- Вступ
- 1. Загальна характеристика голковго дроту і голок з нього
- 2. Особливості термообробки заготовки для голковго дроту і голок з нього
- 3. Постановка завдання і мета досліджень
- 4. Матеріали, методика, обладнання для дослідження
- 5. Результати досліджень
- Висновки
- Список джерел
Вступ
Дріт є універсальним конструкційним матеріалом. Він застосовується в усіх без винятку галузях матеріального виробництва, цим обумовлюється різноманіття властивостей і розмірів, а масовість споживання вимагає технологічності і економічно обґрунтованих схем виготовлення [1].
Одними з виробів масового споживання, виготовлених з дроту, є голки. Голки поділяються на швейні та медичні, виготовлені з високовуглецевих і нержавіючих марок сталі відповідно. До голок як медичного, так і швейного типу, пред'являються високі технологічні вимоги. Виготовлення голкового дроту необхідної якості здійсненно за умови стійкого і якісного технологічного процесу на всіх етапах виробництва. Найбільш важлива роль у виробництві готових виробів з голкового дроту відведена термічній обробці. Отримання необхідних фізико-механічних характеристик досягається за рахунок отримання оптимальної структури матеріалу голкового дроту.
У зв'язку з швидким розвитком техніки, в тому числі і виробництва швейних машин, а також оброблюваного ними матеріалу, виникає необхідність створення більш якісної голкової продукції. Слід зазначити, що в Україні асортимент швейних голок досить обмежений. Вітчизняні виробники побутових і промислових швейних голок змушені конкурувати із зарубіжними виробниками, які випускають більш якісну, але й разом з тим, більш дорогу, продукцію. У спробах зменшити витрати на виробництво, вітчизняні виробники в теж час зменшують показники механічних характеристик готового виробу з голкового дроту.
Таким чином, проблеми в галузі виробництва голкової продукції вітчизняного виробництва є актуальними, що безумовно свідчить про важливість проведення дослідження з розробки та вдосконалення існуючих способів проведення термічної обробки виробів, як попередньої, так і остаточної. При цьому варто враховувати лімітований бюджет вітчизняних підприємств, який не дозволяє проводити дорогих обробок голкової продукції.
1. Загальна характеристика голковго дроту і голок з нього
Голковй дріт використовується для виготовлення голок різного призначення. Найбільш відомі - це голки для шиття вручну (існує 8 видів [2]), машинні (15 видів за типом виконання стержня і більше 50 - по виду виконання вістря [3]). Для виробництва голкового дроту і швейних голок в основному використовують інструментальну вуглецеву сталь, містить від 0,65 до 1,29% вуглецю. Така сталь має маркування У7А-У12А, де цифри означають кількість вуглецю в стали в десятих частках, а буква «А» означає високу якість сталі.
Швейні голки виробляються на так званому голково-платиному виробництві. Асортимент великих підприємств може нараховувати кілька тисяч різних найменувань голок різної товщини, форми вістря і виду покриття поверхні [4]. Машинна голка має більш складну конструкцію в порівнянні із звичайною побутовою голкою (рис. 1). Ручна побутова голка являє собою гладкий тонкий циліндричний стрижень, загострений на одному кінці, а на іншому має вушко для протягування нитки. Машинна голка має більш складну конструкцію, що відповідає спеціальним умовам її роботи [5].
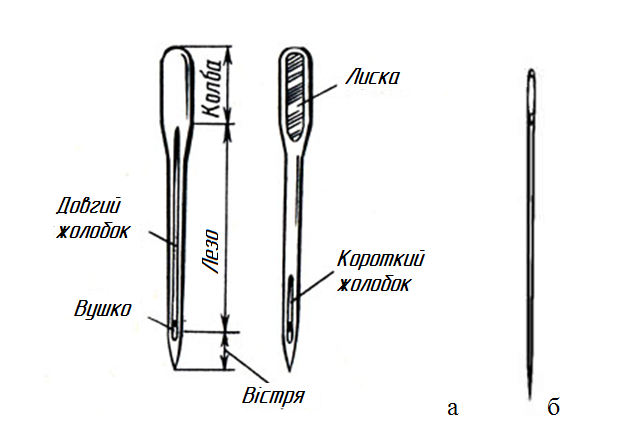
Рисунок 1 - Голка машинна (а) і побутова (б)
У швидкісних машинах під час проколювання тканини голкою за рахунок сил тертя голка нагрівається до 350-400°С з виділенням великої кількості тепла. Нагрівання голки особливо небезпечний для матеріалів, що містять хімічні волокна. У процесі швидкісного шиття голка нагрівається вище температури плавлення хімічних волокон, тому при зіткненні з нагрітою голкою ці волокна розплавляються і забивають вушко і довгий жолобок голки.
Для зниження температури нагріву голки застосовують: редукування леза, зміна геометрії поперечного перерізу голки, охолодження повітрям або повітряно-водяний сумішшю, використання в якості теплоотдатчика різних рідин, попереднє пророблення в матеріалі отвори для проходу голки електричним методом та ін. [6]. Також для боротьби з нагріванням голок, в процесі роботи, деякі виробники використовують покриття. Покриття для голок виконують з нітриду титану; фосфор + тефлон; фосфатні смоли; хромове; поєднання титанового або керамічного у поєднанні з карбоновим[7].
Коефіцієнт тертя є важливою характеристикою при вивченні швейних голок, оскільки, чим вище коефіцієнт тертя, тим сильніше нагріваються поверхні, як голки, так і матеріалу, який зшивається, що в свою чергу тягне за собою утворення шлюбу. Коефіцієнт тертя в швейному виробництві може варіюватися в межах від 0,15 до 0,65 [7].
Таким чином, при виробництві голкової продукції необхідно дотримуватися жорсткіших вимог, встановлених до голок, але серійне виробництво повинно здійснюватися з мінімальними витратами. Важливим показником, який необхідно враховувати при розробці способу, що запобігає нагріву голки в процесі роботи, є коефіцієнт тертя.
2. Особливості термообробки заготовки для голковго дроту і голок з нього
Основним процесом для отримання необхідних механічних властивостей і мікроструктури голкового дроту і швейних голок є термообробка. Класичний спосіб термообробки катанки - це патентування і відпал на зернистий перліт [8]. Патентування відбувається за наступним режимом: аустенізація стали при 920-950°С та охолодження в розплаві свинцю або солі при 480-550°С [8]. Однак патентування значно знижує міцнісні характеристики, але підвищує пластичність. У роботі [9] взамін патентуванню запропонований короткочасний відпал в селітрової ванні при температурі 520 ± 5°С і електрострумом. Згідно з проведеними дослідженнями, такий відпал дещо підвищує характеристики міцності і показники подовження. Відпал на зернистий перліт проводиться при температурі 680°С з наступним охолодженням на повітрі [9].
Існують технологічні схеми, що виключають процес патентування [10]. Дані технологічні схеми включають в себе швидкісну термообробку струмом високої щільності (ТВП). Суть такої технології полягає в короткочасному тепловій дії до температур 500-600°С. Тривалість дії струму (0,5-4с) залежить від щільності пропускається струму (35-80 А/мм2 - для вуглецевих сталей [10]). Така технологія термообробки дозволяє підвищити характеристики міцності сталі, що не знижуючи пластичних властивостей, і процес формування сприятливої ??структури протікає значно швидше, в порівнянні з класичними видами термічної обробки.
Таким чином, основний термообробкою дроту з високовуглецевої сталі є патентування. Готові швейні голки піддають гартуванню та відпуску з метою досягнення необхідних механічних властивостей. Слід зазначити, що голки виробничого типу після заключної термообробки повинні мати структуру, що складається з мелкоігольчатого мартенситу з рівномірно розподіленими карбідами (рис. 2). Твердість ручних і машинних голок повинна бути в інтервалі 54...62 HRC [2, 5].
3. Постановка завдання і мета досліджень
У нашому регіоні асортимент швейних голок досить обмежений. Розміри голок коливаються в межах 35 - 80 мм по довжині і 0,6 - 1,8 мм по діаметру [2]. Вітчизняні виробники побутових і промислових швейних голок змушені конкурувати з найбільшими виробниками. Якісні швейні голки виробляються та імпортуються в нашу країну з країн Європи (Німеччина, Великобританія, Франція), Японії, Китаю. Більшість вітчизняних компаній вважають за краще не виробляти голки самостійно, а розміщувати замовлення на їх виготовлення на китайських заводах. Вони розфасовують готову продукцію у власну упаковку і реалізують її під своєю торговою маркою[4].
Таким чином, метою даної роботи є удосконалення виробництва машинних швейних голок шляхом вдосконалення технологічного процесу їх виготовлення, а саме поліпшення класичних способів термічної обробки, а саме розробка нетрадиційних способів.
Коефіцієнт тертя, як зазначалося вище, це важлива характеристика, яку необхідно враховувати при розробці способів поліпшення голкової продукції. Використання різних покриттів для зниження коефіцієнта тертя є дорогим процесом, тому дана робота присвячена вивченню графитизации голкового дроту з евтектоїдной сталі, з метою використання графіту в якості мастильного матеріалу, понижуючого адгезію поверхні голки з матеріалом, що зшивають.
4. Матеріали, методика, обладнання для дослідження
Для дослідження впливу графитизации використовували дріт діаметром 2 мм з евтектоїдной сталі (сталь 85), недеформованого і зі ступенями деформації 27% і 75%. Хімічний склад сталі наведено в таблиці 1.
C | Si | Mn | Ni | S | P | Cr | Cu |
0.82-0.9 | 0.17-0.37 | 0.5-08 | <0.25 | <0.035 | <0.035 | <0.25 | <0.2 |
Даний дріт різали на зразки довжиною по 30 мм. Зразки піддавали графітізуючому відпалу і графітізіруючому відпалу поєднаному з термоциклічною обробкою.
Графітизуючий відпал проводили наступним чином.
Зразки поміщали в тигель і засипали карбюризатором. Тигель із зразками поміщали в піч (Тпеч = Тком ≈ 18°С) і нагрівали до 750-760°С. Витримка при даній температурі склала 5 годин. Після чого уповільнено охолоджували протягом 1 години до 690-700°С; витримка при даній температурі 2 ч. Подальше охолодження зразків виробляли разом з піччю. Режим графітізіруючого відпалу представлений на малюнку 3.
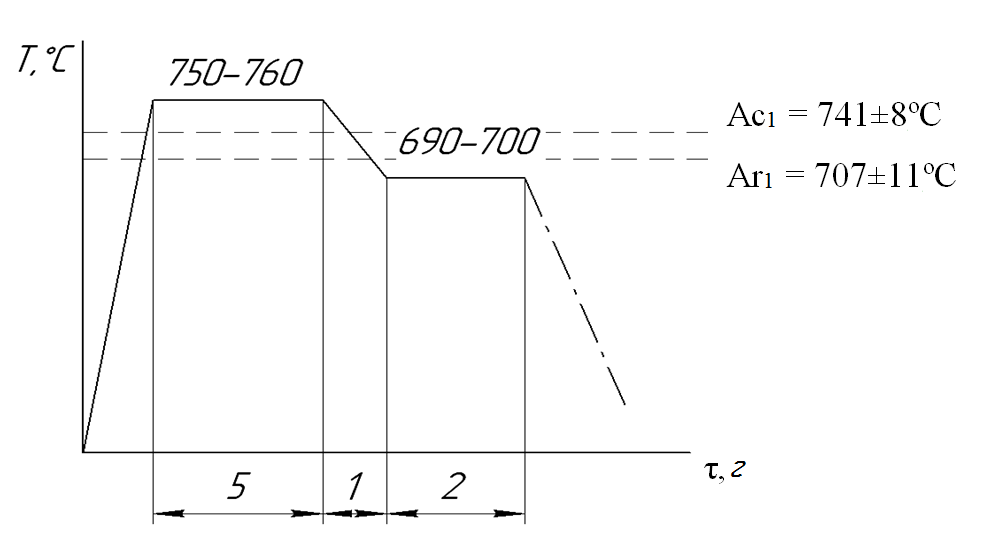
Рисунок 3 - Режим графітізіруючого відпалу зразків зі сталі 85
Після проведення термічної обробки зразки монтували в оправлення з епоксидним клеєм і виготовляли шліфи за стандартною технологією. Шліфи труїли в 6%-ому розчині йоду в спирті. Дослідження структури проводили на мікроскопі МІМ-7. Для посилення яскравості і розширення меж збільшення зображення використовували іммерсійний метод мікроскопічного спостереження. В якості иммерсионной рідини використовували касторове масло. У результаті на мікроскопі МІМ-7 було отримано збільшення 1350.
Вплив графитизації і термоциклічноїобробки проводили на зразках довжиною 30 мм, недеформовані і зі ступенями деформації 27% та 75%. Термоциклічна обробка проводилася за типом маятникового відпалу. Тигель із зразками поміщали в піч і нагрівали до 750-760 & degС. Витримували при даній температурі 1 годину. Після цього охолоджували з піччю до температури 670-680°С і витримували при даній температурі 1 годину. Потім проводиться знову нагрів (з піччю) до температури 750-760°С і витримка при даній температурі 1 година. Таким способом проводиться ще одне охолодження і один нагрів, з витримками по одній годині, з наступним охолодженням в печі. Таким чином, маємо три витримки протягом години при температурі 750-760°С і дві витримки протягом години при температурі 670-680°С. Режим термоцикличної обробки представлений на рисунку 4.
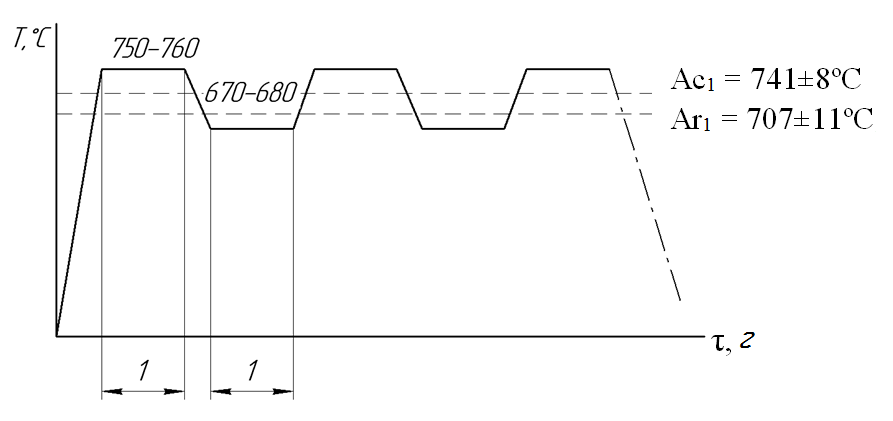
Рисунок 4 - Режим графітизуючого відпалу поєднаному з термоциклічною обрбкою
Для порівняння впливу на властивості евтектоїдной сталі графітізіруючого відпалу та поєднаного графітізіруючого відпалу з подальшою ТЦО були проведені деякі дослідження для зразків трьох видів: 1) без термічної обробки; 2) після графітізіруючого відпалу; 3) після графітізіруючого відпалу і ТЦО.
- Проводилось вимірювання електроопору чотирьохзондовим методом.
- Визначення густини методом гідростатичного зважування.
- Проводили випробування на знос і аналізували отримані дані за допомогою розрахованих коефіцієнтів стирання: масового (КΔm) и розмірного (КΔd).
5. Результати досліджень
Мікроструктура зразків після графітізіруючого відпалу представлена ??на рисунку 5. Як видно з фотографій мікроструктури, після відпалу вдалося отримати графітні включення. Графітні включення мають кулясту форму. Однак графітизація сталі не сталася на зразку, що не піддавався холодної пластичної деформації. У міру збільшення ступенів обтиснення зразків, бачимо, що і збільшується кількість графітних включень. Однак на зразках зі ступенем деформацій 25 і 75% графітні включення розподілені нерівномірно по всій довжині зразка.
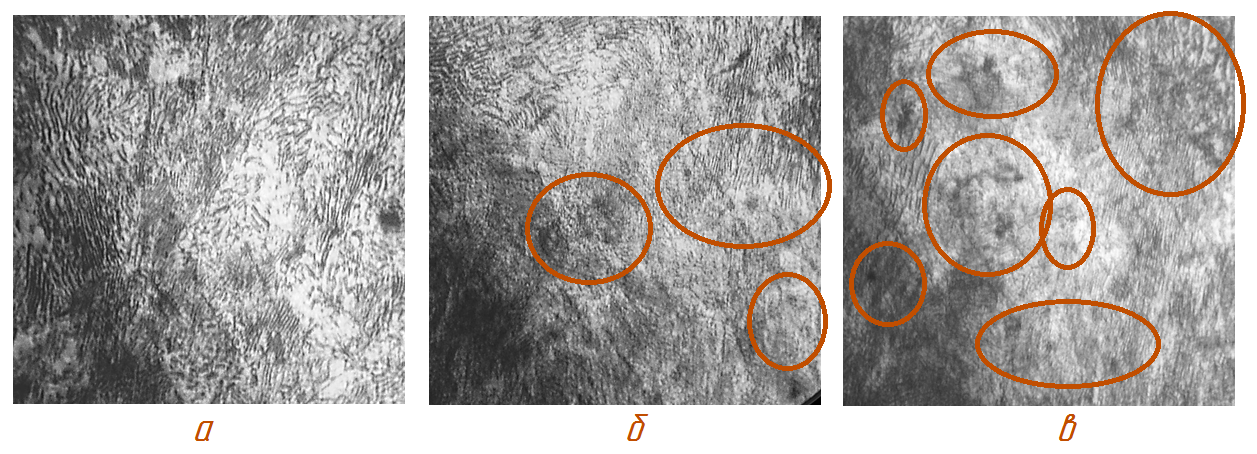
Рисунок 5 - Мікроструктура зразків (включення графіту обведені) зі ступенями обтиску, х1350:
а) не деформований; б) 27%; в) 75%
Таким чином, збільшення ступеня деформації інтенсифікує графітизацію цементиту в сталі: це обумовлено дефектами, що виникли (мікротріщини, викривлення кристалічної решітки), деформуються в структурі при попередній деформації. Аналогічний висновок був зроблений в роботі [12]. Даний метод графітизації евтектоїдной сталі був запатентований [13].
Вплив ступеня деформації на електроопір, залежно від термічної обробки, представлено на рисунку 6.
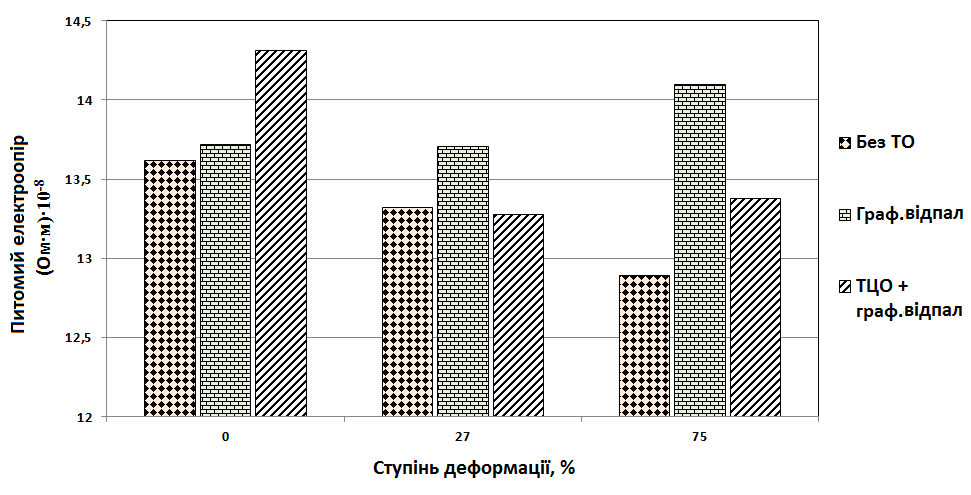
Рисунок 6 - Вплив термічної обробки і ступеня попередньої холодної деформації на питомий опір сталі 85
Зміна густини сталі, залежно від ступеня деформації і термічної обробки сталі представлено на рисунке 7.

Рисунок 7 – Вплив термічної обробки і ступеня попередньої холодної деформації на густину сталі 85
На рисунках 8 і 9 представлені вплив ступеня деформації і термічної обробки на коефіцієнти стирання.
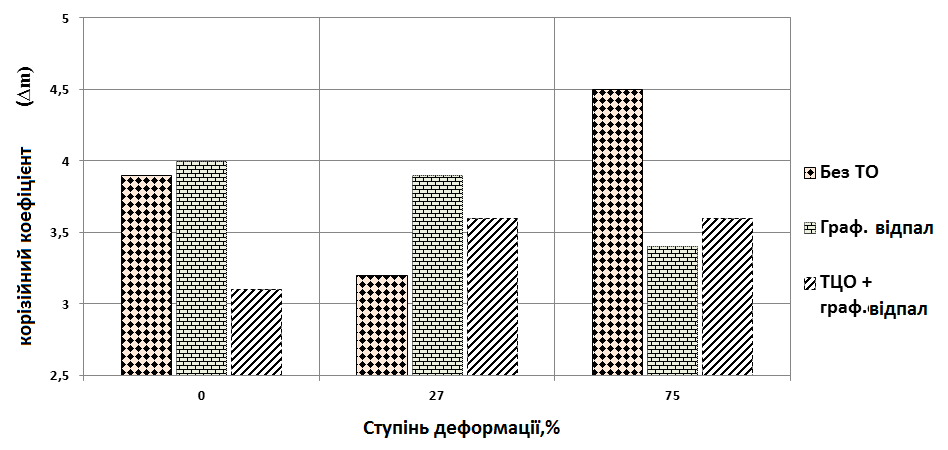
Рисунок 8 – Вплив термічної обробки і ступеня попередньої холодної деформації на масовий коефіцієнт стирання
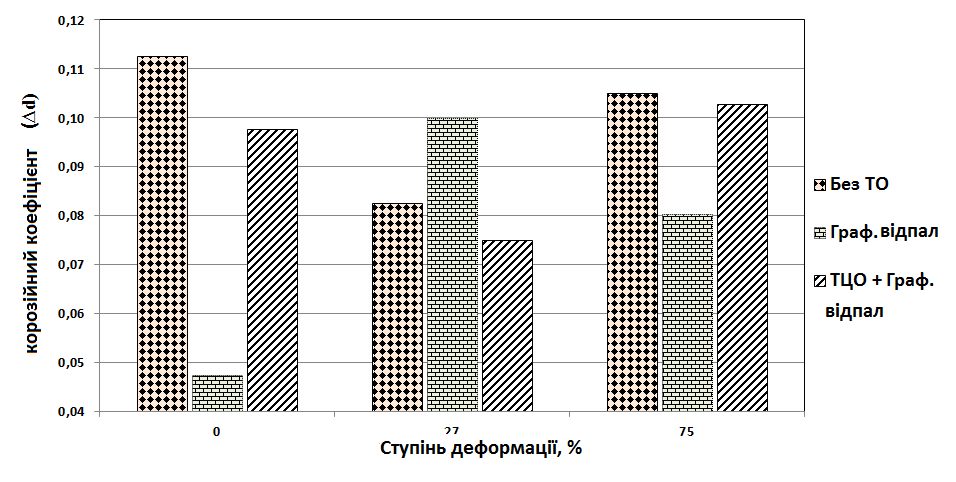
Рисунок 9 – Вплив термічної обробки і ступеня попередньої холодної деформації на розмірний коефіцієнт стирання
Висновки
- Збільшення ступеня деформації на зразках зі сталі 85 інтенсифікує графітизацію цементиту в сталі: це обумовлено, дефектами що виникли (мікротріщини, викривлення кристалічної решітки), які деформуються в структурі при попередній деформації.
- При наявності графіту в мікроструктурі сталі 85 питомий електроопір має збільшуватися. Однак опір деформованих зразків після графітізіруючого відпалу з ТЦО менше опору тих же зразків після тільки графітізіруючого відпалу, але перевищує значення зразків, що не піддавалися термічній обробці. Таким чином, найкраще і стабільне значення питомого електроопору досягнуто при графіізірующем відпалі: ρ0% = 13,72•10-8 Ом•м; ρ27% = 13,71•10-8 Ом•м; ρ75% = 14,10•10-8 Ом•м.
- Густина сталі 85 при наявності графітових включень повинна зменшитися. Але, з наведених даних видно, що дана умова дотримується лише при високому ступені деформування зразків: без термічної обробки густина сталі дорівнює 7,9463 г/см3, графітизуючий відпал – 7,9243 г/см3, графітизуючий відпал поєднаний з термоциклічною обробкою – 7,8839 г/см3.
- Дані отримані при випробуванні на знос вказують, що коефіцієнти стирання в сталях що піддавали термічній обробці, в цілому, перевищують значення, отримані у зразків без термічної обробки, що свідчить про більшу схильність до зносу зразків, що не піддавалися термічній обробці. Однак при високих ступенях деформування (75%) стали, що піддавалися графітізіруючому відпалу (КΔd = 0,07503; КΔm = 3,4•10-4) і графітизуючого відпалу поєднаного з ТЦО (КΔd = 0,10279; КΔm = 3,6•10-4) коефіцієнти стирання нижче ніж у зразків, що не піддавалися термічній обробці (КΔd = 0,10504; КΔm = 4,5•10-4). Таким чином, проведені експерименти не дають однозначної відповіді на поставлене завдання. Тому має сенс продовжити і поглибити дослідження в питанні впливу графітизації на властивості евтектоїдной сталі і можливості її використання у виробництві швейних машинних голок.
Список джерел
- Коковихин, Ю.И. Технология сталепроволочного производства: учеб. / Ю.И. Коковихин; ДонНТУ. – К.: Университет, 1995. – 608 с.
- ГОСТ 8030-80. Иглы для шитья вручную. Технические условия. – Введ. 1981-07-01. – М.: Изд-во стандартов, 1987. – 20 с.
- ГОСТ 22249-82. Иглы к швейным машинам. – Введ. 1984-01-01. – М.: Изд-во стандартов, 1997. – 57 с.
- Свой бизнес: производство швейных игл [Электронный ресурс] – Режим доступа: http://www.openbusiness.ru/html/dop11/shveinie-igli.htm - Загл. с экрана.
- Червяков, Ф.И. Швейные машины. / Ф.И. Червяков, А.А Николаенко. – М.: Машиностроение, 1977. – 416 с.
- Оборудование швейного производства : справочник / Н.М Вальщиков, А.И. Шарапин, И.А Идиатулин, Ю.Н. Вальщиков. – М.: Легкая индустрия, 1977. – 520 с.
- Triumph. Иглы с керамическим покрытием [Электронный ресурс] / Веллтекс-Украина. Все для швейного производства. – Режим доступа : \http://welltex.ua/page/igly-s-keramicheskim-pokrytiem/ - Загл. с экрана.
- Маточкин, В.А. Особенности термической обработки и подготовки поверхности высокоуглеродистой катанки-проволоки при волочении / В.А. Маточкин // Журн. «Сталь» - 2007. - № 6 – С. 55 – 57.
- Алимов, В.И. Фазовые и структурные превращения при деформационно-термической обработке проволоки / В.И. Алимов, О.В. Пушкина. – Донецк: Донбасс, 2012. – 242 с.
- Сташенко, В.И. Скоростная термообработка током высокой плотности при производстве высокопрочной проволоки из среднеуглеродистой стали / В.И. Сташенко // Бюл. «Черная металлургия» - 2011 – № 3 – С. 67-72.
- Парусов, В.В. Усовершенствование технологии производства игольной проволоки / В.В. Парусов, В.Н. Прокофьев, И.И. Долженков, М.И. Сорокин, В.З Марченко, Н.П. Нестерова // Журн. «Сталь» - 1980. - № 12 – С. 1090 – 1092.
- Бунин, К.П. Графитизация стали / К.П. Бунин, А.А, Баранов, Э.Н. Погребной. Киев, 1961 – 86 с.
- Пат. № 94241 України, МПК В23Р 15/00 (2014.01). Спосіб виробництва поршневих кілець / Алімов В.І., Шевелєв О.І., Пушкіна О.В., Георгіаду М.В., Зозуля А.П. - № u201403767; заявл. 10.04.2014; опубл. 10.11.2014