Content
- Introduction
- 1. General characteristics of the needle wire and needle from her
- 2. Features heat treatment blanks for needle wire and needle from her
- 3. Statement of the problem and research objectives
- 4. Materials, methods, equipment for research
- 5. The results of studies
- Conclusions
- List of sources
Introduction
Wire is a versatile construction material. It is used in all the branches of material production, This is caused by the variety of properties and dimensions, and mass consumption requires adaptability and economically justified schemes of manufacturing [1].
One of the consumer product made of wire are needles. Needles are divided into sewing and medical, made from high-carbon and stainless steels, respectively. The needles as medical and sewing type meet high technological requirements. Production of the needle wire required quality feasible, provided a stable and high-quality process at all stages of production. The most important role in the production of finished products from the needle wire assigned to heat treatment. Obtaining the required physical and mechanical properties is achieved by optimum material structure of the needle wire.
With the rapid development of technology, including the production of sewing machines, as well as their processed material there is a need to create a better needle products. It should be noted that in Ukraine assortment of sewing needles is limited. Domestic manufacturers of household and industrial sewing needles are forced to compete with foreign manufacturers that produce better quality, but at the same time, more expensive products. In an effort to reduce costs production, domestic producers at the same time reduce the performance of mechanical characteristics of the finished product from the needle wire.
Thus, the problems in the production of needle domestic products are relevant, that certainly shows the importance of a study on the development and improvement of existing methods heat treatment of products as draft and final. It should take into account the limited budget of domestic enterprises, which does not allow for expensive treatments needle products.
1. General characteristics of the needle wire and needle from her
Needle wire is used for the manufacture of needles for different purposes. The most famous - a needle for hand sewing (there are 8 species [2]), the machine (15 types according to the type of performance rod and more than 50 - by type of performance tip [3]). For the production of the sewing needle and needle wire is mainly used carbon tool steel, containing from 0.65 to 1.29% carbon. This steel is marked U7A-U12A, where the numbers indicate the number of carbon steel in tenths, and the letter «A» means high quality steel.
Sewing needles are made on the so-called needle-platinum production. The range of large enterprises can There are several thousand different kinds of needles of various thickness, shape of the tip and the surface of the coating [4]. Machine needle has a more complex structure compared with a conventional household needle (Fig. 1). Hand household needle is a smooth thin cylindrical rod sharpened at one end and the other having an ear for threading thread. Machine needle has a more complex structure that meets the special conditions of its work [5].
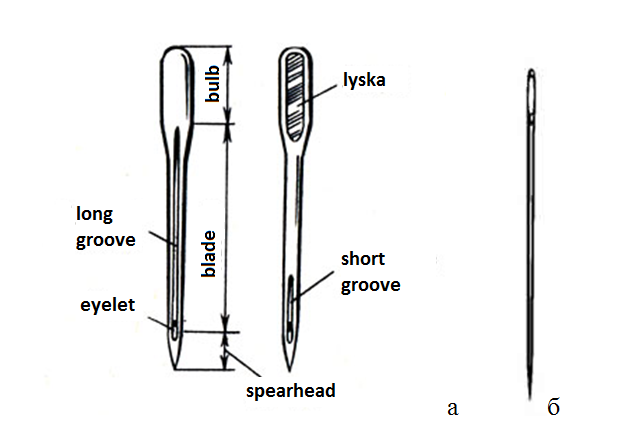
Figure 1 - Needle machine (a) and household (b)
In high-speed machines during the piercing needle tissue due to friction forces the needle is heated to 350-400°C with the release of a large heat. Heating the needle is particularly dangerous for materials containing chemical fibers. During high-speed sewing needle heated above the melting point of fibers, however, in contact with a heated needle, the fibers are melted and clog the eyelet and a long needle groove.
To reduce the heating temperature of the needle used: reducing blade changing cross-sectional geometry of the needle, cooling air or air-water mixture used as teplootdatchikov various fluids prior to breaching holes for the passage of the material of the needle by electrical et al. [6]. Also for controlling heating of needles, during the operation, some coating manufacturers use. Coatings for needles made of titanium nitride; phosphorus + Teflon; phosphate resin; chrome; a combination of titanium or a ceramic in combination with carbon [7].
The coefficient of friction is an important characteristic in the study of sewing needles, since the higher coefficient of friction, the more heated surface as a needle, and cross-linkable material, which in turn leads to the formation of marriage. Coefficient of friction in the clothing industry can range from 0.15 to 0.65 [7].
In such a way in the manufacture of needle products it is necessary to observe the needle stringent set of needles, but batch production must be carried out with minimal effort. Important factors that must be considered when developing a method preventing the needle during the heating operation is the coefficient of friction.
2. Features heat treatment blanks for needle wire and needle from her
The basic process for obtaining the required mechanical properties and microstructure of the needle wire and sewing needles is heat treatment. The classic method of heat treating rod - is patenting and annealing on the granular perlite[8]. Patenting occurs in the following modes: austenization steel at 920-950°C and cooling melt lead or salt at 480-550°C [8]. However patenting significantly reduces the strength characteristics, but also increases the ductility. in work [9] instead of patenting proposed short annealing saltpeter bath at a temperature of 520 ± 5°C and electrocution. According to the research, this annealing slightly increases the strength characteristics and indicators of elongation. Annealing granular perlite is carried out at a temperature of 680°C with followed by cooling in air [9].
СThere are technological schemes, excluding the patenting process [10]. Data flow diagrams include high-speed heat-treated high-density current (HDC). The essence of this technology lies in the short-term thermal exposure to temperatures 500-600°C. The duration of exposure to the current (0.5 - 4) depends on the density of the transmitted power (35 - 80 A/mm2 - for carbon steels [10]). This technology improves heat treating steel strength characteristics, without lowering the plastic properties and process forming a supportive structure is considerably faster in comparison with the classic types of heat treatment.
Thus, the main heat-treatment of high-carbon steel wire is patenting. Finished sewing needles subjected to quenching and tempered to achieve desired mechanical properties. Note that the needle-type after the final production heat treatment should have a structure consisting of martensite minutely bristled with evenly distributed carbides (Fig. 2). Hardness hand and machine needle should be in the range of 54 ... 62 HRC [2, 5].
3. Statement of the problem and research objectives
In our region the range of sewing needles is limited. Dimensions within the range of needles 35 - 80 mm in length and 0.6 - 1.8 mm diameter[2]. Domestic manufacturers of household and industrial sewing needles are forced to compete with major manufacturers. Quality sewing needles manufactured and imported into this country from Europe (Germany, UK, France), Japan, China. Most domestic companies prefer to produce their own needles and outsource their production to Chinese factories. They finished products packaged in its own package and sell it under its own brand [4].
Thus, the aim of this work is to improve the production of machine sewing needles by improving their manufacturing process, namely the improvement of the classical methods of heat treatment, namely the development of non-traditional ways.
Coefficient of friction, as indicated above, an important characteristic which must be taken into account when developing methods for improving the needle products. Using a variety of coatings to reduce the coefficient of friction is a costly process, so this work is devoted to the study of graphitizing needle eutectoid steel wire in order to use graphite as a lubricant, which lowers the adhesion surface needle with the crosslinkable material.
4. Materials, methods, equipment for research
To study the effect graphitization using 2 mm diameter wire eutectoid steel (steel 85) and the undeformed deformation degrees with 27% and 75%. chemical composition steel given in Table 1.
C | Si | Mn | Ni | S | P | Cr | Cu |
0.82-0.9 | 0.17-0.37 | 0.5-08 | <0.25 | <0.035 | <0.035 | <0.25 | <0.2 |
This wire was cut into a sample of length 30 mm. Samples were subjected to graphitizing annealing and annealing, combining the graphitized with thermocyclic treatment.
Graphitizing annealing was performed as follows.
Samples were placed in a crucible and covered carburizing. The crucible with the sample placed in a furnace (Тfur = Тroom ≈ 18°С) and heated to 750-760°C. Holding at this temperature was 5 hours. then slowed to cool for 1 hour to 690-700°C; holding at this temperature for 2 hours. Further cooling of the samples produced in the furnace. Mode graphitizing annealing is shown in Figure 3.
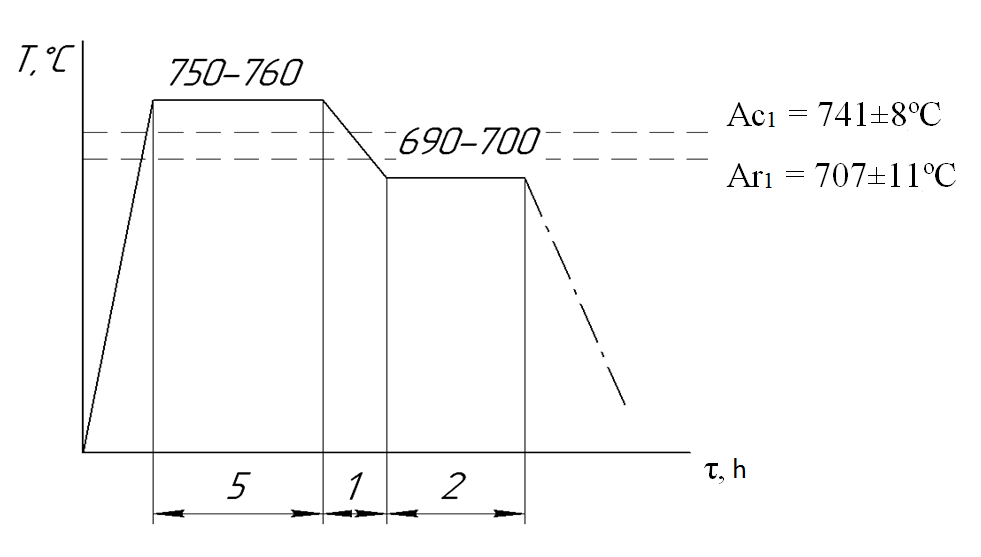
Figure 3 - Regime of graphitizing annealing steel samples 85
After the heat treatment, the specimens were mounted in epoxy glue mandrel and thin sections were prepared by standard techniques. Sections were etched at 6%-th solution of iodine in alcohol. Investigation of the structure was carried out on microscope MIM-7. To brighten and expand the limits of zoom used the immersion method of microscopic observation. As the immersion liquid used castor oil. As a result, on the microscope MIM-7 increase was obtained in 1350.
Influence of thermal cycling and graphitization treatment was performed on samples 30 mm long, and with the undeformed deformation degree of 27% and 75%. Thermocyclic treatmentwas carried out according to the type of pendulum annealing. The crucible with the sample was placed in an oven and heated to 750-760 & degS. Held at this temperature 1 hour. Thereafter, the furnace was cooled to a temperature of 670-680 & degS and kept at this temperature for 1 hour. Then, heating is performed again (the furnace) to a temperature 750-760 & degS and holding at this temperature for 1 hour. In this manner take another one heating and cooling, with the extracts for one hour, followed by cooling in an oven. Thus, we have three hour exposure at a temperature of 750-760 & degS and holding for two hours at a temperature of 670-680°C. Thermal cycling mode processing is shown in Figure 4.

Figure 4 - Regime of graphitizing annealing combined with thermocyclic treatment
To compare the effect on the properties of the eutectoid steel graphitizing annealing and aligning subsequent graphitizing annealing was conducted TCT some research for samples of three types: 1) without heat treatment; 2) after graphitizing annealing; 3) after graphitizing annealing and TCT.
- Takes measurements of the electrical four-probe method.
- Determination of density by hydrostatic weighing.
- Produces a wear test and analyzed the data obtained by the calculated coefficient of friction: mass (КΔm) and size (КΔd).
5. The results of studies
The microstructure of the samples after the graphitizing annealing is shown in Figure 5. As can be seen from the photographs of the microstructure after annealing managed to get the graphite inclusions. Graphite inclusions have a spherical shape. However graphitization steel did not occur on the sample not subjected to cold plastic deformation. As the degree of compression of the samples, we see that an increasing number of graphite inclusions. However, in samples having a degree of deformation of 25 and 75% of graphite inclusions are unevenly distributed across the length of the sample.
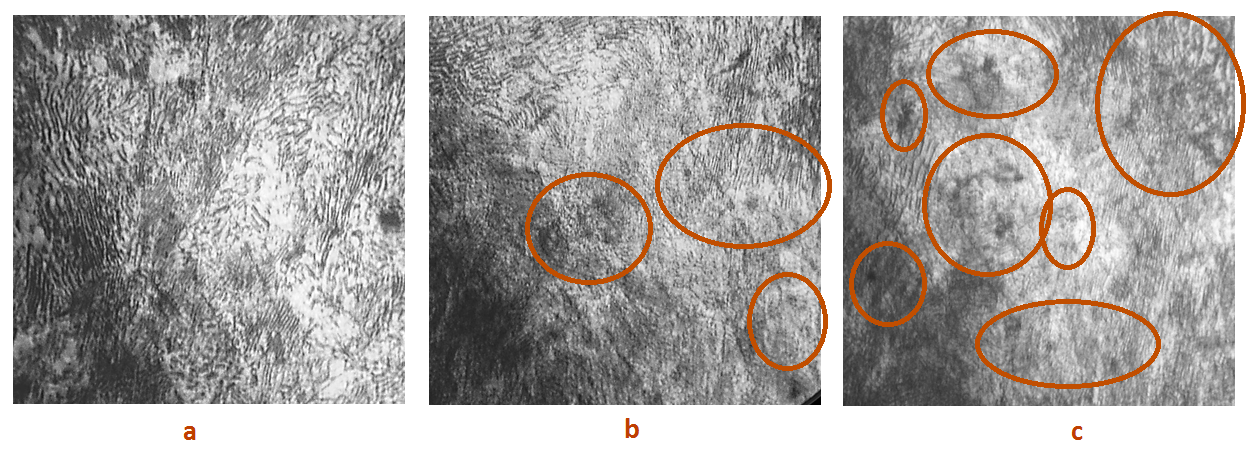
The microstructure of the samples (graphite inclusions circled) with degrees of compression, x1350:
а) is not deformed; b) 27%; c) 75%
Thus, increasing the degree of graphitization of cementite intensifies the deformation in the steel: this is due to defects arising (microcracks distortion of the crystal lattice), deforming the structure during pre-deformation. A similar conclusion was made in [12]. This method graphitization eutectoid steel was patented [13].
The influence of the degree of strain on the electrical resistance, depending on the heat treatment is shown in Figure 6.
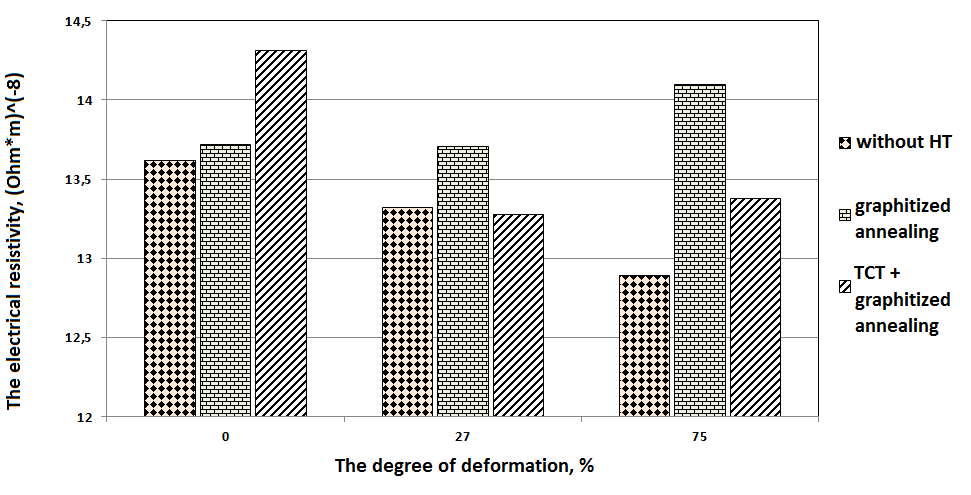
Figure 6 - Effect of heat treatment and the degree of preliminary cold deformation on the resistivity of the steel 85
Changing the density of steel, depending on the degree of deformation and heat treatment of steel is shown in Figure 7.
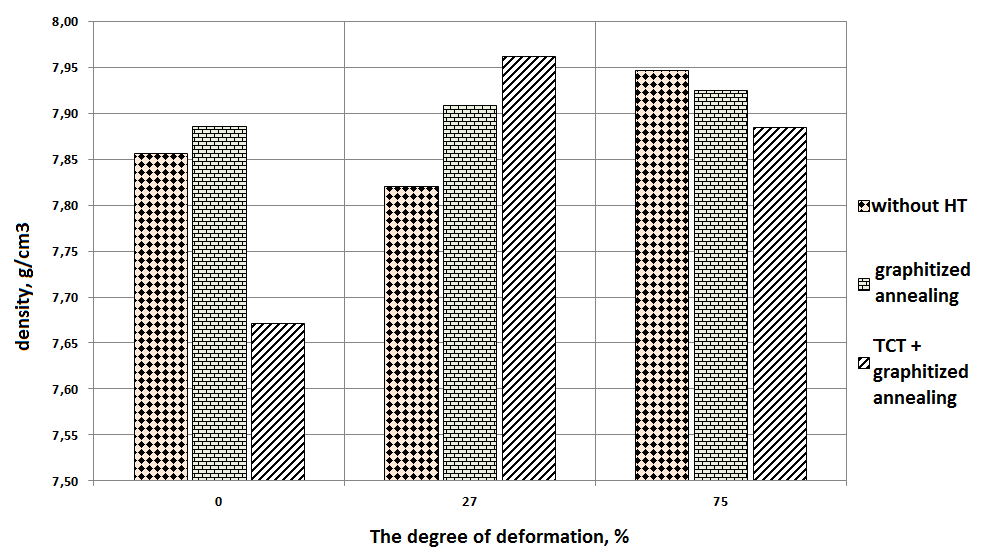
Figure 7 – Effect of heat treatment and the degree of preliminary cold deformation on the density of steel
Figures 8 and 9 show the effect of the degree of deformation and heat treatment on the coefficient of friction.
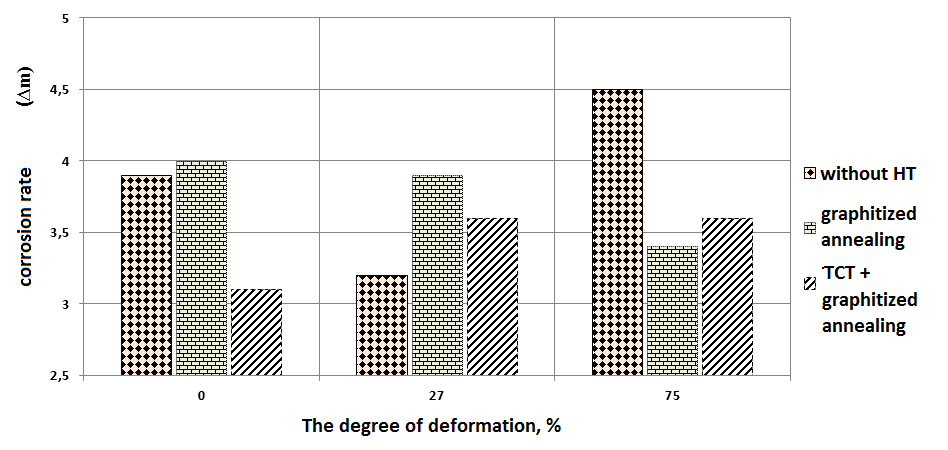
Figure 8 – Effect of heat treatment and the degree of preliminary cold deformation on the mass ratio abrasion
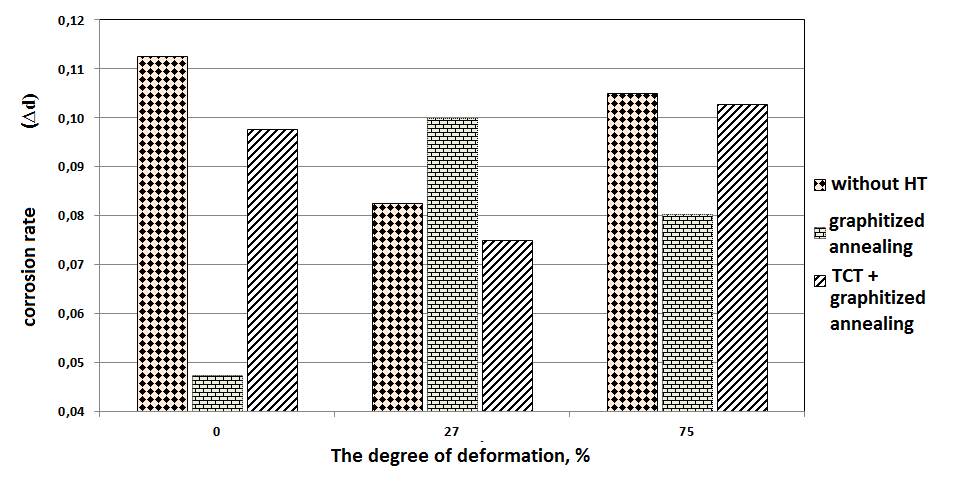
Figure 9 – Effect of heat treatment and the degree of preliminary cold deformation on the size coefficient of friction
Conclusions
- An increase in the degree of deformation on samples of steel 85 intensifies the graphitization of cementite in steel: this is due to defects arising (microcracks, distortion of the crystal lattice), deforming the structure during pre-deformation.
- In the presence of graphite in the microstructure of steel 85 the electrical resistivity should increase. However, the resistance of the deformed samples after graphitizing annealing TCT less resistance to the same samples after only graphitizing annealing, but exceed the value of the samples did not subjected to heat treatment. In such a way the best and stable value of the electrical resistivity achieved by grafiizing annealing: ρ0% = 13,72•10-8 Оhm•m; ρ27% = 13,71•10-8 Оhm•m; ρ75% = 14,10•10-8 Ohm•m.
- The density of steel 85 in the presence of graphite inclusions should decrease. However, from the data it is clear that this condition is met only if a high degree of deformation of the samples: no heat treatment is equal to the density of steel 7,9463 g/сm3, graphitized annealing – 7,9243 g/сm3, graphitized annealing followed by thermocyclic treatment– 7,8839 g/сm3.
- Data obtained from the wear test indicate that the coefficient of friction in the steel is subjected to heat treatment, generally, exceed the values obtained from samples without heat treatment, which indicates a greater propensity to wear the samples not subjected to heat treatment. however at high degrees of deformation (75%) of steel subjected to annealing graphitized (КΔd = 0,07503; КΔm = 3,4•10-4) and graphitized, combining the annealing with TCT (КΔd = 0,10279; КΔm = 3,6•10-4) coefficient of friction lower than that of the samples were not subjected to heat treatment (КΔd = 0,10504; КΔm = 4,5•10-4). In this summary, these experiments do not give a clear answer to the question posed. So it makes sense to continue and deepen research in influencing graphitization on the properties of eutectoid steel and the possibility of its use in the manufacture of sewing machine needles.
List of sources
- Коковихин, Ю.И. Технология сталепроволочного производства: учеб. / Ю.И. Коковихин; ДонНТУ. – К.: Университет, 1995. – 608 с.
- ГОСТ 8030-80. Иглы для шитья вручную. Технические условия. – Введ. 1981-07-01. – М.: Изд-во стандартов, 1987. – 20 с.
- ГОСТ 22249-82. Иглы к швейным машинам. – Введ. 1984-01-01. – М.: Изд-во стандартов, 1997. – 57 с.
- Свой бизнес: производство швейных игл [Электронный ресурс] – Режим доступа: http://www.openbusiness.ru/html/dop11/shveinie-igli.htm - Загл. с экрана.
- Червяков, Ф.И. Швейные машины. / Ф.И. Червяков, А.А Николаенко. – М.: Машиностроение, 1977. – 416 с.
- Оборудование швейного производства : справочник / Н.М Вальщиков, А.И. Шарапин, И.А Идиатулин, Ю.Н. Вальщиков. – М.: Легкая индустрия, 1977. – 520 с.
- Triumph. Иглы с керамическим покрытием [Электронный ресурс] / Веллтекс-Украина. Все для швейного производства. – Режим доступа : \http://welltex.ua/page/igly-s-keramicheskim-pokrytiem/ - Загл. с экрана.
- Маточкин, В.А. Особенности термической обработки и подготовки поверхности высокоуглеродистой катанки-проволоки при волочении / В.А. Маточкин // Журн. «Сталь» - 2007. - № 6 – С. 55 – 57.
- Алимов, В.И. Фазовые и структурные превращения при деформационно-термической обработке проволоки / В.И. Алимов, О.В. Пушкина. – Донецк: Донбасс, 2012. – 242 с.
- Сташенко, В.И. Скоростная термообработка током высокой плотности при производстве высокопрочной проволоки из среднеуглеродистой стали / В.И. Сташенко // Бюл. «Черная металлургия» - 2011 – № 3 – С. 67-72.
- Парусов, В.В. Усовершенствование технологии производства игольной проволоки / В.В. Парусов, В.Н. Прокофьев, И.И. Долженков, М.И. Сорокин, В.З Марченко, Н.П. Нестерова // Журн. «Сталь» - 1980. - № 12 – С. 1090 – 1092.
- Бунин, К.П. Графитизация стали / К.П. Бунин, А.А, Баранов, Э.Н. Погребной. Киев, 1961 – 86 с.
- Пат. № 94241 України, МПК В23Р 15/00 (2014.01). Спосіб виробництва поршневих кілець / Алімов В.І., Шевелєв О.І., Пушкіна О.В., Георгіаду М.В., Зозуля А.П. - № u201403767; заявл. 10.04.2014; опубл. 10.11.2014