцов, не подвергавшихся термической обработке. Однако при высоких степенях деформирования (75%) стали, подвергавшиеся графитизирующему отжигу (КΔd = 0,07503; КΔm = 3,4•10-4) и графитизирующему отжигу совмещенному с ТЦО (КΔd = 0,10279; КΔm = 3,6•10-4) коэффициенты истирания ниже чем у образцов, не подвергавшихся термической обработке (КΔd = 0,10504; КΔm = 4,5•10-4). Таким образом, проведенные эксперименты не дают однозначного ответа на поставленную задачу. Поэтому имеет смысл продолжить и углубить исследования в вопросе влияния графитизации на свойства эвтектоидной стали и возможности ее использования в производстве швейных машинных игл.
Список источников
- Коковихин, Ю.И. Технология сталепроволочного производства: учеб. / Ю.И. Коковихин; ДонНТУ. – К.: Университет, 1995. – 608 с.
- ГОСТ 8030-80. Иглы для шитья вручную. Технические условия. – Введ. 1981-07-01. – М.: Изд-во стандартов, 1987. – 20 с.
- ГОСТ 22249-82. Иглы к швейным машинам. – Введ. 1984-01-01. – М.: Изд-во стандартов, 1997. – 57 с.
- Свой бизнес: производство швейных игл [Электронный ресурс] – Режим доступа: http://www.openbusiness.ru/html/dop11/shveinie-igli.htm - Загл. с экрана.
- Червяков, Ф.И. Швейные машины. / Ф.И. Червяков, А.А Николаенко. – М.: Машиностроение, 1977. – 416 с.
- Оборудование швейного производства : справочник / Н.М Вальщиков, А.И. Шарапин, И.А Идиатулин, Ю.Н. Вальщиков. – М.: Легкая индустрия, 1977. – 520 с.
- Triumph. Иглы с керамическим покрытием [Электронный ресурс] / Веллтекс-Украина. Все для швейного производства. – Режим доступа : \http://welltex.ua/page/igly-s-keramicheskim-pokrytiem/ - Загл. с экрана.
- Маточкин, В.А. Особенности термической обработки и подготовки поверхности высокоуглеродистой катанки-проволоки при волочении / В.А. Маточкин // Журн. «Сталь» - 2007. - № 6 – С. 55 – 57.
- Алимов, В.И. Фазовые и структурные превращения при деформационно-термической обработке проволоки / В.И. Алимов, О.В. Пушкина. – Донецк: Донбасс, 2012. – 242 с.
- Сташенко, В.И. Скоростная термообработка током высокой плотности при производстве высокопрочной проволоки из среднеуглеродистой стали / В.И. Сташенко // Бюл. «Черная металлургия» - 2011 – № 3 – С. 67-72.
- Парусов, В.В. Усовершенствование технологии производства игольной проволоки / В.В. Парусов, В.Н. Прокофьев, И.И. Долженков, М.И. Сорокин, В.З Марченко, Н.П. Нестерова // Журн. «Сталь» - 1980. - № 12 – С. 1090 – 1092.
- Бунин, К.П. Графитизация стали / К.П. Бунин, А.А, Баранов, Э.Н. Погребной. Киев, 1961 – 86 с.
- Пат. № 94241 України, МПК В23Р 15/00 (2014.01). Спосіб виробництва поршневих кілець / Алімов В.І., Шевелєв О.І., Пушкіна О.В., Георгіаду М.В., Зозуля А.П. - № u201403767; заявл. 10.04.2014; опубл. 10.11.2014